J. W. Pinto, G. Sujaykumar, Sushiledra R. M.
Department of Mechanical Engineering, Yenepoya Institute of Technology, Moodabidri, India
Correspondence to: G. Sujaykumar, Department of Mechanical Engineering, Yenepoya Institute of Technology, Moodabidri, India.
Email: |  |
Copyright © 2016 Scientific & Academic Publishing. All Rights Reserved.
This work is licensed under the Creative Commons Attribution International License (CC BY).
http://creativecommons.org/licenses/by/4.0/

Abstract
Composite materials are exponentially growing up and rapidly gaining importance because of their potential to produce the components that features low density while maintain high stiffness, strength, thermal stability, improved fatigue properties and wear resistance. Hybrid composites contain two or more particles that provide better strength wear resistance and superior material properties which find applications in automotive and many engineering fields. Aluminum Alloy- 6061- Bricks have high strength, low density, durability, machinability, and least expensive and can be fabricated by most of the commonly used techniques. Coconut shell ash powder and E-Glass fiber whisker are used as reinforcement. Hybrid Aluminum alloy composite with coconut shell ash and E-glass fiber reinforcement is produced by Stir- Casting method. Hardness test, wear test and tensile test were carried out with and without heat treated composites specimens.
Keywords:
Aluminum-6061, Coconut shell ash, E-Glass fibre, Wear, Micro hardness, Tensile, Heat treatment
Cite this paper: J. W. Pinto, G. Sujaykumar, Sushiledra R. M., Effect of Heat Treatment on Mechanical and Wear Characterization of Coconut Shell Ash and E-glass Fiber Reinforced Aluminum Hybrid Composites, American Journal of Materials Science, Vol. 6 No. 4A, 2016, pp. 15-19. doi: 10.5923/c.materials.201601.03.
1. Introduction
Hybrid composites contain two or more particles that provide better strength wear resistance and superior material properties which find applications in automotive and many engineering fields. The Aluminium alloy composite are made by mixing particulate in a molten alloy. Applications of Aluminium-based Hybrid MMCs have increased in recent years as engineering materials. The introduction of a glass material into a metal matrix produces a composite material that results in an attractive combination of physical and mechanical properties which cannot be obtained with monolithic alloys. The strengthening of aluminium alloys with a reinforcement of fine glass particulates has greatly increased their potential in wear resistant and structural applications. There is an increasing interest in the development of hybrid metal matrix composites having low density and low cost reinforcements. Among the various discontinuous reinforcements used, glass particulate is one of the most inexpensive and low-density reinforcement. The most easy and reliable way to fabricate aluminium hybrid MMC’s is by stir casting also known as vortex casting. The controlled vortex formation during liquid state enables even particulate distribution. A standard heat treatment consists in solutioning (holding the alloy in temperature below temperature of the eutectic reaction in order to dissolve the precipitations of Mg2Si, homogenize the chemical elements concentration on the cross-section of dendrites of the α-phase and the change in the silicon precipitations morphology), and ageing. Holding the castings in constant temperatures during predetermined period of time results in the improvement of the mechanical properties such as: tensile strength and HB hardness; and in simultaneous worsening of plasticity.Coconut shell ash can be used as a low cost reinforcement in Metal Matrix Composites as ash possesses nearly same chemical phases and other functional groups as reinforcement like fly ash, rice husk ash, bagasse ash that have been in Metal Matrix Composites (MMCs) specifically for automobile applications [1]. Hybrid composites of Aluminium alloy reinforced with SiC and Graphite particles possess higher hardness, higher tensile strength, better wear resistance and lower coefficient of friction when compared to pure alloys [2]. Aluminium-Glass particulate composite was successfully synthesized by the stir casting method. The tensile strength and micro hardness of the composite increased with increase in wt% of glass particulates up to 9%. [3]. Test of Flyash-eglass-Al6061 alloy composites having 2 wt%, 4 wt%, 6wt% and 8wt% of fly ash and 2 wt% and 6wt % of e-glass fibre were fabricated by liquid metallurgy (stir cast) method [7]. Significant improvement in tensile properties, compressive strength and hardness are noticeable as the wt % of the fly ash increases [4, 6]. Work should be done to produce high quality and low cost reinforcements from industrial wastes and by-products. There is an urgent need to develop simple, economical and portable non-destructive kits to quantify undesirable defects in AMCs [5]. Aluminium alloys are used in advanced applications because their combination of high strength, low density, durability, machinability, availability and cost is very attractive compared to competing materials. However, the scope of these properties can be extended by using aluminium matrix composite materials [8, 9].
2. Methodology
2.1. Material Selection
Aluminum alloys are used in advanced applications because their combination of high strength, low density, durability, machinability, availability and cost is very attractive compared to competing materials. However, the scope of these properties can be extended by using aluminum matrix composite materials. Aluminum Alloy- 6061- Bricks is the least expensive and can be fabricated by most of the commonly used techniques. It offers a range of good mechanical properties and good corrosion resistance. Applications: This grade is used for a wide variety of products and applications from truck bodies and frames to screw machine parts and structural components. Chemical compositions are Mg (1.08%), Fe(0.17%), Si(0.63%), Cu(0.32%), Mn(0.52%), V(0.01%), Ti(0.02%) and Al as remainder. Physical properties are Low weight, excellent Thermal Conductivity, improved Strength, Stiffness and Wear resistant properties, highly Corrosion resistant and are extricable in nature.Coconut Shell Ash (CSA) - Powder (Reinforcement 1) is prepared by coconut shell which is an agricultural waste and is available in very large quantities throughout the tropical countries of the world. Coconut shell is suitable for preparing carbon black due to its excellent natural structure and low ash content. Conversion of coconut shells into activated carbons which can be used as adsorbents in water purification or the treatment of industrial and municipal effluents would add value to these agricultural commodities, help reduce the cost of waste disposal, and provide a potentially cheap alternative to existing commercial carbons. Coconut shell ash can be prepared by soaking, cleaning, crushing, drying, pulverizing and heating coconut shell powder to 1000°C in a closed furnace. Chemical properties are Al2O3 (15.6%), CaO(0.57%), Fe2O3(12.4%), K2O(0.52%), MgO(16.2%), Na2O(0.45%), SiO2(45.05%), MnO(0.22%) and ZnO(0.3%). Physical properties are Low cost, High strength, modulus & corrosion resistance & thermal resistance, Light weight & density. Measured density is 0.7990 gm/cc and grain fineness number is 92.E-Glass Fibre – Whisker (reinforcement 2) is electric grade glass is originally developed for stand of insulators for electrical wiring. It was later found to have excellent fibre forming capabilities and is now used almost exclusively as the reinforcing phase in the material commonly known as fibre-glass. The fibre orientations, content, distribution and the ability to maintain these parameters are significant for the reinforcement. Chemical properties are SiO2 (54%), Al2O3 (14%), CaO + MgO (22%), B2O3 (10%) and Na2O+K2O (less 2%). Key properties that has made E-glass so popular in fibre glass and other glass fibre reinforced composites includes high production rate, high strength, high stiffness, relatively low density, non-flammable, Excellent Heat Resistance , good chemical resistance, relatively insensitive to moisture, good electrical insulation able to maintain strength over a wide range of conditions.
2.2. Specimen Preparation
Hybrid Aluminum alloy composite with coconut shell ash and E-glass fibre reinforcement is produced by Stir- Casting method. In this work, Stir-casting set up consists of a resistance furnace with coil heating element with 6 Kg capacity and ceramic coated chromium steel impeller with maximum stirring speed of 600 rpm. Maximum temperature of 1000°C can be reached in this set up. Aluminum alloy- 6061 bricks are taken in the furnace and furnace temperature is set to 800°C as melting point of Aluminum alloy is 650°C. Reinforcement material is added to molten matrix of aluminum alloy-6061. To create the perfect interface bond between matrix and reinforcement Preheating of reinforcement, Maintaining stirring speed of 300 to 600 RPM, uniform powder feed rate and addition of Magnesium are essential for perfect interface bonding between matrix and reinforcement. To remove the slag and gas in the molten metal scum powder and degassing tablet (hexachloro ethane) are used. Nitrogen is used to prevent the oxidation of molten metal. Mould is preheated to avoid porosity during casting. Casted composites were machined to different sizes for mechanical and wear tests.
2.3. Heat Treatment
The term “heat treating” for aluminium alloys is frequently restricted to the specific operations employed to increase strength and hardness of the precipitation-hard enable wrought and cast alloys. These usually are referred to as the “heat-treatable” alloys to distinguish them from those alloys in which no significant strengthening can be achieved by heating and cooling. Heat treatment to increase strength of aluminium alloys is a three-step process like solutioning, quenching and ageing.Descriptions of muffle furnace are as follows: Working Temperature is 1350°C or better, Heating Element is Silicon Carbide (SiC), Temperature Accuracy is 2°C or better, Temperature Control is through microprocessor based PID controller with minimum 30 steps, Furnace Insulation material is Ceramic wool, Temperature settings & Display ia done by Digital and double display, Power source is 220 V, 50Hz single phase, Out body and inner body is Stainless Steel.
2.4. Tests Carried out
Hardness test is carried out on Vicker's Micro Hardness tester with load of 100 grams, dwell Duration of 15 Seconds and Speed of Indentation of 5 mm/min with Diamond Shaped indenter. Wear test was carried out on Pin-On-Disc wear tester for different loads of 24.525N (2.5 Kg), 39.24 (4 Kg) and 53.955 (5.5 Kg) with various disc speeds of 300 RPM, 500 RPM and 700 RPM with constant time duration of 10 minutes. Tensile test is carried out on tensile testing machine with uniaxial load and Rate of Loading of 0.2 mm/min.
3. Results and Discussion
All tests have been carried out on the specimens heat treated and non heat treated. Results are compared and analyzed with the help of graph.
3.1. Micro Hardness Test
Figure 1 shows significant improvement in hardness with addition of coconut shell ash (CSA) and E-glass fibre particle in matrix alloy. An improvement of 84.2VHN increase is noticed with addition of 4% CSA and 4% E-glass fibre reinforcement in matrix alloy composite. After heat treatment, hardness of specimen without filler material is increased but considerable decrease in hardness of specimens with filler material.
3.2. Wear Teat
3.2.1. Wear rate vs Load
Wear rate has significantly reduced for composite with the addition of reinforcing phase (%) for both varying RPM and varying load. From obtained results from wear testing, it was noticed, a considerable decrease in wear rate with increasing load and speed.
3.3. Tensile Test
Tensile test helped to determine the tensile strengths of different composite it was found that there was a remarkable increase in tensile strength with a increase in addition of reinforcement. Maximum tensile strength obtained was 83 MPa for 3% CSA + 3% E-glass fibre reinforced aluminum composites. For heat-treated specimens the average tensile strength invariably fluctuates with the reinforcements. 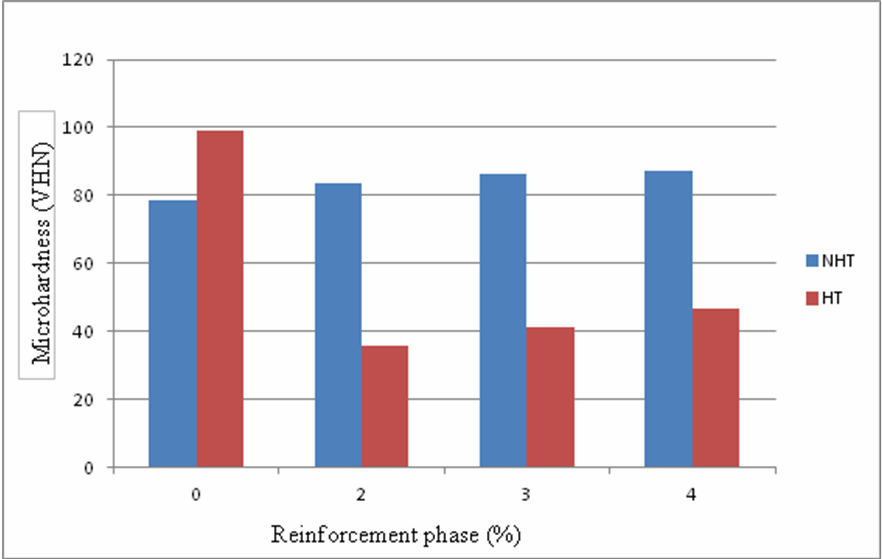 | Figure 1. Microhardness Test results |
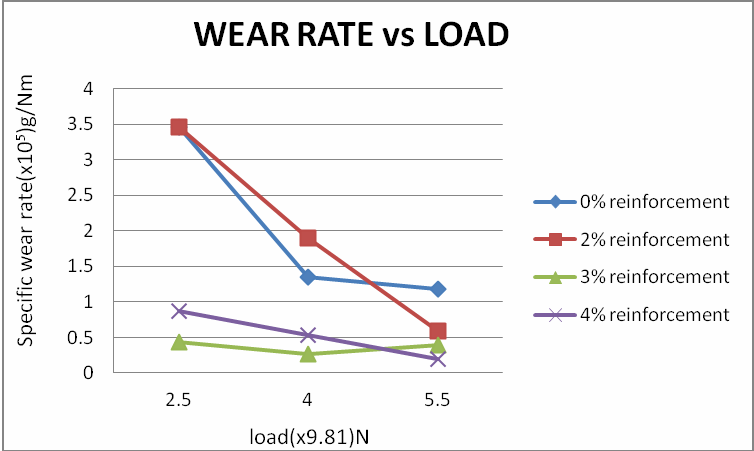 | Figure 2. Specific Wear Rate v/s Load (Non- Heat Treated) |
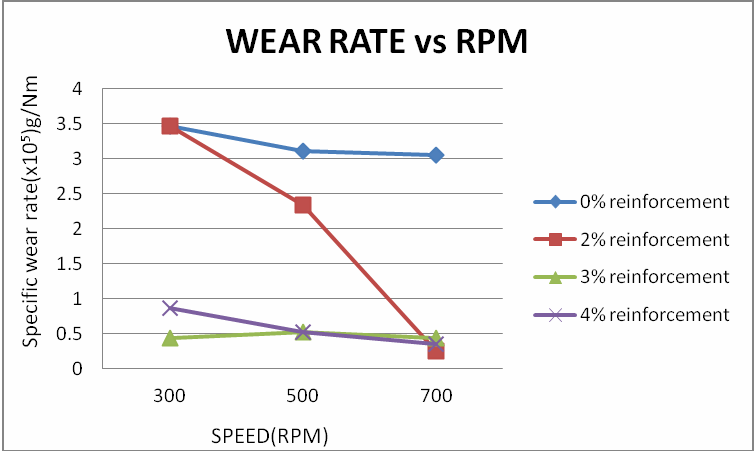 | Figure 3. Specific wear rate v/s RPM (Non heat Treated) |
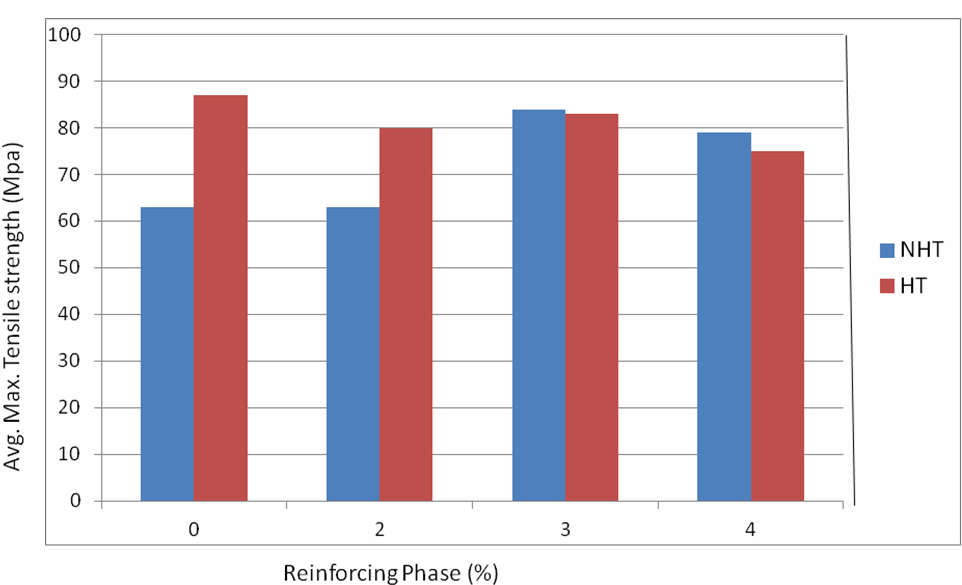 | Figure 4. Tensile test results |
4. Conclusions
Results show a positive response on micro hardness test without heat treatment of the composite material with the addition of low-cost reinforcement. Since coconut shells are abundant in nature having vital elements, which can be extracted via feasible processes. The activated carbon is the vital reason for the increase in hardness. It also shows positive signs on the way of tensile strengthening due to the involvement of E-glass fibres. Thus, varying the amount of reinforcement (%) optimum properties can be achieved. Micro hardness for the composite increase significantly for the non heat-treated composite material. Micro hardness of the heat-treated specimens with reinforcement is lower than the base material, which describes the little brittle nature for heat-treated composite. Wear rate has significantly reduced for non heat-treated composite with the addition of reinforcing phase (%) for both varying RPM and varying load. There is also a considerable decrease in wear rate for heat-treated specimens with increasing reinforcement. Tensile strength increases significantly with addition of the reinforcing phase (%) compared to the base material in non heat treated composites and found fluctuation after heat treatment.
References
[1] | P.B Madakson, D.S. Yawas and A. Apasi, “Characterization of Coconut Shell Ash for Potential Utilization in Metal Matrix Composites for Automotive Applications”, International Journal of Engineering Science and Technology (IJEST). |
[2] | S. Mitrović, M. Babićb., Stojanović, N. Miloradović, M. Pantić D. Džunića “Tribological Potential of Hybrid Composites Based on Zinc and Aluminium Alloys Reinforced with sic and Graphite Particles”, Vol. 34, No. 4 (2012) 177-185. |
[3] | Madhu Kumar YC, Uma Shankar, Evaluation of Mechanical Properties of Aluminium Alloy 6061-Glass Particulates reinforced Metal Matrix Composites, International Journal of Modern Engineering Research (IJMER) Vol.2, Issue.5, Sep.- Oct. 2012 pp-3207-3209 ISSN: 2249-6645. |
[4] | Arun. L.R, Saddam Hussain. B, Dr. Suneel Kumar N. Kulkarni, “Dynamic behaviour of hybrid aluminium6061 metal matrix reinforced with sic and fly ash particulates”, ISSN: 2319-8753, International Journal of Innovative Research in Science, Engineering and Technology, Vol. 2, Issue 6, June 2013. |
[5] | M K SURAPPA, “Aluminium matrix composites: Challenges and opportunities”, S¯adhan¯a Vol. 28, Parts 1 & 2, February/April 2003, pp. 319–334. © Printed in India. |
[6] | Rahul Chanap, May 2012, Study of Mechanical and Flexural Properties of Coconut Shell Ash Reinforced Epoxy. |
[7] | Aldo R. Boccaccini,. Michael Bficker, Jfrg Bossert and Konstantin Marszalek L Fachgebiet Werkstofftechnik, 30-054 Krakow, Poland “Original contribution glass matrix composites from coal flyash and waste glass” S0956-053X(97) 00035-4 Waste Management, Vol.17, No. 1, pp. 39-45, 1997. |
[8] | T.V. Christn, N. Murugan and S. Kumar “A Comparative Study on the Microstructures and Mechanical Properties of Al 6061 Alloy and the MMC Al 6061/tib2/12P”, Journal of Minerals & Materials Characterization & Engineering, Vol. 9, No.1, pp.57-65, 2010, jmmce.org Printed in the USA. All rights reserved. |
[9] | Fredric W. Longenecker Lieutenant, “An Analysis of the Microstructure and Reinforcement Distribution of an Extruded Particle-Reinforced Al 6061-10 Volume Percent A120 3 Metal Matrix Composite”. |