Manjunatha G. , Raji George , Manjunath A.
Dept. of Mechanical Engg. M.S.Ramaiah Institute of Technology, Bangalore, India
Correspondence to: Manjunatha G. , Dept. of Mechanical Engg. M.S.Ramaiah Institute of Technology, Bangalore, India.
Email: |  |
Copyright © 2015 Scientific & Academic Publishing. All Rights Reserved.
Abstract
In this study, graphene filled epoxy nanocomposites were prepared using solution casting method. The graphene at different composition (0.25 0.5, 0.75, 1.0, 1.25 and 1.5 wt. %) were mixed with epoxy before the addition of hardener using mechanical stirring and ultra sonication. The produced nanopolymer composites were post heat treated at different temperature (50o, 100o and 150oC). The mechanical properties of the nanopolymer composites were significantly enhanced by the addition of graphene at different post temperature condition. There is increase in flexural strength and hardness of the composite sample filled with 1.0 wt. % and at heat treated temperature of 100oC as compared to the neat epoxy sample.
Keywords:
Epoxy, Graphene, Nanopolymer composites, Post heat treatment
Cite this paper: Manjunatha G. , Raji George , Manjunath A. , A Study of Post Heat Treatment Temperature Variables on Mechanical Properties of Nanopolymer Composites, American Journal of Materials Science, Vol. 5 No. 3C, 2015, pp. 116-120. doi: 10.5923/c.materials.201502.24.
1. Introduction
Epoxy resin is one of the widely used thermosetting polymers in the production of advanced composites due to its excellent properties, including good dimensional stability, chemical resistance, stiffness and low processing cost. In addition of reinforcing filler the properties of epoxy resin can be improved. The nanomaterial reinforcing fillers into polymeric composite have attracted considerable attention recently [1-3]. The nanomaterials in the nanocomposites system is playing an important role for the high surface to volume ratio of the nanomaterials which well-interact with the polymer matrix and subsequently improved the mechanical properties, electrical, optical and thermal properties. Review of literature showed that very few information is available regarding post heat treatment of polymer nanocomposites to enhance mechanical properties [4-5]. In this study, the graphene/epoxy composite specimens are prepared by varying the percentage of nano fillers using solution intercalation method. and are subjected to post heat treatment at different temperature conditions. The effect of heat treatment on graphene based epoxy composites are interpreted with respect to mechanical properties and morphological characteristics using SEM.Mahesh et al. [6] fabricated epoxy nanocomposites by reinforcing Graphene - Multiwalled Carbon Nanotube with different weight fraction (0.25%, 0.5%, 0.75%, 1%, 1.25%, 1.5%, 1.75% and 2%) of the reinforcement by solution intercalation method. The fabricated specimens were subjected to hardness and tensile test. The mechanical properties of those composites were investigated and found increase in hardness and young’s modulus with increased weight fraction of the reinforcement compared to the base matrix fabricated using the same process.Noorhafanita Norhakim et al. [7] Synthesized graphene oxide by modified hummer’s method and fabricated graphene oxide (GO) filled epoxy nanocomposites by hot pressed method under varying compositions (0.1, 0.3 and 0.5 wt %) of GO in epoxy using ultrasonication process before the addition of hardener. The produced epoxy nanocomposites were investigated to determine the mechanical (flexural and impact) properties and characterized thermal properties of epoxy nanocomposites. The mechanical properties of the nanocomposites were significantly increased by the addition of GO. About one and half times of increment in the flexural strength of the composite sample filled with 0.3 wt% of graphene oxide as compared to the pure epoxy samples.Smrutisikha Bal. [8] fabricated carbon nanofiber reinforced Epoxy composites by varying % of carbon nanofibers upto 1 wt% at room temperature and cured those specimens at two different conditions, i.e., (room temperature and refrigerated at 4˚C) and characterised those specimens using raman spectroscopy. Mechanical properties were also investigated and found that Flexural modulus and hardness were enhanced in refrigerated samples due to prevention of aggregates of nanoparticles during curing condition.
2. Experimental
2.1. Materials
The polymer matrix consisted of Bisphenol A epoxy resin Lapox (L-12) with an amine based hardener (K-6), manufactured by Atul chemicals Ltd Gujarat and were purchased from Yuje marketing, Malleswaram Bangalore. The acetone was chosen as the solvent and was purchased from Vasa scientific, Bangalore.Graphene brand name “UGRAY” are 6 to10 layered aggregates of sub-micron sheet with a diameter of 5 to10 microns and greyish black colour, high aspect ratio, high purity 95-99 % aand chemical formula “C” were purchased from “United Nanotech Pvt Ltd” Hoskote, Bangalore.
2.2. Composites Preparation
The flow chart shows the steps to prepare polymer nanocomposites with various tests and characterization performed, in figure 1. | Figure 1. Flow chart of polymer nanocomposites preparation |
Graphene wt% (0.25, 0.50, 0.75, 1.0, 1.25, and 1.50) was dispersed in acetone (10 to 20 ml) using magnetic stirrer for 20 min. The epoxy resin was added to the mixture and sonicated for 20 min in an ice bath to avoid unwanted heat generated during process [8-9]. The acetone was evaporated by heating the mixture under infrared lamp, (Before and after heating, the mixture is weighed and weight loss is observed to ensure the evaporation of acetone) then the mixture is allowed to cool at room temperature. The hardener was added to the mixture (10:1) using mechanical stirrer for 10 min in an ice bath to prevent premature curing. The mixture is placed in vacuum chamber and degasification was carried out to remove presence of air bubbles. Finally, the mixture was poured into silicone moulds and cured at room temperature for 24 hrs and nanocomposites are prepared. The samples were subjected to post heat treatment at 50,100 and 150˚C for 1 hr.
3. Results and Discussions
Hardness test and Flexural test were conducted according to ASTM standards for reinforced and unreinforced composites at different post heat treatment temperature conditions. The specimens were characterized using scanning electron microscope (SEM) to study the microstructure and to determine the type of dispersion achieved in the epoxy nano composite.
3.1. Hardness Test
Hardness test was performed using Rockwell Hardness tester according to ASTM D785 standard. Hardness test were performed for 5 specimens by varying the wt% of nano particles (0.25, 0.50, 0.75, 1.0, 1.25, 1 50) and were post heat treated at different temperature conditions. [10]The results are tabulated in table 1, the hardness value increased gradually with increase in graphene content up to 1.0 %, and then it is decreased gradually with further increase in graphene content. It was found that all specimens post heat treated at 100˚C showed higher hardness compared with unheat treated and heat treated at 50˚C and 150˚C.Table 1. Rockwell hardness number for Gr/Epoxy composites |
| Sl no | Materials | Load in Kg | HRB | WHT | 50˚C | 100˚C | 150˚C | 01 | Pure Epoxy | 60 | 50 | 53 | 67 | 63 | 02 | 0.25% Gr | 60 | 50 | 54 | 81 | 79 | 03 | 0.50% Gr | 60 | 51 | 56 | 84 | 81 | 04 | 0.75% Gr | 60 | 53 | 55 | 87 | 81 | 05 | 1.00% Gr | 60 | 61 | 63 | 101 | 94 | 06 | 1.25% Gr | 60 | 57 | 61 | 91 | 86 | 07 | 1.50% Gr | 60 | 52 | 59 | 87 | 79 |
|
|
3.2. Flexural Test
Flexural test was performed using computer controlled Universal Testing Machine (UTM) according to ASTM D790 standards [11]. Flexural test were performed for 5 specimens by varying the wt% of nano particles (0.25, 0.50, 0.75, 1.0, 1.25, 1.50) and were post heat treated at different temperature conditions. The results are tabulated in table 2, the flexural strength increased gradually with increase in graphene content up to 1.0 %, and then it is decreased gradually with further increase in graphene content. It was found that all specimens post heat treated at 100˚C showed higher flexural strength compared with unheat treated and heat treated at 50˚C and 150˚C.Table 2. Flexural strength for Gr/Epoxy composites |
| Specimen | Flexural strength(MPa) | WHT | 50˚C | 100˚C | 150˚C | Pure epoxy | 133.7 | 147.47 | 169.20 | 159.11 | 0.25 % Gr | 137.8 | 151.60 | 175.84 | 161.20 | 0.50 % Gr | 142.1 | 162.56 | 181.30 | 164.02 | 0.75 % Gr | 150.2 | 167.02 | 189.01 | 169.03 | 1.00 % Gr | 152.3 | 176.03 | 193.90 | 181.02 | 1.25 % Gr | 147.8 | 170.35 | 186.00 | 174.06 | 1.50 % Gr | 128.1 | 156.42 | 171.01 | 162.36 |
|
|
3.3. Characterization of Gr/Epoxy Composites
Graphene epoxy composites were examined by Scanning Electron Microscope (SEM) in order to observe the distribution of graphene in the epoxy matrix. The Samples with graphene wt % (0.5, 1.0 and 1.5) post heat treated at 100˚C were examined. The SEM for 0.5 % Graphene/Epoxy composites at 100˚C post heat treatment temperature condition taken at 5000X and 50,000X magnification level is shown in fig 2.1(a) and 2.1(b).In fig 2.1(a) & 2.1(b), the particles of graphene are poorly distributed, and no formation of chain link was observed due to agglomerates. In fig 2.2(a) & 2.2(b), the particles of graphene had better distribution comparatively and formation of chain link was observed with very less agglomerates. Due to better dispersion and interfacial bonding between epoxy and nano material which lead to enhanced mechanical properties.In fig 2.3(a) & 2.3(b), the particles of graphene formed cluster due to poor distribution and agglomerates were observed throughout, due to increase in wt% of graphene and lead to failure in most epoxy composites.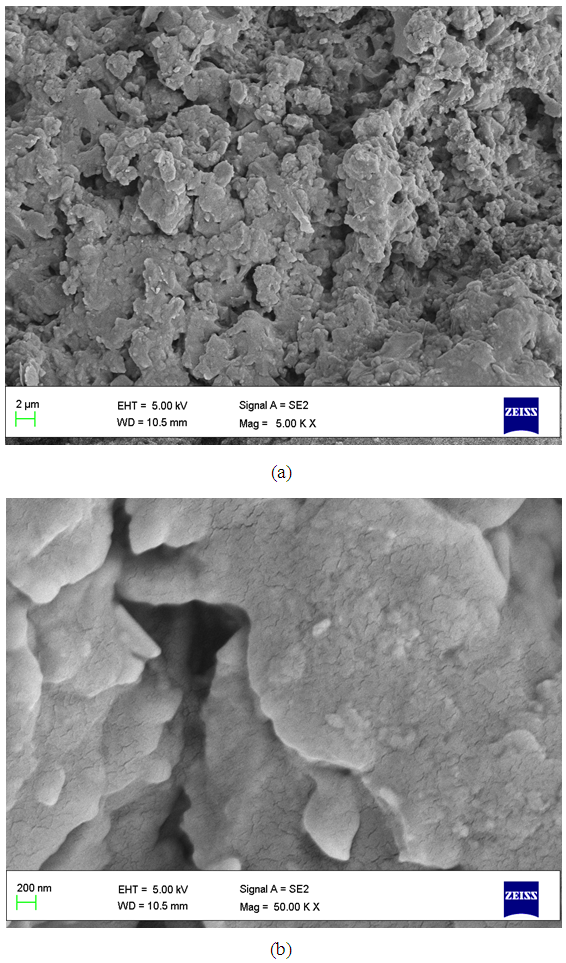 | Figure 2.1. (a) and (b): SEM microstructure of 0.5% Gr at 5,000X and 50,000 X magnification level |
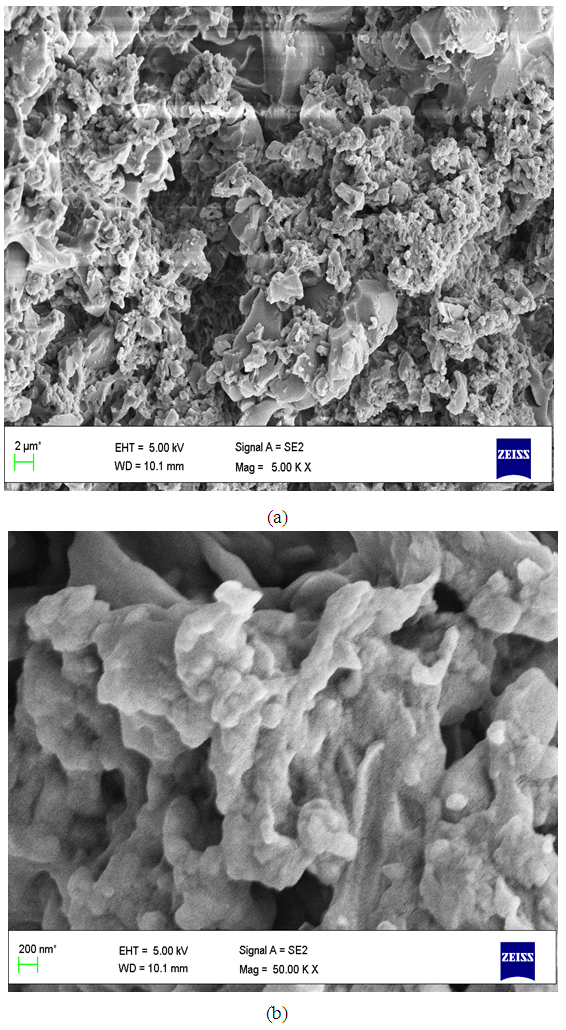 | Figure 2.2. (a) and (b): SEM microstructure of 1.0 % Gr at 5,000X and 50,000 X magnification level |
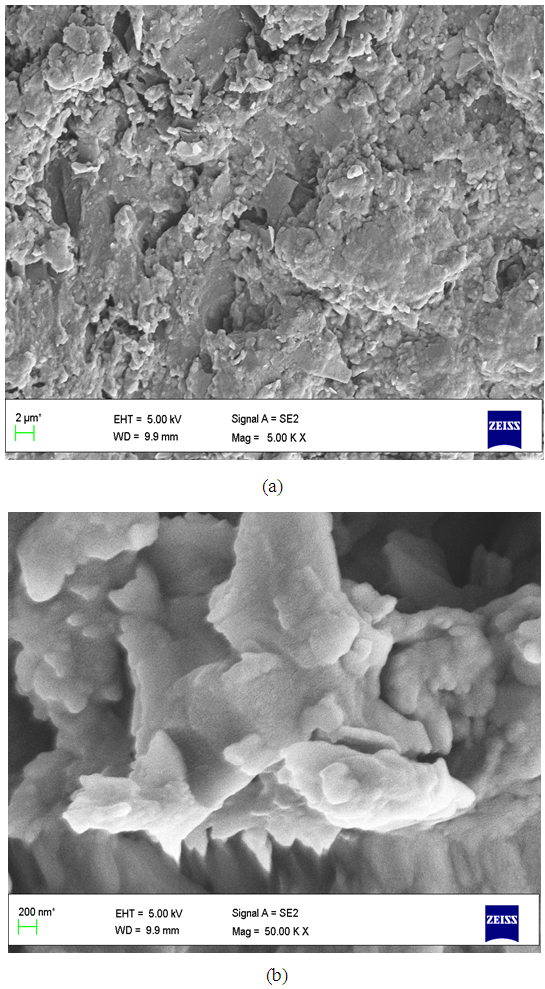 | Figure 2.3. (a) and (b): SEM microstructure of 1.5 % Gr at 5,000X and 50,000 X magnification level |
4. Conclusions
1. The polymer nano composites were developed using solution casting method at room temperature.2. Post heat treatment temperature variables have much effect on mechanical properties of polymer nano composites.3. The additions of 1wt% of graphene resulted in the improvement of hardness and flexural strength as compared to the pure epoxy and other wt % of graphene samples.4. The post heat treated specimen at 100˚C showed higher flexural strength and hardness compared to unheat treated and heat treated specimens at 50˚C and 150˚ C at all levels of graphene loadings.5. At 1.0 wt% graphene content, graphene had better dispersion with very less agglomerates observed in SEM compared to 0.5 and 1.5 wt%.
ACKNOWLEDGEMENTS
The authors would like to thank Principal, Management and non teaching staff, Dept of Mechanical Engg MSRIT Bangalore, Karnataka for their encouragement, support and facilities provided during the completion of the work.
References
[1] | Mohammad A. Rafiee, Javad Rafiee, Zhou, Zhong-Zhen Yu and Nikhil Koratkar “Enhanced mechanical properties of nanocomposites at low graphene content” ACS NANO Vol.3, No. 12 3884 December 3, 2009, 3884-3890. |
[2] | I.A. Ovid KO “Enhanced mechanical properties of poly mer-matrix nanocomposites reinforced by graphene in clusions a review” Rev. Adv Mater. Sci.34 (2013), 19-25. |
[3] | P.S. Shivakumar Gouda, Raghavendra Kulkarni, S.N. Kurbet, Dayananda Jawal” Effects of multi walled carbon nano tubes and graphene on mechanical properties of hybrid polymer composites “Adv. Mat. Lett. 2013, 4(4), 261-270. |
[4] | Rahim Eqra, Kamal Jangorbhan, Habib Daneshmanesh” Mechanical properties and toughening mechanisms of ep oxy/graphene nanocomposites” Journal of Polymer Engi-neering, October 2014(Online) 2191-0340, ISSN (Print) 0334-6447,DOI:10.1515/polyeng-2014-0134. |
[5] | Horacio J. Salavagione, Gerardo Martínez and Gary Ellis “Graphene-based polymer nanocomposites” Intechopen. 2013. P 169-192. |
[6] | Mahesh. V.M, B.K. Muralidhara, Raji George “Influence of different nanomaterial on the mechanical properties of epoxy matrix composites – a comparative study “IJIRSET Vol. 3, Issue 7, July 2014, 14420-14427. |
[7] | Noorhafanita Norhakim, Sahrim Hj, Ahmad, Chin Hua Chia & Nay Ming Huang “Mechanical and thermal properties of graphene oxide filled epoxy nanocomposites” Sains Malay siana 43(4)(2014): 603–609. |
[8] | Hyunwoo Kim, Ahmed A. Abdala and Christopher W. Ma cosko “Graphene/polymer nanocomposites” Macromolecules 2010, 43, 6515-6530. |
[9] | Smrutisikha Bal “Experimental study of mechanical and electrical properties of carbon nanofiber/ epoxy composites” Journal of Materials And Design. Mat Des 2009.11.058, P.1-26. |
[10] | Shivan Ismael Abdullah, M.N.M. Ansari “Mechanical prop-erties of graphene oxide (go)/epoxy composites” HBRC Journal (2014) Received 20 February 2013. |
[11] | Dilini Galpaya, Mingchao Wang, Cheng Yan, Meinan Liu, Nunzio Motta, Eric Waclawik “Fabrication and characterisation of graphene oxide-epoxy nanocomposite” Fourth International Conference on Smart Materials and Nanotechnology in Engineering, Proceedings of SPIE 8793, Vol.1, P.4-7. |