Keerthi A. , Imaad Shaik , Mark Ryan Mendonca , Keerthan K. S. , Pavana Kumara B.
Department of Mechanical Engineering, St Joseph Engineering College, Mangalore, India
Correspondence to: Keerthi A. , Department of Mechanical Engineering, St Joseph Engineering College, Mangalore, India.
Email: |  |
Copyright © 2015 Scientific & Academic Publishing. All Rights Reserved.
Abstract
Arecanut fiber and arecanut with Casuarina fibers are reinforced with epoxy matrix and composites have been developed by manual hand lay-up technique. The effect of arecanut and Casuarina fiber on physical, mechanical and abrasive wear properties of epoxy composites was studied. The mechanical property characterization includes tensile and flexural properties as per ASTM standards. Experimental results indicate that by addition of arecanut fiber to neat epoxy its tensile and flexural strength improves. However, incorporation of Casuarina to arecanut as secondary filler results in improvement of both mechanical and tribological properties of composites. The abrasive wear test was conducted on pin-on-disc arrangement with abrasive paper as counter face. It was also found that tribological properties of filled epoxy composites were closely related with sliding conditions such as sliding distance and applied load.
Keywords:
Arecanut fiber, Casuarina fiber, Epoxy
Cite this paper: Keerthi A. , Imaad Shaik , Mark Ryan Mendonca , Keerthan K. S. , Pavana Kumara B. , Processing and Characterization of Epoxy Composite with Arecanut and Casuarina Fibers, American Journal of Materials Science, Vol. 5 No. 3C, 2015, pp. 96-100. doi: 10.5923/c.materials.201502.20.
1. Introduction
Over the past two decades, there has been a shift in research and industrial practice, and products traditionally manufactured from wood are increasingly combined with other non woody materials of either natural or synthetic origin. Wood and other plant-based fiber are combined with adhesives, polymers, and other “Ingredients” to produce composite materials [1].Pandey and Sujatha [2] have shown that the new environmentally friendly technology for turning agricultural residues like bamboo, rice husk, jute, coconut coirs, bagasse, wheat straw, chir pine needles, cotton stalks, casuarina leaves, banana stem etc., into quality value-added composite products. It is found that the new technology highly favors environmental protection and sustainable development by recovering and re-utilizing organic wastes such as crop residue.Reddy et al. [3] have reported the mechanical performance of Epoxy composites filled with betel nut short fiber at different compositions using the extrusion and hot press molding technique. Sansevieriacylindrica was hybridized with betel nut short fiber in Epoxy system to provide better mechanical performance. The results indicates that the prepared composite with 10% content of Betel nut exhibits better mechanical properties. Remarkable dielectric strength was observed with 30% Betel nut. The results also indicate that it is possible to increase the mechanical performance of hybrid fiber reinforced composites through hybridization of betel nut fiber and Sansevieriacylindrica with Epoxy matrix at optimized ratio (Bn10:Sc10:EP80) of the fiber matrix formulation.Nurulaini et al. [4] studied the effects of tensile and flexural testing on the Casuarinaequisetifolia composite at different loading from 10 % to 50 % loading (wt%). The results for all composite samples on tensile strength and tensile modulus were decreasing as the weight loadings of Casuarinaequisetifolia increased. However, the result from tensile modulus was not significant when the fiber content was increased in the composite. In addition, the result obtained from flexural modulus and strength at 20% of Casuarinaequisetifolia weight loading, increased to 3.147GPa and 3.25 MPa respectively, when its weight loadings increase, the results showed a decrease.Girisha et al. [5] prepared composite by reinforcing arecanut fruit husk fibers and tamarind fruit husk fibers with epoxy matrix by hand lay-up method. These prepared composite were than characterized by mechanical testing. Testing results showed that tensile strength increases with increase in fiber content, however after a certain percentage (40-50%) of fiber content the tensile strength decreased.Samuel et al. [6] studied the mechanical properties of Ukam, Banana, Sisal, Coconut, Hemp and E-glass fiber laminates. Test result showed that E-glass has the maximum tensile strength of 63 MPa and bending strength of 0.5 MPa. The Ukam plant fiber laminate has maximum tensile strength of 16.25 MPa. Sisal laminate has maximum bending strength of 0.0036 MPa.In our present work, we are trying to increase the mechanical, physical and wear properties of neat epoxy by adding arecanut fiber and mixture of arecanut and casuarina fiber. This paper also highlights the effect of addition of fiber on density and water absorption test.
2. Materials Used
2.1. Epoxy Resin and Hardener
The matrix system used was a medium viscosity epoxy resin (Araldite LY556) and Hardener (Aradur HY951), both supplied by Renuka Enterprises, Bangalore.
2.2. Arecanut Fiber
The husk of the Areca is a hard fibrous portion covering the endosperm. It constitutes 30–45% of the total volume of the fruit. Areca husk fibers are predominantly composed of hemicelluloses and not of cellulose. Areca fibers contain 13 to 24.6% of lignin, 35 to 64.8% of hemicelluloses, 4.4% of ash content and remaining 8 to 25% of water content. The fibers adjoining the innerlayer are irregularly lignified group of cells called hard fibers and the portions of the middle layer contain soft fibers. Areca fiber is highly hemi cellulosic and is much greater than that of any other fiber [7].
2.3. Casuarina Fiber
Casuarina equisetifolia, also called Iron wood, is the most popular farm forestry tree in the coastal areas of south India and north India. Casuarina resembles feathery conifer in general appearance. These needles fall on the forest floor and make a thick layer, since their decomposition is slow due to prevalent climatic conditions. Thick layer of un-decomposed needles is a major source of ground fires in the forests recurring annually. Attempts have been made to use these needles to develop usable materials.
3. Steps in Composites Fabrication
3.1. Fiber Extraction
Arecanut:Selected areca fruit husks were used to prepare the composites. Dried areca husk were soaked in de-ionized water for about ten days. The soaking process loosens the fibers, increases the strength and can be extracted out easily. Finally, the fibers were washed again with de-ionized water and dried at room temperature for about a day. The dried fibers are designated as untreated fibers. Casuarina:Casuarina fibers were collected from the beach, cleaned and soaked in water for two days.
3.2. Alkali Treatment
Both, the areca and casuarina fibers were treated in a solution of 15% NaOH (Sodium Hydroxide) to total volume of solution. The fibers were kept in this alkaline solution for 28 hours at room temperature, it was then thoroughly washed in running water then neutralized with a 2% Acetic acid solution. Lastly, it was again washed in running water to remove the last traces of acid sticking to it, so that the pH of the fibers is approximately 7 (neutral). Then, they were dried at room temperature for 24 hours to obtain clean treated fibers for further process.
3.3. Preparation of Mould Box
For the preparation of the composite material, a mould box with specific dimensions was a necessity. The purpose of a mould box is to contain the epoxy (after it is poured over and around a model) until the liquid turns to a solid. The mould box that was prepared had a dimension of 250mm×250 mm and with a depth of 3 mm. The wood that was used for construction was plywood. The entire mould box was covered with a laminate to ensure ease of removal after the finished product was obtained. For the above lid, square plywood with a dimension larger than the mould box was used.
3.4. Preparation of Composite
Fiber configuration and volume fraction are two important factors that affect the property of the composite. In the present study, the following composites were prepared with randomly distributed fibers.● Composite containing 10% of alkali treated areca fiber with epoxy resin.● Composite containing 5% of alkali treated areca fiber and 5% of alkali treated Casuarina fiber with epoxy resin. First, the prepared mould was polished with Wilson wax. Then, a layer of non-adherent sheets was placed on the surface for easy removal of the specimen. The fiber was then mixed thoroughly with the resin and hardener for 5 minutes and poured into the mould. Care was taken to get uniform thickness. It was left to set overnight. Then the prepared composites were removed from the mould box. In this paper the abbreviations used for epoxy, epoxy+arecanut and epoxy+arecanut+casuarina are E, EA, and EAC respectively.
3.5. Preparation of Test Specimen
Specimens are prepared according to ASTM standards as shown in Table 1.Table 1. Test specimen standards 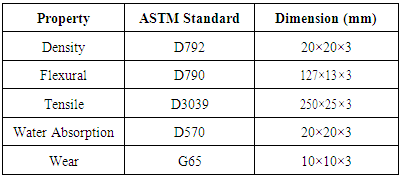 |
| |
|
4. Results and Discussion
4.1. Density Test
The densities of the composites were measured by the displacement method based on Archimedes principle. In this method distilled water was taken in the measuring jar having graduations in millimeters and the initial level of water was noted. Then each of the samples was weighed using an electronic balance of AY220 type (Shimadzu Corporation, Japan with 0.1mg accuracy). The weighed samples were then dropped into the water in the measuring jar. This resulted in the rise in water level. The final level of water was noted and the difference in initial and final reading gives the volume of samples dropped into it. The ratio of weight of sample to its volume as obtained by the above procedure yielded the density of the composites. | (1) |
Density test was carried out based on three different specimen i.e., E, EA and EAC. The results are plotted in the Figure 1.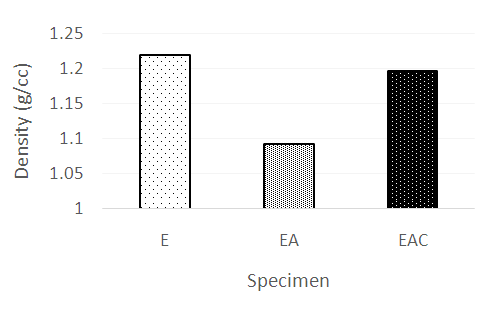 | Figure 1. Densities of different composite specimen |
From the above figure, it is clear that specimen E has a density of 1.22g/cm³. By adding Arecanut fiber to neat epoxy, density is reduced up to 12%, i.e., 1.092g/cm³ and by adding both are canut and casuarina fiber to neat epoxy, density of epoxy is reduced to 1.196g/cm³. This indicates the ability of natural fibers to reduce the density.
4.2. Flexural Test
Test were carried out at room temperature using Instron3366. Test was conducted at a rate of 1mm/min for all the three different specimen i.e., E, EA and EAC, with three trials for each. Results obtained are shown in Figure 2. Table 2 shows Flexural properties at maximum load.From the above figure, it is clear that E has the maximum flexural load (75.119N) than that of EA (46.728N) and EAC (38.061N). Both EA and EAC specimens withstand lower flexural load due to the brittle behaviour of arecanut fiber [7].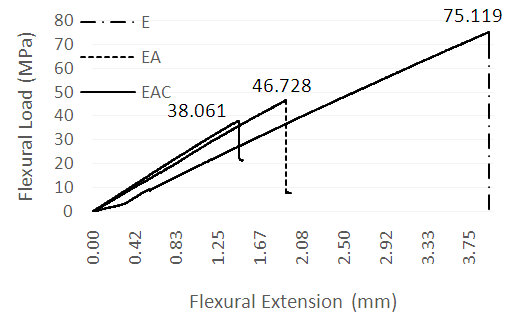 | Figure 2. Flexural test results |
Table 2. Flexural properties at maximum load 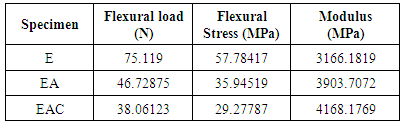 |
| |
|
4.3. Tensile Test
Tensile test was carried out for E, EA and EAC specimen, to determine the stress and strain, and Ultimate breaking stress. The specimen was subjected to continuous load. The load and percentage elongation was noted down at various steps. Figure 3 shows the tensile test result. Table 3 shows tensile properties of the specimen at maximum load.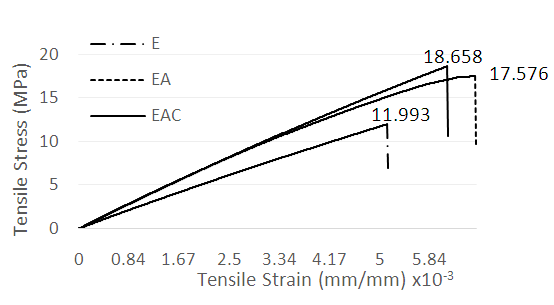 | Figure 3. Tensile test results |
Table 3. Tensile properties at maximum load 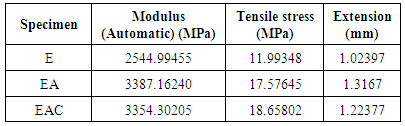 |
| |
|
From Figure 3, it is clear that E composite has a tensile strength of 11.99MPa. By adding arecanut fiber to E, tensile strength can be increased upto 46%, and by adding both arecanut and casuarina fiber to E, tensile strength can be increased upto 56%.
4.4. Water Absorption Test
Mostly natural fibers absorb more moisture compared to synthetic fibers. Water is predominantly absorbed at the fiber interface and matrix. The specimens were immersed in distilled water for 16 days. The moisture content in the composite was measured by the weight gain of the material at regular intervals. The percentage moisture content is expressed as  | (2) |
Were, FW = Final WeightIW = Initial WeightFigure 4. shows a graph of Average % Increase in weight v/s Days.Figure 4 shows that amount of moisture in the composite increases up to 13 days and later it becomes constant. Both EA and EAC absorbs about 5-6% of its weight, were as moisture absorption for commercial wood based particle board is more than 30-40% [7]. Therefore compared to wooden based particle both EA and EAC composite shows better water absorption property.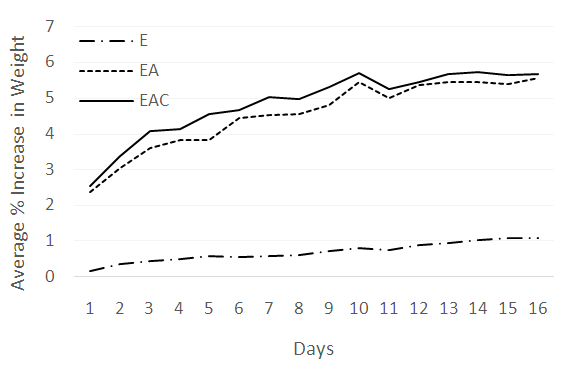 | Figure 4. Average % increase in weight v/s Days |
4.5. Abrasive Wear Test
Wear test were carried out on three different specimen i.e., E,EA and EAC by varying two parameter, i.e., sliding distance and load, with three trials for each.
4.5.1. Effect of Load on Wear Loss
Effect of load on wear loss is illustrated in Figure 5 – Figure 7, the wear loss increases as the load increases in most of the case. It is also observed that for E, wear loss is maximum at highest load. It is worth pointing out that the wear loss of E composite is high due to the poor wear resistance. However wear resistance of neat epoxy was greatly influenced by the addition of fibers. Without the fiber, Epoxy was easily removed resulting in higher wear loss of E. Addition of arecanut and casuarina fibers to E increased wear resistance of the composites, resulting in lower wear loss. During wear loss fiber were worn out of composite and becomes third body abrasive, and protect matrix material.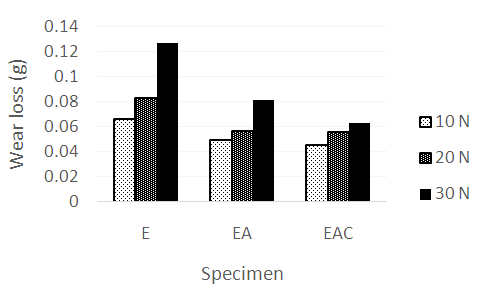 | Figure 5. Variation of Wear loss at different load (80m) |
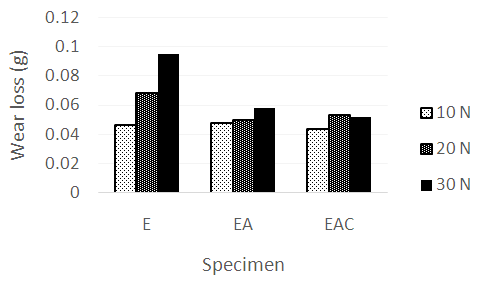 | Figure 6. Variation of Wear loss at different load (60m) |
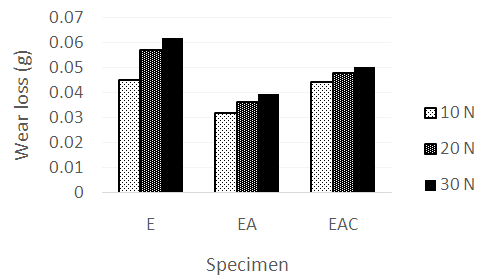 | Figure 7. Variation of Wear loss at different load (40m) |
4.5.2. Effect of Sliding Distance on Wear Loss
Effect of sliding distance on wear loss is shown in the Figure 8 - Figure 10. It can be seen that wear loss increases with the increase in sliding distance for all the samples. As we see from the graph, for a particular distance, the wear loss for neat epoxy is found to be higher than the fiber filled epoxy composite. It can be observed that the wear loss decreases steadily with the increase in the fiber content. This indicates the ability of the fiber to protect the matrix material under different sliding distance. 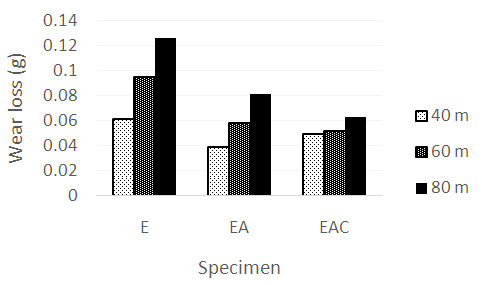 | Figure 8. Variation of Wear loss at different sliding distance (30 N) |
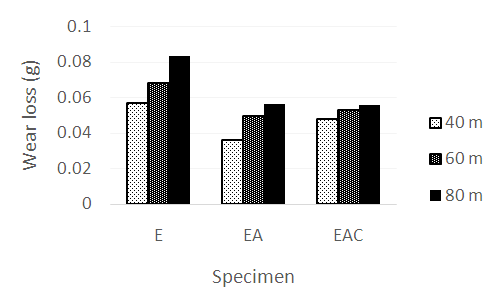 | Figure 9. Variation of Wear loss at different sliding distance (20 N) |
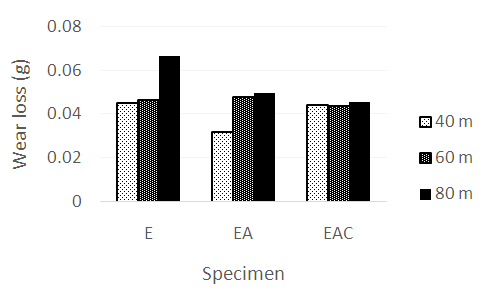 | Figure 10. Variation of Wear loss at different sliding distance (10 N) |
5. Conclusions
The experimental investigation on physical and mechanical property of Arecanut and Arecanut-Casuarina composite leads to the following conclusion:1. Density can be reduced by the addition of Arecanut and Casuarina fibers to neat epoxy.2. Arecanut composite shows good tensile strength of 17 MPa and by adding Casuarina fiber to it, the improved tensile strength is 18 MPa. 3. From flexural test it is clear that the arecanut and Casuarina composite are brittle. For lower loads the flexural strength is higher when compared to that of epoxy.4. By abrasive wear test, it is clear that, wear performance of epoxy composite is improved by the addition of Arecanut and Arecanut + Casuarinafibers.5. Both Areca and Areca-Casuarina fiber show excellent resistance to moisture absorption. It absorbs 5-6% of the total volume of the water, which is very low compared to wood based particle board.
ACKNOWLEDGEMENTS
We take this opportunity to convey our heartfelt gratitude to Director, Principal, Vice Principal and Head of Mechanical Engineering, St. Joseph Engineering College, Mangaluru, for their support to carry out this research work. Authors also gratefully acknowledge the Department of Dental Materials, MCODS, Manipal, Manipal University, for providing the mechanical testing facility.
References
[1] | Douglas D. Stokke, Qinglin Wu, G. Han, Christian V. Stevens, Introduction to Wood and Natural Fiber Composites, Wiley Press, 2013. |
[2] | C. N. Pandey and Sujatha D, “Crop residue. The alternate raw materials of tomorrow for the preparation of composite board”, Indian Plywood Industries Research Institute, Tumkur, Bangalore. |
[3] | G. Ramachandra Reddy , M. Ashok Kumar, K. V. P. Chakradhar, “Fabrication and performance of hybrid Betel nut (Areca catechu) short fiber/ Sansevieriacylindrica (Agavaceae) epoxy composites”, International Journal of Materials and Biomaterials Applications 2011, 1(1): 6-13. |
[4] | B. Nurulaini, A. Z. Romli, M. H. Abidin, “Tensile and Flexural Properties of Casuarina equisetifolia Unsaturated Polyester Composites”, Advanced Materials Research, Vol 812, pp. 231-235, Sep. 2013. |
[5] | Girisha. C, Sanjeevamurthy, G. Rangasrinivas, Manu. S, “Mechanical Performance Of Natural Fiber-Reinforced Epoxy Hybrid Composites”, International Journal of Engineering Research and Applications (IJERA) ISSN: 2248-9622 www.ijera.com Vol. 2, Issue 5, September- October 2012, pp.615-619. |
[6] | O. D. Samuel, S. Agbo, T. A. Adekanye, “Assessing Mechanical Properties of Natural Fibre Reinforced Composites for Engineering Applications”, Journal of Minerals and Materials Characterization and Engineering, 2012, 11, 780-784. |
[7] | G. C. Mohan Kumar, “A study of short Areca fiber reinforced PF Composites”, WCE 2008, July 2-4, 2008, London, U.K. |