Poornesh M.1, Harish N.2, Kiran Aithal2
1Department of Mechanical Engineering, St Joseph Engineering College, Mangaluru, India
2Department of Mechanical Engineering, Nitte Meenakshi Institute of Technology, Bengaluru, India
Correspondence to: Poornesh M., Department of Mechanical Engineering, St Joseph Engineering College, Mangaluru, India.
Email: |  |
Copyright © 2016 Scientific & Academic Publishing. All Rights Reserved.
This work is licensed under the Creative Commons Attribution International License (CC BY).
http://creativecommons.org/licenses/by/4.0/

Abstract
In the present paper, an effort has been made to study about the mechanical properties of composites prepared using Al-18wt%Si as the base metal. The base metal was reinforced with using SiC particles having an average size of 60μm. The composite was produced using a combination of bottom pouring stir cast machine and a horizontally rotating centrifugal casting machine. The prepared samples of the composite was checked for various mechanical properties like hardness, tensile strength, toughness etc and the results obtained where then compared with the mechanical properties of alloy cast under the same conditions. It was hence found that, the addition of SiC reinforcing particles have increased the mechanical properties of the alloy to a greater extent but has reduced its toughness.
Keywords:
Aluminiun, Mechanical Properties, Stir Casting, SiC
Cite this paper: Poornesh M., Harish N., Kiran Aithal, Study of Mechanical Properties of Aluminium Alloy Composites, American Journal of Materials Science, Vol. 6 No. 4A, 2016, pp. 72-76. doi: 10.5923/c.materials.201601.14.
1. Introduction
Aluminium has a density one third the density of steel. Even though they have lower tensile properties when compared to steel their strength to weight ratio is exceptional [1]. It is easy to produce aluminium because of their good thermal and electrical conductivity and they do not exhibit a transition from ductile to brittle phase at low temperatures. They can be recycled as they are nontoxic and require less energy for doing so. Nevertheless, they do not show a true endurance limit so even at low stresses fatigue failure may occur. On the other hand aluminium alloys are favourable as structural materials because of their high specific strength and stiffness. Due to this they are being used in automobile industries as basic constituents of internal combustion engines like cylinder blocks, cylinder heads and pistons [2]. The Al-Si alloys are most common among all the commercially available aluminium alloys. This is because of their extensively useful features like high strength to weight ratio, exceptional castability and pressure tightness, low coefficient of thermal expansion, good mechanical properties and corrosion resistance [3]. The mechanical properties of Al-Si alloys are affected not only by their chemical composition but are also ominously reliant on microstructure of the alloys like the morphologies of α-Al and eutectic Si phases [4]. The aluminium castings are extensively used for piston, cylinder liners, wheels, brackets, brake parts, control arm, cylinder heads and instrument panels. Aluminium alloys have also found widespread usage in heat exchangers. The present, high performance automobiles have a lot of discrete heat exchangers as in engine and transmission cooling, charge air coolers which are fabricated using aluminium alloys. Al-Si alloys finds itself being a part of large uses in marine castings, engine parts, cylinder blocks, rocker arms, water cooled manifolds and jackets, internal combustion engine pistons, parts of pumps, high speed rotating parts, impeller etc.In most of the AMCs, aluminium or aluminium alloys are taken to be the matrix and non-metallic or ceramics like SiC and Al2O3 are chosen to be the reinforcements. The properties of the composites can be varied depending on the reinforcements and the volume fraction. The main advantages of AMCs in comparison to other unreinforced materials are§ Higher Strength§ Better Stiffness§ Lower density § Enhanced high temperature properties§ Precise coefficient of thermal expansion§ Improved resistance to wearChirta [5] has compared the mechanical properties of Al-Si alloys produced using gravity and centrifugal casting technique. He found out that the properties of centrifugally cast samples have improved properties than the latter technique. Achuta [6] in his work has compared the results of Al-Si alloy with the values of the composites reinforced with Si and Graphite and has concluded that the reinforcing particles has increased the mechanical properties of the alloy namely hardness, tensile strength etc but the composite is losing its ductility. The composites produced by Rana [7] have nano SiC particles along with Aluminium alloy as the base material. The results obtained in the wear tests shows that the increasing the percentage of SiC particles in the alloy has given better resistance to wear at higher load and higher sliding distance.
2. Experimental Details
The base alloy used for the study was commercially available Al-18wt%Si. The chemical composition of the alloy is given Table 1.
The castings were synthesised by means of a centrifugal casting machine which had a flange that was linked to a shaft of synchronous DC motor. The speed could be mottled from 20 to 2000rpm. The die used had a length of 129mm, thickness 10mm and inner diameter of 80mm. For the present study, two casting were prepared. The first casting was made up of Al-18wt%Si, liquefied to a temperature of 700°C. This molten metal was then transferred into the die rotating at 800rpm. The metal matrix composite prepared using stir casting technique was the second casting. It involved the melting the base alloy i.e,. Al-18wt%Si in a crucible for 700°C then 5% of warmed SiC particles were agitated into this melt with the stirring speed of 600rpm and stirring time of 2 min. This mix was then poured into the horizontally mounted die running at a speed of 800rpm.
3. Results and Discussion
3.1. Hardness
The Vicker’s hardness test was performed on the centrifugally cast Al-18wt%Si and Al-18%Si-5%SiC from outer diameter to inner diameter in the radial direction. Figure 1 provides the graphical variation of the hardness in both the samples as the hardness is measured along from outer diametrical region to inner diametrical region. The hardness values of Al-18wt%Si-5%SiC (71kg/mm2) were found to be higher than the hardness value of Al-18wt%Si (60 kg/mm2) by 18% at outer diameter. The rotational speed of the mould in centrifugal casting process significantly effect on the particle segregation in centrifugal casing of metal alloys. Since the centrifugal force induced due to rotation forces the denser particles to move radially outward and lighter particles to move radially inward. The higher value of hardness in Al-18wt%Si-5%SiC is due to the presence of SiC in outer diameter of the casting. It has been witnessed that the concentration of Si primary particles is more at the inner diameter than the outer diameter, this is owing to the reason that the Si particle being less dense thrown inward during the rotation of the mould. The direction of solidification is taking place from outer radius to inner radius as the casting gets cooled immediately as soon as the melt touches the cold metal mould. Hence rapid solidification takes place near the mould surface, this leads to the increase in hardness. When the metal gets solidified rapidly some of the Si and SiC particles also trapped in the solidified metal. The trapped particles are also responsible for the increase of hardness of the metal alloys. Therefore, the increase in hardness at the outer radius is due to the rapid solidification of the casting and presence of trapped Si and centrifugally thrown SiC particles. The maximum hardness at the inner diameter is due to the existence of maximum concentration of Si particles and smaller amount of SiC particles in the Al-18wt%Si-5%SiC castings. A slightly higher hardness value is observed at the outer diameter due to the chilling effect of the mould. Because of that, rapid solidification takes place when molten metal comes in contact with cold metal mould. The similar effects have been observed in case of Al-18wt%Si but hardness value are lower compared to the hardness value of Al-18wt%Si-5%SiC. The lower value of hardness value at the radius nearly at 4mm in both the castings is due to the delayed solidification of castings and also the particles present in the mushy region are thrown away either inward or outward along the radial direction due to the centrifugal effect.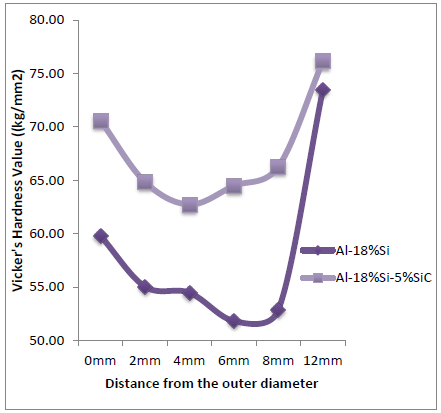 | Figure 1. Comparison of hardness for Al-18wt%Si and Al-18wt%Si-5%SiC casting |
When the load is being applied through the indenter, during the downward motion of the indenter, a pressure will be created which along with a non-uniform flow of the matrix and increased particle concentration tends to resist the deformation. Subsequently, due to the increased particle concentration the hardness value increases.
3.2. Tensile Test
Figure 2 represents the results of the tensile strength of the Al-18wt%Si-5%SiC and Al-18wt%Si. The UTS of the alloy in MPa was averaged around 97-99 whereas for the composite it was 117-120 MPa. This is owing to the occurrence of SiC as the reinforcing particles in the casting.The upsurge in the value was found be more than 20%. The presence of the reinforcing ceramic particles hinders the motion of displacements in the period of plastic deformation and consequently permitting the matrix to behave similar to an isotropic material. This is the reason for the enlarged ultimate tensile strength in the composite. The creation of the particle clusters in the composite has a substantial influence on the strength and their plastic deformation. The cluster formation has no much effect on the elastic nature of the composite. Despite the fact addition of the reinforcements escalates the ultimate tensile strength of the composite, it reduces the ductility. The ceramic reinforcing particles acts as load bearing particles by decreasing the dislocations formed because of the applied load.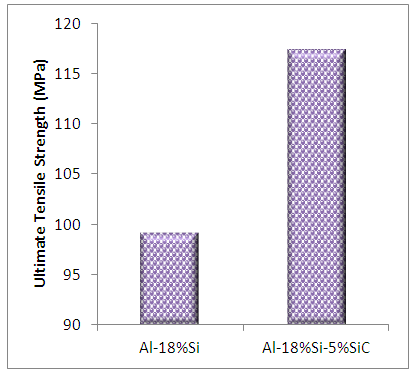 | Figure 2. Comparison of UTS between base alloy and MMC |
But due to the inherent brittleness of the reinforcing particles upon their addition they decrease the ductility of the composites.
3.3. Density
The density of the produced cylinder is measured using Archimede’s principle. The obtained experimental value of density is then compared with the theoretical value. The theoretical value of density is calculated using the rule of mixtures which is given by the formula,
Figure 3 shows the variation in the density of composite and base alloy and the comparison of theoretical and experimental value. It is quite obvious that the density of the composite has been increased in when compared with the density of the base alloy. The hard ceramic particles reinforced into the composite have a density of (3.2 g/cm3) which upon reinforcing with the matrix tends to the increase the density of the base alloy. This increase can be clearly seen in the Figure 3. 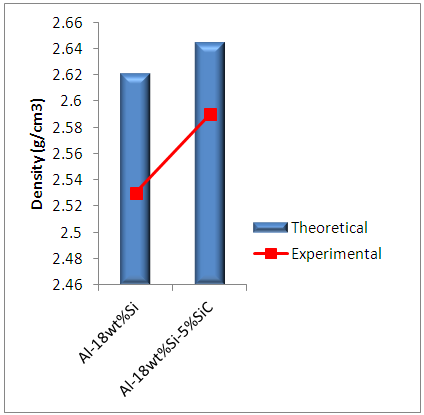 | Figure 3. Variation in density of composite and base alloy |
But when the comparison has been made between the theoretical and experimental values of density, the experimental value is found to be lower than the theoretical value. This decrease in the density can be because of the minor casting defects like presence of voids. The voids which are created due to the entrapped air cause a slight decrease in density. The voids can also be termed as porosity. Figure 4 gives the level of porosity present in the produced casting.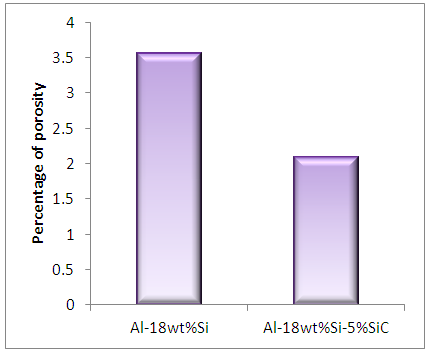 | Figure 4. The level of porosity in the produced castings |
3.4. Impact Test
The impact test is performed to find the impact energy of the specimen or the toughness of the specimen. The impact energy was found by using standard ASTM E23 charpy test having a V-notch of 2mm depth and 45°. The hammer was released at a velocity of 4.15m/s. Figure 5 shows the comparison of the impact energy of the composite with the base alloy.The total impact energy is the sum of energy necessary to start the fracture and the energy required for crack propagation. Impact strength is conveyed into the alloys via the ductile Al matrix. This Al matrix divides low amounts of intermetallic particles from one another at lower additional levels hence there exist only a smaller amount of locations for the stress to concentrate which helps in the initiation of the crack.A discernible drop in the value of the impact energy can be observed in the case of Al-18wt%Si-5%SiC. From the Figure 5, it is clear that the addition of the SiC into the alloy has lowered the toughness. The toughness of the base alloy is more than 66% in comparison to that of the composite. The decrease in the toughness of the composite is due to the presence of the ceramic reinforcing particles. The addition of the ceramic reinforcing particles tends to improve its strength under the slow loading conditions as in the case of tensile test. 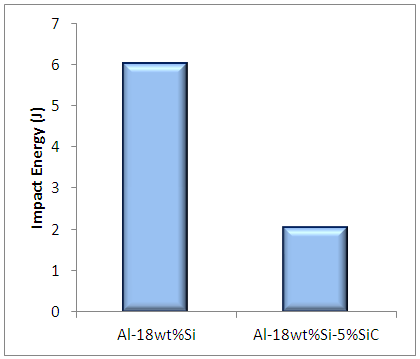 | Figure 5. Comparison of impact energy of composite and base alloy |
Figure 2 clearly shows the increase in the UTS of the composite. But under the sudden loading applied during the impact test, due to its inherent brittleness the reinforcing particles fails to impart the strength to its matrix material.
4. Conclusions
From the study, the following conclusions can be drawn:i. The composite cylinder and the base alloy cylinder was successfully cast using centrifugal casting technique under a speed of 800RPM and 700°C teeming temperature.ii. From the results obtained through the Vicker’s Hardness test, it was remarked that, the hardness value decreases progressively from outer diameter towards the centre and reaches the maximum value at the inner diametrical region. The isolation of primary Si particles causes high hardness in the inner region. The hardness value of 73HV and 76HV was found in base alloy and composite correspondingly in the inner diametrical region. However, in the case of outer diametrical region, the base alloy has a hardness value of 59HV while the composite has a hardness of 70HV. The amassing of higher density SiC particle is credited for this increase in hardness. iii. The tensile test results discovered that the UTS of the composite were 117-120MPa. The solid ceramic reinforcing particles aid in circumventing the local dislocations taking place due to the application of load. Even though the tensile strength has increased due to their addition, the ceramic particle reduces the ductility. iv. The reduction in the ductility of the composite is confirmed by the impact tests conducted on both the samples. It was seen that the composite due to the addition of the ceramic particles has lost its ability to absorb shock loads.v. The result of the density tests perfectly matches with the results obtained through tensile test and impact test.
ACKNOLEDGEMENTS
The authors are grateful to the management of Nitte Meenakshi Institute of Technology, Bengaluru for allowing us to use the facility from the research centre for the completion of this study.
References
[1] | M. Schmitt, D. Paulmier, “Tribological behaviour of diamond coatings sliding against Al alloys”, Tribology International 37, 2004, pp.317-325. |
[2] | Du Jun, Liu Yao-hui, Yu Si-rong, Li Wen-fang, “Dry sliding friction and wear properties of Al2O3 and carbon short fibres reinforced Al–12Si alloy hybrid composites”, Wear 257, 2004, pp. 930-940. |
[3] | S.A. Kori, T.M. Chandrashekharaiah, “Studies on the dry sliding wear behaviour of hypoeutectic and eutectic Al–Si alloys”, Wear 263, 2007, pp.745–755. |
[4] | Hengcheng Liao, Yu Sun and Guoxing Sun, “Correlation between mechanical properties and amount of α - Al phase in as- cast near-eutectic Al - 11.6% Si alloys modified with strontium”, Materials Science and Engineering A ,335, 2002, pp. 62-65. |
[5] | G. Chirita, I. Stefanescu, J. Barbosa, H. Puga, D. Soares and F.S.Silva, “On assessment of processing variables in vertical centrifugal casting technique”, International Journal of Cast Metals Research, Vol 5, No 5 2009. |
[6] | Achutha M.V, Sridhara B.K , Abdul Budan, “Fatigue Life Estimation of Hybrid Aluminium Matrix Composites”, International Journal on Design and Manufacturing Technologies, Vol.2, July 2008, pp.14-21. |
[7] | S Das, “Development of Aluminium Alloy Composites for Engineering Applications”, Trans. Indian Inst. Met, Vol.57, No. 4, August 2004, Pp. 325-334. |