T. S. Shanon 1, N. Ahmed 1, M. Bharath 1, J. Valder 2, M. Rijesh 3
1Department of Metallurgical and Materials Engineering, National Institute of Technology Surathkal, Karnataka
2Department of Mechanical Engineering, St. Joseph Engineering College, Mangalore, Karnataka
3Department of Metallurgy, Amal Jyothi College of Engineering, Koovapally, Kanjirapally, Kerala
Correspondence to: J. Valder , Department of Mechanical Engineering, St. Joseph Engineering College, Mangalore, Karnataka.
Email: |  |
Copyright © 2015 Scientific & Academic Publishing. All Rights Reserved.
Abstract
Equal Channel Angular Pressing (ECAP) has attracted much attention from the material community, because of its ability to produce ultrafine grained microstructures. The advantage in ECAP is that a large amount of strain can be imposed on the material without a significant change in geometric shape or cross section. In the present work, the effect of ECAP on the ageing of aluminum 6063 alloy was studied. The samples were first solutionized, followed by ECAP and were then aged at a temperature of 175°C. Multipass pressings were conducted on the billets for different processing routes such as routes- A, BA, BC and C. The pressings were performed at room temperature using a die having a channel angle of 150°. Post ECAP ageing was found to reduce the ageing time considerably till three passes.
Keywords:
ECAP, Hardness, Route, Ageing, Strain
Cite this paper: T. S. Shanon , N. Ahmed , M. Bharath , J. Valder , M. Rijesh , Post-ECAP Ageing Treatment of Aluminum 6063 Alloy, American Journal of Materials Science, Vol. 5 No. 3C, 2015, pp. 74-76. doi: 10.5923/c.materials.201502.15.
1. Introduction
The effective post ECAP strengthening through low temperature ageing was linked to higher dislocation accumulation rate in the solutionized matrix, avoidance of fragmentation of precipitates in the pre ECAP peak aged alloy after few passes of ECAP, suppression of recovery by precipitation on the sub structure after ECAP and reduction of ageing temperature and accelerated ageing kinetics at low temperatures induced by a high dislocation density [1].Ageing of 6082 alloy after severe plastic deformation revealed that a proper combination of grain-refinement strengthening and age-hardening can be fully exploited in solution annealed ultra fine grained (UFG) alloys only when isothermal ageing is performed at temperatures significantly lower than conventional values and for shorter periods. Ageing conditions have found to be tailored to specific amount of strain imparted during severe plastic deformation (SPD) and to alloy composition [2].Micro-hardness evaluation as a function of ageing time can be used to study the effect of ECAP passes on the kinetics of isothermal ageing. It was found that even a single ECAP pass significantly accelerates the ageing kinetics of 6082 alloy. Ageing revealed to be more effective at 130°C rather than at 160°C and 180°C by virtue of the comparatively slower kinetics and of the limited over-ageing effects. The improvement in hardness achieved after optimised post-ECAP ageing was significant for the samples subjected to a limited amount of plastic strain but became negligible after a relatively large number of ECAP passes [3]. So the present study is carried out to know the effect of post ageing on 6063 aluminium alloy processed by ECAP by various routes at 175°C.
2. Experimental Details
The material used in this work was 6063 aluminium alloy with the composition given in Table 1. The experiments were carried out using samples machined to size of 20 mm radius and 60 mm height which was solutionized at 525°C for 1.5h. The die angles of ø: 150° and
30° were chosen for ECAP. The schematic diagram of ECAP process is shown in Figure 1 [4]. The pressings were carried out by route A, BA, BC and C up to three numbers of passes at room temperature. The four different processing routes are summarized schematically in Figure 2 [5]. After each pass the samples were cut into 8 equal sections for ageing and hardness studies. The ageing treatment was carried out at 175°C for different times. The hardness was measured before and after respective ageing treatments.Table 1. Composition of Al 6063 alloy  |
| |
|
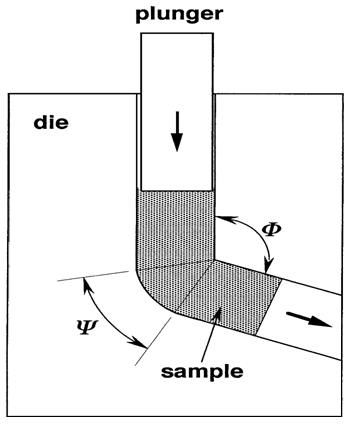 | Figure 1. The schematic diagram of ECAP process |
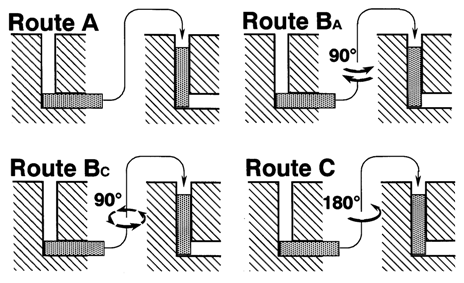 | Figure 2. The four fundamental processing routes in ECAP |
3. Results and Discussion
The hardness testing conducted on the samples (before ECAP) aged for durations between 1 and 8 hours, gave a peak hardness value of 96 BHN between 6 and 8 hours. The hardness profile of the samples processed by first pass showed that the peak hardness was obtained between 1 and 3 hours of ageing, clearly indicating that ECAP reduced the ageing time. Peak hardness of 82 BHN was obtained, following which there was a constant drop in the hardness indicating over ageing, as shown in figure 3. The phenomena of sharp drop in ageing time can primarily be explained by the large amount of strains in the sample after ECAP. Strain produces new dislocations in the matrix which is the driving force for recovery [6]. Moreover, the dislocations act as short-circuit paths for the solutes and facilitate the atomic migrations. This in turn decreases the activation energy for the growth of precipitates and enhances the aging kinetics after ECAP [7, 8] and subsequently decreases the time at which the maximum hardness is achieved.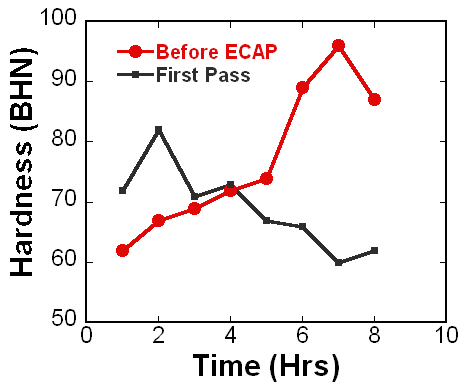 | Figure 3. Variation of Hardness with ageing time is seen before and after ECAP |
From the figure 4 & 5, it can be seen that the highest hardness after second and third pass is achieved for pass BC . This is because, in route BC, where the sub grain boundaries evolve most rapidly into high angle grain boundaries, the two shearing directions lie on planes which intersect at 150°.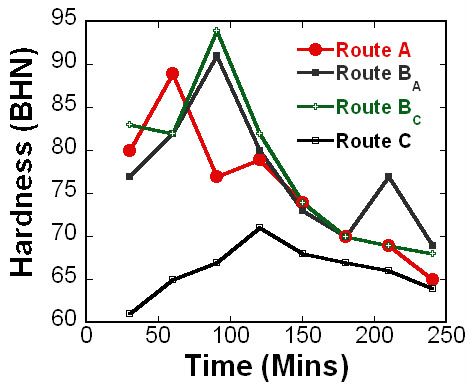 | Figure 4. Variation of Hardness with ageing time for the 4 different routes after second pass |
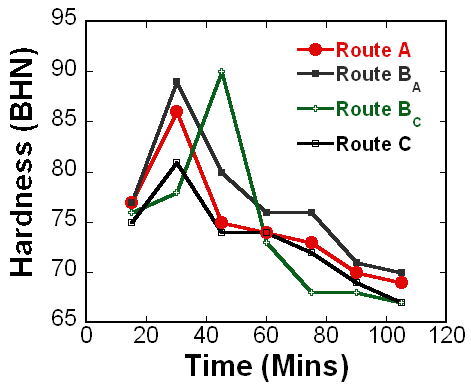 | Figure 5. Variation of Hardness with ageing time for 4 different routes after third pass |
As a result of this duality in the shearing directions, sub grain bands are developed on repetitive pressings along two separate and intersecting sets of planes and this leads rapidly to an evolution in the boundary structure into a reasonably equiaxed array of high angle grain boundaries. The second highest hardness is for BA in both cases. Both BA and BC show similar hardness and peak ageing time values in both passes as they undergo the same treatment till this stage.Route A shows a slightly lesser hardness while Route C is the least. This is because in Route C, the shear continues on the same plane in each consecutive passage through the die but the direction of shear is reversed on each pass. Thus, route C is termed a redundant strain process and the strain is restored after every even number of passes. Out of 4 samples subjected to the third pass, one for each route, severe deformation caused cracking in all cases except Route C. So the subsequent ECAP passes were not possible. The increase in punch pressure from first pass to third pass is from 85 N/mm2 to 110 N/mm2 which is because of the higher die angle chosen for the ECAP. The increase in punch pressure with progressive passes was much lower than for low die angles. While ECAP done using a die angle of 900 can drastically decrease the peak ageing time within one pass, the die is subjected to very high stresses. This can cause rapid wear of the die and reduces its service life. Therefore, it is more advantageous to use a high die angle of 150° which extends the life of the equipment used and hence reduces cost.
4. Conclusions
Peak ageing time was significantly reduced from 6-8 hours before ECAP to 1-3 hours after first pass, 1 hour after second pass and 15-30 minutes after third pass for all the routes.Maximum hardness was observed for Route BC, followed by Route BA, Route A and Route C for second and third pass.
ACKNOWLEDGEMENTS
The authors deeply acknowledge Mr Vijeesh V Assistant Professor, AJCE for taking the pain of proof reading this article.
References
[1] | J.K. Kim, H.G. Jeong, S.I. Hong, Y.S. Kim and W.J. Kim, 2001, Effect of aging treatment on heavily deformed microstructure of a 6061 aluminum alloy after equal channel angular pressing, Scripta Mater. 45, pp. 901-907. |
[2] | S. Farè, N. Lecis, and M. Vedani, “Aging Behaviour of Al-Mg-Si Alloys Subjected to Severe Plastic Deformation by ECAP and Cold Asymmetric Rolling,” Journal of Metallurgy, vol. 2011, Article ID 959643, 8 pages, 2011. doi:10.1155/2011/959643. |
[3] | Giuliano Angella, Paola Bassani, Ausonio Tuissi and Maurizio Vedani, 2004, Behaviour and Mechanical Properties of a Solution Treated and ECAP Processed 6082 Alloy, Materials Transactions, Vol. 45, No. 7, pp. 2282-2287. |
[4] | Tjong S.C., Haydn Chen (2004), “Nanocrystalline materials and coatings” Materials Science and Engineering R, Vol.45, Issues 1–2, 30, 1–88. |
[5] | Nakashima Kiyotaka, Zenji Horita, Minoru Nemoto and Terence G. Langdon (2000), “Development of a multi-pass facility for equal-channel angular pressing to high total strains”, Materials Science and Engineering A, Vol.281 (1-2), 82–87. |
[6] | G.E. Dieter, in: S.I. Metric (Ed.), 1988, Mechanical Metallurgy, McGraw-Hill Book Co., New York. |
[7] | S. Dadbakhsh, A. Karimi Taheri, 2010, Study on static strain aging of 6082 aluminium alloy, Mater. Sci. Technol. 26, 169–175. |
[8] | R.S. Yassar, D.P. Field, H. Weiland, 2005, Effect of Cold Deformation on the Kinetics of the Precipitates in an Al-Mg-Si Alloy, Metall. Mater. Trans. 36A, 2059–2065. |