Premkumar Naik 1, Vinod Kumar 1, Sunil Kumar S. 1, Srinivasa K. R. 2
1Department of Mechanical Engineering, Mangalore Institute of Technology & Engineering, Moodbidri, India
2Department of Aeronautical Engineering, Mangalore Institute of Technology & Engineering, Moodbidri, India
Correspondence to: Premkumar Naik , Department of Mechanical Engineering, Mangalore Institute of Technology & Engineering, Moodbidri, India.
Email: |  |
Copyright © 2015 Scientific & Academic Publishing. All Rights Reserved.
Abstract
In this paper, Mechanical properties of areca fibers extracted from areca husk are determined. Further these Areca fibers were chemically treated and the effect of this treatment on fiber strength is studied. Areca fiber composite laminates were prepared with randomly distributed fibers in wood powder and Phenol Formaldehyde. Composite laminates were prepared with different proportions of phenol formaldehyde and fibers. Tensile test, moisture absorption test, and flexural (three-point bending) tests on these laminates were carried out. Properties of these areca-reinforced phenol formaldehyde (PF) composite laminates were analyzed and observed that composite plate of 300ml resin shows the maximum tensile strength, composite plate of 400ml PF shows the maximum bending stress and a composite plate of 500ml PF shows better moisture absorption resistance.
Keywords:
Areca fibers, Polymer Matrix Composites (PMCs),Wood powder
Cite this paper: Premkumar Naik , Vinod Kumar , Sunil Kumar S. , Srinivasa K. R. , A Study of Short Areca Fiber and Wood Powder Reinforced Phenol Formaldehyde Composites, American Journal of Materials Science, Vol. 5 No. 3C, 2015, pp. 140-145. doi: 10.5923/c.materials.201502.28.
1. Introduction
Acomposite is a structural material that consists of two or more constituents that are combined at a macroscopic level and are not soluble in each other. Composites have two constituents, a matrix phase and a dispersion phase. One constituent is called the reinforcing phase and the one in which it is embedded is called the matrix. In principle, composites can be constructed of any combination of two or more materials, whether metallic, organic or inorganic. Advanced composites are a blend of two or more components, one of which is made up of stiff long fibers and the other, for polymeric composites, a resinous binder or matrix that holds the fibers in place. High performance fiber reinforced composite materials are comprised of high strength and modulus fibers, embedded in, or bonded to, a matrix, with a distinct interface between them. In a composite, the fiber, as well as the matrix, retain their physical and chemical identities, but still provide a combination of properties that cannot be achieved with either of the constituents alone. In general the fibers play the role of load bearer. The matrix, while keeping the fibers in the desired location and orientation, act as a load transfer agent and protects the fibers from external conditions such as chemicals, heat and moisture [1]. Manmade fibers using glass, carbon, boron etc. are being used as reinforcing materials in the fiber reinforced plastics (FRP), which have been widely accepted as materials for structural and non-structural applications. The main reason or the interest in FRP is due to their specific modulus, high stiffness and strength to weight ratio compared to other conventional materials. However, these materials are prohibitively expensive in their use for other general purpose and applications. Nowadays-natural fibers like banana, cotton, coir, sisal jute have attracted the attention of scientists and technologists for applications in packaging, low-cost housing and other structures. It has been found that these natural fiber composites [1, 2] possess better electrical resistance, good thermal and acoustic insulating properties and high resistance to fracture. The lowcost, less weight, and density make the naturalfibers an attractive alternative. The current majoruses of hard cellulose fibers like flax, jute, banana, sisal, are in textile, packaging, and paper manufacturing. These fibers are considered as hard cellulosic fibers because of their reasonably high tensile modulus and elongation at break [3].
2. Materials and Methods
The raw materials are used in this work are areca fiber, wood powder and phenol formaldehyde. The composite materials have fueled the growth of new applications in markets such as transportation, construction, marine, infrastructure, consumer products, electrical, aircraft and aerospace appliances and business equipments.
2.1. Biofiber
The fibrous material derived from the tree, plant, or shrub sources is defined as biofiber. This contains the fibers usually explained as natural fibers such as wood, bamboo, wheat, jute, kenaf, sisal, flax, hemp, and cotton. Natural fibers can be considered as naturally occurring composites consisting mainly of cellulose fibrils (fibers) embedded in lignin matrix (resin). These cellulose fibrils are aligned along the length of the fiber, irrespective of its origin, i.e. whether it is extracted from bark or stem, leaf or fruit. It appears that such an alignment renders maximum tensile and flexural strengths, in addition to providing rigidity in that direction of the fiber as observed in the case of bamboo. Further, these fibers exhibit high electrical resistance in addition to being thermally and acoustically insulating. It can therefore be expected that when such fibers are incorporated in low-modulus matrix such as polyester, they would yield materials with better properties suitable for various applications. It is interesting to note that natural fibers such as jute, coir, banana, sisal, etc., are abundantly available in developing countries like India [4].At present these fibers are used in a conventional manner for the production of yams, ropes, mats and mattings, as well as in making fancy articles like wall hangings, table mats, handbags and purses. Fibers such as cotton, banana and pineapple are also used in making cloth in addition to being used in the paper industry, in recent times many of the conventional applications of these natural fibers are threatened by synthetic products [4, 5] (plastics and synthetics such as glass and nylon fibers). This poses the problem that limiting the utilization of natural fibers in the fiber industry, which is basically a rural/cottage industry, leads to displacement of labour. Hence, there is an urgent need for finding diversified uses of these fibers [6].
2.2. Areca Fiber Extraction
Dried areca husk was soaked in water for about 8-10 days. The soaking process loosens the fibers and fibers can be extracted easily. The Areca fibers were separated from the partial dried Areca husk using slow speed hammer mill. Completely dried and thrashed husks were forced through the cyclone separators repeatedly till the neat fibers were separated [7].Fig. 1 shows the variation of fiber size of areca fiber. The sizes of about 100 fibers were measured and distribution curve is plotted. The fibers diameter varies from 0.21 to 0.56 mm for randomly selected 100 fibers. From this distribution curve the mean diameter of the areca fibers is found to be 0.385mm. The calculated average diameter of the areca fibers is 0.39305 mm. From this it can be conclude that the mean diameter and the calculated average diameter are the same and are equal to 0.39mm. Therefore the average diameter of the areca fibers varies from 0.39 ± 0.12mm.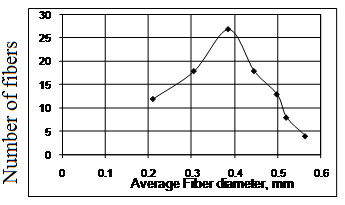 | Figure 1. Variation of fiber diameter of areca fiber |
2.3. Wood Powder
Wood powder is finely pulverized wood that has a consistency fairly equal to sand or sawdust, but can vary considerably, with particles ranging in size from a fine powder to roughly the size of a grain of rice. Most wood powder manufacturers are able to create batches of wood powder that have the same consistency throughout. All high quality wood powder is made from hardwoods because of its durability and strength. Very low grade wood powder is occasionally made from sapless softwoods such as pine or fir. Wood powder is commonly used as filler in thermosetting resins such as bakelite, and in linoleum powder coverings. Wood powder is also the main ingredient in wood/plastic composite building products such as decks and roofs. Large quantities of wood powder are frequently to be found in the waste from woodworking and furniture companies. An adaptive reuse to which this material can be directed is composting as shown in Fig. 2.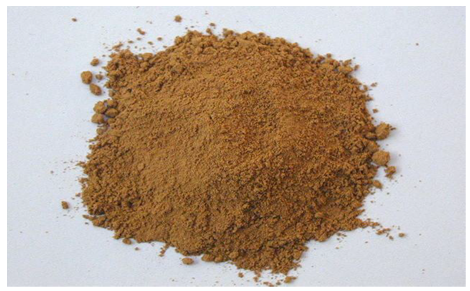 | Figure 2. Wood powder |
2.4. Phenol-Formaldehyde Resin
Phenol-formaldehyde (PF) resins were the first completely synthetic polymers to be commercialized. Phenol-formaldehyde resins include synthetic thermosetting resins such as obtained by the reaction of phenols with formaldehyde. Sometimes the precursors include other aldehydes or other phenol. In the form of Bakelite, they are the earliest commercial synthetic resin. Any of a number of synthetic resins made by reacting phenol (an aromatic alcohol derived from benzene) with formaldehyde (a reactive gas derived from methane). Phenol-formaldehyde resins, as a group, are formed by a step-growth polymerization reaction that can be either acid- or base-catalyzed. Since formaldehyde exists predominantly in solution as a dynamic equilibrium of methylene glycol oligomers, the concentration of the reactive form of formaldehyde depends on temperature and pH.
2.5. Low Density Composite Board Preparation
Known quantities of areca fiber, wood powder and phenol-formaldehyde resin are mixed thoroughly. A mould made of aluminum sheet dimension of 300x300 mm was used to prepare the board. In order to get required dimension of 300x300x10 mm3 of board, two frames of same dimension were placed adjacently on the mould. Thoroughly mixed mixture of areca fibers, wood powder and phenol-formaldehyde resin was taken and placed in the mould uniformly. A layer of aluminum foil was placed both at the top and bottom of the board so that board can be easily taken out from the mould.
2.6. Different Types of Composite Plate
For preparation of 200A composite plate, an Areca fiber of 800 grams and wood powder of 200 grams along with 200 ml Phenol-formaldehyde resin are uniformly mixed and used for preparation of boards. For preparation of 200B Composite plate, 700 grams of Areca fiber and 300 grams of Wood powder along with 200 ml of Phenol-formaldehyde resin are uniformly mixed and used for preparation of boards. Similarly for the 200C and 200D composite plates are prepared as per their proportions. For preparation of 300A Composite plate, an Areca fiber of 800 grams and wood powder of 200 grams along with 300 ml Phenol-formaldehyde resin are uniformly mixed and used for preparation of boards. For preparation of 300B Composite plate, 700 grams of Areca fiber and 300 grams of wood powder along with 300 ml of Phenol-formaldehyde resin are uniformly mixed and used for preparation of boards. Similarly for the 300C and 300D composite plates are prepared as per their proportions. For preparation of 400A Composite plate, an Areca fiber of 800 grams and wood powder of 200 grams along with 400 ml Phenol-formaldehyde resin are uniformly mixed and used for preparation of boards. For preparation of 400B Composite plate, 700 grams of Areca fiber and 300 grams of Wood powder along with 400 ml of Phenol-formaldehyde resin are uniformly mixed and used for preparation of boards. Similarly for the 400C and 400D composite plates are prepared as per their proportions. For preparation of 500A Composite plate, an Areca fiber of 800 grams and Wood powder of 200 grams along with 500 ml Phenol-formaldehyde resin are uniformly mixed and used for preparation of boards. For preparation of 500B Composite plate, 700 grams of Areca fiber and 300 grams of Wood powder along with 500 ml of Phenol-formaldehyde resin are uniformly mixed and used for preparation of boards. Similarly for the 500C and 500D composite plates are prepared as per their proportions.
3. Experimentation
The composite boards were prepared prepared by compressing at an appropriate temperature and pressure in the hydraulic press as shown in Fig.3.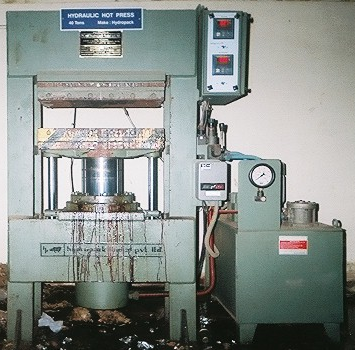 | Figure 3. Hydraulic Hot Press |
The prepared mould is placed in hydraulic press, which is maintained at 140°C, and then a pressure of 2 MPa is applied. The set up is maintained undisturbed about 15-20 minutes. Later, the mould is taken out and allowed to cool for half-an-hour and remove the composite board from the mould.
3.1. Tensile Strength
According to IS 2380 (part 3)-1977, the composite specimens were prepared [10] for tensile testing to determine the Young’s modulus of the material.Each test specimen of 150 mm gauge length, 30 mm wide and thickness 10mm were prepared as shown in Fig. 4.The specimens were subjected to tensile test in the UTM of capacity 50 kN interfaced with the computer and the stress, strain and young's modulus were determined.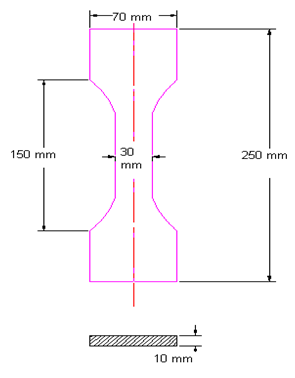 | Figure 4. Dimensions of the specimen for tensile test |
3.2. 3-Point Bending
According to IS: 2380 (part 4)-1977 the composite specimens were prepared [10] for bending test with the dimensions of 50-mm width, length 240 mm, thickness 10 mm and span length of 150 mm as shown in Fig. 5. The specimens are tested at a crosshead speed of 0.5 mm/min. 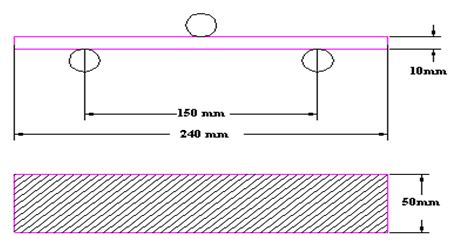 | Figure 5. Dimensions of bending test specimen |
The arrangement for three point bending test with bending fixtures is as shown in Fig.6.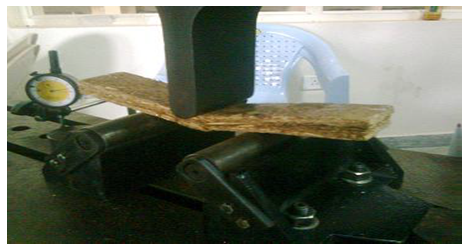 | Figure 6. Arrangement of bending specimens in UTM |
3.3. Moisture Absorption Test
Most Natural fibers absorb excessive moisture compared to synthetic fibers. The effect of this absorbed moisture will degrade the material properties such as tensile strength [8, 9]. The specimens were prepared from a 10mm thickness plate with size 50 mm wide and 75 mm long as shown in Fig. 7. The specimens are immersed in normal water and distilled water separately for a period of 7-15 days. The moisture content in the composite is measured by the weight gain of the material in regular intervals. The percent moisture content is expressed as the ratio of increase in weight to the weight of dry specimen.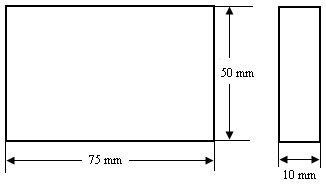 | Figure 7. Dimensions of Specimen used for moisture absorption test |
4. Result and Discussion
The young's modulus, maximum deflection and the moisture absorption of the specimens are determined and are discussed below.
4.1. Tensile Test Results
From the load-deflection curves for various specimens, the composite plate with 300 ml resin (700 grams of Areca fiber and 300 grams of wood powder with 300ml of PF resin) is found to have maximum tensile strength. The maximum tensile strength is for 300B composite plate is as shown in Fig. 8. 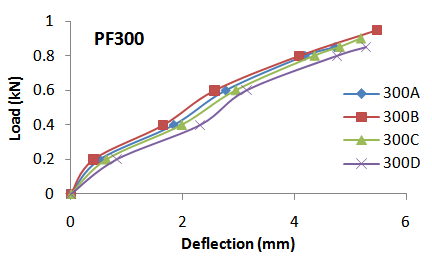 | Figure 8. Tensile test for 300ml PF |
The values of Young’s modulus for different specimens are as shown in table 1 and the maximum value of 91.59 MPa is found for 300B.Table 1. The values of young's modulus for different plates 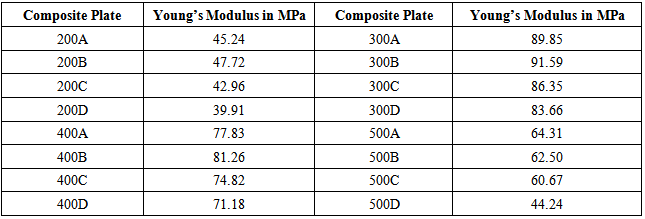 |
| |
|
4.2. Bending Test Results
From the load-deflection curves for bending strength of various specimens, the specimen with 400 ml PF resin (600 grams of Areca fiber and 400 grams of wood powder with 400ml PF resin) withstands maximum bending load with maximum deflection compared to other specimens as shown in Fig. 9. The 400 C specimens are found to withstand maximum load of 0.854 kN.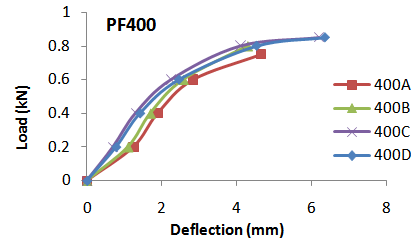 | Figure 9. Bending result for 400PF |
4.3. Moisture Absorption Test Results
Composite specimens were immersed in normal water and distilled water. Initially moisture increased proportionately and attained saturation at later levels of longer period of 10 - 15 days. The moisture specimen immersed in distilled water showed better results than for the specimens immersed in normal water as shown in Fig 10. The composite plate D-500D showed better moisture absorption resistance with increase in weight of 5.6 – 7.3%. The moisture absorption was found to decrease as the resin content was increased. 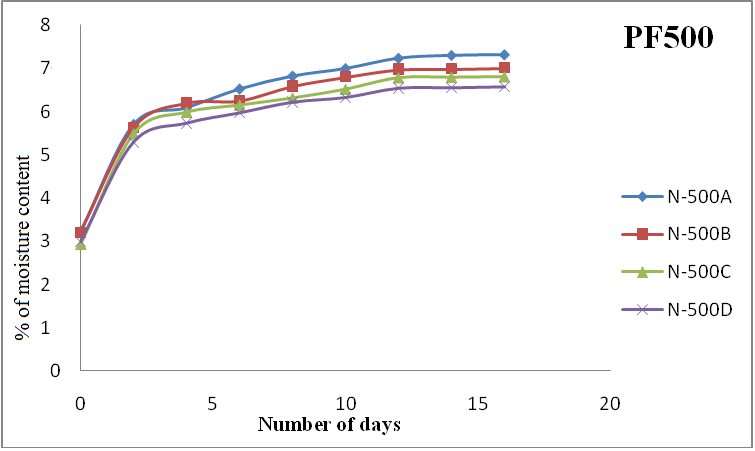 | Figure 10. Moisture content v/s time curves for 500PF composites immersed in distilled water |
The 100 ml of PF is very less to be mixed properly with more quantity of areca fibers and wood powder due to which there will be improper bonding in 100 ml PF composite plates. Therefore the composite plates with 100 ml PF are not used in the present work. Similarly 600ml PF is more to bond areca fiber and wood powder and therefore composite plate with 600ml PF also cannot be used. In 300B composite plate, the young's modulus is maximum. This is because of proper bonding between matrix and reinforcing materials. In case of bending, the composite plate of 400C is found to withstand maximum bending load because the fact being the proper bonding between matrix and reinforcement. It is finally observed that, as the resin (PF) content is increased above 500 ml, the composite plate becomes brittle with reduction in its strength.
5. Conclusions
The strength of the specimen are determined. It is determined that, specimen 300B withstands maximum load of 0.95 kN with a deflection of 5.48 mm. The Young’s modulus for composite plate of 300B is 91.59 MPa. The results for static bending test of composite shows that the maximum load is 0.854 kN with deflection of 8.2 mm for composite plate of 400C. Later the bending strength decreased with the increase in the PF content. The amount of moisture absorbed by composite specimens immersed in distilled water showed excellent results when compared with the specimens immersed in normal water. Also the moisture content decreased with the increase in phenol-formaldehyde content. The composite plate 500 D showed better moisture absorption resistance.
References
[1] | G. C. Mohan Kumar, “A Study of Short Areca Fiber Reinforced PF Composites", WCE 2008, ISBN:978-988-17012-3-7. |
[2] | R.P. Swamy, Y. Vrushabhendrappa, Vince Joseph, 2004, “Study of Areca Reinforced Phenol-formaldehyde Composites” Journal of reinforced Plastics and Composites, vol. 23 no. 13, pp. 1373-1382. |
[3] | K. G. Satyanarayana, K. Sukumaran, R S. Mukherjee, C. Pavithran & S.G.K. PiUai, 1990, “Natural Fiber-Polymer Composites” Cement& Concrete Composites 12, pp.117-136. |
[4] | R.P. Swamy, G.C. Mohan Kumar, Vince Joseph, 2004, “Study of areca reinforced phenol formaldehyde composites”, Journal of Reinforced Plastics And Composites, Vol. 23, No. 13, pp. 1373-1382. |
[5] | J. Giridhar, Kishore, R.M.V.G.K. Rao, 1986, “Moisture absorption characteristics of natural fibrecomposites”, Journal of reinforced plastics and composites, Vol. 5,pp. 141-150. |
[6] | K.N. Bharath, R.P. Swamy, 2009,“Adhesive Tensile and Moisture Absorption Characteristics Of Natural Fibers Reinforced Urea Formaldehyde Composites” International Journal of Recent Trends in Engineering, Vol. 1, pp. 60-62, Academy publisher. |
[7] | Kazuya Okubo*, Toru Fujii, Yuzo Yamamoto, 2004, “Development of bamboo-based polymer composites and their mechanical properties” Composites: Part A 35, pp. 377–383. |
[8] | Prasad S. V, Pavithran C, Rohatgi P. H, 1983, “Mechanical properties of treated and untreated coir fiber with polyster composites”, Journal of Material Science, 18: pp. 1443-1450. |
[9] | Han-Seung Yang, Hyun-Joong Kim, Hee-Jun Park , Bum-Jae Lee, Taek-Sung Hwang, 2006, “Water absorption behavior and mechanical properties of lignocellulosic filler–polyolefin bio-composites” Composite Structures 72,pp. 429–437. |
[10] | Indian Standard, IS:2380 (Part: 1 toxxi) -1977, Methods of teest for wood particle boards and boards from other lignocellulosic materials, Bureau of Indian Standards, New Delhi, India. |