S. Chatterjee
Department of Information Technology Electronics Niketan, 6, C.G.O. 110003, Complex New Delhi
Correspondence to: S. Chatterjee, Department of Information Technology Electronics Niketan, 6, C.G.O. 110003, Complex New Delhi.
Email: |  |
Copyright © 2012 Scientific & Academic Publishing. All Rights Reserved.
Abstract
Electronics waste is becoming a major global issue. Huge accumulation of e-waste and their recycling through primitive means for extraction of precious metals are real concern in the developing countries due to presence of hazardous materials in e-waste. Recycling of e-waste through appropriate technologies is, however, considered to be a profitable business as the printed circuit boards (PCBs) contain the precious metals (including gold, silver etc.). The present recycling cost in developed country is, however, not viable, and thereby, huge volume of e-waste is being exported to the developing countries like India, China, Brazil etc., where manpower is in-expensive and enforcement of environmental laws is not so stringent. This article has proposed an outsourcing model where equal participation of the organised and unorganised sector is ensured to make the e-waste management business a profitable one. The main motivation of the units in unorganised sector is to extract the precious metals like gold, silver and copper from the printed circuit board (PCB). The unscientific and unhygienic methods, used for extracting the metals, are harmful to the workers and the environment. This practice needs to be discouraged by providing alternative earning mechanism of the unorganised operators for the collected materials. In the proposed approach, unorganised operators will concentrate on collection, disassembly, segregation of e-waste, whereas, organised sector will concentrate on processing the PCBs to extract precious metals. The 95-97% of the e-waste by weight contains metal, glass and plastics, which can easily be dissembled and segregated manually without damaging environment; whereas, the rest 3-5% by weight of e-waste actually consists of PCBs/connectors, need environmentally friendly recycling techniques to manage. The major segregated materials from e-waste include metals, glass and plastic parts can be managed through the conventional recycling practices used in municipality waste management by organized smelters and re-processors. The segregated PCB and connectors will be pulverized by professional agency to make homogenous powder and assessment of assay content of the powder will be done to know the worth of the PCBs. Once the right price is decided, unorganised sector can sell the PCBs to the organised recyclers for further process. This approach will allow the organised recyclers to concentrate only on processing PCBs, which requires technologies, specialized skills and expertise. The said approach will eradicate the unhygienic practice prevailing in unorganised units in developing countries and thereby will stop polluting environment, soil, water, and will also protect the health of the worker. Once the outsourced model is established, the recycling of e-waste business will again be viable. It will also ensure the higher yield of metal recovery from e-waste as well as minimum landfill.
Keywords:
Electronics Waste Management, Sustainable Recycling Technology, Printed Circuit Board Recycling
Cite this paper: S. Chatterjee, Sustainable Electronic Waste Management and Recycling Process, American Journal of Environmental Engineering, Vol. 2 No. 1, 2012, pp. 23-33. doi: 10.5923/j.ajee.20120201.05.
1. Introduction
Electronics waste (E-waste) is the fastest growing waste stream in the industrialized and urbanized world. Few decades back, the amount of waste generated was considered small enough to be diluted in the environment. With massive growth of electronics and hardware sector, the demand of the electronics products has been enhanced manifold. Faster change of features in the electronics devices and availability of the improved products forcing the consumers to dispose the electronics products rapidly. This has caused generation of e-waste alarmingly. The major source of e-waste is the disposal of the hardware and electronic items from Government offices, public and private sectors, academic and research institutes. The household consumers are also contributing significant volume of end-of-life electronics products. Apart from domestic generation in India, the imported e-waste volume is also growing substantially, though, import is prohibited in India.Like other parts of the world, India is also facing serious crisis due to growing generation of e-waste. The main challenge in India is to create awareness of the environmental, social and economic aspects of e-waste among the public, consumers, producers, institutions, policy makers and legislators. The situation is not so grim in the developed countries, as the laws are adequate to take care of the stocking, disposal and land-filling of the end-of life electronics products. Moreover, availability of skilled recyclers and adequate technologies in those countries make the e-waste recycling a profitable business. It is observed in recent years that large volume of e-waste is being exported from western countries to Asian countries like China, India, etc. for disposal. It seems the recycling business in western countries is becoming economically non-viable due to rising cost of manpower and availability of input materials for running the plant in full capacity. The western countries are, therefore, compelled to find out alternative destinations for disposal, where the labour cost is comparatively low and the environmental laws are not enforced so strictly. The imported e-waste materials are thus reaching through illegal routes in India, China for recycling at small-scale units in unorganised sector. These units use primitive, non-scientific, and non-environment-friendly methods. E-waste is hazardous in nature due to presence of toxic substances like Pb, Cr6+, Hg, Cd and flame retardants (polybrominated biphenyls and polybrominated diphenylethers etc.). E-waste disposal mixed with solid municipal waste is posing a greater threat for environmental degradation in the developing countries, where organised recycling technology is not available and unorganised operators are extracting precious metals through crude means for easy money. The extraction of metals in unorganised units is carried out by dipping printed circuit board (PCBs) in the acidic/alkaline solutions and heating/burning of PCB. These processes are harmful to the workers and to the environment, which are the major concern of e-waste management in developing countries. Unorganised units are not registered and their operations are also considered illegal in India as per the existing laws on industry, labour and hazardous substances. Despite, unorganised business is flourishing in India through the network involving collectors, traders and unorganized recyclers. It is felt that just enacting laws and routine vigilance, the growing business of unorganised sector cannot be stopped. It is appropriate to provide alternative source of income to nearly half million people, involved in this profession. The e-waste recycling, however, can be made a profitable business if it is managed professionally. E-waste contains valuable materials including metal, plastics and glass, which are of the 95% of the total e-waste by weight. The populated PCBs/ connectors are of 3-5% of the total e-waste[1,2], contain valuable metals like gold, silver, copper, and other precious metals like palladium, tantalum etc. In developed countries, well established processes are available for processing PCBs to extract the precious metals with highest yields[1, 3, 4-6]. These processes are automated and minimal involvement of manpower is required. In contrast, the e-waste processing technologies in developing countries are not yet matured and the recycling is still being carried out in unorganised units by primitive ways. It is estimated that 95% of the e-waste recycling in India has been carried out in unorganised units[7]. Therefore, a substantial amount of valuable materials are being lost due to unskilled operation. The recycling units is developed countries, on the other hand, are also facing shortage of materials and thereby the operation becomes economical non-viable. An attempt has thus been made to bridge the organised and unorganised sectors in holistic manner to provide a profitable business model. In the proposed approach, unorganised units will carry out activities including collection, dismantling, disassembly and segregating of the e-waste. The segregated materials like metals (iron, aluminium and copper), glass and plastic parts will be sold to the respective smelters, re-processors etc. for recycling through the conventional practices, which are already prevailed for other materials recovered from municipality waste. The segregated item like PCB and connectors which are most valuable due to presence of gold, silver, and copper, palladium, tantalum and traces of other precious metals will be converted into powder by a professional agency. The metal assay content of the powder will be assessed by the recognized laboratory. The unorganised will bear the cost of the process as well as the assay testing. The worth of the powder will then be decided based on the metal assay content. Unorganised sector can sell the PCB powder to the established recyclers at the right market price. This will prevent them from carrying out the hazardous extraction route of precious metals. The unorganised sector will be responsible from the collection of the e-waste till the selling of the PCB powder. The process of PCB powder to recover metals (copper, lead, gold, silver) and precious metals (palladium, tantalum etc.) will be carried out by the organised units in the developed countries, where the maximum yield of recovery will be achieved and loss of value metals to the landfill can be minimized. The e-waste recycling and management will be profitable proposition in near future, once the outsource model is established in the society.
2. Inventory of E-Waste in India
The actual inventory on generation of e-waste and also the imported electronics products are not currently available in India. Several studies have, however, been conducted by various agencies to find out the inventory of e-waste in the country. Most of these studies are based on the model of obsolescence of electronic products, which requires validation with the field data. The statistics of production, exports and sales of each product and their average life were used during the study. The average life of a personal computer (PC) was assumed to be 5 to 7 years, television (TV) to be 15 to 17 years[7]. It was also assumed that 100 percent of electronic units sold in one particular year would become obsolete at the end of the average life. These perceptions of life of e-waste are based on urban conditions; the conditions are far from it considering the rural scenario. The Manufacturers Associations of Information Technology (MAIT), India and Deutsche Gesellschaft für Internationale Zusammenarbeit (GIZ), India had jointly conducted a field study during 2007 to estimate mainly the inventory of three products, namely, television, personal computers and refrigerators. The study concluded that total quantities of generated, recyclable and recycled e-waste were 3, 32, 979 Metric Tonnes (MT, i.e. 1MT=1000Kg). The inventory of Personal Computer (PC), Mobile Phones and Televisions (TV) estimated were 56,324 MT, 1,655 MT, and 2,75,000 MT respectively. The study found that the e-waste processed during 2007 consisted of 12000 Kg of PC and 7000 Kg of TV. The 2.2 million PC had become obsolete in 2007. India had about 20 million PC in 2007, which grew to 75 million by 2010. Around 14 million mobile handsets had been replaced in 2007 as per another study 8. The highlights of the study are given in Table 1. Table 1. Invitatory of E-waste in India |
| Sr.No. | Items | Weight (MT) | 1 | Domestic Generation | 332979 | 2 | Imports | 50000 | 3 | Total | 382979 | 4 | WEEE available for recycling | 144143 | 5 | WEEE actual recycled | 19000 | 6 | Projected quantity of WEEE by 2011 (without including the imports) | 467098 |
|
|
Source: MAIT,GIZ, 2007, 1MT= 1000KgThe Central Pollution Control Board (CPCB), India had carried out a survey during 2005, which estimated 0.1347 million MT of e-waste was generated in the country in the year 2005. The e-waste generation would reach 0.8 million MT by 2012[9]. Apart from the domestic generation, the imported electronics waste has also contributed a significant impact in the total inventory of the material. India is becoming a big market for imported e-waste. A study indicated that PCs imported to Delhi in 2003 was nearly 3,600 MT/year[10]. Another study predicted that the nearly 50,000 to 70,000 MT of e-waste is being imported annually to India[11]. Most developed countries, find it financially profitable to send e-waste for re-use /recycling in developing countries. The cost of recycling of a single computer in the United States is US $ 20 while the same could be recycled in India for only US $ 2, a gross saving of US $ 18 if the computer is exported to India[12].
3. Unorganized Units in India
The government data on the actual volume of business in unorganised and number of employed manpower are not available. It is estimated that more than 2000 unorganised recyclers along with 270 medium and big scrap dealers are involved in the recycling business in India[13-14]. Nearly 20,000 to 25,000 numbers of unskilled workforces are involved in unorganised sector alone in Delhi[13-14]. Due to substantial profit margin in selling extracted waste materials, many small-scale units are engaged in the recycling business. The secondary market of refurbished old electronics products, old components, modules and the metals recycling in unorganised sectors are growing steadily due to substantial demand in rural consumers. One study shows that after spending typical US$ 12.5-19 per piece for a single computer with colour monitor, a trader can earn around US$ 50-60 by selling its disassembled components, modules to different recyclers or re-users and by recovering precious metals and other valuables[13].The work force in unorganised units is often children and women from poor section of the society. The labours are neither paid their due wages as prescribed by government, nor any compensation like medical/transport/ etc. are offered. Labours are also not aware of their rights such as working hours, social security benefits etc. The occupational requirement including hygiene, safety etc. is being ignored. The legal punitive action against these units from Governmental agencies is difficult, as they are not registered. A study has estimated that 95% of e-waste in India is processed by unorganised sectors units[8]. Several awareness programmes are conducted by the Government and non-governmental level to educate the operators in unorganised sector about the ill-effect of extracting metals by primitive methods. In spite of the harmful consequences, the recycling of discarded electronic products is being carried out in unorganised sector. The unorganised business is growing steadily due to demand and the market value of recoverable materials. This value chain mainly motivates the unorganised recyclers to flourish.
4. Market Scenario in Unorganized Sector
The reasons of attraction of the unorganised sector into the recycling business can be understood if one sees the quantities and qualities of the materials recovered from e-waste and their market value. The data collected from one of the organised sector has been indicated in this context[2]. The amount of ferrous and non-ferrous metals, cable and PCBs recovered from 1MT (1000 Kg) of PC is indicated at Table 2. The 1MT of assorted e-waste contains a substantial amount of saleable materials like mild steel, stainless steel, glass, plastic, copper, aluminium etc (Table 3). The volume and cost of the metals recovered from PCBs are indicated at Table 4. In another study, it is estimated that the 1000Kg of populated PCB of computer as e-waste yields 284 gram of gold[1].Table 2. Recovered Materials from 1000 Kg of PC |
| | % by Weight | Weight in Kg | Plastics | 23 | 230 | Metals | 57 | Cables | 5 | 570 | Cables | 50 | Non-Ferrous Metals | 29 | Non-Ferrous Metals | 290 | Ferrous Metals | 20 | Ferrous Metals | 200 | PCBs | 4 | PCBs | 40 |
|
|
NB: After recycling process of all items 99% was recovered and only 1% was sent for secured landfill.Table 3. Saleable Material recovered from 1000 Kg assorted. E-waste (containing PC, TV, Mobile Phone etc.) |
| Sl.No. | Material | % Composition (by weight) | 1. | Mild Steel | 23 | 2. | Stainless Steel | 8 | 3. | Glass | 27 | 4. | Plastics | 27 | 5. | Copper | 3 | 6. | Aluminium | 3 | 7. | Other Materials | 8 | 8. | Hazardous Materials | 1 |
|
|
NB: E-Waste also contains precious metals like gold, silver, palladium, platinum etc.Table 4. Market value of the Metal recovered from 1000Kg of PCBs |
| Recovered Metal | Weight | Approximate cost (in US$) | Gold | 279.93gms | 6115 (@685.00 per 31gms) | Precious metals (Pt, Pd, In) | 93.31 gms | 3852 (@ 1284.00 per 31gms) | Copper | 190.512Kg | 1470 (@ 3.50 per 453.59gms) | Aluminium | 145.152 Kg | 448 .00 (@ 1.28 per 453.59gms) | Lead and Tin (Pb/Sn) | 30.844Kg | 144.16 (@2.12 per 453.59gms) | Silver | 450 gms | 213.15 (@ 14.70 per 31gms) |
|
|
NB: Data generated on average recovery of one ton of populated PCBs and value is taken from the prevailing rate at that point of time. These are only to give a perception of value from the metal recovery from e-waste.
5. Major Operations in Unorganized Sector
The unorganised sector units include kawaries (rag-pickers), scrap dealers, whole sellers, recyclers etc. The e-waste management in unorganised sector has following major operations:
5.1. Collection
The kawaries, small scrap dealers collect the e-waste from consumer with suitable compensatory price. The consumers are also encouraged in putting the e-waste in recycling chain instead of storing the e-waste or throwing away in municipality garbage. The kawaries are one of the most efficient collectors of e-waste and also reduce the load of municipalities’ responsible for waste collection. The collected waste materials are thus channelized effectively for future endeavour. E-waste is collected in bulk quantity by large scrap dealers from government offices, public sector agencies, school, universities and other corporate houses etc. The importers of scrap also collect discarded electronics products in bulk quantity from various developed countries.
5.2. Segregation
The collected e-waste from diversified sources is segregated in various categories such as components, modules, metals, glass and plastics depending on the saleability for highest economic returns.
5.3. Disassembly
The disassembly methods would be of two types, non–destructive and destructive. Non–destructive recovers the certain disassembled parts for reuse while the destructive disassembly separates each material type for recycling processes. Non–destructive method is not feasible as designs of the products are changing very fast, new functionalities are being added. The composition of various electronic components has also gone a significant change in last few decades, which makes majority of de-soldered components obsolete for re-use. The disassembly can be realised in the following ways. The dissembled items are broadly classified into following categories:For an example, disassembly of Cathode Ray Tube (CRT) recovered from television and computer monitors recovers following items: Similarly, disassembly of personal computer (PC) recovers following items:The typical contents of Television, Personal Computer (PC) and Refrigerator[9] are shown in Fig 1.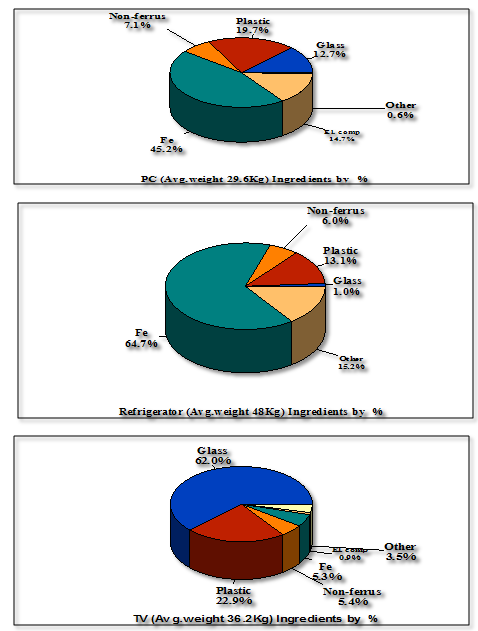 | Figure 1. Contents of materials recovered from PC, Refrigerators and TV |
5.4. Reuse of Recovered Materials
The Kawaries and the scrape dealers sell all the dismantled and segregated parts of metal, glass and plastics to metal and glass smelters and plastic re-processor who specialize in converting these scrap of coppers, aluminium, iron, glass and plastics. The unorganised units lack in expertise and knowledge of the processes of smelting or reprocessing and, therefore, prefer to sell such scrap. The unorganised operators play an important role in managing and recovering of a large quantum of e-waste (~ 95% by weight) in reuse chain without harming environment.
5.5. Recycling of Printed Circuit Boards (PCBs)
The populated PCBs, constituting 3 to 5% by weight of total e-waste, have rich value of metals such as copper, silver, gold, palladium, platinum, tantalum and other metals in traces level. The recovery of all the metals requires professional skill, expensive equipments and machineries. The lack of knowledge, affordable logistics and greed for quick money motivates unorganised sector to employ unhygienic and un-scientific methods for recovery of valuable metals such as Cu, Ag, and Au etc. The typical methods employed by unorganised units are focussed to recover gold from the integrated circuits (ICs), gold plated terminals of connectors/PCBs and other components etc. The gold rich components are removed by loosening of the lead solder by surface heating, which causes air pollution. The stripped PCBs are then subjected to open burning to recover copper. The boards are heated to extract the thin layer of copper foils in the PCBs. In the acid bath process, the circuit boards are dipped in acid for few hours for de-soldering. Then the used chemical solutions are drained to the ground causing soil pollution. The lead sludge that collects in the bottom during the process is recovered and sold. After a water bath the de-soldered PCBs are boiled with a caustic soda solution and manual scrubbing is done to remove the paint. The PCBs are again dipped in an acid solution for few hours, which results in copper sulphate formation. Iron wires are added to the solution and the sludge contained copper settles in the bottom. The acid solution is drained out to recover the sludge, which is dried, grounded to power and sold in the market. This is one of the most hazardous processes in e-waste recycling. It creates occupational as well as environmental hazards.
6. E-waste Management in Organized Sector
6.1. Disassembly and Segregation
The units in organised sector use both manual or semi-automated or automated techniques to disassemble and segregate the e-waste materials. The methods are environmental friendly and take care of the safety of the health of the operators. Disassembly involves the removal of hazardous components such as batteries and other high and low grade including component, part, group of parts or a sub-assembly from a product (partial disassembly) or the separation of a product into all of its component parts (complete disassembly). The recovery of valuable materials such as printed circuit boards, cables and engineering plastics is simplified by such approach.
6.2. Recycling of Printed Circuit Boards (PCBs)
The segregated populated PCBs are processed for the recovery of copper, gold, and other precious metals. The PCBs are grounded to powder of desired size through various mechanical processes including physical impaction, shredding/fragmentation and granulation, etc. Shredding breaks down the PCBs into pieces via ripping or tearing which may then be sorted into material streams having dissimilar subsequent processing demands. The mechanical process, granulation is used to make PCBs scrap into fine particles. Precious metal particles are further concentrated by means of various separation techniques. Magnetic separation technique is used to separate magnetic materials (iron, nickel and cobalt) from the PCB powder and the aluminium particles are being separated by eddy current separation technique. The metal rich power is then separated from plastic rich particles by electrostatic separation technique. The processes are elaborately discussed in the reported articles[1,3-6].The metal recovery involves various thermal and chemical treatments depending on their merits and demerits. Thermal treatment avoids the liquid effluent disposal problems associated with wet chemical extraction methods. Thermal incineration combined with pyrometallurgical treatments is in commercial use for metal recovery from PCBs. The hydrometallurgical methods are also used to recover metals from PCBs. Electro-refining is generally used alter thermal processing for the purification of copper with the separation of precious metals. Selective recovery of pure metal products directly from waste streams is key advantage of these methods. The cyanide solution is generally used for gold recovery from the PCBs powder. The metal recovery is discussed in details in the articles[15-17]. An indicative tentative process flow chart for recovery of metals/precious metals from the populated PCBs is shown in Fig.2.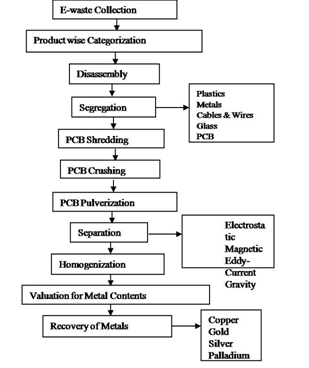 | Figure 2. Process Flow Chart for Recovery of Saleable Materials E-Waste |
7. Present Scenario of E-waste Recycling in Developed Countries
The electronic waste recycling was considered to be profitable business in the western countries till the recent past. Appropriate technologies as well as adequate infrastructures are available in developed countries to process the end-of-life electronic products to extract precious metals to the best possible yields. The consumers support financially to the recycling activity in western countries the form of EPR (Extended Producers Responsibility). Though, over the years, it is observed that the e-waste recycling is becoming non-viable in the developed countries due to following reasons: The profitability of the e-waste recycling business depends on the recovery of the precious metals primarily copper, gold and silver. The business viability also depends on the capability of recovering other precious metals like palladium, tantalum, platinum, etc., which are present in traces in PCBs. While recycling is carried out through automated methods, the precious metals are often lost in the bulk of other less valuable metal dust and plastics particles. The automated disassembly and segregation methods may not be appropriate to recover all these precious metals from the waste stream of PCB powder. The prior knowledge of the electronic components and their composition will guide recyclers to identify the origin of precious metals in PCBs. These identified components will preferably need segregation at early stage and process separately for better recovery yield. Therefore, in order to enhance the yield of recovery of precious metals, the manual disassembly and segregation are inevitable for the recycling process. The high manpower cost in the developed countries, however, does not allow the recyclers to encourage any manual operations. The electronics products are being continuously modified, improvised and miniaturized through technological developments and advancement of materials research. The design of the PCBs is also being modified and sizes are also drastically reduced. The precious metals contain in the PCBs are thereby reducing with these modernization and miniaturisations. The advancement of material research is also replacing conventional usages of gold, silver, copper and other precious metals (tantalum, palladium, platinum etc.) without compromising the functionality. The design change reduces the cost of the products drastically. The percentage usages of gold, platinum etc. have been reduced many occasions in modern devices with less-expensive and improvised metal alloy. The recovery of precious metals from PCBs of modern electronics devices are reducing compare to the historical PCBs. Less recovery of value metals would definitely challenge the viability of the e-waste recycling business. The reduction in profitability of the recycling business forces many recyclers to shift the businesses in the emerging countries like China, India and Brazil.In order to move up in the ladder of the technology value chain, the developed countries prefer to transfer the manufacturing or processing technology to the developing countries. Those technologies are often transferred, which are comparably established and needs no further innovation. In contrast, developed countries could concentrate on the value added technology. The E-waste recycling technology is no longer a high end technology where further innovation is required. The trend has therefore been started to shift the operation in destinations like China, India and Brazil, where operation costs are low.
8. Proposed Model for E-waste Recycling
The major reason for the domination by unorganised units is economics of metal recovery in the e-waste recycling business and abundance of low cost labour. The present situation does not appeal to the unorganised sector to divert waste materials to professional recyclers due to obvious economic reasons. They are compelled to extract precious metals mainly copper and gold through unhygienic practices. Due to their lack of knowledge, the recovery yield of the precious metals is very poor and, thereby, substantial percentage of the metals like cooper, gold, silver, and other precious metals (palladium, tantalum, platinum, etc.) are lost. The author feels that if suitable prices for the precious metal present in PCBs/connectors are offered to unorganised units, primitive extraction of metals can be discouraged. A study by government agency had predicted that electronic waste, comprising of personal computers, mobile phones, and televisions would reach 8,00,000 MT by 2012[9]. The unorganised operators can efficiently manage a large quantum of e-waste (~>95% by weight) without polluting the environment. Therefore, out of the estimated e-waste inventory, the 95% of the mass (7,60,000 MT) could have been easily managed by the unorganised sector without polluting the environment. The rest 5% of the weight (40,000 MT) of e-waste consists actually of PCBs and connectors, which need environmentally friendly recycling treatment to manage. In the proposed approach, unorganised units will concentrate on collection, disassembly, and segregations. The segregation of metals, glass and plastics from e-waste by non-destructive methods and channelizing them for further processing by professional smelters can be safely carried out by unorganised sectors as these will not harm the environment. The metal extraction from PCBs and connectors requires innovative approach for environment friendly disposal approach. In this article, a novel methodology involving unorganised sectors has been devised so that ill effects on the environment can be eliminated. The proposed approach will have following steps.
8.1. Step: 1 - Collection, Disassembly and Segregation
E-wastes will be collected by unorganised e-waste collectors (Kawaries) from various consumers from home, offices, industry and corporate houses, private and public organizations etc. The e-waste collectors (Kawaries) can form a co-operative domain. The collected e-waste will be segregated in to various categories, dissembled and segregated to separate populated PCBs and connectors. Variety of electronic, electrical (WEEE) products will be segregated from e-waste depending on their market demand. The concentrated e-waste will be created by manual removing of items such as glass components, metal fittings, screws, connectors etc., cables, heat sinks, plastic enclosures, fans, transformers, batteries etc. The kawaries can sell the recovered items with suitable market price.The PCBs and connectors are most valuable parts as it contains gold, silver copper and other precious metals. The treatment of the PCBs in primitive means by unorganised recyclers could be discouraged if one could ensure them to provide remunerative returns for collection and segregation of quality materials including gold rich PCBs. The populated PCB containing connectors, chips etc. will be separated for further process to recover precious metals such as copper, silver, gold, palladium, tantalum etc.
8.2. Step: 2 - Shredding, Crushing and Pulverization
The pulverisation of populated PCBs and connectors and other gold rich components will be carried out to make homogeneous mixture of populated PCBs, obtained from various electronic products. The pulverised powders will primarily be assessed to know the exact quantity of saleable metals present in wide variety of populated PCBs. Once metal assay is completed, the pulverized powder will be subjected to appropriate metal extraction technology to separate different types of metal contents, also to liberate metals from plastic part of individual components and laminate of PCBs. The particle size of pulverized PCBs needs to be further processed by suitable method to improve the homogenized powder of PCBs. The pulverization will also help to maximize separation of metal particles from plastic to which it is normally adhered. The PCBs populated with whole range of passive, active, electro mechanical and inductive components in both leaded and surface mount configuration will be shredded in a mechanical shearing machine down to a size of about 3mm x 3mm. Finally, these shredded pieces will be subjected to dry grinding in a ball mill to a top size of 1.0 mm. The shredded materials will then be pulverized less than 1.0 mm size for liberation of metal and plastic by physical beneficiation techniques[1,3]. Fine shredding will be helpful to liberate metals from the cladding materials or composite laminates such as resin, fibreglass and plastics.In the proposed approach, the industrial acceptable standards of pulverization will be used to ensure the standardization of the powder with respect to their particle size distribution, homogenization, sampling procedure and sample collection. These industrial acceptable PCB powder would be analysed for metal assay content from international recognised laboratory.
8.3. Step: 3 - Valuation Methods for PCBs: Assay Metal Contents
The metal rich powders are subjected to essay content by professional agencies having adequate instrumental facilities. It is essential as different metals in PCBs are very unevenly distributed. The standardised method of sampling and assay analysis of metal content in PCBs and subsequent certification from professional (private/public) agencies will be done to motivate unorganised recyclers to know the presence various metals in transparent manner. The exact quantitative data on the metal composition of PCBs in pulverized form can be obtained by using atomic absorption spectroscopy (AAS) or inductively coupled plasma/atomic emission spectroscopy (ICP/AES). This process includes acid or caustic leaching of the powdered material with, HCL, HF, in appropriate proportion and sequence. All of the metals can be extracted and determined by AAS or ICP/AES, using atomization by either flame or hydride system or graphite furnace. Although AAS can analyze a number of elements in the range of ppm or ppb concentration, it is more time and cost intensive. The standard sampling from homogenized pulverized powder is important for valuation method. The proper worth of the PCBs, segregated by unorganised sector will be decided from the assay analysis report, and the market value of the metal. The price of such powders can be ascertained in a transparent manner and suitable money can be paid to the collector. The confidence of e-waste collector can be earned in a progressive manner, thereby, encourage them to sell the collected populated PCBs to agencies for processing them in environment friendly manner.
8.4. Step: 4 - Metals Extraction
The pulverized PCB powder will then be sold to the professional authorised smelters who have the adequate knowledge and facilities to extract metals like lead, copper, gold, silver, palladium, platinum etc. The powder can be segregated into various groups containing rich copper rich, iron rich, aluminium rich, lead rich and other mixed metal rich. The magnetic separation can be used for separating iron, nickel and cobalt metal and aluminium will be separated by eddy current separation. The electrostatic separation will be used for separating plastic and metals and various embedded plastic and metal clusters are separated by gravity separation methods. The extraction of the precious metal will be carried out by the well-established techniques, which are discussed in details at various articles[1, 3-6, 15-17]. Alternatively, pulverized PCB powder can be pyrolysed with suitable technology to recover the precious metals. Through gasification or pyrolysis, over 50% of PCB powder will be decomposed and its total heat value nearly 20000MJ/Kg can be used as energy for metal recovery[18].
9. Methodology for the Proposed Approach
In the proposed recycling process, unorganized sector will collect the e-waste from various stakeholders by paying suitable prices (~5US$/ Kg). The collected e-waste will be categorized and usable modules and components will be disassembled and segregated depending their usability and market demand. The disassembly, segregation of remaining e-waste will be carried out to recover the larger parts of metals, plastics and glasses manually, which will incur further labour cost (~1US$/ Kg). The usable modules (modules, batteries etc.), metals (copper, iron, steel etc.), plastics (casing, bobbins, etc.), glasses will be sold to the respective smelters and re-processors for further use of these materials depending of the market value Table 5). Unorganized operators will recover some cost (~ 1US$/ Kg on average) by selling these usable materials. The selling prices will include a margin of US$ 0.1-0.15 per kg for miscellaneous cost of labour, godown charges, transport etc. An indicative price of scrape metals, plastics and other recovered items based on prevailing rate in Indian market[19] are shown in Table 5. Table 5. Economics of Recycled Materials |
| Old recovered Items | Price range (in US$) | Metals | | Mixed Aluminium | 0.73-0.98/Kg | Yellow Brass | 2.36-3.93/Kg | Scrap copper | 5.89-6.3/Kg | Mixed Lead | 0.88-1.46/Kg | Scrap nickel | 15.42-20.57/Kg | Scrap steel | 0.31-0.39/Kg | Scrap stainless steel | 2-2.68/Kg | Mixed scrap zinc | 0.67-1.32/Kg | Plastics (Resin type) | | ABS | 0.73-0.8/Kg | HIPS | 0.44-0.55/Kg | Hard plastics | 0.11-0.38/Kg | Mixed plastics | 0.33-0.49/Kg | Norell | 0.33-0.49/Kg | PVT | 0.24-0.44/Kg | Others | | Scrap Computers | 73.25-146.49/Kg | Circuit Boards | 1.15-2.28/Kg | Scrap capacitor | 21.47-42.92/Kg | Scrap electronic battery | 20.93-62.78/Kg |
|
|
NB: Prices are indicative to give a perception of recovered worthThe unorganized sectors will use professional mining firms to covert the remaining e-waste items such as connectors, switches and PCBs in to a homogenous powder. The process will involve the shredding, crushing, pulverizing and homogenization. The professional firms will charge appropriate prices (approximately ~0.2 US$/ Kg) to the unorganized sectors for converting the PCBs to homogenous powder. The unorganized sectors will take help of the authorized laboratory to test the assay content of the homogenous powder and obtain the appropriate certificate by the by paying nominal charges (approximately ~0.01 US$/ Kg).The PCB powder will then be ready to sell to the organized recyclers based on their appropriate market prices. The price will depend upon the presence of the precious metals (assay content) in the PCB powder. The unorganized sector may earn approximately 20 US$/ Kg from organized sector. The indicative cost incurred and earning potential based on the market demand and metal prices can be shown in Table 6. The prices estimated in the forgoing discussion are indicative and based on the market prices of various materials in India. The indication of the price structure is only to give a perception of the value recovered from various stages of the recycling process. The actual money flow and profitability of both unorganized and organized sector can only be obtained by actual market survey. The detailed process flow chart of the recommended recovery of metals/precious metals from the populated PCBs, responsible stakeholders and the money flow is described[20] in Fig.3.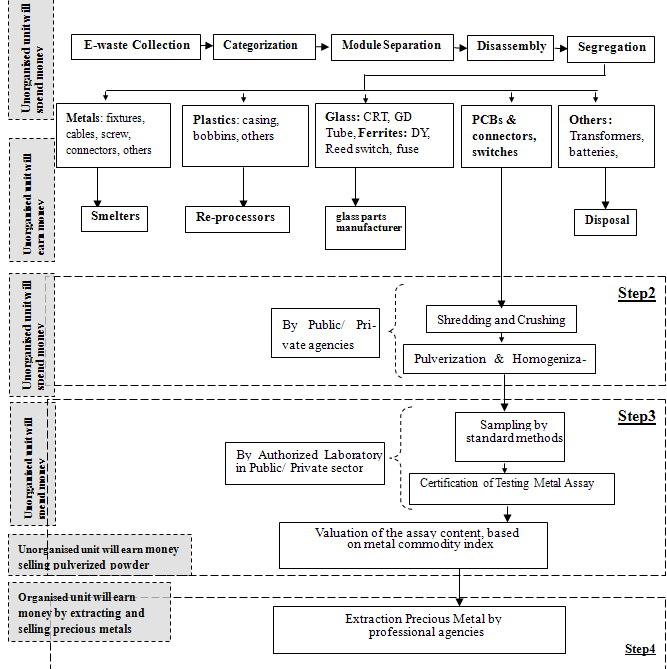 | Figure 3. Process Flow Chart for E-waste Management |
Table 6. Indicative Cost and Earning potential of Unorganised Units |
| Various steps | Cost incurred | Cost recovered | E-waste collection | ~5US$/ Kg | - | Labour cost for disassembly, segregation of e-waste | ~1US$/ Kg | - | Selling of usable modules (modules, batteries etc.), metals (copper, iron, steel etc.), plastics (casing, bobbins, etc.), glasses | - | ~1US$/ Kg | Shredding, crushing, pulverizing and homogenizing of PCBs, connectors and switches from professional mining firms to covert homogenous powder | ~0.2 US$/ Kg | - | Testing and certification of assay content of the homogenous powder from the authorized laboratory | ~0.01 US$/ Kg | - | Selling of homogenous pulverized powder to organized sector | | ~20US$/ Kg | Sub-Total | 6.21 US$/ Kg | 21US$/ Kg | Total profit potential | 14.79 US$/ Kg |
|
|
10. Conclusions
The e-waste recycling is becoming non-viable business in western countries due to high cost of labour, transportation, electric power etc. With reducing percentage of precious metal content in the improved electronics design, the modern devices are becoming less expensive. The precious metal recovery in electronic waste is thus reducing. The viability of the recycling business is becoming a real concern. The volume of e-waste is, however, enhancing alarmingly in the world. Due to presence of the toxic elements, it is all the more dangerous for the society to stock them without carrying out appropriate disposal. It is also observed that the growth of consumption of the electronics products and subsequent disposal are increasing in the developing countries, whereas, the consumption rate in the developed countries are getting saturated. The volume of the e-waste is thus increasing alarmingly in the developing countries due to local consumption as well as imported disposable electronics hardware products. It is, therefore, appropriate to devise a holistic approach to manage and recycle the e-waste in self-sustained manner to save the environment and the human health. The developed countries have technology and infrastructure, whereas, the cost of labour, transportation, processing etc. is less expensive in the developing countries. It is, therefore, proposed in this article to manage the e-waste involving unorganized sectors at developing countries and organized sectors in the developed countries. In the proposed approach, unorganized units will be involved in collection, disassembly and segregation of e-waste and will earn compensative incentive for their efforts. The unorganized sector will also be responsible for preparing the homogenous powder of the PCB, assessing their precious metal content as well as obtaining certificate for attracting organized sector to buy their powder in the best market price. It will encourage e-waste collector to earn maximum without indulging in extracting gold, silver etc. through burning and chemically exposing processes. The harmful impact on environment and to human being will be reduced. This is an outsourced model of e-waste recycling, where organised sector will only concentrate on the core activity of PCB recycling. The cost of the initial phases of the process can be saved and the profitability will improve. Enough PCBs materials will be available for the established recyclers at developed countries. It would thus address the shortage of materials for the organised units. The zero/minimum waste disposal to landfills will be achieved through this model. The proposed approach would bring mutual trust between unorganised and authorised metal extractors.Since the unorganised recyclers are dealing major amount of e-waste in India, the said approach will impact on the majority of the e-waste management value chain. Moreover, nearly 95% of e-waste by weight will be segregated and then managed by the conventional municipality waste recycling techniques. The said approach is, therefore, will be impacted major recycling management mechanism. Since the primitive methods are avoided, the recovery percentage of the precious metals will also be improved to a significant level. The metals (palladium, platinum, tantalum etc.) those are present in the trace level will also be recovered. At present these metals are lost due to lack skill level. The employment of the manpower involved in the unorganised sector will also remain. The present inventory of e-waste in India is nearly 8,00,000 MT. The major portion (95%) of the e-waste i.e. 7,60,000 MT can easily be managed by the unorganised units using aforesaid model without polluting the environment. The estimated volume of the e-waste generation and its associated concerns in managing such a volume in the society will be drastically reduced. The remaining 5% of the weight (i.e. 40,000 MT) of e-waste consisted of PCBs/connectors needs environmentally friendly recycling techniques to manage, which will be very small volume and can be amicably addressed. In another table (Table-7) it is indicated that the approximate intrinsic value of metals recovered typically from medium graded PCBs scrap and non-metal[3]. It may also be noted from the table, that 33% of typical medium graded PCBs has saleable metal contents whereas 67% consist of combusable material like epoxy resins and fabric etc. Table 7. Approximate intrinsic value of typical medium graded PCBs waste |
| Component | Wt. (by %) | Value (by Kg) | Intrinsic Value | | | | (pound per Kg) | % | Gold | 0.025 | 6500.0 | 1.625 | 57.48 | Palladium | 0.010 | 8000.0 | 0.8 | 28.30 | Silver | 0.100 | 70.0 | 0.07 | 2.48 | Copper | 16.00 | 0.8 | 0.128 | 4.53 | Tin | 3.000 | 3.0 | 0.09 | 3.18 | Lead | 2.000 | 0.3 | 0.006 | 0.21 | Nickel | 1.000 | 5.0 | 0.05 | 1.77 | Aluminium | 5.000 | 0.9 | 0.045 | 1.59 | Iron | 5.000 | 0.1 | 0.005 | 0.18 | Zinc | 1.000 | 0.8 | 0.008 | 0.28 | Total | 33.135 | - | 2.827 | 100.00 | Note: Metal values are based on June 2002 London Metal Exchange Levels. |
|
|
(Source: Xuefeng Wen et.al. China University of mining Technology, Xuzhou University)Table 8. Approximate Precious Metal in E-waste requires Authorized Recycling Process |
| Items | Weight | Wt. (by %) | E-waste | 8,00,000 MT | 100% | PCBs | 40,000 MT | 5 % | Precious Metal content in PCB (33% of the weight) | 13,200 MT | 1.65% |
|
|
The Table 8 further indicates that the 5% of the PCB in e-waste needs to be processed by the organised sector and 1.65% of the metal content (i.e. 13, 200 MT in Indian perspective) of the initial total volume of the e-waste (8,00,000 MT) needs actually an environmental friendly, skilled recycling process. This volume is sizable enough to be tackled by the society by authorized metal extractors at the developed countries in viable business proposition. Once the proposed model will be implemented effectively and unorganised units will develop the trust level of selling their PCBs to the organised units for recovering their initial expenses and better profit margin, the market driven force will be established. The organised metal recyclers can start up their plant in the developing countries like India, China for further reducing the operation cost once the outsourced recycling model will be fully matured.
ACKNOWLEDGEMENTS
The author gratefully acknowledge to Mr. P. Parthasarathy, Managing Director, E-Parisaraa Pvt. Ltd. Bangalore, India for his valuable suggestions on the subject and also thankful for sharing inputs and important data for the electronic waste recycling operations. The author is also grateful to Dr. Krishna Kumar, Ex-Senior Director, Department of Information Technology, New Delhi for valuable inputs on the subject.
References
[1] | Z. Gao, J. Li, H.C. Zhang, Electronics and the Environment, 2002 IEEE International Symposium , p234-241, Jianzhi Li, Puneet Shrivastava, Zong Gao, and Hong-Chao Zhang, IEEE Transactions on Electronics Packaging Manufacturing, Vol. 27, No. 1, January 2004, p33-42 |
[2] | http://www.ewasteindia.in/environment.asp: Industrial operation data shared by E-Parisaraa Pvt. Ltd, Bangalore, India |
[3] | Study on metals recovery from discarded printed circuit boards by physical methods, Xuefeng Wen Yuemin Zhao Chenlong Duan Xiaohua Zhou Hongguang Jiao Shulei Song, Electronics and the Environment, 2005, Proceedings of the 2005 IEEE International Symposium, May 2005, P121- 128 |
[4] | A physical process for recycling and reusing waste printed circuit boards, Mou Peng Wa Layiding Xiang Dong Gao Jiangang Duan Guanghong, Dept. of Precision Instrum. & Mechanology, Tsinghua Univ., Beijing, China, IEEE International Symposium on electronics and the environment, 10-13 May 2004, p 237- 242 |
[5] | Selective Liquid-Liquid Extraction of precious metals from semiconductor wastes, Dr. Hanapi Bin Mat, Tang Boon Seng, Department of Chemical Engineering Faculty of Chemical and Natural Resources Engineering, University of Teknologi Malaysia, 2006 |
[6] | The Practice and Challenges of Electronic Waste Recycling in Korea with Emphasis on Extended Producer Responsibility (EPR), Hyunmyung Yoon; Yong-Chul Jang, IEEE International Symposium on electronics and the environment, 8-11 May 2006, P326 – 330. |
[7] | http://www.e-wasteproject.org/docs/del_amitjain.pdf |
[8] | Report on “E-waste Inventorisation in India”, MAIT-GTZ Study, 2007 |
[9] | http://www.cpcb.nic.in/docs/E-Waste Guidelines-2007/Front page1.pdf. |
[10] | A report on “Managing Electronics Waste: Dumping old TV? First read the rule”, The Hindustan Times, New Delhi Edition, p1, 15, October 2007 |
[11] | http://www.industelegraph.com/story/2005/9/2/33438/17285 |
[12] | Report on “Study on Status and Potential for E-waste Management in India”, by ELCINA, India sponsored by Department of Scientific ad Industrial Research (DSIR),India February 2009 |
[13] | http://toxicslink.org/dn.php?section=1&id=37&atn=0 |
[14] | http://www.toxicslink.org/dn.php?section=1&id=171&atn=0 |
[15] | Selective Liquid-liquid extraction of precious metals from semiconductor wastes, Dr. Hanapi Bin Mat, Tang Boon Seng, Department of Chemical Engineering Faculty of Chemical and Natural Resources Engineering University Teknologi, Malaysia, 2006, http://eprints.utm.my/2743/1/72157.pdf |
[16] | Meta-analysis of Hazard Criteria Designation for Electronic Waste, John D. Lincoln, Oladele A. Ogunseitan, and Andrew A. Shapiro, Proceedings of the 2006 IEEE International Symposium on Electronics and the Environment, 2006 |
[17] | Recovery of high purity precious metals from printed circuit boards, Journal of hazardous materials 164(2-3):1152-8, 2009 May 30 |
[18] | Study on the Gasification and Melting Characteristics of Electronic Waste, Wenlong Wang, Jing Sun, Chunyuan Ma, Yong, Dong, Zhiqiang Wang, Xiren Xu, Zhanlong Song, IEEE Computer Society, Proceeding of “2009 International Conference on Energy and Environment Technology”, p574-577 |
[19] | http://scrapmetalpricesandauctions.com/2008/05/india-current-scrap-metal-and-recycling-prices-may-26-2008/ |
[20] | Effective Electronic Waste Management and Recycling Process involving Formal and Non-formal Sectors, Dr. S. Chatterjee and Dr. Krishna Kumar, International Journal of Physical Sciences Vol. 4 (13), pp. 893–905, December 2009, ISSN 1992-1950 © 2009 Academic Journals |