Vijay Kumar S. L. , Vikranth Kannanth M. S. , Vinay D. R.
Department of Mechanical Engineering, Mangalore Institute of Technology & Engineering, Moodbidri, India
Correspondence to: Vijay Kumar S. L. , Department of Mechanical Engineering, Mangalore Institute of Technology & Engineering, Moodbidri, India.
Email: |  |
Copyright © 2015 Scientific & Academic Publishing. All Rights Reserved.
Abstract
The main aim of this study is to examine the three body abrasive wear of A356 aluminum alloy under T6 heat treated condition and comparing the same with that of the base A356 alloy. The parameters employed are speed, load applied on the specimen and number of revolutions or number of turns. Three body wear test has been carried out on dry sand low stress rubber wheel type of abrasive wear test machine. T6 heat treatment is the commonly used heat treatment for this class of alloys. Mechanical properties of A356 aluminum alloy have been investigated by tensile and hardness tests. The effects of heat treatment on abrasion resistance, tensile strength and hardness of the A356 aluminum alloys have been investigated. It is observed that abrasion resistance increases for T6 heat treated alloy at different speed, load and number of revolutions.
Keywords:
Heat treatment, Abrasive wear, Abrasion resistance
Cite this paper: Vijay Kumar S. L. , Vikranth Kannanth M. S. , Vinay D. R. , Three Body Abrasive Wear Study on A356 Aluminum Alloy under T6 Heat Treated Conditions, American Journal of Materials Science, Vol. 5 No. 3C, 2015, pp. 43-47. doi: 10.5923/c.materials.201502.09.
1. Introduction
The dry sand/rubber-wheel abrasion test is widely used to evaluate low-stress abrasive wear of materials, particularly for evaluating wear-resistant materials used in the mining, oil sand and agricultural machinery industries. During such a test, a specimen is loaded against the rim of a rotating rubber wheel; a sand flow is directed to the gap between the wheel and specimen, abrading the specimen under an applied normal load at a certain sliding speed. Abrasion resistance of a material is evaluated by measuring its volume loss. A high wear-resistant material has a low volume loss.The A356 alloys commonly named as Al-Si alloys pertain to the most popular aluminum casting alloys. Mechanical properties of castings made from these alloys depend on the process of melting and pouring, structure of the casting and mould, as well as their heat treatment. In A356, aluminum (Al) is the major metal. The distinctive alloying elements are silicon, magnesium, manganese, copper and zinc. It is distinguished by good mechanical characteristics, high ductility, excellent casting characteristics as well as high corrosion resistance. The alloy has been widely applied in the machinery, aircraft and defence industries and particularly in the automotive industry to replace steel components [1-5]. A standard heat treatment for Al-Si alloys consists of solutioning and artificial ageing. Solutioning process includes holding the alloy below the eutectic reaction temperature in order to dissolve the precipitations of Mg2Si and homogenize the chemical elements concentration on the cross-section of dendrites of α phase. In ageing, supersaturated alloy is soaked to separate strengthening phases from the super saturated solution [6]. The T6 heat treatment produces maximum strength (hardness) in aluminum alloys. Unfortunately it requires a relatively long time to be carried out and therefore has significant financial implications. However, they need more than 4 h for solution at 540°C, and more than 6 h for aging at 150°C, thus cause substantial energy consumption and low production efficiency. It is beneficial to study a method to reduce the holding time of heat treatment. According to Rosso and Actis Grande, a solution heat treatment of 1 h at 540°C is sufficient to obtain a high level of mechanical properties in the T6 temper (hardness, yield strength, ultimate tensile strength and % elongation) [7]. The T6 heat treatment of Al-7Si-0.3 Mg alloy includes two steps: solutioning and artificial aging; the solution step is to achieve α (Al) saturated with Si and Mg and spheroidized Si in eutectic zone, while the artificial aging is to achieve strengthening phase Mg2Si. Recently, it has been shown that the spheroidization time of Si is dependent on solution temperature and the original Si particle size [8-12].
2. Experimental Details
2.1. Material
A356 alloy for testing was melted in a induction furnace at 650°C and poured in to the sand mould to get the slab shape. Subsequently the castings are machined into different size samples for testing. Table 1 shows the chemical composition of A356 alloy material used in the present study.Table 1. Composition of A356 (wt. %)  |
| |
|
2.2. Heat Treatment
In the present investigation A356 alloy is subjected to solution heat treatment at 550°C for 1 hour followed by water quenching. Artificial ageing is performed by maintaining specimen at 170°C for 1 hour followed by air quenching.
2.3. Hardness Test
Brinell hardness measurement is carried out in order to investigate the hardness of the material. The applied load was 500 kg and an indenter of 10 mm diameter of steel ball is used. The specimens were metallographically polished before the hardness measurement in Brinell hardness tester.
2.4. Tensile Test
The tensile tests were performed using a screw driven Instron tensile testing machine in air at room temperature. The cross-head speed was 1 mm/min. The strain has been measured by using an extensometer attached to the sample and with a measuring length of 50 mm. The 0.2% proof stress has been used as the yield stress of alloys. The values of yield strength, ultimate strength, young’s modulus and elongation are determined for the heat treated material and Al356 base alloy. The specimens are prepared as per ASTM E8-M11 standard as shown in Figure 1. 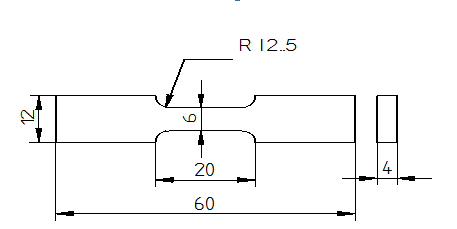 | Figure 1. The tensile test specimen |
2.5. Abrasion Test
The Three body abrasion test has been carried out at room temperature on A356 alloy. The test has been performed using standard rubber wheel abrasion testing apparatus as per ASTM G65 standard. Details of the sand abrasion tester employed in the present study are reported in Table 2 below. The specimen size of 76×25.4×12.7 mm was cut from the cast samples (ASTM G65) and were metallographically prepared and polished. Loads are varied from 2 kg to 5 kg at different wheel speed and silica sand of grain size 50µm has been used as the abrasive media. The abrasive has been fed at the contacting face between the rotating rubber wheel and the test sample. The tests were conducted at a rotational speed of 100, 150, 200 rpm. The rate of feeding the abrasive was 350 g/min.Table 2. Details of the sand abrasion testing machine 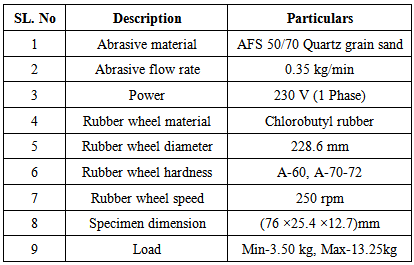 |
| |
|
The sample has been cleaned with acetone and then dried. Its initial weight has been determined in a high precision digital balance, before it has been mounted in the sample holder. The abrasive particles were introduced between the test specimen and rotating abrasive wheel composed of Chlorobutyl rubber tire (hardness: Durometer-A 60, A70-72). The diameter of the rubber wheel used was 228 mm.
3. Results and Discussion
3.1. Microstructural Studies
SEM images of base A356 and T6 heat treated A356 alloy samples are shown in Fig. 2 (a) and (b). It can be observed that precipitation size is larger in non-heat treated material compared to heat treated material. Hence it can be concluded that the size of the precipitation will play a major role in strengthening of A356 alloy. The precipitation size is small in the heat treated specimen and thus the material shows high resistance to plastic deformation. In the present study heat treated materials are showing very high resistance to abrasive wear compared to non heat treated material. Fig. 3 (a) and (b) shows worn surfaces of A356 base alloy and T6 heat treated A356 alloy. It can be observed that more number of grooves in Fig.3 (a) due to low fracture elongation in base A356 alloy and also observed that in Fig.3 (b) the number of grooves are minimized after T6 heat treatment.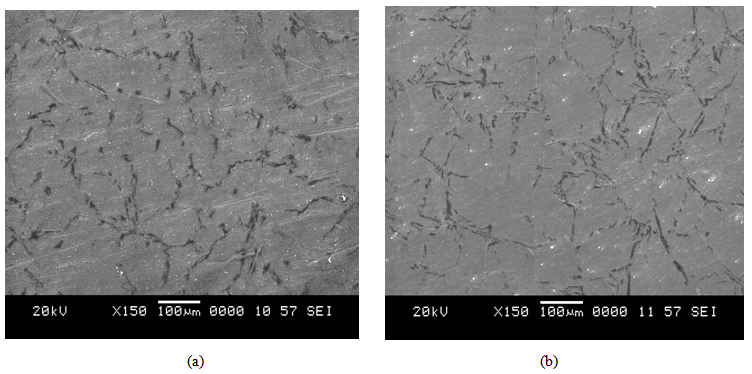 | Figure 2. SEM images of (a) base A356 alloy & (b) T6 heat treated A356 alloy |
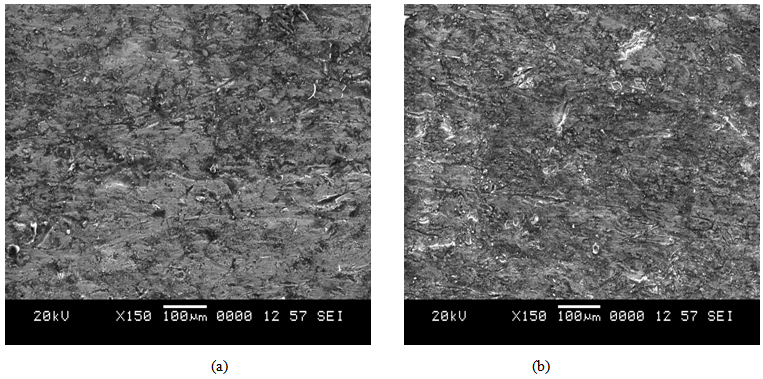 | Figure 3. SEM images of worn surfaces (a) Base A356 alloy & (b) T6 heat treated A356 alloy |
3.2 Hardness Test
In this study, three trails for each specimen are taken into consideration. From Table 3, it can be observed that the hardness value of heat treated specimens is more than that of non-heat treated specimens the reason being drastic changes in the microstructure of A356 alloy as a result of T6 heat treatment process.Table 3. Hardness values of A356 alloy  |
| |
|
3.3. Tensile Test
The Table 4 shows the Tensile test results of A356 base alloy and A356 T6 heat treated condition.It can be observed from Table 4 that, Young’s modulus (E) of base A356 material is lower compared to that of T6 heat treated material, the reason being an increase of yield strength (YS) and ultimate tensile strength (UTS) with ductility during T6 heat treatment. The % elongation, of the material without heat treatment is significantly higher. Spheroidization of the brittle silicon is the main reason for the decreased % elongation values for T6 heat treated condition [10].Table 4. Tensile tests results  |
| |
|
3.4. Abrasion Test
Tables 5 and 6 show the abrasive wear test results of base A356 and A356 T6 heat treated specimens for 20 and 30 rotations respectively.Table 5. Abrasion test results of 20 rotations 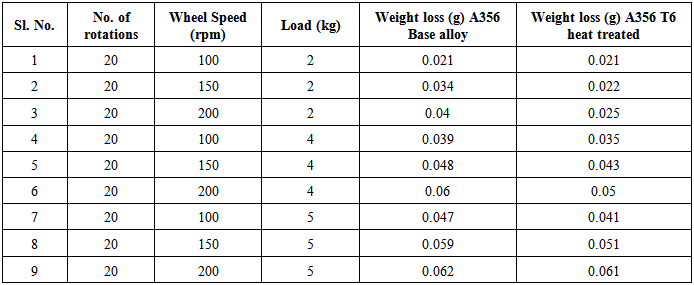 |
| |
|
Table 6. Abrasion test results of 30 rotations 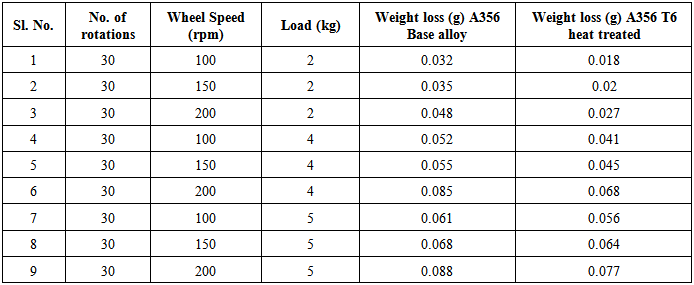 |
| |
|
Fig. 4 and 5 shows the graph of speed vs. weight loss of A356 aluminum alloy with and without heat treatment condition for 20 and 30 rotations respectively. In this experiment, under varying load, speed and number of revolutions of rubber wheel, it has been observed that weight loss is more in A356 base alloy compared to that in T6 heat treated A356 alloy. From abrasion study it is evident that, the material having higher yield strength shows better abrasion resistance compared to that of low yield strength material. Tensile test results show that heat treated material possesses higher yield strength compared to base A356 alloy again spheroidization of silicon being the reason for increase in the fracture elongation of material under T6 heat treated material.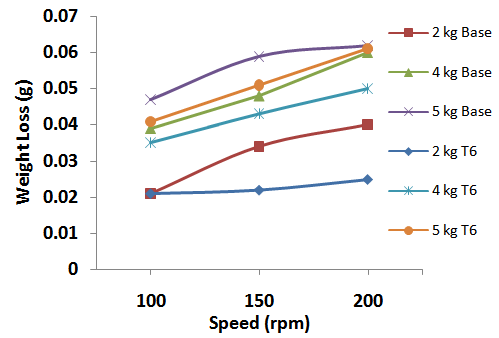 | Figure 4. Effect of wheel speed on weight loss of A356 Base alloy and T6 heat treated alloy at different loads for 20 rotations |
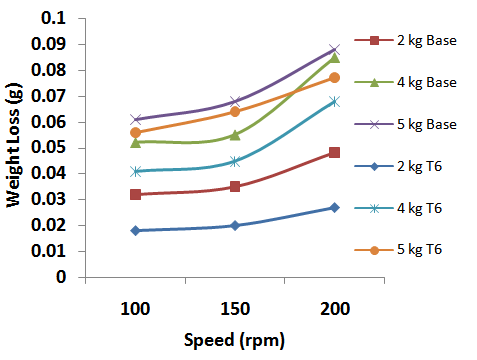 | Figure 5. Effect of wheel speed on weight loss of A356 Base alloy and T6 heat treated alloy at different loads for 30 rotations |
4. Conclusions
Based on the experimental observations, the following conclusions can be drawn: The three body abrasive wear resistance of the material increases when it is subjected to T6 heat treatment process. Also the, hardness, yield strength values of heat treated specimen are significantly higher compared to that of A356 Base alloy. Analysis of worn surface by Scanning Electron Microscope (SEM) indicates that in non heat treated specimen the size of the precipitation is larger, but in case of heat treated specimen the precipitation size is smaller. This factor plays major role during fracture in three body abrasion test.The Authors would like to thank Materials and Metallurgical Department, NITK Surathkal, Department of Mechanical Engineering, MIT Manipal and Dr. C.R Rajashekhar, HOD of Mechanical Department, MITE Moodbidri.
References
[1] | M. Ishak, A. Amir, A. Hadi, 2013, “Effect of Solution treatment temperature on Microstructure and mechanical properties of A356 alloy”, International Conference on Mechanical Engineering Research , Malaysia, 320. |
[2] | Ali Mazahery and Mohsen Ostad Shabani, 2012, “Characterization of cast A356 alloy reinforced with nano SiC composites”, Trans. Nonferrous Met. Soc. China, 22(2); 275-280. |
[3] | E Ogris, A Wahlen, H Luchinger, P J Uggowitzer, 2002,” On the silicon spheroidization in Al-Si alloys”, J Light Metals, 2(4): 263−269. |
[4] | E Sjolander, S Seifeddine, 2010, “Optimisation of solution treatment of cast Al-Si-Cu alloys”, Material Design, 31(s1), s44−s49. |
[5] | PENG Ji-hua, TANG Xiao-long, He Jian-ting, XU De-ying, 2011, “Effect of heat treatment on Microstructure and tensile properties of A356 alloys”, Trans. Nonferrous Met. Soc. China, 21. |
[6] | J. Pezda, 2014, “The effect of the T6 Heat treatment on Hardness and Microstructure of the EN AC-AlSi12CuNiMg alloy”, Poland, Metalurgija, 53, 63-66. |
[7] | M. Rosso and M. Actis Grande, 2006,” Optimization of heat treatment cycles for automotive parts produced by rheocasting process” Solid State Phenom, 116– 117, 505–508. |
[8] | H Möller, G Govender, & W.E Stumpf, 2008, “The T6 Heat Treatment of Semi-Solid Metal Processed Alloy A356”. The Open Materials Science Journal, 2: 6-10. |
[9] | Aleksandar Vencla, Ilija Bobicb Structural, 2010, “Mechanical and Tribological properties of A356 Aluminum Alloy reinforced with Al2O3, SiC and SiC + graphite particles”, Journal of Alloys and Compounds, 506(2): 631-639. |
[10] | E Ogris, A Wahlen, H Luchinger, P J Uggowitzer, 2002, “On the Silicon Spheroidization in Al-Si alloys”, J Light Metals, 2(4): 263−269. |
[11] | E Sjolander, S Seifeddine, 2010, “Optimisation of solution treat ment of cast Al-Si-Cu alloys”, Mater Design, 31(s1): s44−s49. |
[12] | Liu Bin-yi, Xue Ya-jun, 2006, “Morphology transformation of eutectic Si in Al-Si alloy during solid solution treatment”. Special Casting & Nonferrous Alloys, 26 (12): 802−805. |