Pankaj R. Jadhav1, B. R. Sridhar2, Madeva Nagaral3, Charan Raj K. A.1
1East Point College of Engineering & Technology, Bangalore, Karnataka, India
2South East Asian Engineering College, Bangalore, Karnataka, India
3Aircraft Research & Design Centre, HAL, Bangalore, Karnataka, India
Correspondence to: Pankaj R. Jadhav, East Point College of Engineering & Technology, Bangalore, Karnataka, India.
Email: |  |
Copyright © 2016 Scientific & Academic Publishing. All Rights Reserved.
This work is licensed under the Creative Commons Attribution International License (CC BY).
http://creativecommons.org/licenses/by/4.0/

Abstract
In the present investigation, microstructure study and tensile behaviour of B4C particulate reinforced A356 alloy composites has been reported. A356 matrix composite containing boron carbide was fabricated by conventional stir casting method. The composites containing 4 wt. % of B4C particulates were fabricated for the study. The microstructure of the composite was examined by scanning electron microscopy; images were taken to identify the presence of B4C particle in aluminum matrix. Further, tensile behaviour of as cast A356 alloy and A356-5 wt. % B4C composites were studied. Tensile properties like ultimate tensile strength, yield strength and percentage elongation were evaluated as per ASTM standards. Microstructural observation revealed the uniform distribution of particles in the A356 alloy matrix. From the analysis, it was found that the ultimate tensile strength of composite was increased due to boron carbide particles in the composite and the yield strength was increased due to the presence of boron carbide. Further, from the study percentage elongation of the composite decreases with the addition of boron carbide.
Keywords:
A356 Alloy, B4C Particulates, Ultimate Tensile Strength, Yield Strength, Stir casting
Cite this paper: Pankaj R. Jadhav, B. R. Sridhar, Madeva Nagaral, Charan Raj K. A., Mechanical Behavior of B4C Particulates Reinforced A356 Alloy Composites, American Journal of Materials Science, Vol. 6 No. 4A, 2016, pp. 51-55. doi: 10.5923/c.materials.201601.10.
1. Introduction
Metal matrix composites (MMCs) have emerged as advanced materials for several prospective applications. As they have high specific strength and stiffness, superior wear and seizure resistance, MMCs are used in automotive, aircraft and other engineering industries. The primary matrix materials are being used in the manufacture of MMCs such as aluminium, copper, titanium, magnesium and super alloys. The matrix is continuous phase which provides a binding support for the reinforcement. MMCs exhibit extremely good thermal stability associated with high strength, fatigue and toughness at higher temperature. These characteristics of MMCs are most desirable for design applications [1, 2].The attractive physical and mechanical properties that can be obtained with MMCs, such as high specific modulus, strength and thermal stability have been documented extensively. Metal matrix composites combine metallic properties, leading to greater strength in shear and compression and high service temperature capabilities [3]. Interest in MMCs for aerospace, automotive and other structural applications, has increased over last fifteen years as a result of availability of relatively inexpensive reinforcements, and the development of various processing routes which result in reproducible microstructure and properties [4].Most metals and alloys could be used as materials and require reinforcement materials which need to be stable over a range of temperatures and also non reactive. Only light metals, with their low density prove to be advantageous. Aluminium, titanium and magnesium are the popular matrix materials [5]. The reinforcements are being used in the form of fibers, whiskers and particulates. The advantages of particle reinforced composites over others are their formability with cost advantage and improved abrasion resistance hence they find applications as cylinder blocks, bearings, disk brakes, calipers, connecting rods and space structures.The elastic properties of MMCs are strongly influenced by micro structural parameters of the reinforcement such as shape, size, orientation, distribution and volume fraction. The ceramic particle reinforced Al-alloy composites led to a new generation engineering materials with enhanced specific properties. Depending on the specific applications, metal matrix composites are significant potential advantage compared to other material classes. Different types of reinforcements widely used in MMCs are graphite, SiC, Al2O3, TiC, WC and B4C [6, 7]. Processing methods for discontinuous Al-MMCs include stir casting, squeeze casting, rheocasting, liquid metal infiltration, spray deposition, powder metallurgy and extrusion. Among the variety of manufacturing processes available for particulate matrix composites, stir casting is generally accepted as a promising route because of its simplicity, flexibility and applicability to large quantity production.Several researches have been developed and investigated the properties of Al based metal matrix composites. Baskaran [8] investigated the dry sliding wear behavior of in situ casted AA7075-TiC metal matrix composites. In this investigation TiC particulates were developed bu in situ process in AA7075 matrix and evaluated the wear properties at different loads and sliding speeds. Yang et al. [9] studied ageing properties of aluminium alloy 6061-spinel whisker MgAl2O4. Here, fabrication of Al6061-MgAl2O4 composites was done by in situ process and solutionizing and age hardening treatment was performed on the composites. The hardness and ultimate tensile strength increase with increasing content of whisker, whereas ductility decreases at the same time.There is a growing interest worldwide in manufacturing ceramic particulate reinforced metal matrix composites which processes combined properties of its reinforcements and exhibit improved physical, mechanical and tribological properties. In the present study, aluminium A356 alloy based composites were fabricated by stir casting process. B4C particulates of size 70-80 microns were used as the reinforcement. The 4 wt. percentage of ceramics reinforcements were taken to fabricate the A356-B4C composites. The composites were tested for mechanical properties like ultimate tensile strength, yield strength and percentage elongation as per ASTM standards.
2. Experimental Study
The A356-B4C composites fabricated in this study contains 4 wt. % of ceramic B4C particulates. The density of A356 alloy is 2.71 g/cm3 and the density of B4C is 2.52 g/cm3. The density of composites decreases with addition of B4C particulates. The B4C particulates are used in the study procured from Speedfam (India) Limited, Chennai and A356 alloy is produced by Fenfe Metallurgist, Bangalore. The chemical composition of A356 alloy is shown in the Table 1.Table 1. Chemical composition of A356 alloy 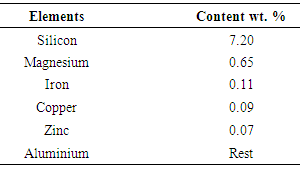 |
| |
|
The fabrication of A356-B4C composites was carried out by liquid metallurgy route via stir casting technique. The major components of the casting process consist of electrical resistance furnace; zirconium coated steel impeller and cast iron permanent mould. The power rating of electrical furnace used was 60kw and maximum temperature limit was 1200 degree Celsius. The mechanical stirrer used for stirring the molten alloy during the preparation of composites was coated by zirconium to withstand high temperature and to prevent migration of ferrous ions from the stirrer material into A356 alloy melt. The permanent type of mould made of cast iron used in fabrication is shown in Fig. 1.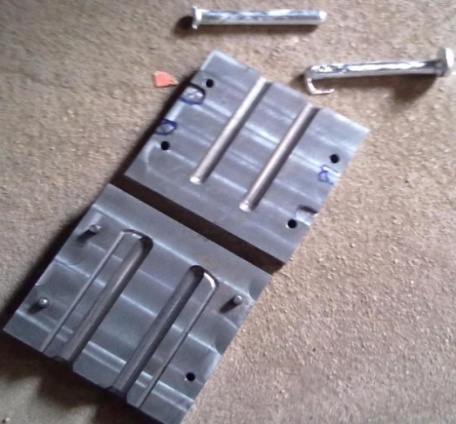 | Figure 1. Cast iron die used to prepare the samples |
Calculated amount of the A356alloy ingots were charged into the furnace for melting. The melting point of Aluminium alloy is 660°C. The melt superheated to a temperature of 750°C. The temperature was recorded using achrome-alumel thermocouple. The molten metal was then degassed using solid hexachloroethane (C2Cl6) for 3 min. A stainless steel impeller coated with zirconium was used to stir the molten metal to create a vortex. The stirrer was rotated at a speed of 300rpm and the depth of immersion of the impeller was 60 percent of the height of the molten metal from the surface of the melt. Further, the B4C particulates were preheated in a furnace upto 500°C were introduced into the vortex. Stirring was continued until interface interactions between the reinforcement particulates and the matrix promotes wetting. Then, A356- 4 wt. % B4C mixture was poured into permanent cast iron mold having dimensions 125mm length and 15mm diameter.The microstructural study was carried out on the investigating composites using scanning electron microscope. Samples around 10 mm diameter cut from the castings and were polished properly. Keller’s reagent was used to etch the samples. Tensile specimens were machined from the cast samples. The tensile specimens of circular cross section with a diameter of 9 mm and gauge length of 45mm were prepared according to the ASTM E8 standard testing procedure. The tests were conducted on a universal testing machine. All the tests were conducted in a displacement control mode at a rate of 0.1 mm/min. Multiple tests were conducted and the best results were averaged. Various tensile properties like ultimate tensile strength, yield strength and percentage elongation were evaluated for both as cast A356 alloy and A356-4 wt. % B4C composites.
3. Results and Discussion
3.1. Microstructural Analysis
The micro structural studies are useful in determining the grain size, grain shape and distribution of reinforcement particulates within the base matrix, which have a greater effect on the mechanical and tribological properties. Micro-structural features have been studied using scanning electron microscope (SEM). The SEM micrographs of as cast A356 alloy and A356-4 wt. % B4C composites are shown in Fig. 2 (a-b) respectively. The micrographs of A356-B4C composites reveal the uniform distribution of B4C particulates throughout the matrix. Uniformly distributed reinforcements increase the hardness and reduce the porosity of the metal matrix composites.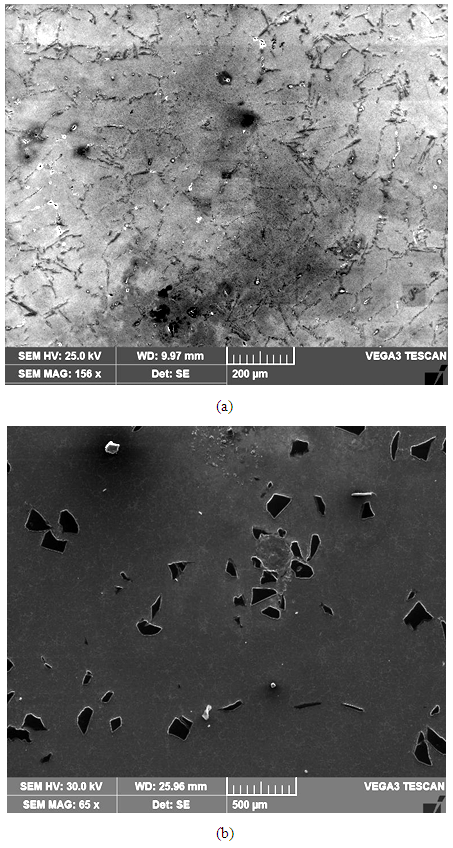 | Figure 2. Showing the SEM micrographs of (a) as cast A356 alloy (b) A356-4 wt. % B4C composite |
3.2. Tensile Properties
Fig. 3, 4 and 5 showing the tensile properties of as cast A356 alloy and A356-4wt. % B4C composite. Fig. 3 showing the ultimate tensile strength (UTS) of A356 alloy and it’s composite. From the figure, it is evident that UTS of A356-B4C composite is higher than the base matrix alloy. By adding 4 wt. % of B4C particles to the base A356 alloy, UTS has been increased from 166 MPa to 191MPa.From the fig. 4 it was found that yield strength (YS) of the as cast A356 base alloy is 131MPa and in A356-4 wt. % B4C composite is 154MPa. It showed an improvement of 17% in yield strength as compared with as cast base matrix.The increase in UTS and YS is mainly due to strong bonding between reinforcement particles and A356 matrix, plays an important role on the load transferring from matrix to reinforcement. This is because of grain refinement and particle strengthening [10]. The enhancement of strength is affected by the higher load bearing and mismatch strengthening caused by micro B4C particles. It is expected that due to the difference in the coefficients of thermal expansion between matrix and B4C reinforcement and therefore thermal mismatch stress, there is a possibility of increased dislocation density within the matrix during cooling from solidification temperature [11]. The dislocations might be lead to make local stress at the interface of particle and matrix. In comparison to the base aluminium, the great enhancement in the strength observed in the composites is due to the presence of the particles as obstacles that restrict the motion of dislocations trapped by B4C particulates. This will lead to increase the tensile strength of the micro composites during tensile tests.Fig. 5 shows the percentage elongation of as cast A356 alloy and its composites. The percentage elongation was reduced in A356-B4C composite as compared to the base alloy. It can be seen from the graph that the ductility of the composites decrease significantly with the 4 wt. % B4C reinforced composites. This decrease in percentage elongation in comparison with the base alloys is a most commonly occurring disadvantage in particulate reinforced metal matrix composites. The reduced ductility in A356-4 wt. % composites can be attributed to the presence of B4C particulates which may get fractured and have sharp corners that make the composites prone to localised crack initiation and propagation. The embrittlement effect that occurs due to the presence of the hard ceramic particles causing increased local stress concentration sites may also be the reason [12].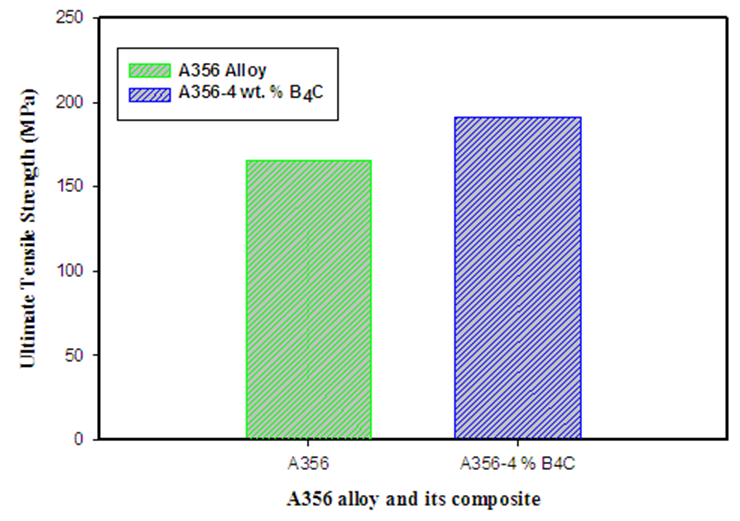 | Figure 3. Showing the ultimate tensile strength of as cast A356 alloy and A356-4wt. % B4C composite |
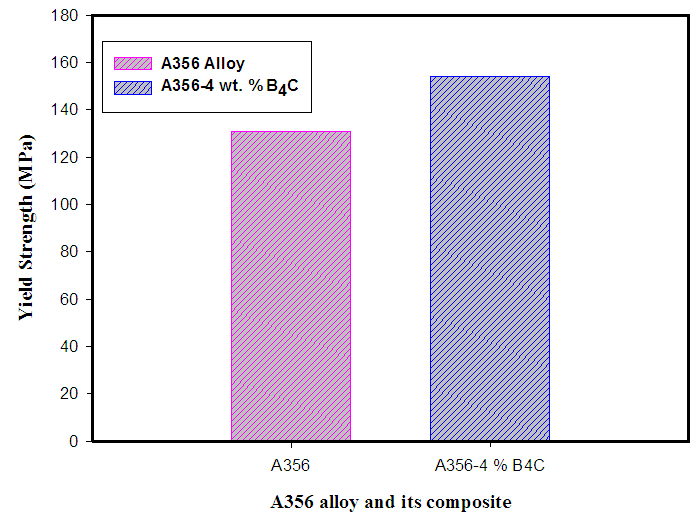 | Figure 4. Showing the yield strength of as cast A356 alloy and A356-4wt. % B4C composite |
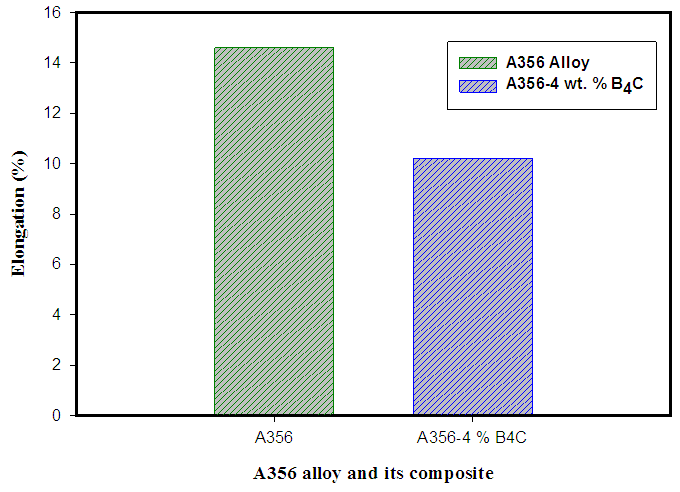 | Figure 5. Showing the percentage elongation of as cast A356 alloy and A356-4wt. % B4C composite |
4. Conclusions
This present research is centered on the development and characterization of the microstructure and tensile behavior of A356 alloy and its composites containing 4 wt. % of B4C micro particles. From the above results and discussion the following conclusions are made:1. From the liquid metallurgy techniques A356-B4C composites were prepared successfully.2. The scanning electron micrographs revealed the uniform distribution of B4C particulates in A356 base alloy.3. The ultimate tensile strength of A356 base alloy and A356-4% B4C composites were 166MPa and 191MPa respectively. This shown an improvement of 15%, when compared with the base alloy A356.4. The yield strength of A356 base alloy and A356-4% B4C composites were 131MPa and 154MPa respectively. This shown an improvement of 17%, when compared with the base alloy A356.5. The ductility of base alloy A356 reduced with the addition of hard ceramic B4C particulates.
References
[1] | Ezatpour, H. R., Sajjadi, S. A., Sabzevar, M. H., Huang, Y. Z., 2014, An investigation of the tensile and compressive properties of Al6061 and its nano composites in as-cast state and in extruded condition, Material Science & Engineering A, 607, 589-595. |
[2] | Baradeswaran, A., Elaya Perumal, A., 2014, Study on mechanical and wear properties of Al 7075/Al2O3/graphite hybrid composites, Composites: Part B, 56, 464-471. |
[3] | Suresh, S., Shenbaga Vinayaga Moorthi, N., Vettivel, S. N., Selvakumar, N., 2014, Mechanical behavior and wear prediction of stir cast Al-TiB2 composites using response surface methodology, Material and Design, 59, 383-396. |
[4] | Madeva Nagaral, Auradi, V., Kori, S. A., 2015, Microstructure and Mechanical Properties of Al6061-graphite Composites Fabricated by Stir-Casting Process, Applied Mechanics and Materials, 766-767, 308-314. |
[5] | Pattanashetty Basavaraja, Madeva Nagaral, Vidyashankar S., Auradi, V., 2015, Evaluation of Mechanical properties of Al2219-SiC-Graphite reinforced hybrid Composites, International Journal of Applied Engineering Research, 10, 9. |
[6] | Sankaranarayanan, S., Sabat, R.K., Jayalakshmi, S., Gupta, M., 2014, Microstructural evolution and mechanical properties of Mg composites containing nano B4C hybridized micro Ti particulates, Materials Chemistry and Physics, Vol. 143, 1178-1190. |
[7] | Suresh, S., Shenbaga, N., Vinayaga Moorthi, 2013, Process development in stir casting and investigation on microstructures and wear behavior of TiB2 on Al6061 MMC, Procedia Engineering, 64, 1183-1190. |
[8] | Baskaran, S., Anandkrishnan, V., Muthukannan Duraiselvam, 2014, Investigations on dry sliding wear behavior of in situ casted AA7075-TiC metal matrix composites by using Tagushi technique, Materials and Design, 60, 184-192. |
[9] | Yang Zhou, Naiqin Zhao, Chunsheng Shi, Enzuo liu, Xiwen Du, 2014, In situ processing and aging behaviors of MgAl2O4 spinel whisker reinforced 6061Al composite, Materials Science and Engineering A, 598, 114-121. |
[10] | Hamid Raja Ezatpour, Seyed Abolkarim Sajjadi, Mohsen Haddad Sabzevar, Yizhong Haung, 2014, Investigation of microstructure and mechanical properties of Al6061 nano-composite fabricated by stir casting, Materials and Design, 55, 921-928. |
[11] | Mohsen Hossein Zadeh, Omid Mirzaee, Peyman Saidi, 2014, Structural and mechanical characterization of Al based composite reinforced with heat treated Al2O3 particles”, Materials and Design, 54, 245-250. |
[12] | Shin, J. H., Choi, Bae, D. H., 2014, The structure and properties of 2024 aluminium composites reinforced with TiO2 nanoparticles, Materials Science and Engineering A, 607, 605-610. |