Deepak Sequeira , Jeevan Mascarenhas , Darren Picardo , Rayen Dias , Orville Sutari
Department of Mechanical Engineering, St Joseph Engineering College, Mangalore, India
Correspondence to: Deepak Sequeira , Department of Mechanical Engineering, St Joseph Engineering College, Mangalore, India.
Email: |  |
Copyright © 2015 Scientific & Academic Publishing. All Rights Reserved.
Abstract
A majority of aerospace components made of Glass Fiber Reinforced Polymer (GFRP) composites are still made using hand layup technique. In places where vertical mould surfaces are used, having control over the rheological properties of the laminating resin becomes highly beneficial. Thus, the importance of highly dispersed Fumed Silica (FS) as a thickening and thixotropic agent for laminating resins has increased with time. This paper investigates the effect of adding small quantities of AEROSIL®200 FS to composite materials made of E-glass fibers and unsaturated polyester resin. Hand layup technique was used and the effects on the mechanical properties of the nanocomposites for different amounts of FS were studied. The nanocomposites with FS filler showed a small improvement in tensile properties and a significant improvement in flexural properties. SEM images taken indicates that the addition of the FS filler alters the polyester resin system from being brittle to ductile in nature.
Keywords:
Fumed Silica, Glass Fiber Reinforced Polymer, Hand Layup, Nanocomposite
Cite this paper: Deepak Sequeira , Jeevan Mascarenhas , Darren Picardo , Rayen Dias , Orville Sutari , Mechanical Behaviour of Fumed Silica/Glass Reinforced Polyester Nanocomposites, American Journal of Materials Science, Vol. 5 No. 3C, 2015, pp. 92-95. doi: 10.5923/c.materials.201502.19.
1. Introduction
Fiber Reinforced Polymer (FRP) is a composite material made of a polymer matrix reinforced with fibers. The fibers are usually glass, carbon, or aramid. The polymer matrix is usually an epoxy, vinylester, or polyester thermosetting plastic. The matrix forms a significant volume fraction of a polymer composite and it has a number of critical functions; it binds the reinforcements together, maintains the shape of a component and transfers the applied load to the reinforcing fibers [1]. FRP composites are lightweight, non-corrosive, exhibit high specific strength, and specific stiffness, are easily constructed, and can be tailored to satisfy performance requirements [2]. The hand layup method for manufacturing composites is still being used even today. The importance of hand layup is justified by its extensive application in the aerospace industry. Although the manufacturing processes have been undergoing constant technical changes, the hand layup still persists as the method in use for more than half of all advanced aerospace composite structures. Its large use results from the extreme flexibility which allows the manufacturing of a large variety of shapes [3].In the industry, the addition of filler materials to a polymer is a common practice; this not only improves several properties but also reduces the processing cost significantly [4]. The variation in the properties can be due to the change in the microstructure of fiber/filler and matrix reinforcement [5]. The purpose of incorporating FS filler is for the rheological and thixotropic control of liquid systems including polymers. While manufacturing composites, it is difficult to prevent resin from sagging on vertical surfaces of a mould. The addition of FS imparts anti-sagging properties to resin, thus ensuring proper wetting out of fibers during composite moulding. Dispersion of FS in composite is related to the viscosity of the mixture and the shear stresses generated in the preparation of the mixtures [6].A brief summary of some of the relevant work is presented. Kumar et al. [7] studied the tensile properties of epoxy polymer filled with hydrophilic FS. Contrary to the fact that hydrophilic FS fillers are not compatible with resin systems that are polar in nature (epoxy is polar, thus making it also hydrophilic), their tests show an increase in the tensile strength for the addition of up to 2% by weight of FS filler. Marinković et al. [8] reported that the tensile strength and tensile modulus of composites prepared from unsaturated polyester resin decreased on the addition of hydrophobically modified silica nanoparticles, used as filler. This is in congruence with the given knowledge that hydrophobic FS fillers are not suitable for use in unsaturated polyester resins, which are generally non-polar in nature (hydrophobic). Bhagat and Verma [9] studied the effect of FS taken as different weight fractions and their interactive influences on the morphological characteristics of polyester composites. The results showed that amorphosity is inversely proportional to crystallinity with increasing the filler loading. The main objective of this research is to find out the effects of adding small quantities of FS filler into the laminating resin of a GFRP composite and the changes in its mechanical properties.
2. Materials and Methods
2.1. Materials Used
The matrix is orthophthalic unsaturated polyester resin. The resin curing system comprises of cobalt octoate (accelerator) and methyl ethyl ketone peroxide (catalyst). The reinforcement is E-glass fibers of chopped strand mat type. The filler is AEROSIL®200 hydrophilic FS, having specific surface of 200 m2/g and an average primary particle size of 12 nm. The composites were fabricated using hand layup technique. Three different compositions were prepared by varying the amount of filler added to resin (i.e. 0, 1, and 2% by weight). It was noticed that for filler contents of above 2% by weight, wetting of the glass fibers became extremely difficult owing to the thickening effect and highly viscous nature of the filled resin. Therefore, the nanocomposites prepared had a maximum of 2% by weight added to the resin. The FS filler was incorporated into the accelerated resin by mechanical shear mixing. The FS-resin system was then catalysed right before impregnating the fiberglass mat by hand layup, then stacked up to the desired thickness. The nanocomposites were left to be cured under room temperature conditions for duration of 24 hours. The cured nanocomposites were then de-moulded and specimens were prepared for conducting tensile test and flexural test in accordance with ASTM standards.
2.2. Mechanical Testing and Morphology Study
Mechanical testing was performed to find out the tensile and flexural properties of the nanocomposite specimens. Both tensile and flexural tests were carried out using Instron 3366 – 10 kN machine with a load rating of 2mm/min. In tensile test, the loading applied to both ends of specimen is equal and opposite in direction. For flexural test, a three-point bend test is done. The tensile test samples were rectangular in shape made with the dimensions 250 mm x 25 mm x 2.5 mm, made in accordance with ASTM D 3039/D 3039M standard. The flexural test samples were also rectangular in shape made with the dimensions 90 mm x 12.7 mm x 2.8 mm and having a span length of 46 mm, made in accordance with ASTM D 790 standard.In addition to mechanical testing, a morphology study is made on the fracture surface of the tensile specimens to observe the influence of FS filler on the composite structure. A Carl Zeiss Scanning Electron Microscope (SEM) instrument, EVO MA 18, was used for obtaining the images of the fractured specimen surfaces. The specimens were initially silver coated for the SEM analysis.
3. Results and Discussion
3.1. Tensile Properties
Figures 1 and 2 show the graphs of tensile strength and tensile modulus versus the FS filler content respectively. The tensile strength increases for the addition of FS filler up to 2% by weight to resin. This suggests that there is good bonding between the glass fibers, polyester resin and the nanophase FS particles. The large surface area of the FS nanoparticles would mean that the bonding surface area between the different constituent phases would increase; this could be the possible reason for the improvement in the tensile strength of the nanocomposites. The nanocomposite specimens show an increase in tensile strength by 8% and 11% for the addition of 1% and 2% weight of FS filler respectively. The SEM images of the fractured surfaces of the tensile specimens are shown in Fig. 3. The images show the different phases of the composite. Our focus needs to be on the matrix phase because of its crucial role in the case of mechanical loading. A close look at the fractured matrix surface of the composite containing neat polyester in Fig. 3a, shows a fracture that is smooth in appearance, suggesting that it was caused due to brittle failure. Figure 3c shows the fracture surface of the nanocomposite with 2% of FS filler added in the polyester resin. In this image the fracture surface is very rough in appearance. This suggests that the crack took a longer path of propagation and lead to a failure that is characteristically ductile. This justifies the improvement seen in the tensile properties of the nanocomposites through better bonding of its constituent phases. Figure 3b shows the presence of microvoids (encircled in the image) in the nanocomposite. 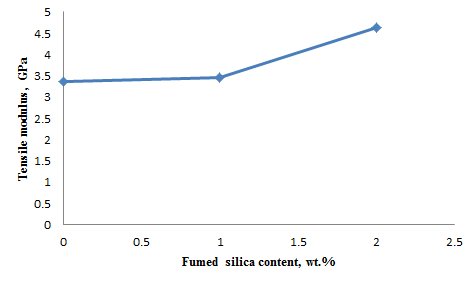 | Figure 1. Effect of fumed silica content on tensile strength |
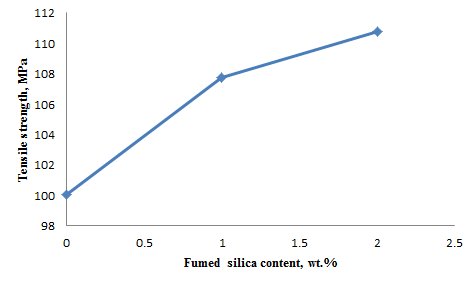 | Figure 2. Effect of fumed silica content on tensile modulus |
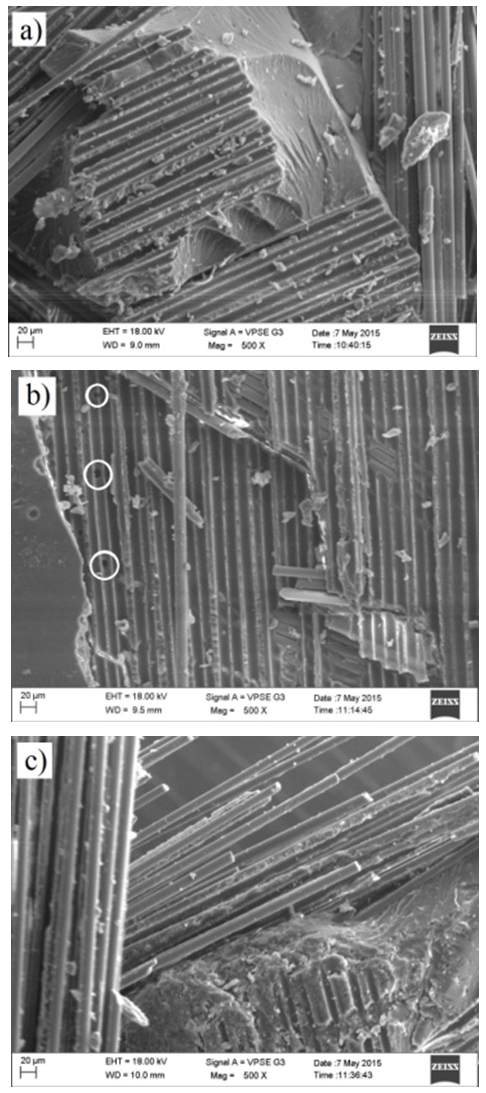 | Figure 3. SEM images of tensile fracture surface of nanocomposite with FS filler content by weight of (a) 0%, (b) 1%, and (c) 2% |
3.2. Flexural Properties
Figures 4 and 5 show the graphs of flexural strength and flexural modulus versus the FS filler content respectively. There is a substantial increase in the flexural strength for the addition of up to 2% by weight of FS filler to resin. This can be explained by the fact that the FS filled polyester can transfer loading to the glass fibers far more effectively as compared to the neat polyester. As stated earlier, the FS filled polyester resin is more ductile in nature, thus the nanocomposite’s ability to resist deformation under load is greatly increased in the case of flexural loading. There is substantial increase in the flexural strength of the nanocomposite specimens by 45% and 59% for the addition of 1% and 2% weight of FS filler respectively.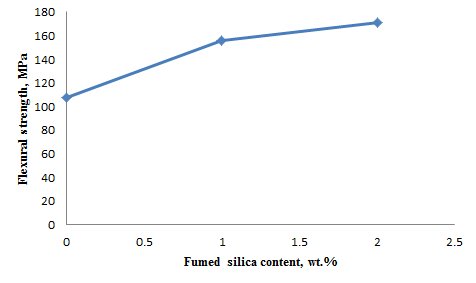 | Figure 4. Effect of fumed silica content on flexural strength |
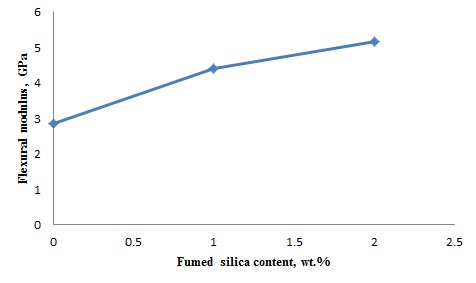 | Figure 5. Effect of fumed silica content on flexural modulus |
4. Conclusions
Nanocomposites comprising of glass reinforced polyester filled with FS were fabricated using hand layup technique and tests were carried out to determine its mechanical properties. SEM analysis was also done to determine the influence of added FS filler in the composite. There is improvement in the tensile strength of the nanocomposite specimens by 8% and 11% for the addition of 1% and 2% weight of FS filler respectively. There is substantial improvement in the flexural strength of the nanocomposite specimens by 45% and 59% for the addition of 1% and 2% weight of FS filler respectively. SEM images of the fractured surfaces taken, indicates that the addition of FS filler turns the polyester resin system from brittle to ductile in nature.
ACKNOWLEDGEMENTS
The authors acknowledge the Department of Dental Materials, MCODS, Manipal, Manipal University for granting the use of their test machine for mechanical testing.
References
[1] | M. Davallo, H. Pasdar, M. Mohseni, “Mechanical properties of unsaturated polyester resin,” International Journal of Chem Tech Research, vol. 2, pp. 2113-2117, Oct-Dec 2010. |
[2] | Luke S. Lee, Ravi Jain, “The role of FRP composites in a sustainable world,” Springer-Verlag, vol. 11, pp. 247-249, Aug 2009. |
[3] | D. T. S. Morais, A. F. Avila, “A methodology for quality control evaluation for laminated composites manufacturing,” J. Braz. Soc. Mech. Sci. & Eng., vol. 27, July/Sept 2005. |
[4] | K. Devendra, T. Rangaswamy, “Determination of mechanical properties of Al2O3, Mg(OH)2 and SiC filled E-glass/epoxy composites,” International Journal of Engineering Research and Applications, vol. 2, pp. 2028-2033, Sept-Oct 2012. |
[5] | Gaurav Agarwal, Amar Patnaik, Rajesh Kumar Sharma, “Thermo-mechanical properties of silicon carbide-filled chopped glass fiber-reinforced epoxy composites,” International Journal of Advanced Structural Engineering, vol, 5, 2013. |
[6] | J. Tarrio-Saavedra, J. Lopez-Beceiro, S. Naya, C. Gracia, R. Artiaga, “Controversial effects of fumed silica on the curing and thermomechanical properties of epoxy composites,” eXPRESS Polymer Letters, vol. 4, pp. 382-395, Apr 2010. |
[7] | M. Ashok Kumar, G. Ramachandra Reddy, K. V. P. Chakradhar, “Hydrophilic fumed silica/clay nanocomposites: Effect of silica/clay on performance,” International Journal of Nanomaterials and Biostructures, vol. 1, pp. 1-11, June 2011. |
[8] | Aleksandar D. Marinkovic, Tijana Radoman, Enis S. Dzunuzovic, Jasna V. Dzunuzovic, Pavle Spasojevic, Bojana Isailovic, Branko Bugarski, “Mechanical properties of composites based on unsaturated polyester resins obtained by chemical recycling of poly(ethylene terephthalate), Hemijska Industrija, vol. 67, pp. 913-922, Oct 2013. |
[9] | Subita Bhagat, Pardeep Kumar Verma, “Analysis of microstructure of fumed silica reinforced polyester composites,” International Journal of Engineering Research and Technology, vol. 2, pp. 1-5, Feb 2013. |