Manjunatha G.1, Raji George1, Iranna Hiremath2
1Department of Mechanical Engineering, M.S.Ramaiah Institute of Technology, Bangalore, India
2Research Student, M.S.Ramaiah Institute of Technology, Bangalore, India
Correspondence to: Manjunatha G., Department of Mechanical Engineering, M.S.Ramaiah Institute of Technology, Bangalore, India.
Email: |  |
Copyright © 2016 Scientific & Academic Publishing. All Rights Reserved.
This work is licensed under the Creative Commons Attribution International License (CC BY).
http://creativecommons.org/licenses/by/4.0/

Abstract
The nanocomposites were prepared by solution cast technique (functionalized graphene mixed with epoxy resin). Several composites with different weight % (between 0 to 1 wt %) of functionalized graphene loading in epoxy were prepared with the aim of improving the bonding strength of functionalized graphene /epoxy composites. The mechanical properties were determined by measuring the impact strength and compression strength. The results obtained in this study indicated that the impact strength of the composites is improved by approximately 55% and compression strength improved by approximately 14% with the addition of fillers material. The Functionalized graphene fillers contributed to improved interfacial interaction between the epoxy resin and the fillers. The nanocomposites were characterized by SEM techniques. The bonding between graphene and epoxy resin is confirmed by microscopy observations.
Keywords:
Nanocomposites, Solution cast technique, Epoxy, Functionalized graphene
Cite this paper: Manjunatha G., Raji George, Iranna Hiremath, Functionalized Graphene for Epoxy Composites with Improved Mechanical Properties, American Journal of Materials Science, Vol. 6 No. 4A, 2016, pp. 41-46. doi: 10.5923/c.materials.201601.08.
1. Introduction
Epoxy resins based on diglycidyl ether of bisphenol A (DGEBA) have been widely used as matrices for advanced composites, coatings, structural adhesives, and microelectronics. These composites have many useful properties such as a high tensile strength and modulus, low shrinkage, good adhesion, high heat resistance, good dimensional stability, outstanding mechanical and insulating properties, and excellent chemical corrosion resistance. Epoxy resins are key materials in polymer engineering. In particular, these materials have relatively good thermal stability, combined with a high stiffness and strength and a low creep [1-3]. The various polymer matrices that are currently available, epoxy resins remain dominant for the development of high-performance materials because of their thermal stability, electrical, and mechanical properties [4-5].In this study, the functionalized graphene (FGr) is used as a nano filler and epoxy composite are prepared using solution intercalation method. The effect of nano filler on the mechanical properties of epoxy nanocomposites is discussed.Minoo Naebe et al, studied the functionalized graphene nanoplatelets by bingel reaction to improve their dispersion and interfacial bonding with an epoxy resin and characterized those functionalized graphene using microscopic, thermal and spectroscopic techniques. Nanocomposites were prepared using functionalized graphene and epoxy resin and was subjected to mechanical testing to compare the properties. Thermal analysis of functionalised graphene revealed a significantly higher thermal stability compared to graphene oxide. Inclusion of only 0.1 wt% of functionalised graphene in an epoxy resin showed increase in flexural strength and storage modulus. The improvement in mechanical properties of nanocomposites was due to uniform dispersion of functionalised graphene and strong interfacial bonding between modified graphene and epoxy resin as confirmed by microscopy observations [6].Santosh Kumar Yadav et al, have fabricated high performance polyurethane (PU) nanocomposites by incorporating functionalised graphene nano plates during polymerization. It was found that addition of 2% graphene nanoplatelets exhibited significant improvement in mechanical and thermal shape recovery properties. The modulus of functionalised graphene nanoplatelets /polyurethane nanocomposites at 2% graphene loading is 10 times greater than the pure PU. The reasons for this improved results indicates efficient load transfer between graphene and matrix. The composites demonstrated improved shape recovery to the extent of 96% which is significant and offers wider applications for these materials [7].Alireza Ashori et al, synthesized functionalised graphene oxide (FGO) using three different diamines, namely ethylenediamine (EDA), diaminodiphenyl sulfone (DDS) and P-Phenylenediamine (PPD) and reinforced them in epoxy adhesive. This was done to improve the bond strength of carbon fibre/epoxy composites. Tensile and flexural results were enhanced by addition of FGO. This is due to the excellent elastic modulus of FGO. It was observed that 0.3% wt of FGO addition effectively improved the overall composites mechanical performance. The failure mechanism of carbon fibers pulled out from the epoxy matrix observed from SEM images [8].
2. Experimental
2.1. Materials
Functionalised graphene used as the material for the preparation of nanocomposites. The functionalised graphene had purity of 99% and surface area of 160 m2/g were purchased from United Nanotech pvt.ltd, Bangalore, India. Epoxy resin (L-12) liquid based on bisphenol-A and amine based hardener K-6 was obtained from Atul ltd polymer division Gujarat, India. Acetone solvent was procured from Vasa Scientific Bangalore, India.
2.2. Preparation of Nanocomposites
Hydroxyl graphene was dispersed in acetone of 5ml by using magnetic stirrer for 20 min. Then the mixture was dispersed in acetone of 10 ml sonicated for 20 min under ice-bath to avoid unwanted heat generated during process. Then resulted functionalised graphene was heated by using infrared heater to remove acetone. The required amount of epoxy is calculated and mixed with above mixture by manual stirring and it is treated by sonication for 1 h under ice-bath. The curing agent was added to the mixture in the ratio 10:1 and mixed for 10 min under ice-bath to prevent premature curing. The prepared mixture was transferred to an open mold and cured at room temperature for 24 hr to get the nanocomposites samples. Similarly the epoxy nanocomposites containing functionalised graphene with different weight fractions were prepared. The pure epoxy sample was also prepared under room temperature condition.
3. Results and Discussion
3.1. Compression Properties
Compression test was performed using Universal Testing Machine according to ASTM D695 standard for 5 specimens by varying the wt% of nano particles (0.0, 0.25, 0.5, and 1.0)The results of compression test are tabulated in Table 1. The compression strength increased gradually with increasing functionalised graphene content up to 0.50%, and then it is decreased with further addition of functionalised graphene. It was found that 0.5 wt% of nano particles showed higher compression value compared with pure epoxy and specimens content of 0.25 wt% and 1.0 wt% of nano particles.
3.2. Impact Properties
Charpy test was performed using Impact testing machine according to ASTM D256 standard for 5 specimens by varying the wt% of nano particles (0.0, 0.25, 0.5, and 1.0)The results of charpy test are tabulated in Table 2. The impact strength increased gradually with increasing functionalised graphene content upto 0.5%, and then it is decreased gradually with further increase in functionalised graphene content. It was found that all specimens of content 0.5 wt% of nano particles showed higher impact strength compared with pure epoxy and specimens content of 0.25 wt% and 1.0 wt% of nanoparticles. The higher compression strength and impact strength at 0.5 wt% due to uniformly distributed in the functionalized graphene/epoxy nanocomposites with very less agglomerates.Table 1. Compression strength for FGr/Epoxy composites 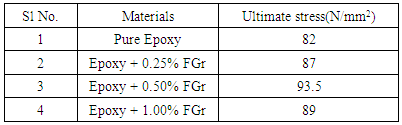 |
| |
|
Table 2. Impact strength for FGr/Epoxy composites 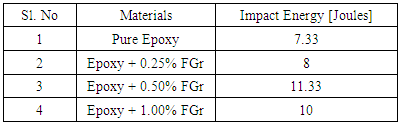 |
| |
|
3.3. Characterization of Epoxy Nanocomposites
Functionalised graphene epoxy nanocomposites were examined by Scanning Electron Microscope (SEM) in order to observe the distribution of functionalsed graphene in the epoxy matrix. The samples with functionalised graphene wt% (0.25, 0.50, 1) were examined. The SEM for 0.25, 0.50, and 1 wt% functionalised graphene/epoxy nano composites taken at 5000X and 20,000X magnification level is shown in fig 1, 2, and 3.In fig 1(a) & 1(b) the particles of functionalised graphene are not properly dispersed due to an vander walls forces.In fig 2(a) & 2(b) indicates that functionalised graphene are uniformly dispersed in the FGr/epoxy nanocomposites with very less agglomerates. In fig 3(a) & 3(b) the particles of functionalised graphene formed cluster due to poor distribution and poor interficial bonding between epoxy and nano material was observed.
4. Conclusions
1. The polymer nanocomposites were developed using solution casting method at room temperature.2. The additions of 0.50 wt% of functionalized graphene resulted in the improvement of compression and impact strength as compared to the pure epoxy and other wt% of functionalized graphene samples.3. The specimen of 0.50 wt% functionalized graphene shows increase in properties by 14% and 55% for compression and impact strength as compared to pure epoxy.4. At 0.50 wt % functionalized graphene content, the functionalized graphene had uniformly distributed in the functionalized graphene/epoxy nanocomposites with very less agglomerates.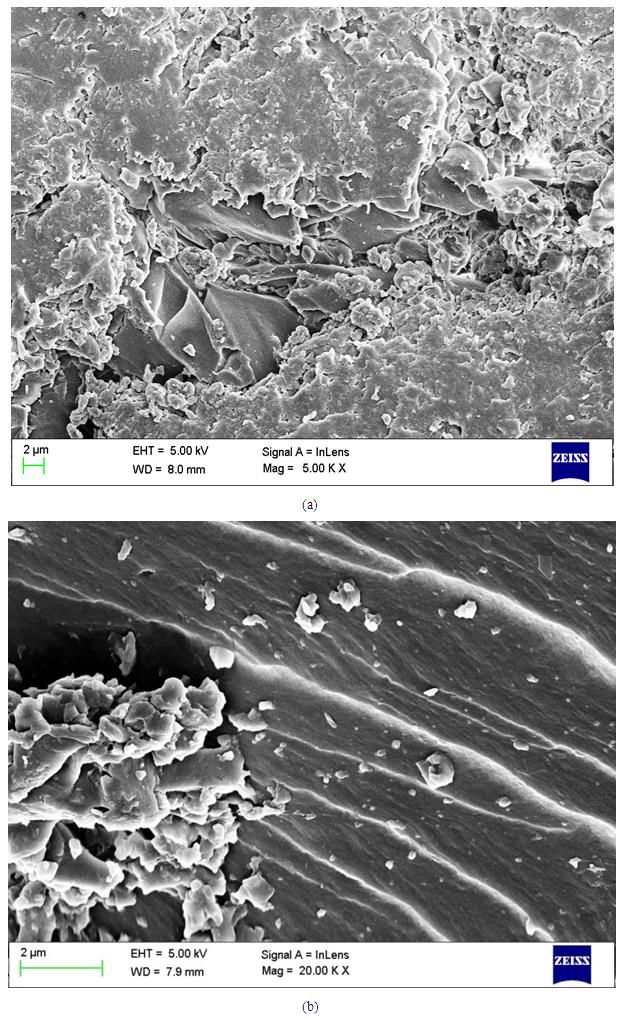 | Figure 1. (a) and (b): SEM microstructure of 0.25% Functionalised graphene at 5,000X and 20,000X magnification level |
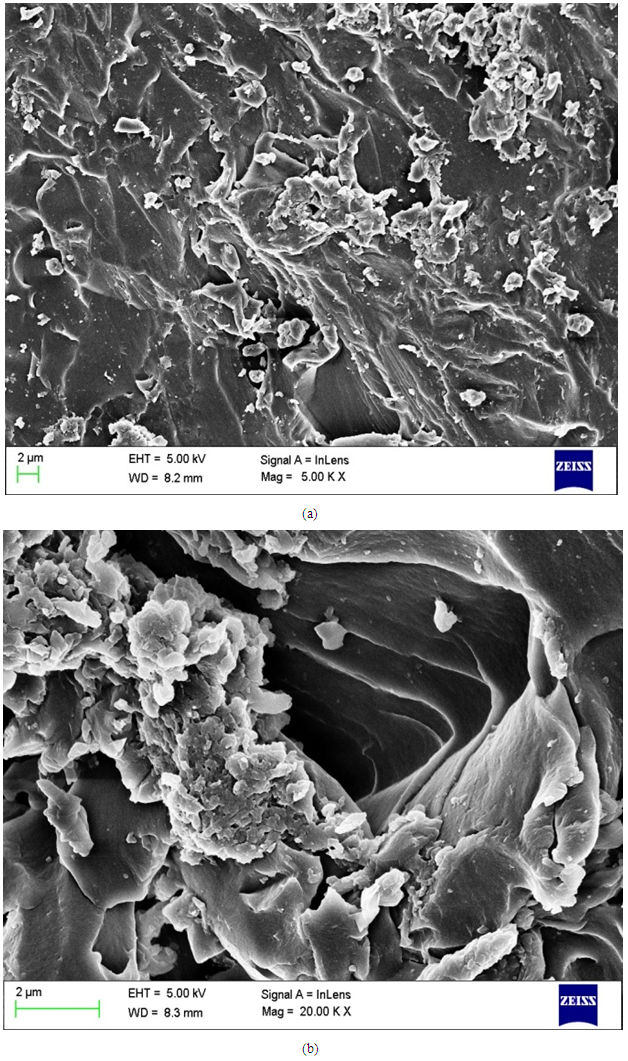 | Figure 2. (a) and (b): SEM microstructure of 0.50% Functionalised graphene at 5,000X and 20,000X magnification level |
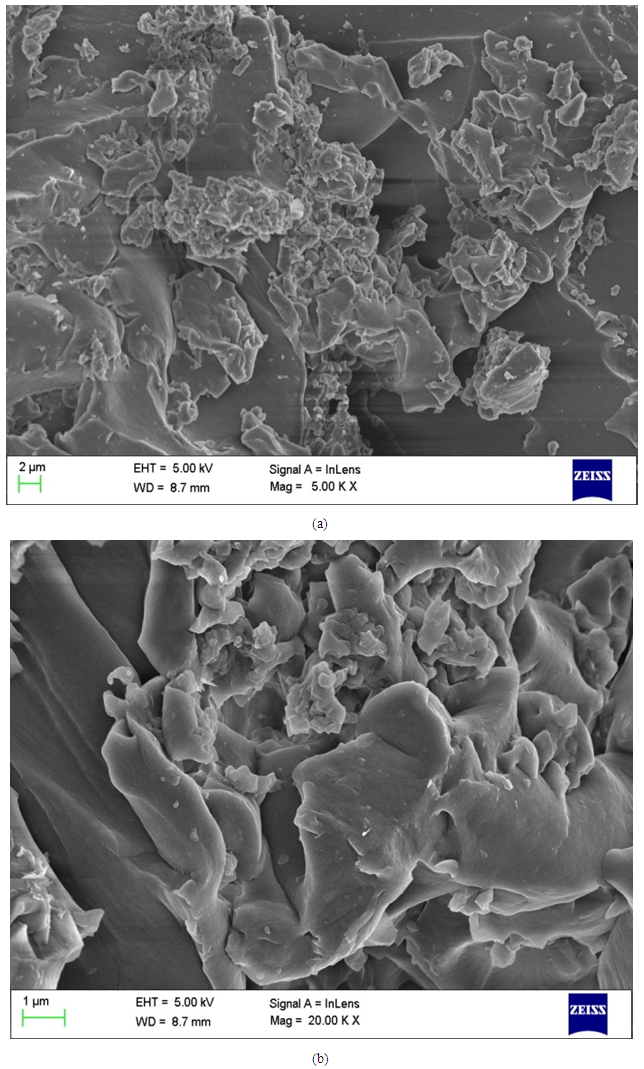 | Figure 3. (a) and (b): SEM microstructure of 1.0% Functionalised graphene at 5,000X and 20,000X magnification level |
References
[1] | Jerzy J. Chru´sciel El˙zbieta Le´sniak Modification of epoxy resins with functional silanes, polysiloxanes, silsesquioxanes, silica and silicates, Polymer science 41 (2014). 67-121. |
[2] | Asif Abdul Azeez, Kyong Yop Rhee, Soo Jin Park, David Hui, Epoxy clay nanocomposites – processing, properties and applications, Composites: Part B 45 (2013) 308–320. |
[3] | Soo-Jin Park, Fan-Long Jin, Thermal stabilities and dynamic mechanical properties of sulfone-containing epoxy resin cured with anhydride, Polymer Degradation and Stability 86 (2004) 515-520. |
[4] | K.S. Novoselov, A.K. Geim, S.V. Morozov, D. Jiang, Y. Zhang, S.V. Dubonos, et al., Electric field effect in atomically thin carbon films, Science 306 (2004) 666–669. |
[5] | X. Wang, Y. Hu, L. Song, H. Yang, W. Xing, H. Lu, In situ polymerization of graphene nanosheets and polyurethane with enhanced mechanical and thermal properties, Journal of Materials Chemistry 21 (2011) 4222–4227. |
[6] | Minoo naebe, Jing Wang, Abbas Amini, Hamid Khayyam, Nishar Hameed, Lu Hua Li, Mechanical property and structure of covalent functionalized grapheme/epoxy nanocomposites, Scientific reports 4 (2014) 4375. |
[7] | Santosh Kumar Yadav, Jae Whan Cho, Functionalized graphene nanoplatelets for enhanced mechanical and thermal properties of polyurethane nanocomposites, Journal of Polymer Science Part B: Polymer Physics 51 (2013) 39-47. |
[8] | Alireza Ashori, Hossein Rahmani, Reza Bahrami, Preparation and characterization of functionalized grapheme oxide/carbon fibre/epoxy nanocmposites, Polymer Testing 48 (2015) 82-88. |