Manjunatha G. , Rajesh S. , Raji George, Kumara Naik
Dept. of Mechanical Engg. M.S. Ramaiah Institute of Technology, Bangalore, India
Correspondence to: Manjunatha G. , Dept. of Mechanical Engg. M.S. Ramaiah Institute of Technology, Bangalore, India.
Email: |  |
Copyright © 2015 Scientific & Academic Publishing. All Rights Reserved.
Abstract
Nanocomposites of epoxy with 0.25, 0.5, 0.75 1.0, 1.25 and 1.5 wt. % Multi walled carbon nanotubes (MWCNT) were fabricated by dispersing within an epoxy resin using a sonication process followed by mechanical stirring. The samples were post heat treated at different temperature 50°C, 100°C and 150°C. The mechanical properties of the composites were investigated. Wear and hardness properties measurements of these nanocomposites indicated higher wear rate and low hardness with increasing concentration of MWCNT and at heat treatment condition. The incorporation of less concentration of MWCNT significantly improved the wear rate and hardness at heat treatment condition compared to pure epoxy samples.
Keywords:
Epoxy, MWCNT, Nanocomposites
Cite this paper: Manjunatha G. , Rajesh S. , Raji George, Kumara Naik , Influence of Post Heat Treatment Temperatures on Wear Properties of MWCNTs Reinforced Epoxy Composites, American Journal of Materials Science, Vol. 5 No. 3C, 2015, pp. 183-187. doi: 10.5923/c.materials.201502.35.
1. Introduction
Epoxy resins are the most common class of thermosetting resins used in various applications. These include composite materials, adhesives, coatings, potting compounds etc. Due to the high content of rigid groups and high cross-linking density, normally an epoxy resin is brittle, high-modulus material after curing [1]. The concept of combining /mixing various materials through synergy is the most successful way to achieve materials with desired properties with great efficiency and cost effectiveness [2]. Development of strong durable and cost efficient polymer matrix materials for current and future technologies is still an unsolved problem .The field of nanoscience has blossomed over decades and has widespread its application in many areas [3]. Many attempts have been made to modify epoxy by reinforcing nanomaterials to polymer matrix composites [4]. So, search for novel materials as reinforcing fillers is of prime importance and has wide scope. Carbon nanotubes are considered to be one of novel reinforcement for developing advanced nanocomposites due to their outstanding thermo-mechanical properties. Carbon nanotubes (CNTs) are long one dimensional structure made up entirely of carbon in which carbon atoms are SP2 hybridized. Carbon nanotubes were first synthesized by Iijima in 1991. In this family, the multi-walled carbon nanotubes are of special interest for the scientist and engineers and will be the subject of this research work. Structurally multi walled carbon nanotubes consist of multiple layers of graphite which are rolled on themselves to form a tubular structure. Superior strength, high young’s modulus, fracture toughness , high specific geometry, extremely large surface area (surface to volume ratio), gas impermeability, very good thermal and electrical conductivity suits as a perfect match to be used in various applications such as aerospace, photonics.Mahesh et al. [4] fabricated epoxy nanocomposites by reinforcing Graphene-Multiwalled Carbon Nanotube with different weight fraction (0.25%, 0.5%, 0.75%, 1%, 1.25%, 1.5%, 1.75% and 2%) of the reinforcement by solution intercalation method. The fabricated specimens were subjected to hardness and tensile test. The mechanical properties of those composites were investigated and found increase in hardness and young’s modulus with increased weight fraction of the reinforcement compared to the base matrix fabricated using the same process. Dong et al. [5] fabricated Multi-walled carbon nanotubes/ epoxy resin (MWNTs/EP) nanocomposites with different weight proportion of MWNTs (0 to 4%). The MWNTs are synthesized by a catalytic chemical vapor deposition method and it was purified by chemical treatment process, and compared the friction and wear behaviors of the nanocomposites with the pure epoxy, MWNTs/EP nanocomposites have higher wear resistance and also smaller friction coefficient than pure epoxy.Smrutisikha et al. [6] fabricated carbon nanofiber reinforced Epoxy composites by varying % of carbon nanofiber up to 1 wt% at room temperature and cured those specimens at two different conditions .i.e. (room temperature and refrigerated at 4°C) and characterized those specimens using Raman spectroscopy. Mechanical properties were also investigated and found that Flexural modulus and hardness were enhanced in refrigerated samples due to prevention of aggregates of nanoparticles during curing condition.Sarah et al. [7] analyzed the effect of replacing the entire volume of structural Aluminium with carbon nanotube reinforced polymer (CNRP) as primary structural material, without any modifications to the geometry or design of the airframe Airbus A320, Boeing 747-400 and 757-200, and Embraer E145. The benefits are reduction in mass at take-off, increases in aircraft flight range and cruise altitude, and a decrease in fuel consumption.Shankar et al. [8] Fabricated polymer/cement beams reinforced with multi-walled carbon nanotubes (MWCNTs). The weight percentage of MWCNTs was varied at 0.25, 0.5, 0.75 and 1% by weight of polymer/cement matrix. The ultra-sonication process is carried out to enhance the dispersion of MWCNTs in matrix material. And the Composite beams were tested under flexure in order to evaluate their mechanical property such as load–deflection criteria. The tested results were then compared with the plain polymer/cement beams. The polymer/cement beams reinforced with multi-walled carbon nanotubes are have improved properties than plain polymer/cement beams.
2. Materials
The Multi walled carbon nanotubes used in this study was procured from Nanoshell Pvt Ltd. Punjab, which was produced by Arc discharge method, having purity of about 95 to 99% pure, 10 – 100 nm in length, 20 micron meter in dia and has a surface area of 200 – 300 m²/gm. Epoxy resin used was Lapox (L-12), Procured from Atul Ltd Gujarat, it is an unmodified resin of DGEBA (Diglyceride Ether of Bisphenol A), and Hardener used was K-6 with mix ratio of 10:1 and low viscosity of 5000 – 6000MPa-. Acetone (2 Propanane-Dimethyl Ketone) was procured from Vasa scientific Bangalore.
3. Experimental Details
Initially, the pure Epoxy sample was fabricated by mixing epoxy resin with curing agent in 10:1 ratio using mechanical stirrer at room temperature and mixture was degassed using vacuum pump for 5 – 10 minutes and poured into moulds and cured at room temperature for 24 hours and then post heated at different temperatures (50, 100, 150°C) for 1 hour in electric oven. Later on, Multi walled carbon nanotubes (0.25, 0.50, 0.75, 1.0, 1.25, 1.50) % was dispersed in acetone by magnetic stirring for 20mins, calculated and measured quantity of epoxy resin was added to the above mixture and sonicated for 20mins in an ice bath to avoid the heat generated during sonication process, acetone was evaporated by exposing the above mixture to infrared lamp. Hardener was added to the mixture (10:1 ratio) and mechanical stirred for about 5-10 minutes, and also the degasification was carried out for 5 -10 minutes using vacuum pump and above mixture was poured into silicone moulds and cured at room temperature for 24 hours. After curing the samples were subjected to post heat treatment at 50,100 and 150°C for 1 hour each and were subjected to mechanical testing.
3.1. Hardness Test
Hardness test was performed using Rockwell Hardness tester according to ASTM D785 standard. A ball indentor of 1/16th of an inch was used with a major load of 60 kgf by pressing the material under the pressure of the knob. Test was carried out at room temperature and 5 specimens were tested for each level of nanofiller loading. The dimensions of the specimen were 6 mm dia and 7 mm length.
3.2. Wear Test
Wear test was performed according to ASTM G99-95b standard by using Pin on disc tribometer, the specimens dimensions is 7mm diameter and 30mm length. The wear track of pin on disc wear tester is cleaned thoroughly with acetone before test. The specimen is pressed against the disc at a specified load usually by means of an arm or lever and attached weights, the speed and load was kept constant.
4. Results and Discussions
4.1. Hardness Test Results
Hardness test was conducted on MWCNT/EP nanocomposites on 5 specimens of each wt% of MWCNTs (pure epoxy, 0.25, 0.50, 0.75, 1.0, 1.25, 1.50 %) and post heat treated at different temperature conditions (50, 100, 150°C). The results of which are shown in the figure 1.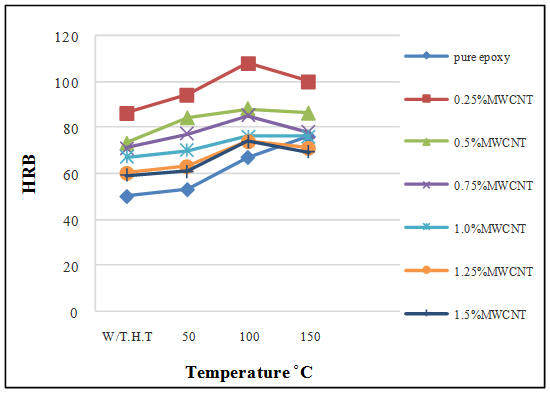 | Figure 1. Hardness values of MWCNT/EP nanocomposites at different MWCNT wt. % and at different post heat treatment temperature |
4.2. Wear Test Results
The wear test was conducted by using Pin on disc tribometer by keeping load and speed as constant and by varying time. The test results are shown in the figure 2, 3, 4 and 5.Wear rate of without post heat treated MWCNTs/EP nanocomposites is presented in figure 2.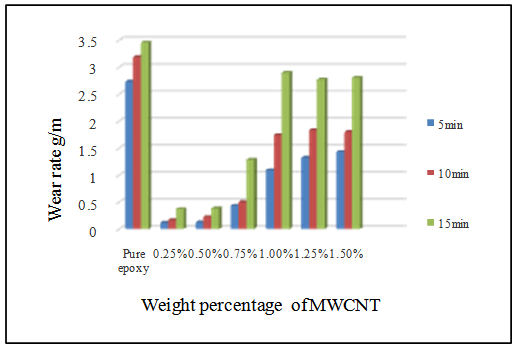 | Figure 2. Wear rate of without post heat treated MWCNT/EP nanocomposites |
Wear rate of MWCNTs/EP nanocomposites post heat treated at 50°C is presented in figure 3.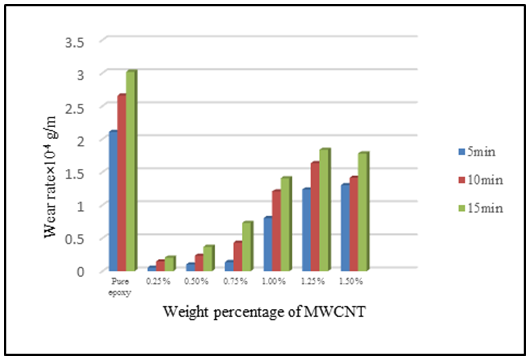 | Figure 3. Wear rate of MWCNT/EP nanocomposites post heat treated at 50°C |
Wear rate of MWCNTs/EP nanocomposites post heat treated at 100°C is presented in figure 4.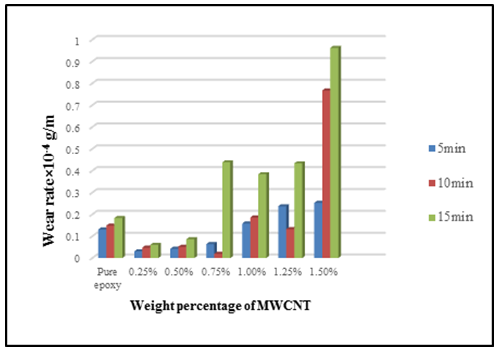 | Figure 4. Wear rate of MWCNT/EP nanocomposites post heat treated at 100°C |
Wear rate of MWCNTs/EP nanocomposites post heat treated at 150°C is presented in figure 5.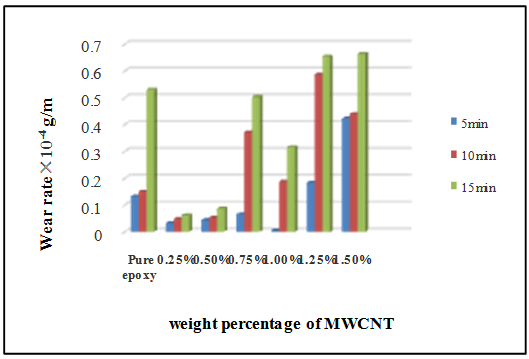 | Figure 5. Wear rate of MWCNT/EP nanocomposites post heat treated at 150°C |
The figure 1 shows the hardness values obtained for MWCNTs/EP nanocomposites for different MWCNTs wt. % and for different post heat treatment temperature. The hardness number for 0.25% MWCNTs is 50 and 10, 12, 20, 25, 27% higher compared to pure epoxy and with 0.5, 0.75, 1.0, 1.25, 1.5% of MWCNT. The hardness number for post heat treated at 100°C is higher compared to without post heat treated at 50, and 150°C.The figure 2, 3, 4, and 5 shows the wear rate of MWCNT/EP nanocomposites, without and with post heat treated at 50, 100, 150°C and for different concentrations of MWCNTs. The wear rate at 0.25% MWCNTs is low compared to pure epoxy and 0.5, 0.75, 1.0, 1.25, and 1.5% MWCNT, because due to uniform dispersion of nanoparticle. The wear rate for post heat treated at 100°C is low compared to without post heat treated at 50, and 150°C.
4.3. Characterization
4.3.1. Scanning Electron Microscope (SEM)
The SEM morphology of MWCNTs/EP nanocomposites were investigated to determine the dispersion of MWCNTs in the nanocomposites (0.25, 1.0 1.5%) and post heat treated at 100°C. The SEM of 0.25% MWCNTs at 100°C post heat treatment temperature condition taken at 10000X, 25000X and 100000X magnification level is shown in figure 6(a), and 6(b).Figure 6(a) and 6(b) shows the SEM images of 0.25% MWCNT post heat treated at 100°C, the particles of MWCNTs had good dispersion, and also the formation of chain link was observed due to uniform distribution of MWCNTs with epoxy.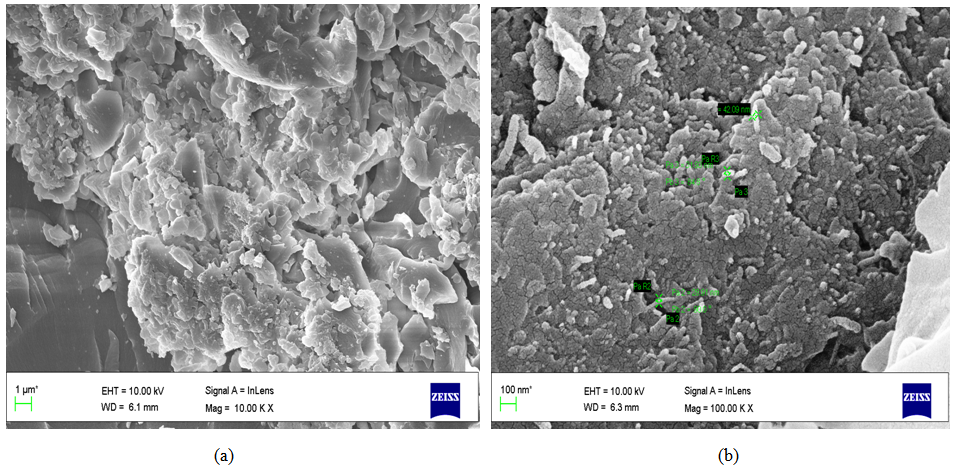 | Figure 6. (a) and (b) SEM microstructure of 0.25% MWCNTs heat treated at 100°C at 10000X and 100000 X magnification level |
Figure 7(a) and 7(b) shows SEM images of 1.0% MWCNTs post heat treated at 100°C, the particles of MWCNTS was not properly dispersed and there is no chain link formation was observed. It is observed that MWCNTs were agglomerated.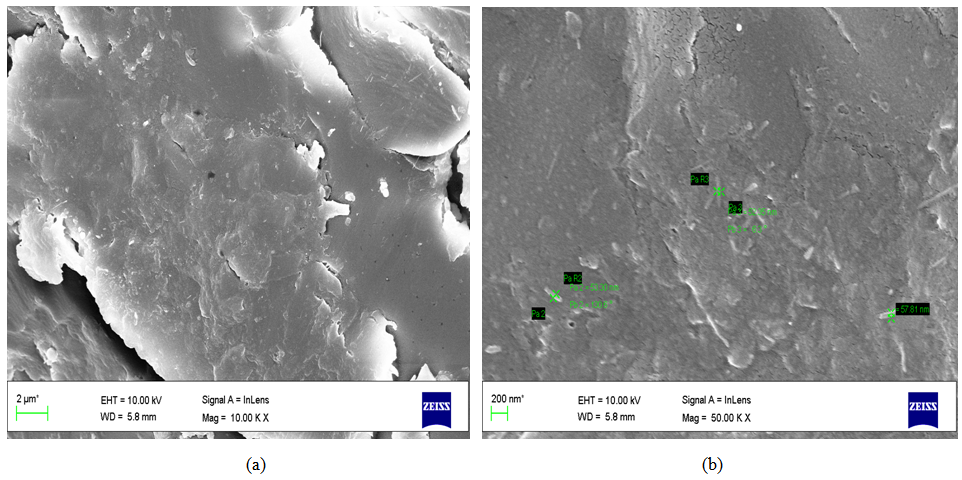 | Figure 7. (a) and (b) SEM microstructure of 1.0 % MWCNTs heat treated at 100°C at 10000X and 50000X magnification level |
Figure 8(a) and 8(b) shows SEM images of 1.5% MWCNT post heat treated at 100°C. The particles of MWCNTs are formed cluster due to poor distribution, also agglomerates were observed throughout which lead to typical stress concentration and causes to early failure. 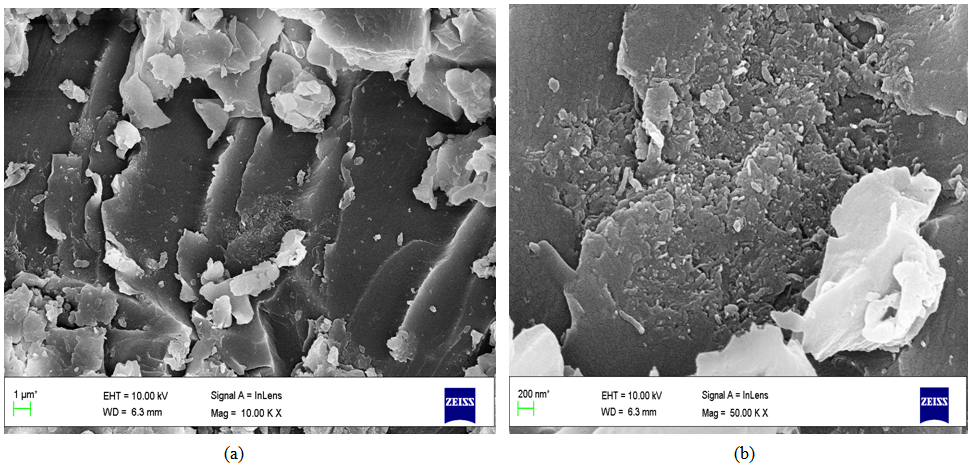 | Figure 8. (a) and (b) SEM microstructure of 1.5% MWCNTs heat treated at 100°C at 10000X and 50000 X magnification level |
5. Conclusions
1. Multi walled carbon nanotube reinforced polymer composite were fabricated successfully by Casting Method.2. The ultra-sonication is an efficient method of infusing MWCNTs in to epoxy resin when MWCNTs weight fraction is 0.25wt% and at higher wt% of MWCNTs leads to agglomeration. 3. The hardness of pure epoxy at 100°C is 67 HRB, but for 0.25% MWCNTs/EP composite is 108 HRB which is almost near to double of pure epoxy.4. The incorporation of MWCNTs significantly decreases the wear rate of epoxy. The wear rate of MWCNTs/EP nanocomposites decreases at 0.25wt% compared to higher percentage of MWCNTs, however wear rate increases with increasing the time from 5 to 15min.5. At 0.25 wt% MWCNTs content, the MWCNTs had better dispersion. The interfacial bonding between epoxy and nano material was found good and formation of chain link with very less agglomerates were observed in SEM.6. Increase in addition of MWCNTs to the epoxy decrease the mechanical properties of the composites. The improved properties can be obtained by addition of lower weight percentage of MWCNTs into epoxy.
References
[1] | S. Ganguli, M. Bhuyan, L. Allie, H. Aglan. “Effect of multi-walled carbon nanotube reinforcement on the fracture behavior of a tetra functional epoxy”. Journal of materials science 40 (2005) 3593–3595. |
[2] | Muhammad Mansoor, Muhammad Shahid, Amir Habib. “Strengthening of Bisphenol-A Epoxy Resin by the Addition of Multi-Wall Carbon Nanotubes” Arab J Sci Eng (2014)39:6411-6420. |
[3] | E.N. Ganesh. “Single Walled and Multi Walled Carbon Nanotube Structure, Synthesis and Applications”. ISSN: 2278-3075, Volume-2, Issue-4, March 2013 Pg no 311-320. |
[4] | Mahesh. V.M, B.K. Muralidhara, Raji George “Influence of different nanomaterials on the mechanical properties of epoxy matrix composites – a comparative study “IJIRSET Vol. 3, Issue 7, July 2014. |
[5] | B. Dong, Z. Yang, Huang and H.-L. Li. “Study on tribological properties of multi-walled carbon nanotubes/epoxy resin nanocomposites”. Tribology Letters, Vol. 20, Nos. 3–4, December 2005 (2005). |
[6] | Smrutisikha Bal “Experimental study of mechanical and electrical properties of carbon nanofiber/epoxy composites “Journal of Materials and Design. |
[7] | Sarah E. O’Donnell and Kevin R. Sprong and Brennan M. Haltli. “Potential Impact of Carbon Nanotube Reinforced Polymer Composite on Commercial Aircraft Performance and Economics”. American Institute of Aeronautics and Astronautics. |
[8] | Shankar A and Hallad, Nagaraj R. and Banapurmath, Anand M. Hunashyal. “Experimental Investigation to study the Effect of Multi Walled Carbon Nanotubes in Polymer / Cement-Based Matrix for Structural Applications” The International Journal of Science & Technology. |
[9] | O. Jacobs, W. Xu, B. Scha¨ dela and W. Wub “Wear behavior of carbon nanotube reinforced epoxy resin composites”. Tribology Letters, Vol. 23, No. 1, July 2006 Pg. no 65-75. |
[10] | Khalid R. Al-Rawi and Adawiya j. Hedarand Olfat A. Mahmood. “Effect of Different Multi-Walled Carbon Nanotubes (MWCNTs) Type on Mechanical Properties of Epoxy Resin Nanocomposites” International Journal of Application or Innovation in Engineering & Management (IJAIEM). |