Manjunatha G.1, Nagesh S. N.1, Raji George1, Suraj Kamble2
1Dept. of Mechanical Engg., M.S.Ramaiah Institute of Technology, Bangalore, India
2Research student, M.S.Ramaiah Institute of Technology, Bangalore, India
Correspondence to: Manjunatha G., Dept. of Mechanical Engg., M.S.Ramaiah Institute of Technology, Bangalore, India.
Email: |  |
Copyright © 2016 Scientific & Academic Publishing. All Rights Reserved.
This work is licensed under the Creative Commons Attribution International License (CC BY).
http://creativecommons.org/licenses/by/4.0/

Abstract
This study investigated the effect of functionalized carboxyl graphene (FCG) on mechanical properties of epoxy composites. The different content of FCG (0.25-1.00 wt %) were added to epoxy resin. The functionalized carboxyl graphene epoxy composite is prepared using solution casting method at room temperature. The mechanical properties were studied and results shows the tensile strength and impact strength of the composites increased significantly with increasing FCG loading. A microstructure analysis using scanning electron microscope (SEM), which showed the interface between the FCG and the epoxy. The improved mechanical properties of composites are due to the uniform dispersion of FCG with epoxy resin and strong interfacial bonding as observed by SEM.
Keywords:
Composites, Solution cast method, Epoxy, FCG
Cite this paper: Manjunatha G., Nagesh S. N., Raji George, Suraj Kamble, Effect of Functionalized Carboxyl Graphene Dispersion on the Mechanical Properties of Epoxy Composites, American Journal of Materials Science, Vol. 6 No. 4A, 2016, pp. 47-50. doi: 10.5923/c.materials.201601.09.
1. Introduction
Epoxy is the most important thermosetting polymers used in wide range of application as adhesive, electronic encapsulants, coatings and including structural materials, tissue substitutes, flame retardant additives, the composites due to its outstanding performance, processability and low cost [1, 2]. However, epoxy resins are inherently brittle, which makes them vulnerable to micro-crack produced in service, and this limits their applications [3].Graphene is two-dimensional material consisting of sp2-hybridized carbons arranged in a honeycomb structure. The carbon atoms are strongly bonded in hexagonal plane but weakly bonded to normal the plane. It showed extraordinary mechanical properties, electrical conductivity, optical transparency and thermal property. It is expected that graphene reinforced polymer composites show important improvement in their mechanical properties, electrical and thermal conductivity and other thermo physical properties [4, 5].The main challenge in the fabrication of Graphene nanoplatelets (GNPs) based composites are achieving a homogeneous dispersion of GNPs in epoxy resin without damaging its structure and improving the quality of interface between the GNPs and matrix [6].To this end, efforts have been made to develop approaches to tackle processing issue associated with graphene based materials. Chemical functionalization of graphene could facilitate uniform dispersion and improve compatibly with polymer matrices. The presence of carboxylic functional group on functionalized graphene which may form covalent bonding with epoxy matrix further improves the interfacial bonding with epoxy leading to further improvement in mechanical properties [7].Roey Nadiv et al. [8] have been worked on functionalization of graphene, preserving the in plane of sp2 of the graphene, thereby both graphene and epoxy are compatible and strong. The results showed an enhancement in mechanical properties at low content of graphene. Chang Yeong Lee et al. [9] studied the silane functional on graphene oxide (GO) results in improvement in the bonding of carbon/epoxy composite. The average thickness of functionalized graphene oxide is more compared to GO and thus improved mechanical properties were obtained.Although there are very few studies on functionalization of GNPs in the literature, they are mainly focused on the electrical and thermal properties of resultant composites, while little attention has been given to their effect on the mechanical response of GNPs based composites.In this study, we investigated the effect of functionalized carboxyl graphene (FCG) on epoxy resin through using relatively simple casting method. The composites are prepared at different wt% (0.25, 0.5 and 1.0) of FCG reinforcing in epoxy. The mechanical properties are evaluated. The microstructure and dispersion of FCG in epoxy is analyzed using field emission scanning electron microscope.
2. Experimental
2.1. Materials
Graphene carboxyl is procured from United Nanotech Innovation Pvt. Ltd. Bangalore, India. An epoxy resin (Lapox L-12) based on bisophenol-A, with an epoxy equivalent weight of 182-192 gms/eq and hardener (K-6) was purchased from Atul Ltd Polymer Div. Gujarat, India. Acetone was purchased from Vasa Scientific Co. Bangalore India and used as-received.
2.2. Composite Preparation
The calculated amount of carboxyl graphene (0.5-2 g) was suspended in 5ml acetone using borosil beaker. The beaker was then covered and stirred using magnetic stirrer. Further addition of 10ml of acetone to the above mixture and sonicated using a probe sonicator (150V) for 20 min. During sonication the mixture is kept cool by using an ice bath. To remove acetone, the above suspension is subjected to infrared heating. The epoxy resin is then added and the mixture was sonicated for 1 hr. The hardener was added to mixture with constant stirring using mechanical stirrer at 250 rpm for 15 minute. The finally mixture was poured in silicone rubber mould and allowed 24 hours for curing at room temperature.
2.3. Measurements and Characterisations
Scanning electron microscopy (SEM) images were obtained by Zeiss Ultra 55. The SEM was used to examine fractured surface of specimens, which are coated with gold to form conductive layer. The tensile test was conducted according to ASTM D638 using Mecmesin Multi Tester. The dimensions of specimen are 57mm (gauge length) X 13mm (gauge width) X 3.2mm (thickness). He test was performed at a cross head speed of 5mm/min with 10KN load cell. The impact test was performed at room temperature according to ASTM D256. The dimension of rectangular specimen is 127(L) X 13(B) X 13(H). At least three specimens were tested for each samples.
3. Results and Discussions
3.1. Mechanical Property
The effects of carboxyl graphene addition influences on mechanical properties were experimentally investigated. The tensile and impact tests were conducted on specimen and various mechanical properties observed.The ultimate tensile stress and Young’s modulus of the composites are shown in the Fig. 1. In general, the results obtained that the incorporation of carboxyl graphene has improved the ultimate tensile stress and Young’s modulus. The tensile strength was improved by 3% at 0.25wt% of FCG. Further increased content of FCG also displayed higher ultimate tensile stress compared to pure epoxy but more immodest than the 0.25wt% of FCG. The ultimate tensile showed maximum improvement about 26% at 0.5 wt% compared to pure epoxy. The additional FCG content in epoxy, resulting UTS is decreased. At 1wt% of FCG, the UTS was obtained less than that of pure epoxy.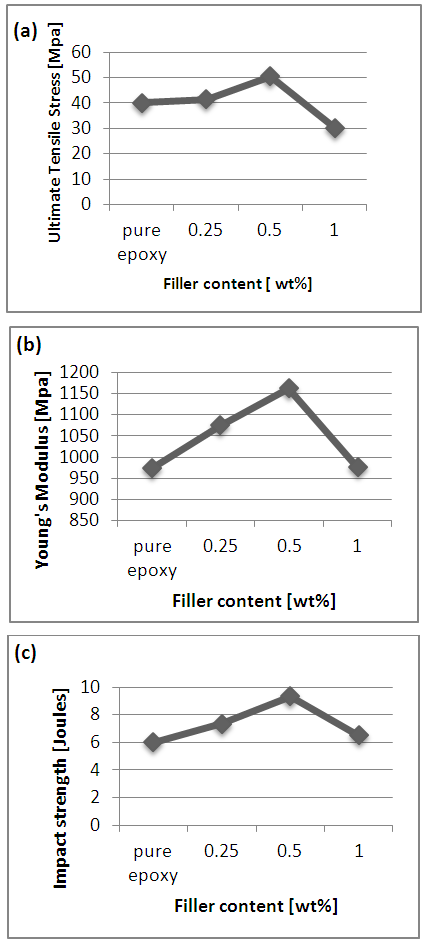 | Figure 1. The mechanical properties of pure epoxy and various composites (a) Ultimate tensile strength (b) Young’s modulus (c) Impact strength |
The Young’s modulus almost increases gradually as the content of FCG. This is mainly because of Young’s Modulus of FCG is 900 GPa and for epoxy is 4.4 GPa. The increase in the Young’s modulus at 0.25wt% is 11%. The highest Young’s modulus is ~20% at loading of FCG 0.5wt%. Further addition of FCG content which results in impairs Young’s modulus with previous one. At loading content of FGC at 1wt% the resultant Young’s modulus is approaches the Young’s modulus of epoxy value.The Charpy impact strength of the sample is function of carboxyl weight percentage from zero to 0.5wt% as shown in fig. 1c. The impact strength reaches maximum improvement about 55% compared to epoxy at 0.5wt% FCG. Similarly the improvement obtained at 0.25wt% and 1wt% is 22% and 11% respectively. At 0.5wt% of carboxyl graphene, the improvement of the mechanical property is up to the best. Since there is lots of oxygen containing functional groups, carboxyl graphene has good compatibility and well dispersion in epoxy resin. The large surface area of carboxyl graphene enhances the mechanical property significantly. When the FCG increased up to 1wt%, which leads to poor dispersion of carboxyl graphene in epoxy resin with increase in FCG content, stress concentration and agglomeration appears thus the mechanical strength decreases.
3.2. Morphological Characterization FCG/Epoxy Composites
Further to evaluate the dispersion and interface in epoxy resin of FCG were examined with scanning electron microscope (SEM).The pure epoxy resin exhibited typical brittle fracture surface and showed an oriented bamboo-like fracture patterns initialized from the cracks. The area between bamboo-like patterns was very smooth, featureless fracture surfaces [10].From the fig. 2a and 2b it can be seen that the quality dispersion of FCG in epoxy matrix and also interface between them was achieved. But the reason behind minimal improvement in properties of composite at this content is that the strength provider the FCG is not sufficient to offer optimum property to prepared composites.In the lower magnification image the uniform distribution and dispersion in different orientation of FCG in epoxy resin and also the smooth mirror like fracture pattern of pure epoxy is disturbed it can be seen in the fig. 2c.The fig. 2d shows the interface between the epoxy and FCG of composites. At this content of FCG, the strong interfacial bonding and good adhesion between the epoxy resin and FCG was obtained. Throughout composites the flows of epoxy resin is uniform and thus epoxy resin able to wet FCG efficiently. The cross linking density of epoxy resin and carboxyl group is on the graphene platelets obtained to be optimum. From this microstructure analysis it is clear that effective stress or load transfer from matrix to reinforcement or vice-versa, which leads to optimal mechanical properties at this content, is obtained.From the fig. 2e it can be seen that the concentration of FCG is more. At high filler content possibility of consumption of curing agent, thus the crosslinking density of epoxy resin is decreased. Because of this reason the flow of epoxy resin is restricted in formed agglomerates, which leads to formation of voids and cracks and thus responsible for early crack initiation. On the other hand, the formed agglomerates turned micrometer size which causes to reduce available surface area of FCG to form bond with epoxy resin. This may cause for worsening of the mechanical properties. From the higher magnification image the cracks, voids are obtained because of insufficient flow of epoxy matrix between the agglomerated clusters resulting early failure of composites as depicted in the fig 2f. 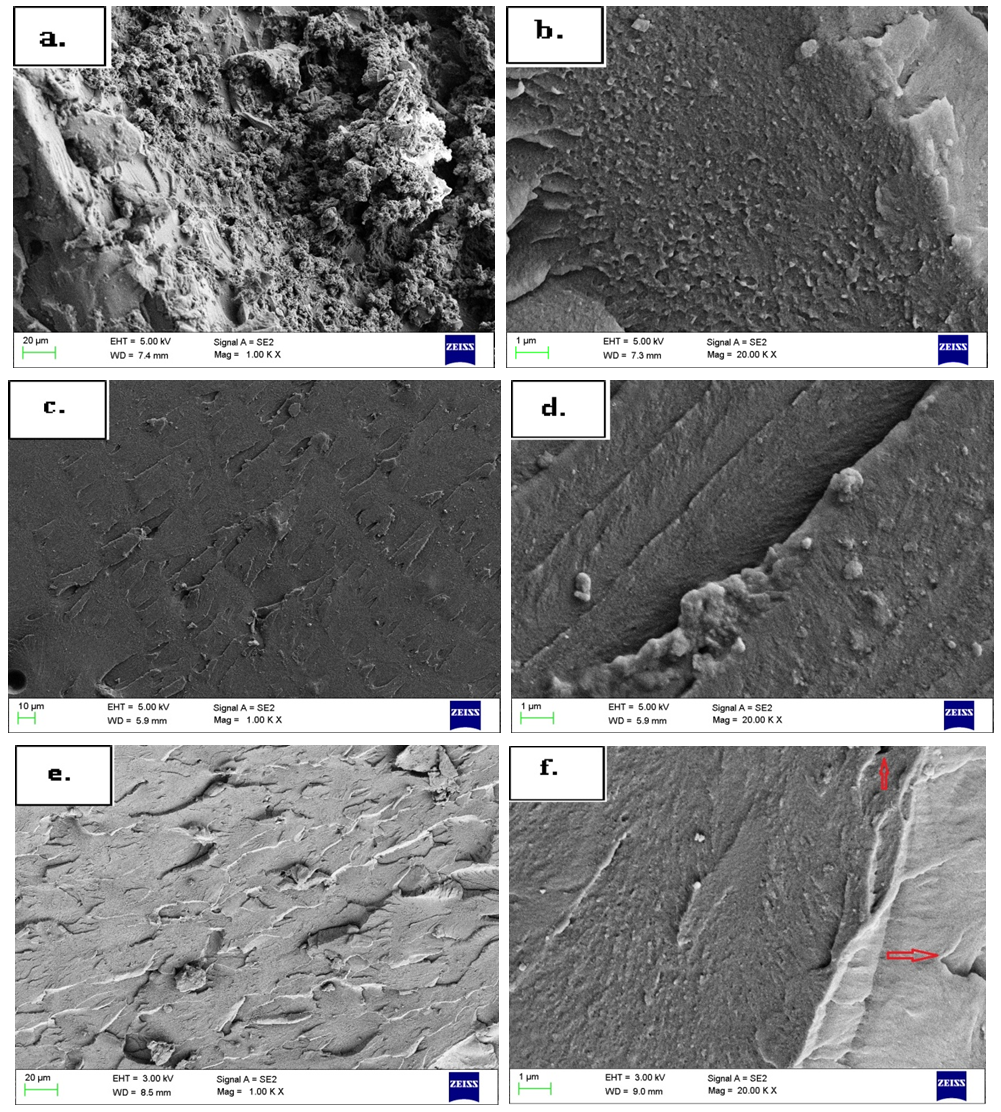 | Figure 2. SEM images of composites surface at different filler content and at different magnifications: (a & b) 0.25wt% FCG/epoxy, (c & d) 0.5wt% FCG/epoxy and (e & f) 1.0wt% FCG/epoxy composites |
4. Conclusions
The functionalized carboxyl graphene/epoxy composites have been fabricated and the effect of the FCG reinforcement has been examined for enhancing the mechanical properties of the epoxy resin. It is showed that the incorporation of FCG about 0.25wt% and 0.5wt% into epoxy resin can simultaneously enhance the mechanical properties such as ultimate tensile strength, Young’s modulus and impact strength of composites. The maximum improvement in the ultimate tensile strength, Young’s modulus and impact strength is 26%, 20% and 55% at 0.5wt% loading of FCG. The reason for this enhancement is the higher surface area, higher Young’s modulus of FCG and interface bonding between constitutes. Further the interface between the constituents and quality of dispersion examined by scanning electron microscope (SEM). Consequently the functionalized carboxyl graphene is a promising nano-material for improvement the mechanical properties of epoxy resin.
References
[1] | Yan-Jun Wan, Long-Cheng Tang, Li-Xiu Gong, Dong Yan, Yi-bao Li, Lian-Bin Wu, Jian-Xiong Jiang, Guo-Qiao Lai, Grafting of epoxy chain onto graphene oxide for epoxy composites with improved mechanical and thermal properties, Carbon 69 (2014) 467-480. |
[2] | Xi Zhang, Ouassima Alloul, Qingliang He, Jiahua Zhu, Michael Joseph Verde, Yutong Li, Suying Wei, Zhanhu Guo, Strengthened magnetic epoxy composites with protruding nanoparticles on the graphene nanosheets, Polymer 54 (2013) 3594-3604. |
[3] | Izzuddin Zaman, Tam Thanh Phan, Hsu-Chiang Kuan, Qingshi Meng, Ly Truc Bao La, Lee Luong, Osama Youssf, Jun Ma, Epoxy/graphene platelets composites with two levels of interface strength, Polymer 52(2011) 1603-1611. |
[4] | S.G. Prolongo, A. Jimenez-Suarez, R. Moriche, A. Urena, Graphene nanoplatelets thickness and lateral size influence on the morphology and behavior of epoxy composites, European polymer journal 53 (2014) 292-301. |
[5] | Rani Rohini, Prajakta Katti, Suryasarathi Bose, Tailoring the interface in graphene/thermoset polymer composites: A critical review, Polymer 70 (2015) A17-A34. |
[6] | B. Ahmadi-Moghadam, M. Sharafimasooleh, S. Shadlou, F. Taheri, Effect of functionalization of graphene nanoplateletes on the mechanical response of graphene/epoxy composites, Materials and Design xxx (2014) xxx-xxx |
[7] | Minoo Naebe, Jing Wang, Abbas Amini, Hamid Khayyam, Nishar Hameed, Lu Hua Li, Ying Chen & Bronwyn Fox, Mechanical property and structure of covalent functionalised graphene/epoxy composites, Mechanical and Structural Properties and Devices Nanoparticles (2014) Scientific report |4: 4375 | DOI; 10.1038/srep04375. |
[8] | Roey Nadiv, Michael Shtein, Matat Buzaglo, Sivan Pretz-Damari, Anton Kovalchuk, Tuo Wang, James M. Tour, Oren Regev, Graphene nanoribbon-polymer composites: the critical role of edge functionalization, Carbon 99 (2016) 444-450. |
[9] | Chang Yeong Lee, Ji-Hun Bae, Tea-Yoon Kim, Seung-Hwan Chang, Soo Young Kim, Using silane-functionalization graphene oxides for enhancing the interfacial bonding strength of carbon epoxy/composites, Composite: Part A 75 (2015) 11-17. |
[10] | Xiao Wang, Jie Jin, Mo Song, An investigation of mechanism of graphene toughening epoxy, Carbon 65 (2013) 324-333. |