Tian Ze Cheng, Mahir Tuli
Dubai Amateur Rocketry, Dubai, UAE
Correspondence to: Tian Ze Cheng, Dubai Amateur Rocketry, Dubai, UAE.
Email: |  |
Copyright © 2012 Scientific & Academic Publishing. All Rights Reserved.
Abstract
By using prepolymers to dissolve oxidisers and solid components in a propellant system, we can overcome the complicated procedure and problems faced during the casting of propellants that have a low binder content. Dissolving all or even parts of the solid components can decrease the viscosity thus increasing the solid loading capacity of the propellant. This method of casting propellants has many advantages over traditional preparation methods, such as being able to cast the propellant without the use of vacuuming or vibrating machines. This paper mainly discusses the high density oxidiser, Lithium Perchlorate, and the effect of its high solubility in polar solvents. By adding these solvents to functional groups, we can create a solution that once cured, turns into a rubber that could be used as a high performance propellant. We are not the origin of this idea, however we're the first to test it. This method could also be applied to energetic materials and gun propellants in order to reach a higher density with binders.
Keywords:
Lithium perchlorate, Dissolve, Propellant, Easy manufacture, High density, High energetic performance, Easy casting
Cite this paper: Tian Ze Cheng, Mahir Tuli, Dissolving Lithium Perchlorate in Prepolymers for Easier and Cheaper Propellant Manufacture, International Journal of Aerospace Sciences, Vol. 3 No. 1, 2014, pp. 1-5. doi: 10.5923/j.aerospace.20140301.01.
1. Introduction
Eutectic composite propellants were invented way back in the 60s by Monsanto Research Center in the USA[1]. However, they have never tested this propellant in any engine and its advantages were forgotten. Our team has tested the world’s first engine using a dissolved oxidiser in prepolymers. We have also found some new advantageous attributes (compared to APCP) which were unmentioned by Monsanto.Eutectic composite propellants contain prepolymers that have the ability to dissolve its oxidisers before polymerising. This means the binder can embody far more solid mass per unit volume than it could before. Unlike the manufacturing procedures of traditional propellants, Eutectic propellants does not need expensive machines such as vacuum pumps, or machines used to shake the propellant to expel gas bubbles during processing; thus greatly reducing the cost of manufacturing. APCP often sacrifices some of it's performance due to the need to add extra binder in order to counteract the high viscosity during casting. This is unfavourable because adding more binder causes a higher than required fuel to oxygen ratio (forming unburnt carbon). However, by dissolving Lithium Perchlorate in prepolymers, we can solve this[2].Air bubbles and voids are often trapped in APCP if it is not manufactured very carefully or professionally[3]. Whereas while using Eutectic composite propellants one can easily avoid these problems. Since the oxidiser is dissolved in the propellant, the propellant has a lower than usual viscosity, this has proved to form less or no air bubbles. This makes it simpler to cast by requiring less time and effort to mix. By adding a small percentage of dissolved Lithium Perchlorate to APCP can substantially lower the viscosity of the propellant during casting, allowing more ease in mixing and a more uniform distribution of oxidiser.Eutectic composite propellant could achieve higher density than propellants prepared using traditional methods because of the low viscosity of binder in Eutectic propellants[4]. Eutectic propellant are also safer to handle and store as it is found that dissolved oxidiser is very inert. Another interesting fact about Eutectic propellants is that they also conduct electricity.We have found out that the ideal oxidiser for the job is Lithium Perchlorate (anhydrous), due to its high solubility in different polymers. Lithium Perchlorate has also been chosen because it produces the most oxygen upon decomposition in comparison to all other Perchlorates, except for Nitronium Perchlorate. Lithium Perchlorate’s high density compared to Ammonium Perchlorate allows it to produce 248% more oxygen than Ammonium Perchlorate in the same volume. This means that adding dissolved Lithium Perchlorate to APCP can allow for an increase in the amount of binder, and a decrease in the required Ammonium perchlorate content.
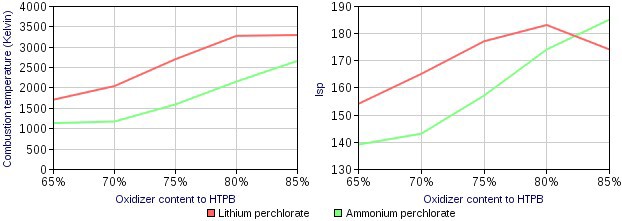 | Figure 1. A comparison of specific impulse(Isp) and combustion temperature between lithium perchlorate and ammonium perchlorate, with HTPB as fuel/binder. Note that 80% is around the maximum solid loading for HTPB and many other binders[1]. Combustion temperature and Isp (specific impulse) was calculated using the PROPEP code |
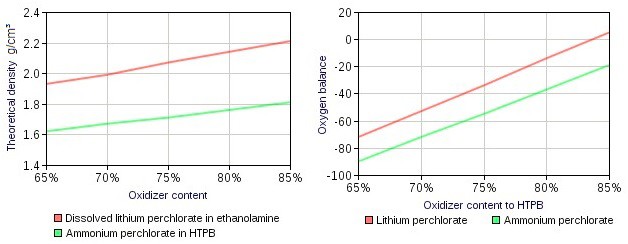 | Figure 2. Note that dissolved oxidiser in prepolymers can near its theoretical density whereas the traditional AP-HTPB propellant which usually have a density of around 1.6 at 80% oxidiser content[5] |
1.1. Comparison between Lithium Perchlorate and Ammonium Perchlorate
At 80% solid loading, Lithium Perchlorate out performs Ammonium Perchlorate. Eutectic propellants also combust at very high temperatures, this causes Aluminium to vaporise and allows it to react easier.By adding Lithium perchlorate into APCP, we can increase its binder content due to the extra oxygen Lithium Perchlorate provides. By doing this we lower the propellant's viscosity. We tend to add 5-20% Lithium Perchlorate to APCP, because using Lithium Perchlorate alone as the oxidiser would produce very high temperatures which is not desirable. Lithium Perchlorate is also more expensive than Ammonium Perchlorate, and using it alone would not be economical. The cost of anhydrous lithium perchlorate is at around 15 dollars per kilogram in China[6].
1.2. Polymer Chemistry & Solubility Data of Common Perchlorate Salts in Prepolymers
The prepolymers for Eutectic propellants can only be made of liquids that can solidify after it is mixed with the oxidiser, therefore our solvents are limited. In order to polymerise and be casted into a propellant grain, common polymers containing isocyanate groups can react with NH2 or OH groups to form Polyurea, and Polyurethane respectively. Other polymers such as epoxides can react with another wide range of compounds.For a more desirable combustion, HDI (Hexamethylene Diisocyanate) is preferred over MDI (Methyl Diphenyl Diisocyanate), because it has a lower carbon content yet higher hydrogen and nitrogen content than MDI. Which is better for the specific impulse. However, MDI cures better with hydroxyl groups than HDI in our experiments. Table 1. Solubility of perchlorate salts in some alcohols. (Perchlorates in this table are in anhydrous form.)Lithium perchlorate trihydrate's solubility and oxidizing properties hugely suffer compared to it's anhydrous form. This table is drawn from our own experimental results[2] |
| Solubility g/g solvennt | Lithium perchlorate | Ammonium perchlorate | Sodium perchlorate | Ethylene glycol | 3.4 at 90°C | 1 at 90°C | >1 at 90°C | | 1.5 at rt | <1 at rt | ~1 at 90°C | Methanol | 1.9 | 0.1 | 0.5 | Propanol | 1 | 0.1 | 0.1 | Glycerol | 0.2 | 0 | 0 | 1,3 Propanediol | ~3.3 at 90°C | Low solubility | ~1 at 90°C | 1,4 Butanediol | ~3 at 90°C | Low solubility | ~1 at 90°C | 1,6 Hexanediol | ~2 at 90°C | Low solubility | ~0.5 at 90°C |
|
|
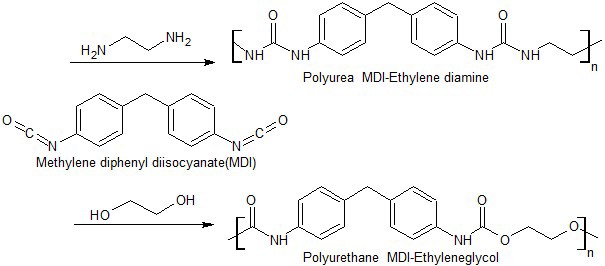 | Figure 3. Ethylene glycol and ethylene diamine react with MDI to form polyurethane linkages. This reaction could be carried out at room temperature |
1.3. OH Group Solvents
All of the above react with MDI to form polyurethane or urethane links. However, methanol and propanol produce gas bubbles during the polymerisation with MDI, which is extremely undesirable. Suitable solvents that can be used in APCP are Ethylene glycol, 1,3 Propanediol, 1,4 butanediol, 1,5 pentanediol, 1,6 hexanediol and many other polar liquids can also be used. Ethylene glycol is very inexpensive and can be used to dissolve up to 3.5 times it's own weight of lithium perchlorate at 100 degrees Celsius.The ratio of solvent to MDI/HDI shall be calculated by each hydroxyl group for each isocyanate group. When using Ethylene glycol for example, it is a rough 8:2 ratio of MDI to Ethylene glycol respectively[1,7].
1.4. Solvents Containing Both OH and NH2 Groups
Amino alcohols contain both OH and NH2 groups, which means when they react with isocyanates to give polyurea and polyurethane links, they can form a class of flexible rubber, suitable for propellants[1].Ethanolamine, 1,3 propanolamine, 1,4 butanolamine, and 1,6 hexanolamine can dissolve around 6 times its own weight of lithium perchlorate at 80-100 degrees. On the other hand, Ammonium perchlorate dissolves far less than Lithium perchlorate in amino alcohols, while sodium perchlorate and magnesium perchlorate are also quite soluble. For example upon curing with HDI if 18% binder by weight is used, roughly 4.5% of ethanolamine would be added to dissolve over 25% of Lithium perchlorate of the whole propellant.Ethanolamine is cheaper than HTPB and cures to form a flexible rubber with isocyanate compounds similar to what HTPB does, in addition, Ethanolamine can also dissolve perchlorate salts. Cheap amino alcohols, or glycols can be considered as a replacement to a large percentage of compounds in the modern APCP.
1.5. NH2 Group Solvents
Perchlorate salts dissolve quite well in diamine solvents, for example, Ethylene diamine can dissolve around 8 times its own weight of Lithium perchlorate at 80 degrees, trimethylene diamine can dissolve up to around 12 times its own weight of lithium perchlorate at 95 degrees, Hexamethylene diamine can dissolve around 8 times its own weight of lithium perchlorate at around 110C. Ammonium perchlorate's solubility in these liquids is about a quarter of the solubility of lithium perchlorate. Magnesium (II) perchlorate and Sodium perchlorate which have a better solubility in diamine solvents[6]. It's solubility is between that of Ammonium perchlorate and Lithium perchlorate. These can be used for cost or other reasons. Amines can react with any isocyanate compound to form polyurea.Although diamines has a higher solubility for perchlorate salts, diamines cure with extremely exothermic reactions upon mixing with a isocyanate compound, it can heat up to more than 50 degrees Celsius, and it could turn disastrous if the temperature is not controlled. The final product of a polyurea solid solution containing Lithium perchlorate would be a hard, strong material with superior mechanical properties compared to those not containing a dissolved perchlorate, even while using similar quantities of oxidizer. Solvents with diamine groups also cure faster, a typical rate can be around 1 hour. *Lithium perchlorate used has to be anhydrous.
1.6. Epoxies and Other Binders
It is found lithium perchlorate can dissolve in many types of epoxy hardeners, and resins, however, in much lower amounts compared to the solvents mentioned above. Some epoxides compounds have been researched by the Monsanto research center, such as limonene diepoxide, but due to cost and availability of epoxide compounds, solid solutions of polyurethane and polyurea are preferred over epoxides. Lithium perchlorate can also dissolve in acrilamide, which was what the Monsanto research group tried. After adding acrilamide, ethylene glycol was also added, and the solution was heating until acrilamide thermally polymerized with it self to form a solid solution of lithium perchlorate in polyacrilamide[9].An eutectic propellant of lithium perchlorate with hydrazine perchlorate has also been researched by the Monsanto research center in the 60s and 70s, however, the toxicity of hydrazine compounds hinders its development[1].
2. Experimental
Testing different types of solvents, and the properties of eutectic propellants after cured with isocyanates. All chemicals mentioned in this paper are used with purities >99%. Lithium perchlorate used in our experiment was stored in a nitrogen atmosphere with less than 0.1% water.
2.1. Formulation 1, APCP Containing Dissolved Lithium Perchlorate in Solid Solution of Polyurethane
This example illustrates a solid solution of polyurethane and Lithium perchlorate, mixed into APCP for better casting system.To cast the propellant we begin by adding 3.6% ethylene glycol, which completely dissolves 12.5% of Lithium Perchlorate at 100 degrees. Cool the solution back down to 80 degrees to prevent ethylene glycol from evaporating too fast. Next 16% atomized aluminum powder is introduced. After a few minutes of mixing, 14.4% of MDI (2,4-methylene diphenyl diisocyanate) and 53.5% of ammonium perchlorate (200 mesh, spherical prilled for aerospace use) is added to the mixture. After around half an hour of mixing, pour the liquid into a mold containing the shape of the grain desired, the grain shall be kept above 60 degree for the next 5 hours to cure. After curing, it produces a tough polymer with low elasticity, however this can be greatly improved by adding a plasticiser(After curing, it produces a tough polymer with low elasticity, however this can be greatly improved by adding a small amount of plasticiser into the mixture (about 2-3%). Burn rate: 2.1mm/s at 14.7psi for formulation #1.
2.2. Formulation 2 - APCP Containing Dissolved Lithium Perchlorate in Solid Solution of Polyurea
5.4 grams of 1,6 Hexamethylene Diamine dissolved 15% of lithium perchlorate completely at 100 degree celsius. Upon adding isocyanate, extreme exothermic reaction was observed. We abandoned the experiment for safety reasons. We will test 1,3 Ethanolamine in the near future, and expect it to outperform ethylene glycol and ethylene diamine greatly. We expect its cured polymer to have better / more desirable mechanical properties.The impact sensitivity for both formulations are also likely to be out of range.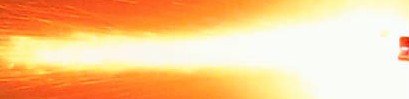 | Picture 1. Static test of our motor containing eutectic propellant formulation 1 |
 | Picture 2 and 3. Static firing of our rocket engine using formulation 1. This is the world's first rocket engine that uses dissolved oxidiser in prepolymers as its propellant. Mach diamonds can be seen on the second picture(right), which was post processed with filters. The visibility of mach diamonds were distorted by the bright combustion of aluminium powder |
2.3. Viscosity
Two formulations of Ammonium perchlorate and lithium perchlorate with binder were tested at different temperatures. Formulation 1 contains 75% Ammonium perchlorate, 5% Ethylene glycol, and 20%MDI. Formulation 2 has 75% Lithium perchlorate, 5% Ethylene glycol, and 20% MDI.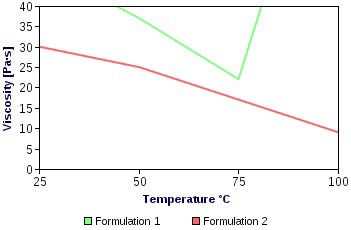 | Figure 4. Viscosity of tested formulations |
We faced some difficulties in testing the viscosity especially in formulation 1. Upon heating formulation 1 near the boiling point of water, the mixture becomes a hard solid. At room temperature, formulation 1 is a semi solid and is very hard to mix, its viscosity is similar to that of partially dried cement. Whereas formulation 2 had a much lower viscosity, something similar to that of honey.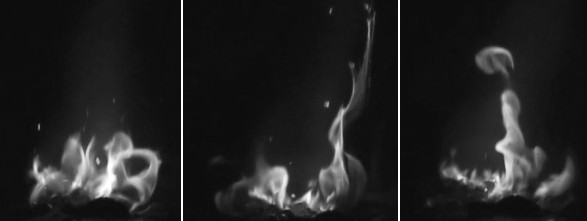 | Picture 4. A Burn test of Formulation 2 mentioned above. This propellant is also water proof, a small sample was dropped into distilled water for 1 hour, after taking it out we could easily ignite it under a torch |
3. Conclusions & Prediction
Dissolving an oxidizer such as lithium perchlorate can greatly decrease the viscosity and the difficulties during propellant casting. The properties of a propellant that has its oxidizer partially dissolved in polyurethane could be more uniformly mixed, have a higher density and have a cleaner and more complete combustion.Adding around 10-20% dissolved lithium perchlorate could give a good mix between cost, ease of casting, and performance.We're high school students and therefore our research results might not be precise. We have tested eutectic propellants in a rocket engine two times, both tests were successful and had formulations close to formulation 1 mentioned above. Although we have made many grain samples of polyurea solid solution containing lithium perchlorate, we have yet to try it in an engine, however we plan to do so in the near future.Compounds that dissolve in polar liquids, such as lithium perchlorate, might also dissolve in polymers such as Nitrated-HTPB, Poly-GLYN, and plasticisers such as Nitroglycerin, EGDN, DEGDN, and BTTN. Hydroxylammonium nitrate and Hydroxylammonium perchlorate might have a higher solubility over AP[10]. ADN, a new oxidiser with a higher performance compared to AP, can dissolve in most polar solvents with good solubility[11]. This can decrease the sensitivity of ADN while preventing mixing or prilling which is hazardous. The idea can also be used with binder bonded explosives, gun propellants, or other polymer bonded materials to achieve higher density in comparison to normal binders.
ACKNOWLEDGMENTS
We would like to thank our parents who funded us in our purchase of chemicals and any other people who contributed and supported us.
References
[1] | Bedell Stanley F, Gilman Lucius G, Lait Robert I, Polymeric propellant composition containing lithium perchlorate/ ammonium perchlorate eutectics, US patent 3567530, Mar 2, 1971. |
[2] | Robert F. Mcalevy, Suh Yong Lee, Frank A. Lastrina, and Norman A. Samurin - Investigation of the ammonium perchlorate composite propellant deflagration mechanism by means of experimental analog techniques - technical report - rt 67006 - 1967 department of the navy office of naval research, power branch contract nonr 263. |
[3] | Hans Olaf Toft - Voids in solid propellants, June, 2002. |
[4] | P.J.T. Mills1, a, J.P.K. Sevilleb,P.C. Knighta, M.J. Adamsb - The effect of binder viscosity on particle agglomeration in a low shear mixer/agglomerator - Powder Technology - Volume 113, Issues 1–2, 20 November 2000, Pages 140–147. |
[5] | Lockheed Propulsion Company - Solid Propeallant Structural Intergrity Investigations: Dynamic Response and Failure Mechanisms Quarterly Progress. Report no2, Jan, 1965. |
[6] | Email with sales department of Shanghai China Lithium Industry Co., Ltd. |
[7] | US enviromental protection agency Technical Fact Sheet – Perchlorate. United states, May 2012. |
[8] | Hedrick Ross M, Lucius Gilman, Mottus Edward H. Solid propellant containing lithium perchlorate. US patent 3117898 Jan 14, 1964. |
[9] | Hedrick Ross M, Motlus Edward H - Solid composite propellants containing lithium perchlorate and polyamide polymers. US patent 3094444, June 18, 1963. |
[10] | Ronald Sasse - Analysis ofhydroxylammonium nitrate based liquid propellants. Sep, 1990. |
[11] | Anders Larsson and Niklas Wingborg Green Propellants Based on Ammonium Dinitramide. FOI - Swedish Defence Research Agency, 2011. |