Sunith Babu L. 1, H. K. Shivanand 2
1Department of Mechanical Engineering, MSRIT, Bangalore, India
2Department of Mechanical Engineering, UVCE, Bangalore, India
Correspondence to: Sunith Babu L. , Department of Mechanical Engineering, MSRIT, Bangalore, India.
Email: |  |
Copyright © 2015 Scientific & Academic Publishing. All Rights Reserved.
Abstract
Sandwich composites possess higher directional properties and are made of relative lower density core which makes them ideally suited for light weight applications. In the pursuit of better material selection for aerospace application, effects of damage modes resulting from Low Velocity Impact on aircraft structures are little explored since the damages arising from tool drop, debris effect during runway and bird hit may result in BVID – barely visible impact damage. The main aim of this paper is to detect and record the impact damages in structures made from GFRP and CFRP sandwich panels made from Polyurathene foam core. A SEM – scanning electron microscope was used to assess the type and level of damage on the panels with impact energies – 9.81J, 29.43J and 49.05J in turn inspect the topography at higher magnification. The resulting out come from SEM analysis were matrix cracking, fiber fracture and delamination / dent on the sandwich panels. The core material chosen for the analysis was PU foam type with densities 70kg/m3, 100kg/m3 & 200kg/m3 with a constant thickness of 14mm. It was found that sandwich panels made from CFRP facings displayed higher impact energies followed by severe matrix cracking and fiber pullout as compared to GFRP sandwich panels.
Keywords:
Low Velocity Impact, SEM, GFRP, CFRP, Sandwich Composites
Cite this paper: Sunith Babu L. , H. K. Shivanand , SEM Based Studies on Damage Analysis of GFRP and CFRP Sandwich Composites, American Journal of Materials Science, Vol. 5 No. 3C, 2015, pp. 146-150. doi: 10.5923/c.materials.201502.29.
1. Introduction
In the recent past, pursuit of newer materials have been on the rise especially in the aerospace industry, wherein conventional materials are being replaced by sandwich composites since these provide better properties than a combination of conventional materials. Sandwich composites are designed to provide better and higher strength to weight ratio, better stiffness and increased damping factor and corrosion resistant. Since the early 1940’s composites have been extensively used by aerospace engineers [1-3]. However, one striking issue that aerospace industry still faces is the effect of impact damage due to bird hit, dropping of tools during service operation [4]. This kind of impact at times may be difficult to determine by visual examination and in turn, the cracks developed due to impact may propagate to the structural level and may lead to catastrophic failures. A number of studies have been carried out by researchers related to low velocity impact [5-8]. When a damage is formed and cannot be seen by naked eye its termed as BVID – barely visible impact damage [9]. This type of damage needs special attention, if these are left unnoticed can lead to significant reduction in strength and subsequent failure of the sandwich panel can take place. These problems can be resolved only by NDE techniques which can provide layer by layer analysis on the impacted specimen. Further the region of impact can also be determined which can provide a detailed analysis of the impacted region and also cross sectional area that had undergone damage due to impact. It is worth noting that C – Scan technique is ideally not suited for the sandwich panels as the emission of electrons or back wall echo cannot be obtained when the core is made of PU foam. Alternatively SEM was used to determine the fiber fracture, matrix cracking, and fiber pullout and in turn develop a knowledge base for future reference.
2. Specimen Preparation
The sandwich specimen used for this investigation was made from GFRP and CFRP facings with PU foam core of densities – 70kg/m3, 100kg/m3 & 200kg/m3. The resin used for the sandwich construction is Epoxy Resin with a combination of 10:1 ratio – LY556 resin and HY951 hardener. The sandwich composite were fabricated with a 1mx1.5m panel as shown in figure 1 and in turn were post cured for about 2 hours at 60°C and later cut with a dimension of 150mmX150mm using a diamond saw for both GFRP and CFRP sandwich composites. The top and bottom facings were maintained at 1mm. The cut sandwich panel were later checked for dimensional accuracy before being tested. The core material was kept constant at 14mm.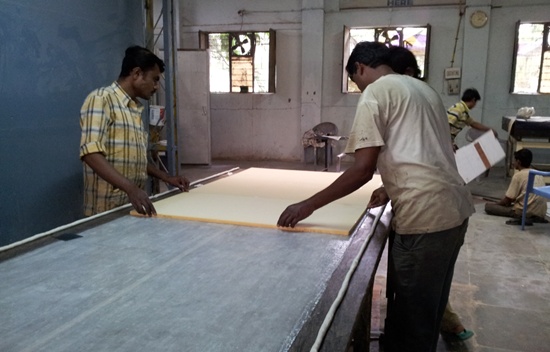 | Figure 1. Sandwich panel fabrication |
3. LVI Testing
A low velocity impact testing (LVI) machine (falling weight drop test) was chosen for impact analysis. The velocity of impact chosen for the test ranges from 1.401, 2.426, 3.132 m/sec for all densities selected. Different mass of impactor of 2.5, 5 and 10kg is selected with hemispherical indentor. The impact energies with a range from 2.45J to 49.05J was selected for the test. The specimen was clamped with all degrees of freedom fixed and an impact region of 100mmX100mm was exposed for the impact test. The impactor was raised for different height and in turn was dropped to determine the impact energy absorption capacity. A free fall (frictionless) along the guide rails was ensured and the results were recorded using DAC – digital acquisition card, which can capture all signals from the piezoelectric setup mounted on the test setup. Details such as energy absorption, depth of penetration (displacement), max load during impact are recorded. 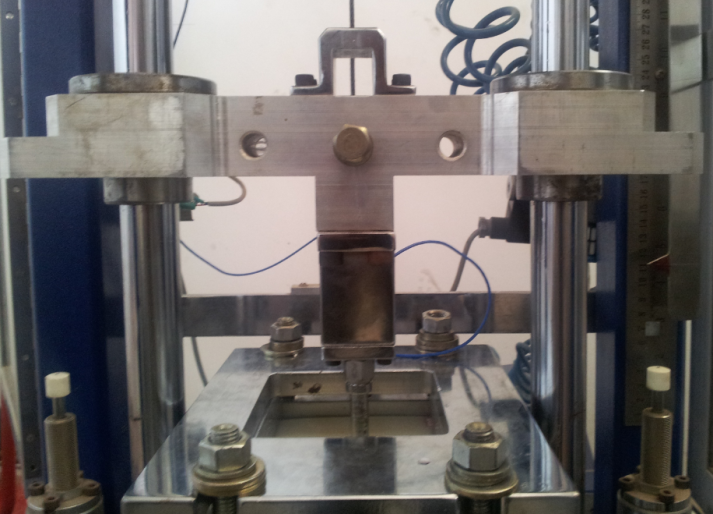 | Figure 2. Low Velocity Impact testing machine setup |
4. SEM Analysis
Several NDE evaluation techniques are available to test the post impact damage of laminates and sandwich structures. However some methods are not suited for particular application like magnetic particle inspection methods cannot be used in composites since these are polymer based materials, unless they are of MMC’s such methods may be adopted. In the present study, the use of C – Scan technique cannot be applied although they provide better results in laminates. This is mainly due to the fact that, core materials do not reflect back the electrons after striking the damaged region. Hence these are not recommended for the damage detection in case of sandwich composites subjected to low velocity impact. When the damage is very insignificant, the use of C – Scan or any type of NDE technique cannot be adopted as the region of damage cannot be accurately detected. Hence better methods are need to determine the level of damage or depth of indentation followed by type failure on the facings and core materials. The use of SEM plays an important role as this type of analysis provides better and accurate results about the failure mode type and detailed analysis and conclusion can be obtained for the type of impact. Here the electron beam is rather of higher intensity and in turn is sent back to provide better images of the damaged specimen. For this research work a Hitachi S-4700 Type II cold field emission SEM is used which is capable of producing resolution up to 1.5nm is used. The specimen images were captured at different magnifications which ranged from 10x to 500x. It is worth noting that with magnifications ranging from 10x – 100x the different cracks developed on the surface can be recorded, which includes matrix debonding, matrix cracking. However when the magnification is increased to 100x – 500x the different failure mechanism can be detected which includes fiber fracture, fiber pullout and severe failure modes can be viewed without any issues. The images once captured are verified with the height of fall, impact energy and correlations are made to develop a knowledge base. Further the damage area is visually examined and recorded.
5. Results and Discussion
With different combination, totally 18 specimens were tested using SEM. The impact energies tested were in the range of 2.45J to 49.05J and were reviewed for different densities and height of fall. In case of damage analysis, on the surface, visual inspection was adopted. The damage area was circular in nature for all specimens impacted and are listed in table 1. Although X – Ray techniques are available, they may not provide the best results in detecting the damage area [10]. Further it is clear that most of the damage in sandwich structure are categorized into matrix cracking, matrix debonding, fiber pullout and fiber fracture. Ideally these cannot be seen by naked eye hence the use of SEM plays a major role.Table 1. Impact Damage Analysis of Sandwich Panel 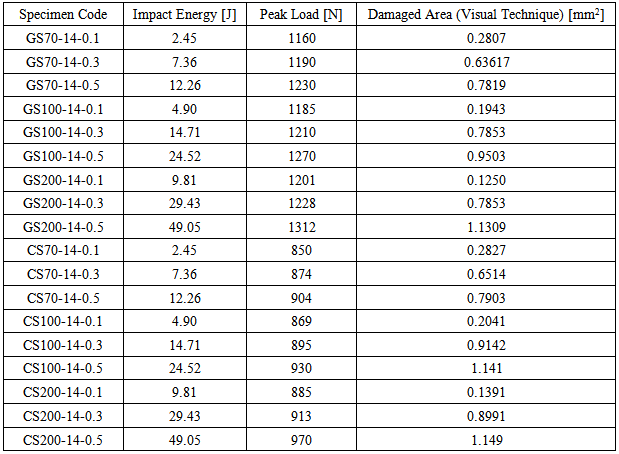 |
| |
|
It was found that sandwich panels showed local failure at the impacted area. It is evident that matrix cracking originates due to impact and this leads to damage resulting in matrix cracking [11]. As the impact energy is increased, the type of damage is different for different combination. The SEM images for GFRP and CFRP are shown in figure 3 and figure 4 respectively. It is clear from the SEM analysis that Matrix Cracking was found in all the specimen since the facings are the first component to have undergone the impact. However, the fiber pull out and fiber breakage were noticed only in 0.3m and 0.5m height of fall for both glass and carbon facing sandwich specimen. The peak load for glass was higher as compared to carbon. This was due to the fact that carbon displayed less resistant to impact damage and resulted in decreased peak load before failure. However, the peak load increased with increase in core density and thickness. There was a reduction of 26% in peak load for carbon as compared to glass. The damage area increased in carbon/epoxy sandwich panels as compared to glass/epoxy as carbon displayed lower resistance to impact loads.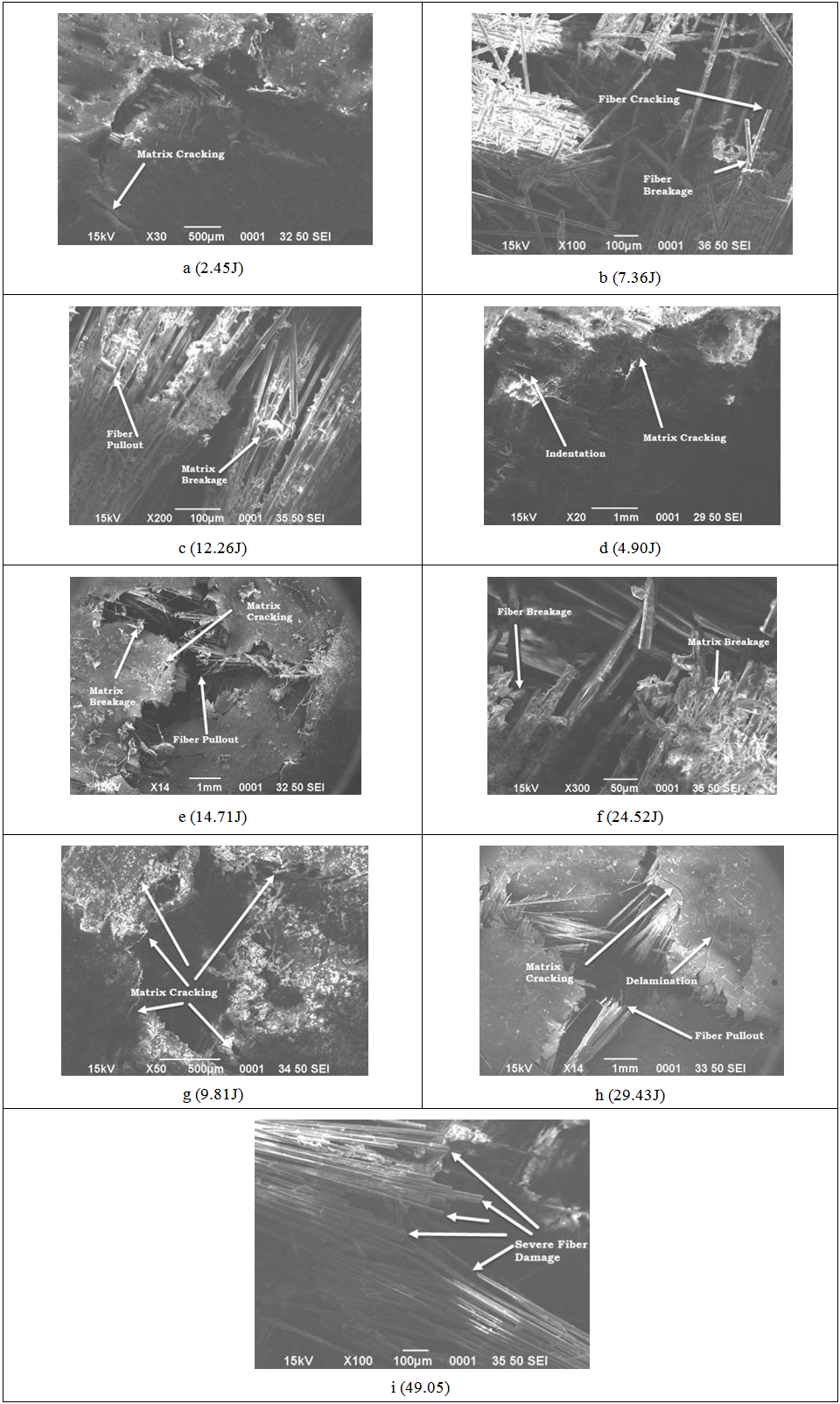 | Figure 3. SEM analysis of GFRP sandwich panels for different impact Energies |
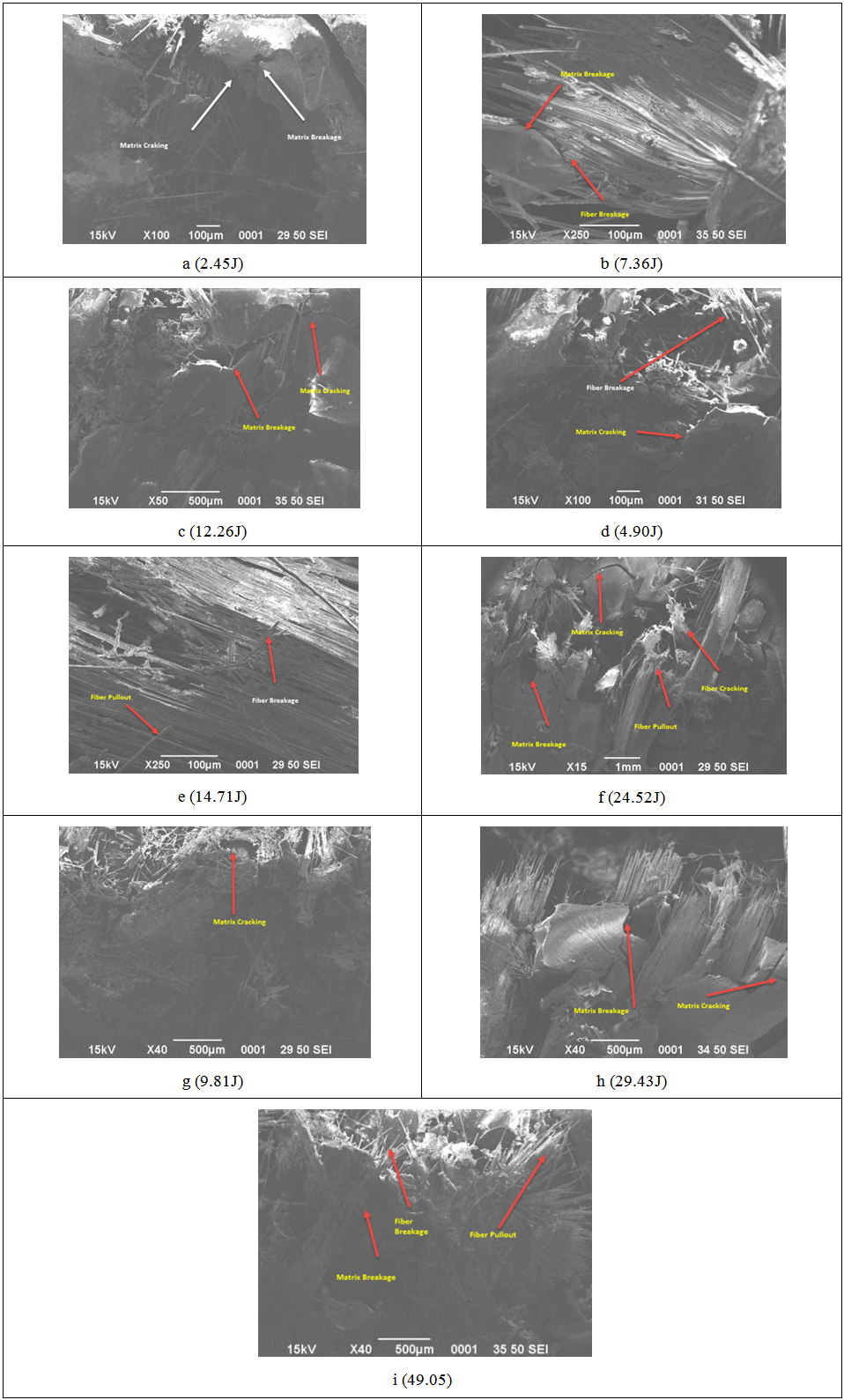 | Figure 4. SEM analysis of CFRP sandwich panels for different impact Energies |
6. Conclusions
The outcome of the study was to develop a knowledge base for impact damage assessment. All the specimen were reviewed under SEM to analyze the effect of damage based on matrix cracking, matrix breakage, fiber pullout and fiber fracture. It was viable that as the impact energies increased from 24.52J there was significant increase in fiber failure even with increase in density, in both Glass / Carbon based sandwich panels. These data’s obtained from SEM will prove to be viable information for future research related to impact damage. Further, the results obtained from SEM proved to be in close agreement with the results related to peak loads and impact energies absorbed. The extent of damage assessment also provided through damage area was convincing since with increase in height of fall the effect of damage area also increase. However, the extent of damage was higher in carbon/epoxy panels as compared to glass/epoxy panels.
ACKNOWLEDGEMENTS
The authors would like to thank the Management, Principal, and Head of Department of their respective college in providing support to carry out the research work.
References
[1] | Williams, J.C. and Starke, E.A. Progress in structural materials for aerospace systems. Acta Materialia, 2003, 51(19), 5775-5799. |
[2] | Bannister, M. Challenges for composites into the next millennium - a reinforcement perspective. Composites Part A: Applied Science and Manufacturing, 2001, 32(7), 901-910. |
[3] | Lubin, George (Ed.), Handbook of Composites, New York: Van Nostrand Reinhold Company Inc., 1982. |
[4] | Whittingham B, Marshall IH, Mitrevski T and Jones R. The response of composite structures with pre-stress subject to low velocity impact damage. Composite Structures 2004; 66(1-4):685-698. |
[5] | Abrate S., Impact on composite structures. Cambridge University Press, 1998. |
[6] | Davies G.A.O., Hitchings D., Besant T., Clarke A., Morgan C.: Compression after impact of composite sandwich panels, Composite structures 63 (2004) pp. 1-9. |
[7] | Shih W.K. Jang B.Z.: Instrumented impact testing of composite sandwich panels. Journal of Reinforced Plastics and Composites, 8 (1989) pp. 270-298. |
[8] | Caprino G., Teti R.: Impact and post-impact behaviour of foam core sandwich structures. Composite Structures 29 (1994), pp. 47-55. |
[9] | U. Polimeno, M. Meo, Detecting barely visible impact damage detection on aircraft composites structures, Composite Structures, Volume 91, Issue 4, December 2009, Pages 398-402. |
[10] | M.T.H. Sultan, A. Hodzic, W.J. Staszewski and K. Worden, A SEM-Based Study of Structural Impact Damage, Applied Mechanics and Materials Vols. 24-25 (2010) pp 233-238. |
[11] | Soutis, C. and Curtis, P.T. Prediction of the post-impact compressive strength of CFRP laminated composites. Composites Science and Technology, 1996, 56(6), 677-684. |