Ghanaraja S. 1, Ramanuja C. M. 2, Ravikumar K. S. 3, Madhusudan B. M. 4
1Department of Mechanical Engineering, P.E.S. College of Engineering, Mandya, India
2Department of Mechanical Engineering, ATME College of Engineering, Mysuru, India
3Department of Mechanical Engineering, Maharaja Institute of Technology, Mysuru, India
4Department of Mechanical Engineering, GSSIETW, Mysuru, India
Correspondence to: Ghanaraja S. , Department of Mechanical Engineering, P.E.S. College of Engineering, Mandya, India.
Email: |  |
Copyright © 2015 Scientific & Academic Publishing. All Rights Reserved.
Abstract
In the present investigation cast composites have been synthesized by addition of the desired amount of TiO2 (3, 6, 9 and 12 wt %) powder to molten Al 1100-Mg alloy and all the composites of varied compositions were extruded. Study of microstructure on the hot extruded cast composites using Scanning Electron Microscopy (SEM) reveals that there are increasing numbers of bright particles of oxide with increasing addition of TiO2 powder. Also, the particle distribution in the composites developed by the additions of TiO2 powder shows individual particles and no significant clustering is observed. The hardness of the extruded composites increases with increasing addition of TiO2 particles when compared to Al-Mg (AM) base alloys, this may be due to healing of porosity, strain hardening and process of recovery and recrystallization. The yield and tensile strength increases with increasing addition of TiO2 powder. Yield strength and tensile strength improves most with 12 wt% addition of powder with values of 215.13 MPa and 239.7 MPa respectively. The percentage elongation increases with increasing addition of TiO2 powder up to 6 wt%, but addition beyond 6 wt% impairs ductility. The extruded composite with 6 wt% TiO2 particles shows ductility improvement of about 25.54%.
Keywords:
TiO2, Hot Extrusion, SEM and Mechanical Properties
Cite this paper: Ghanaraja S. , Ramanuja C. M. , Ravikumar K. S. , Madhusudan B. M. , Study on Mechanical Properties of Hot Extruded Al (Mg)-TiO2 Composites, American Journal of Materials Science, Vol. 5 No. 3C, 2015, pp. 188-193. doi: 10.5923/c.materials.201502.36.
1. Introduction
Aluminium is the most popular matrix for the metal matrix composites due to their attractive properties like low density, their capability to be strengthened by precipitation, their good corrosion resistance, high thermal and electrical conductivity, and their high vibration damping capacity. Aluminium matrix composites have been used since 1920s and are now used in sporting goods, electronic packaging, armors, automotive industries and widely used in the aerospace and automobile industries [1-2]. They offer a large variety of mechanical properties depending on the chemical composition of the aluminium matrix. Traditionally, the Al-MMCs are produced by directly adding reinforcements into the Al matrices [3-6]. Recently, some in situ methods have been developed and are being adopted in the production of Al-MMCs [7]. They are usually reinforced by aluminium oxide, silicon carbide, silicon dioxide, Titanium dioxide, Manganese dioxide, Graphite and boron etc [8-11]. The properties of metal matrix composites are inevitably a compromise between the properties of the matrix and reinforcement phases. It is clear that the composition and properties of the matrix phase affect the properties of the composite both directly, by normal strengthening mechanisms, and indirectly, by chemical interactions at the reinforcement / matrix interface. Aluminium based composites, reinforced with ceramic particles, offer improvements over the matrix alloy an elastic modulus higher than that of aluminium has a value of 70 GPa, a coefficient of thermal expansion which is closer to that of steel or of cast iron, a greater resistance to wear and an improvement in rupture stress especially at higher temperatures and possibly improved resistance to thermal fatigue. The major methods to produce aluminium metal matrix composites are stir casting, vortex mixing method, powder metallurgy, liquid metal infiltration, squeeze casting, rheocasting, and spray deposition technique. Stir casting route is the most promising one for synthesizing discontinuous reinforcement aluminum matrix composites because of its relative simplicity and easy adaptability with all shape casting processes used in metal casting industry. Stir casting involves incorporation of ceramic/metallic particulate into liquid aluminium melt and allowing the mixture to solidify. Here, the crucial thing is to create good wetting between the particulate reinforcement and the liquid aluminium alloy melt. The simplest and most commercially used technique is known as vortex technique or stir-casting technique. The vortex technique involves the introduction of pre-treated ceramic particles into the vortex of molten alloy created by the rotating impeller. In homogeneity in reinforcement distribution in these cast composites could also be a problem as a result of interaction between suspended ceramic particles and moving solid-liquid interface during solidification. Generally it is possible to incorporate up to 30% ceramic particles in the size range of 5 to 100 micrometer in a variety of molten aluminium alloys. The melt-ceramic particle slurry may be transferred directly to a shaped mould prior to complete solidification or it may be allowed to solidify in billet or rod shape so that it can be reheated to the slurry form for further processing by technique such as die casting and investment casting. The process is not suitable for the incorporation of sub-micron size ceramic particles or whiskers. Another variant of stir casting process is compo-casting, where ceramic particles are incorporated into semisolid slurry of alloy. Number of secondary processes like extrusion, rolling and forging can be applied to the cast composites with the objectives of reducing porosity and improving the particles distribution. It is known that secondary processing of the discontinuously reinforced composites can lead to break up of particle (or whisker) agglomerates, reduction or elimination of porosity, and improved bonding, all of which contribute to improve the mechanical properties of metal matrix composites (MMCs) [12-14]. MMCs can be formed by conventional deformation processes such as rolling, extrusion or forging. Extrusion has been used as one of the most common secondary processing because of its excellent preferential axial alignment of discontinuous fibers as well as large compressive hydrostatic stress state. It is reported that tribological and strength properties of aluminum matrix composites have been improved by subjecting the cast composites to hot extrusion [15-17]. The extruded composites exhibited reduced porosity, a more uniform particle distribution, improved tensile and hardness properties.The present investigation involves synthesis of composites where Al 1100 was used as the matrix material and it was alloyed with 2 wt% magnesium to impart wetting to the TiO2 particles, added as reinforcements in amounts of 3, 6, 9 and 12 wt% and hot extruded the cast composites. The objective of developing composites is to study their potential applications in structural components and the mechanical properties of these composites. There is an effort to understand the microstructure of the hot extruded composites including particle distribution and defects like porosity, in order to correlate with the observed mechanical properties measured in terms of hardness and tensile properties.
2. Material and Methods
The physical properties of Al 1100 are as shown in the Table. 1. In this investigation, Al 1100 of 99.674% purity and commercial magnesium of 99.92% purity was used as the matrix for the synthesis of particle reinforced metal matrix composites.Table 1. Physical properties of Al 1100 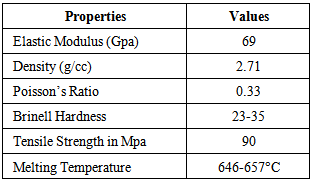 |
| |
|
The molten Al 1100 was alloyed with magnesium since it promotes wetting between the molten alloy and the oxide particles, to be used for reinforcement, in order to retain these particles inside the melt. The chemical compositions of the commercial Al 1100 and magnesium ingots, in weight percent, are as shown in the Table 2. The specifications of TiO2 powder used as reinforcement in the present work are as shown in Table 3.Table 2. Chemical composition of Al 1100 and commercial magnesium 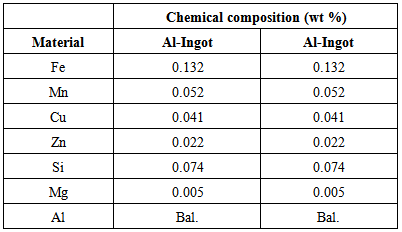 |
| |
|
Table 3. Specifications of Titanium dioxide (TiO2) powder  |
| |
|
2.1. Solidification Processing of Composites
About 600 g of commercially pure Al 1100 was melted and superheated to a 900C temperature in a clay-graphite crucible inside the muffle furnace. Before any addition, the surface of the melt was cleaned by skimming. The weighed amount of powder was added into molten Al 1100 at a processing temperature of 900C and the rate of addition of oxide particles was controlled at an approximate rate of 6-8 g/min. A coated flat blade stirrer was used to disperse the TiO2 particles in the melt. The speed of the stirrer was kept constant at 300 rpm. A non-contact type speed sensor was used to measure the stirring speed. The temperature of the melt was measured by using a digital temperature indicator connected to a chromel-alumel thermocouple. During stirring, the temperature of the slurry was maintained within ±10C of the processing temperature. A magnesium lump of 2 wt% was wrapped by aluminium foil and plunged into the melt-particle slurry after the addition of TiO2 particles. When the desired time of the stirring elapsed, reduce the stirrer speed. After completion of processing steps, the graphite stopper at the bottom of the crucible is removed by using the lever to pour the melt-particle slurry into split type graphite coated and preheated permanent steel mould of three cavities of 12 mm and one cavity of 36 mm diameter and length of 80 mm cavities are provided in the mould. When the desired time of stirring is elapsed the melt particle slurry is poured in to split type graphite coated and preheated steel mold kept right below the graphite stopper and allowed to cool in air, in order to achieve better uniformity in distribution of the particles throughout the casting.
2.2. Extrusion
All the composites and matrix of varied compositions are extruded. Before extrusion all the composites and matrix compositions were heated in furnace up to a temperature of 500°C for 90 min to homogenize the sample temperature throughout the volume. The solid lubricant graphite powder is mixed with semi solid lubricant grease with a proportion of 1: 3 by making a mixture of solid and semi solid lubricant. The mixture is applied to inner surface of the die and container in order to reduce the friction during extrusion process. The mixture is used due to its capacity of withstanding high temperature of the billet, which is to be extruded. There after they were hot extruded from 35 mm to 10 mm diameter with an extrusion ratio of 12.25 and then cooled in air. Alloy and four composites developed with the addition of different amounts of TiO2 but with the same 2 wt% of magnesium have been examined for microstructure. The scheme of sectioning the extruded alloy and composite were used to prepare specimens for metallographic studies. Samples from extruded ingots of the alloy and composite were prepared by standard metallographic procedure for metallographic examination under scanning electron microscope (SEM), Phenom Desktop SEM Phenom World, Netherland. The SEM studies were carried out with an electron beam accelerating potential of 15 kV. The polished specimens of different extruded composites and unreinforced alloys were examined under optical and scanning electron microscopes to study the presence of particles in the matrix.Average Brinell hardness has been measured for extruded alloy and composites developed by addition of TiO2 Powder, with 10 mm hardened steel ball indenter of 5000 N load was applied for 30 seconds on a sample and then the diameter of indentation was measured with the help of tool maker’s microscope. For each indentation, an average of two diameters measured perpendicular to each other was used to find the corresponding hardness. On each sample at least eight indentations were made to find the average Brinell hardness and the readings are reported as the average hardness value of the material.The tensile tests were carried out at ambient temperature for extruded composites and cast and extruded unreinforced alloys. The specimens were machined from each cast and extruded composites. The shape and dimension of the tensile specimens conforming to ASTM–E8M specification, at least three tensile specimens of 5.0 mm gauge diameter and 25 mm gauge length, machined out from segment of each extruded composite and unreinforced alloy, were tested under uniaxial tension in a Hounsfield, Monsanto, H25KS/05, Surrey, England, tensile testing machine at a strain rate of 6.67 x 10-4 s-1 and the average of ultimate tensile strength, yield strength and percentage elongation is reported as the tensile property of the material.
3. Results and Discussion
3.1. Morphology of TiO2 Particles
The size and particle shape of the TiO2 particles in the powder has been observed under SEM and the results are shown in Figure 1. The size is in the range between 2 µm and 40µm and the shape of the smaller particles are spherical while the larger particles have somewhat irregular shape. The powder has been examined for their X-ray diffraction (XRD) pattern using X-ray diffractometer in the two theta range of 5-80 using CuKα radiation target and nickel filter, step size and dwell time were suitably adjusted, which was used for identification of various phases with the help of inorganic JCPDS (joint committee on powder diffraction standards) x-ray diffraction data card which shows the TiO2 particles are fairly pure as shown in Figure 2.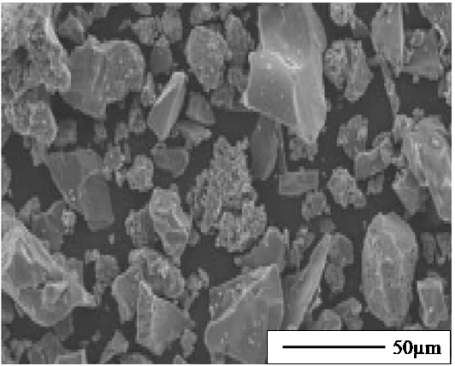 | Figure 1. SEM micrographs showing size and particle shape of the titanium dioxide powder |
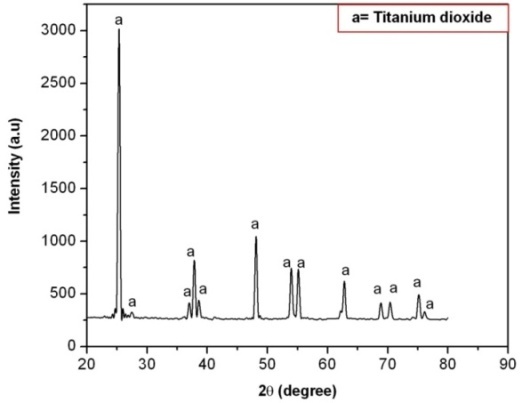 | Figure 2. XRD pattern of tio2 particles used in the synthesis of al 1100 (mg)-tio2 composites |
Different composites have been synthesized by adding TiO2 powder as given in Table 4 and these composites have been designated by using the letters AM to indicate Al 1100-Mg alloy followed by a letter P indicates the amount of powder mix of 3, 6, 9 and 12 wt% respectively.Table 4. Nominal Composition of the composites 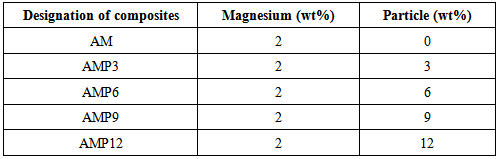 |
| |
|
The composite designated as AMP3 indicates that it has been synthesized by addition of powder by 3 wt%. Al 1100-Mg alloy has been prepared by addition of 2 wt% of magnesium into Al 1100 melt and these alloys are designated as AM. All the composites and matrix of varied compositions were hot extruded.
3.2. Scanning Electron Microscopy (SEM)
The microstructures of these in-situ composites designated as AMP3, AMP6, AMP9 and AMP12 respectively are shown in Figure. 3(a), (b), (c) and (d) respectively.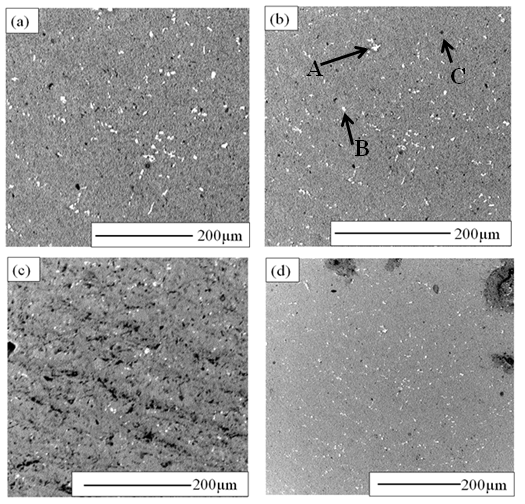 | Figure 3. Sem micrographs of different extruded composites developed by increasing amounts of tio2 powder designated as (a) amp3 (b) amp6 (c) amp9 and (d) amp12 respectively |
The SEM micrographs clearly reveals possibly the presence of intermetallic compound (bright needles, A-marked by arrow) and reaction will also produce alumina (B-marked by arrow) by oxidizing aluminium and also some dark spots (C-marked by arrow) due to porosities which could be seen very clearly in Figure 3(b). There are increasing numbers of bright particles of oxide with increasing addition of TiO2 powder as evident from microstructures of composites developed by addition of 3, 6, 9 and 12 wt% TiO2 powder respectively in Figure 3 (a), (b), (c) and (d). The microstructure clearly reveals possibly the presence of intermetallic compound Al3Mg2 (bright needles) and reaction will also produce alumina by oxidizing aluminium and also some dark spots due to porosities which could be seen very clearly in Figure.3.
3.3. Mechanical Properties of Al 1100 (Mg) –TiO2 Composites
3.3.1. Brinnell Hardness
Average Brinell hardness has been measured and the readings are reported as the average hardness value of the material. The hardness of the extruded composites increases with increasing addition of TiO2 particles to AM base alloys as shown in Figure 4. After extrusion there is an increase in hardness which may be due to healing of porosity and the strain remaining after incomplete dynamic process of recovery and recrystallization.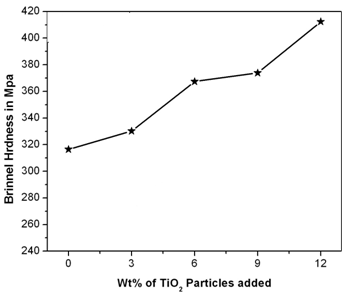 | Figure 4. Average hardness in extruded alloy and composites developed by increasing addition of TiO2 powder |
3.3.2. Tensile Properties
The stress-strain behaviour of the extruded alloy and composites developed by addition of different amounts of TiO2 powder has been determined by tensile tests and the results are shown in Figure 5.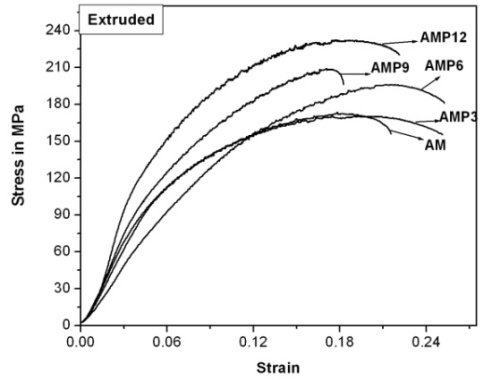 | Figure 5. Tensile stress-strain behaviour of extruded AM alloy and composites |
After the extrusion there is significant improvement in the strength and ductility with powder addition. Extrusion reduces the shape size and distribution of the porosity in the material and thereby increases the mechanical properties but it could not reduce the porosity completely.The yield strength and tensile strength of the extruded composites increases with increasing addition of TiO2 particles to AM base alloys as shown in Figure 6. The 12 wt% of TiO2 powder addition extruded composite exhibited high yield strength and tensile strength. The improved strength in extruded composites may be due to reduction in porosity content, reduction in grain size and uniform distribution of TiO2 particles. This may be due to compressive strains involved in the extrusion process. The extruded composite with 6 wt% of TiO2 powder exhibiting higher percentage of elongation. Whereas percentage elongation in extruded composite decreases with the increase in the reinforcement content for 3 wt% of TiO2 and then percentage elongation again increases with 6 wt% of reinforcement. This may be due to high porosity content. When the content increased to 12 wt% of TiO2, there is slight increase in percentage elongation may be due to the clustering of particles in the composites.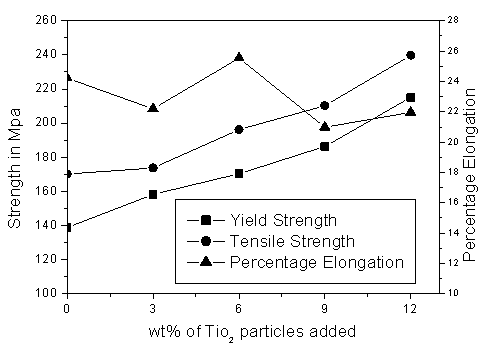 | Figure 6. Comparison of yield strength, tensile strength and percentage elongation in extruded alloy and composites with increasing addition of tio2 powder |
4. Conclusions
The conclusions of the present study are outlined below. 1. The Liquid metallurgy route (stir casting technique) was successfully adopted in the preparation of alloy and composites containing 0, 3, 6, 9 and 12 wt% of TiO2 powder reinforcement.2. XRD analysis shows that the TiO2 particles are fairly pure and SEM analysis shows that the TiO2 particles have irregular shapes.3. Due to hot extrusion, reduction in porosity content, matrix grain size and grain refinement is achieved. This may be due to the action of compressive forces in hot extrusion process. 4. The hardness and tensile strength properties of the extruded composites is found to be increased with the increase in percentage of reinforcement. Higher hardness and tensile strength properties are noticed for the 12 wt% of TiO2 powder addition.5. The 12 wt% extruded composite developed after extrusion exhibited good strength and percentage of elongation around 21.96%.
References
[1] | J.M. Wu, Z.Z. Li, 2000, Nanostructured composite obtained by mechanically driven reduction reaction of CuO and Al powder mixture, Journal Alloys Compounds. 299 (1) 9-16. |
[2] | Shashi Prakash Dwivedi, Satpal Sharma, Raghvendra Kumar Mishra, 2014, A356 Aluminum Alloy and applications- A Review, Advanced Materials Manufacturing and Characterization, 4 81-86. |
[3] | M. Taya, R.J. Arsenault, Metal Matrix Composite, Pergamon, Oxford, 210S, 1989. |
[4] | Bhargavi Rebba, N. Ramanaiah, 2014, Studies on Mechanical Properties of 2024 Al –B4c Composites, Advanced Materials Manufacturing & Characterization, 4 (1), 42-46. |
[5] | P.B. Pawar, Abhay A. Utpat, 2014, Development of Aluminium Based Silicon Carbide Particulate Metal Matrix Composite for Spur Gear, Procedia Materials Science 6, 1150 – 1156. |
[6] | V. Bharath, Madev Nagaral, V. Auradib and S. A. Kori, 2014, Preparation of 6061Al-Al2O3 MMC's by Stir Casting and Evaluation of Mechanical and Wear Properties, Procedia Materials Science 6, 1658 – 1667. |
[7] | S.C. Tjong, Z.Y. Ma, 2000, Microstructural and mechanical Characteristics of In Situ Metal Matrix Composites, Mater. Sci. Eng. R, 29, 49-113. |
[8] | A.H. Abdulhaqq, P. K. Ghosh, S.C. Jain, and Ray, S., 2005, Processing, microstructure, and mechanical properties of cast in-SituAl(Mg, Mn)-Al2 O3 (MnO2 ) composite, Metall. and Mater. Trans. 36, 2211-2223. |
[9] | HX Peng, DZ Wang, L Geng, CK Yao, JF Mao, 1997 Evaluation of the microstructure of in-situ reaction processed Al3Ti-Al2O3-Al composite, Scripta materialia 37 (2), 199-204. |
[10] | Yuyong Chen, and D.D.L. Chung, 1995, Ductile and strong aluminium-matrix titanium aluminide formed in situ from aluminium, titanium di oxide and sodium hexafluoroaluminate, Journal of materials science 30, 4609-4616. |
[11] | H.X. Peng, Z. Fan and D.Z. Wang, 2000, In situ Al3Ti-Al2O3 intermetallic matrix composite: Synthesi, microstructure and compressive behavior, Journal of materials research, 15 (9), 1943-1949. |
[12] | Yuyong Chen, and Chung, D.D.L, 1996, In situ Al-TiB composite obtained by stir casting, composite materials research laboratory, state university of New York at Buffalo, Buffalo., 311-315. |
[13] | Amir Pakdel, and Hassan Farhangi., 2009, Influence of Extrusion Ratio On The Mechanical Behavior of AA 6061/SiC Composites, The Arabian Journal for Science and Engineering, 34(1C) 167. |
[14] | Ramesh, C.S, Adarsha Hirianiah, Harishanad, K.S, and Naveen Prakash Noronha., 2012, A review on hot extrusion of metal matrix composites (MMC's), “International Journal of Engineering and Science”, ISBN: 2319-6483,ISSN: 2278-4721,1 (10),30-35. |
[15] | S.S Joshi, N. Ramakrishna, P. Ramakrishna, 2000, Hot extrusion of Al/SiCp composites, Proceedings of the Third International Conferences on "Advances in composites", ADCOMP. 911. |
[16] | V.V. Ganesh, C.K. Lee, M. Gupta, 2002, Enhancing the tensile modulus and strength of an aluminium alloy using interconnected reinforcement methodology, Materials Science and Engineering A. 333(1-2),193-198. |
[17] | Ghanaraja. S., Vinuth Kumar. K.L. Raju. H.P. and Ravikumar. K.S. 2014, Processing and Mechanical Properties of Hot Extruded Al (Mg)-Al2O3 composites". Procedia Material Science. (Article in press) |