Arun Augustin , K. Rajendra Udupa , Udaya Bhat K.
Department of Metallurgical and Materials Engineering, National Institute of Technology Karnataka, Mangalore, India
Correspondence to: Udaya Bhat K. , Department of Metallurgical and Materials Engineering, National Institute of Technology Karnataka, Mangalore, India.
Email: |  |
Copyright © 2015 Scientific & Academic Publishing. All Rights Reserved.
Abstract
Adhesion strength of the coating to substrate determine its applicability in real time engineering. Antimicrobial copper coated touch surface has been prepared by DC magnetron sputtering on zincated and non-zincated aluminium substrate. The adhesion strength of both types of sample has been measured by pull-off adhesion tester and shows that zincated surface is 15 times better than non-zincated one. XRD characterization indicates that by zincating, the tendency for copper alignment could be reduced. SEM studies indicate that the copper crystallites on zincated substrate are predominantly in the range of 125-200 nm whereas in the case of non-zincated substrate, it is in the range of 40-60 nm. Contact angle studies showed that the wettability of copper coated on non-zincated Al is more compared to copper coated on zincated aluminium.
Keywords:
DC magnetron sputtering, Copper thin film, Adhesion strength
Cite this paper: Arun Augustin , K. Rajendra Udupa , Udaya Bhat K. , Effect of Pre-Zinc Coating on the Properties and Structure of DC Magnetron Sputtered Copper Thin Film on Aluminium, American Journal of Materials Science, Vol. 5 No. 3C, 2015, pp. 58-61. doi: 10.5923/c.materials.201502.12.
1. Introduction
Copper coated touch surface is getting a significant role in the health sector due to its proven antimicrobial action during hospital acquired infection. Studies have shown that healthcare associated infections cause a major economic loss in the GDP [1]. From economic point of view, copper coated item is cheaper compared to identical item produced from bulk copper. Copper coating can be given by various techniques and DC magnetron sputtering is one important route. Coatings through DC magnetron sputtering route offers the benefit of uniform and homogenous coatings over a large area. It offers much better functional properties than the thicker coatings produced by other coating techniques [2]. Moreover, the properties of the thin film could be tuned by varying deposition parameters. Hence, copper coating by DC magnetron sputtering on aluminium health care related systems can give better antimicrobial properties than alumnium item or may be better than bulk copper. But the challenge in engineering systems is to improve adhesive strength of the coating on aluminium. Durability of the coating in real time engineering applications is affected by limited value of adhesive strength between coated copper and substrate aluminium. During the deposition of copper thin film directly on aluminium, there is a large drop in adhesive strength due to the presence of oxide layer on the aluminium [3]. This may be due to the large lattice mismatching between ceramic aluminium oxide and metallic copper. The aluminium oxide can be easily replaced by zinc by double zincation process [4]. It is reported that double zincation gives better surface finish as compared to single zincation [5]. In this investigation, the effect of replacement of aluminium oxide with zinc on adhesive strength, coating morphology and wettability of DC magnetron sputtered coating was investigated and compared with copper thin film deposited on non- zincated substrate.
2. Experiments
The commercial pure aluminium samples of 70 mm x 25 mm x 1 mm size were polished by using 1/0, 2/0, 3/0, and 4/0 emery papers and followed by diamond paste. The polished surface was degreased using trichloroethylene using ultrasonic cleaner for 10 minutes. The surface roughness was measured by using stylus profilometer (Mitutoyo SJ301), with a resolution of 0.02 μm and confirmed that the surface is smooth with Ra=0.08 μm for all samples. The half of the polished area on the sample was double zincated by dipping twice in the bath containing zinc oxide (100 g/l), sodium hydroxide (525 g/l), ferric chloride (1 g/l) and Rochelle salt (10 g/l) for 1 minute duration [6]. During zincate process, the natural oxide layer on the Al is removed and the surface is activated. A thin intermediate layer is deposited and it improves adherence of the next layer. The double zincated and non-zincated aluminium surfaces were coated with copper using DC magnetron sputtering system (VR Technology, India). The 99.99% pure copper was used as target. The sputtering chamber with sample is shown schematically in Figure 1. Half of the aluminium substrate was zincated so that the same coating environment could be ensured for both zincated and non-zincated substrates. The sputtering was done for 20 minutes duration at room temperature with a substrate rotation speed of 100 rpm. The argon pressure was 17mL/min, initial pressure was 5x10-5 mbar and working pressure was 0.012 mbar. The sputtering power was maintained as 75 W throughout the experiment.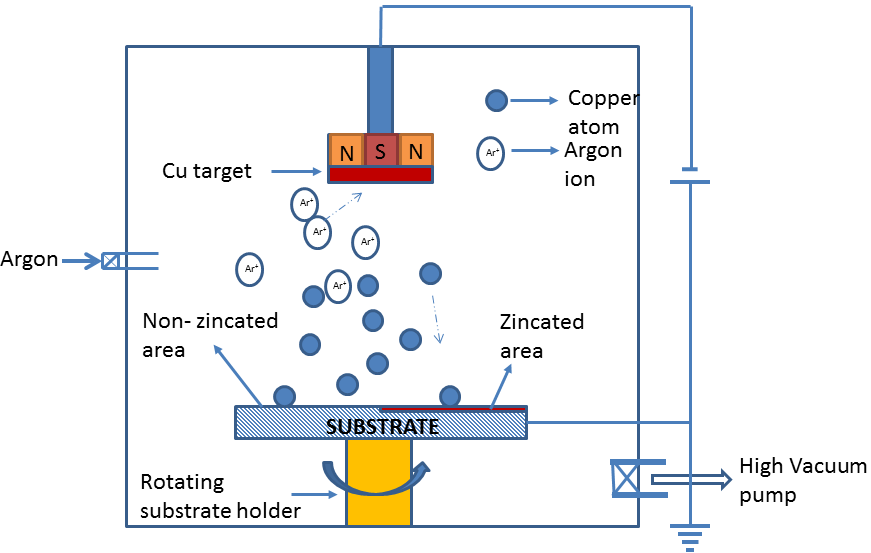 | Figure 1. Schematic representation of sputtering chamber with a sample |
The adhesive strength between the substrate and coating was tested as per ASTM D4541, with a pull-off-adhesion tester (Positest AT, DeFelsko make). A 20 mm diameter aluminium dolly with loading rate of 0.3 MPa/second is used for testing the adhesion strength. Epoxy patch adhesive (Loctite 907 Hysol) is used to fix the dolly on the coated samples. The crystal structure of the coating was analysed by using X-ray diffractometer (XRD, Model JDX-8P, JEOL make) using Cu Kα (λ= 1.5406 Å) radiation with a scanning speed of 2 degree/min and 0.02 degree step size. Secondary electron images of copper coated samples on zincated as well as non-zincated substrates were taken by using scanning electron microscope (SEM, Model JSM-6380 LA, JEOL make) and field emission scanning electron microscope (FESEM, Model Ultra 55, ZEISS make). The contact angle and spreading rate of double distilled water for 500 seconds were measured on both types of samples using FTA 200 equipment with the help of a flexible video system attached to the equipment.
3. Results and Discussion
3.1. Adhesion Strength Analysis
The adhesion strength of the copper thin film deposited on non-zincated and zincated aluminium substrate was analysed by pull-off adhesion method. The detachment of copper film in the double zincated sample was at the interface of copper to zinc. Whereas in non-zincated one, copper got detached easily in Cu-Al2O3 interface (shown in Figure 2). Images in Figure 2 clearly show that copper coating is partially detached from substrate in zincated one, whereas on non-zincated sample, coating is completely removed. The adhesion strength values measured by pull-off adhesion tester for non-zincated and zincated substrates are tabulated in Table 1.Table 1. Adhesion strength values of copper thin films with the substrate  |
| |
|
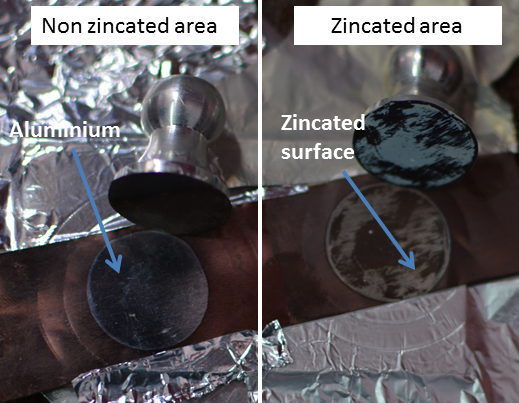 | Figure 2. Pull-off adhesion tested samples with non-zincated and zincated aluminium substrates. Corresponding dolly is also visible |
The low value of adhesion strength obtained in non-zincated system compared to zincated system can be explained using change in the interaction. In the case of non-zincated system, the interaction at the interface is physical interaction, whereas, in zincated system, the interaction is chemical interaction [7]. In non-zincated system, the surface of the Al substrate is covered by a thin passive layer of Al2O3. The adhesive strength of the substrate-copper interface is dictated by the strength of the metal (Cu)-ceramic (Al2O3) bonding. The strength is indicated in terms of work of adhesion. Opposite of this value is the work required to separate the interface in to two free surfaces. When Al is exposed to environment, a thin scale of Al2O3 form rapidly on the surface. Al-O network in the Al2O3 scale is highly saturated and this interaction is a strong interaction. When Cu is added to a saturated Al2O3 film, the interaction is extremely poor. In many cases, the interaction is due to van der Waal’s interaction and in some other cases; there may be additional physical locking due to surface roughness. Added to that Cu is a metal without much affinity for oxygen. Also, the lattice mismatch between Al2O3 and copper is around 13%. All these factors increase energy of the interface or reduce adhesive strength. In the case of zincated aluminium substrate, the aluminium oxide is replaced by thin metallic zinc layer during ion exchange reaction, due to zincating step [4]. As a result Zn-Al strong bond is formed. On zinc layer, copper is deposited. Since, three layers involved are metallic ones the interaction between them is chemical in nature. Chemical interaction is due to primary bonds and hence the adhesive strength is at least one order higher than that in metal-ceramic combination [7].
3.2. XRD Analysis
Figure 3 shows the x-ray diffraction patterns of copper thin film on non-zincated aluminium surface and zincated aluminium surface. The non-zincated aluminium surface shows preferred growth in (111) direction. Whereas, for zincated aluminium substrate, peaks corresponding to (111) and (200) are observed. The FWHM of the peak corresponding to (111) for copper at 43.316° is increased from 0.3085 degree (in non-zincated substrate) to 0.5535 degree (in zincated system). This is attributed to finer crystallite size and microstrain of the copper thin film [8]. The major peak of the zinc corresponding to (101) at 43.22° is merged with copper peak at 43.31° also causes the widening of copper peak.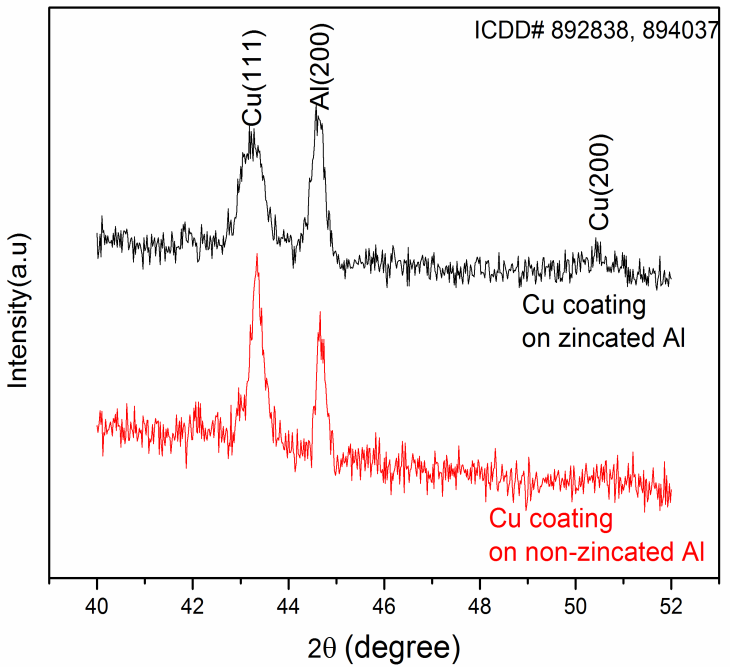 | Figure 3. XRD patterns of copper thin film on zincated and non-zincated aluminium substrates |
3.3. Scanning Electron Microscopic Study
Figure 4 shows scanning electron microscopic view of the top surface of the copper coating. Figure 4(a) shows the copper thin film deposited on non-zincated aluminium surface. Topographic image shows that coating is formed by very fine clusters of crystallites. The histogram for size distribution of clusters of crystallites shown in Figure 4(a) (insets) indicates that major clusters are in between 40-60 nm size. Figure 4(b) shows the copper thin film deposited on double zincated aluminium substrate. The size distribution of clusters of crystallites is shown in Figure 4(b) (insets) and it indicates that most of them are in the range of 125-200 nm. The increased size of the clusters is due to the rougher zincated substrate as compared to non-treated aluminium. In non-zincated aluminium, copper atoms are deposited on aluminium oxide surface. The smooth aluminium oxide surface facilitates more number of nucleation sites than rough zincated surface. As a result copper coating on zincated aluminium surface shows more surface area.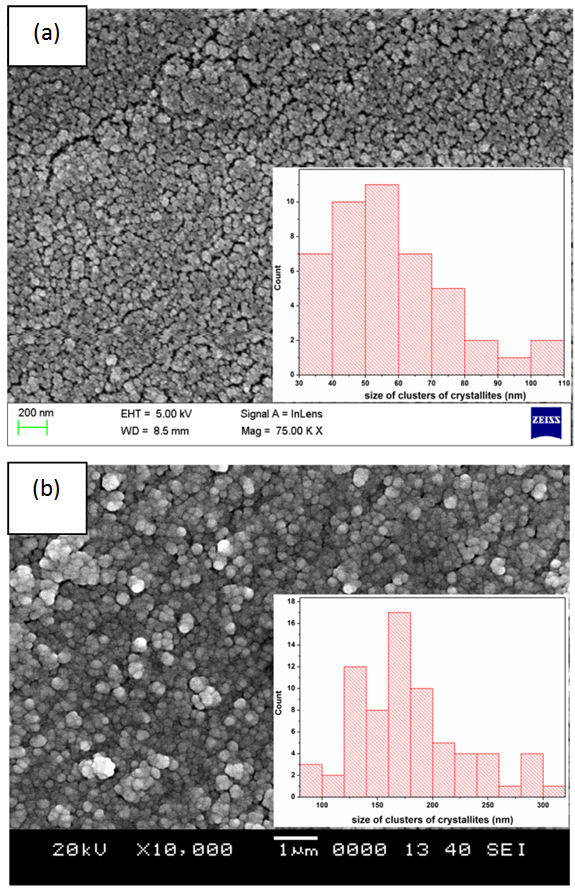 | Figure 4. Scanning electron microscopic view of copper thin film on (a) non-zincated substrate (b) double zincated substrate. Size distribution of clusters of crystallites is visible as histogram |
3.4. Contact Angle Measurement
The spreading behaviour of double distilled water on copper thin film deposited on non-zincated and zincated substrate is shown in Figure 5. The initial value of the contact angle on zincated surface is in hydrophobic region (90>θ).Initial hydrophobic region may form due to long wavelength roughness ratio formed due to hills and valleys on the coating. So liquid fails to penetrate into the narrow valleys due to the air pockets and form Cassie and Baxter regime [9]. Contact angle on copper thin film deposited on non-zincated surface shows hydrophilic nature in the starting stage itself. It may be due to the more uniformity and higher surface energy of fine nano structured clusters of copper grains. The average spreading rate of the coating is calculated from the slope of the graph (Figure 5) and it is equal to 0.0125 degree/second for copper thin film deposited on both zincated and non-zincated substrates.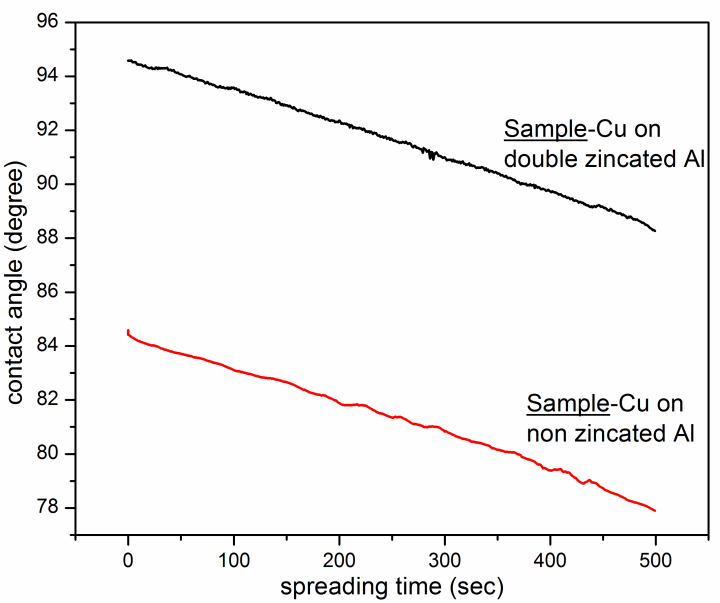 | Figure 5. Variation of contact angle with time of double distilled water on copper thin film deposited on zincated and non-zincated aluminium substrates |
4. Conclusions
The following conclusions may be drawn from the present study:1)Adhesion strength of copper thin film on aluminium has improved from 0.75MPa to 12 MPa by the double zincation process prior to sputtering.2)The morphology study using scanning electron microscope indicates that the size of clusters of crystallite has been increased from 60 nm to 175 nm. This is attributed to the double zincation process prior to DC magnetron sputtering. 3)XRD studies showed that the preferred growth is absent in the copper coating done on double zincated aluminium.4)The increase in contact angle of the copper thin film deposited on double zincated surface may be due to the less surface energy.
ACKNOWLEDGEMENTS
Authors would like to thank Dr. Narayana Prabhu and his research student Ms. Mrunali Sona, Department of Metallurgical and Materials Engineering, NITK, India, for helping in contact angle measurements. Arun Augustin would like to thank the National Institute of Technology Karnataka (NITK), India, for the research fellowship.
References
[1] | Reed, D., Kemmerly, S.A., 2009. Infection control and prevention: a review of hospital-acquired infections and the economic implications., The Ochsner Journal, 9, 27-31. |
[2] | Kelly, P., and Arnell, R., 2000, Magnetron sputtering: a review of recent developments and applications., Vacuum, 56(3), 159–172. |
[3] | Lunder, O., Olsen, B., and Nisancioglu, K., 2002, Pre-treatment of AA6060 aluminium alloy for adhesive bonding., International journal of adhesion and adhesives, 22(2), 143–150. |
[4] | R.R. Willigan, L. Chen and M.R. Jaworowski, “Bimetallic zincating processing for enhanced adhesion of aluminium on aluminium alloys”, U. S Patent WO2014150482 Feb. 6, 2015. |
[5] | Murakami, K., Hino, M., Hiramatsu, M., Osamura, K., and Kanadani, T., 2006, Effect of zincate treatment on adhesion of electroless nickel-phosphorus coating for commercial pure aluminum., Materials transactions 47(10), 2518–2523. |
[6] | N.V. Parthsarathy, Practical Electroplating Handbook, Prentice Hall PTR, New Jersey, USA, 2007. |
[7] | Finnis, M., 1996, The theory of metal-ceramic interfaces., Journal of Physics: Condensed Matter, 8(32), 5811-5836. |
[8] | Biju, V., Sugathan, N., Vrinda, V., and Salini, S.L., 2008, Estimation of lattice strain in nanocrystalline silver from X-ray diffraction line broadening., Journal of Material Science, 43(4), 1175–1179. |
[9] | Arora, H.S., Xu, Q., Xia, Z., Ho, Y.-H., Dahotre, N.B., Schroers, J., and Mukherjee, S., 2013, Wettability of nanotextured metallic glass surfaces., Scripta Materialia 69(10), 732–735. |