Jathin K. J.1, Chinthankumar D. M.1, Manujesh B. J.1, Umashankar K. S.1, Prajna M. R.2
1Department of Mechanical Engineering KVGCE, Sullia, D.K, Karnataka, India
2Department of Computer Science & Engineering, KVGCE, Sullia, D.K, Karnataka, India
Correspondence to: Manujesh B. J., Department of Mechanical Engineering KVGCE, Sullia, D.K, Karnataka, India.
Email: |  |
Copyright © 2016 Scientific & Academic Publishing. All Rights Reserved.
This work is licensed under the Creative Commons Attribution International License (CC BY).
http://creativecommons.org/licenses/by/4.0/

Abstract
The need of light materials that exhibit high strength to weight ratio is finding a new area of interest in recent days. The rigid polyurethane foams are one among them which shows good mechanical properties and are used in various structural applications. Present work aims at determining mechanical properties of the alumina filler filled polyurethane foams. The rigid polyurethane foams reinforced with alumina fillers (3%, about 18.23g, 45μm and 99.7% purity) in order to increase mechanical properties and to minimize the bubble formation. The mechanical properties such as flexural and compression strength was examined. The test results showed that higher density PU foams show better performance. The inclusion of the filler has drastically minimized the bubble formation during the foaming process.
Keywords:
Alumina filler, Rigid, Polyurethane (PU), Foam, Flexural, Compression
Cite this paper: Jathin K. J., Chinthankumar D. M., Manujesh B. J., Umashankar K. S., Prajna M. R., Synthesis and Characterization of Alumina Filler Reinforced Polyurethane Foams for Light Weight Applications, American Journal of Materials Science, Vol. 6 No. 4A, 2016, pp. 67-71. doi: 10.5923/c.materials.201601.13.
1. Introduction
In the olden days, manufacturing companies were used to construct the product using spare materials. The materials used as spares include bricks, stones, wood, iron and steel. Use of these materials and methods were implemented during eighteenth to nineteenth century of industrial revolution [1]. But the handling of products which was constructed by using these materials became difficult. Handling of these materials resulted in higher energy consumption and made the system bulk. But the materials such as iron and steel are used even today in the construction of variety of products due to its high strength [1]. During the year 1709 the researcher named Abraham Darby developed techniques to produce cast iron [1]. At the end of eighteenth century, the wrought iron was replaced with cast iron. Later in the year of 1850 mild steel production techniques were developed by the research worker named as Henry Bessemer [1]. As an effect most economical steels were developed. During 19th century revolution has taken part in the field of light weight structures. At the beginning of 20th century industrially developed light weight structures are started to emerge. Polymer foams are first invented in the 1930's and 40's, with foamed polystyrene being the first polymer foam made in 1931 [2, 3]. Polyurethane was found by Dr. Otto Bayer during the beginning of the Second World War. That was first used as a replacement for rubber. Polyurethanes are divided into rigid foams and flexible foams [2]. Flexible PU foams are soft and used for cushioning applications. Polyurethane (PU) rigid foams have good thermal properties than thermoplastics and thus commonly used for insulation purposes. They have low thermal conductivity [2].With the growing concern for energy conservation, there is a need to improve the properties of rigid foams. This can be achieved by making the foams with smaller cell sizes. Another method is by adding fillers which will act as diffusion barriers. Fillers can inhibit the bubble growth by affecting local archeology surrounding the growing bubbles. Fillers have been successfully used in thermoplastic foams to reduce cell size [4]. There were lots of studies carried out by reinforcing different types of fillers in polyurethane foaming process [4-6].Therefore the work aims at the synthesis and characterization studies on mechanical properties of polyurethane foam reinforced with alumina filler with varied foam densities.
2. Materials and Methods
The raw material used for the production of polyurethane foam was obtained from Polynate Foams Pvt. Ltd, Bangalore, Karnataka State, while the Alumina powder was obtained from S. P Circle Shop, Bangalore.
2.1. Materials
2.1.1. Alumina Filler for Reinforcement.
The mechanical properties of polymer foams can be improved by adding fillers [4]. In this study the alumina fillers of 45 micron and 99.7% purity is used as reinforcing agents. The use of fillers for reinforcement of polymers foams is a new technology which throws high expectations since they improve the mechanical properties. Improved mechanical properties could allow a reduction in the amount of material needed for an application [6].  | Figure 1. Alumina Filler |
2.1.2. Polyurethane Foam Components
There are two main components necessary for the formation of polyurethane foam, namely Polyol and diphenylmethane diisocyanate (MDI). Commercially polyol is represented as part B and diphenylmethane diisocyanate (MDI) is represented as part A. The chemicals being supplied by Polynate Foams Bangalore.
2.1.3. Mold Box
The mold box is prepared by the use of M.S steel. It is welded to the dimension of 300x300x25mm. During the foaming process there will be a tremendous temperature and pressure setup, to resist this condition the mold box was fabricated with the help of M.S steel. Surface of the mold box is covered by the help of Teflon sheets for the purpose of easy removal of fabricated foam.
2.2. Procedure for the Foam Production
The PU foams with and without varied content of fillers were prepared by the following method. 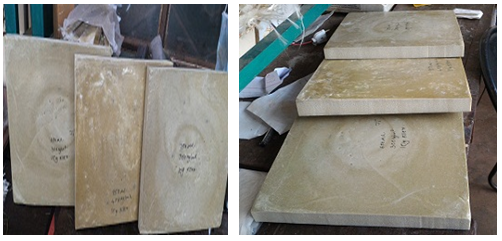 | Figure 2. Produced PU Foam Blocks |
The desired amount of filler was mixed with MDI (Part A) using a stirrer. Then, polyol (Part B) was added and stirred or mixed for about 10 to 20 seconds. The composition was then poured rapidly into the mold space and then the mold box is closed with the help of G-cramp such that to avoid the air gaps on the mating surfaces of mold box. The compositions undergo exothermic reaction to form foaming approximately 10-30 seconds after pouring. The mold was allowed to cure at room temperature for about 1 hour and then opened.
2.3. Preparation of Testing Specimens
The test samples are prepared as according to the ASTM standards. For the purpose of performing flexural and compression tests, the foams were cut in accordance to the ASTM C 393/C 393M- 06 and C365/C 365M-05 respectively. Below Figures 3 and Figure 4 show the test specimens to perform flexural and compression tests. 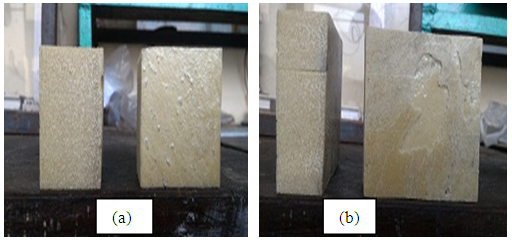 | Figure 3. (a) Specimen for Flat Wise Compression (b) Specimen for Edge Wise Compression Test |
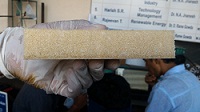 | Figure 4. Specimen for Flexural Test |
4. Results and Discussions
The prepared specimens were tested using the Universal Testing Machine (ZWICK/ ROELL Z020) in KONSPEC, Pvt. Ltd. Mangalore.
4.1. Flexural Testing
The test span length of the samples was set to 100mm and the load is applied at the mid span of span length. It was observed that a 6 mm (maximum) deflection due to bending, and load was continuously applied till the fracture of the specimens. The Figure 5 shows the specimen under 3- Point Bend Test.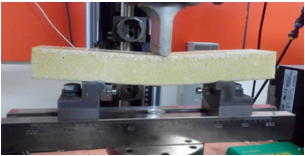 | Figure 5. Specimen under 3- Point Bend Test |
The Figure 6 shows the flexural curves obtained during the flexural tests. It was arbitrarily observed with two distinct phases. In the first phase, the curve tends to increase linearly up to a certain limit and then paves way to the second phase, where it was observed to form instantaneous drop. The failure was impended as cells start to expand and this expansion will continue till the elastic limit of the cells. Upon crossing the peak load condition the cell fail through yielding. The cell walls found cracking illustrating the drift over the elastic limit. The structure shows yielding featured through gradual cell wall breaks thus initiating the sudden failure. The similar mechanism was reported by various authors [7-11]. 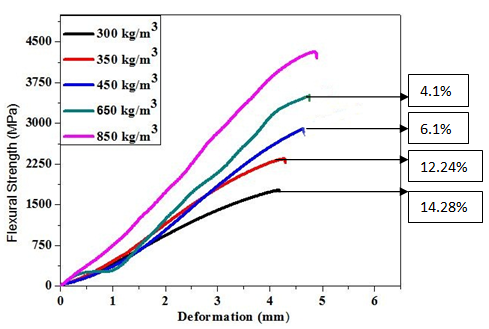 | Figure 6. Flexural Curves under 3P Bend Test |
In the present work it was observed that the foam specimens of density 850kg/m3,, the flexure strength decreases by 4.1%, 6.1%, 12.24%, 14.28% for densities 650kg/m3 450kg/m3 350kg/m3 300kg/m3 respectively. The phenomenon may be attributed to the fact of mere densification resulting in loss of flexure. The Figure 7 shows the post test 3- Point bend specimens. The specimens were kept in (L to R) with increasing order of densification. It was observed that higher density foams were brittle fractured with shear angle less than 30°. The lighter foams featured with in-line cracks at approximately mid-span.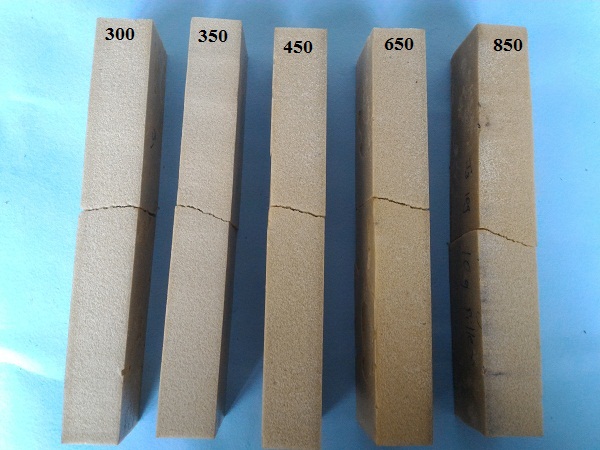 | Figure 7. The post test 3- Point bend specimens |
4.2. Compression Strength
Under this study flat wise and edge wise compression tests were performed. During this test 2mm/min loading speed was adopted.
4.2.1. Edgewise Compression
The Figure 8 shows the Edgewise Compression Test. The edgewise compression tests conducted to explore the foam properties on the transverse direction.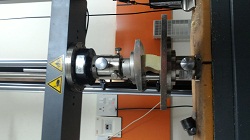 | Figure 8. Edgewise Compression Test |
The Figure 9 shows the Edgewise Compression test curves. The tests also prevailed with 3 different phases.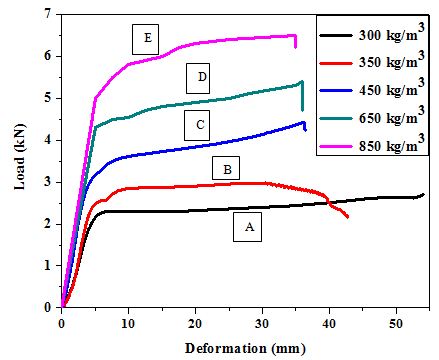 | Figure 9. The Edgewise Compression test curves |
The featured zones in the edgewise compression tests namely linear rise, a steady and gradual loaded plateau and a sudden fall in the loading behavior. The 3 discrete phases were observed in the Figure 9. During the first phase the curve increases randomly up to the elastic region. In the second phase the curve increases gradually till the end of plastic region and the phase is termed as a plateau regions. The final phase initiated when the curve increases with peak formation followed by sudden drop resulting the failure. Z.H. Tu et. al observed the similar trends in working with Plastic deformation modes in rigid polyurethane foam under static loading.The Figure 10 shows the edgewise compressed test specimens. The specimens were kept in (L to R) with decreasing order of densification. It was observed that higher density foams capable of withstanding the edgewise loading with minimum damage but the lower density foams tends to crumpled. The test justifies the acceptance of higher density foams under edgewise loading. In the present study the foam specimens of densities 300kg/m3, 350kg/m3, 450kg/m3, 650kg/m3, 850kg/m3 found to deform by 73.68%, 68.75%, 47.62%, 33.33% and 28.57% respectively.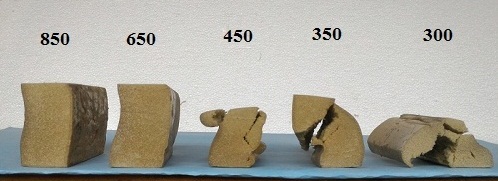 | Figure 10. Edge wise compressed specimens |
4.2.2. Flatwise Compression
The Figure 11 shows the flatwise compression test curves. The tests also prevailed with 3 different phases. The curves indicate the clear formation of plateau which enables the compressive loading. For the present studies it was observed that for the foam specimens of densities 300kg/m3, 350kg/m3, 450kg/m3, 650kg/m3, 850kg/m3 the flatwise compressive strength was observed to be 55.8%, 50%, 41%, 36.36% and 25% respectively.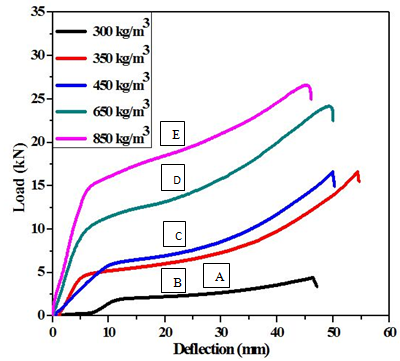 | Figure 11. Fatwise Compression test curves |
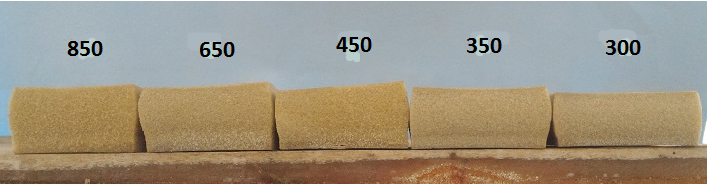 | Figure 12. Flat wise compressed specimens |
5. Conclusions
The paper attempts to synthesize the alumina filler reinforced polyurethane foam slabs with five different densities using one step one shot method. The foaming process is observed to be associated with the huge pressure and few typical arrangements were developed to overcome the set-up pressure optimized mold design. The alumina fillers used in the study has modified the foaming process. The good cure kinetics has been observed during the process which showed better mechanical properties. The bubble formation has drastically reduced and thus resulted with minimum flaws in the foaming process. The flexural and compression studies have revealed that the filler reinforced PUF witness better properties than unfilled. It is concluded that the mechanical strength is directly related to foam density.
References
[1] | F.C. Campbell. Lightweight Material—Understanding the Basics, Copyright © 2012 ASM International. |
[2] | Katrine Sivertsen. Spring 2007, Polymer Foams, 3.063 Polymer Physics. |
[3] | Shoaib Suleman, Shahzad Maqsood Khan, Nafisa Gull, Waqas Aleem, Muhammad Shafiq, and Tahir Jamil. A Comprehensive Short Review on Polyurethane Foam, ISSN 2351-8014 Vol. 12 © 2014 Innovative Space of Scientific Research Journals http://www.ijisr.issr-journals.org/. |
[4] | Tomy Widya and Christopher W. Macosko. Nanoclay-Modified Rigid Polyurethane Foam. ISSN 0022-2348 print/ 1525-609X online DOI: 10.1080/00222340500364809. |
[5] | Hongyu Fan, Ali Tekeei, Galen J. Suppes, and Fu-Hung Hsieh. Research. Properties Of Biobased Rigid Polyurethane Foams Reinforced With Fillers: Microspheres And Nanoclay. |
[6] | Juan Lobos and Sachin Velankar. A technical Report on How much do Nanoparticle Improve the Modulus and Strength of Polymer Foams. |
[7] | A. P. Mouritz. Flexural properties of stitched GRP laminates. Hassan Mahfuz a, Tonnia Thomas b, Vijay Rangari c, Shaik Jeelani. On the dynamic response of sandwich composites and their core materials. |
[8] | R.V Rao, BJ Manujesh, Behavior of sandwich composites under flexural and fatigue loading: Effect of variation of core density, International Journal of Engineering Science and Technology. |
[9] | S.C. Sharma, M. Krishna, H.N. Narasimha Murthy, M. Sathyamoorthy, and Debes Bhattacharya. Fatigue Studies of Polyurethane Sandwich Structures. |
[10] | Z.H. Tu, V.P.W. Shim, C.T. Lim. Plastic deformation modes in rigid polyurethane foam under static loading. |
[11] | Manujesh B. J, Vijayalakshmi Rao. Fatigue behavior and failure mechanism of PU foam core e-glass reinforced vinyl ester sandwich composites. International Journal of Materials Engineering 2013, 3(4): 66-81. DOI: 10.5923/j.ijme.20130304.02. |