Suresh S. Bujari1, R. V. Kurahatti2
1Department of Mechanical Engineering, Agadi College of Engineering and Technology, Laxmeswar, India
2Department of Mechanical Engineering, Basaveshwar Engineering College, Bagalkot, India
Correspondence to: Suresh S. Bujari, Department of Mechanical Engineering, Agadi College of Engineering and Technology, Laxmeswar, India.
Email: |  |
Copyright © 2016 Scientific & Academic Publishing. All Rights Reserved.
This work is licensed under the Creative Commons Attribution International License (CC BY).
http://creativecommons.org/licenses/by/4.0/

Abstract
The work is carried out to investigate and study the microstructure and tensile behavior of B4C reinforced Al-4.5% Cu alloy metal matrix composites. In the present work Al-4.5% Cu alloy was taken as the base matrix and B4C particulates as reinforcement material to prepare metal matrix composites by stir casting method. For metal matrix composites the reinforcement material was varied from 0 to 4 wt. % in steps of 2 wt. %. For each composite, the reinforcement particulates were preheated to a temperature of 300°C and dispersed into a vortex of molten Al-4.5% Cu alloy. The microstructural characterization was done using scanning electron microscope. Tensile properties like ultimate tensile strength and yield strength were evaluated as per ASTM standards. Further, scanning electron microphotographs revealed that there was uniform distribution of B4C particulates in Al-4.5% Cu alloy matrix. Ultimate tensile strength and yield strength increased as wt. % of B4C increased in the base matrix.
Keywords:
Al-4.5%Cu alloy, B4C, Microstructure, Ultimate Strength, Yield Strength
Cite this paper: Suresh S. Bujari, R. V. Kurahatti, Microstructure and Tensile Behavior of B4C Particulates Reinforced Al-4.5% Cu Alloy Composites, American Journal of Materials Science, Vol. 6 No. 4A, 2016, pp. 36-40. doi: 10.5923/c.materials.201601.07.
1. Introduction
Conventional monolithic materials have limitations with respect to achievable combinations of strength, stiffness, and density. In order to overcome these shortcomings and to meet the ever-increasing engineering demands of modern technology, Metal Matrix Composites (MMCs) are gaining importance. In recent years, discontinuously reinforced aluminium (DRAMMCs) based metal matrix composites have attracted worldwide attention as a result of their potential to replace their monolithic counterparts primarily in automobile and energy sector.The conventional aluminum alloys do not always provide the required properties under all service conditions which are overcome by reinforcing those alloys with ceramic particles. Such reinforced aluminum alloys are universally known as AMCs [1-3]. AMC refer to a class of light weight high performance aluminum centric material systems. In the present scenario, aluminum is the one of the most popular matrix for the metal matrix composites [4]. Amongst metal matrix composites, AMCs have received particular attention in the past three decades due to their high specific strength and stiffness and superior wear resistance. AMCs are widely used in aerospace, automobile, marine etc. There are some advantages in using particles reinforced AMC’s materials than unreinforced materials such as - greater strength, high specific modules, improved stiffness, light weight, low thermal expansion coefficients, high thermal conductivity, tailored electrical properties, increased wear resistance, improved damping capabilities [5].AMCs when compared to unreinforced alloy have better properties such as greater strength, improved stiffness, reduced density, good corrosion resistance, improved high temperature properties, controlled thermal expansion coefficient, thermal/heat management, enhanced and tailored electrical performance, improved wear resistance and improved damping capabilities. The most commonly employed Metal Matrix Composites (MMCs) consists of aluminium alloy reinforced with hard ceramic particles usually silicon carbide, alumina and soft particles usually graphite, talc.Depending on their application, the composite materials are characterized, in relation to the matrix, by improved wear resistance, high strength properties, proper sliding characteristics, resistance to thermal shocks and fatigue phenomena with consideration of reduced weight of the final product. Therefore the application of hard ceramic particles reinforced composites depends on technological properties of composite but also the costs of its manufacturing and ecological aspect of the product.Among the various matrix materials available, aluminium alloys are promising materials due to their high specific strength and stiffness. However, their applications are restricted because of their poor wear resistance.Particulate reinforced aluminium matrix composites are now being considered for their superior mechanical and tribological properties over the conventional alloys, and therefore, these composites have gained extensive applications in automotive and aerospace industries. The emphasis has been given on developing affordable Al-based MMCs with various hard and soft reinforcements like SiC, Al2O3, B4C, Zircon, Tungsten Carbide, Graphite and Mica [6].The primary function of the reinforcement in MMCs is to carry most of the applied load, where the matrix binds the reinforcements together, and transmits and distributes the external loads to the individual reinforcement [7]. Good wetting is an essential condition for the generation of a satisfactory bond between particulate reinforcements and liquid Al metal matrix during casting composites, to allow transfer and distribution of load from the matrix to the reinforcements without failure [8].It is proven that the ceramic particles are effective reinforcement materials in aluminium alloy to enhance the mechanical and other properties. The reinforcement in MMCs are usually of ceramic materials, these reinforcements can be divided into two major groups, continuous and discontinuous. The MMCs produced by them are called continuously (fiber) reinforced composites and discontinuously reinforced composites. However, they can be subdivided broadly into five major categories: continuous fibers, short fibers (chopped fibers, not necessarily the same length), whiskers, particulate and wire (only for metal). With the exception of wires, reinforcements are generally ceramics, typically these ceramics being oxides, carbides and nitrides. These are used because of their combinations of high strength and stiffness at both room and elevated temperatures.Many modern fabrication techniques where in use for the manufacture of MMC materials according to the type of base material and the type of reinforcement used like stir casting; squeeze casting, liquid metal infiltration and spray co-deposition [9]. Among the above, stir casting technique is the simplest and most economical used technique is known as ‘vortex technique’ or stir casting technique’ it is attractive because of simplicity, low cost of processing, flexibility, most economically for large sized components to be prepared as well as production of near net shaped components.In this study, an attempt has been made to prepare Al-4.5Cu alloy composites by adding 2 and 4 wt. % of B4C particulates. Al-4.5Cu-B4C composites were prepared by stir casting process. Further, prepared samples were tested for microstructure and tensile behavior as per ASTM standards.
2. Experimental Details
2.1. Materials Used
Metal matrix composites containing 2 and 4 weight percentages of B4C particles were produced by liquid metallurgy route. For the production of MMCs, an Al-4.5%Cu alloy was used as the matrix material while B4C were used as the reinforcements. The theoretical density of matrix material Al-4.5% Cu alloy is 2.80g/cm3 and reinforcement particulates B4C density is 2.52g/cm3.
2.2. Synthesis of Composites
The B4C particle reinforced Al-4.5% Cu alloy metal matrix composites have been produced by using a vortex method. Initially calculated amount of Al-4.5% Cu alloy was charged into SiC crucible and superheated to a temperature 750°C in an electrical resistance furnace. The furnace temperature was controlled to an accuracy of ±20 degree Celsius using a digital temperature controller. Once the required temperature is achieved, degassing is carried out using solid hexachloroethane (C2Cl6) to expel all the absorbed gases [10]. The melt is agitated with the help of a zirconia coated mechanical stirrer to form a fine vortex. A spindle speed of 300 rpm and stirring time 3-5 min. were adopted. The B4C particulates were preheated to a temperature of 500 degree Celsius in a pre-heater to increase the wettability. The pre-heated B4C particles introduced into melt in steps of two at constant feed rate of 1.2-1.4 g/sec. After holding the melt for a period of 5 min., the melt was poured from 720 degree Celsius into a preheated cast iron mould having dimensions of 125mm length x 15mm diameter.
2.3. Testing of Composites
The microstructure of the as cast Al-4.5% Cu alloy and its composites reinforced with different wt. % of B4C particulates were examined by using scanning electron microscope. The samples of as cast and Al-4.5Cu-B4C composites for microstructural study were cut from casted rods and ground by means of abrasive papers followed by rotating disc cloth polishing. Keller’s reagent was used as an etching agent.Tensile testing of the prepared samples were conducted in accordance with the ASTM E8 standard on round tension test specimens of gauge diameter 9mm and gauge length 45mm. Tension test was conducted by using Instron made servo-hydraulic machine, with cross head speed set at 0.280mm/min. The experiments were conducted at room temperature. Stress versus strain graph was plotted to know the effect of B4C particulates on tensile behaviour of Al-4.5%Cu alloy composites. Figure 1 shows the dimensions of tensile test specimen used in the study.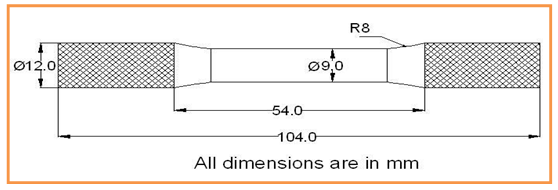 | Figure 1. Showing the dimensions of tensile test specimen |
3. Results and Discussion
3.1. Microstructural Studies
Figure 2 (a-c) shows the SEM microphotographs of Al-4.5% Cu alloy as cast and Al-4.5Cu with 2 and 4 wt. % of B4C particulate composites. This reveals the uniform distribution of B4C particles and very low agglomeration and segregation of particles, and porosity.Figure 2 b-c clearly show and even distribution of B4C particles in the Al-4.5% Cu alloy matrix. In other words, no clustering of B4C particle is evident. There is no evidence of casting defects such as porosity, shrinkages, slag inclusion and cracks which is indicative of sound castings. In this, wetting effect between particles and molten Al-Cu alloy matrix also retards the movement of the B4C particles, thus, the particles can remain suspended for a long time in the melt leading to uniform distribution.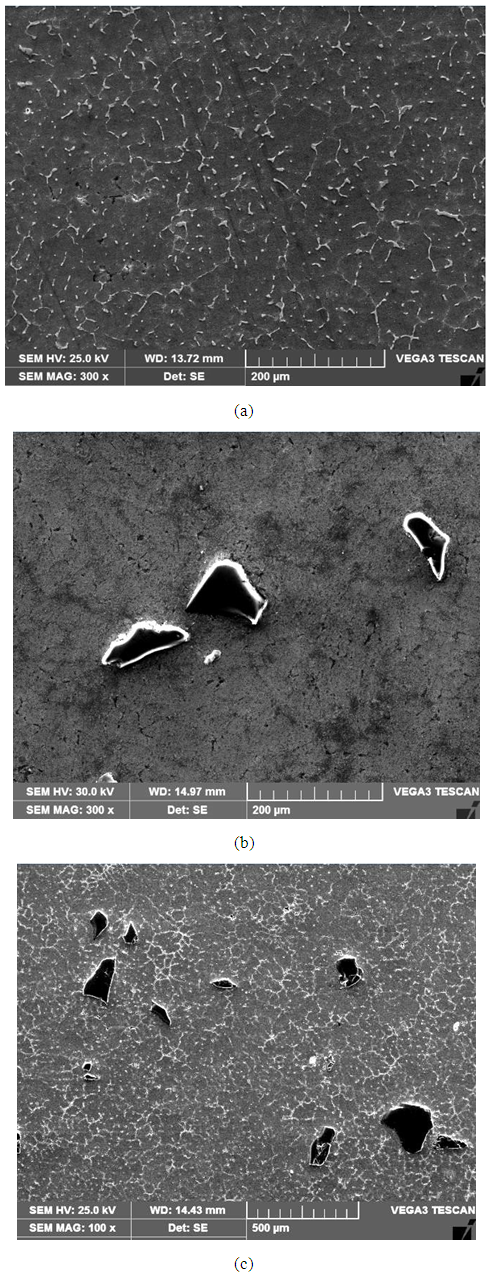 | Figure 2. Showing the SEM microphotograph of (a) as cast Al-4.5% Cu alloy (b) Al-4.5% Cu Alloy -2 wt. % B4C (c) Al-4.5% Cu Alloy -4 wt. % B4C |
Figure 3 show energy dispersive X-Ray spectrograph of Al-4.5% Cu alloy – 4 wt. % of B4C composite. The EDS analysis confirmed the presence of B4C particulates in the Al matrix alloy. The presence of B4C shows in the form of B (Boron) and C (Carbon), which is evident from the EDS spectrum.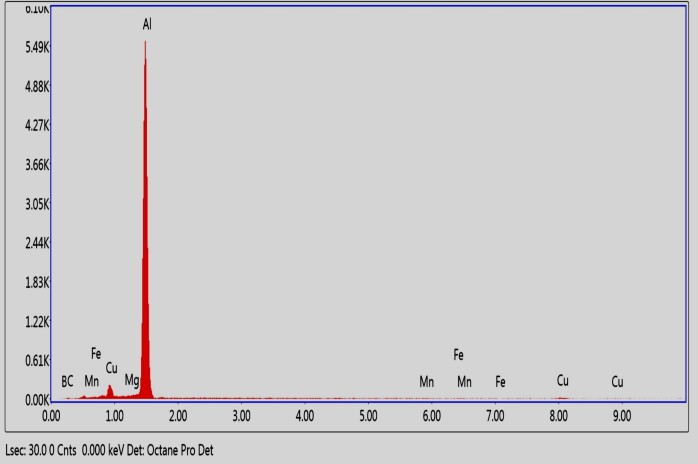 | Figure 3. EDS analysis of Al-4.5% Cu alloy – 4 wt. % B4C composite |
3.2. Tensile Behavior
Figure 4 shows variation of ultimate tensile strength (UTS) with 2 and 4 wt. % of B4C particulates. The ultimate tensile strength of Al-4.5% Cu - 4 wt. % B4C composite material increases by an amount of 14.6% as compared to as cast Al-4.5%Cu alloy matrix. The microstructure and properties of hard ceramic B4C particulates control the mechanical properties of the composites. Due to the strong interface bonding load from the matrix transfers to the reinforcement exhibiting increased ultimate tensile strength [11].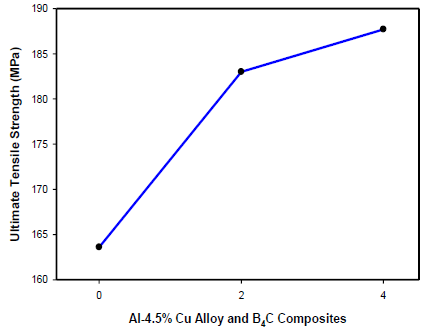 | Figure 4. Variation in ultimate tensile strength with wt. % of B4C particulates |
This increase in UTS mainly is due to B4C particles acting as barrier to dislocations in the microstructure. The improvement in UTS may be due to the matrix strengthening following a reduction in Al-4.5%Cu-B4C grain size, and the generation of a high dislocation density in the Al-Cu alloy matrix a result of the difference in the thermal expansion between the metal matrix and the B4C reinforcement.Figure 5 shows variation of yield strength (YS) of Al-4.5%Cu alloy matrix with 2 and 4 wt. % of B4C particulate reinforced composite. It can be seen that by adding 4 wt. % of B4C particulates yield strength of the Al-4.5%Cu alloy increased from 145 MPa to 165 MPa. This increase in yield strength is in agreement with the results obtained by several researchers [12], who reported that the strength of the particle reinforced composites is more strongly dependent on the volume fraction of the reinforcement. The increase in YS of the composite is obviously due to presence of hard B4C particles which impart strength to the soft aluminium matrix resulting in greater resistance of the composite against the tensile stress. In the case of particle reinforced composites, there is a restriction to the plastic flow due to the dispersion of the hard particles in the matrix, thereby providing enhanced strength to the composite.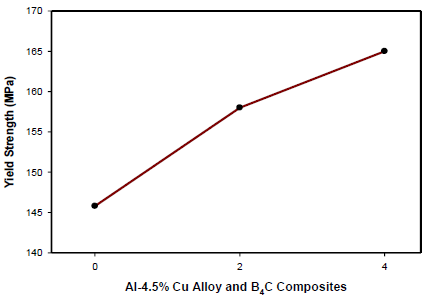 | Figure 5. Variation in yield strength with wt. % of B4C particulates |
Figure 6a-c shows stress versus strain plots of as cast Al-4.5% Cu alloy and Al-4.5%Cu alloy with 2 and 4 wt. % of B4C particulates reinforced composites. Stress values for Al-Cu alloy increased from 164 MPa to 188 MPa after addition of 4 wt. % of B4C particulates. This increase in stress is mainly due to presence hard B4C particulates in the Al-Cu alloy matrix, these particulates acts as the load barrier member during tension test.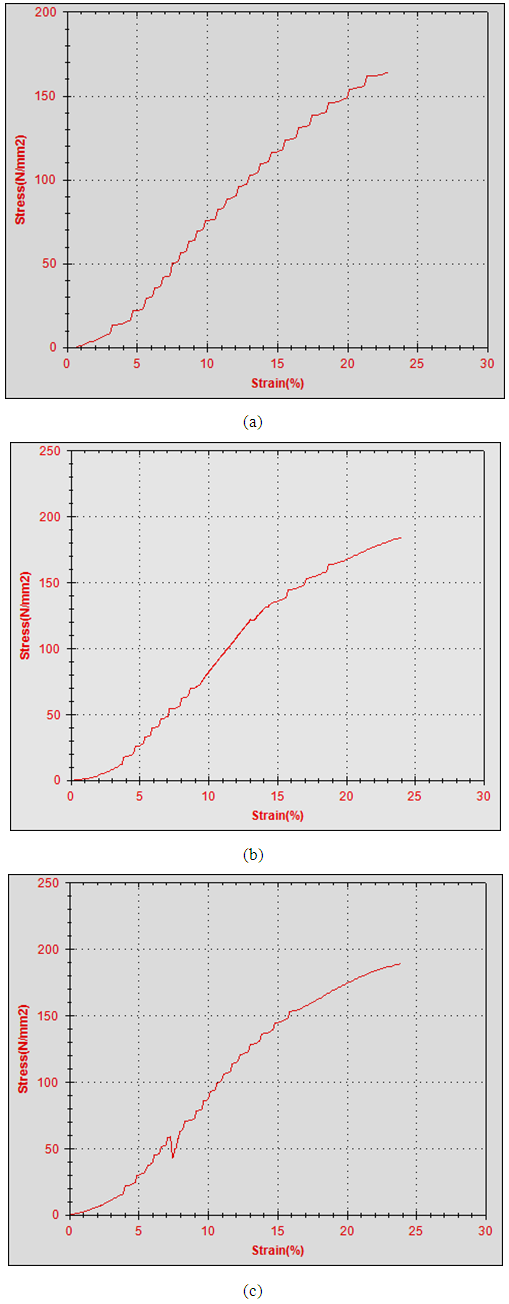 | Figure 6. Showing stress Vs strain plots of (a) Al-4.5%Cu alloy (b) Al-4.5%Cu alloy – 2wt. % B4C (c) Al-4.5%Cu alloy – 4 wt. % B4C composite |
4. Conclusions
The results of the study of microscopic structure and tensile behavior of the Al-4.5% Cu alloy – 2 and 4 wt. % of B4C composites materials produced by stir casting are remarked as below: The liquid metallurgy technique was successfully adopted in the preparation of Al-4.5% Cu alloy – 2 and 4 wt. % of B4C composites. The microstructural studies revealed the uniform distribution of the B4C particulates in the Al-4.5% Cu alloy matrix and EDS analysis confirmed the presence of B4C particulates in the matrix. The ultimate tensile strength and yield strength properties of the composites found to be higher than that of base matrix. The improvements in UTS and YS by adding 4 wt. % of B4C was increased by 14.6% and 13.7% respectively. Stress value of Al-4.5%Cu alloy increased from 164MPa to 188 MPa after addition of 4 wt. % of B4C particulates.
References
[1] | Hasim, J., Looney, L., M. S. J. Hashmi, M. S. J., 1999, Metal matrix composites production by the stir casting method, Journal of Materials Processing Technology, 92-93, 1-7. |
[2] | Sahin, Y., 2003, Preparation and some properties of SiC particle reinforced aluminium alloy composites, Materials and Design, 24,671-679. |
[3] | Madeva Nagaral, Auradi, V., Kori, S. A., 2014, Dry sliding wear behavior of graphite reinforced Al6061 alloy composites, Applied Mechanics and Materials, Vol.592-594,170-174. |
[4] | Sudarshan, Surappa, M. K., 2008, Dry sliding wear of fly ash particle reinforced A356 Al composites, Wear, 265, 349-360. |
[5] | Umanath, K., Palanikumar, K., Selvamani, S. T., 2013, Analysis of dry sliding wear behavior of Al6061-SiC-Al2O3 hybrid metal matrix composites, Composites Part-B, 53, 159-168. |
[6] | Ramesh, C. S., Keshavamurthy, R., Channabasappa, B. H., Promod, S., 2010, Friction and wear behaviour of Ni-P coated Si3N4 reinforced 6061-Al composites, Tribiology Int., 43, 623-624. |
[7] | Suresh, S., Shenbaga V. M., Vettivel, S.C., and Selvakumar, N., 2014, Mechanical behaviour and wear prediction of stir cast Al-TiB2 composites using response surface methodology, Materials and Design, 59, 383-396. |
[8] | Madeva Nagaral, Bharath, V., and Auradi, V., 2013, Effect of Al2O3 particles on mechanical and wear properties of 6061al alloy metal matrix composites, Materials Science and Engineering, 2:1. |
[9] | Vijay, R., Elanchezhian, C., Jaivignesh, M., Rajesh, S. and Parswajinan, C., 2014, Evaluation of mechanical properties of aluminium alloy alumina boron carbide metal matrix composites, Materials and Design, Vol. 58, 332-338. |
[10] | Nagaral, M., Attar, S., Reddappa, H. N., Auradi, V., Suresh Kumar and Raghu, S., 2015, Mechanical behaviour of Al7025-B4C particulate reinforced composites, Journal of Applied Mechanical Engineering, 4:6. |
[11] | Shorowordi, K. M. and Laoui, T., 2001, Microstructure and interface characteristics of B4C, SiC and Al2O3 reinforced Al matrix composites: A comparative study, 4th International Conference on Mechanical Engineering, December 26-28, Dhaka, Bangladesh, 175-181. |
[12] | Harichandran, R. and Selvakumar, N., 2016, “Effect of nano/micro B4C particles on the mechanical properties of aluminium metal matrix composites fabricated by ultrasonic cavitation assisted solidification process”, Archives of Civil and Mechanical Engineering, 16, 147-158. |