T. N. Praveen Kumar 1, N. Suresh 1, S. Venkateswaran 2, S. Seetharamu 3
1Department of ME, BMS Institute of Technology, Bengaluru, India
2BMS Evening College of Engineering, Bengaluru, India
3Central Power Research Institute, Bengaluru, India
Correspondence to: T. N. Praveen Kumar , Department of ME, BMS Institute of Technology, Bengaluru, India.
Email: |  |
Copyright © 2015 Scientific & Academic Publishing. All Rights Reserved.
Abstract
Metallic foams belong to cellular solid structure consisting of gas filled pores. Foamed materials are a family of new materials with unique characteristics. Aluminium foams have become popular because of their properties such as high stiffness combined with very low density. There are two types of foams i.e., open or closed cell. Aluminium foams are being used in many applications like automobiles, railways, aerospace, ship building, household applications etc. Metallic foams are commonly produced using hydride and carbonate foaming agents. However carbonate foaming agents are safer to handle than hydrides and are easily available and enable aluminum foam to be produced at low cost with a fine, homogenous cell structure, low cost and easily available. The present work deals with the effect of grain size of the calcium carbonate forming agent on the physical properties and mechanical properties of an eutectic Al-Si alloy closed cell foam. The foam was produced with different grain size of calcium carbonate (150µm, 106µm, 75µm and 53µm) as a foaming agent. The pores per inch, density, relative density and compressive strength of the eutectic Al-Si alloy closed cell foam produced with different grain size of calcium carbonates as foaming agent were determined. Relative density was in the range of 0.33 to 0.54, pores per inch were in the range of 10.75 to 15.5, compression strength in the range of 7.82MPa to 11.72MPa. It is observed that as grain size of calcium carbonate used for production of aluminium foam increases, the number of pores per inch decreases, relative density decreases, compression strength decreases and porosity increases.
Keywords:
Keyword Eutectic Al-Si alloy foam, Calcium carbonates, Foaming process, Compressive strength
Cite this paper: T. N. Praveen Kumar , N. Suresh , S. Venkateswaran , S. Seetharamu , Effect of Grain Size of Calcium Carbonate Foaming Agent on Compressive Strength of Eutectic Al-Si Alloy Closed Cell Foam, American Journal of Materials Science, Vol. 5 No. 3C, 2015, pp. 69-73. doi: 10.5923/c.materials.201502.14.
1. Introduction
Metallic foams are known for their interesting combinations of physical and mechanical properties such as high compression strength combined with good energy absorption characteristics [1]. If the solid of which the foam is made is contained in the cell edges only, i.e. cells are connected through open faces, the foam is said to open-celled. If each cell is sealed off from its neighbors, it is said to be closed-celled foam [2]. Metallic melt can be foamed by creating gas bubbles in the liquid provided that the melt has been prepared such that the emerging foam is fairly stable during processing. This can be done by adding fine ceramic powders or alloying elements to the melt which form stabilizing particle, or by other means [3]. Closed cell foams can be produced by i) Bubbling gas through molten Al-SiC or Al-Al2O3 alloys ii) By stirring a foaming agent (typically TiH2) into a molten alloy iii) Consolidation of a metal powder with a particulate foaming agent (TiH2) followed by heating into the mushy state when the foaming agent releases hydrogen, expanding the material [4]. Aluminium foams synthesized with CaCO3 powder as a blowing agent can be prepared by both powder metallurgy and melt route. The properties of aluminium foam significantly depend on its porosity, so that a desired property can be tailored by controlling the foam density [5]. The foams can be produced by CaCO3 having appreciably finer cells and more uniform cell structures than currently available melt route foams. The decomposition characteristics of CaCO3 is well suited to foaming of aluminium melts [6]. The relative high dispersion of aluminium foam properties is often caused by the use of samples manufactured in small series, which do not allow keeping the foaming parameter constant. The aluminium foam of similar density can exhibit a wide dispersion of properties due to the various defects, such as gradient density distribution, surface skin, preferred pore orientation, etc. These effects result from the foaming process and significantly depend on the geometry of foamed part [7]. The calcium carbonate foaming agent has a significant effect on foam stability due to oxidation of the melt by CO2 gas [8].Uniaxial compressive tests are best performed on prismatic or cylindrical specimens of foam with a height-to-thickness ratio exceeding 1.5. The minimum dimension of the specimen should at least seven times the cell size to avoid size effects. The compressive strength of the foam is taken to be the initial peak stress if there is one; otherwise, it is taken to be the stress at the intersection of two slopes: that of the initial loading and that for stress plateau. Variation in the microstructure and cell wall properties of some present day foams gives rise to variability in the measured mechanical properties [4]. Depending on the type of alloy of which foam is made, the cells suffer brittle fracture, deform plastically without breaking, or show an even more complicated deformation pattern. Metal foams collapse gradually under the critical compressive load until a high degree of compaction is achieved. That process absorbs a great deal of mechanical energy. Metal foam has a high yield stress compared to polymer foams [9]. In the present work, eutectic Al-Si closed cell foam has been produced using CaCO3 as a foaming agent by melt route. From an application point of view, the main concern is to control the size of the pore, porosity level and foam structure, which affect the physical and mechanical properties of the foam. Hence, in this work, effect of grain size on mechanical properties of closed cell aluminium foam was studied.
2. Methodology Adopted
2.1. Material Used
Aluminum alloy chosen for production of the foam is eutectic aluminium silicon alloy because of its good flowability and calcium carbonate was used as a foaming agent. The composition of the alloy used in wt.% was Silicon11.8, Iron 0.32, Copper 0.002, Manganese 0.62, Magnesium 0.065, Zn 0.021and the remainder being aluminum.
2.2. Production of Foam
The eutectic aluminium silicon alloy was weighed and melted in a graphite crucible by using an electric resistance furnace. Molten metal temperature is measured using thermocouple. When the melt temperature reached around 700°C, melt was stirred at 400rpm to 500rpm with stainless steel stirrer for about 30-50 seconds. Required grain size of calcium carbonate of 3% by weight was added into the molten metal while stirring. The stirring was continued for two to three minutes till the foaming agent was distributed uniformly with 200 to 400rpm. All mixing process was carried out in the furnace around 730°C. The crucible was kept about 3-5 minutes in the furnace until it completes the foaming process. Then the crucible was taken out from the furnace, the foam was cooled in ambient air. Graphite crucible was used as it suited the temperature range also it has self-lubricating properties which facilitates easy removal of metal once it has foamed and cooled down. The cut section of the foam produced with different grain sizes of calcium carbonate is shown in figure 1.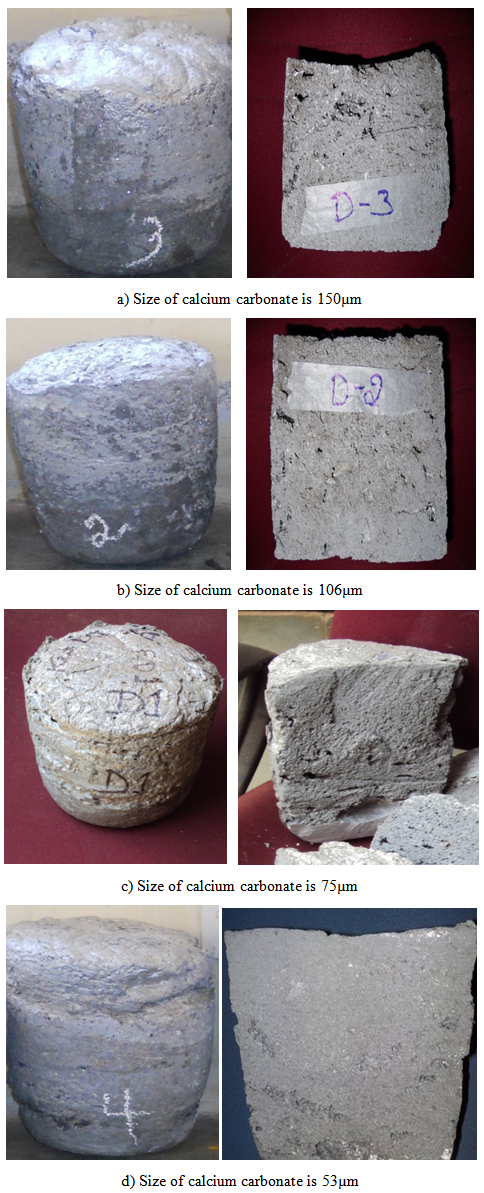 | Figure 1. Foam casting and its cut section |
The decomposition of CaCO3 is usually described by the reaction
It was reported that te thermal decomposition of pure calcium carbonate is at a temperature of about 900°C, but when calcium carbonate is in contact with the molten metal, it decomposes at temperatures above 700°C. The overall chemical reaction is complex, consisting of several successive reactions which lead to the formation of various solid (CaO, Al2O3, Al4C3) and gaseous phases (CO2, CO) [5].
2.3. Density of the Foam
Volume of specimen is calculated from its dimensions. The density was calculated by dividing the sample weight over its volume. The cast foam was cut. Specimens for compression testing were prepared from cast foam and individually weighed and measured in order to calculate the actual and relative densities before testing.The relative density, ρ*, is calculated as:-
where f and m refer to the foam and metal used for producing foam respectively[10].
2.4. Compression Testing
Compressive strength is determined for foam produced with 53µm, 75µm, 106µm and 150µm. The choice of specimen size was based on the premise that valid test requires about 10 cells per side [11]. The specimen dimension chosen is 30mm×30mm×45mm. All compression tests were performed at room temperature by using a Electronic Universal Testing Machine UTM-Hydraulic type, FIE make, 40 tonnes capacity. The size of the Aluminium foam sample used for this study is 30mm×30mm×45mm. The surface skin of the samples was removed during the preparation of the samples. The density was calculated from the weight and volume of samples.Specimen was placed on the bottom ram of the machine and load was applied. The foam specimen was deformed between the two circular compression platens of Universal Testing Machine. It was reported that due to stress concentration caused by defects in the cellular structure of the aluminium foams, a small amount of plastic deformation can occur even at a very low stress level [12]. In all of compression testing, load and displacement were recorded from the digital indicator of the machine. The compressive strength (plastic collapse stress) was calculated from the initial peak load on the specimen i.e. initial peak stress.The experimentally measured values of compression force F(N) and deformation L(mm) were evaluated [13] as follows:The collapse stress σ was calculated from the force F[N] using an apparent cross sectional area A[mm2] of the specimen:
The foam sample before compression and after compression is shown in figure 2.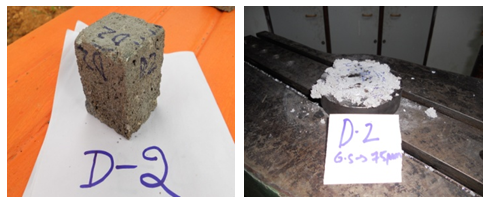 | Figure 2. Compression test specimen and specimen after compression |
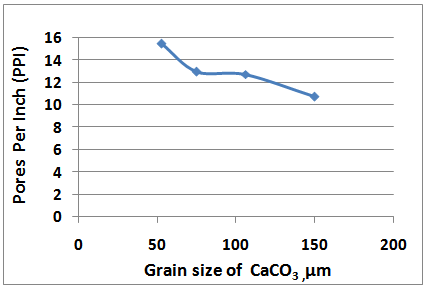 | Figure 3. Plot of grain size verses pores per inch |
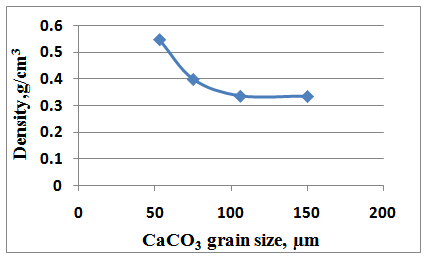 | Figure 4. Plot of grain size versus density |
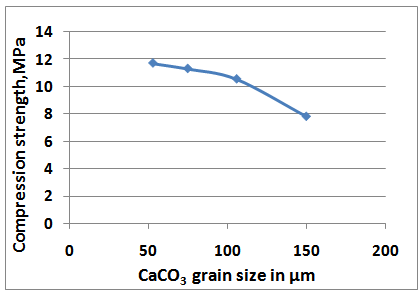 | Figure 5. Plot of grain size verses compression strength |
3. Results
Pores per inch of the foam were measured along vertical (foaming direction) and horizontal direction of cut section and then the average number of pores per inch was calculated. The density, relative density and porosity were calculated. Pores per inch, density, relative density and porosity of the foam produced with different grain sizes of CaCO3 are tabulated in Table 1.Table 1. Grain size and other physical properties 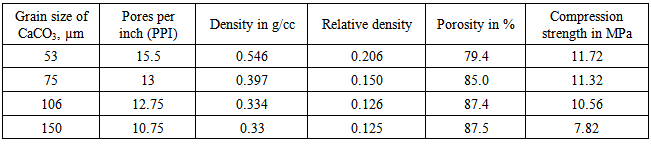 |
| |
|
It was reported that there are two basic deformation mechanisms that depend on the types of used aluminium alloy: cast aluminium alloys exhibit brittle failure of the cell–walls already at low strains. Failure of the cell-walls leads to the multiple stress drops and thus to the uneven stress/strain curve in plateau region. The magnitude of first stress drop depends on the average pore size [14]. It is observed from the table-1 that, compressive strength increase as average pores per inch increase (PPI). The compression strength increases as the density of the foam increases as shown in the table-1 and was also reported by J Banhart [15]. The compressive strength is also function of relative density [10], it is observed that as relative density increase, compressive strength also increases.
4. Conclusions
In the present work, Eutectic Al-Si alloy closed cell foam was produced with calcium carbonate foaming agent of different grain sizes (53µm, 75µm, 106µm and 150µm). The compression strengths were determined for different samples produced from different grain sizes of calcium carbonate. The pores per inch, porosity, relative density were calculated. It is observed that as the grain size of calcium carbonate foaming agent used for production of aluminium foam increases, density and relative density decreases, porosity increases and compressive strength decreases. It is also observed that compressive strength of the foam is a function of size of calcium carbonate used for production of aluminium foam and higher the densities lead to higher compression strength. The results indicate that the density of the foam produced was in the range of 0.33g/cc to 0.546g/cc and compression strength was between 7.82MPa to 11.72MPa.
ACKNOWLEDGMENTS
The authors would like to thank and acknowledge Visvesvaraya Technological University, Belagavi, Karnataka, India, for the financial support for this Project, under University Research Grant Scheme [Ref. No. VTU/Aca./2009-10/A-9/11476, Dated: 02-01-2010].
References
[1] | M.C. Gui, D.B. Wang, J.J. Wu, G.J. Yuan, C.G. Li, Deformation and damping behaviour of foamed Al-Si-SiCp composite, Material Science & Engineering A286(2000) 282-288. |
[2] | Lorna J. Gibson, Michel F. Ashby, Cellular Solids, Structure and properties, Second Edition, Cambridge University Press, August 1999. |
[3] | John Banhart, Aluminium foams for lighter vehicles, Int. J. Vehicle Design, Vol. 37, Nos.2/3, 2005. |
[4] | Ashby, A.G. Evans, N.A. Fleck, L.J. Gibson, J.W. Metal Foams: A Design Guide, M.F. Hutchinson and H.N.G. Wadley, Butterworth Heinemann, 2000. |
[5] | Varuzan Kevorkijan, Low cost aluminium foams made by CaCO3 particulates, Scientific paper, UDC:549.74.621.762, Association of Metallurgical Engineers of Serbia AMS, MJoM Vol 16(3), 2010, 205-219. |
[6] | V. Gergely, D.C. Curran, T.W. Clyne, The FOAMCARP process: foaming of aluminum MMCs by the chalk-aluminum reaction in precursors, Composite Science and Technology 63, (2003) 2301-2310. |
[7] | F. Simansick, Reproducibility of aluminum foam properties, International conference on Metal Foams and Porous Structures, 14-16, June-1999, Bremen, Eds. J.Banhart, M.F. Asby, N.A. Fleck, MIT Publishing, Bremen, 235-240. |
[8] | Aleksandra V. Byakova1, Svyatoslav V. Gnyloskurenko, Alexander. Sirko, Yuliy V. Milman and Takashi Nakamura, The Role of Foaming Agent in Structure and Mechanical Performance of Al Based Foams, Materials Transactions, Vol. 47, No.9, (2006), pp.2131 to 2136. |
[9] | John Banhart, Denis Weaire, On the Road Again: Metal Foams Find Favor, July 2002, Physics Today, 37-429. |
[10] | I. W. Hall, M. Guden and C.-J. Yu, Crushing of aluminum closed cell foams: density and strain rate effects, Scripta Materialia, 43(2000)515-521. |
[11] | Y. Sugimura, J. Meyer, M.Y. He, H.Bart-Smith, J. Grensted And A.G. Evans, On the Mechanical Performance of Closed Cell Al alloy Foams, Acta Materialia, Vol.45, No.12, 5245-5259, 1997. |
[12] | Xinzhu Wang and Guangtao Zhou, The static compressive behaviour of aluminium foam, Reviews on Advanced Material Science 33(2013)316-312. |
[13] | R. Florek, F. Simancik, M. Nosko, J. Harnuskova, Compression Test Evaluation Method for Aluminium Foam Parts of Different Alloys and Densities, Powder Metallurgy Progress, Volume 10(2010), No.4. |
[14] | Fransek Simoncik, Jaroslav Kovacik, Natalia Minarikova, Deformation and Fracture Mechanism of aluminium Foams, Metfoam Conference, 1998, www. metfoam.net. |
[15] | J. Banhart, J. Baumeister, ‘Deformation characteristics of metal foams’, Journal of Material Science 33(1998) 1431-1440. |