K. Srinivas 1, M. S. Bhagyashekar 2
1Department of Mechanical Engineering, Don Bosco Institute of Technology, Bangalore, India
2Department of Mechanical Engineering, Raja Rajeshwari college of Engineering, Bangalore, India
Correspondence to: K. Srinivas , Department of Mechanical Engineering, Don Bosco Institute of Technology, Bangalore, India.
Email: |  |
Copyright © 2015 Scientific & Academic Publishing. All Rights Reserved.
Abstract
Several series of epoxy composites were prepared from micro metallic particulates of aluminium, copper and hybrid aluminium and copper. The weight fractions of three different fillers were varied from 10 to 40 wt % at varying intervals of 10%. The hybrid Aluminium-Copper filled epoxies were prepared by varying fillers in four different combinations. The effect of addition of the above particulate fillers on flexural properties of polymer composite with epoxy LY556 matrix has been studied. The increase in filler fraction increases the flexural modulus of epoxy composites while degradation in flexural strength was observed. Further studies were carried out on fractured surfaces using scanning electron microscopy to understand the fracture mechanism.
Keywords:
Al-aluminium, Cu-Copper, Ep-Epoxy, Epoxy composites, Hybrid fillers, Flexural strength, Flexural
Cite this paper: K. Srinivas , M. S. Bhagyashekar , Effects of Mono (Al/Cu) Metallic and Hybrid (Al-Cu) Metallic Fillers on Flexural Performance of Epoxy Composites, American Journal of Materials Science, Vol. 5 No. 3C, 2015, pp. 81-85. doi: 10.5923/c.materials.201502.17.
1. Introduction
Epoxy a widely used engineering polymer due to its qualities such as good chemical and corrosion resistance, compatibility with many fillers good mechanical properties [1] has innumerable applications in transportation, construction, marine, rapid tools [2, 3], packaging industries [4] coatings, adhesives [5]. Epoxies are brittle in nature due to its cross linked structure and are costlier than some other thermosets. Hence reinforcing fillers serve dual purpose like modify some specific property and to reduce overall cost [1]. The properties of epoxy can be modified or enhanced by reinforcing it with fibers or use of different types of fibre mats, or combine fibres and particulate fillers where fibers takes the load and particulate improves specific properties, or combine short fibers and particulates. The fillers can be metallic, ceramic, whiskers, oxides, or blending with thermo plasts [6]. Epoxies filled with metallic particulates have applications in rapid tooling, thermal management systems, electrical and tribological applications. Mechanical behaviour of a particulate filled polymer composite is dependent on characteristics of reinforcing material such as type, size, content and shape, chemical structure and cross link density [7]. The present study employs particulates of copper and aluminium as reinforcing fillers for epoxy resin individually and combined together in various combinations to evaluate flexural properties of composites. Copper which is soft and ductile and aluminium characterized by relatively low density, high electrical and thermal conductivity, resistance to corrosion in ambient atmosphere [8].
2. Material and Methods
2.1. Materials
Epoxy resin of type LY556 (RT cure) and an amine hardener HY951 (Huntsman India Ltd) are used as matrix. The resin and hardener are mixed in the ratio 10:1. The reinforcements used are particulates of aluminium (Loba cheme India) and copper (Loba cheme India) shown in figure 1 and 2 respectively. The size of aluminium particulates are in the range 10 to 80 µm appears like a rod while particulates of copper are dendric in shape and size ranges from 5µm to 15 µm. 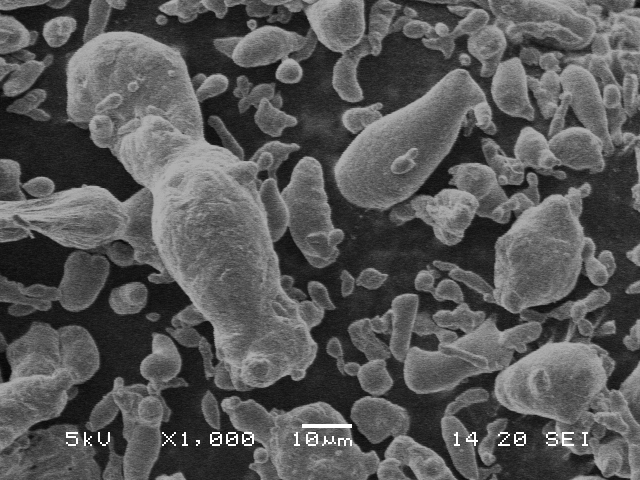 | Figure 1. SEM of metallic particulates of aluminium |
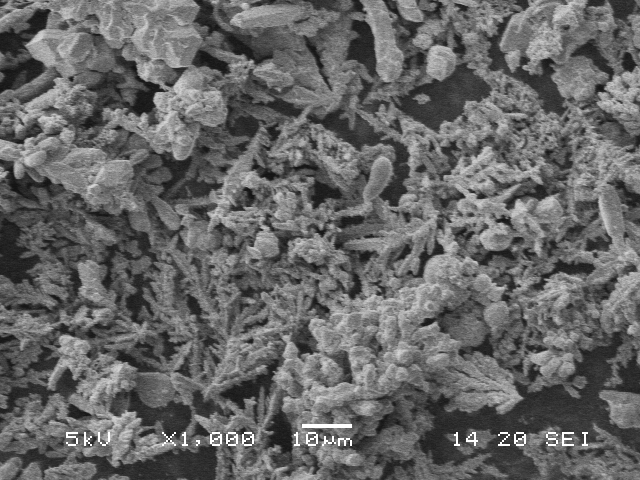 | Figure 2. SEM of particulates of copper |
2.2. Specimen Preparation
The predetermined amounts of metallic reinforcements were preheated to remove any moisture present in it and were dispersed in epoxy. The mixtures were stirred continuously until the reinforcements were properly distributed. Hardener was added to the mixture with continuous stirring, followed by pouring the mixture in to a prepared mould. The specimens were allowed to cure in the mould for 24 hours at room temperature followed by post curing at 50°C for 30 minutes, 70°C for 60 minutes and 85°C for 120 minutes. The cast test specimens had the following dimensions: length 127 mm, width 10mm and thickness 3mm. Schematic diagram of the test specimen is shown in figure 3. The fillers were varied from 10wt% to 40wt% in steps of 10%. The maximum filler fraction was limited to 40wt% due to processing difficulties above 40%. Table 1 presents the details of cast composite specimens and the codes indicating reinforcement fraction. For example 10A20C-Ep represents 10wt% aluminium, 20wt%, copper and 70wt% epoxy.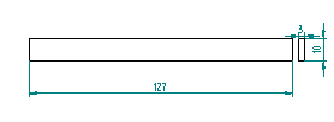 | Figure 3. Schematic Diagram of test specimen |
2.3. Flexural Testing and Micro Structural Studies
Flexural measurements were carried out using LYOD’S LR50K universal tester. ASTM D 790 test method was followed for a three point bend test at 1mm/min deformation rate. The flexural strength is evaluated using the equation 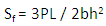 | (1) |
Where, Sf = ultimate flexural strength (MPa)
P = maximum load in Newton
L = length of the specimen in mm
b = width of the specimen in mm
h = thickness of the specimen in mmFlexural modulus is evaluated using the equation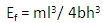 | (2) |
Where Ef = flexural modulus (GPa)
m = slope of load deflection curveMicro structural studies are carried out on fractured surfaces of composite specimens to investigate dispersion of fillers, understand the nature and the reasons for fracture. The SEM studies were carried out for fillers and fractured surfaces of test specimens. The images were captured using a scanning electron microscope of type JOEL 5600 LV. The specimens were coated with platinum before observation. SEM images were taken at different magnifications.
3. Results and Discussions
3.1. Flexural Strength of Al / Cu Filled Epoxy and Hybrid (Al-Cu) Filled Epoxy
Table 1 presents the flexural test data in terms of flexural strength and flexural modulus of epoxy and its composites containing various fillers, tested under flexural mode. From figure 4, the neat epoxy casting exhibits a flexural strength of 103.25 MPa and the flexural strength decreases with increased Al / Cu content except for 20C-Ep exhibiting a flexural strength of 103.32Mpa. Maximum reduction is seen at 40% filler content. The increase in filler content above 10% makes the interface weak [9, 10]. The addition of fillers creates the stress concentration at the interface of filler and matrix [11]. Further, agglomeration of particulates at higher particulate loading reduces the flexural strength of filled polymer composites [12, 13]. Epoxy filled with Al particulates show lower flexural strength than Cu particulate filled epoxy. This may be due to bigger size of Al particulates as the mechanical behaviour of a particulate filled polymer is dependent on size, type, content and shape. Further composite properties are affected by the chemical structure and cross link density when they are filled with metallic fillers [7].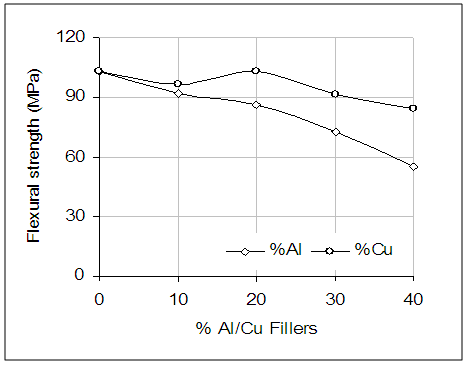 | Figure 4. Flexural strength of Al-Ep & Cu-Ep |
Table 1. Flexural strength and flexural modulus of epoxy and its composites 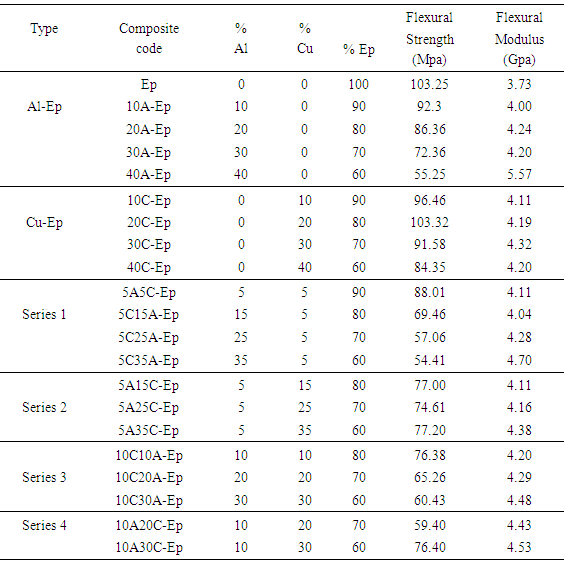 |
| |
|
Figure 5 compares the flexural strength of series 1 and series 2 composites. Series 1 has Cu at 5wt%, while Al is varied from 5 to 35wt% in steps of 10%. Series 2 has Al at 5wt%, while Cu is varied from 5 to 35wt% in steps of 10%. Degradation of flexural strength was observed for both types of composites and is higher in series 1. This may be due to higher Al content in series 1 composite. Figure 6 compares the flexural strength of series 3 which has Cu at 10wt%, while Al is varied from 10 to 30wt% in steps of 10% and series 4 which has Al 10wt%, while Cu varied from 10 to 30wt% in steps of 10%. Trend similar to previous composites are seen for series 3 and 4 i.e. increased filler content reduces the flexural strength and higher Al content further reduces the strength.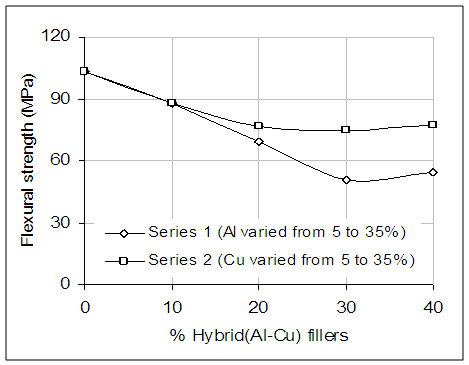 | Figure 5. Flexural strength of Series 1 and series 2 Ep-composites |
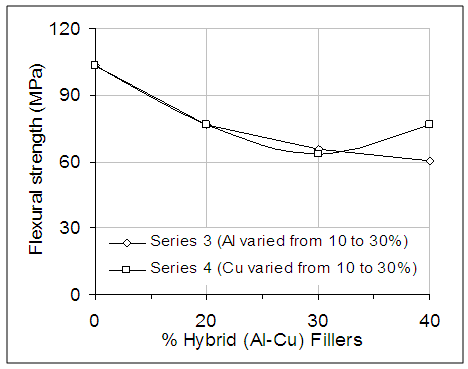 | Figure 6. Flexural strength of series 3 and series 4 Ep- composites |
3.2. Flexural Modulus of Al / Cu Filled Epoxy and Hybrid (Al-Cu) Filled Epoxy
Figure 7 compares the flexural modulus of Al-Ep and Cu-Ep composites. Neat epoxy exhibits a flexural modulus of 3.73 GPa. Flexural modulus increases with an increase in aluminium or copper content. Up to 20% filler content much variation was not seen for Al-Ep or Cu-Epoxy. A steep rise in modulus was seen for 40% aluminium filled epoxy (5.57GPa) while a fall in modulus was noticed for 40% copper filled epoxy (4.20GPa). However the improvement in modulus for 40A-Ep is 49% and for 40C-Ep is 12.60% over neat epoxy. 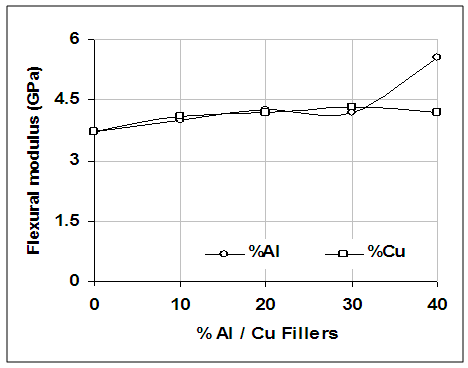 | Figure 7. Flexural modulus of Al-Ep and Cu-Ep |
Flexural modulus of series 1 and series 2 which are filled with hybrid (Al-Cu) fillers are shown in figure 8. These composites show a trend similar to mono Al/Cu filled epoxy composites. Series 1 which has a dominance of aluminium exhibit marginally higher modulus than series 2. 5C35A-Ep exhibits a modulus of 4.70 GPa while 5A35C-Ep exhibits 4.38GPa. The improvement over neat epoxy is 26% and 17.42% respectively. The flexural modulus of series 3 and 4 is shown in figure 9. Series 4 exhibits higher modulus than series 3 though it has higher copper fraction. This may be due to increased Al by 5wt%. 10C30A-Ep of series 3 and 10A30C-Ep of series 4 exhibits a modulus of 4.48GPa and 4.53GPa highest in their series. This amounts to an improvement of 20.10% and 21.44% over neat epoxy. | Figure 8. Flexural modulus of series 1 and series 2 Ep-composites |
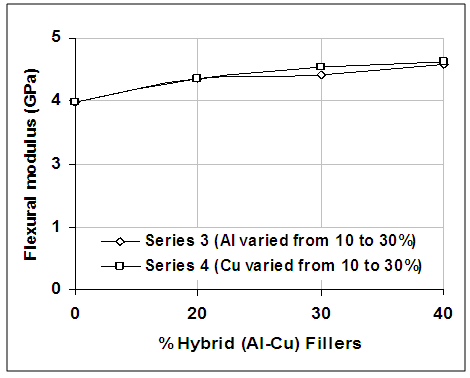 | Figure 9. Flexural modulus of series 3 and series 4 Ep- composites |
The fillers which are stiffer than matrix, increases modulus of the composites when they are reinforced [4]. Addition of fillers increases the modulus of the composite as the moduli of fillers are higher than matrix and also modulus is also dependent on particle size [14]. Since copper particles are smaller in size compared to aluminium particles, copper filled epoxy and copper dominated hybrid epoxies show lower modulus than aluminium composites. At higher filler loading percolation network of fillers develops which increases the modulus of the composites. Increasing modulus with increased filler content is attributed to inherent stiffness of the fillers [15].
3.3. SEM of Fractured Surface
The SEM of the fractured surface of specimens of series 1 is shown in figures 10-13. Figure 10 presents the fractured surface of 5C5A-Ep. This composite has equal blend of both type of fillers. The image show severe cracks all over the surface and fewer particles are seen. Figure 11, the fractured surface of 5C15A-Ep presents a surface with reduced cracks. Figure 12 fractured surface of 5C25A-Ep which has a filler content of 30%, lot of particles are seen. A crack formed around a particle shown is seen in figure 12 shown by an arrow, where particle has acted as a crack pinning mechanism. Figure 13, image of fractured surface of 5C35A-Ep displays crack formation and dislodged particles.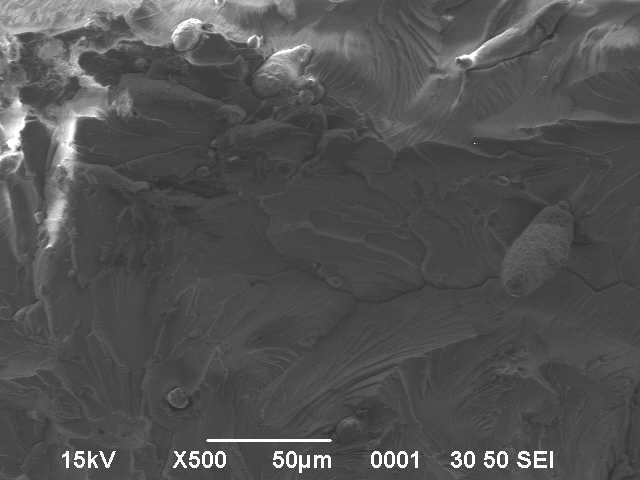 | Figure 10. SEM of fractured surfaces hybrid 5C5A-Ep |
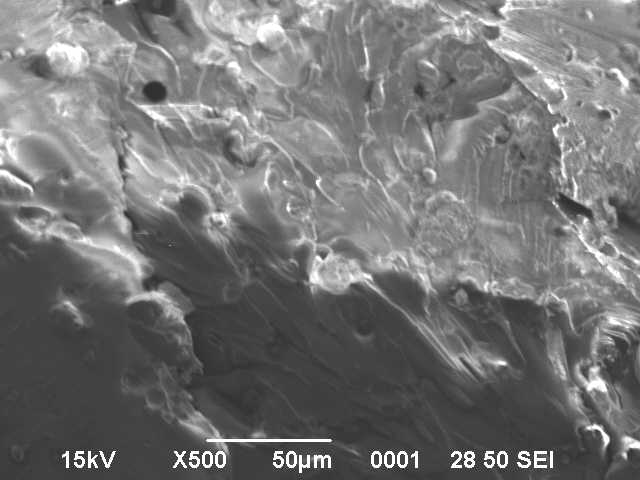 | Figure 11. SEM of fractured surfaces hybrid 5C15A-Ep |
 | Figure 12. SEM of fractured surfaces hybrid 5C25A-Ep |
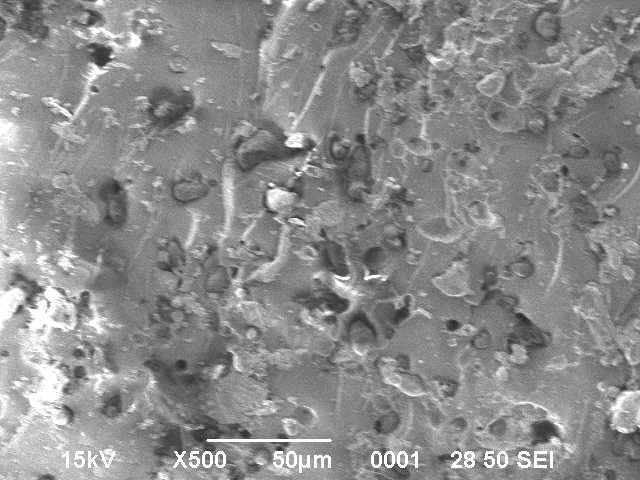 | Figure 13. SEM of fractured surfaces hybrid 5C35A-Ep |
4. Conclusions
Flexural strength of epoxy composites decreased with an increase in aluminium or copper content. The degradation of strength is more in aluminium filled epoxy. Similar trend is observed for hybrid (Al-Cu) fillers filled epoxy. Hybrid (Al-Cu) fillers of copper dominance exhibits higher strength than aluminium dominant composites. Flexural modulus of all composites increases with filler increase. Flexural modulus of aluminium filled and aluminium dominant hybrid (al-cu) fillers filled composites are higher than copper filled and copper dominated hybrid composites. Fractured surface images show even distribution of particulates at higher filler loadings and cracks are observed.
ACKNOWLEDGEMENTS
The authors thank the management of Don Bosco Institute of Technology and Raja Rajeswari College of Engineering Bangalore.
References
[1] | H. V. Ramakrishna, S. Padma Priya And S. K. Rai 2006 Utilization of Granite Powder as Filler in Epoxy Phenol Cashew Nut Shell Liquid-toughened Epoxy Resin for Impact and Compression Strength Journal of Reinforced Plastics and Composites 25 227. |
[2] | S.Ma Rapid tooling with particulate reinforced epoxy composites for low volume production SIM Tech technical reports Jan - Mar 2007 Volume 8 Number 1 11-17. |
[3] | P. V. Vasconcelos, F. J. Lino, F. W.J. van Hattum, R. J.L. Neto, "Mathematical Models for Particulate Filled and Milled Fibre Reinforced Composites", Materials Science Forum, Vols 455-456, pp. 742-745, May. 2004. |
[4] | P. L. Teh, M. Mariatti and H. M. Akil Effect of Ethanol as Diluent on the Properties of Mineral Silica Filled Epoxy Composites Journal of Composite Materials2008 42 129. |
[5] | Payam Saadati, Habibollah Baharvand*, Azam Rahimi1, and Jalil Morshedian Effect of Modified Liquid Rubber on Increasing Toughness of Epoxy Resins Iranian Polymer Journal 14 (7), 2005, 637-646. |
[6] | S. Padma Priya and S. K. Rai Studies on the Mechanical Performance of PMMA Toughened Epoxy-Silk and PC Toughened Epoxy -Silk Fabric Composites Journal of Reinforced Plastics and Composites 2006 25: 33. |
[7] | Z. Brito, G. Sachez Influence of metallic fillers on thermal and mechanical behaviour in composites of epoxy matrix composite structures 48 (2000) 79-81. |
[8] | William D. Callister Jr. Material Science and Engineering. Revised Indian edition Wiley India (P) Ltd. ISBN10: 81-265-1076-5. |
[9] | Gaurav Agarwal1, Amar Patnaik and Rajesh Kumar Sharma Thermo-mechanical properties of silicon carbide-filled chopped glass fiber-reinforced epoxy composites International Journal of Advanced Structural Engineering 2013, 5:2. |
[10] | M. N. Channapagoudra, Ajith G Joshi, Sunil Thaned, Mahantesh Patil International Journal of Innovative Research in Science, Engineering and Technology Vol. 2, Issue 11, November 2013. |
[11] | M. Sudheer, N. Karthik Madhyastha, M. Kewin Amanna, B. Jonthan, and K. Mayur Jayaprakash Mechanical and Abrasive Wear Behavior of Metal Sulphide Lubricant Filled Epoxy Composites ISRN Polymer Science Volume 2013, Article ID 242450, 8 pages. |
[12] | Erfan Suryani Abdul Rashid, Kamarshah Ariffin and Hazizan Md Akil Mechanical and Thermal Properties of Polymer Composites for Electronic Packaging Application Journal of Reinforced Plastics and Composites 2008; 27; 1573 originally published online Mar 28 2008. |
[13] | Shetty Ravindra Rama and S.K. Rai Studies on Physico mechanical properties of Fly Ash-filled Hydroxyl-terminated Polyurethane-toughened Epoxy Composites Journal of Reinforced Plastics And Composites, Vol. 29, No. 14/2010. |
[14] | Y. Ishigure, S. Iijima, H. Ito, T. Ota, H. Unuma, M. Takahashi, Y. Hikichi Electrical and Elastic properties of conductor-polymer composites. Journal of material science 34 (1999) 2979-2985. |
[15] | H. V. Ramakrishna, S. Padma Priya and S. K. Rai 2006 Utilization of Granite Powder as Filler in Epoxy Phenol Cashew Nut Shell Liquid-toughened Epoxy Resin for Impact and Compression Strength Journal of Reinforced Plastics and Composites 25 227. |
[16] | Erfan Suryani Abdul Rashid, Hazizan Md Akil Kamarshah Ariffin Chee Choong Kooi The Flexural and Morphological Properties of α-Alumina Filled Epoxy Composites Malaysian Polymer Journal (MPJ), Vol 1, No. 1, p 25-38, 2006. |