Chiranth B. P. 1, Siddaraju 2, Shobha R. 3, Poornesh K. 1
1Dept of Mechanical Engg, St. Joseph Engineering College, Mangaluru
2Dept of Mechanical Engg, M.S. Ramaiah Institute of Technology, Bengaluru
3Dept of I.E.M, M.S. Ramaiah Institute of Technology, Bengaluru
Correspondence to: Chiranth B. P. , Dept of Mechanical Engg, St. Joseph Engineering College, Mangaluru.
Email: |  |
Copyright © 2015 Scientific & Academic Publishing. All Rights Reserved.
Abstract
Equal channel angular pressing (ECAP) is an effective metal forming method to produce an ultra-fine grained structure in the metal. In the present paper sever plastic deformation (SPD) of aluminium 6% titanium boride is deformed through ECAP at a temperature of 200°C up to 4 passes by using route Bc where samples is rotated by 180° after each pass along its longitudinal axis through the die which is having an included angle of 130° Ø angle and 30° Ψ angle. Conventional extrusion was carried out for the same material to compare the mechanical properties of the ECAPed and Extruded samples. The hardness and microstructure of the alloy processed by ECAP and Extrusion were investigated. It is found that hardness increased by 61.77% compare to the as cast Aluminium 6061 alloy, 14.6% to Extruded composite and Microstructural studies showed the dendritic coarse grain structure were broken down to fine structured and grains were elongated after ECAP. But this effect of microstructure was restricted to the surface and the central region was unaffected in Extruded sample microstructure.
Keywords:
Insitu composites, Severe plastic deformation, Equal channel angular pressing, Al-TiB2
Cite this paper: Chiranth B. P. , Siddaraju , Shobha R. , Poornesh K. , Equal Channel Angular Pressing of Aluminium 6%wt Titanium Boride Composite, American Journal of Materials Science, Vol. 5 No. 3C, 2015, pp. 77-80. doi: 10.5923/c.materials.201502.16.
1. Introduction
Materials processed by severe plastic deformation have received vast focus in the research community in the last five to ten years due to unique physical and mechanical properties obtainable by SPD [1-3]. The process of SPD is based on intense plastic deformation of a work piece, resulting in alteration of the microstructure and texture, in principal reduction of the grain size to the sub-micron or the nano-metre scale [4]. Therefore, some SPD methods such as equal-channel angular pressing (ECAP), high-pressure torsion (HPT), multi-axial compression (MAC) and accumulative roll bonding (ARB) has been developed in recent years [5-6]. The most common process of SPD is the Equal channel angular pressing, which involves pressing a billet through a die consisting of two channels of equal cross sections, intersecting at an angle, typically at 90o. The process allows us to introduce very large plastic deformation to a work piece without altering the overall geometry of the work piece [10]. The application of Aluminium alloy in the field of automobile, structural applications have been increasing exponentially because of good formability, density, corrosion resistance and other properties, a literature survey reveals that a very little amount work have been done on Al-TiB2 insitu composites by using ECAP [7]. Equal channel angular pressing of Al-6%wt TiB2 was done up to 4 pass by using the route Bc which gives high-level of grain refinement among all other processing routes to break the course grain into fine grain structure which significantly increased the hardness, ultimate tensile strength and other properties. So in this study the effect of number of pass on microstructure and hardness is investigated by preparing composite under identical condition. 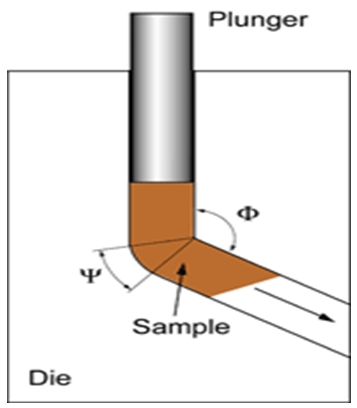 | Figure 1. Scheme of ECAP Process |
2. Experimental Material and Procedures
2.1. Materials
Aluminium-6% TiB2 composite was prepared using a stir casting technique by using Aluminium 6061 as a matrix material and TiO2, KBF4 & Na3AlF6 as a reinforcement material due to thermodynamic and kinetic reaction between the chemicals, the by product is titanium boride formation inside the matrix alloy. The Al-6% TiB2 composite thus prepared is used for further testing. To confirm the formation reinforcement XRD analysis was carried out.
2.2. ECAP and Extrusion Procedures
ECAP was done at temperature of 200°C, the sample was annealed for about an hour, then ECAP was carried out by using die which is having an included angle of 130° by using the route Bc where samples are rotated 90° after each pass for four times consecutively to create intense strain rate that can be imposed on the sample equal to is ~1 [8, 9], the sample had a diameter of 10mm & length of 65mm which is pressed by using a plunger of different length in a hydraulic press of capacity of 100 tons. After each pass the corner edge of the samples was trimmed which is not deformed. Extrusion was done at a temperature of 200°C, sample was annealed at a temperature of 200°C for a duration of one hour, the die was designed such a way that 60% reduction of the sample occurs after Extrusion Following ECAP and extrusion, samples were cut for hardness testing, samples were cut parallel to the pressing directions with a length of 10mm and diameter of 10mm after each passing. The hardness of these samples was measured by mechanically polishing and then using Rockwell hardness tester equipped with B-scale indenter. For each measurement, a load of 100kg was applied for 15s at three different locations and measurement was done.To check whether there was any breaking of the TiB2 during the ECAP, polished samples were prepared by using different grades of paper and keller’s reagent is used as a solution for etching and these samples were examined using a quantitative image analyzing facility attached to an optical microscope.
3. Result and Discussion
3.1. Hardness
The Rockwell hardness test results obtained for Al-TiB2 composite after different passes during ECAP are shown in Fig 2. It was observed that the Al-TiB2 composite that underwent 4 passes had the highest hardness value than that of the ‘as-cast’ Al-TiB2 composite (i.e. the one that did not undergo ECAP) had the lowest hardness value, the hardness value has been increased from 46.36 to 75 HRB, with increase in number of press the hardness of the composite also increases.The increase in hardness is mainly due to strain hardening and for getting equiaxed grains accompanied with gradual decrease in dislocation density [8, 9], this result shows that the behaviour (in this case hardness) of a material is improved after ECAP. [10]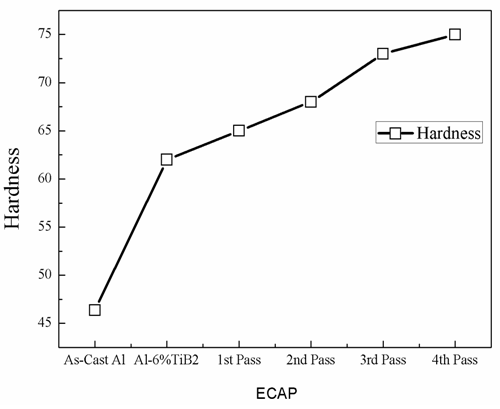 | Figure 2. Variation of hardness with number of ECAP passes |
3.2. Comparison of ECAP and Extrusion
Hardness which was obtained after Extrusion for Al-6%TiB2 is 64HRB, by comparing the result with ECAP, the Extrusion sample has hardness value 64HRB which is less by 14.6% compare to ECAPed sample and this is due to non uniformity of grain distribution and also amount of load that is required to deform the sample is more in case of extrusion compare with ECAP.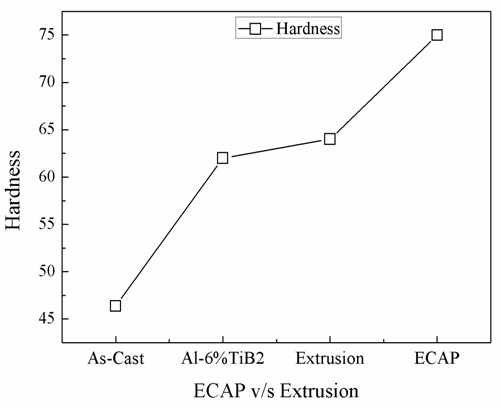 | Figure 3. Comparison of ECAP with Extrusion |
3.3. Microstructure
Optical microscope with a magnification 200X is used for microstructure studies, study reveals that with increase in number of ECAP passes the grains will elongate and leads to the formation of ultra fine grain structure, as shown in fig 4 in first pass, microstructure shows dendrites of aluminium solid solution with intermetallic particles at the inter-dendritic regions after Second ECAP pass microstructure shows coarse grains of aluminium solid solution with intermetallic particles at the grain boundary regions were found, after third ECAP pass it shows elongated grains of aluminium solid solution with intermetallic particles and after fourth ECAP pass the grains are very elongated and uniformly distributed throughout the composite.  | Figure 4(a). ECAP Pass |
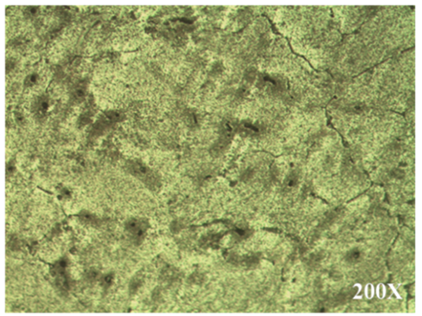 | Figure 4(b). ECAP Pass |
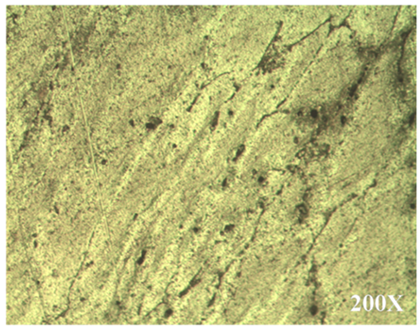 | Figure 4(c). ECAP Pass |
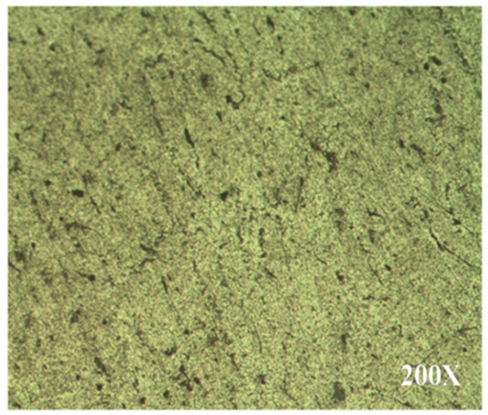 | Figure 4(d). ECAP Pass |
Fig 5 shows the microstructure of Extruded sample in that grain are severely elongated and also fine grains of aluminium solid solution with intermetallic particles could be seen at grain boundaries regions.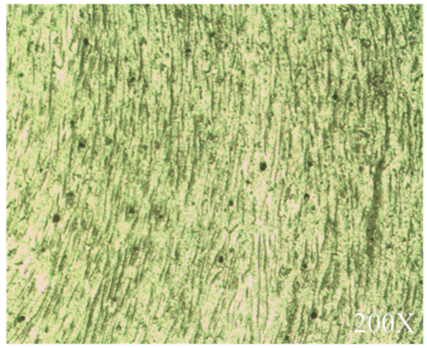 | Figure 5. Extrusion |
4. Conclusions
Al-6%wt TiB2 was successfully produced using a stir casting insitu technique.ECAP was done at a temperature of 200°C up to 4 passes by using the route Bc. Conventional extrusion was done for the same sample to compare the different forming methods.Exponential increase in hardness from 46.36 HRB (As-cast 6061) to 75 HRB in case of ECAP and 46.36 HRB to 64 HRB in case of Extrusion Microstructure shows that grains were elongated after ECAP.Results show that ECAP is better than Conventional Extrusion forming method.
ACKNOWLEDGEMENTS
The authors would like to thank their corresponding managements for allowing us to carry out the work and for their motivation.
References
[1] | J. Zrnik, S. V. Dobatkin, I. Mamuzi, 2008, Processing Of Metals By Severe Plastic Deformation (Spd) – Structure And Mechanical Properties Respond, Metabk 47(3), 211-216. |
[2] | W.J. Kim, S.I. Hong, Y.S. Kim, S.H. Min, H.T. Jeong, J.D. Lee, 2003, Texture development and its effect on mechanical properties of an AZ61 Mg alloy fabricated by equal channel angular pressing, Acta Materialia, 51, 3293. |
[3] | Shobha R, K R Suresh, H B Niranjan and K G Sathyanarayana, 2013, Achieving enhanced mechanical properties and analysis of chemical kinetics of the in-situ reaction in an al – Tib2 in-situ composite”, International Journal of Material and Manufacturing Technology, 129-131, 1385- 1388. |
[4] | Shobha R, K R Suresh, H B Niranjan and C Siddaraju, 2014, Mechanical and Microstructure Evaluation of Insitu Aluminum Titanium Boride Composites Processed by Severe Plastic Deformation, 5, 281 – 288. |
[5] | X.D.H. Shin, I. Kim, J. Kim, Y.S. Kim, S.L. Semiatin,2003, Microstructure development during equal-channel angular pressing of titanium, Acta Materialia, 51, 983–996. |
[6] | Kim H.S, 2001, Finite element analysis of ECAP using a round corner die, Material Science & Engineering. A, 315, 122-128. |
[7] | K.R. Ravi, M. Saravanan, R.M. Pillai, A. Madal, B.S. Murthy, M. Chakraborty, B.C. Pai, 2008, Equal channel angular pressing of Al-5%wt TiB2 in situ composites, Journal of Alloys and Compounds, 459, Issues 1–2, 239–243. |
[8] | Y. Iwhashi, J. Wang, Horita, M. Nemoto and T.G. Langdon, 1996, Principle of equal-channel angular pressing for the processing of ultra-fine grained materials”, Scripta Materialia 35 (2), 143-146. |
[9] | Ferrasse S., Hartwig T., Goforth R.E., Segal V.M., 1997, Microstructure and properties of copper and aluminum alloy 3003 heavily worked by equal channel angular extrusion, Metallurgical and Materials Transactions A, (1997), 28A, 1047-1057. |
[10] | M Saravanan, R M Pillai, B C Pai, M Brahmakumar, K R Ravi, 2006, Equal channel angular pressing of pure aluminium—an analysis, Bulletin of Materials Science, 29(7), 679–684. |