Jayasheel I. Harti 1, B. R. Sridhar 2, H. R. Vitala 1, Pankaj R. Jadhav 1
1Department of Mechanical Engineering, East Point College of Engineering and Technology, Bangalore, India
2Department of Mechanical Engineering, South East Asian Engineering College, Bangalore, India
Correspondence to: Jayasheel I. Harti , Department of Mechanical Engineering, East Point College of Engineering and Technology, Bangalore, India.
Email: |  |
Copyright © 2015 Scientific & Academic Publishing. All Rights Reserved.
Abstract
The present work, aims at investigating the wear properties of Al2219 alloy before and after introducing micro size TiC particulates. TiC particulate reinforced Al2219 alloy metal matrix composites were prepared by stir casting method. Weight fraction of the reinforcement was varied from 0 to 6 wt. % in steps of 2 wt. %. For each composite, during processing the reinforcement particles were pre-heated to a temperature of 600°C and then dispersed into the vortex of molten Al2219 alloy. The microstructural characterization was done using Scanning Electron Microscope, which revealed fairly uniform distribution of TiC particles in Al matrix. Pin-on-disc wear testing machine was used to evaluate the wear rate of prepared specimens, in which a hardened EN32 steel disc was used as the counter face. The results revealed that the wear rate was increased with increase in normal load and sliding speed for all the conditions. Further, wear studies also suggest that wear rate of the Al2219-TiC composites was lesser than that of the Al2219 matrix.
Keywords:
Al2219 alloy, Wear, TiC, Stir casting, Composites
Cite this paper: Jayasheel I. Harti , B. R. Sridhar , H. R. Vitala , Pankaj R. Jadhav , Wear Behavior of Al2219-TiC Particulate Metal Matrix Composites, American Journal of Materials Science, Vol. 5 No. 3C, 2015, pp. 34-37. doi: 10.5923/c.materials.201502.07.
1. Introduction
Metal Matrix Composites (MMCs) are increasingly becoming attractive materials for advanced aerospace applications but their properties can be tailored through the addition of selected reinforcement [1]. In particular particulate reinforced MMCs have recently found special interest because of their specific strength and specific stiffness at room or elevated temperatures. Due to advancement in technology, there is enlarged demand for an economical, light weight, harder, stronger and energy saving material in the area of space, aircraft, defence and automotive applications and aluminium matrix composites (AMCs) found applications in these areas. Since last two decades there is wide exploration and pioneering development in the field of composite materials. In the past few years most of the researchers tried to reinforce monolithic metal and alloy with ceramic phase to enhance their properties [2].The most commonly employed Metal Matrix Composites (MMCs) consists of aluminium alloy reinforced with hard ceramic particles usually silicon carbide, fly ash, alumina and soft particles usually graphite and talc. Ceramic particles are known for low density, high strength, low thermal expansion, high thermal conductivity, high hardness, high elastic modulus, excellent thermal shock resistance and superior chemical inertness.Aluminium alloy 2219 is one type of wrought alloy containing copper as a major alloying element. Presence of copper makes this alloy heat treatable alloy leading to enhancement in the mechanical and tribological properties.Aluminium alloy Al2219 has been reinforced with particles of WC, SiC, Al2O3, B4C and graphite for forming a composite to realise improvements in mechanical properties such as hardness, young’s modulus, Yield strength and ultimate tensile strength. The composite finds applications in Aerospace and Automotive Industries [3].Several fabricating methods are available to process metal matrix composites. Stir casting is a liquid state method for the fabrication of metal matrix composites, in which hard ceramic particles are mixed with a molten matrix by means of mechanical stirring method [4]. However, a main problem such as wettability is associated with conventional stir casting of Aliminium Metal Matrix composites. To overcome this wettability problem several researchers used magnesium as a wetting agent. Due to friction and sliding of the components the major problem is of wear which requires the parts of the assemblies to be replaced frequently. Attempts have been made to minimize wear. To improve the wear properties in aluminium and its alloys work has been carried out by several researchers. Dry sliding wear studies for Al alloy A356 and SiC composites have been investigated and it has been found that reinforcements coated with copper and nickel show better mechanical behavior compared to those without any coating [5, 6].Literature survey indicates lack of data on the wear behavior of Al2219 reinforced with TiC particulates. In the present work a composite of this alloy with titanium carbide (TiC) has been fabricated and characterised. In the present work an investigation has been made to study the microstructure and the wear behavior of Al2219 alloy matrix reinforced with TiC particulates. Further, wear rate is determined by taking effect of load and sliding speeds for both the unreinforced Al2219 alloy and Al2219-2, 4 and 6 wt. % of TiC particulate reinforced composites. Worn surface study was carried out to understand the wear morphology of test specimens at 2kg load and 800 rpm sliding speed.
2. Experimental Details
2.1. Materials Used
Al2219 used as a matrix alloy and TiC particulates with 50-60µm are used as a reinforcement material to fabricate Al2219-TiC metal matrix composites. Al2219 has a density of 2.84g/cc and that of a reinforcement particle TiC is 4.93g/cc. The chemical composition of Al2219 for the work carried out to determine the wear characterization with the reinforcement of TiC is given in the Table 1.Table 1. Chemical composition of Al2219 alloy 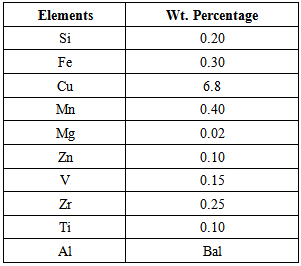 |
| |
|
2.2. Composite Preparation
Al2219-TiC composites were prepared by liquid metallurgy route. The weight of percentage TiC particulates were varied from 2-6 wt. % in step of two. The required amount of Al2219 wastaken and charged into SiC crucibles and heated to the required temperature of 730°C in an electrical resistance furnace. The required temperature was monitored on a digital temperature controlled with an accuracy of ± 50 degree Celsius. For the degassing of the molten metal, solid hexachloroethane (C2Cl6) was used to remove the absorbed gases [7]. To achieve a fine vortex, stirring was carried out mechanically; by using zirconia coated steel rod. The stirrer was immersed into the molten metal in the crucible at a depth of 2/3 from the bottom. The molten material was stirred for about 10-15mins at a motor speed of 300rpm. TiC particulates were preheated to increase the wettability. The preheated TiC particles were introduced into the vortex of molten Al2219 alloy.The weight of reinforcement TiC was divided into 2 equal weights and poured into vortex of molten Al2219 alloy two times for that particular casting instead of pouring it at once so that fine segregation is achieved in the casting. Before pouring the molten metal into the cast iron die, stirring was done before and after adding the TiC reinforcement. Stirring helps to avoid agglomeration and separation of particles and homogeneity is attained. The molten metal is poured into the mould die which was preheated and has the dimension of 140mm X 25mm diameter. Al2219-TiC particles of 2wt. %, 4wt. % and wt. 6% were carried out in a similar manner.
2.3. Wear Test
As per ASTM G-99 [8] standard testing procedure, the tests were conducted for dry sliding wear behavior for Al 2219 base alloy and Al 2219-TiC composite. The test conducted were carried on computerized Pin-On-Disc wear testing machine, the steel disc is made of high carbon EN-32 and has the hardness of HRC60 and disc diameter of 160mm. The specimen for wear test have the dimension 6mm diameter and length 30mm of cylindrical shape. The loads taken for wear test are 0.5kg, 1kg and 1.5kg with constant speed at 800rpm. The wear test where also carried for other sliding speeds at 600,700 and 800 rpm by keeping 1.5 kg load as a constant parameter. Before taking each reading for the variable parameters the steel disc was cleaned with 320grit and then 600grit SiC abrasive for a few minutes followed by cleaning with acetone.
3. Results and Discussion
3.1. Microstructural Features
Figure 1 (a) - (d) shows the Scanning Electron Microscope micrographs of as cast Al2219 alloy and its composites. Figure 1 (b) – (d) shows the SEM micrographs of 2, 4 & 6wt. % of TiC particulate composites. This reveals the uniform distribution of TiC particles and very low agglomeration and segregation of particles. The vortex generated in the stirring process breaks solid dendrites due to higher friction between particles and Al matrix alloy, which further induces a uniform distribution of particles.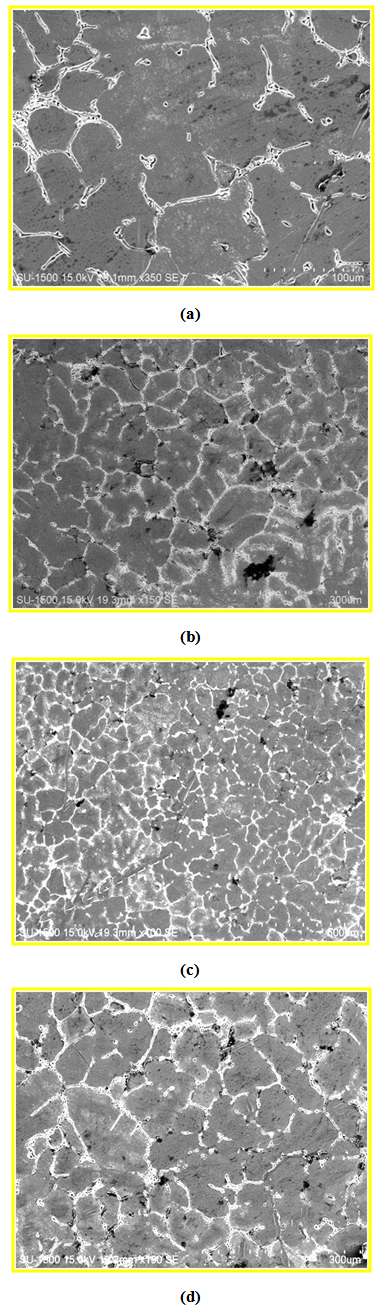 | Figure 1. SEM micrographs of (a) Al2219 as cast alloy (b) Al2219-2% TiC composite (c) Al2219-4% TiC composite (d) Al2219-6% TiC composite |
3.2. Wear Studies
3.2.1. Effect of Load on Wear Rate
The variation of wear rate as a function of normal load and sliding velocity at 800rpm for the Al2219 alloy and Al2219-TiC composites were shown in Figure 2. It is seen from the plots that the wear rate of as cast Al2219 alloy and its composites increases as the normal load increases from 0.5 kg to 2 kg in steps of 0.5 kg. During the test, when the applied load on the pin is increased, the actual contact area would increase towards the nominal area which increases the frictional force between the pin and steel disc. This increased frictional force causes high wear [9].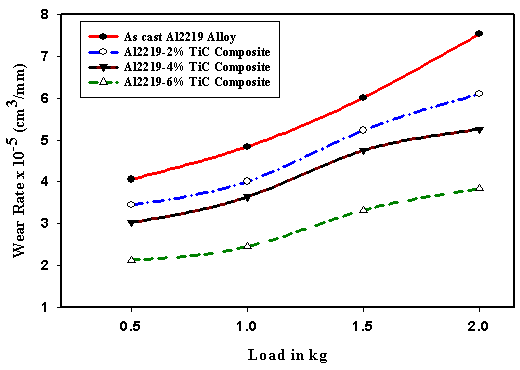 | Figure 2. Wear rate of Al2219 and Al2219-TiC composites at varying loads and 800rpm constant sliding speed |
Also it could be seen that wear rate of composites decreased with the addition of TiC particulates into the Al2219 base matrix alloy. The increase in the wear resistance can be attributed to the strengthening of the matrix due to the reinforcement, which results from an increase in the dislocation density as the percentage of reinforcement increases.
3.2.2. Effect of Sliding Speed on Wear Rate
The effect of sliding speed on wear rate is shown in Figure 3.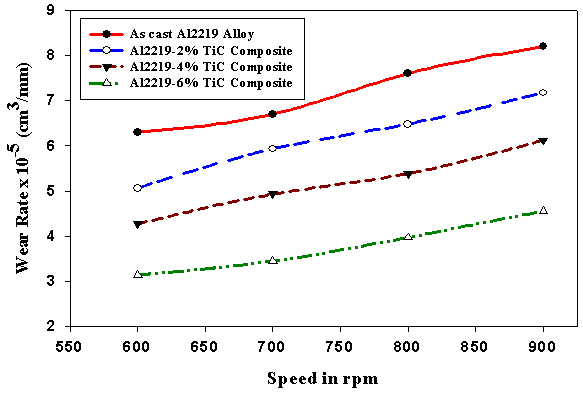 | Figure 3. Wear rate of Al2219 and Al2219-TiC composites at varying sliding speeds and 2kg constant load |
From the plot, it can be revealed that wear rate of Al2219 alloy and its composites increases with increase in sliding speed from 600 to 900 rpm at constant load of 2 kg.From the graph, the wear rate is increasing with the increase in sliding speed. This is mainly due to increase in heat generation between the Al specimen and steel disc, which leads to more softening of the matrix due to the overheating [10-11].Wear rate was less in the case of Al2219-TiC composites due to formation of mechanically mixed layer on the disc surfaces, which contained fractured TiC particulates. The presence of TiC particles acts as load bearing member.
3.2.3. Worn Surface Analysis
Figure 4 (a) - (b) shows the optical micrographs of worn surfaces of cast Al2219 alloy and Al2219-6wt. % TiC composites at an applied load of 2kg and 800rpm sliding speed. Figure 4 (a) shows the some damaged regions in as cast Al2219 alloy. At higher load, degree of grooves formed at the worn surface of the matrix alloy is quite larger and undergo severe plastic deformation leading to severe wear. Figure 4 (b) shows the amount of grooving in the worn surfaces of the Al2219 alloy composite, which is reduced with increased content of TiC showing the lower material removal in comparison with Al2219 base matrix material.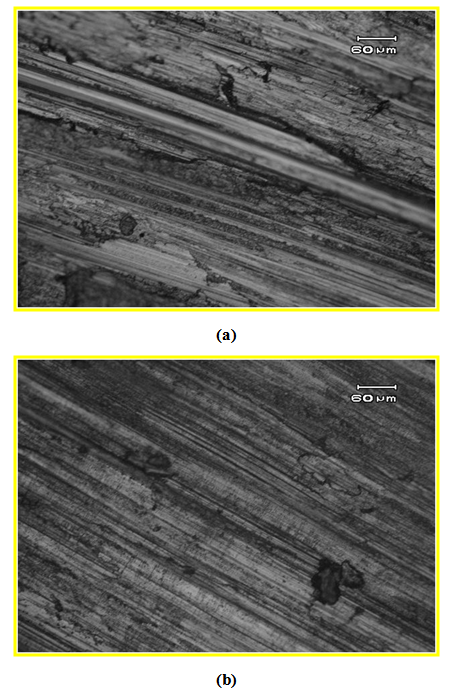 | Figure 4. Optical micrographs of worn surfaces of (a) as cast Al2219 alloy and (b) Al2219-6wt. % TiC Composite at 2kg load and 800rpm sliding speed |
4. Conclusions
The present work on processing and evaluation of Al2219-TiC metal matrix composite by melt stirring has led to following conclusions. Al2219 alloy based composites have been successfully fabricated by melt stirring method. The scanning electron micrographs of composites revealed fairly uniform distribution of reinforcement particulates in the Al2219 alloy metal matrix. The addition of TiC particles to Al2219 alloy matrix improves the wear resistance of the composite. The wear rate is dominated by load factor and sliding speed. The increase of loads and sliding speeds leads to a significant increase in the wear rate. The Al2219-2, 4 and 6 wt. % of TiC composites have shown lower rate of wear as compared to that observed in as cast Al2219 alloy matrix.
References
[1] | Hasim, J., Looney, L., M. S. J. Hashmi, M. S. J., 1999, Metal matrix composites production by the stir casting method, Journal of Materials Processing Technology, 92-93, 1-7. |
[2] | Madeva Nagaral, Auradi, V., Kori, S. A., 2014, Dry sliding wear behavior of graphite reinforced Al6061 alloy composites, Applied Mechanics and Materials, 592-594, 170-174. |
[3] | Devaraju, A., Kumar, A., Kotiveerachari, B., 2013, Influence of addition of Gr/Al2O3 with SiC on wear properties of aluminium alloy 6061-T6 hybrid composites via friction stir processing, Transactions of Nonferrous Metal Society of China, 23, 1275-1280. |
[4] | Sahin, Y., 2003, Preparation and some properties of SiC particle reinforced aluminium alloy composites, Materials and Design, 24,671-679. |
[5] | Mohan Vanarotti, Shrishail, P., Sridhar, B. R., Venkateswarlu, K., 2014, Surface modification of SiC reinforcements & its effects on mechanical properties of aluminium based MMC, Applied Mechanics and Materials, 446-447, 93-97. |
[6] | Mohan Vanarotti, Shrishail, P., Sridhar, B. R., Venkateswarlu, K., Kori, S. A., 2Study of Mechanical Properties & Residual Stresses on Post W14, wear Samples of A356-SiC metal matrix composites” Procedia Material Science, 5, 873–882. |
[7] | Madeva Nagaral, Auradi, V., Kori, S. A., 2014, Dry sliding wear behavior of graphite reinforced Al6061 alloy composites, Applied Mechanics and Materials, Vol.592-594, 170-174. |
[8] | Babu, J. S. S., Kang, C. G., Kim, H. H., 2011, Dry sliding wear behavior of aluminium based hybrid composites with graphite nanofiber and alumina fiber, Materials and Design, 32, 3920-3925. |
[9] | Zang, J., Alpas, A. T., 1993, Wear regims and transition in Al2O3 particulate reinforced Al-alloy, Material Science and Engineering, 161, 273-284. |
[10] | Shettigar A. K., Giridhar Salian, Mervin Herbert, Shrikantha Rao, 2013, Microstructural characterization and hardness evaluation of friction stir welded composite AA6061-4.5Cu-5SiC, Defence Science Journal, 63(4), 429-434. |
[11] | Dobrzanski L. A., Wlodarczyk, Admiak, 2006, AW-Al-Cu4-Mg1(A) Aluminium alloy reinforced with the Ti(C,N) ceramic particles, Material Science Forum, 530-531, 243-248. |