Anwar Abu-Zarifa, Manal Abu-Shammala, Anwar Al-Sheikh
Department of Mechanical & Industrial Engineering, Faculty of Engineering, Islamic University of Gaza, Gaza, Palestine
Correspondence to: Anwar Abu-Zarifa, Department of Mechanical & Industrial Engineering, Faculty of Engineering, Islamic University of Gaza, Gaza, Palestine.
Email: |  |
Copyright © 2018 The Author(s). Published by Scientific & Academic Publishing.
This work is licensed under the Creative Commons Attribution International License (CC BY).
http://creativecommons.org/licenses/by/4.0/

Abstract
In this paper particleboard panels were manufactured from sawdust and agricultural materials such that Wheat bran, Banana stems and Orange peels at different ratios (25 agricultural material: 75 sawdust) and (75 agricultural material: 25 sawdust) compared to 220g with constant amount 88g polypropylene (PP) under constant conditions at pressure 24 ton, 170C temperature, press time was 2.5 hours and particle size is 1 mm sieve. Properties of the boards were examined using mechanical tests, which include bending test and tensile test, and physical tests, which include water absorption and thickness swelling. The results of mechanical tests show that the maximum modulus of elasticity (MOE) value was 2160.78 Mpa at wheat 75%, the maximum modulus of rapture (MOR) value was 11.07 MPa at sawdust 100%, and the maximum value of max-stress was 7.8 MPa at banana 75%, the range of water absorption values was between (8.19%, 19.3%), these results were better than commercial types (MDF, Fiber and Press wood), which reach to 103% in MDF. The best mechanical properties were 75% wheat bran and sawdust 100% particleboard in bending test, and sawdust 100% particleboard in tensile test. Physical tests show that 75% banana particleboard has least water absorption value and thickness swelling percent, but 75% orange particleboard has the highest water absorption and thickness swelling percent.
Keywords:
Sustainability, Particleboards, Sawdust, Agricultural Waste
Cite this paper: Anwar Abu-Zarifa, Manal Abu-Shammala, Anwar Al-Sheikh, Sustainable Manufacturing of Particleboards from Sawdust and Agricultural Waste Mixed with Recycled Plastics, American Journal of Environmental Engineering, Vol. 8 No. 5, 2018, pp. 174-180. doi: 10.5923/j.ajee.20180805.02.
1. Introduction
Particleboard panel is product made of wood particles or other lignocellulose materials bonded together by resin under high temperature and pressure [1-4].The primary lignocellulose materials used in the particleboard industry are wood residues and agro-based residues are also investigated for producing particleboards such as palm stalks, rice straw, rice husks and other types plant waste. The successful utilization of such agricultural residues for particleboard production is significant for reducing the demand of woods and improving environment [5].Jinguo Wang and Yingcheng Hu studied the coir fiber board that reinforced with banana stem fiber and its improved the MOE and MOR of the hybrid coir fiber boards. However, the internal bond strength (IB) of the artificial board decreased and the thickness swelling from water absorption increased [6]. In other experiments V.S. Aigbodion, C.U. Atuanya and E.A. Igogori used orange peels as a reinforcing material and high-density polyethylene (HDPE). The results shown that there was a fairly uniform distribution of the orange peels particles in the microstructure of HDPE composites which is the major factor responsible for the improvement in the mechanical properties [7]. Also wheat flour was used in Takian Fakhrul's and Rubayyat Mahbub's study, it was mixed with sawdust and polypropylene, the young’s modulus and flexural modulus increased, whereas the yield strength and elongation at break decreased [8].The severe shortage in wood amounts that enters Gaza strip, at rate of 39175 ton/year, and there is a big amount of sawdust and agricultural wastes. As a way of finding a lasting solution to these problems, this paper aims to produce a particleboard from sawdust and agricultural wastes, mixed with plastic as agent for several objectives:1. Producing new manufactured wood with new high mechanical, physical properties and good price compared to other types of manufactured wood (MDF, Fiber, pressed wood).2. Solve problem of wearing out of wood that used in kitchen, doors, interior uses and other wet places.3. To analyze and interpret the main effect of the factors.In this paper, sawdust and agricultural materials that are banana stems, wheat bran and orange peels, each one of agricultural materials was mixed with sawdust in two ratios 25% and 75% with constant percent 40% of Polypropylene plastic.The constant conditions of this experiment were 24 ton pressure, 170C temperature, which is melting point of Polypropylene, 1 mm sieve size and press time is 2.5 hours, this time was required to reach heaters' temperature to 170C. The experiments were performed at Islamic University labs at temperature 25C.Seven particleboard samples were produced in this experiment with dimensions 20x15 cm and thickness 9±.2 mm, the samples tested by physical and mechanical tests to determine the effect of additive materials and it is percent on particleboard's properties.
2. Materials and Method
2.1. Materials
The materials used for production of particleboard from sawdust and agricultural waste: wheat bran, orange peels and banana stems, these materials were dried at oven until the moisture content reduced, and then mixed with polypropene plastic to increase strength and improve moisture resistance. The different moisture percent for each material shown in Table 1.Table 1. Moisture percent for materials 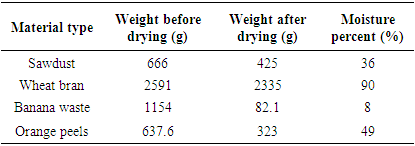 |
| |
|
2.2. Manufacture of Particleboard
In this paper, each one of agricultural materials mixed with sawdust at different ratios (25 agricultural material: 75 sawdust) and (75 agricultural material: 25 sawdust) compared to 220g with constant amount 88g polypropylene (PP) under constant conditions and pressed using steel mold with dimension of 15 cm×20 cm×4 cm.The constant conditions of this experiment were 24-ton pressure, 170C temperature, which is melting point of Polypropylene, 1 mm sieve size and press time is 2.5 hours, this time was required to reach heaters' temperature to 170C.
2.3. Mechanical and Physical Tests
To investigate the properties of manufactured particleboard samples, it was examined using mechanical and physical tests. For the mechanical properties static bending and tensile tests, for the physical properties water absorption and thickness swelling were performed according to ASTM D1037-12.
2.3.1. Static Bending Test
Static bending tests should be made to determine the flexural properties, such as modulus of rupture and apparent modulus of elasticity.The test was executed using Computerized Twin screw Universal Testing Machine UTM-Servo Controlled. The test specimen was cut as rectangular shape with dimensions 5×20 cm and thickness 9±.2 mm, as shown in Fig.1.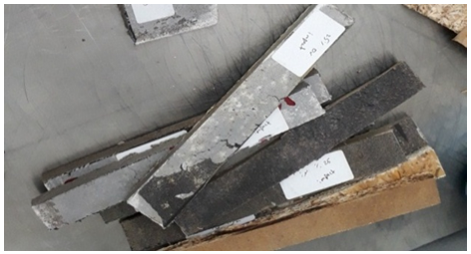 | Figure 1. Static bending tests' samples |
From this test, load-deformation curve was plotted, and then the values of MOE and MOR was calculated using the Eq1 and Eq2. | (1) |
 | (2) |
b = width of specimen measured in dry condition, (mm),d = thickness (depth) of specimen measured in dry condition, in. (mm),E = apparent modulus of elasticity, (MPa),L = length of span, (mm),P⁄y = slope of the straight line portion of the load deflection curve, (N/mm),Pmax = maximum load, (N),Rb = modulus of rupture, (MPa)
2.3.2. Tension Parallel to Surface Test
The tension test parallel to the surface should be made to determine the tensile strength in the plane of the panel. When required, the axial stiffness or modulus of elasticity can be determined.The sample clapped by jaws 3cm distance from each sides, and cross head displacement rate was 4mm/min according to ASTM D137-12. The max-tensile stress calculated from Eq3: | (3) |
b = width of the reduced cross-section of the specimen measured in dry condition, (mm),d = thickness of the specimen measured in dry condition, (mm),Pmax = maximum load, (N)Rt = maximum tensile stress, (MPa).
2.3.3. Water Absorption Test
Wood was soaked in water, this results a variation in weight of samples, this variation express on moisture content, which calculated from Eq4.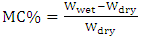 | (4) |
In this test, there are two methods were applied to measure water absorption:a) Soaking samples in water for 24 hr at 25C. b) Water absorption using by water bath for 4 hr at 50C.
2.3.4. Thickness Swelling
This test used to measure the variation in thickness of samples before and after soaking samples in water over period at constant temperature. After the two methods of water absorption, caliper is used to measure sample's thickness.
3. Results and Discussion
From load deflection, curve and the equations Eq1 and Eq2, MOE and MOR values were calculated. As shown in table 2, the max value of MOE is 2160.03MPa for Wheat 75% and the minimum is 436MPa for Banana 25%, although its max load higher than orange and banana 75%, since the effect of slope of each curve on MOE value in addition of max-load effect. For MOR values, the max value was 11.07 MPa for Sawdust 100% and the minimum value was 4.949 MPa for Orange 75%. There is a positive relation between additive material percent and MOR value, expect orange percent.Table 2. Results of mechanical and physical tests 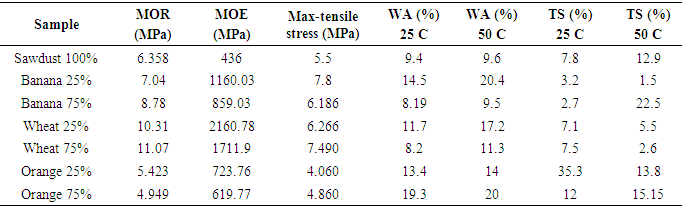 |
| |
|
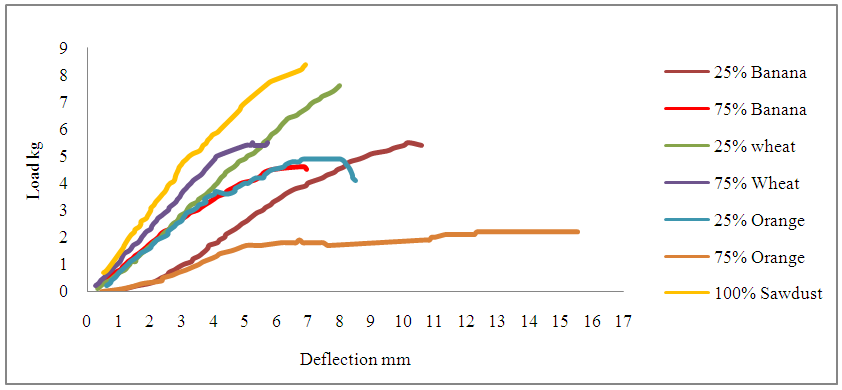 | Figure 2. Load- deflection |
The values of MOR for particleboard were compared with the MOR values of other types manufactured wood, which were MDF, fiber wood and pressed- wood, 5.64, 1.38, 1.5 MPa respectively. The MOR values of banana, wheat and sawdust particleboard were higher than MDF, fiber and press-wood.
3.1. Results of Mechanical Tests
As shown in Figure 3, the max value of tensile stress was 7.8 MPa for Banana 75% and the minimum was 4.06 MPa for Orange 25%. Compared to other types of manufactured wood existing in local market, the max-tensile stress values of Banana 75%, Sawdust 100% particle board were higher than MDF. All other particleboard max- stress values higher than fiber and press wood.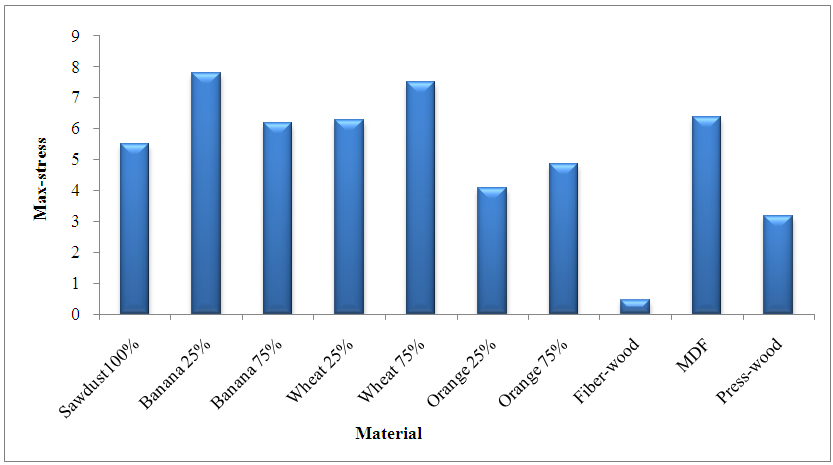 | Figure 3. Max- stress values |
3.2. Results of Physical Tests
As shown in Figure 4, the values of WA% of particleboard were much lower than WA values of commercial wood (MDF, Fiber, Press) and MDF was the highest WA%.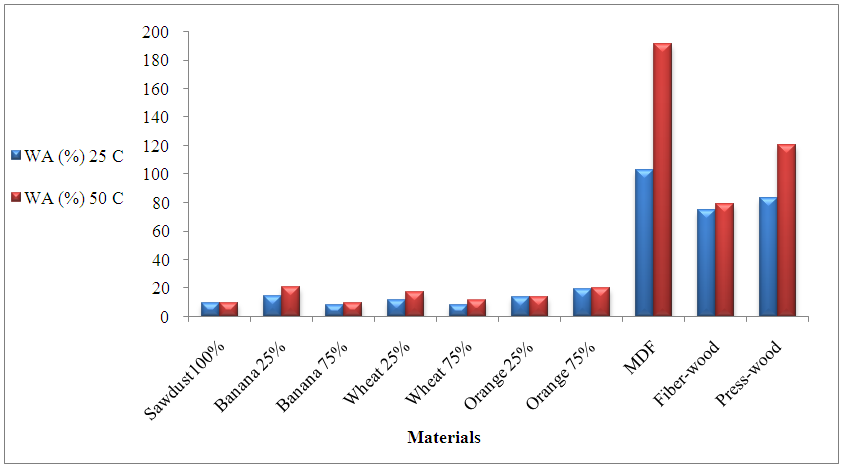 | Figure 4. Water Absorption results |
Water bath method was used to study the effect of temperature on water absorption values. There is positive relationship between water absorption and temperature, as shown in Figure 5 this rule doesn't applied on thickness swelling test, since the material compression ability has larger effect than temperature.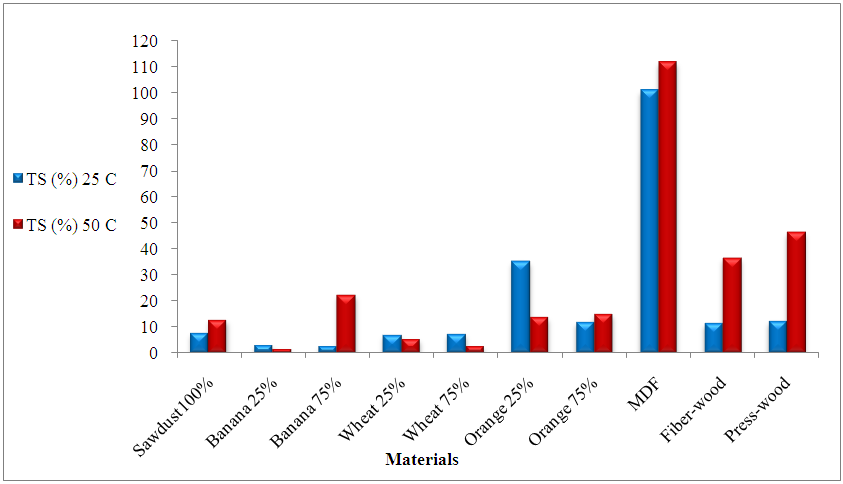 | Figure 5. Thickness swelling results |
3.3. Results Using Software Program Minitab®
The test results of MOE, MOR and max-stress were analyzed using Minitab program. The data is entered and 2-Way ANOVA was applied to determine the effect of the two factors were additive material type (wheat bran, banana stems, orange peels) and material percent (75%, 25%) and their interaction on three responses (MOE, MOR, max- stress).As shown in Figure 6, there is positive effect of material percent on MOE value. In case of material, straw (wheat bran) has the largest max-stress value and orange peels has minimum MOE value.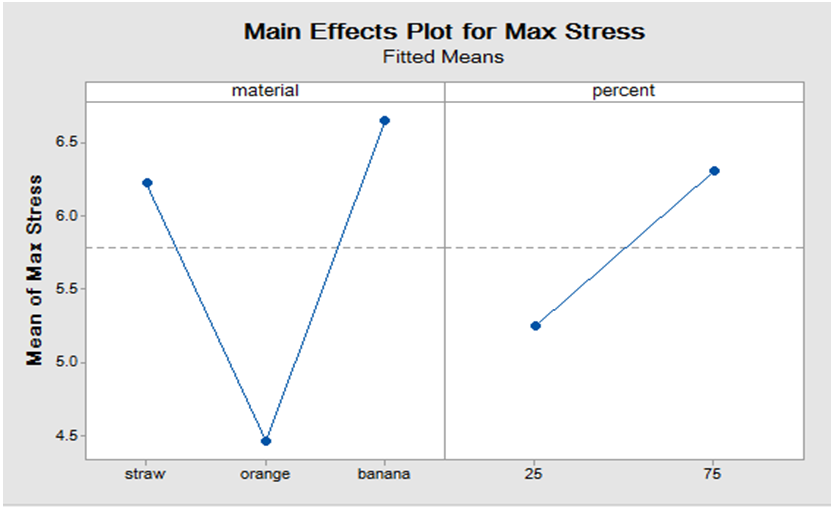 | Figure 6. Main effect plot for max-stress |
As shown in Figure 7, there is no significant difference of 25% and 75% percent on MOR values. In case of material, wheat bran has the largest MOR value.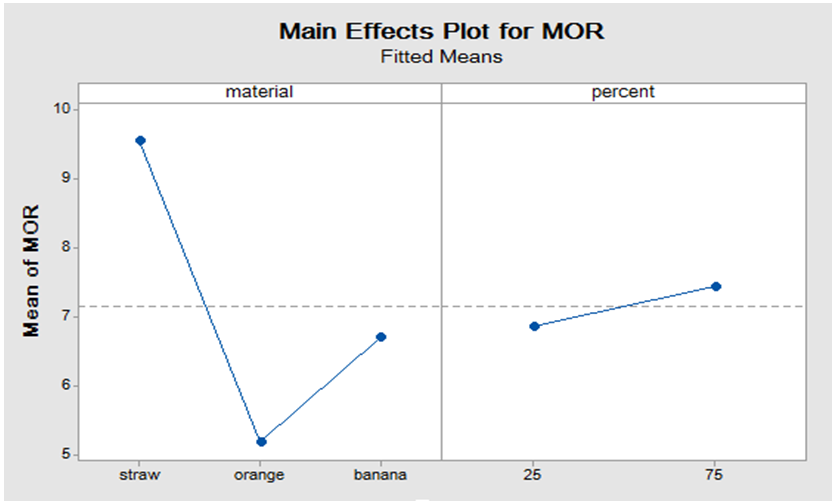 | Figure 7. Main effect plot for MOR |
As shown in Figure 8. the values of max stress for three materials increase with increasing percent from 25% to 75%, the values of max stress weren’t affected significantly by increasing percent, the values of max stress for banana and wheat bran were closed, this leads to interact lines.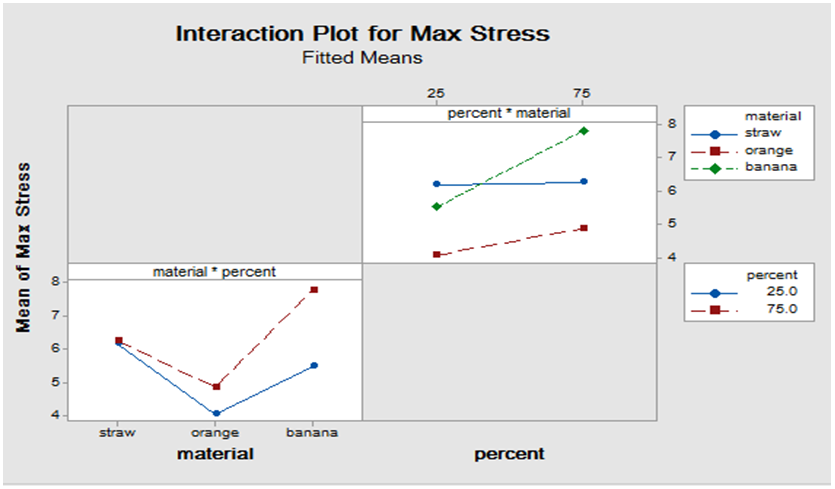 | Figure 8. Interaction plot for max stress |
As shown in Figure 9, the MOE values increases with increasing percent from 25% to 75% except particleboard from orange peels there is slight decrease in MOE value. In percent 75% the larger MOE value was straw then banana, then orange, but at 25% the MOE value for orange larger than banana.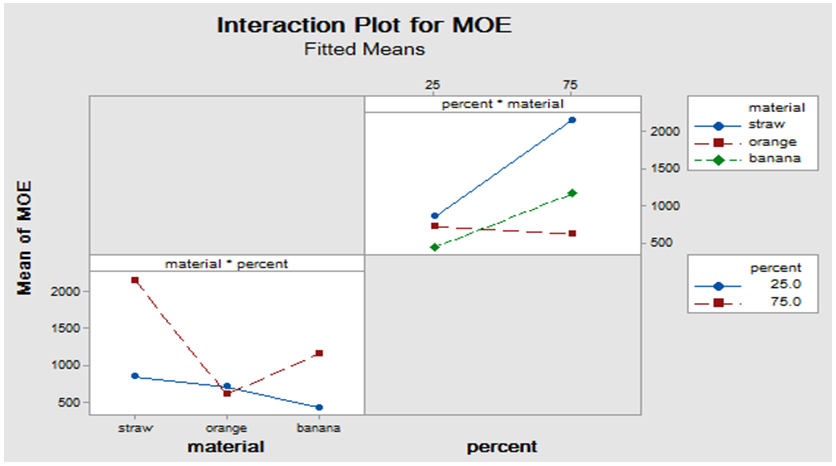 | Figure 9. Interaction plot for MOE |
As shown in Figure 10, the MOR values increases with increasing percent from 25% to 75% except particleboard from orange peels there is slight decrease in MOR value. In percent, 75% the larger MOR value was straw then banana, then orange.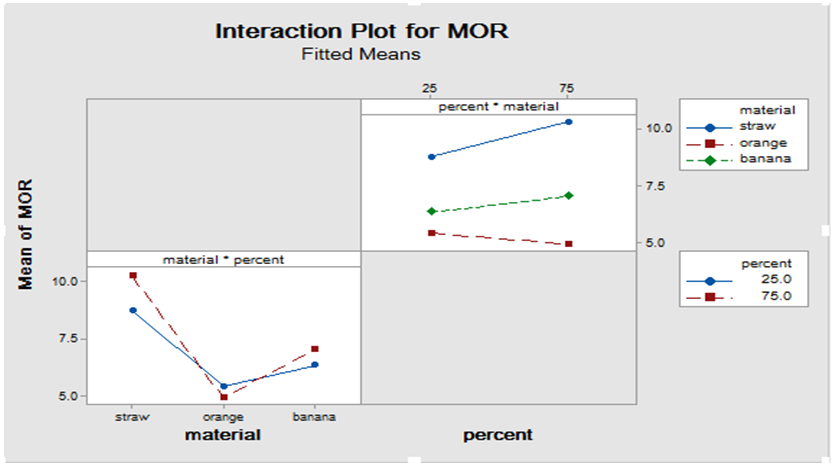 | Figure 10. Interaction plot for MOR |
4. Conclusions
Manufactured particleboard’s properties were better than other types of wood. In tensile test, SD 100% has the highest max stress value and orange 25% has the lowest max stress value.In bending test Wheat bran 75% and SD 100% have the highest MOE, MOR values, while Orange 75% the lowest. In water absorption test at 25C Banana 75% the lowest while Orange 75% the highest, and at 50C Orange 75% the lowest and Banana 25% was the highest. In thickness swelling test at 25C Banana 75% the lowest and Orange 75% the highest, at 50C, Banana 25% has the lowest thickness swelling value and Orange 75% the highest.The Minitab results shows that the main effect of the two factor do not have significant effect on particleboard properties; increasing material percent does not mean improving properties. The interaction between material type and percent have significant effect on particleboard properties. More factors should be considered to improve the properties of particleboard. The suggested uses of this particleboard, it can be used as a substitute product of existing types of wood in local market, in addition it has competitive advantage that can be used in wet places (indoor design, kitchens) and outdoor uses.
References
[1] | D. Wang, X.S. Sun, Low density particleboard from wheat straw and corn pith, Ind. Crops Prod. 15 (2002) 43–50. |
[2] | G. Nemli, H. Kirci, B. Sedar, N. Ay, Suitability of kiwi (Actinidia sinensis Planch.) prunings for particleboard manufacturing, Ind. Crops Prod. 17 (2003) 39–46. |
[3] | Ramadan Abdel-Sayed Nasser, Physical and mechanical properties of three layer particleboard manufactured from the tree pruning of seven wood species, World Appl. Sci. J. 19 (5) (2012) 741–753. |
[4] | Iwona Frackowiak, Karolina mytKo, Ryszarda BeNdowsKa, Content of formaldehyde in lignocellulosic raw materials for particleboard production, Drewno. Pr. Nauk. Donies. Komunik. 55(188) (2012). |
[5] | American Society of Testing and Materials, 1999. Standard Test Method for Evaluating Properties of Wood-Base Fiber and Particle Panel Materials. Designation: D1037- 99.West Conshohocken, PA, pp. 142–171. |
[6] | Wang, Jinguo, and Yingcheng Hu. "Novel Particleboard Composites Made from Coir Fiber and Waste Banana Stem Fiber." Waste and Biomass Valorization 7.6 (2016): 1447-1458. |
[7] | Victor, Aigbodion S., et al. "Development of high-density polyethylene/orange peels particulate bio-composite." Gazi University Journal of Science 26.1 (2013): 107-117. |
[8] | Fakhrul, Takian, Rubayyat Mahbub, and M. A. Islam. "Properties of wood sawdust and wheat flour reinforced polypropylene composites." Journal of Modern Science and Technology 1.1 (2013): 135-148. |
[9] | Fakhrul, Takian, Rubayyat Mahbub, and M. A. Islam. "Properties of wood sawdust and wheat flour reinforced polypropylene composites." Journal of Modern Science and Technology 1.1 (2013): 135-148. |
[10] | Rahman, Khandkar Siddikur, et al. "Flat-pressed wood plastic composites from sawdust and recycled polyethylene terephthalate (PET): physical and mechanical properties." SpringerPlus 2.1 (2013): 629. |
[11] | Azumah, Oscar Kofi. Production of particleboard using Sawdust and Plastic Waste. Diss. 2015. |