Chinthankumar D. M.1, Jathin K. J.1, Manujesh B. J.1, Umashankar K. S.1, Prajna M. R.2
1Department of Mechanical Engineering KVGCE, Sullia, D.K, Karnataka, India
2Department of Computer Science & Engineering, KVGCE, Sullia, D.K, Karnataka, India
Correspondence to: Manujesh B. J., Department of Mechanical Engineering KVGCE, Sullia, D.K, Karnataka, India.
Email: |  |
Copyright © 2016 Scientific & Academic Publishing. All Rights Reserved.
This work is licensed under the Creative Commons Attribution International License (CC BY).
http://creativecommons.org/licenses/by/4.0/

Abstract
The paper aims at the synthesis and characterization of high density rigid Polyurethane Foams (PUF’s). Five varied density PUF’s viz., (300,350,450,650 and 850kg/m3) have been synthesized at lab standards. Effects of PUF density on the flexural, edgewise and flat wise compressive strength of the rigid polyurethane foams have been investigated. Experimental results indicate that the bending strength increases with increasing density and deformation decreased with the increase in density. The study reveals 43.67% increase in the flexural and 34.26% improvement in the flat wise compression strength of the PUF’s. The edgewise compression strength is found to be unaffected, as most of the foams were weak along the transverse direction. It is concluded that the most of the physical properties of PUF’s affected with the density variation.
Keywords:
Polyurethane foams, Flexural, Flat wise, Edge wise
Cite this paper: Chinthankumar D. M., Jathin K. J., Manujesh B. J., Umashankar K. S., Prajna M. R., Synthesis and Experimental Investigation of Density on the Structural Properties of Rigid Polyurethane Foams, American Journal of Materials Science, Vol. 6 No. 4A, 2016, pp. 77-81. doi: 10.5923/c.materials.201601.15.
1. Introduction
Polymer foams are in immense demand due to their versatile properties like ultra light weight with moldabilty [1, 2]. The polyurethane foam was invented by Dr. Otto Bayer at the start of the World War II. It was first used as a replacement for rubber and also used as a coating to protect other common materials such as metals and wood and few years later, the flexible polyurethane foam was invented and sought to be used for cushioning in furniture and automotive industries. Polymer foams were found virtually everywhere in our modern world and were used in wide variety of applications such as disposable packaging of fast-food, cushioning and insulation. The reason polymer foams were widely used was that they have a lot of advantageous like lower density and the weight reduction compared to other options. Some polymer foams have very low heat transfer, making them optimal insulators. Many are flexible and soft and more comfort when used for furniture and bedding [3]. The amount of pores in the foam structure affects many of its properties. When there are more and smaller pores the foam is a much better mechanical and insulating properties. Increased number of pores generates tortuous the path, and thus there is less chance of the heat transfer happening effectively. In this case, the gas phase is more dominant in determining the foam properties than the actual polymer. The mechanical response of the foam is also dictated by the structure. The size of the cell also affects the properties of the foam. Foams with smaller cells are better at energy absorption. At smaller cell sizes the amount of open-cell structure also decreases. Mechanical behavior of the PU foams since gas has the least mechanical strength, more the trapped gas less is the strength of the foam which means the lower density foams exhibit the smallest Young's modulus. Even if the cells of the foam have varying shape, there is usually some anisotropy to the foam because of the direction it is being formed at. The strength is better along the direction of foaming. If the ratio of the height to width of the cell is increased by a certain amount, the compressive strength and the tensile strength of the foam also found to increase by the same amount. So the geometry of the cells could have more to say for the strength than density. The open-cell structures have the disadvantage of lower mechanical properties, but showed much better at sound deadening. The reason could be, the open-cell structure affects the modulus of the foam and must be taken into account when calculating the modulus. The polyurethane (PU) rigid foams are commonly used for insulation purposes because they have better thermal properties than do thermoplastic foams or other common insulation materials [4-6]. With growing concern for energy conservation, there is a strong incentive to improve the insulation property of rigid foams. This can be done by making foams with smaller cell sizes [7, 8]. Rigid PU foams are extensively used as core material in many sandwich constructions [9]. This paper aims to evaluate some of the important properties of the rigid PU foam by manually synthesizing different density PU foams using appropriate volumes of chemicals. The flexural and compression strength (Flatwise & Edgewise) has been conducted and the results have been reviewed and reported.
2. Materials and Methods
2.1. Materials
2.1.1. Polyurethane Foam Components
There are two main components necessary for the formation of polyurethane foam, namely Polyol and diphenylmethane diisocyanate (MDI). The raw material used for the production of polyurethane foam diphenylmethane diisocyanate (MDI) and Polyol was obtained from Polynate Foams Pvt. Ltd, Bangalore, Karnataka state. The chemicals used in the study are as shown in Figure 1. 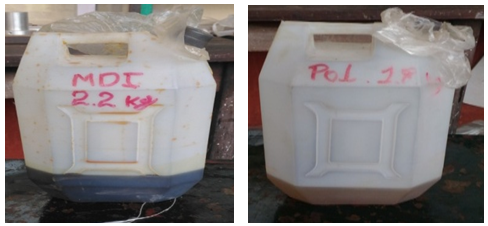 | Figure 1. The Chemicals used for the synthesis of PU Foams |
2.1.2. Mold Box
The mold was prepared by using M.S. A regular section with 300 x 300 x 25mm was formed by welding. The suitable arrangements were incorporated to evacuate the trapped air from the mold cavity. The measures also have been considered to withstand the pressure built-up during the foaming process. The internal mould surface was covered with Teflon sheets prior to the foam formation. The typical M.S mould used to synthesize the variety of foams has been shown in the Figure 2. 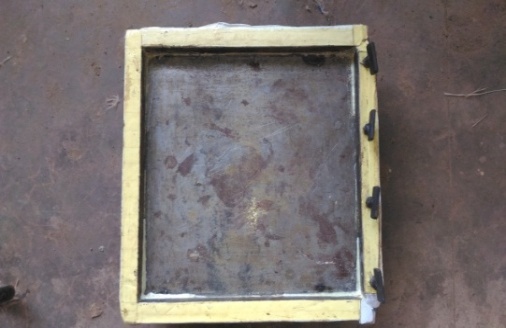 | Figure 2. The Mould Used to Fabricate PUF’s |
2.2. Procedure for the Foam Production
The desired amount of chemicals referring to the density of formation i.e., MDI & Polyol was mixed with MDI (Part A) using a stirrer. Then, the contents Polyol (Part B) was added and stirred or mixed for about 10 to 20 seconds. The composition was then poured rapidly into the mold space and then the mold box is closed with the help of G-clamp such that to avoid the air gaps on the mating surfaces of mold box. The compositions undergo exothermic reaction to form foaming approximately 10-30 seconds after pouring. The mold was allowed to cure at room temperature for about 1 hour and then opened. The Figure 3 shows the mold used to synthesize the variety of PUF’s. 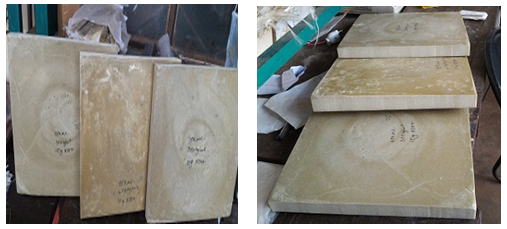 | Figure 3. Produced PU Foam Blocks |
2.3. Methodology Adopted
The test samples were prepared and characterized in accordance with ASTM C 393/C 393M- 06 and C365/C 365M-05 respectively. The flexural tests conducted using Universal testing machine (ZWICK/ROELL Z020 20KN) with the test speed of 6 mm/min. The specimen used to conduct the flexural test is as shown in the Figure 4.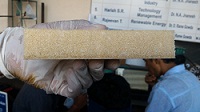 | Figure 4. Specimen for Flexural Test |
The specimen used to conduct the flexural test is as shown in the Figure 5.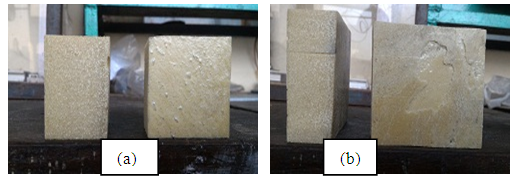 | Figure 5. (a) Specimen for Flat Wise Compression (b) Specimen for Edge Wise Compression Test |
3. Results and Discussions
A novel methodology for the development of PU foam and their characterization was carried out successfully.
3.1. Flexural Test
The bending strength, deflection due to the loads and stress values obtained are used to study the behavior of the PUF specimens. Load V/s deflection data was obtained from the flexural tests is shown in Figure 6. Comparison study of typical load-deflection curves for various 5 densities of rigid PU foams ((300,350,450,650and850) kg/m3), subjected to flexural load is studied. It is observed that flexural property of the 300 kg/m3 foam was minimum i.e., 14% less than PUR 350 kg/m3. Further it is observed that 450 kg/m3 PUR resulted in between 26% than 300 kg/m3. And the PUR foam densities of 650 kg/m3 & 850 kg/m3 showed 33% and 41% from their predecessor densities. It is affirmed as the density increased the flexural strength. Many researchers lime S.C Sharma et al [10] observed that the flexural strength increases due to the increase density of foam. The wall thickness shows the poor performance. It was also reported by RV Rao et al [11] flexural strength of 300 kg/m3 PUR revealed to be 1.63MPa in their work with PUR foams with varying skins types for varieties of sandwich composites. In the present work with PUR foam densities, 300 kg/m3 exhibited minimum flexural strength where as 850 kg/m3 density PUR showed Maximum stress 2.64MPa. Thus it can be confirmed that the as the density of the PUF’s increased the flexural strength also improved. The reason can be closely formed close rigid cells. The Figure 7 shows the fractured specimens under flexural strength test. It is clear from the fractured specimen that lower density foams undergo severe bending before the fracture but the higher density foams suffered with cell shear and cell wall crushing before the complete rupture.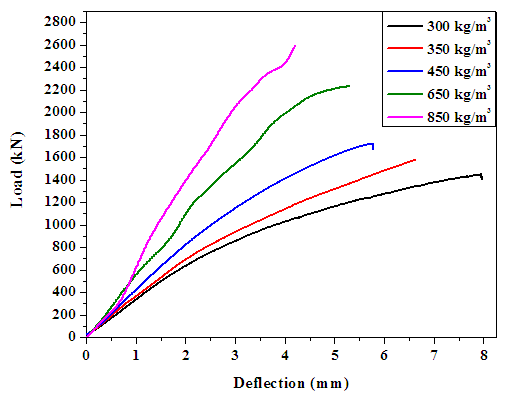 | Figure 6. Flexural Load v/s Foam trends |
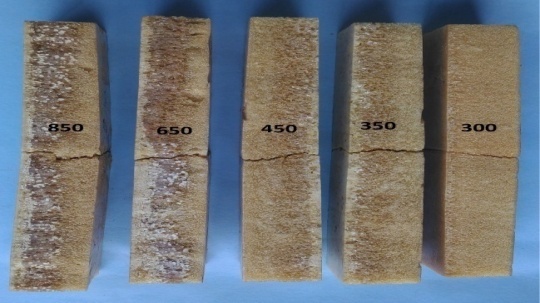 | Figure 7. Specimens after Applying Flexural Testing |
3.2. Flat Wise Compression Test
The compression test has been carried out in a computerized universal testing machine (ZWICK/ROELL Z020 20KN), at a cross head speed of 2mm/min. the compression strength, deflection, variation in the stress value is shown in the Figure 8. The load v/s deflection data obtained features similar trend with all the variety of PUF’s.A comparisons of typical load-deflection curves for various 5 densities of rigid Polyurethane foams (300,350,450,650 and 850 kg/m3), subjected to flat wise compression load is studied. PU Foam density described an initial elastic region up to initial failure, as the compression increases failure of the elastic region take place, next region featured with progressive deformation by forming a stress plateau, finally densification was observed followed by longitudinal and transverse cracks on the foam specimens. It is observed that the stress plateau in case of 300 kg/m3 is 62% of the total elapsed curve, 350 kg/m3 with 57%, 450 kg/m3 with 47%, 650 kg/m3 with 37%, similarly 850 kg/m3 27%. Therefore maximum stress plateau is 300 kg/m3 density foam. It is believed that lower density foams shows maximum deformation. Minimum stress plateau is 850 kg/m3 density foam. Gibson and Ashby [12] is an explained on flexible PUR. The cell size of foam decreases because the density of foam increases, which means large number of the solid formed to the foam. Brenzy and Green [13] in an explained about cellular carbon foam of their mechanical behavior, smaller strain formed by faster densification of higher density of the foam this effect a shortening of the stress plateau. 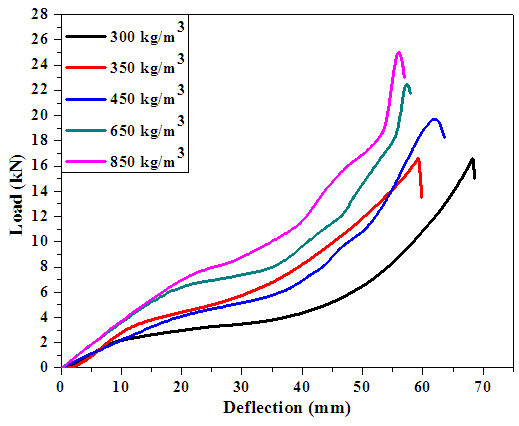 | Figure 8. Difference in Flat wise Compression Load v/s Deflection |
The Figure 9 shows the post test flat wise compressed test specimens. It was observed that lower density foams undergo huge elongation, because of the density factor.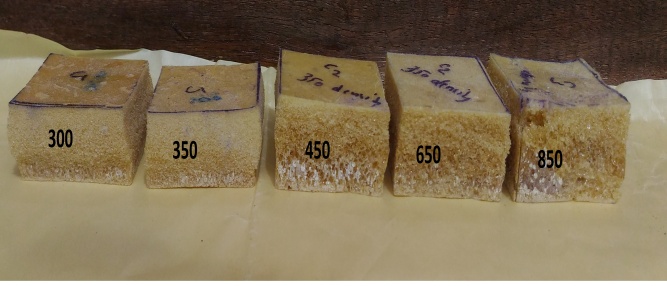 | Figure 9. Specimens after Applying Flat Wise Compression Load |
3.3. Edgewise Compression Test
Edge Compression test has been carried out according to ASTM C365 standards. The edge wise compression test has been carried using computerized universal testing machine at a cross head speed of 2mm per minute. Compression strength, deflection in load, stress value is obtained in the edge wise compression test method. Load-deflection data was obtained from the compression tests is shown in Figure 10. A comparisons of typical load-deflection curves for five densities of rigid PUR foams (300,350,450,650 and 850 kg/m3), subjected to edge wise compression load is studied. The PU foam density described an initial elastic region up to initial failure, as the compression increases failure of the elastic region take place, next region progressed by stress plateau, finally densification region formed. 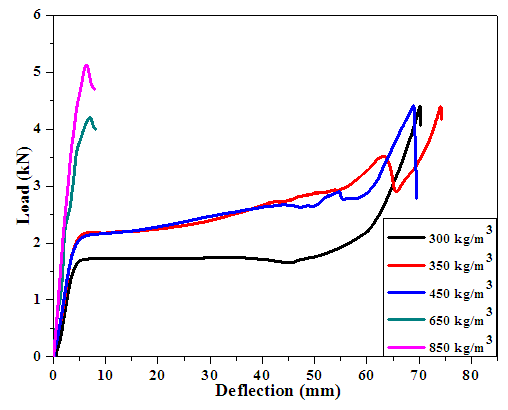 | Figure 10. Difference in Edge Wise Compression Load V/S Deflection |
The stress plateaus in the case of foam are 300 kg/m3 (81%), 350 kg/m3 (72%), 450 kg/m3 (68%), 650 kg/m3 (57%), similarly 850 kg/m3 (33%). Therefore maximum stress plateau is 300 kg/m3 density foam.It is believed that smaller density foam will gives larger deformation.Minimum stress plateau is 850 kg/m3 density foam. Gibson and Ashby [12] explained few contexts of PUF’s taking density as one of the criterion. As the density of the foams increased the foams cells size decreased, which means more solid walls restraining the compressive load.Brenzy and Green [13] explained about the cellular carbon foam of their mechanical behavior, smaller strain formed by faster densification of higher density foams affected through the formation of the plateau. Figure 11 shows the edge wise compressed test specimens. i.e., (300kg/m3) compressed largely because its lower density factor with the wider array of cells, but high density of the foams (850 kg/m3) possesses increased number of cells in a limited space contribute to the higher load carrying capacity. 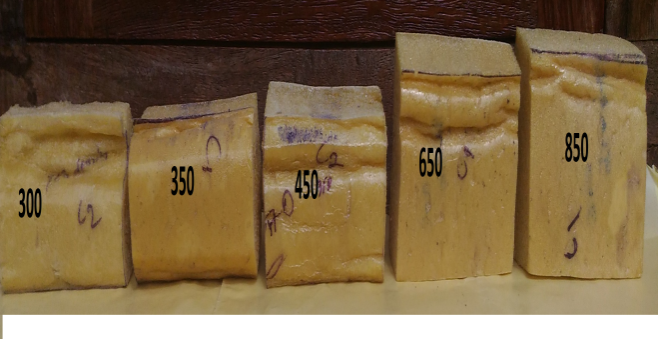 | Figure 11. Edge Compressed Specimens |
4. Conclusions
The synthesis and characterization of PU foam with varying density is carried out successfully and the following results were drawn.This work shows the successful fabrication of different densities of polyurethane foam of varied densities.The PUF’s density of 850 kg/m3 has the maximum flexural strength and 300 kg/m3 foam has the minimum flexural strength. This shows that as the density increased the cell wall thickens increased thus increasing the bending strength.The PU foam (850 kg/m3) has the maximum compressive strength and PUF 300 kg/m3 has the minimum compressive strength. This shows that as the density increased, decreasing the cell size, which means more solid walls restraining the compressive load.
References
[1] | Ashida, K. Polyurethane and Related Foams, Taylor and Francis, 2007. |
[2] | Klempner, D., Sendijarevic, V. Polymeric foams and Foam Technology, 2nd.ed., Hanser, 2004. |
[3] | Lee, S.T., Park, C.B., Ramesh, N.S., Polymer foams, Taylor and Francis, 2007. |
[4] | Khemani, K.C., Polymeric foams, American Chemical Society, 1996. |
[5] | Throne, J., Thermoplastic Foam Extrusion, Hanser, 2004. |
[6] | Gendron, R., Thermoplastic Foam Processing, CRCPress, 2005. |
[7] | F.C. Campbell, Lightweight, Material—Understanding the Basics, Copyright © 2012 ASM International. |
[8] | Katrine Sivertsen. Polymer Foams, 3.063 Polymer Physics. Spring 2007. |
[9] | R. Gayathri. Studies on polyurethane and its hybrid foams with micro and nano fillers for low frequency sound absorption. A thesis, August 2013. |
[10] | S.C. Sharma, M. Krishna, H.N. Narasimha Murthy, M. Sathyamoorthy, and Debes Bhattacharya. Fatigue Studies of Polyurethane Sandwich Structure. |
[11] | RV Rao, BJ Manujesh, and Behavior of sandwich composites under flexural and fatigue loading: Effect of variation of core density, International Journal of Engineering Science and Technology 3 (10). |
[12] | Gibson L J, Ashby M F, Cellular solids – structure and properties. Cambridge, United Kingdom: Cambridge University Press; 1997. |
[13] | Brenzy R, Green DJ. The effect of cell size on the mechanical behavior of cellular materials. Acta Metall Mater 1990; 38(12): 2517–26. |