Pruthvi Serrao1, Jagannath Nayak2
1Department of Mechanical Engineering, St Joseph Engineering College, Mangaluru, India
2Department of Metallurgical & Materials Engineering, NITK, Surathkal, India
Correspondence to: Pruthvi Serrao, Department of Mechanical Engineering, St Joseph Engineering College, Mangaluru, India.
Email: |  |
Copyright © 2016 Scientific & Academic Publishing. All Rights Reserved.
This work is licensed under the Creative Commons Attribution International License (CC BY).
http://creativecommons.org/licenses/by/4.0/

Abstract
The commercially pure titanium (grade 2) was subjected to surface mechanical attrition treatment (SMAT) to obtain a nanocrystallized surface which was further subjected to oxidation in a fluidized bed furnace for 5 hours at three different temperatures; 500, 600 and 700°C. The effectiveness of this two stage treatment was assessed using optical microscopy, X-ray diffraction, glow discharge optical emission spectroscopy (GDOES) and Vickers hardness tester. The effect of SMAT on oxidation was found to influence the surface hardness profoundly though they featured lower oxidation rates and the coating thickness than the coarse grained titanium.
Keywords:
SMAT, Nanocrystallization, Oxidation, Titanium, Surface engineering
Cite this paper: Pruthvi Serrao, Jagannath Nayak, Effect of Surface Mechanical Attrition Treatment on High Temperature Oxidation of CP Titanium, American Journal of Materials Science, Vol. 6 No. 4A, 2016, pp. 20-24. doi: 10.5923/c.materials.201601.04.
1. Introduction
Titanium is a highly reactive metal and will react within microseconds to form an oxide layer when exposed to the atmosphere. The oxidation product of titanium during exposure to air is TiO2 (titania) which has a tetragonal rutile crystal structure. This oxide layer is often called scale. During the oxidation process, the high affinity of titanium to oxygen and the high solid solubility of oxygen in titanium (about 14.5%) results in the simultaneous formation of the scale and an adjacent oxygen rich layer in the base metal. This oxygen rich layer is called α-case because it is a continuous layer of oxygen stabilized α-phase [1, 2].The formed oxide layer adheres strongly to the titanium substrate surface. Adhesion and adhesive strength of Ti oxide to substrates are controlled by oxidation temperature and thickness of the oxide layer as well as the significant influence of nitrogen on oxidation in air. The adhesion of the oxide layers to the metal substrate decreases with the decrease in the layer thickness as well as when the oxidation temperature increases. With higher oxidation temperatures the bond strength between Ti and TiO2 will be weakened due to the significant differences in coefficients of thermal expansion, as TiO2 does not exhibit any phase transformations upto its melting point where as Ti substrate undergoes phase transformation at 885°C [1].The high reactivity of titanium with oxygen limits the maximum use temperature of titanium alloys to about 600°C. Above this temperature the diffusion of oxygen through the oxide surface layer becomes too fast resulting in excessive growth of the oxide layer and embrittlement of the adjacent oxygen rich layer of the titanium alloy [1, 2]. Also, high reactivity of titanium with oxygen necessitates certain surface treatments to be carried out in an inert atmosphere to avoid preferential oxidation [4, 6].A newly developed surface nanocrystallization technique ―Surface Mechanical Attrition Treatment (SMAT) is an efficient technique to refine the grain structure and induce numerous surface defects on the sample surface [3]. SMAT is being extensively studied and a lot of research work has been done on this aspect since a decade and there have been several works reporting enhanced subsequent surface treatment parameters after SMAT.
2. Experimental Methods
A titanium disc was first subjected to SMAT on one side; in the treatment process, the sample is clamped to a vacuum chamber containing steel shots and vibrated at a relatively low frequency of 50Hz; the surface of the sample is impacted by a large number of randomly flying steel balls having 8 mm diameter for duration of 1 hour. The repeated multidirectional impacts at high strain rates onto the sample surface result in severe plastic deformation and a nanostructured layer is formed in the surface of the sample. The titanium disc was then cut down to smaller samples and then subjected to oxidation at different temperatures. Oxidation treatment was carried out in a fluidized bed furnace for 5 hours. The three different samples; all treated with SMAT on one side were treated at three different temperatures of 500, 600 and 700°C respectively. The air flow during the treatment was maintained at 2 m3/hr.Various analysis techniques were employed to study the effect of the surface treatments. The major notable aspects of the surface treatment are coating thickness, amount diffused across the depth, and compounds formed; accordingly optical micrography, GDOES and XRD were used to study/measure these parameters. Also the hardness across the depth from the surface was measured in order to verify the property of the compound formed and its thickness.The surface treated samples hardly required any specimen preparation for GDOES and XRD techniques but were required to be hot mount for optical microscopy analysis; which then required a thorough polishing for observing its microstructure. The mounts were initially polished using SiC abrasive papers of 250, 600 and 1200 grit successively; which then was polished using 4000 grit SiC paper using ethanol. Final polishing was done on a polishing disc using a solution of OPS (Oxide Polishing Suspension) and H2O2. This technique of incorporating H2O2 in an OPS solution would enable partial etching of the sample and is known to give better results for observing surface details than post polish etching. A 30% H2O2 in an OPS solution was used for final polish and the sample was polished for 20 minutes. The microstructure of the polished samples and the phases developed were not accessible through optical microscopy in the unetched condition so the samples were etched with Kroll’s etchant (100 ml distilled water, 02 ml hydrofluoric acid and 06 ml nitric acid) for 3 minutes [6-8].The surface treated samples were examined under GDOES in order obtain a quantitative depth profile. The equipment used was LECO GDS850A and the results were obtained directly through the software coupled with the equipment. The surface treated samples were required to have a flat surface with a minimum section width of 12x12mm to apply vacuum. This is a destructive testing involving plasma sputtering leaving the sample burnt at the surface upto certain depth.The intermetallic compounds formed were identified by X-ray diffractometer (PANAnalytical XRD) using monochromatic Cu Kα radiation. The X-ray diffraction measurements were performed using a goniometer at a scanning range of 20<2θ<120, and a step size of 0.05, at 45 kV and 50 mA using a collimator with 2x2 spot size. The patterns obtained were analyzed using X’pert Highscore Plus software and compared with the ICDD database to identify the elements and compounds present in the surface treated samples.
3. Results and Discussion
3.1. Physical Appearance
The effect of oxidation was differentiable through their colors as shown in Figure 1. The oxidation samples on the coarse grained side showed sky blue, golden brown (brass) and golden colors at 500, 600 and 700°C respectively whereas the SMATed side showed greyish blue, greyish brown and dark brown colors at 500, 600 and 700°C respectively. The colors of the coatings may be the result of the light interference phenomenon within the surface layer above the substrate and the different colors at different temperatures could be attributed to the coating thickness and also the composition to some extent.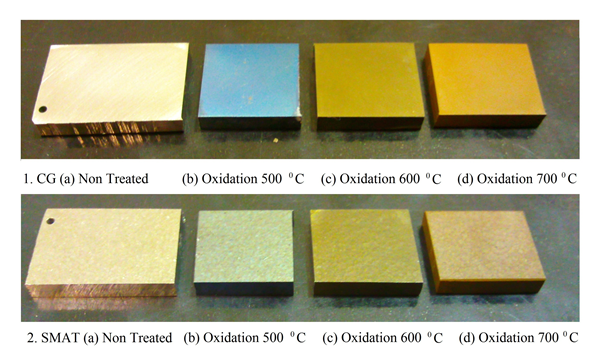 | Figure 1. Physical appearance of the oxidized samples |
3.2. Optical Microscopy
The etched samples were then observed under an optical microscope attached with a digital image recorder through which photomicrographs were taken at 1000x magnification.
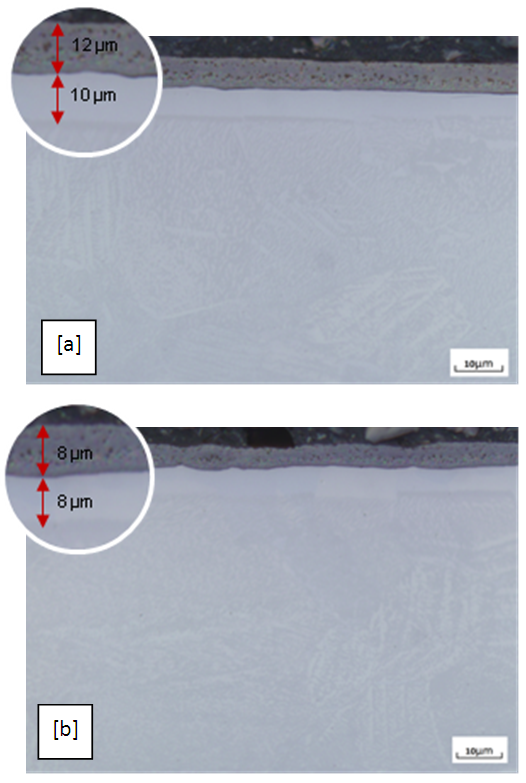 | Figure 2. Optical micrograph of titanium oxidized at 700°C for 5 hours; (a) un-SMAT; (b) SMAT. |
At 500C there was hardly any coating but a diffusion layer of about 0.5 μm and 0.8 μm thick were visible in CG and SMAT samples respectively. At 600°C two distinct layers were observed in the micrograph of both SMAT and CG samples; an outer oxide layer about 2.5 μm thick in CG sample whereas 1.5 μm thick in a SMAT sample and a diffusion layer below it measuring approximately 3 μm in both samples. The coating was continuous and uniform in case of CG sample on the other hand the SMAT sample showed a discontinuous coating. At 700°C much thicker and uniform coating was obtained as shown in Figure 2. An oxide layer upto 12 μm thick and a diffusion layer about 10 μm thick were obtained in a CG sample. In SMAT sample an oxide layer and a diffusion layer both 8 μm thick were obtained but the thickness of the compound layer was not uniform. It should be noted that the SMAT surface prior to surface treatment was not flat due to ball impacts and the compound layer formed on the substrate did not follow the surface contour instead was uneven and non-uniform, this could be due to preferential diffusion of oxygen into the material along grain boundaries and dislocations.
3.3. GDOES
A quantitative depth profile showing the atomic percent of the element diffused across the depth from the surface of the sample is shown in Figure 4 after Oxidation for both SMAT and CG samples.The percentage atomic diffusion across the depth increases as the treatment temperature increases. Near the surface upto a depth of few microns the atomic percent of oxygen upto 95% is achieved and it gradually reduces with the depth. The oxygen diffusion across the depth is found effective in case of CG samples than the SMAT samples. At 700°C the oxygen diffuses through a depth of about 20 and 25 micrometers in SMAT and CG samples respectively.The percentage atomic diffusion across the depth increases as the treatment temperature increases. Near the surface upto a depth of few microns the atomic percent of oxygen upto 95% is achieved and it gradually reduces with the depth. The oxygen diffusion across the depth is found effective in case of CG samples than the SMAT samples. At 700C the oxygen diffuses through a depth of about 20 and 25 micrometers in SMAT and CG samples respectively.
3.4. X-ray Diffractometry
When titanium and titanium alloys are heated in air at a temperature of 450–800°C for 2–10 min, protective oxide films can be formed. Oxide layers formed on titanium change from lower to higher oxides as oxidation progresses and temperature increases. The following phases form in air:Ti+O→Ti(O)→Ti6O→Ti3O→Ti2O→TiO→Ti2O3→Ti3O5→TiO2Among these oxides of different stoichiometry (e.g., TiO, Ti2O3, TiO2), TiO2 is the most common and stable thermodynamically. TiO2 is very resistant against chemical attack, which makes titanium one of the most corrosion resistant metals [1, 5].In the present work at 500°C, both CG and SMAT samples show only the Ti peaks suggesting weak oxidation effects at the relatively lower temperature. With the increase of temperature to 600°C the peaks of rutile (TiO2) were observed in both the samples; wherein CG sample shows stronger rutile (110) peak than SMAT sample suggesting better oxidation effects in a CG sample. At 700°C there were hardly any Ti peaks visible in both samples which is evident in Figure 3. The CG sample shows all rutile peaks along with few peaks of Ti6O whereas the SMAT sample shows strong and broad peaks of both rutile and Ti6O.
3.5. Microhardness
Hardness profiles were obtained before and after the surface treatments for both CG and SMAT samples. Before the surface treatments the measured hardness values were about 160 Hv for a CG sample whereas the SMAT sample was found to have a peak hardness of 240 Hv at the surface, and the hardness decreases slowly with a longer distance of about 40 microns from the surface.The oxidation treated samples were cut across the treated surface and the hardness values were measured at various depths from surface to the core in order to find the effectiveness of oxidation treatment. Hardness values of 225, 296 and 560 Hv in a CG sample and hardness of 260, 320 and 580 Hv in a SMAT sample were obtained respectively at 500, 600 and 700°C. The variation of the hardness along the depth is shown in Figure 5. 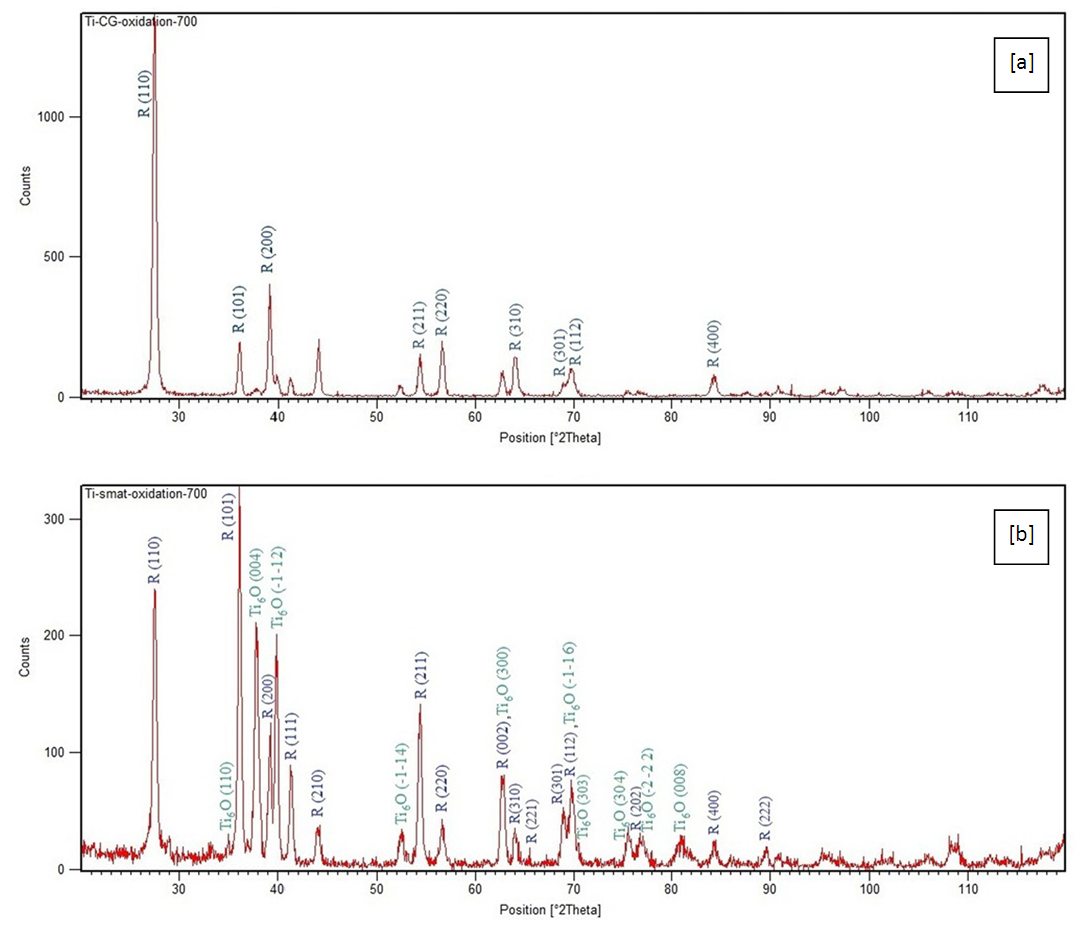 | Figure 3. The XRD patterns of titanium nitrided at 700C; (a) un-SMAT; (b) SMAT |
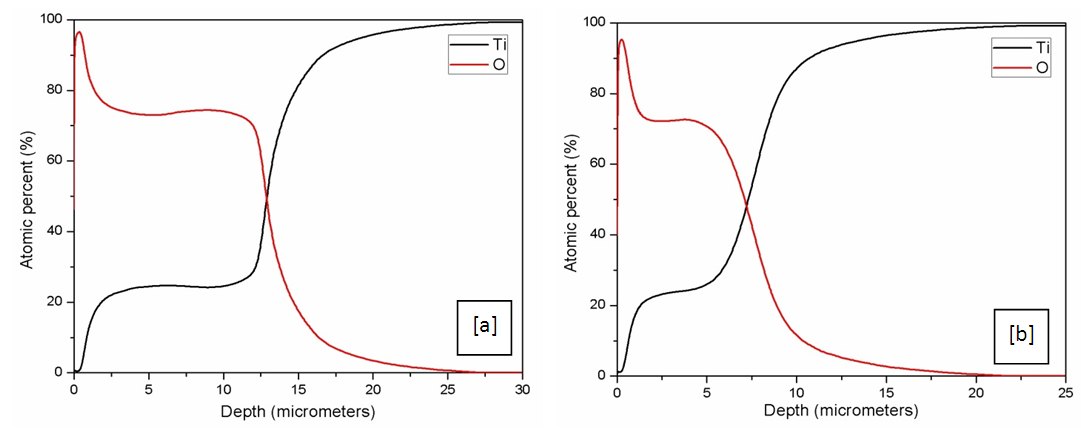 | Figure 4. Quantitative depth profile showing the atomic percent of oxygen diffused across the depth from the surface after oxidation at 700C; (a) un-SMAT; (b) SMAT |
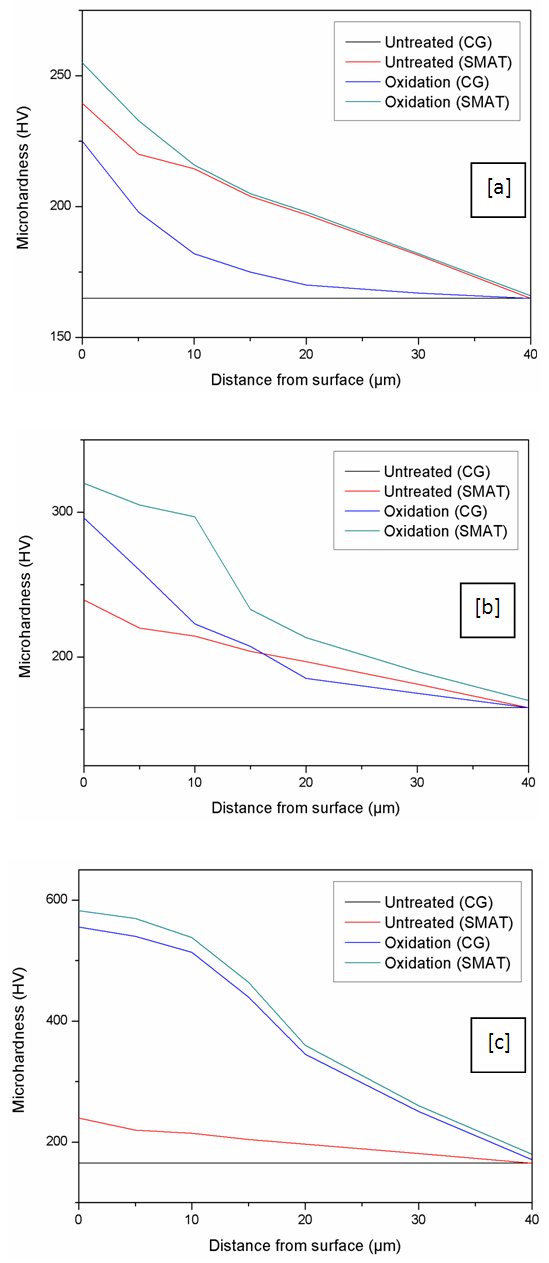 | Figure 5. Hardness profiles for SMAT and un-SMAT titanium before and after oxidation; (a) at 500°C; (b) at 600°C; (c) 700°C |
4. Conclusions
Oxidation was more effective in a CG sample than a SMATed sample. At lower temperature (500°C) the effects were similar in both the samples but much thicker oxide layers were obtained in a CG sample at higher temperatures (600 and 700°C). Although, the SMAT is known to enhance the diffusion kinetics to promote oxidation rate, the present work didn’t not reflect the above hypothesis. However the SMAT samples were better in terms of surface hardness. It was also observed that the oxide layers were quite brittle and they could be easily damaged by mechanical impact; thus the process cannot significantly improve the wear resistance.
ACKNOWLEDGEMENTS
The author wishes to acknowledge all the contributors for carrying out the research work. The research lab facilities and equipments provided by Deakin - Institute of Frontier Materials (IFM), Geelong, Australia is gratefully acknowledged.
References
[1] | Oshida, Yoshiki. Oxidation and Oxides. Bioscience and Bioengineering of Titanium Materials. 1st ed., Elsevier, 2007, 4, pp. 81-103. |
[2] | Gerd Lütjering, James C. Williams. Titanium. 2nd ed., Springer, 2007. |
[3] | Lu, K. and Lu, J. (2004). “Nanostructured surface layer on metallic materials induced by surface mechanical attrition treatment” Materials Science and Engineering, Vol 375–377: 38–45. |
[4] | Gang Lu, Steven L. Bernasek, Jeffrey Schwartz (2000). “Oxidation of a polycrystalline titanium surface by oxygen and water” Surface Science 458: 80–90. |
[5] | Ming Wen, Cuie Wen, Peter Hodgson and Yuncang Li, (2012). “Thermal oxidation behaviour of bulk titanium with nanocrystalline surface layer” Corrosion Science 59:352-359. |
[6] | Cotell, C.M. Sprague, J. A. and Smidt, F. A. (1994). “Surface Engineering” ASM Handbook 10th edition, ASM International, Materials Park, OH, Vol 5: 2232-2268. |
[7] | Donlevy, A. Blicker, S Cliff Bugle, James Grauman, Lian, Z. Bob McHugh, John Mountford, Rick Porter, Flavio Portello, Saiki, T. Ronald Schutz and Wilson, A. (2005) “Specifications Guide” International Titanium Association, Fourth Edition. |
[8] | George F. Vander Voort, (1999), “Metallography - Principles and Practice” ASM International, Materials Park, OH, p 692. |