T. N. Praveen Kumar1, N. Suresh1, S. Venkateswaran2, S. Seetharamu3
1BMS Institute of Technology & Management, Bengaluru, India
2NM Institute of Technology, Bengaluru, India
3BMS College of Engineering, Bengaluru, India
Correspondence to: T. N. Praveen Kumar, BMS Institute of Technology & Management, Bengaluru, India.
Email: |  |
Copyright © 2016 Scientific & Academic Publishing. All Rights Reserved.
This work is licensed under the Creative Commons Attribution International License (CC BY).
http://creativecommons.org/licenses/by/4.0/

Abstract
In this work Eutectic Al-Si Alloy Fly-ash Cenosphere Open Cell Foamed Composite were produced by melt route i.e., core casting method. AFSP (Aluminium Foam Sandwich Panel) was further fabricated by open aluminium foam and two face aluminium sheet. The Flatwise compression strength is a fundamental mechanical property of sandwich cores that are used in design purpose. Core properties are usually required in a direction normal to the plane of facing sheet as the core is placed in a sandwich construction. The Flatwise compressive behaviour of AFSP studied. The Flatwise compressive strength of AFSP is found to be 45.1MPa and compressive strength of only Al foam is 25.7MP. It is observe that compressive strength of AFSP higher than of compressive strength of aluminium foam alone. Relative density, density and porosity of the foam produced are 0 .35and its density is .92g/cm3and 65% respectively.
Keywords:
Open cell foam, Sandwich panels, Aluminium foams, Flatwise Compression test
Cite this paper: T. N. Praveen Kumar, N. Suresh, S. Venkateswaran, S. Seetharamu, Development and Study of Flat Wise Compressive Strength of Eutectic Al-Si Alloy Fly-ash Cenosphere Open Cell Foamed Composite Core Sandwich Panel, American Journal of Materials Science, Vol. 6 No. 4A, 2016, pp. 56-60. doi: 10.5923/c.materials.201601.11.
1. Introduction
1.1. Aluminium Foams
Metallic foams are generally classified into two types: open-cell foams and closed cell foams. If the solid of which the foam is made is contained in the cell edges only, so that cells are connected through open faces, the foam is said to open-celled and closed cell foams are one which contains pores that are not interconnected [1]. The production methods for open cell foam include i. Co-processing of a metal powder with a leachable powder. ii. Manufacture of a ceramic mould from a wax or polymer foam precursor, followed by burning-out of the precursor and pressure infiltration with a molten metal or powder slurry for the production of Al, Mg, Ni-Cr, stainless steel and Cu foams. iii. Vapour phase deposition or electro-deposition of metal onto a polymer foam precursor which is subsequently burned out leaving cell edges with hollow cores for the production of Ni, Ti foam. [2]. Fly ash particles can be either solid (precipitator) or hollow (cenosphere). Cenosphere are beneficial in synthesizing lightweight composites. Over million tons of fly ash is produced each yearin thermal power plants and most of it is land filled. Fly ash- aluminium composite will require reduced energy for re-melting during recycling since the fly ash will not melt and only aluminium fraction will have to be re-melted. Addition of fly ash can make automotive casting lighter, leading to further energy savings during the use of cars and trucks by means of reduced fuel consumptions. The density and co-efficient of thermal expansion of castings decrease, and hardness and wear resistance increases as their fly ash content increase [3].A356 Al-fly ash MMCs exhibit superior damping characteristics compared to unreinforced alloy at ambient temperature. Damping capacity of fly ash reinforced Al-based composite increases with the increase in volume fraction of flyash [4].
1.2. Aluminium Foam Sandwich Panels (AFSP)
A sandwich structures usually consists of two high stiffness and high strength face sheets or skins with a large volume and low weight core layers in between. The face sheets bear tensile and compressive forces from bending loads. The core layer bears shear and compressive loads. A high thickness core layer increases the sandwich’s moment of inertia and supports the face sheets against buckling. Application of AFS: The superior weight specific bending stiffness of aluminium foam sandwich material qualifies sandwich material for use in automotive structures [5].Aluminium foam sandwich showed a specific strength 25% higher than the specific strength of the basic material, thus making them interesting for light structure constructions. The foam is becoming compact, but the real behaviour of AFS is strongly affected by open cell morphology, cell edge bending, cell edge contraction and other complex phenomena occur and the stiffness of the panels depends mainly from the cell edges mechanical behaviour [6]. The foam filling into core of an empty corrugated sandwich could increase the compressive strength and energy absorption capacity of the hybrid sandwich by as much as 211% and 300% respectively, and the specific energy absorption by 157%. With high specific strength and specific energy absorption, all-metallic sandwich panels filled with aluminium foams hold great potential as novel light weight structural materials for a wide range of crushing and impulsive loading applications. [7] Metal/metal foam sandwich beams containing a core composed of one or three layers of metal foam were produced and tested in bending. Lightweight graded metal/metal foam beams show little promise from the standpoint of stiffness-limited design, they may be of interest from the standpoint of load-limited design [8].
1.3. Applications of AFS
Aluminium foam technology and especially aluminium foam sandwich (AFS) technology has led to a number of promising small-small scale applications.i. Electromagnetic shielding: AFS shields electromagnetic waves very well. ii. Solar thermal energy generation: AFS can be bent to the large radii required (20m). A thin reflecting foil on top of the AFS trough would provide the high reflectivity needed. Thermal warping is small. Lower deformation caused by the wind due to high stiffness to mass ratio. iii. Architectural panels: Architecture is a classical application field for metal field, e.g. for their sound absorbing properties, non-inflammable, light and robust and have good corrosion resistance. iv. Protecting against blast, bullets and other hazards [9].
2. Development of AFSP
2.1. Materials
Aluminum alloy chosen for production of the foam is eutectic aluminium silicon alloy because of its good flowability and calcium carbonate is used as a foaming agent. The composition of the alloy is (wt%) Silicon 11.8, Iron 0.32, Copper 0.002, Manganese 0.62, Magnesium 0.065, Zn 0.021 and the remainder being aluminum.Reinforcement material used was 7wt% fly ash cenosphere.
2.2. Production of Open Cell Foam
Sand, bentonite, chalk powder, coal powder, molasses and water were properly mixed and used as filler materials. The cores were prepared manually to the required size and made into approximately spherical shape from the core ingredients. The cores were arranged properly in the metal sand mould. Eutectic Al-Si alloy was melted in the electric resistance furnace. Metal in the molten state was stirred at a speed of around 650rpm and 7wt.% fly-ash was added into the molten metal slowly and stirred further until fly-ash particles were uniformly distributed in the mould. The molten metal was then poured into the mould, allowed to solidify and cooled to room temperature. Solidified foam casting was taken out from the mould and then cores were completely removed from the casting by washing with water leaving behind open cell foam.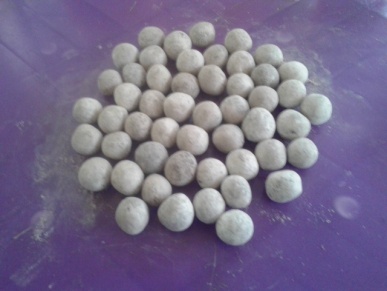 | Figure 1. Spherical cores |
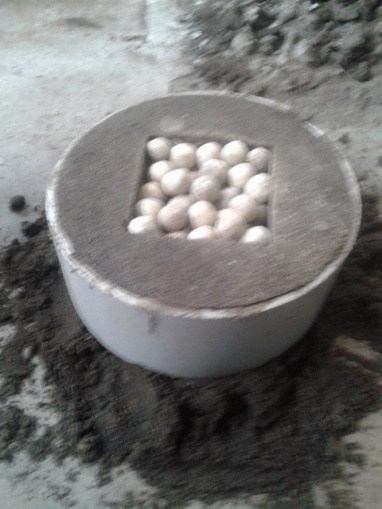 | Figure 2. Mould filled with cores |
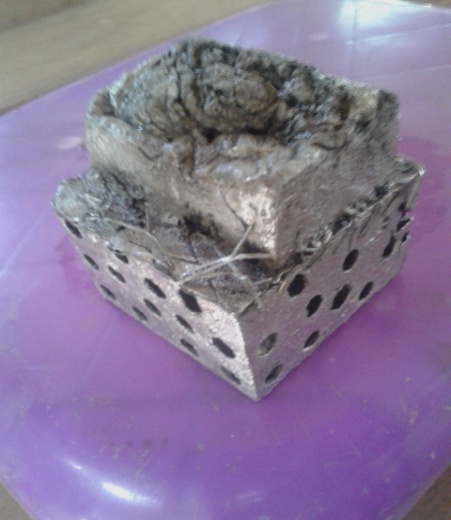 | Figure 3. Foam casting |
2.3. Density and Porosity of Foam
Distribution of the cells is relatively uniform in produced open cell foam. Mechanical and physical properties open cell metal foam is governed by density and porosity. Density of open cell foam casting was determined by weighing the foam castings using digital balance and measuring their dimension. The density was then obtained by using the formula given below: Density of the foam = Weight of cast foam/Volume of the foam =135.24g/(7cm×7cm×3cm)= 0.92g/cm3The mechanical properties of the foam depends mainly on the metal with which the foam is made and the relative density of the foam. The percentage of porosity is calculated from the formula as given below: % porosity = (ρs-ρf)/ρs X100= (2.65g/cm3-0.92g/cm3)/2.65g/cm3 = 65%ρs – Density of solid aluminium from which foam is made ρf– Density of aluminium foam 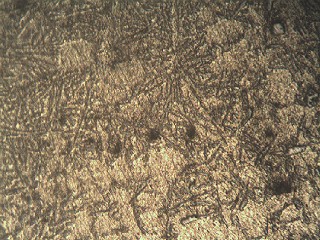 | Figure 4. Micrograph of eutectic Al-Si alloy fly-ash cenosphere composite foam |
2.4. Fabrication of AFS
The core material used for sandwich panels was open-cell aluminium silicon eutectic alloy developed sandwich panels consist of bottom face sheet, top face sheet and metal foam core. Face sheet is bonded to the aluminium foam core using adhesive. The adhesive was cured in ambient temperature for one hour. The foam mass was measured with digital weighing balance and the volume was calculated from the geometry of the foam specimen. The density of foam used for core was calculated by using the mass and volume. The foam cores density of was 0.92g/cm3.
3. Flatwise Compression Test
A compression test was conducted to determine behaviour of the aluminium foam sandwich panels. Uni-axial compression tests were carried out on AFSP. Electronic Universal Testing Machine UTM -Hydraulic type, 40 tonnes capacity, FIE make was used for this purpose. Load and displacements noted down from the digital display. Maximum load and corresponding displacements are noted down from the plot from the printer interfaced with UTM. The test specimen is placed between two parallel plates for flatwise test. Foam alone i.e., foam without face- sheet was prepared to evaluate the effect of face-sheet and foam core on compressive strength.ASTM C365 testing covers the determination of compressive strength of sandwich cores. Sandwich core will be subjected to a uni-axial compressive force normal to the plane of the facing sheet. The result of ASTM C365, Flatwise compressive strength is a fundamental property sandwich cores that are used in the design of sandwichpanels [10]. Based on the above ASTM standard. The foam specimen dimension chosen is 70mm×70mm×30mm. The bottom and top face sheets were made of aluminium sheet of thickness 1mm. Photographs of tested specimens have been acquired before and after the tests execution in order to better understanding of the failure mechanism of each specimen. Stress verses strain curves have been plotted for all tested specimens. Stress strain curve consist of initial elastic region, a large plateau region and followed by densification region.Two set of experiments were conducted, one with core and another without face sheets to study the compressive strength only with foam and with foam with face sheet.Area of the AFSP = 70mmx70mm = 4900mm2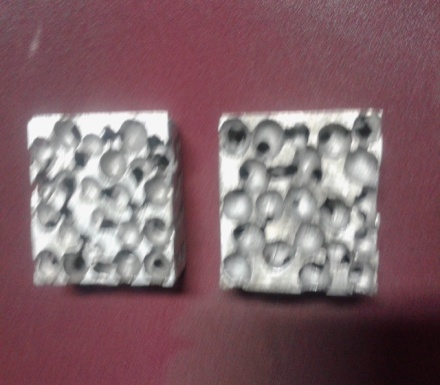 | Figure 5. Flatwise Compression Test Specimen |
3.1. Flatwise Compression Testing of Al Foam Alone
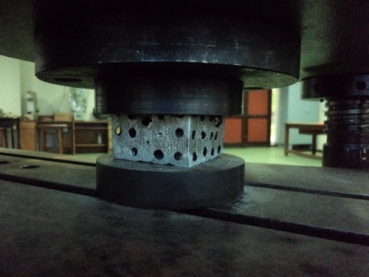 | Figure 6. AFSP before compression |
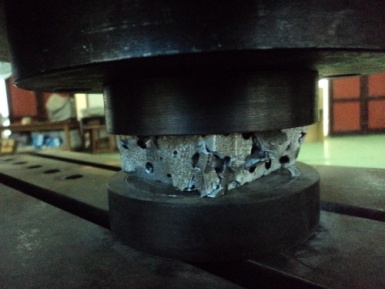 | Figure 7. AFSP during compression |
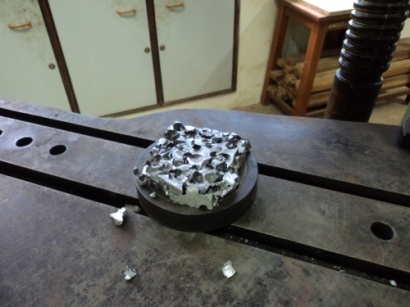 | Figure 8. AFSP after compression |
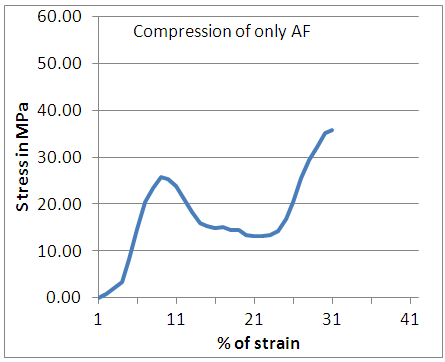 | Figure 9. Stress verses strain diagram for Al foam alone Fmax. = 126 KN Compression Strength =25.71 MPA |
3.2. Flatwise Compression Testing of AFSP
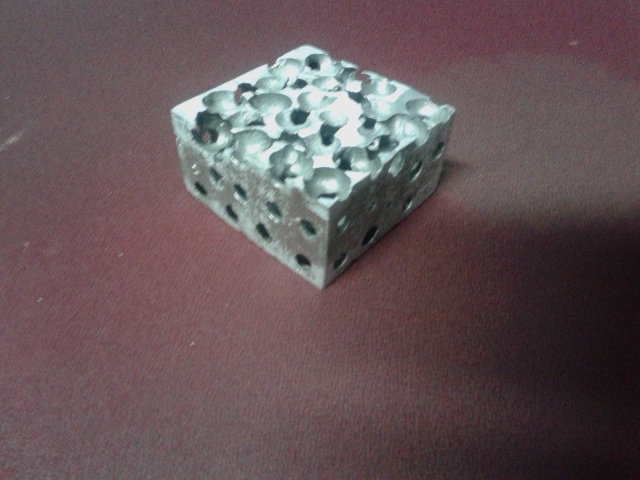 | Figure 10. Specimen without face sheets |
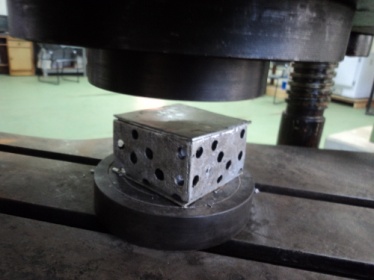 | Figure 11. AFSP before compression |
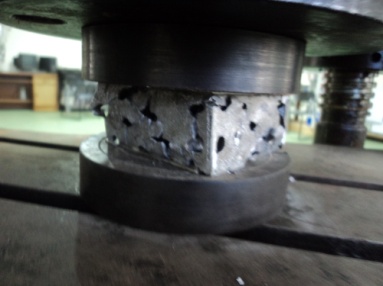 | Figure 12. AFSP during compression |
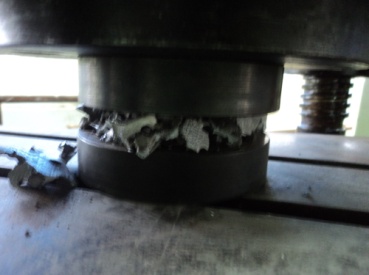 | Figure 13. AFSP after compression |
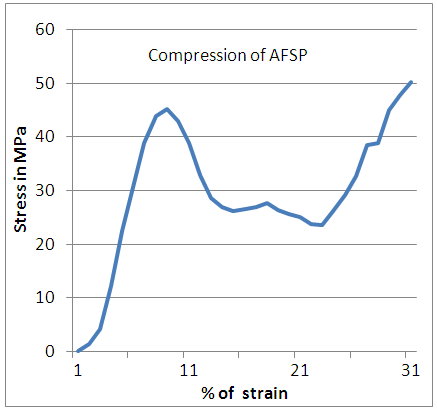 | Figure 14. Stress verses strain diagram for AFSP Fmax. = 221KN Flatwice compression strength = 45.1MPa |
4. Conclusions
Experiments have been carried out to investigate the Flatwise compressive behaviour of eutectic Al-Si alloy open cell foam produced from melt route by core casing method. Compression test was conducted on AFSP and aluminium foam. The stress verses strain curve is plotted and the stress verses strain curves exhibit a typical three-stage behaviour: elastic region, approximate plateau region and densification region. Stress-strain diagram was drawn, flat wise compressive strength of AFS is 45.1MPa and foam alone is 25.7MPa. Flat wise compressive strength of AFSP is almost 1.75 times the aluminum foam alone.
ACKNOWLEDGEMENTS
The authors would like to significantly thank and acknowledge Visvesvaraya Technological University, Belagavi, Karnataka, India, for the financial support for this Project through the University Research Grant Scheme [Ref. No.VTU/Aca./2009-10/A-9/11476, Dated: 02-01-2010].
References
[1] | Lorna J. Gibson, Michel F. Ashby, Cellular Solids, Structure and properties, Second Edition, Cambridge University Press, 1999. |
[2] | M. F. Asby, A.G. evans, N.A. Fleck, L.J. Gibson, J.W. Hutchinson and H.N.G. Waddley, Metal Foams: A Design Guide, Butterworth-Henemann, 2000. |
[3] | P. K Rohatgi, D. Weiss, Nikhil Gupta, Application of Fly Ash in Synthesizing Low cost Metal Matrix Composites for Automotive and other Engineering Applications, JOM Vol.58, No.11,2006, pp.71-76. |
[4] | Sudarshan, M K Surappa, Synthesis of fly ash particle reinforced A356 Al composites and their characterisation, Material Science and Engineering A 480(2008)117-124. |
[5] | KarstenStobner, Joachim Baueister, Dirk Lehmmhus, HeikoStanzick, VolkerZollmer, Composite based metallic foams: Phenomenology; Production; properties and Principles, International Conference “ADVANCED METALLIC MATERIALS” 5-7 November, 2003, Smolenice, Slovakia. |
[6] | C. Casavola, V. Dell’Orco, R. Giannoccaro, C. Pappalettere, Structural response of aluminium foam sandwich under compressive loading, Proceedings of the SEM Annual Conference June 1-4, 2009, Albuquerque New Mexico, USA. |
[7] | L.L. Yan, B. Yu, B. Han, C.Q. Chen, Q.C. Zhang, T.J. Lu, Compressive strength and energy absorption of sandwich panels with aluminium foam-filled corrugated cores, Composite Science and Technology 86(2013) 142-148. |
[8] | Arnaud Pollien, Yves Conde, Laurent Pambauian, Andreas Mortensen, Graded open-open cell aluminium foam core sandwich beams, Material Science and Engineering A 404(2005)9-18. |
[9] | John Banhart, Hans-Wolfgang Seelinger, “Recent trends in aluminium Foam sandwich technology”, Advanced Engineering Materials 14(12), 2012. |
[10] | Test Method for Flatwise Compressive Properties of Sandwich Cores, www.astm.org/Standards/C365html. |