Noel Deepak Shiri, Shreeranga Bhat, Babisha K. C., Krishna M. Moger, Minal Patricia D’almeida, Clyde Jofan Menezes
Department of Mechanical Engineering, St. Joseph Engineering College, Mangaluru, India
Correspondence to: Noel Deepak Shiri, Department of Mechanical Engineering, St. Joseph Engineering College, Mangaluru, India.
Email: |  |
Copyright © 2016 Scientific & Academic Publishing. All Rights Reserved.
This work is licensed under the Creative Commons Attribution International License (CC BY).
http://creativecommons.org/licenses/by/4.0/

Abstract
In this paper an attempt has been made to optimize the waste plastic-rubber composite materials using the Taguchi’s Design of Experiment Methodology. Moreover, an investigation has been carried to find out the effect of various parameters such as waste plastic mix, rubber powder, and filler materials (calcium carbonate and fly ash) on the compressive strength of the material. The main objective was to reutilize the waste plastics into developing plastic-rubber composite materials. In the present research, waste plastics have been blended with rubber powder, calcium carbonate, and fly ash in a plastic extruder. Then the melt was transferred into cube moulds, and rammed to form the specimens. Taguchi’s L9 orthogonal array has been utilized to perform the experiment, and to optimize the parameters. The samples have been subjected to compression tests on the Universal Testing Machine. The data obtained has been analyzed using MINITAB statistical software to draw the robust conclusion. SEM micrographs and Particle size analysis have been performed on the fly ash filler material. The results show that fly ash is a mixture of micro and nano sized particles with a wide range of particle sizes. Further, it is evident from the research that all the selected parameters like waste plastic, rubber powder, fly ash and calcium carbonate are having significant effect on the compressive strength of the material under study. The Analysis of Variance (ANOVA) revealed that waste plastic mix is the most influencing parameter for the compressive strength. Experimental results of compressive strength for optimum values of waste plastic-rubber composite material in comparison with clay brick revealed that it is 3 times stronger than the normal clay brick. These results indicate that waste plastic-rubber composite material could be used as low cost construction material and a cheaper substitute to clay bricks and various other building materials.
Keywords:
Waste plastics, Plastic/Rubber composite, Plastic Extruder, Compression Testing, Taguchi’s Technique
Cite this paper: Noel Deepak Shiri, Shreeranga Bhat, Babisha K. C., Krishna M. Moger, Minal Patricia D’almeida, Clyde Jofan Menezes, Taguchi Analysis on the Compressive Strength Behaviour of Waste Plastic-Rubber Composite Materials, American Journal of Materials Science, Vol. 6 No. 4A, 2016, pp. 88-93. doi: 10.5923/c.materials.201601.17.
1. Introduction
Plastic is one of the most commonly used materials in the modern era mainly due to its versatility and durability. It has also made life easier and better, but it is also very hazardous when not properly managed. Due to its non-biodegradable nature it gets accumulated in the environment and causes a lot of problems [1]. Plastics are generally lightweight, non-corrosive, soft, flexible, not easily damageable. And its high heat and electrical insulation features make plastics an indispensable packaging material. Also plastics rank first in the total amount of global waste produced. Four percent of the oil produced in the world is used in the production of plastics. Plastics are mostly used in packaging and construction industries. Polyethylene (PE), Polypropylene (PP), Polyethylene Terephthalate (PET), Polyvinyl Chloride (PVC) and Polystyrene (PS) are the main types of plastics [2]. Waste plastics can be used for production of construction materials like building blocks, roof and floor tiles and also for bridge construction materials. This in turn optimises the problem of waste material storage and the high cost of building materials. The waste plastics are incorporated with sand and other additives to form the construction materials [3]. Plastic waste recycled in India is in an unorganized method and 60% of the plastic-waste collected and segregated gets recycled back into materials for further processing into consumer products, while the balance is left unutilized and it is a source of hazard to environment. Plastics account for 16% of chlorine in the environment and have 54 carcinogens. Polythene bags for disposal if burnt irresponsibly releases highly toxic gases like phosgene, carbon monoxide, chlorine, sulphur dioxide, nitrogen oxide, besides deadly dioxin. Polymer materials are steadily replacing natural materials like metal, timber and fibres and thus conserving the natural environment [4]. Using a waste plastic extruder, the method for effectively converting waste plastics into building materials like bricks and interlocks have been studied and the plastic brick obtained was shown to have a compressive strength 2 times that of a traditional clay brick. The maximum compressive load sustained by the polypropylene-rubber composite brick was found to be 17.06 tons whereas a clay brick sustained only 9.03 tons. Bricks made from waste plastic sustain a higher load and compressive strength compared to normal clay brick [5]. The waste tire rubber powder is strongly compressible and has very low density of about 0.83, therefore is used in a variety of civil and non-civil engineering applications [6].Design of experiments (DOE) is a powerful tool that can be used in a variety of experimental situations. DOE allows for multiple input factors to be manipulated determining their effect on a desired output response. Thus, DOE can identify important interactions that may be missed when experimenting with one factor at a time. By applying the Taguchi’s Technique it is possible for us to significantly reduce the time required for experimental investigations. It is one of the most widely used powerful tools in DOE [7]. Taguchi’s Method has been fruitfully used around the planet for many manufacturing and research based applications like Heat Treatment and Abrasive Wear [8], damping characteristics [9] and many other applications etc. The Taguchi method uses Signal-to-Noise Ratio (S-N Ratio) as the quality characteristic. The S-N ratio for larger is better characteristic is as shown in the equation below:“Larger is Better” characteristic: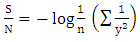 | (1) |
Where y is the average of observed data,
the variation of y, n the number of observations,and y the observed data or each type of the characteristics, with the above S-N ratio transformation [10]. The present research has been planned to investigate the effect of parameters like waste plastic mix, rubber powder, calcium carbonate and fly ash on the compressive strength of the waste plastic-rubber composite material using Taguchi’s Statistical Technique.
2. Experimental Investigation
2.1. Materials
The materials used for developing waste plastic-rubber composite materials are as follows: the matrix materials selected for this work is shredded waste plastics like Polypropylene (PP), High Density Poly-Ethylene (HDPE) and Low Density Poly-Ethylene (LDPE) and their percentage mix is shown in the table 1. Table 1. Plastic Mix Proportions 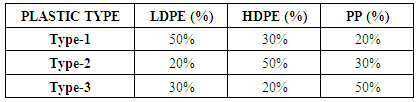 |
| |
|
The reinforcing material used are waste rubber powder from used automobile tyres, and additives like calcium carbonate and filler materials like fly ash which is waste produced by burning coal in thermal power plants, and it was procured from Udupi Power Corporation Limited (UPCL), Padubidri, Udupi District, Karnataka State.The composites were prepared by mixing the waste plastics LDPE, HDPE and PP along with rubber powder, calcium carbonate and fly ash in a vessel and stirred so that proper mixing is finished. The band heater temperature of the waste plastic extruder is preset to around 250°C. The mixture is then slowly poured into the hopper of the plastic extruder. Waste plastics from the hopper travels further in the extruder screw and gets melted and conveyed towards the nozzle of the extruder and a uniform blended mix of the composite which comes out in the form of a semi solid paste which is then transferred into steel cube moulds of 50.8 mm x 50.8 mm size to produce cube specimens as directed in ASTM C 579 standard. Then the composite material mix is rammed to remove any air pockets present in the mix and to form a dense specimen. Later the steel cube moulds along with the specimens is submerged in a water bath for uniform cooling and cured for a day. After the cooling the specimens are removed from the moulds.
2.2. Taguchi Experimental Array Design
In this present work four factors at three levels were selected. The four parameters or Factors selected are (1) Waste Plastic Mix Type, (2) Rubber powder, (3) Calcium Carbonate and (4) Fly ash. The three levels for each of the four variables selected are shown in Table 2.Table 2. Parameters for 4 Factors and 3 Levels 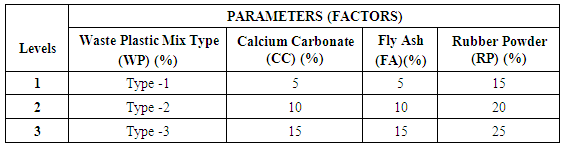 |
| |
|
In conventional method of experimental study, the measurements for Compressive strength as a function of four factors and three levels each would require (level)factors = 34 or 81 experiments along with 3 replications for all the combinations of parameters. Similar results can be obtained by using Taguchi’s L9 orthogonal array experiments by only performing 9 experiments along with 3 replications for each experimental run.
2.3. Experimental Setup for Compression Test
The Compressive Strength test was performed on different waste plastic-rubber composite materials using the Universal Testing Machine (UTM). The cube specimens were prepared according to the ASTM C 579 standard and the specimens were placed in between the top and bottom compression pads of the UTM and then loaded uniformly at a load rate of 5 mm/minute.
3. Results and Discussions
3.1. Microstructure and Particle Size Analysis
SEM image of the Fly Ash particles shows that in fly ash the proportion of small sized particles is higher and the proportion of larger sized particles is only a few. Fly ash used in the study is a combination of various sizes ranging from macro, micro to nano size range of flyash particles. Micro sized particles of fly ash are having size ranging from 5 µm to 50 µm. Also the agglomeration of the fly ash particles can be seen in figure 1 with the small sized nano fly ash particles. Fly ash is mainly used as a particulate filler material and the addition of this can improve the Ultraviolet resistance properties and the performance of the material developed (As reported by Wahid Ferdous et al [11]).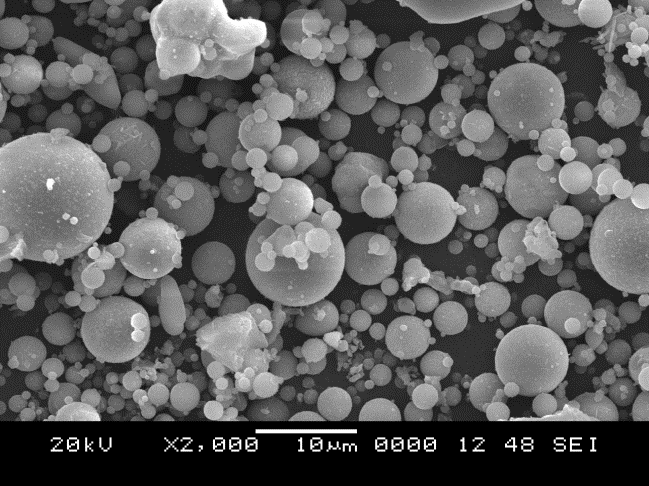 | Figure 1. SEM image of Fly Ash particles at 2000x Magnification |
The particle size analysis of fly ash nano particles revealed the presence of a wide variety of fly ash particles varying in their sizes as represented in Figure 2. The apparent majority size of the fly ash nano particles in the sample was determined to be in the range of 1380-1389 nm.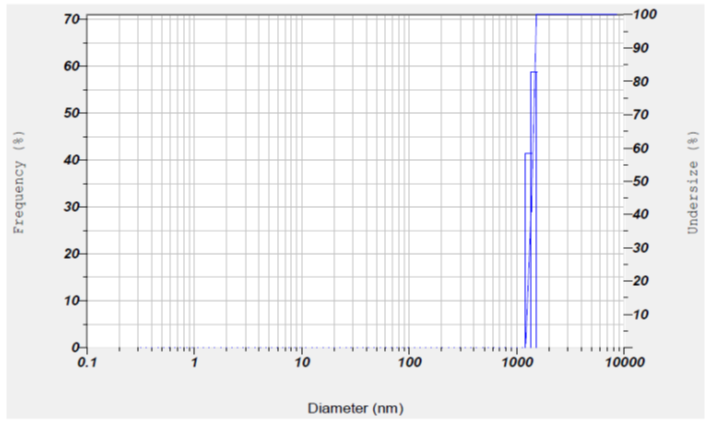 | Figure 2. Frequency vs Diameter of Particle size distribution of the fly ash nano particles |
The fly ash added as filler aided in modifying the compressive strength properties of the final treated waste plastic in a uniform manner, taking into account that the homogeneity of the additives directly influences the compressive strength of the final composite material. It was also observed that the increase of filler material resulted in the increase of the darkness of samples as the fly ash itself is grey in colour and the rubber powder is black. The colour of the final specimen is an indicative of how well the shredded plastics have mixed with the reinforcing, additive and filler materials. The colour is also a visual indicative of how well the plastic is mixed with additives and reinforcing materials.
3.2. Statistical Analysis for Compressive Strength using Taguchi Method
The results of Compression test conducted according to the Taguchi’s L9 Orthogonal Array for various combinations of parameters given in Table 3. The statistical software package MINITAB Release 14 was used to analyze the results of the orthogonal array experiments, depending on the number of factors and their levels. Here the S-N Ratio of “Larger is Better” is selected for Compressive Strength, since in this case the purpose was to get the highest Compressive Strength values. Hence, the expression for the S-N Ratio in equation (1) was used for analysis. Investigating from the Main Effects Plot for S-N Ratio shown in figure 3 we can concluded that for Compressive Strength for the factors with the largest effect appears to be Waste Plastic Mix Type followed by Calcium Carbonate, Flyash and Rubber Powder. The optimal combination predicted for various parameters from figure 3 are Waste Plastic Mix Type = Type-3, Calcium Carbonate = 10 %, Fly Ash = 5% and Rubber Powder = 15%.Table 3. L9 orthogonal array for Compressive Strength 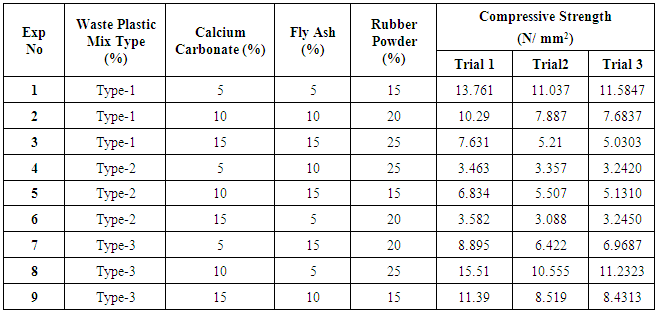 |
| |
|
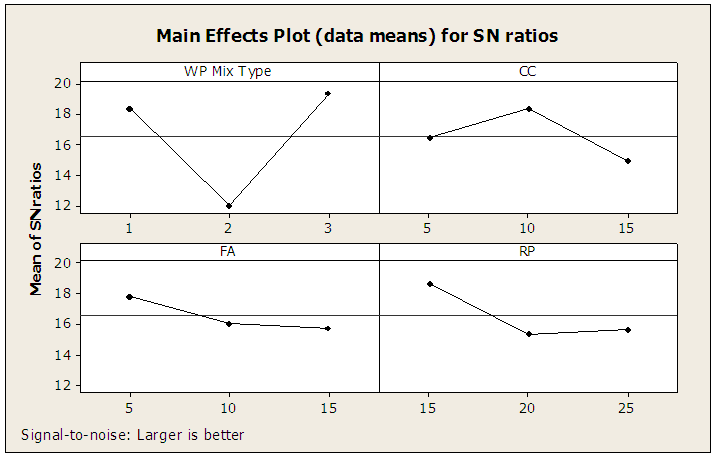 | Figure 3. Effect of Control Factors on Compressive Strength (S-N ratio) |
Analysis of Variance (ANOVA) was used to investigate which design parameter significantly affects the Compressive Strength characteristic. The analysis was carried out at 95% confidence level. The Table 4 shows the summary of ANOVA for Compressive Strength and column 8 of the table 4 indicates the percentage contribution (%) of each individual factors. From the table it can be seen that the factor Waste Plastic Mix Type has the highest significance (52.96%) followed by the Fly Ash (13.05%), Rubber Powder (11.01%) and Calcium Carbonate (10.78%). Also the ‘P’ value for any source which is less than 0.05, indicates that all the selected factors had their significant effect on Compressive strength. Table 4. Analysis of Variance (ANOVA) for Compressive Strength 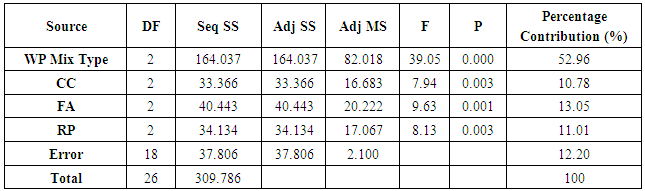 |
| |
|
By using Regression Analysis, Compressive strength was predicted, which can be further compared with the experimental result for the same set of conditions. The regression equation obtained is:- | (2) |
Where WP, CC, FA and RP indicate Waste Plastic Mix Type, Calcium Carbonate, Fly Ash and Rubber Powder respectively. By substituting the Predicted Optimum factor levels in the Regression Equation the predictable optimum value of Compressive strength is 10.437 N/mm2. Additional validation experiments were conducted for the predicted optimum conditions. Compressive strength from the validation experiments was obtained as 10.97 N/mm2. The Percentage Error was also calculated and found to be 4.85% confirming the success of Taguchi statistical analysis.
3.3. Comparing the Compressive Strengths of Waste Plastic-Rubber Composite Material with Traditional Clay Brick
From the experimental results obtained for optimum value predicted by the S-N ratio plot revealed that the compression strength of Waste Plastic-Rubber Composite material is 10.97 N/mm2 and for the normal fired Clay Brick the compressive strength was obtained as 3.64 N/mm2. From this result we come to know that the waste plastic-rubber composite material is 3 times stronger than the normal fired clay brick. 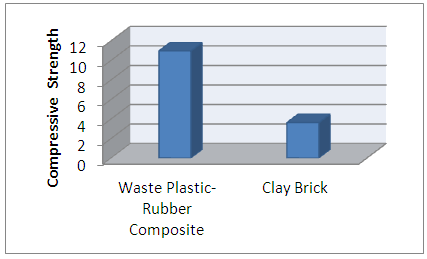 | Figure 4. Comparison of Compressive Strength for Waste Plastic-Rubber Composite material and fired Clay Brick |
These results imply that the waste plastic-rubber composite material could be used as a cheaper alternative to clay bricks and various other building materials in construction like bricks, interlocks, floor tiles and roof tiles etc. Also the waste-plastic rubber composite has the following essential feature like the material is durable, water proof and not vulnerable to insect infestation and it does not decompose and has Low Carbon Footprint while manufacturing the material and finally the material is 100% recyclable.
4. Conclusions
The following conclusions were drawn from this study:1) Taguchi’s method of L9 orthogonal array experimentation is successfully used to analyze the material parameters for the waste plastic-rubber composite material.2) The results have shown that all the selected parameters like waste plastic mix, rubber powder, fly ash and calcium carbonate are highly contributing.3) Effect of Waste plastic mix was very highly significant in determining the Compressive strength property of the material.4) ANOVA table revealed that all the selected factors had their significant effect on Compressive strength.5) Experimental results of compressive strength for optimum value of waste plastic-rubber composite material revealed that it is 3 times stronger in comparison with normal fired clay brick. 6) The comparison results indicate that waste plastic-rubber composite material can be used as low cost construction material which could be used as a cheaper substitute to clay bricks, interlocks, Roof tiles, floor tiles and various other building materials. 7) The developed waste plastic-rubber composite material is strong, water proof and is not vulnerable to insect infestation and it does not decompose with time and it has low carbon footprint during the manufacturing process and finally this material can be 100% recyclable. 8) Mainly the waste plastics which generally end up in landfill can be diverted and recycled to produce waste plastic-rubber composite materials for development of low cost different types of construction materials.
ACKNOWLEDGEMENTS
The authors would like to thank Mr P. Varun Kajava, Mr Ranjan H. V, Mr Nikhil Lloyd Pais, Mr Vikhyat M. Naik, Alumni's of St Joseph Engineering College for developing a award winning Waste Plastic Extruder which was very much helpful for this research work. We are extremely grateful to Mr Robinson Furtado, Mr Babu Jeevarathna and Mr Sunil Frank of Hebich Technical Training Institute, Balmatta, Mangaluru for the useful interactions. We are and extremely indebted to Mr Fayaz Ali and Mr Abdul Rasheed, Fauziya Plastics, Baikampady Industrial Area, Mangaluru for supplying us with the useful raw materials for the research work and sincere thanks to Mr Ashok, Technical Manager, Gurucharan Industries, Baikampady Industrial Area, Mangaluru for the useful interactions. We would like to thank Chrisage Engineering Company, Baikampady Industrial Area, Mangaluru for fabricating the steel moulds. We thank Ms Pooja Nanda, Chemical Engineering Department, NITK for her help in SEM and Particle Size Analysis. We are extremely thankful to Dr Joseph Gonsalvis, Principal, St Joseph Engineering College, Mangaluru for his invaluable suggestions and comments that gave us direction for the success and completion of this research work.
References
[1] | Anslem E. O. Eneh, “Application of Recycled Plastics and Its Components in the Built Environment”, BEST: International Journal of Management, Information Technology and Engineering (BEST: IJMITE), ISSN 2348-0513, Vol. 3, Issue 3, Mar 2015, pp. 9-16. |
[2] | Semiha Akçaözoğlu, “Evaluation of waste plastics as recycled plastic composite materials”, Edorium Journal of Waste Management, 2015; Vol. 1, pp. 16–19. |
[3] | Siti Aishah Wahid, Sullyfaizura Mohd Rawi, Norlia Md Desa, “Utilization of Plastic Bottle Waste in Sand Bricks” , Journal of Basic and Applied Scientific Research, ISSN 2090-4304, , Vol. 5(1), 2015, pp. 35-44. |
[4] | Dr. Pawan Sikka, "Plastic Waste Management In India", Department of Science & Technology, Government of India New Delhi, India, pp. 1 - 4. |
[5] | Noel Deepak Shiri, P. Varun Kajava, Ranjan H. V., Nikhil Lloyd Pais, Vikhyat M. Naik, "Processing of Waste Plastics into Building Materials Using a Plastic Extruder and Compression Testing of Plastic Bricks", Journal of Mechanical Engineering and Automation, 2015, Vol.5(3B), pp. 39 - 42. |
[6] | Melik Bekhiti, Habib Trouzine, Aissa Asroun, “Properties of Waste Tire Rubber Powder”, Engineering, Technology & Applied Science Research, Vol. 4, No. 4, 2014, pp. 669-672. |
[7] | Philip J. Ross, “Taguchi Techniques for Quality Engineering”, Second Edition, 1996, McGraw-Hill, New York, USA. |
[8] | Noel Deepak Shiri, Thirumaleshwara Bhat, Shreeranga Bhat, Girish Kumar, "Effect of Heat Treatment Variables on the Abrasive Wear Behaviour of Al-6061 Alloy and Al 6061-SiCP Composites Using Taguchi Technique", American Journal Of Materials Science, 2015, Vol.5(3C), pp. 151-156. |
[9] | Raman Bedi, Renu Sharma, "Damping studies on fibre-reinforced epoxy polymer concrete using Taguchi design of experiments", International Journal of Materials Engineering Innovation, Vol.6, No.1, 2015, pp. 42 - 48. |
[10] | Raviraj Shetty, Raghuvir B. Pai, Shrikanth S. Rao, Rajesh Nayak, “Taguchi’s Technique in Machining of Metal Matrix Composites”, Journal of the Brazilian Society of Mechanical Sciences and Engineering, January-March 2009, Vol. XXXI, No.1, pp. 12-20. |
[11] | Wahid Ferdous, Allan Manalo, Thiru Aravinthan, Gerard Van Erp, “Design of epoxy resin based polymer concrete matrix for composite railway sleeper”, 23rd Australasian Conference on the Mechanics of Structures and Materials (ACMSM23), vol. I, Byron Bay, NSW, 9-12 December, Southern Cross University, Lismore, NSW, ISBN: 9780994152008, pp. 137-142. |