Margarita Mezzetti 1, Markus Radajewski 2, Matthias Reich 1, Lutz Krüger 2
1TU Bergakademie Freiberg, Institute of Drilling Engineering and Fluid Mining, Freiberg, Germany
2TU Bergakademie Freiberg, Institute of Materials Engineering, Freiberg, Germany
Correspondence to: Margarita Mezzetti , TU Bergakademie Freiberg, Institute of Drilling Engineering and Fluid Mining, Freiberg, Germany.
Email: |  |
Copyright © 2016 Scientific & Academic Publishing. All Rights Reserved.
This work is licensed under the Creative Commons Attribution International License (CC BY).
http://creativecommons.org/licenses/by/4.0/

Abstract
The steadily increasing need for energy resources represents a challenge in every aspect. The fossil energy resources are limited and may be locked several thousand meters below the surface, which may also imply the need of highly complex wellbores and results in high costs. In order to be able to reach these resources, special tools and equipment are needed. These tools are exposed to extreme conditions such as high loads, high temperatures and pressures as well as abrasive conditions while in contact with the formation. Under such conditions, the tool and component lifetime also has an economic impact. A current challenge is to extend the lifetime of the tools and components. The materials being used include polycrystalline diamond compact (PDC), thermally stable polycrystalline diamond (TSP) and cemented carbides, i.e. tungsten carbide-cobalt alloys. Tungsten carbide-cobalt alloys are extensively used for several applications such as inserts for roller cone drilling bits, cutting plates and wear protection. For these alloys, the wear resistance is closely related to the hardness, however, an increase in the hardness reduces the fracture toughness of the material. In sintered hard metals processed through the traditional routes, such as Hot Isostatic Pressing (HIP) or Hot Pressing (HP), grain growth inhibitors are often used to accomplish a fine grain size in the order of µm. With the FAST technique (Field Assisted Sintering Technology) it is possible to produce bulk materials in the near-nano range (WC grain size dWC ≈ 200 nm) without the use of grain growth inhibitors. In order to prove the suitability of FAST tungsten carbide alloys in the near-nano range for drilling tools and components, comparative tests between standard materials and FAST material are conducted in a small scale drilling test stand. Tests are performed on different rocks to reproduce different formation types. The results of a test series on granite and sandstone are presented. The preliminary results are promising, since the FAST material exhibits less wear than the standard materials.
Keywords:
Sintering, FAST, Near-Nano, Tungsten carbide - cobalt, Cemented carbide
Cite this paper: Margarita Mezzetti , Markus Radajewski , Matthias Reich , Lutz Krüger , FAST Materials for Rock Destruction Applications, Nanoscience and Nanotechnology, Vol. 6 No. 1A, 2016, pp. 77-82. doi: 10.5923/c.nn.201601.15.
1. Introduction
Drilling applications require materials that can keep up with the extreme conditions encountered while drilling, e.g. high loads, high pressures, abrasive formations and in some cases also high temperatures. There is a variety of materials currently being used for drilling applications, ranging from tungsten carbide cobalt alloys up to polycrystalline diamond compact (PDC). Cemented carbides are used extensively, for example as inserts in drilling bits or as wear protection in drilling components. Drilling operations are expensive and an important part of it is represented by the costs from tools and components. One of the current challenges is to extend the lifetime of the materials being used for these applications, which would result in an economical effect. Current research efforts include the combination of materials, such as PDC with boron nitride or reinforcement from the binder. In the case of hard metals, a more traditional approach has been followed, namely the grain refinement. The traditional sintering methods, e. g. Hot Isostatic Pressing (HIP) and Hot Pressing (HP), have allowed the achievement of ultra-fine grades with grain sizes in the order of some µm or less [1, 2], however until now the use of grain growth inhibitors has been unavoidable [3]. Some recent studies claim that the use of grain growth inhibitors may have a detrimental effect in the overall properties, such as fracture toughness and wear resistance [4]. The latent question is whether the near-nano materials perform better as their “coarser„ counterparts or if they have the potential to substitute the traditional materials in the long run [5].The further development of new technologies, for example the Spark Plasma Sintering (SPS) or Field Assisted Sintering Technology (FAST), have allowed the sintering of samples with grain sizes in the near-nano range. It is expected that the grain refinement results in a high hardness, consequently in a higher wear resistance but at the same time in a deterioration of the fracture toughness.Recent investigations conducted within the Freiberg High Pressure Research Centre, FHP, at the Technische Universität Bergakademie Freiberg have shown that it is possible to consolidate samples with a WC grain size in the near-nano range, about 200 nm, without the aid of grain growth inhibitors while keeping the fracture toughness at a reasonable level [6-9]. Further research efforts at the FHP include the evaluation of the FAST materials for drilling applications. An overview of some of the tests conducted in a laboratory rig drilling test stand to evaluate the performance of FAST-materials for drill hammer inserts will be presented in the following sections.
2. Experimental Procedure
2.1. Testing Materials
The FAST-materials used for the comparative tests were tungsten carbide- cobalt samples sintered by using the FAST technique without the aid of grain growth inhibitors. The raw samples were cylindrical shape (diameter 15.5 mm, height: 20-21 mm) and they were afterwards machined to the desired insert form. Additionally, commercial samples were tested. The typical geometry of the samples after the sintering process and the final geometry of the test inserts are shown in Figure 1.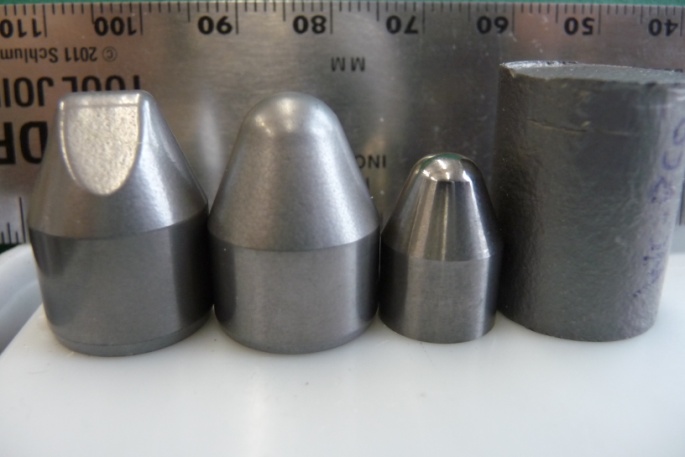 | Figure 1. Inserts for tests with the drill hammer and raw cylindrical sample after sintering with the FAST technique |
The FAST-materials used in this study are presented in Table 1. On this table the relevant properties, for example, WC grain size, hardness and indentation fracture toughness can be found. For the commercial counterparts, not all of the information was readily available. Table 1. Typical properties of FAST-materials and commercial samples |
| Sample ID | Density, g/cm3 | Grain Size, nm | Hardness, HV 10 | KIc, MPa m1/2 | FHP-A WC-8Co | 14.737 | 185 nm | 2050 ± 30 | 9.4 ± 0.2 | FHP-B WC-8Co | 14.746 | 185 nm | 2050 ± 30 | 9.4 ± 0.2 | FHP1 WC-12Co | 14.309 | 195 nm | 1670 ± 20 | 10.6 ± 0.9 | FHP2 WC-12Co | 14.305 | 195 nm | 1670 ± 20 | 10.6 ± 0.9 | W1 / W2 WC-15Co | 14.134 | n. a. | 1090 | n. a. | C / E WC-12Co | 14.100 | 0.2-0.5 µm | 1730 | 7.8 |
|
|
For the samples W1 and W2 the density and hardness were determined in the laboratory. The measurement of the fracture toughness on those samples was not possible due to the absence of resulting cracks at the hardness indentations. This indicates a high fracture toughness.For samples C and E, the information regarding the typical properties have been provided by the manufacturer.
2.2. Tests in the Small Scale Laboratory Drilling Rig
The tests were performed with drilling hammer prototype inserts in a small scale drilling test stand. With this drilling test stand it is possible to perform tests to analyse the rock destruction process by impact drilling with an electrically driven drilling hammer. With this device is possible to set up the frequency and the duration of the impacts [10]. The test conditions were a frequency of 10 Hz and a test time duration ranging from 5 up to 30 min. The tests were performed in block rock samples. Two different rock samples were chosen, sandstone and granite. Sandstone is a sedimentary rock and exhibits a high abrasivity, which makes it ideal to evaluate the performance under abrasive conditions. Granite is an igneous crystalline hard rock, which in the praxis is difficult to drill through. A picture showing the typical experimental set-up in the small scale drilling test stand is shown in Figure 2.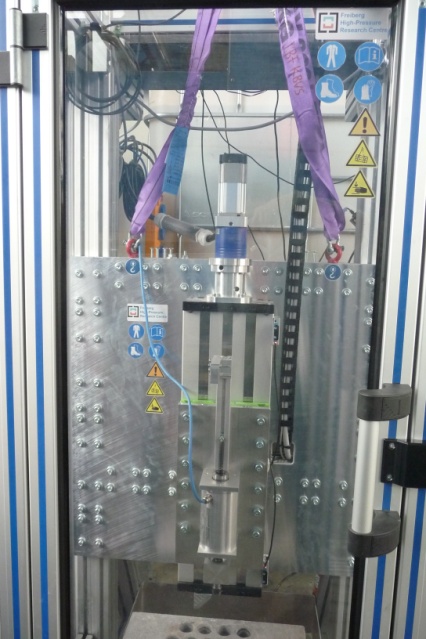 | Figure 2. Typical experimental set-up in the small scale drilling test stand |
Some of the typical geological properties of the rocks used in this study, the unconfined compressive strength (UCS) and the Cerchar Abrasivity Index (CAI), can be found in Table 2. Table 2. Typical Rock Properties |
| Rock | CAI Abrasivity [11] | UCS, MPa [12] | Sandstone | 2-6 | 90.1 | Granite | 3.5-5 | 181.7 |
|
|
It needs to be pointed out that rocks are nature products, therefore their properties are bound to vary quite strongly depending on the specific mineralogical composition. Tests were comparative, so the FHP samples were tested under the same conditions as commercially available counterparts. In order to quantify the volume loss of the samples after the tests, the starting and finishing mass was determined. Mass measurements were conducted on a Sartorius BA210S scale with a measurement exactitude of 0.1 mg. If there is a mass loss, than is converted to volume loss by using the basic density formula. Figure 3 shows the electrical drill hammer with the test insert during a test in a granite block.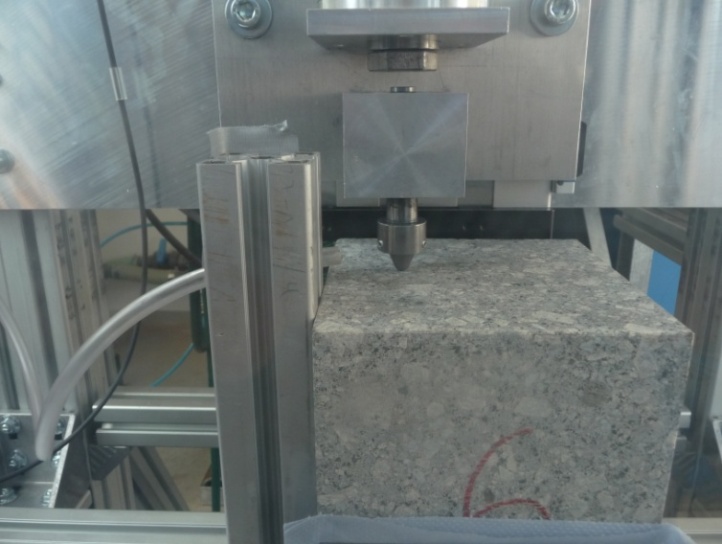 | Figure 3. Tests in granite with the electrical drill hammer |
Microstructural investigations were performed using a Carl Zeiss LEO 1530 scanning electron microscope (SEM) to identify which deterioration mechanisms are active in both samples, the commercial and the FAST samples. The results and observations after the tests are presented in the following section.
3. Results and Discussion
3.1. Volume Loss after Drill Hammer Tests
The results of the volume loss after the tests in granite and in sandstone are presented in Figures 4 and 5.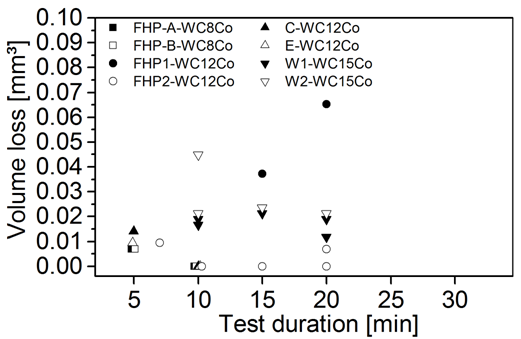 | Figure 4. Volume loss after tests with the electrical drill hammer prototype in granite |
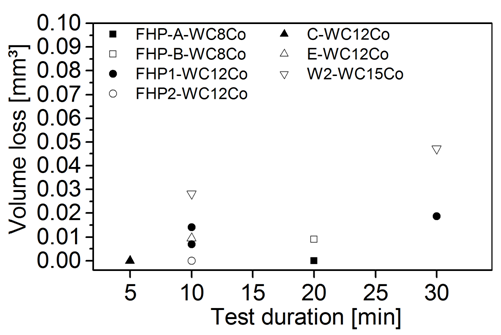 | Figure 5. Volume loss after tests with the electrical drill hammer prototype in sandstone |
The tests in granite were conducted at durations between 5 and 25 minutes and those in sandstone between 5 and 30 min. Samples marked as FHP-A, FHP-B und FHP 1 and FHP2 represent the FAST samples, while Samples W1, W2, C and E are commercial samples.
3.2. SEM Characterization
The SEM micrographs from the surface of the inserts after the first series of tests in sandstone are presented in detail in figures 6 and 7 for the FAST-material and the commercial material, respectively, Representative samples of the commercial and FAST-material were analysed by scanning electron microscopy to evaluate the existing deterioration mechanisms.In the FAST material the present deterioration features are not that obvious. It was possible to identify regions with local deformation and partial detachment of small grain groups, see in Figure 6 the areas marked as A and B, respectively. However, no extensive damage or such evident damage to single grains, as observed in the commercial sample, could be identified.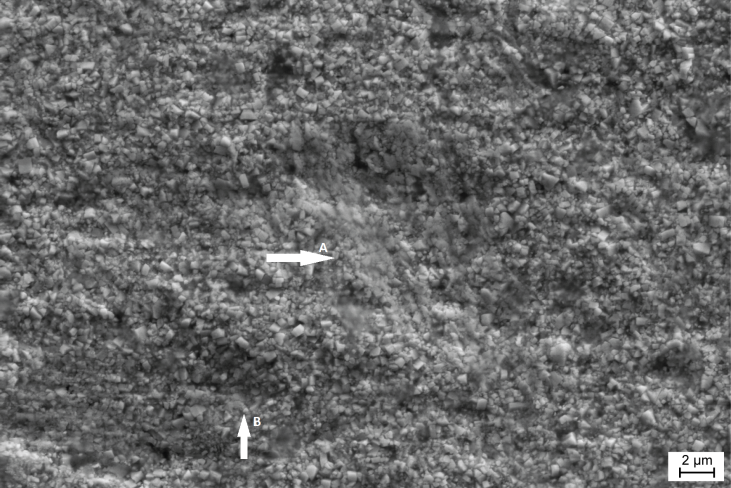 | Figure 6. SEM Micrograph from WC- 8Co FAST sample after testing in sandstone |
In the SEM micrograph for the commercial samples it is possible to see that the single grains of WC are to a great extent partially broken, see area marked with C in Figure 7 and there are regions in which the grains are already partially detached (area marked with D in Figure 7).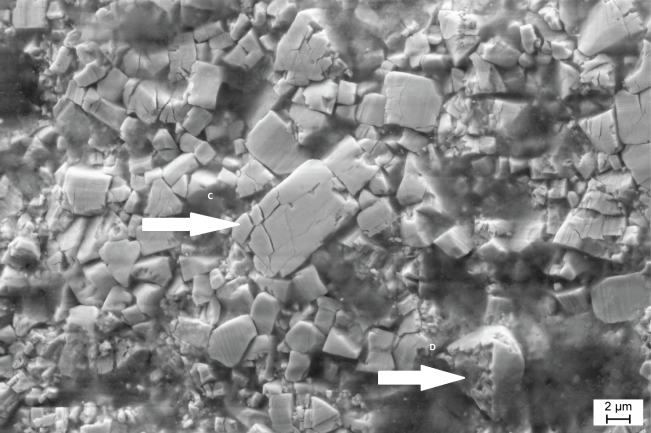 | Figure 7. SEM Micrograph from the commercial sample after testing in in sandstone |
3.3. Discussion
Since its introduction in the market as a new promising technology, the FAST process has been used quite often with the purpose of eliminating the problems bound to the traditional HP and HIP sinter techniques [2, 13]. One of the main issues with the traditional techniques has been that a grain refinement was not easily achieved. With the FAST Technique it has been possible to accomplish the grain refinement without the aid of grain growth inhibitors [14].Tungsten carbide-cobalt alloys are widely used for tools and components, particularly for applications requiring high wear resistance. The system tungsten carbide cobalt offers the possibility of having the high hardness combined with a certain fracture toughness by varying the cobalt content. It is also well known that the wear resistance is directly related to the hardness of the material. In general, the following principle applies: as the hardness increases, so does the wear resistance of the material. Under this assumption, a grain refinement with subsequent increase in the hardness will result in a better wear resistance. Thus, near nano materials would be the ideal candidates to replace the existing materials in the µm range. A better wear resistance would result in an extended lifetime of the material or component.However, an increase in the hardness may also result in a decrease of the fracture toughness of the material. The question arises, could near-nano materials substitute or represent an alternative to traditional materials? Some researchers have tried to evaluate this possibility and their results do not seem to provide a conclusive answer [4, 5, 15, 16]. In the series of tests conducted by those authors, the materials were chosen according to their hardness, although this also resulted in a widespread composition, which may not provide the definitive answer to this question. There have been many efforts to predict the wear resistance and lifetime of the components. From the side of the user, the wear resistance is considered to be mainly influenced by the formation and its abrasivity. In this way, several indexes relating the mineralogical composition of the formation are used to predict the lifetime of a component. From the side of the manufacturer of the tools and components, the wear resistance of hard materials is typically evaluated by using the standard abrasion tests, e. g. ASTM B611. This standard describes a rotating wheel abrasion test under specific conditions. The results are usually reported as volume loss [17]. When comparing the wear resistance of the material or when looking for an evaluation of the wear resistance, it has been found that quite often modifications to the standard conditions have been made [18, 19].Under these conditions, what can be used as a reliable reference for the wear resistance? Obviously the best way of evaluating the wear resistance and lifetime can be done by conducting field tests or by reproducing closely the encountered conditions in the laboratory.For the investigations conducted within this project, the choice was to replicate the application of hard materials for drill hammer inserts and to perform a series of drill hammer tests on rock samples by using an electrically driven drill hammer. As mentioned previously, one of the objectives followed within FHP is to evaluate the applicability from the FAST-materials for drilling applications. Because of this, samples replicating the form of inserts have been obtained and tested.In this work, materials with a quite similar composition were chosen. The approach was to use materials with the similar composition and evaluate whether the materials perform better or worse. In this case the differences between the FAST samples and the commercial samples are the actual grain size and the resulting properties of the materials, e.g. hardness and fracture toughness. The FAST-materials exhibit a higher hardness and a higher fracture toughness when compared to the commercial materials used in this study, as can be seen in the Table 1. It is as well expected that these materials exhibit also a higher wear resistance. The results of the tests show that the FAST-materials perform better than the standard materials in most of the cases, see Figures 3 and 4. For the tests in granite, there are two points that show a somehow higher volume loss for sample FHP2. The rock samples are of a heterogeneous nature that means there might be some variation depending on the composition and the mineral components present at a certain location. Although the tests were conducted under similar conditions, it is possible that the sample FHP2 was tested at a particularly abrasive location in the granite sample. Since the impact tests with the electrical drill hammer prototype are unique and it is not possible to repeat the tests at the same location, it remains only the possibility to increase the number of tests to minimise the uncertainty.The preliminary results from the tests in sandstone show that the FAST-materials exhibit less volume loss than the commercial materials particularly by the long duration tests. The active deterioration mechanisms in typical WC-Co alloys used for rock destruction applications have been identified and summarized by Beste et al. [20]. A good review from the general mechanisms observed in WC-Co alloys is also provided by Gee [21]. No extensive information is available for near-nano materials. An attempt has been started by Konyashin with his work in near nano materials with higher cobalt content and lower hardness [5, 16]. For that particular case, the observed features were the presence of microchipping and microcracking as well as the separation of large WC-Co fragments. The active deterioration mechanism was attributed to the reduced fracture toughness of the material due to the use of grain growth inhibitors.In the case of FAST-materials the analysis of the microstructural features after tests in sandstone revealed only the presence of small areas with local deformation and partial detachment of grains. It would be important to further investigate the active deterioration mechanisms as well as the evolution of such features.
4. Conclusions
A preliminary evaluation of the wear resistance of hard metals for drilling applications has been possible by performing tests with a small scale rig test stand. Characterization of the commercial samples in the SEM confirmed the microstructural active deterioration mechanisms for the standard materials. In the FAST-materials, in the other hand, it was only possible to identify local deformation and local detachment of small grain groups. The comparative tests between commercially available materials and FAST near-nano materials are promising, since in most cases the near-nano materials exhibited less volume loss than the commercial counterparts.Further tests in other rocks and further microstructural characterization of the samples is needed. It is also desirable to develop a reliable method for predicting the lifetime of tools and components for rock destruction applications based on their properties and specific working conditions.
ACKNOWLEDGEMENTS
The authors gratefully acknowledge the Dr. Erich Krüger Stiftung for the financial support of this project. A special thanks to Nikolai Jordanow for his assistance during the tests.
References
[1] | Ou, X. Q.; Song, M.; Shen, T. T.; Xiao, D. H.; He, Y. H.: Fabrication and mechanical properties of ultrafine grained WC–10Co–0.45Cr3C2–0.25VC alloys. In: International Journal of Refractory Metals and Hard Materials 29 (2011) 2, S. 260–67. |
[2] | Eriksson, M.; Radwan, M.; Shen, Z.: Spark plasma sintering of WC, cemented carbide and functional graded materials. In: International Journal of Refractory Metals and Hard Materials 36 (2013), S. 31–37. |
[3] | Fang, Z. Z.; Wang, X.; Ryu, T.; Hwang, K. S.; Sohn, H.: Synthesis, sintering, and mechanical properties of nanocrystalline cemented tungsten carbide – A review. In: International Journal of Refractory Metals and Hard Materials 27 (2009) 2, S. 288–99. |
[4] | Konyashin, I.; Ries, B.: Wear damage of cemented carbides with different combinations of WC mean grain size and Co content. Part I: ASTM wear tests. In: International Journal of Refractory Metals and Hard Materials 46 (2014), S. 12–19. |
[5] | Konyashin, I.; Ries, B.; Lachmann, F.: Near-nano WC–Co hardmetals: Will they substitute conventional coarse-grained mining grades? In: International Journal of Refractory Metals and Hard Materials 28 (2010) 4, S. 489–97. |
[6] | Dipl.-Ing. Kristin Mandel, D.-I. L. K.: Spark plasma sintering and compressive strength behaviour under dynamic loading conditions of nanocrystalline WC-Co. In: FHP -TUBAF (Hrsg.): Freiberg High Pressure Symposium. |
[7] | Mandel, K.; Krüger, L.; Krause, R.; Radajewski, M.: The influence of stress state on the compressive strength of WC–Co with different Co contents. In: International Journal of Refractory Metals and Hard Materials 47 (2014), S. 124–30. |
[8] | Mandel, K.; Krüger, L.; Schimpf, C.: Study on parameter optimisation for field-assisted sintering of fully-dense, near-nano WC–12Co. In: International Journal of Refractory Metals and Hard Materials 45 (2014), S. 153–59. |
[9] | Mandel, K.; Radajewski, M.; Krüger, L.: Strain-rate dependence of the compressive strength of WC–Co hard metals. In: Materials Science and Engineering: A 612 (2014), S. 115–22. |
[10] | Lehmann, F.; Reich, M.: Development of alternative drive concepts for down-the-hole hammer in deep drilling: Conference Proceedings - OMAE 2015. |
[11] | Plinninger, R. J.; Restner, U.: Abrasiveness Testing, Quo Vadis? – A Commented Overview of Abrasiveness Testing Methods. In: Geomechanik und Tunnelbau 1 (2008) 1, S. 61–70. |
[12] | Schön, J. H.: Geomechanical Properties. |
[13] | Ren, X.; Miao, H.; Peng, Z.: A review of cemented carbides for rock drilling: An old but still tough challenge in geo-engineering. In: International Journal of Refractory Metals and Hard Materials 39 (2013), S. 61–77. |
[14] | Mandel, K.: Untersuchungen zum feldaktivierten Sintern und zum geschwindigkeitsabhängigen Festigkeits- und Versagensverhalten von near-nano WC-Co-Hartstoffen unter Druckbeanspruchung 2014. |
[15] | Konyashin, I.; Ries, B.: Wear damage of cemented carbides with different combinations of WC mean grain size and Co content. Part II: Laboratory performance tests on rock cutting and drilling. In: International Journal of Refractory Metals and Hard Materials 45 (2014), S. 230–37. |
[16] | Konyashin, I.; Ries, B.; Hlawatschek, D.; Zhuk, Y.; Mazilkin, A.; Straumal, B.; Dorn, F.; Park, D.: Wear-resistance and hardness: Are they directly related for nanostructured hard materials? In: International Journal of Refractory Metals and Hard Materials (2014). |
[17] | G02 Committee: Test Method for Abrasive Wear Resistance of Cemented Carbides (2013) B611-13. West Conshohocken, PA. |
[18] | Gant, A. J.; Gee, M. G.; Roebuck, B.: Rotating wheel abrasion of WC/Co hardmetals. In: Wear 258 (2005) 1-4, S. 178–88. |
[19] | Angseryd, J.; From, A.; Wallin, J.; Jacobson, S.; Norgren, S.: On a wear test for rock drill inserts. In: Wear 301 (2013) 1-2, S. 109–15. |
[20] | Beste, U.; Jacobson, S.: A new view of the deterioration and wear of WC/Co cemented carbide rock drill buttons. In: Wear 264 (2008) 11-12, S. 1129–41. |
[21] | Gee, M. G.; Gant, A.; Roebuck, B.: Wear mechanisms in abrasion and erosion of WC/Co and related hardmetals. In: Wear 263 (2007) 1-6, S. 137–48. |