Poornesh M.1, Harish N.2, Kiran Aithal2
1Department of Mechanical Engineering, St Joseph Engineering College, Mangaluru, India
2Department of Mechanical Engineering, Nitte Meenakshi Institute of Technology, Bengaluru, India
Correspondence to: Poornesh M., Department of Mechanical Engineering, St Joseph Engineering College, Mangaluru, India.
Email: |  |
Copyright © 2016 Scientific & Academic Publishing. All Rights Reserved.
This work is licensed under the Creative Commons Attribution International License (CC BY).
http://creativecommons.org/licenses/by/4.0/

Abstract
In this paper an effort has been made to study the properties of composites made using Al-18wt%Si as the base alloy and SiC particles as the reinforcement. The composite was prepared using a combination of stir casting with bottom pouring technique and centrifugal casting. The prepared samples where then checked for various mechanical and tribological properties and were then compared with that of the base alloy produced using centrifugal casting. It was seen that, the introduction of the SiC particles have improved the mechanical and tribological properties of the base alloy.
Keywords:
Stir Casting, Aluminium alloys, Mechanical, Tribological
Cite this paper: Poornesh M., Harish N., Kiran Aithal, Mechanical and Tribological Properties of Centrifugally Cast Al-Si-SiC Composites, American Journal of Materials Science, Vol. 6 No. 4A, 2016, pp. 31-35. doi: 10.5923/c.materials.201601.06.
1. Introduction
Functionally Graded Materials (FGM) is a new class of materials that has been successfully produced and being used as a major element in many of the industrial equipment’s like beams, plates and shell like structures. The main reason of using FGM is because the material properties vary continuously and smoothly through the thickness coordinates. The gradual change in properties can be tailored to specific applications for example, those in which high wear resistance and high bulk toughness are required. FGM refer to the composite materials where the composition or the microstructure is locally varied so that a certain variation of the local material properties is achieved. In a typical FGM, the volume fractions of the constituents are varied gradually over a macro-scale geometrical dimension such as coating thickness [1].Aluminium alloys are favourable as structural materials because of their high specific strength and stiffness. Due to this they are being used in automobile industries as basic constituents of internal combustion engines like cylinder blocks, cylinder heads and pistons [2]. The Al-Si alloys are most common among all the commercially available aluminium alloys. This is because of their extensively useful features like high strength to weight ratio, exceptional castability, low coefficient of thermal expansion and good corrosion resistance. [3] Stir casting technique is the most promising method for making particulate reinforced aluminium alloy composite because of its simplicity and flexibility to all shapes of castings and stir casting is generally accepted processing route which is practiced commercially. Chirita [4] have examined the difference in the properties of Al-Si alloys when produced in gravity casting and centrifugal casting. The properties of the alloys were dependant on: (a) centrifugal pressure; (b) vibration induced; (c) fluid dynamics and (d) the silicon content present in the melt. Sakthivel [5] have found that the presence of SiC particles in the composite has improved the hardness, density as well as the tensile strength. The particle size of the SiC particles also influences the properties of the composites. Mazahery [6] showed that the addition of SiC as the reinforcing particles will not only increase the hardness but will also improve the wear resistance of the composite. The increase in particle size as well as increase in the particle content has shown a substantial improvement towards the betterment of the wear resistance. Das [7] found that wear resistance offered by the SiC reinforced Al composites is higher than the Al alloys. Sandeep kumar [8] concluded in his study that increasing the particle size and particle content may improve the properties but will also increase the porosity level in the composite.
2. Experimental Details
The base alloy used for the study was commercially available Al-18wt%Si. The chemical composition of the alloy is given Table 1 [9].
The castings were manufactured using a centrifugal casting machine which had a flange that was connected to a shaft of synchronous DC motor. The speed could be varied from 20 to 2000rpm. The die used had a length of 129mm, thickness 10mm and inner diameter of 80mm. The first casting was made of Al-18wt%Si, melted to a temperature of 700°C. This molten metal was then poured into the die rotating at 800rpm. The second casting was production of MMC using stir casting. It consisted of melting the base alloy i.e,. Al-18wt%Si in a crucible for 700°C then 5% of preheated SiC particles were mixed into this melt with the stirring speed of 600rpm and holding time of 2 min. This mixture was then poured into the horizontally mounted die running at a speed of 800rpm. The tensile test was conducted according to the standard ASTM E8M-09 and wear test was performed under ASTM G99 standard.
3. Results and Discussion
3.1. Microstructure
To obtain the metallographic image of the cast sample, the sample was cut parallel to the axis. The aim was to find the distribution of the primary Si and SiC particles from outer diameter to the inner diameter.The surface of the sample was first initially filled and then a series of abrasive papers of mesh size ranging from 600, 1000, 1/4, 2/4, 3/4, 4/4 was used. Finally the sample was polished on the rotating disc using alumina powder mixed with water to obtain a scratch free surface.It can be seen from Figure 1 (a) - 1 (f) that due to the centrifugal force and difference in density between aluminium and silicon, the silicon particles are accumulated more in the inner compared to the outer region. The primary silicon content decreases from outer diameter and at one point it reaches the minimum value and once again increases to reach the maximum point in the inner region. The primary silicon content was found to be more than the eutectic silicon content. The primary silicon particles were unevenly distributed and formation of clusters at certain places was easily visible. Due to the density difference silicon particle and aluminium and the centrifugal force developed during the rotation of the mould causes the lighter silicon particles to be thrown out. This is clearly visible from the images as region consists maximum primary silicon particles spread over the area. This primary silicon particle is accompanied with the eutectic silicon phase.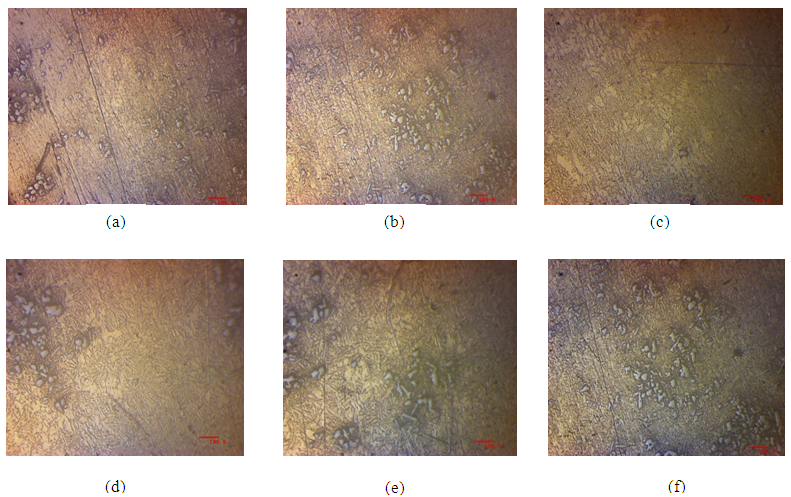 | Figure 1. Microstructure of Al-18wt%Si cylinder taken at 2mm interval from outer diameter to inner diameter |
Figure 2 gives the microstructural images of the composite. Similar to the microstructure of Al-18wt%Si alloy, the distribution clearly specifies the presence of eutectic silicon, primary silicon phases and α-Al phase. The SiC particles present in mix because of their density as well as centrifugal force are pushed towards the outer periphery. 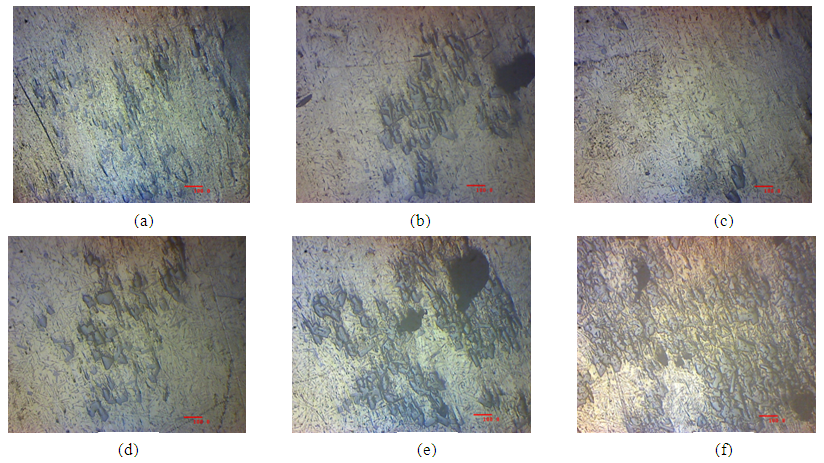 | Figure 2. Microstructure of Al-18wt%Si-5wt%SiC cylinder taken at 2mm interval from outer diameter to inner diameter |
3.2. Hardness
Figure 3 shows the variation of Vicker’s hardness value for centrifugally cast Al-18wt%Si and Al-18%Si-5%SiC from outer diameter to inner diameter in the radial direction. The hardness values of Al-18wt%Si-5%SiC (70.58 kg/mm2) were found to be greater than the hardness value of Al-18wt%Si (59.79 kg/mm2) by 18% at outer diameter. This higher value of hardness in Al-18wt%Si-5%Sic is due to the presence of SiCp in outer diameter of the casting. It has been observed that the concentration of Si primary particles is more at the inner diameter than the outer diameter, this is due to the reason that the Si particle being less dense thrown inward during the rotation of the mould. Since the direction of solidification is taking place from outer radius to inner radius the casting gets cooled immediately as soon as the melt contacts the cold metal mould. Hence rapid solidification takes place near the mould surface, this leads to the increase in hardness. When the metal gets solidified rapidly some of the Si and SiC particles also trapped in the solidified metal. The trapped particles are also responsible for the increase of hardness of the metal alloys.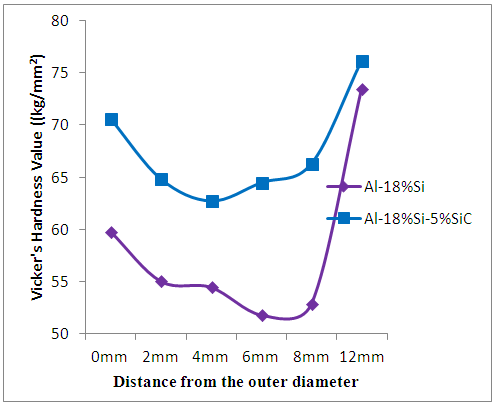 | Figure 3. Comparison of hardness for Al-18wt%Si and Al-18wt%Si-5%SiC casting |
3.3. Wear Test
The wear test was performed to find the specific wear rate of the produced cylinders under varying loads from 20N to 40N with an increment of 10N each, with a constant sliding distance of 1800m and a constant speed of 360rpm.In the SiC reinforced metal matrix composites, the SiC particles tend to support the load. Because of this the contact area between pin and disc becomes less thus decreasing the wear rate. They also help in avoiding the any form of cuts and graze marks on the surface of the pin. Hence, the resistance to wear in composite is found to be higher.According to the Archard’s law, the wear rate is always inversely proportional to the hardness. From the Figure 3, it can be seen that the hardness of the composite is very much higher than the matrix material thus it should possess a lower wear rate. Figure 4 proves the Archard’s law as the specific wear rate of the composite is clearly lower in comparison to that of the matrix material. 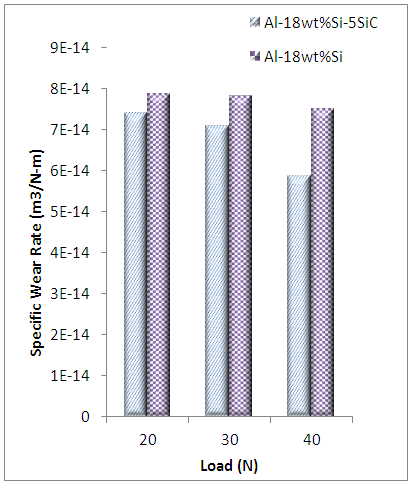 | Figure 4. Plot of specific wear rate against load |
3.4. Tensile Test
The results from Figure 5 shows that the tensile strength of the Al-18wt%Si-5%SiC is 117MPa which is higher than 99MPa, the tensile strength of Al-18wt%Si. This is due to the presence of SiC particles in the casting. The increase in the value was found be more than 18%. This result is also proved from the hardness results. 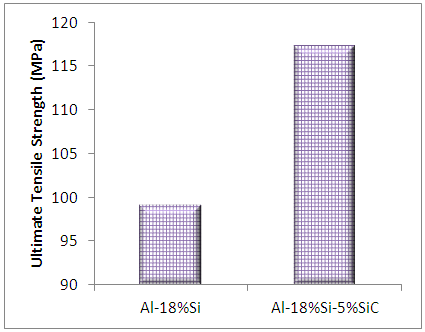 | Figure 5. Comparison of UTS between base alloy and MMC |
The presence of the reinforcing ceramic particles obstructs the motion of dislocations in the period of plastic deformation and thus allowing the matrix to behave like an isotropic material. This is the reason for the increased ultimate tensile strength in the composite. The formation of the particle clusters as seen in the microstructural images has a significant influence on the strength and their plastic deformation of the composites. The cluster formation has no much effect on the elastic nature of the composite. Even though addition of the reinforcements increases the ultimate tensile strength of the composite, it decreases the ductility. The ceramic reinforcing particles acts as load bearing particles by decreasing the dislocations formed because of the applied load. But due to the inherent brittleness of the reinforcing particles upon their addition they decrease the ductility of the composites.
4. Conclusions
The following conclusions were drawn from the study:1) The microstructural analysis revealed that, the Si particles are largely accumulated at inner diametrical region. Under the combination of high speed and density difference, the Si particles which are have a lower density gets settled in the inner region. In the case of composite, the SiC particle due to their higher density gets thrown away towards the outer diametrical region.2) From the Vicker’s Hardness test, it was observed that, the hardness value decreases gradually from outer diameter towards the center and attains the maximum value at the inner diametrical region. The segregation of primary Si particles in the inner region is the reason for the high hardness. The hardness value of 73HV and 76HV was found in base alloy and composite respectively in the inner diametrical region. However, in the case of outer diametrical region, the base alloy has a hardness value of 59HV whereas the composite has a hardness of 70HV. The accumulation of higher density SiC particle is attributed for this increase in hardness. The density results perfectly justifies with the increase in hardness.3) The tensile test result revealed that the UTS of the composite is 117MPa. The hard ceramic reinforcing particles help in avoiding the local dislocations occurring due to the application of load.4) The results of the wear test give away the fact that the wear resistance offered by the composites to the wear is very much higher than the base alloy. The ceramic particles have a property to carry the load when acted upon it.
ACKNOLEDGEMENTS
The authors are grateful to the management of Nitte Meenakshi Institute of Technology, Bengaluru for allowing us to use the facility from the research centre for the completion of this study.
References
[1] | Tetsuro Ogawa, Yoshimi Watanabe, Hisashi Sato, Ick-Soo Kim, Yasuyoshi Fukui, “Theoretical study on fabrication of functionally graded material with density gradient by a centrifugal solid-particle method”, Composites: Part A 37, 2006, pp.2194–2200. |
[2] | Y. Sahin, “Preparation and some properties of SiC particle reinforced aluminium alloy composites”, Materials and Design, Volume 24, 2003, pp. 671-679. |
[3] | S.A. Kori, T.M. Chandrashekharaiah, “Studies on the dry sliding wear behaviour of hypoeutectic and eutectic Al–Si alloys”, Wear 263, 2007, pp.745–755. |
[4] | Chirita G, Stefanescu I, Soares DSilva F.S, “Centrifugal versus gravity casting techniques over mechanical properties”, Anales de Mecánica de la Fractura Vol. I, 2006. |
[5] | A. Sakthivel, R. Palaninathan, R. Velmurugan, P. Raghothama Rao, “Production And Mechanical Properties of Sicp Particle-Reinforced 2618 Aluminium Alloy Composites”, J Mater Sci, 2008. |
[6] | Ali Mazahery, Mohsen Ostad Shabani, “Microstructural and Abrasive Wear Properties of Sic Reinforced Aluminium-Based Composite Produced By Compocasting”, Transaction of Nonferrous Society of China, Volume 23, 2013, 1905-1914. |
[7] | S Das, “Development of Aluminium Alloy Composites for Engineering Applications”, Trans. Indian Inst. Met, Vol.57, No. 4, August 2004, Pp. 325-334. |
[8] | Er. Sandeep Kumar Ravesh, Dr. T. K. Garg, “Preparation and Analysis for some Mechanical Property of Aluminium Based Metal Matrix Composite Reinforced with SiC and Flyash”, International Journal of Engineering Research and Applications, Vol. 2, 2012, pp.727-731. |
[9] | Dr Jameel Habeeb Ghazi, “Production and Properties of Silicon Carbide particles reinforced aluminium alloy composites”, International Journal of Mining, Metallurgy and Mechanical Engineering, Volume 1, 2013, pp.191-194. |