Noel Deepak Shiri 1, Thirumaleshwara Bhat 1, Shreeranga Bhat 1, Girish Kumar 2
1Department of Mechanical Engineering, St. Joseph Engineering College, Mangaluru, India
2Department of Mechanical Engineering, Sri Dharmasthala Manjunatheshwara Institute of Technology, Ujire, India
Correspondence to: Noel Deepak Shiri , Department of Mechanical Engineering, St. Joseph Engineering College, Mangaluru, India.
Email: |  |
Copyright © 2015 Scientific & Academic Publishing. All Rights Reserved.
Abstract
In this paper an effort has been made to study the effects of ageing variables on the abrasive wear behavior of Aluminium 6061 alloy and Silicon Carbide particulate reinforced Aluminum 6061 Composites. The composite material was prepared by using stir casting technique. The as-cast material was heat treated by a method called homogenization annealing to obtain uniform grain size. Fractional factorial experimentation was carried out using four parameters namely volume fraction of reinforcement, solutionizing time, ageing temperature and ageing time at three different levels. The results show that the predicted values for abrasive wear loss were in close agreement with experimental results. And moreover the volume fraction of reinforcing particles was found to be most influential parameter in affecting the wear loss of the materials followed by the ageing temperature and all the other parameters and their interactions.
Keywords:
Taguchi’s Technique, Ageing Parameters, Abrasive Wear, Regression Analysis
Cite this paper: Noel Deepak Shiri , Thirumaleshwara Bhat , Shreeranga Bhat , Girish Kumar , Effect of Heat Treatment Variables on the Abrasive Wear Behaviour of Al-6061 Alloy and Al 6061-SiCP Composites Using Taguchi Technique, American Journal of Materials Science, Vol. 5 No. 3C, 2015, pp. 151-156. doi: 10.5923/c.materials.201502.30.
1. Introduction
Metal matrix composites (MMC) are a new variety of materials with metals as the base and with usually ceramic phases added as reinforcements to enhance their physical and mechanical properties. The reinforcements which are usually added to the matrix can be in the form of fibers, whiskers and particulates. Properties of the metal matrix composites can be tailored by varying the nature of the constituents and their volume fraction of the reinforcement. They present superior blend of properties in such a way that today no existing monolithic material can equal. They are more and more being used in the aerospace and automobile industries because of their enhanced strength, stiffness and increased wear resistance [1]. Aluminum is the most accepted matrix for metal matrix composites because of its low density, ability to be strengthened by precipitation hardening, very good corrosion resistance, high thermal conductivity and electrical conductivity, and its high damping capacity. They are usually reinforced with SiC, Al2O3, carbon and other ceramic materials etc [2]. Stir casting technique is the most promising method for making particulate reinforced aluminum alloy composite because of its simplicity and flexibility to all shapes of castings and stir casting is generally accepted processing route which is practiced commercially [3]. Precipitation hardening or age hardening is a heat treatment technique used to strengthen malleable materials, especially non-ferrous alloys including most structural alloys of aluminum and titanium [4]. E-Baradie et al. [5] has examined the age-hardening behavior of discontinuously reinforced aluminum matrix composites that has been a subject of great interest both from scientific and technological view-points. The nature of the change in the kinetics and the magnitude of hardening during Ageing of these composites depend on: (a) the matrix material; (b) the type of reinforcement including its size, shape and volume fraction; (c) the method of processing the composite; (d) the temperature of Ageing; and (e) the post-fabrication treatment. Muratoglu et al. [6] has found that the application of Ageing before and after diffusion bonding decreases SiC particulate accretion, and increases other elemental concentration at interface of the composite. Gupta and Surappa [7] showed that an increase in Ageing kinetics is associated with an increase in volume fraction of SiC particulates in the composite. The results of accelerated Ageing kinetics thus observed were rationalized in terms of an increase in the heterogeneous nucleation volume in the metallic matrix and the constitutional characteristics of the Al-SiC inter-facial region. Veeresh et al. [8] reported that the SiC and Al2O3 particulates resulted in improving the hardness and density of their respective composites and by further increasing the percentage of these reinforcements contributed to increased hardness and density of the composites. Design of experiments (DOE) is a powerful tool that can be used in a variety of experimental situations. DOE allows for multiple input factors to be manipulated determining their effect on a desired output (response). By doing so, DOE can identify important interactions that may be missed when experimenting with one factor at a time. By applying the Taguchi’s Technique it is possible for us to significantly reduce the time required for experimental investigations. It is one of the most widely used powerful tool in Design of Experiments [9].Taguchi method uses Signal-to-Noise Ratio (S/N Ratio) as the quality characteristic of choice. The S-N ratio characteristics can be divided into three categories when the characteristic is continuous as shown in the equation below:(1) “Nominal is Best” characteristic: | (1) |
(2) “Smaller is Better” characteristic: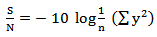 | (2) |
(3) “Larger is Better” characteristic: | (3) |
y is the average of observed data,
the variation of y, n the number of observations,and y the observed data or each type of the characteristics, with the above S/N ratio transformation [10].
2. Experimental Investigation
2.1. Materials
Aluminium Alloy 6061 was used as the matrix material and it has been confirmed by studying the chemical composition (%) analysis using Arc Atomic emission spectrometer, the results are shown in Table 1.Table 1. Composition Analysis of Al6061 alloy 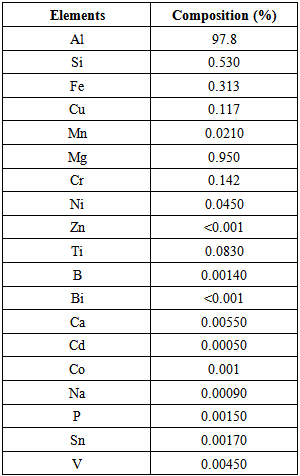 |
| |
|
Silicon Carbide (SiCp) reinforcement particles was used with size range 30 μm - 60 μm. The composites were prepared by Stir Casting technique, the Al6061 alloy was melted, held at 800°C temperature for two hours and effectively degassed, and then a ceramic-coated steel impeller was placed inside the crucible. The impeller was rotated at speed of 400 RPM and the temperature of the furnace temperature was maintained at 770°C to 800°C during the stirring action. Preheated SiCp particulates were added into the vortex of the molten alloy during the continuous stirring of the molten alloy. Mechanical stirring of the molten alloy was carried out for around 15 minutes. Then the molten composite was poured into preheated cast iron mould boxes and allowed to solidify. Three materials were cast, one was base alloy of Al6061 and the other two materials were MMC's with varying volume fraction of 7.5% and 15% volume SiC particulates were cast for the experimental work.
2.2. Taguchi Experimental Array Design
In the present study four factors at three levels were selected. The four parameters selected are (1) Volume fraction of Reinforcement, (2) Solutionizing Time, (3) Ageing Temperature and (4) Ageing Time. Solutionizing Temperature was kept constant for all heat treatment operations at 550°C. The three levels for each of the four parameters selected are shown in Table 2.Table 2. Heat Treatment Parameters for 4 factors and 3 levels 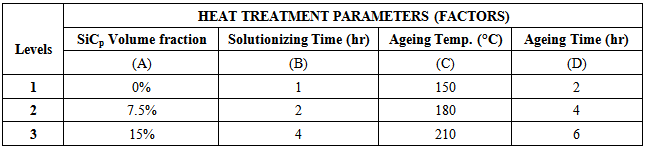 |
| |
|
In the full factorial method of experimental study, the measurements for Abrasive wear (Volumetric Wear Loss) as a function of four factors and three levels would require (level)factors = 34 or 81 experiments and with three replications for all the combinations of parameters would require 243 number of specimens to perform 81 experiments. The same results can be obtained by using Taguchi's L27 fractional factorial experimentation. Here only 27 experiments have to be performed for three replications and only 81 number of specimens have to be prepared to perform 27 experiments for each type of experimental run. Before performing the wear tests, all the materials were subjected to homogenization annealing to obtain uniform grain size before carrying out the required experimental heat treatments to ensure uniform grain size.
2.3. Experimental Setup and Abrasive Wear Testing
The abrasive wear test was performed on different heat treated materials using the DUCOM TR-201C Pin-on-Disc machine. The samples were machined according to the ASTM G99 – 95 standards and the specimens with a diameter of 10 mm and height of 40 mm was cut and machined in a lathe machine from cast samples. During the test, specimen was held stationary against the rotating abrasive disc and a normal force was applied through a lever mechanism. A series of abrasive wear tests were conducted with constant track radius of 44 mm, sliding distance of 500 m, normal load of 10N and a speed of 500 RPM. Material loss from the composite surface was measured using a precision electronic balance with accuracy ±0.0001 g. SiC abrasive wheel P100 coarse (rough) grade was used for the test. After the abrasive wear test the specimens were removed from the machine and cleaned with acetone, dried and weighed.Volumetric Wear Loss expressed as:- | (4) |
Where, | (5) |
 | (6) |
Where m = mi – mf = Difference of mass of the specimen in grams (g),ρ = Density of the specimen (g/mm3), V = Volumetric wear loss (mm3),mi = Initial of mass of the specimen in grams (g), mf = Initial of mass of the specimen in grams (g), v = Volume of the specimen (mm3), d = Diameter of the specimen (mm), l = Length of the specimen (mm).
3. Results and Discussions
3.1. Microstructure
SEM image of the silicon carbide powder shows a mixture of angular and irregular shaped particles dispersed randomly and these particles have a wide size range from 30 μm to 60 μm as shown in Figure 1. The microstructures of homogenized Al6061 alloy, Al6061 + 7.5% SiC MMC and Al 6061 + 15% SiC MMC are shown in the Figure 2 (a to c).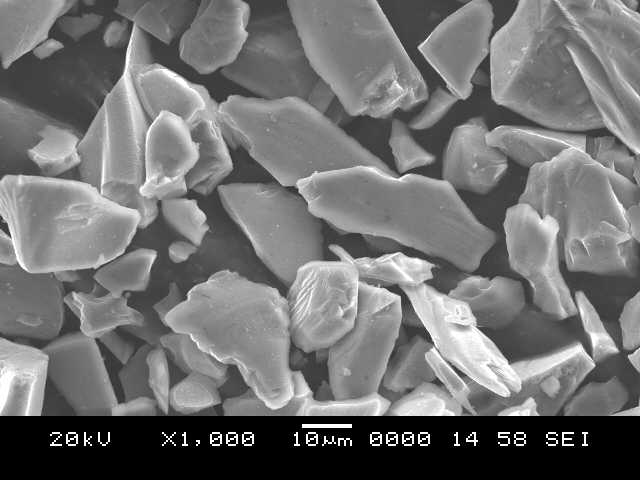 | Figure 1. SEM image of Silicon Carbide powder |
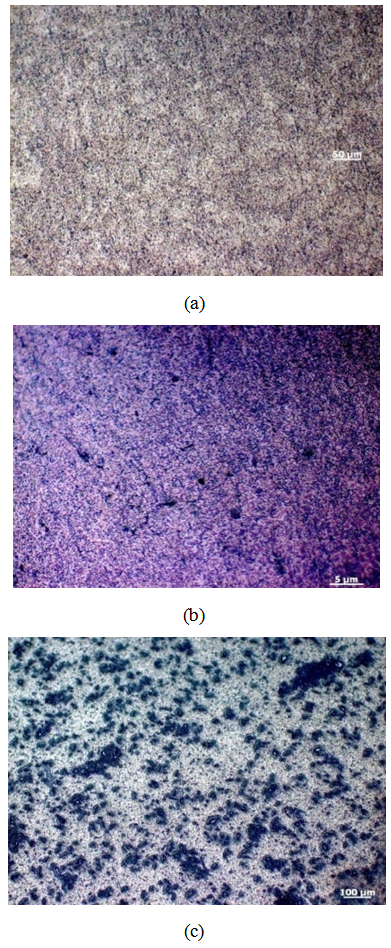 | Figure 2. Microstructures of the homogenized (a) Al6061 alloy (b) 7.5 vol% SiCp MMC and (c) 15 vol% SiCp MMC |
3.2. Abrasive Wear using Taguchi Method
Results of abrasive wear tests conducted according to the Taguchi’s orthogonal array for various combinations of parameters are given in Table 3. Statistical software package MINITAB Release 14 was used to analyze the results of the orthogonal experiments, depending on the number of factors, interactions and their levels. The Signal to Noise ratio of “Smaller is Better” is selected for Volumetric Wear Loss, since the goal is to find the lowest wear loss values. Hence, the expression for the signal to noise in Equation (2) was used for analysis.Table 3. L27 orthogonal array for Abrasive Wear (Volumetric Wear Loss) 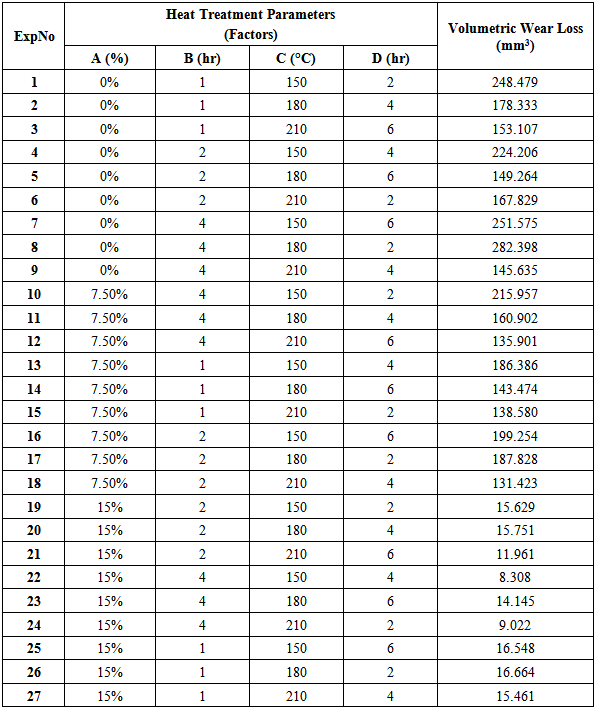 |
| |
|
By examining from the main effects plot for S/N Ratio shown in Figure 3 we can concluded that for volumetric wear loss, the factors with the largest effect appears to be Volume fraction followed by Ageing Temperature. Optimal heat treatment combination predicted for various parameters from Figure 3 are (A) Volume fraction of Reinforcement = 15%, (B) Solutionizing Time = 4 hours, (C) Ageing Temperature = 210°C and (D) Ageing Time = 4 hours.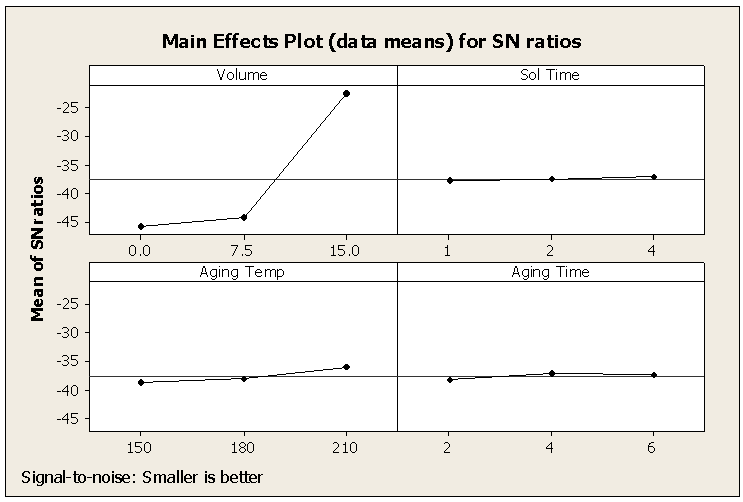 | Figure 3. Effect of control factors on Volumetric Wear Loss (S/N Ratio) |
Analysis of Variance (ANOVA) was used to investigate which design parameter significantly affects the Abrasive wear characteristic. The analysis was carried out at 95% confidence level. Table 4 shows the summary of ANOVA for volumetric wear loss and column 8 of Table 4 indicates the percentage contribution (PC) of each source (individual factors and their interactions). From the ANOVA table it can be seen that the factor volume fraction (A) has the highest significance (PC=85.73%) followed by the ageing temperature (C) with (PC=5.61%) and the interaction of the factors between volume fraction and ageing temperature (A × C) with (PC=2.85%). Also the ‘P’ value for any source which is less than 0.05, indicates that from the selected factors only volume fraction, ageing temperature had significant effect in the volumetric wear loss.Table 4. ANOVA table for Volumetric Wear Loss 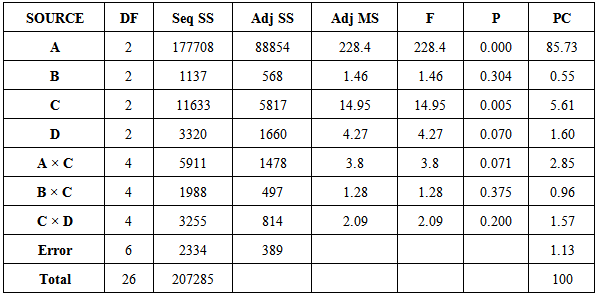 |
| |
|
By using Regression Analysis, volumetric wear loss was predicted, which can be further compared with the experimental result for the same set of conditions. The regression equation obtained is:- | (7) |
where A, B, C and D indicate volume fraction, solutionizing time, ageing temperature and ageing time respectively. By substituting the predicted optimum heat treatment factor levels in the regression equation the estimated optimum Abrasive Volumetric Wear Loss = 17.05 mm3. Further validation experiments were conducted for the predicted optimum conditions and volumetric wear loss from the validation experiments was obtained as 14.74 mm3. The percentage error was also calculated and found to be 13.54% confirming the success of statistical analysis.
4. Conclusions
The following conclusions were drawn from this study:1) The Taguchi’s method of fractional factorial experimentation is successfully used to analyze the optimal ageing heat treatment parameters for the Al6061 alloy and Al 6061-SiCP Composites.2) The effect of volume fraction of reinforcing particles was significant in determining volumetric wear loss. The ageing temperature also contributed considerably along with the interaction of volume fraction and ageing temperature in affecting wear loss. Other parameters, namely, ageing time and solutionizing time did not play major role in influencing the tribological behavior.3) Signal-to-noise ratio factor effect plots successfully indicated the effect of parameters on properties individually or in combination. The plot was also useful in identifying the optimal conditions for Abrasive Volumetric wear loss.4) The regression model can be used to predict the abrasive volumetric wear loss for any combination of material and heat treatment process parameters within the levels selected for analysis. Predicted values using developed mathematical model for volumetric wear loss were in close agreement with the results obtained in validation experiments.
ACKNOWLEDGEMENTS
The authors are grateful to Dr. Jagannath Nayak, Professor in Department of Metallurgical and Materials Engineering, National Institute of Technology Karnataka, Surathkal, for useful interactions and the Management of St. Joseph Engineering College, Vamanjoor, Mangaluru for providing the laboratory equipment for Abrasive Wear testing and their constant support and encouragement during the research work.
References
[1] | E. Paul DeGarmo, J.T. Black, Ronald A. Kohser, “Materials and Processes in Manufacturing”, Eighth Edition, 1997, Prentice Hall, Inc, USA, pp. 218 - 220. |
[2] | Mel Schwartz, “Composite Matrials Handbook”, Second Edition,1992, McGraw-Hill, Inc, USA, pp. 2.92 and pp. 4.71 – 4.72. |
[3] | Manoj Singla, D. Deepak Dwivedi, Lakhvir Singh, Vikas Chawla, “Development of Aluminium Based Silicon Carbide Particulate Metal Matrix Composite” (India), Journal of Minerals & Materials Characterization & Engineering, Vol. 8, No.6, 2009, pp. 455-467. |
[4] | I. Novikov, “Theory of Heat Treatment of Metals”, Second Edition, Mir Publishers, Russia, 1978, pp. 9-30. |
[5] | Z.M. El-Baradie, O.A. El-Shahat, A.N. Abd El-Azim, “Accelerated ageing processes in SiC-7020 aluminium composite”, Journal of Materials Processing Technology, Vol. 79, 1998, pp. 1–8. |
[6] | M. Muratoglu, O. Yilmaz, M. Aksoy, “Investigation on diffusion bonding characteristics of aluminum metal matrix composites (Al/SiCp) with pure aluminum for different heat treatments”, Journal of Materials Processing Technology, Volume 178, Issues 1-3, 14 September 2006, pp. 211-217. |
[7] | M. Gupta, M.K. Surappa, “Effect of increase in heterogeneous nucleation sites on the ageing behavior of 6061/SiC metal matrix composites”, Materials Research Bulletin, Volume 30, Issue 8, August 1995, pp. 1023-1030. |
[8] | G. B. Veeresh Kumar, C. S. P. Rao, N. Selvaraj, M. S. Bhagyashekar, “Studies on Al6061-SiC and Al7075-Al2O3 Metal Matrix Composites”, Journal of Minerals & Materials Characterization & Engineering, Vol. 9, No.1, 2010, pp. 43-55. |
[9] | Philip J. Ross, “Taguchi Techniques for Quality Engineering”, Second Edition, 1996, McGraw-Hill, New York, USA. |
[10] | Raviraj Shetty, Raghuvir B. Pai, Shrikanth S. Rao, Rajesh Nayak, “Taguchi’s Technique in Machining of Metal Matrix Composites”, Journal of the Brazilian Society of Mechanical Sciences and Engineering, January-March 2009, Vol. XXXI, No.1, pp. 12-20. |