Ayman Elsayed
Powder Technology Lab, Central Metallurgical Research and Development Institute, Cairo, Egypt
Correspondence to: Ayman Elsayed , Powder Technology Lab, Central Metallurgical Research and Development Institute, Cairo, Egypt.
Email: |  |
Copyright © 2016 Scientific & Academic Publishing. All Rights Reserved.
This work is licensed under the Creative Commons Attribution International License (CC BY).
http://creativecommons.org/licenses/by/4.0/

Abstract
Tungsten-copper composites combine high density and high electrical and thermal conductivities in a high strength mixture of insoluble phases that are easy to form by powder metallurgy. The combination of tungsten and copper optimizes properties such as ductility, strength, corrosion resistance, wear resistances, and thermal properties. Accordingly, W-Cu composites are used in electric and electronic materials such as heavy-duty electrical contacts, high current circuit breakers, resistance welding electrodes, heat sinks, and contact tips in gas-metal arc welding guns. Elemental powders of nano-sized tungsten and chemically deposited nano-sized copper were used for preparing tungsten/copper nano composites. A composite of 50.%W/50wt.%Cu composition was prepared by mixing. Then, multi-walled carbon nanotubes were added using wet mixing to be well distributed in the composite. The obtained powder blends underwent consolidation by cold compaction, then vacuum pressureless sintering. Eventually, sintered samples were finished by hot isostatic pressing. Results proved that the synthesis of the composite by the investigated route yields good performance. W-Cu-CNT manufactured nanocomposites have shown much better density than previously reported similar samples. Hot isostatic pressing has played a very important role in gaining the good density of the nanocomposite at relatively low processing temperatures.
Keywords:
W-Cu-CNT Nanocomposites, Powder fabrication, Vacuum sintering, HIP
Cite this paper: Ayman Elsayed , W-Cu-CNT Nanocomposite by Vacuum Sintering and Hot Isostatic Pressing, Nanoscience and Nanotechnology, Vol. 6 No. 1A, 2016, pp. 35-38. doi: 10.5923/c.nn.201601.06.
1. Introduction
The combination of tungsten and copper in a single composite optimizes properties such as ductility, strength, corrosion resistance, wear resistances, and thermal properties. Hence, W-Cu composites are used in electric and electronic materials such as heavy-duty electrical contacts, high current circuit breakers, resistance welding electrodes, heat sinks, and contact tips in gas-metal arc welding guns [1–6]. Tungsten-copper is a two phase composite consisting of tungsten as the base constituent forming the refractory hard phase which possess high strength and low thermal expansion coefficient. On the other hand, copper is the ductile phase having high thermal and electrical conductivities. The fabrication of a fully dense W-Cu composite is very difficult due to the big difference between the melting points of tungsten (approximately 3400°C) and copper (approximately 1083°C). Also, there is no overlap between their sintering temperature ranges. Moreover, W-Cu system has no mutual solubility, which usually results in poor sinterability [7]. Mechanical alloying is a popular technique for producing tungsten-copper homogeneous nanocomposites. Various W-Cu composites have been developed including ultrafine micro-composite structures by this technique [8]. The dispersion technique is another fabrication method that depends greatly on the powder characteristics which affects the sintering behaviour [8]. The dispersion of the copper phase and the fineness of the tungsten phase play a big role in the sinterability of W-Cu powders. The milling behavior depends on the composition, milling time, and milling atmosphere. High energy milling produces particles containing small tungsten grains embedded with copper. This type of powder significantly improves sintering in the W-Cu system [9].The aim of the current work is to synthesize (50wt.%W/50wt.%Cu) composite by mixing. Consolidation using vacuum sintering and hot isostatic pressing techniques are presented. Nanosized copper and tungsten powders were used for manufacturing the composites, where the nanosized copper powder was prepared by electroless deposition. The optimal conditions for powder blending and consolidation and their influences on the properties are reported.
2. Experimental work
Powder technology was used to manufacture the composite using nano-sized powders of both tungsten and copper. Nano tungsten powder with purity 99.95% and particle size ~ (40-60 nm) was provided from US Research Nanomaterials, Inc. On the other hand, a homemade nano-copper powder with an average particle size of ~50 nm has been prepared by electroless deposition using formaldehyde as a reducing agent for copper sulphate solution in an alkaline tartarate path at a pH ~ 12. For each liter of distilled water, 200 mL of formaldehyde, 35 g of CuSO4, 170 g of potassium sodium tartarate and ~50 g of sodium hydroxide were added. Then the deposited copper powder was cleaned with distilled water and dried at 120°C for 2hrs. Carbon nanotubes “CNT” were also added to some specimens to investigate their effect on the microstructure and properties of the composite. A mixture of the powders with the composition 50wt.%W/50wt.%Cu has been prepared by dry mixing in a stainless steel container of a planetary mill using a ball to powder ratio of 1:1 at 200 rpm for 2 hrs. The mixture was then cold compacted using a single action hydraulic press at 400 MPa and then consolidated by vacuum sintering at 1100°C for 1 hr using the heating rate of 4˚C/min. Some samples were further processed by hot isostatic pressing “HIP” to enhance their characteristics. HIP was performed using the pressure of 200 MPa at both 1050 and 1150°C. The microstructure investigation was performed for the consolidated specimens by using scanning electron microscopy equipped with EDS analyses (JEOL JSM5410). Hardness was measured using Vickers hardness tester (Indentec 5030 SKV) at 3 kg load for 10 s. Table 1 gives a brief illustration of the conditions used to manufacture various samples in this study.Table 1. Various manufacturing conditions used in the study 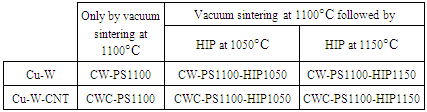 |
| |
|
3. Results and Discussion
Transmission electron microscope was used to investigate the morphology and particle size of both tungsten and copper powders. Both the tungsten and copper powders had an average particle size of slightly below 50 nm, as shown in Fig. 1(a) and (b). They both show almost perfectly spherical morphologies with considerable homogeneity of particle sizes, especially in case of Cu powder obtained by electroless deposition. The dry mixing process resulted in a mixture of powders without the formation of globules, as shown in Fig. 1(c), where there was not any sign of further particle size reduction. 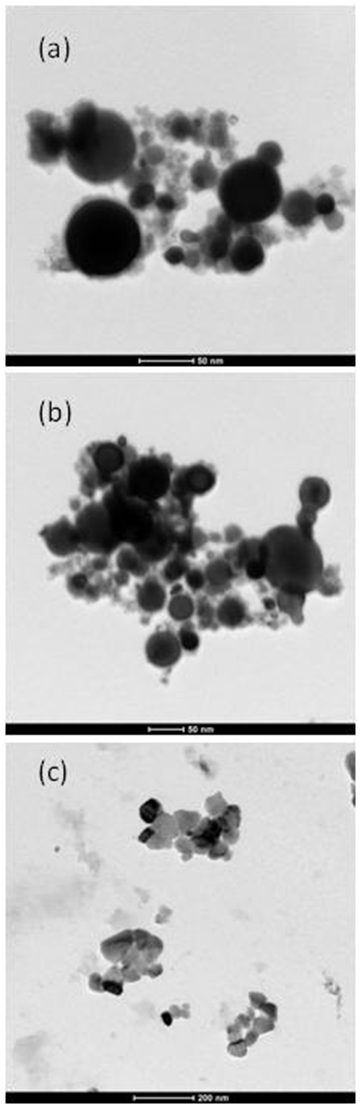 | Figure 1. TEM observation of W (a), Cu (b) and mixed (c) powders |
The microstructure of specimens manufactured by cold compaction of mixed nano powders and sintering in vacuum for 60 minutes at 1100°C, with and without further HIP processing, are shown in Fig. 2. The microstructure consisted of a homogeneous distribution of W-rich phase grains in a Cu-rich matrix. The size of the W grains has reached an average grain size of about 1 to 5 μm, larger than the starting particle size. The size could also be seen to increase in the case of HIP processing at 1150°C compared to that of 1050°C. Microvoids could be obviously found in the case of Cu-W specimens at all manufacturing conditions. However, the amount of those microvoids has been large in case of the specimen processed only by vacuum sintering, Fig. 2-a, and has been significantly reduced after HIP processing, Fig. 2-b and c. On the other hand, the specimens which contain Cu-W-CNT, Fig. 3-a-c, have shown much fewer void for mation compared to those of Cu-W specimens. This may be attributed to the affinity of CNTs to react with W and form carbides which does not leave the chance for W particles to form oxides rich with oxygen that boast void formation. Is can also be noticed that Cu-W-CNT specimens have shown considerably finer grain sized than those of Cu-W specimens as a direct result of limiting the growth of Cu-rich grains by the distributed CNTs. It is also worth mentioning that the CNTs could not be directly observed in the microstructure of the composite due to the limitation of SEM observation capabilities. Closer inspection of the microstructure by scanning electron microscopy equipped with EDS analysis revealed that the bright phase of W-rich grains contained considerable amount of dissolved Cu, as shown in Fig. 4. On the other hand, the Cu-rich phase contained much less amount of dissolved W. 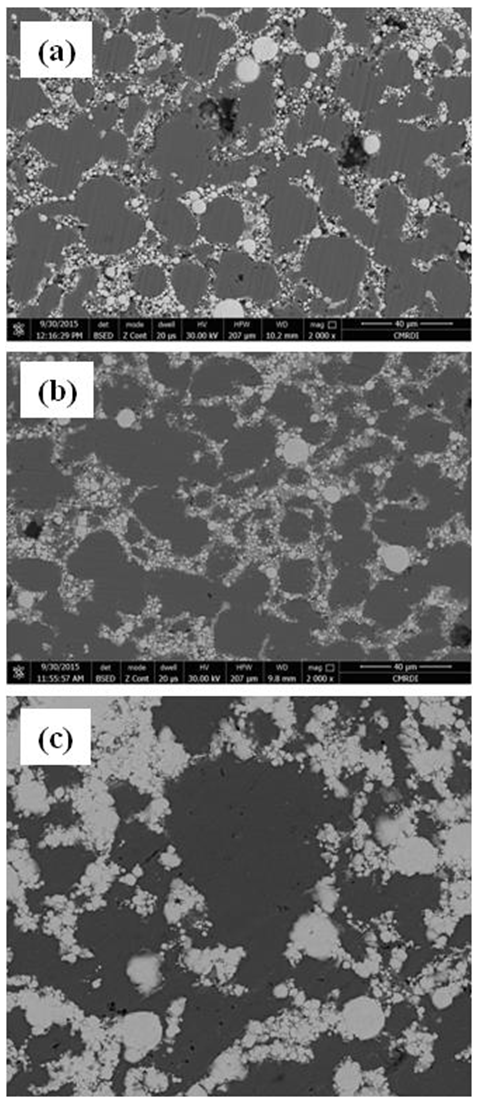 | Figure 2. SEM observation of Cu-W specimens CW-PS1100 (a), CW-PS1100-HIP1050 (b) and CW-PS1100-HIP1150 (c) |
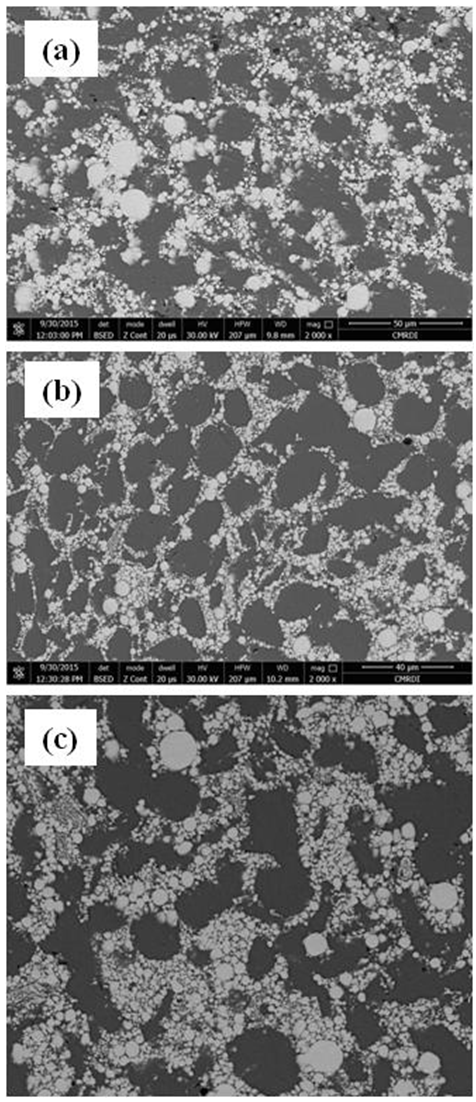 | Figure 3. SEM observation of Cu-W-CNT specimens CWC-PS1100 (a), CWC-PS1100-HIP1050 (b) and CWC-PS1100-HIP1150 (c) |
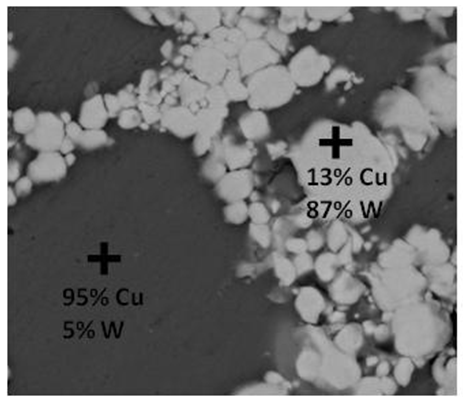 | Figure 4. EDS analysis of phase constituents in CW-PS1100-HIP1150 specimen |
The observation of microvoids coincides well to the measurements of relative densities of manufactured specimens obtained by Archimedes technique, shown in table 2. The maximum relative density could be obtained when manufacturing by vacuum sintering followed by HIP processing at 1150°C of Cu-W-CNT powders. The obvious reasons are the fewer amounts of voids and the enhanced densification by the high pressure during HIP processing.Table 2. Relative densities of specimens 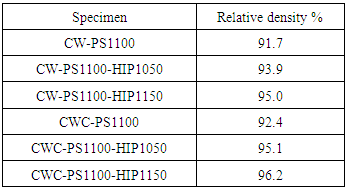 |
| |
|
4. Conclusions
This study presents a suitable method for fabricating W-Cu-CNT nano composites through vacuum sintering and HIP processing. The manufacturing route resulted in specimens which show good microstructure. The grain sizes, void amounts and relative densities have shown that HIP processing has played an important role in increasing the relative density especially for Cu-W-CNT specimens.
References
[1] | Ayman Elsayed, Wei Li, Omayma ElKady, Walid Daoush, Eugene Olevsky, Randall German. Experimental investigations on the synthesis of W–Cu nanocomposite through spark plasma sintering. Journal of Alloys and Compounds 639 (2015) 373–380. |
[2] | Hiraoka Y, Inoue T, Hanado H, et al, “Ductile-to-Brittle Transition Characteristics in W–Cu Composites with Increase of Cu Content”, Elsevier, Materials Transactions, vol. 46, no. 7, pp. 1663-1670, 2005. |
[3] | Hanado H, Hiraoka Y, “Localized Deformation Behavior of W-80vol%Cu Composite at Room Temperature”. Elsevier, Materials Transactions, vol. 48, no. 4, pp. 775-779, 2007. |
[4] | Ryu SS, Kim YD, Moon IH, “Dilatometric analysis on the sintering behavior of nanocrystalline W–Cu prepared by mechanical alloying”, Elsevier, Journal of Alloys and Compounds, vol. 335, no. 1-2, pp. 233-240, 2002. |
[5] | Amirjan M, Zangeneh-Madar K, Parvin N, “Evaluation of microstructure and contiguity of W/Cu composites prepared by coated tungsten powders”, Elsevier, International Journal of Refractory Metals and Hard Materials, vol. 27, no. 4, pp. 729-733, 2009. |
[6] | Yunping L, Yu S, “Thermal–mechanical process in producing high dispersed tungsten–copper composite powder”, Elsevier, International Journal of Refractory Metals and Hard Materials, vol. 26, pp. 540-548, 2008. |
[7] | Ibrahim A, Abdallah M, Mostafa SF, et al, “An experimental investigation on the W–Cu composites”, Elsevier, Materials and Design, vol. 30, pp. 1398-1403, 2009. |
[8] | Dongdong G, Shen Y, “Influence of Cu-liquid content on densification and microstructure of direct laser sintered submicron W–Cu/micron Cu powder mixture”, Elsevier, Materials Science and Engineering A, vol. 489, pp. 169-177, 2008. |
[9] | Franciné AC, Angelus GPS, Uilame UG, “The influence of the dispersion technique on the characteristics of the W–Cu powders and on the sintering behavior”, Elsevier, Powder Technology, vol. 134, no. 1-2, pp. 123-132, 2003. |
[10] | Kim JC, Moon IH, “Sintering of nanostructured W-Cu alloys prepared by mechanical alloying”, Elsevier, Nanostructured Materials, vol. 10, no. 2, pp. 283-290, 1998. |