Kiran R. Garadimani , G. U. Raju , K. G. Kodancha
Department of Mechanical Engineering, B.V.B College of Engineering and Technology, Hubballi, India
Correspondence to: Kiran R. Garadimani , Department of Mechanical Engineering, B.V.B College of Engineering and Technology, Hubballi, India.
Email: |  |
Copyright © 2015 Scientific & Academic Publishing. All Rights Reserved.
Abstract
The role of natural and manmade fibers reinforced hybrid composite materials are growing in a faster rate in the field of engineering and technology due to its considerable properties. In the present study the Corn cob particles and E-Glass fibers reinforced polymer hybrid composites were fabricated and evaluated the mechanical properties such as tensile strength, flexural strength and impact strength. The composite boards were prepared by varying both glass fibers and corn cob weight percentage and testing was carried out according to ASTM standards. From the experimental results, it has been observed that the corn cob particles and E-Glass fibers reinforced hybrid epoxy composites exhibited superior properties. The highest Modulus of Rigidity, impact strength, Modulus of Elasticity, was observed for the sample having Corn Cob particles, E-Glass Fibers and Epoxy in proportion 25:5:70. However, the sample with 27.5:2.5:70 has maximum tensile strength and tensile modulus.
Keywords:
Corn Cob particles, E-Glass Fiber, Epoxy, Mechanical Properties
Cite this paper: Kiran R. Garadimani , G. U. Raju , K. G. Kodancha , Study on Mechanical Properties of Corn Cob Particle and E-Glass Fiber Reinforced Hybrid Polymer Composites, American Journal of Materials Science, Vol. 5 No. 3C, 2015, pp. 86-91. doi: 10.5923/c.materials.201502.18.
1. Introduction
Now-a-days, natural fibers reinforced composites exhibit the superior mechanical properties than synthetic fiber reinforced polymer composites due to its inherent properties. Natural fiber reinforced composites are renewable, biodegradable, environment friendly, light weight material when compared to the synthetic fiber reinforced composites [1, 2]. The potential applications of these composites are growing rapidly in many engineering fields especially the cost of the material is main factor and to improve erosive environment [3, 4]. The mechanical properties of sodium hydroxide treated natural fiber composites under saturation pressure can be improved without any major changes in mechanical behavior as indicated by Benitez [5].R. Bhoopathia et al. [6] have studied the fabrication and property evaluation of Banana-Hemp-Glass fiber reinforced composites. The following conclusions were drawn with considering microstructure and mechanical properties, The banana-glass fiber hybrid composites had a tensile strength of 39.5MPa followed by the hemp-glass fiber reinforced composites which holds the value of 37.5MPa. The maximum flexural strength of 0.51kN hold by the banana-hemp-glass fiber reinforced composites followed by banana-glass fiber reinforced composites which is having the value of 0.50kN. The impact strength of the hybrid composites varies from the 5.33 to 8.66Joules.Ajith Gopinatha et al. [7] have investigated mechanical properties of Jute- Polyester and Jute –Epoxy composites. They found that the tensile strength for jute-epoxy and jute-polyester composites was 12.46 N/mm2 and 9.23N/mm2. The flexural strength of jute-epoxy and jute-polyester composites was found to be 38.68 and 44.71 N/mm2 respectively. The jute polyester composite seemed to have better impact energy than jute-epoxy composites. The 5% NaOH treated jute fiber reinforced composites seemed to show much better results than the 10% NaOH treated jute composites. From the above results, it revealed that the jute epoxy exhibited better tensile and flexural properties.Rahul Kumar et al. [8] have studied the mechanical properties of wood dust reinforced epoxy composite, they got to the conclusion that the experimental results support that successful fabrication of sundi wood dust reinforced epoxy composites is possible and that sundi wood dust possesses good filler characteristics as it improves the tensile and flexural properties of the polymeric resin. The maximum load, tensile stress and strain, and flexural stress and strain values are found to be maximum and minimum at the filler wt of 10 % and 15 % respectively with speed of 1 mm/min. but the tensile and flexural modulus values are found to be maximum and minimum at 10% filler wt with speed of 2 mm/min and at 0% filler wt with speed of 1 mm/min respectively. The best mechanical properties are observed for 10% filler wt. and speed of 1 mm/min and 2 mm/min speed.M. Ramesh et al. [9] have studied the processing and mechanical property evaluation of banana fiber Reinforced Polymer Composites and they got to the conclusion that the maximum tensile strength is 112.58MPa which is hold by the 50% banana fiber and 50% epoxy resin composites. The maximum flexural strength is 76.53MPa and this is also hold by the same combination of the composite samples. The maximum impact strength hold by the 60% glass fiber and 40% epoxy resin composites is 11.22 Joules followed by 50% banana fiber and 50% epoxy resin composites can withstand the impact load of 9.48 Joules. From the experimental study it can be suggested that, the 50% banana fiber and 50% epoxy resin composite materials can withstand the higher loads when compared to the other combinations.M. Ramesh et al. [10] had studied the comparative evaluation on properties of hybrid glass fiber-sisal/jute reinforced epoxy composites and they got to conclusion that the sisal/GFRP composite samples possess good tensile strength and can withstand the strength up to 68.55 MPa. The jute/GFRP composite specimen is holding the maximum flexural load of 1.03KN slightly higher than the sisal/GFRP composite sample. The failure morphology of the tested samples is examined by using Scanning Electron Microscope. From the results, they concluded that sisal-GFRP composites performing better for tensile loading and jute-GFRP composites are performing better for flexural loading.Sukhdeep Singh et al. [11] have studied the effect of tensile and flexural behavior of hemp fiber reinforced virgin recycled HDPE matrix composites and they got to the conclusion that reinforcement of hemp fibers in HDPE matrix reduces the tensile strength. Tensile strength of the composite decreases by 0.53 MPa to 2.20 MPa with the increase in hemp content from 10% to 30% respectively when compared with specimen made of 50% fresh and 50% recycled HDPE. However, the composite with 20% hemp fibers was observed to have tensile strength higher by 0.28 MPa as compared to HDPE sample containing 50-50 mixture of fresh and recycled HDPE. Flexural strength decreases with the addition of hemp fibers.
2. Experimental Details
2.1. Materials
Corn CobCorn Cob botanically known as Zea mays belongs to Poaceae family. A corn cob is the central core of maize. It is the part of the ear on which the kernels grow. Clean and dried Corn Cob shells were first washed with water to remove dirtand other impurities. Then, washed shells were chemically treated with 5% NaoH solution for 2h and then washed with distilled water until all NaoH gets eliminated. Corn Cob shells are ground in hammer mill and appropriate sieves are used to get the required particle size of 175-212 microns. The Table 1 shows chemical characteristics of corn cob particles which was tested in ESSAR Laboratories Hubli.Table 1. Chemical characteristics of Corn Cob particles 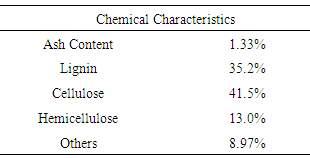 |
| |
|
E-Glass FibersThe most common types of glass fiber used in fiberglass is E-Glass fibers, which is alumino-borosilicate glass with less than 1% w/w alkali oxides, mainly used for glass-reinforced plastics. In this present work E-Glass fibers of 2-3mm in length are used. E-Glass Fibers were provided by Anuj Fibers, Delhi.EpoxyEpoxy is the cured end product of epoxy resins, as well as a colloquial name for the epoxide functional group. Epoxy is also a common name for a type of strong adhesive used for sticking things together. In this present work Lapox L-12 resin and K-6 hardener were used and this was provided by Yuje Marketing Ltd. Bangalore, India.
2.2. Preparation of Composite Specimen
The composite board was prepared by hand layup process. Corn Cob particles and E-Glass Fibersare used for the composite preparation. Corn Cob particles are varied from 27.5, 25, 22.5, and 20, volume percent and E-Glass Fibers is varied from 2.5, 5, 7.5, and 10 volume percent. Corn Cob particles of 27.5 and Glass Fibers of 2.5% is coded as CGE1, 25(CC) and 5 % (GF) is coded as CGE 2, 22.5 (CC) and 7.5%(GF) coded as CGE3 and 20 and 10% as CGE4. Appropriate amounts of corn cob particles and E-Glass Fibers along with constant Epoxy resin were taken in a plastic container and stirred thoroughly to get a homogeneous mixture. After adding the hardener, the mixture was again stirred for 10 min and thoroughly mixed mixture was placed in a mold and compressed uniformly. This set up was kept for 24h of time and after curing composite board was taken out from the mold. The thickness of the composition is limited to 7mm and the mold size is 230x160 mm. After curing, the edges of the specimen are neatly cut as per the required dimensions.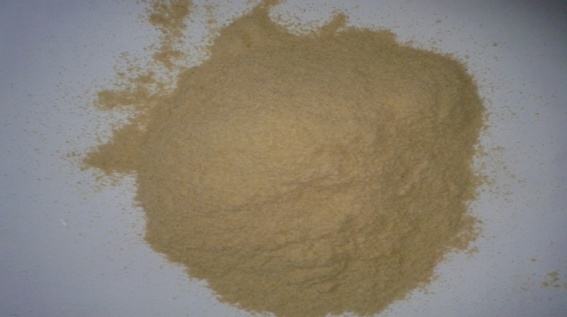 | Figure 1. Corn Cob particles |
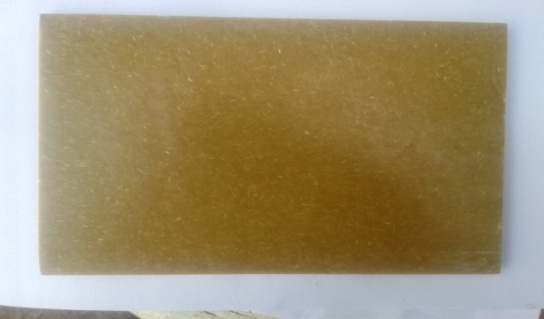 | Figure 2. Fabricated CGE Composite board |
2.3. Mechanical Properties of Composites
2.3.1. Tensile Test
The test method covers the determination of the tensile properties of corn cob particle and E-Glass fibers reinforced hybrid polymer composites in accordance with ASTM D638 test procedure. A computerized universal testing machine (UTM) was used to conduct the tension test. The test specimen of 50mm gage length, 13mm width and 7mm thickness was placed between the holders of the universal testing machine and the constant rate of loading of 3mm/min was applied. Stress, strain and Young modulus were calculated. The computed values of young’s modulus are based on the slope of the linear portion of the stress-strain curve. Three specimens for each sample were tested and tensile strength and tensile modulus were calculated automatically by the machine. Specimens are shown in Fig 3.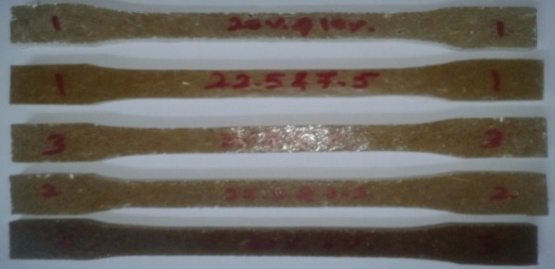 | Figure 3. Tensile test specimen |
2.3.2. Flexural Test
The test method determines the flexural properties of corn cob particles and E-Glass fiber reinforced composites in accordance with ASTM D790. Flexural tests were performed using universal testing machine at a constant rate of 0.25mm/min. four test specimens were cut to 165×15mm and 7mm depth. The span length for loading the specimen was 112mm. Flexural strength and flexural modulus were calculated using equation (1) and (2) | (1) |
 | (2) |
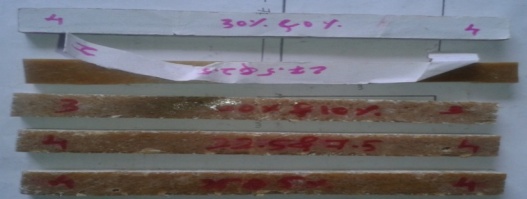 | Figure 4. Flexural test specimens |
2.3.3. Impact test
The three test specimens are prepared from each composition of Corn Cob particles and E-Glass fiber reinforced composites for evaluating the impact load carrying capacity of the material. The test specimens were prepared as per the ASTM standard D256 and the edges of the specimens are neatly finished and small ‘v” notches are also provided by using hack saw blade. During the test the maximumenergy that can bestored to break the specimens are noted for the entire specimen for analysis of results. The impact test CGE specimens before and after fracture are presented in Fig. 5.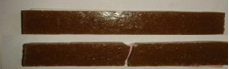 | Figure 5. Impact test specimen before and after failure |
3. Results and Discussion
The use of natural and manmade fibers reinforced hybrid composite materials are growing day by day due to its characteristics like eco-friendly, recyclable, bio-degradable and user friendly in nature. Many researchers are working in this field to make the composites hybrid and to replace metals and alloy materials in the field of engineering and technology without affecting the load carrying capabilities and cost aspects. In the present experimental study, Corn Cob particles are hybridized with E-Glass fiber and hybrid composites were prepared. Then the test specimens are prepared as per ASTM standards and testing of materials has been carried out for tensile, flexural and impact properties.
3.1. Analysis of Tensile Properties
The composite samples are tested in UTM and the typical Load v/s deformation curve generated directly from the universal testing machine during tensile loading for the hybrid composites is presented in Fig.6. The tensile strength and tensile modulus of different hybrid composites is presented in Fig.7 and Fig 8. Tensile strength of CGE is in the range of 15.68-18.04MP aindicating maximum tensile strength for CGE2, bears load of 977.26N. Tensile modulus of CGE is in the range of 629.96-926.78MPa indicating maximum tensile modulus for CGE2 of 926.78MPa. From the results of the experiments presented in Figures 7 and 8; the tensile test shows a steady increase in tensile strength with increases in fiber content. This may be attributed that the fibers had created some reinforcing effect and had been responsible for the increase in tensile strength. However, further increment in the fiber content from 7.5% onwards, a decrease in the tensile strength was witnessed. This is due to increase in fiber–fiber interactions that may also cause difficulties in dispersion resulting in composites having low mechanical properties [13, 14]. Similar type of results were found for sisal fiber/GF and Jute/GF reinforced polymer composites, initially they have witnessed the increase in tensile strength for 5% to 10% volume fraction and gradually there was a decrease in the tensile strength for 15% onwards [10]. At high levels containing 45wt% fiber loading (oil palm fibers & GF), the increased population of fiber leads to agglomeration. Therefore, the fibers are unable to contribute to the effective stress transfer between fibers and the matrix [12].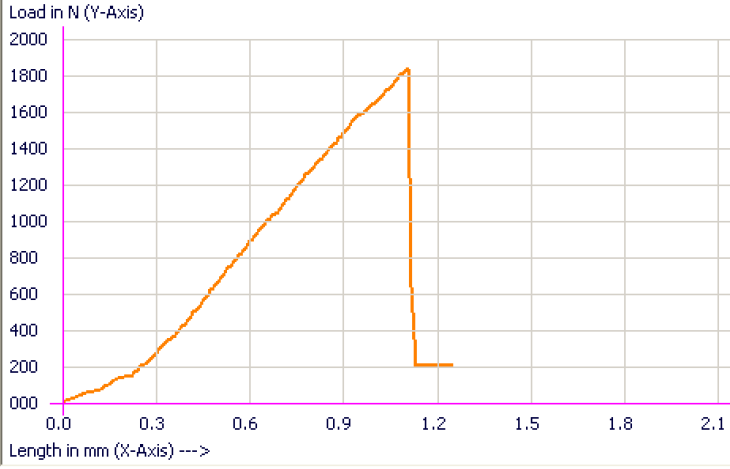 | Figure 6. Typical Load vs. deformation curve during tensile loading |
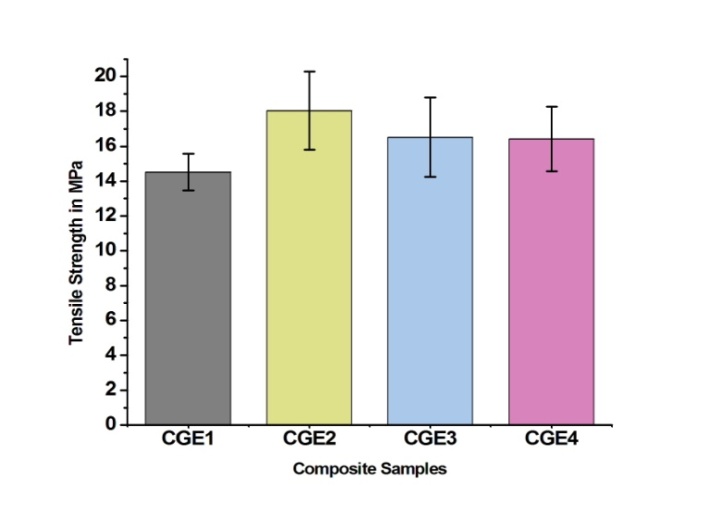 | Figure 7. Tensile strength of different hybrid composite samples |
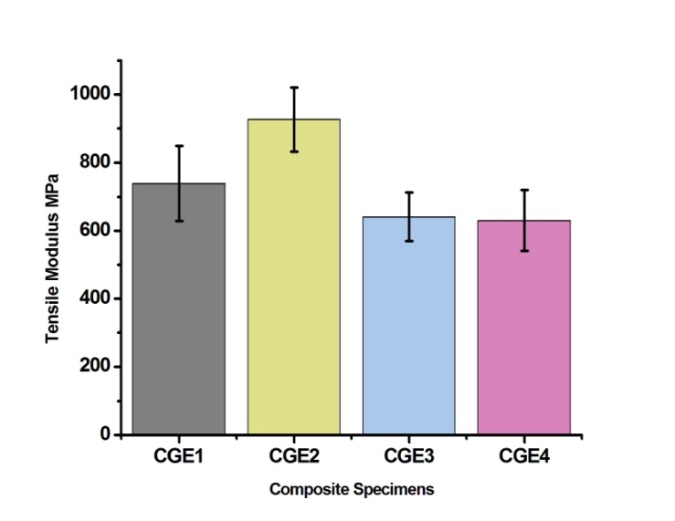 | Figure 8. Tensile Modulus of different hybrid composite samples |
3.2. Analysis of Flexural Properties
Flexural strength and Flexural modulus of CGE composites are shown in Figures 9 and 10. From the results of the experiments shown in Figures 9 and 10, MOR of CGE is in the range of 26-35 MPa, indicating maximum for sample CGE3.MOE of CGE is in the range of 3200-4700 MPa and sample CGE3 has maximum MOE.FromCGE3 on wards MOR and MOE value reduces gradually. It is observed that flexural properties increase as the glass fiber loading increases in hybrid composites. The increased flexural strength of the hybrid composites with the loading of glass fiber is mainly due to the increased resistance to shearing of the composites as a result of the inclusion of rigid glass fiber [15]. The decrease in the flexural properties at higher fiber loadings is due to the increased fiber-to-fiber interactions and dispersion problem which results in low mechanical properties of composites.Similar observation has been reported by the researcher in the study onOil palm fibers/GF hybrid composites [12] and on Sisal/GF hybrid composites [16]. Results show that for EFB (Oil Palm fibers)/polyester composite, both flexural strength and modulus value are found to have decreased at low weight fraction (15-25 wt%) and only show an improvement after further additions of up to45 wt%.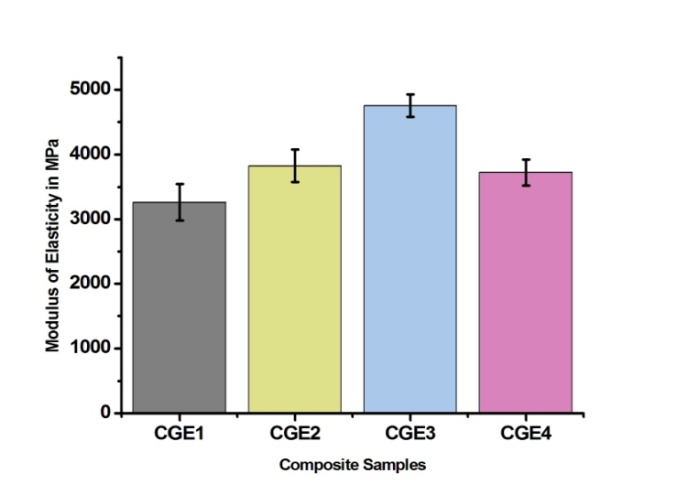 | Figure 9. Modulus of Elasticity for flexural loading |
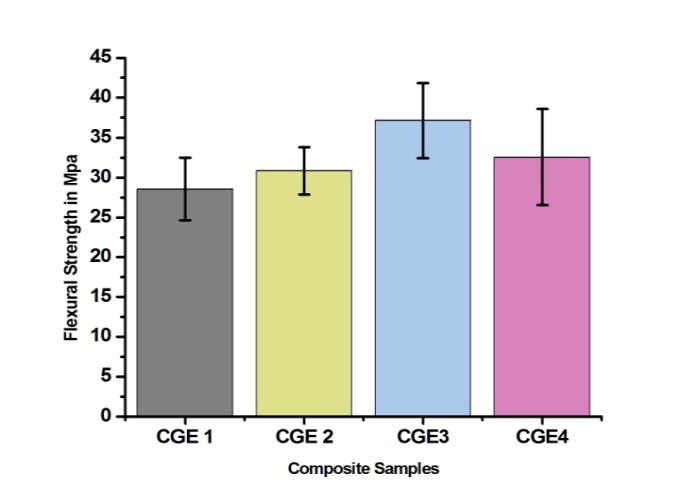 | Figure 10. Flexural strength of different hybrid composite samples |
3.3. Impact Strength Analysis
The impact test results are shown in Figure 11. Impact strength is in the range of 14.06-27.16KJ/m2 indicating maximum value for CGE3. From CGE4 onwards impact strength value decreases gradually. Increase in impact strength is by the fibers which are present in sufficient amounts that canprovide the effective stress transfer between the fiber and matrix. Excellent dispersion of the fibers also occurs at this composition it also shows decrease in impact strength for increase in fiber content after 7.5%. This may be attributed to the weak interfacial interaction between the fiber and the matrix for higher fiber content. Similar type of results were found for oil palm fibers and glass fibers reinforced hybrid composites, impact strength was found to have increased with anincrease in the fiber content of composites up to 35 wt%. Composites having fiber loading of over 35% weight fraction exhibits areduction on impact properties among the composites [12, 16]. At higher loading fiberto-fiber contact increases in the composites. The inter fiber interaction decreases the effective stress transfer between the fiber and matrix. This contributes to decreases in impact properties at higher fiber loading.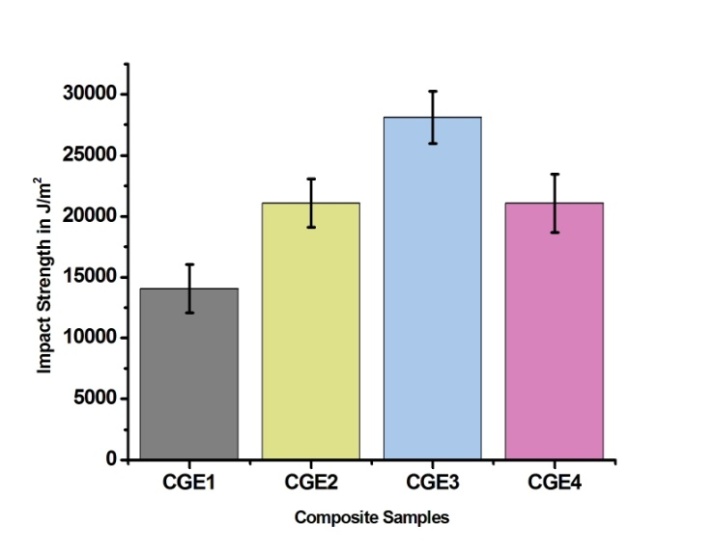 | Figure 11. Impact strength of different hybrid composite samples |
4. Conclusions
The Corn Cob particles and E-Glass fiber reinforced composites are fabricated and the mechanical properties such as tensile strength, flexural strength and impact strength of these composites are evaluated. The following conclusions have been derived from the experimental investigations.● CGE2 (25% Corn Cob particle & 5% E-Glass fiber) is exhibiting good tensile strength of 18.04MPa and again there is a decrease in the tensile for CGE 3 and CGE 4.● The flexural load carrying capacity of Corn Cob particles and E-Glass fiber reinforced composites is better for CGE1 to CGE 3 and it is giving optimum value for CGE3 of 37.14 MPa.● The impact strength of the hybrid composites varies from the 14.06-27.16KJ/m2.● It is suggested that Corn Cob and E-Glass fibers reinforced hybrid epoxy composites can be used as an alternate material for synthetic fiber reinforced composite materials.
References
[1] | K.M.M. Rao and K. M. Rao, “Extraction and tensile properties of natural fibers: vakka, date and bamboo,” Composite Structures, 2007;77:288–295. |
[2] | M. Boopalan, M. Niranjana and M. J. Umapathy, “Study on the mechanical properties and thermal properties of jute and banana fiber reinforced epoxy hybrid composites,” Composites: Part B; 2013; 51:54–57. |
[3] | Bledzki AK, Mamun AA and Faruk O, “Abaca fibre reinforced PP composites and comparison with jute and flaxfiber PP composites,” Express Polymer Letters; 2007; 1:755–762. |
[4] | Mukhopadhyay S. S., Fangueiro R. R and Yusuf A, “Banana fibers–variability and fracture behavior,” Journal of Engineered Fiber and Fabrics; 2008; 3:1–7. |
[5] | Benítez AN, Monzón MD, Angulo I, Ortega Z, Hernández PM and Marrero MD, “Treatment of banana fiber for use in the reinforcement of polymeric matrices,” Measurement; 2013; 46:1065–1073. |
[6] | R. Bhoopathi, M. Ramesh and C. Deepa, “Fabrication and Property Evaluation of Banana-Hemp-Glass Fiber Reinforced Composites,” Procedia Engineering 97 (2014) 2032 – 2041. |
[7] | Ajith Gopinath, Senthil Kumar. M and Elayaperumal A, “Experimental Investigations on Mechanical Properties of Jute Fiber Reinforced Composites with Polyester and Epoxy Resin Matrices,” Procedia Engineering 97 (2014) 2052 – 2063. |
[8] | Rahul Kumara, Kausik Kumarb, Prasanta Sahooc and Summit Bhowmika, “Study of Mechanical Properties of Wood Dust Reinforced Epoxy Composite,” Procedia Materials Science 6 (2014) 551 – 556. |
[9] | M. Rajesh, T. Sri Ananda Atreya, U. S. Aswin, H. Eashwar and C. Deepa, “Processing and Mechanical Property Evaluation of Banana Fiber Reinforced Polymer Composites,” Procedia Engineering 97 (2014) 563 – 572. |
[10] | M. Ramesh, K. Palanikumar and K. Hemachandra Reddy, “Comparative Evaluation on Properties of Hybrid Glass Fiber- Sisal/Jute Reinforced Epoxy Composites,” Procedia Engineering 51 (2013) 745 – 750. |
[11] | Sukhdeep Singh, Dharmpal Deepak, Lakshya Aggarwal and V.K. Gupta, “Tensile and flexural behavior of hemp fiber reinforced virgin recycled HDPE matrix composites”, Procedia Materials Science 6 (2014) 1696 – 1702. |
[12] | H. P. S. Abdul Khalil, S. Hanida, C. W. Kang and N. A. Nik Fuaad, “The Effects on Mechanical and Physical Proper ties of OilPalm Fiber (EFB)/Glass Hybrid Reinforced Polyester Composites”, Journal of Reinforced Plastics and composites 2007 26: 203. |
[13] | Sreekala, M. S., George, J., Kumaran, M. G. and Thomas, S. (2002), “The Mechanical Performance of Hybrid Phenol-Formaldehyde-based Composites Reinforced with Glass and Oil Palm Fibers”, Composites Science and Technology, 62: 339–353. |
[14] | Devi, U., L. Bhagawan, S. S. and Sabu T, “Mechanical Properties of Pineapple Leaf Fiber Reinforced Polyester Composites”, Applied Polymer Science, (1997). 64: 1739–1748. |
[15] | Mishra, S., Mohanty, A. K., Drzal, L. T., Misra, M., Panja, S., Nayak, S. K. and Tripathy, S. S, “Studies on Mechanical Performance of Biofiber/Glass Reinforced Polyester Hybrid Composites”, Composites Science and Technology, (2003)65: 1377–1385. |
[16] | Jacob, M., Thomas, S. and Varughese, K. T. “Mechanical Properties of Sisal/Oil Palm Hybrid Fiber Reinforced Natural Rubber Composites”, Composites Science and Technology, (2003)64: 955–965. |