Raúl Montiel1, Rosalba Patiño-Herrera2, J. A. Gonzalez-Calderón3, Elías Pérez4
1Área de Polímeros, Depto. de Física, DCBI, Universidad Autónoma Metropolitana-Iztapalapa, Vicentina, México
2Departamento de Ingeniería Química, Instituto Tecnológico de Celaya, Guanajuato, Mexico
3Departamento de Ingeniería Ambiental, Instituto Tecnológico de Celaya, Guanajuato, Mexico
4Instituto de Física, UASLP, San Luis Potosí, México
Correspondence to: Raúl Montiel, Área de Polímeros, Depto. de Física, DCBI, Universidad Autónoma Metropolitana-Iztapalapa, Vicentina, México.
Email: |  |
Copyright © 2016 Scientific & Academic Publishing. All Rights Reserved.
This work is licensed under the Creative Commons Attribution International License (CC BY).
http://creativecommons.org/licenses/by/4.0/

Abstract
The present work presents the design and construction of a device that allows for the continuous processing of a scaffold based on three interconnected steps: 1) melting for extrusion; 2) electrospinning for achieving nanoscale fibers and finally 3) exposure to UV radiation for reaching proper fiber crosslinking. All necessary for fabricating crosslinked networks or meshes with important applications in biomedicine.The suggested design, based on twin screw extrusion, meets the conventional methods of plastic extrusion at different temperatures and different loading and feeding speeds. This novel design includes a secondary feed port to incorporate other plastics, additives, or plasticizers. Therefore, it can be used like a co-extruder. In addition, by applying high voltage to the isolated output capillary, the device can act as an electro-spinning machine. This allows for obtaining a graduated ´layer by layer´ scaffolding generation, including phase separation during the melting process, which permits the production of scaffolds of a wide range of compositions, porosity and mechanical properties.
Keywords:
Design, Twin screw extrusion, Electrospinning
Cite this paper: Raúl Montiel, Rosalba Patiño-Herrera, J. A. Gonzalez-Calderón, Elías Pérez, Novel Twin Screw Co-Extrusion-Electrospinning Apparatus, American Journal of Biomedical Engineering, Vol. 6 No. 1, 2016, pp. 19-24. doi: 10.5923/j.ajbe.20160601.03.
1. Introduction
Twin extruders, produce a thrust much greater that of a single screw, providing higher accelerations as well as shear stress of greater intensity. Twin screw extruders may be found rotating in the same direction (co-rotating), and in opposite directions (counter-rotating). According to the thrust or flow, the twin screw extruders are counter-rotating when the flight depth of first one does not penetrate into the corresponding flight depths of the second one, see Figure 1(a), and have little dependence on the viscosity of the load, Figure 1(b). In this type of extruder, the materials tend to move the screws towards the barrel wall and therefore cannot generate speeds high enough to be adequately mixed.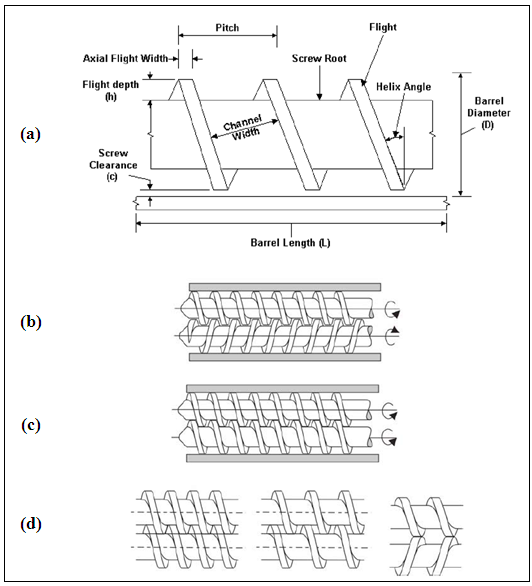 | Figure 1. (a) twin screw parameters, (b) counter-rotating, (c) co-rotating and (d) interpenetration degree |
In turn, extruders with interpenetrated flight depths are able to co-rotate, in this arrangement the flow depend primarily on viscosity, but the screws are not pushed into the barrel walls. Therefore it is possible to generate high speeds, and since the material alternat between the screws, a better and homogeneous mixing can be obtained. The performance of an extruder can be obtainedby applying the laws of conservation of mass and energy according to the equations of motion describing the physical state of a moving fluid subject to pressure. An important factor to be considered is the temperature, so depending on this, the extruder will allow plastic mixtures to melt and incorporate well with the rest of the components. It is important to note that for purposes of use in the next step electrospinning process, you should use small amounts of polymer melt feed to a temperature at which its viscosity is low enough to flow continuously, but this temperature temperature of the molten mixture should not reach the degradation temperature of any of its components. The temperature of the melt depends practically on the extruder temperature profile. According to the experimental data of melt (TM) and softening temperatures (TG) of engineering plastics, these temperatures have a range from 149 to 166 °C, Therefore, these plastics are not affected by the degradation effects (below 200 °C).In this regard, most of the samples are process able because none exceeds the degradation temperature of the materials, and since the temperature profile does not affect any other process or parameters (pressure, output, torque or elasticity). Under these conditions may be considered in first approximation that the molten polymer behaves as a Newtonian fluid. The fill ratio (FR) is a measure of the volume in the screw barrel which is filled with the molten polymer. FR It can also be considered as the flow rate of actual flow velocity driven by rotation of the two extruder screws.
According to Mani et al [1], an acceptable approximation for the flow rate is:
N is screw speed (revolutions per hour), D is diameter of screw (m), θ is flight angle, W is width of screw (m) and H is flight depth (m), see Figure 1 and 6.This design allows the scaffolding graduates generation layer by layer including phase separation in the melt [2, 3]. Another option suggested by Leong, K, 2008 [2], used in bone tissue engineering, is based upon the use of porous polymeric scaffolds seeded with one individuals own stem cells. This approach promotes tissue constructs based upon cells´ proliferation and differentiation on a scaffold within a bioreactor which are then implanted in the injured area.Common polymeric materials used in tissue engineering scaffolds are polyglycolic acid, polylactide, polycaprolactone (PCL) and its copolymers or their bio-particles, such as hydroxyapatite and tricalcium phosphate, as well as other growth factors bio agent and some proteins [4, 5, 6-10]. From bio-resorbable polymers, osteo-conductive and additives extrusion technology twin screws can be applied to manufacture implants and scaffolds for the regeneration and repair of bone tissue. In this twin screw co-extrusion technology (TSE), it includes a head electrospinning device. Normally, for making graded structures, PCL and PGS-PCL biocomposites with high availability and tricalcium phosphate particles (TCP) and PCL is used. This study's results suggest that PGS elastomer is an auspicious osteoconductive material for the regeneration of bony defects. These results can be an innovative reassessment of the current art of selection for novel bone scaffold materials.This twin screw co-extruder has the versatility to make electrospinning and co- electrospinning for developing new production processes more viable to use in scaffold for tissue engineering in the regeneration of both bone and soft tissue. This design will be able to scale the size and distribution of porosity scaffolds varying continuously, by adding bioactive agents and other components. As an example scaffolds with interconnected porosity from polycaprolactone, incorporating different concentrations and particle size distribution of β-hydroxiapatita and tricalcium phosphate can be produced to increase the conductivity; with the possibility of additional bioactive agents for cell proliferation and differentiation [13-15].In addition to controlling the mechanical properties in both directions: radial and axial, potentially allowing the best imitation of the natural complexity of native tissues, might even be suitable for the repair of critical size bone defects and fusion for spinal applications. Despite advances in tissue engineering, none of these methodologies is flexible enough to allow industrially scalable and reproducible classification of bone graft substitutes and scaffolding for a wide range of compositions, porosity and specific mechanical properties.
2. Apparatus Description
The Twin co-extruder consists of a stainless steel cylinder block which at its center has two cylindrical bores next to one another to allow the placement of two screws with chord pitch equal to the length of the screws which rotate in the same direction, to drag and compress a polymer melt, forcing it out for an small extrusion die or capillary nozzle. In Figure 2, an assembly drawing of the main parts is shown. The co-extruder has a secondary feed port for adding others polymers, additives and plasticizers, the co-extruder die can be replaced by a capillary nozzle or needle to fabricate scaffolds by electrospinning. The device has independent variable resistors for controlled heating, according to the temperature profile of engineering plastics fed on the main port or hopper at the opposite of the output die. The twin screw extrusion system is controlled by tree coupled gears and a servo motor whose speed control is mounted on a small console along with other registry systems and temperature control.In Figure 2 and Table 1, the identification numbers (ID), the quantity of these (ITEMS), description and material machining are listed.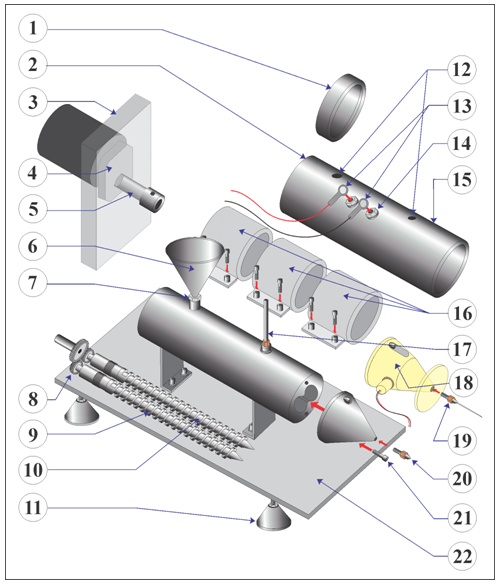 | Figure 2. Identification of main parts of the extruder |
Table 1. Identifying parts 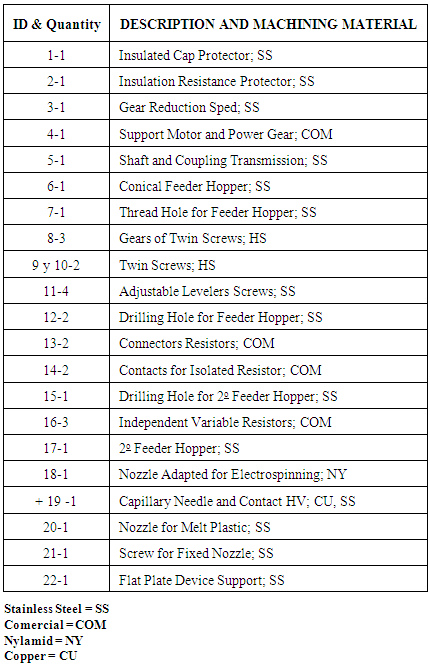 |
| |
|
*In Figure 3 the parts forming the nozzle Electro-spinning are shown, and the details of machining material. + Application of High Voltage (HV: KV 20,000 - 50,000 KV).The co-extruder nozzle has an attachment consisting of a UV lamp installed inside a glass tube, to proyect the ultraviolet radiation (UV) directly into the flow of the polymer solution, in order to induce crosslinking, on electro-spun fibers as they pass through the nose up to the capillary-needle. This UV lamp is installed transversally and below the flow Figure 3.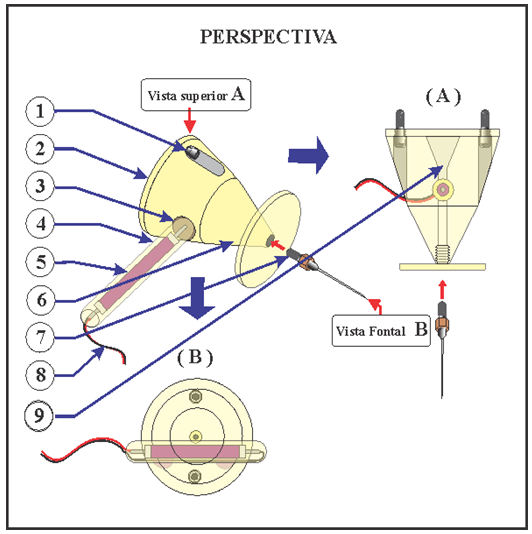 | Figure 3. Drawing of the parts of the nozzle electrospinning |
Table 2. Nozzle Parts 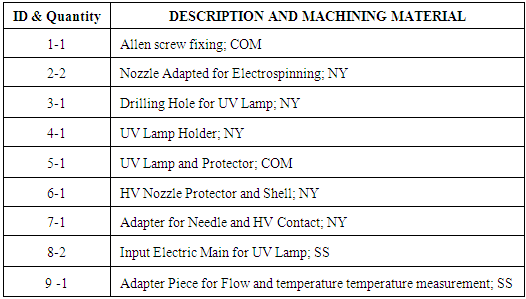 |
| |
|
Figure 4, shows the extruder from a side view, the identification numbers correspond to those in Table 1.The rotation of the twin screw is critical, and dependent on the type of material to be subjected to the process of extruding. For our present purposes, the extruder will be used primarily for engineering plastics, therefore requiring the rotation of both screws in the same direction, i.e., co-rotating, see Figure 5. The extruder was calibrated and adjusted to the speed of the screws in the heating chamber (see Figure 4). The extruder was calibrated and adjusted to the speed of the screws in the heating chamber (see Figure 4).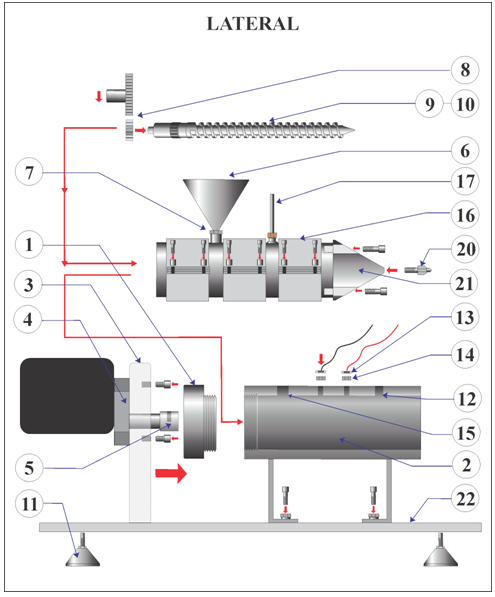 | Figure 4. A drawing showing the extruder from a lateral view |
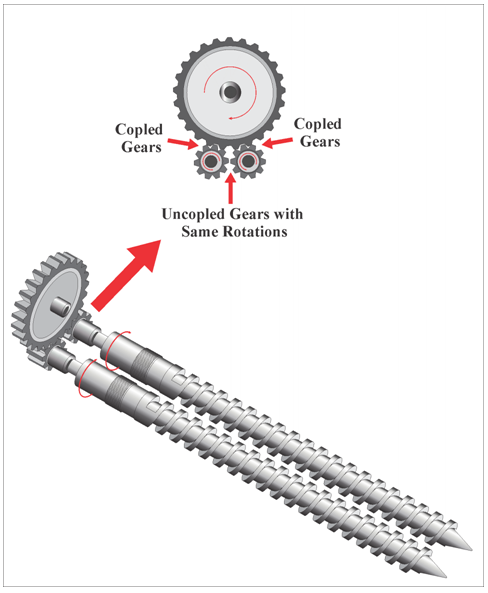 | Figure 5. Shows the engagement of the gears and twin screw to obtain the same rotation at the screws, i.e., co-rotating |
The extruder was calibrated and adjusted to the speed of the screws in the heating chamber (see Figure 4). The rotational speed can be adjusted to the mass of polymer in the loading hopper (see Figure 4).The heating rate is calculated based on the speed of rotation and transp transport of the molten polymer mass, and the mean recident time defined as:
The dimensionless time as given by:
Were r is the throttle ratio and L the effective length of screw.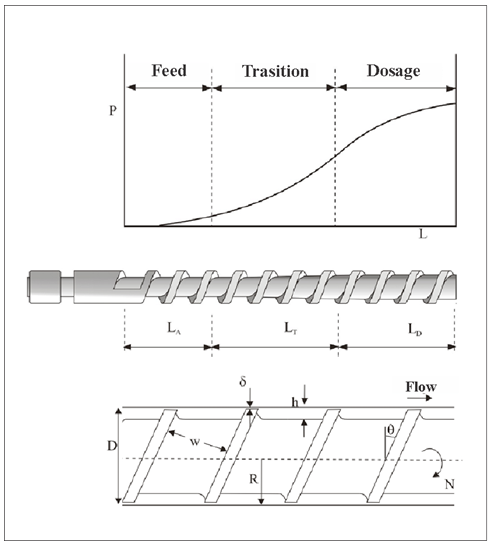 | Figure 6. Sections and parameters of the screw |
In Figure 6, R screw radius, D screw diameter,
helix angle, W channel width, h channel depth, d clearance between the cylinder and the fillet, wf flight width (see Figure 1).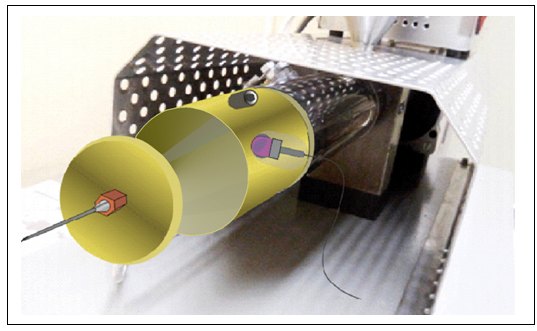 | Figure 7. Displaying the electrospinning accessory coupled to the extruder |
The Figures 8 (a) and (b) show photographs in extrusion mode for engineering plastics.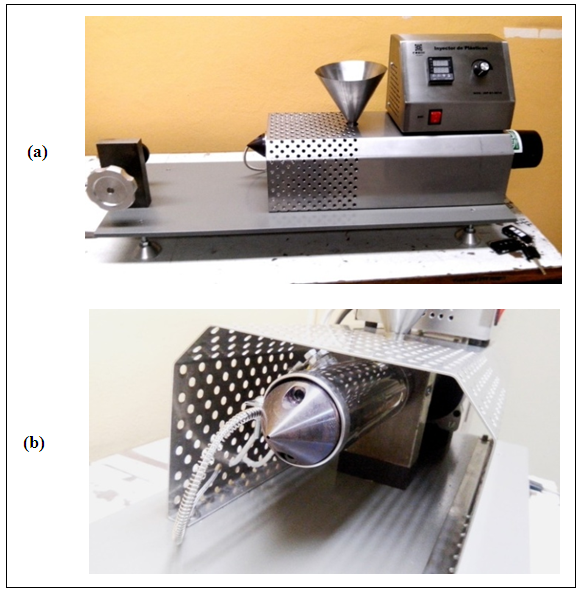 | Figure 8. (a) Photography in side view, (b) Photography in 25 ° front view |
3. Results and Calibration
Several tests were made in engineering plastics, in which the melting temperature and mixing speeds were calibrated. In the Figure 9, shows a photograph of polypropylene films obtained with several loads of titanium oxides (TiO2), Silicon and Alumina. These films were annealed to relieve the stresses in the extrusion. Small parts of these films were cut for the purpose of their characterization by means of X-ray, DSC, IR, etc.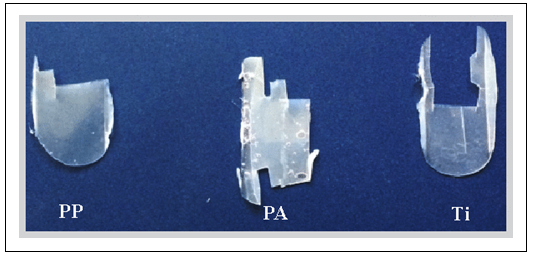 | Figure 9. Extruded polypropylene films with TiO2 |
In Figure 10 shows the microphotography of scanning electron microscopy (SEM) of poly(glycerol sebacate) PGS and poly(ε-caprolactone) PCL fibers, obtained by electrospinning and reinforcing crosslinked by UV, while in Figure 11, we show the cross section of scalfold, co-extruding PGS-PCL fibers in layer by layer, with different loads of PCL, whit 25% hydroxyapatite particles.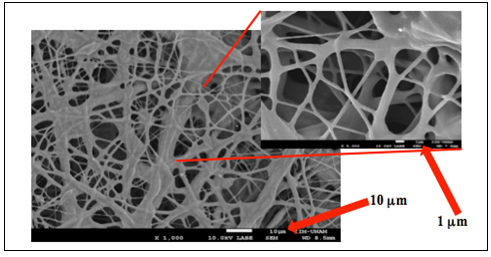 | Figure 10. PGS-PCL UV crosslinked fibers |
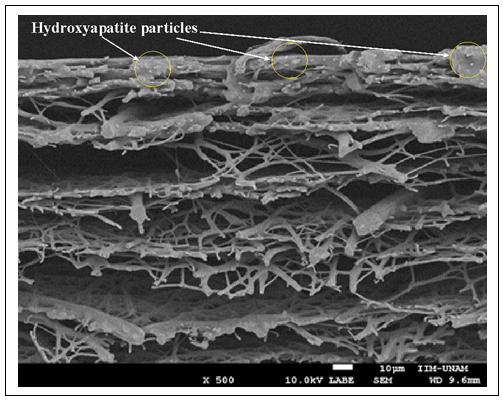 | Figure 11. Co-extruding PGS-PCL fibers in layer by layer, at different loads of PCL, whit 25% hydroxyapatite particles |
4. Conclusions
Since the mesenchymal cells culture protocols require more extended study biomedical approach, we only claim the design and construction of the co-extruder, which allows the extrusion of films and electrospinning with the formation of crosslinked fibers, for the potential of soft and hard tissue regeneration. Therefore we suggest that we have achieved a novel design and simple and cheap fabrication of an extruder that provides a method for co-extruding engineering plastics, oppening the possibility of adding new plastics at different proportions to produce homogeneous mixtures of copolymers or related polymers with a wide variety of links on structural properties. In electrospinning mode, this design allows fabricating scaffolds that can vary according to the composition and distribution of the shape and size of the micro and nano fibers, allowing for the production of scaffolds with a wide range of compositions, porosities and mechanical properties.
ACKNOWLEDGEMENTS
The authors express their gratitude to Dr. Augusto Jacobo Montiel Castro for language assistance in the drafting of this document.
References
[1] | Mani, R., Bhattacharya, M., European Polymer Journal, vol. 3737:515 (2001). |
[2] | Leong, K. F.; Chua, C. K.; Sudarmadji, N.; Yeong, W. Y. J Mech Behav Biomed Mat 2008,1(2), 140-152. |
[3] | Pompe, W.; Worch, H.; Epple, M.; Friess, W.; Gelinsky, M.; Greil, P.; Hempel, U.; Scharnweber, D.; Schulte, K. Mater Sci Eng A 2003, A362, 40-60. |
[4] | Lichte, P.; Pape, H. C.; Pufe, T.; Kobbe, P.; Fischer, H. Injury 2011, 42(6), 569-573. |
[5] | Faour, O.; Dimitriou, R.; Cousins, C. A.; Giannoudis, P. V. Injury 2011, 42(S2), S87-90. |
[6] | Liu, X.; Ma, P. X. Ann Biomed Eng 2004, 32(3), 477-486. |
[7] | Hutmacher, D. W. Biomaterials 2000, 21, 2529-2543. |
[8] | Navarro, M.; Michiardi, A.; Castano, O.; Planell, J. A. J R Soc Interface 2008, 5, 1137-1158. |
[9] | Nair, L. S.; Laurencin, C. T. Prog Polym Sci 2007, 32, 762-98. |
[10] | Martina, M.; Hutmacher, D. M. Polym Int 2007, 56, 145-157. |
[11] | Gunatillake, P. A.; Adhikari, R. Eur Cell Mat 2003, 5, 1-16. |
[12] | Erisken, C.; Kalyon, D. M.; Wang, H. Nanotechnology 2008, 18, 1-8. |
[13] | Erisken, C.; Kalyon, D. M.; Wang, H. Biomaterials, 2008, 29, 4065-4073. |
[14] | Erisken C.; Kalyon, D. M.; Wang, H.; Ornek-Ballanco, C.; Xu, J. Tissue Eng Part A 2011,17(9-10), 1239-1252. |