B. M. Ganiger 1, T. M. Chandrashekharaiah 1, T. B. Prasad 2
1R & D Centre, Dept. of Mechanical Engineering, Kalpataru Institute of Technology, Tiptur, Karnataka, India
2R & D Centre, Dept. of Mechanical Engineering, Sri Siddhartha Institute of Technology, Tumkur, Karnataka, India
Correspondence to: T. M. Chandrashekharaiah , R & D Centre, Dept. of Mechanical Engineering, Kalpataru Institute of Technology, Tiptur, Karnataka, India.
Email: |  |
Copyright © 2015 Scientific & Academic Publishing. All Rights Reserved.
Abstract
In the present paper the microstructure, mechanical properties and wear behavior of commercial LM-29 [Al-24Si-Cu-Mg] alloy before and after the addition of phosphorus (0.02, 0.03, 0.04, 0.05 and 0.06wt %) were investigated. The microstructures and worn surfaces of the alloys were characterized by optical metallurgical microscope/SEM. The results suggest that, the wear resistance of LM-29 alloy were improved with the addition of phosphorus as compared to as cast alloy. However, the maximum improvement in wear and mechanical properties were observed at 0.06wt%P addition to LM-29 alloy. This is due to the change in microstructure resulting from modification of primary silicon present in LM-29 alloy.
Keywords:
LM-29 cast alloy, Cu-14P master alloy, Microstructure, Normal pressure, Hardness
Cite this paper: B. M. Ganiger , T. M. Chandrashekharaiah , T. B. Prasad , The Effect of Modification of Primary Silicon on the Microstructure, Mechanical and Sliding Wear Behavior of Commercial LM-29 Cast Alloy, American Journal of Materials Science, Vol. 5 No. 3C, 2015, pp. 1-6. doi: 10.5923/c.materials.201502.01.
1. Introduction
Amongst the commercial aluminum casting alloys Al-Si alloys are the most common, particularly due to some very attractive characteristics such as excellent castability, high strength to weight ratio, pressure tightness and low coefficient of thermal expansion, good thermal conductivity, good mechanical properties and corrosion resistance [1]. The engine blocks cast from hypoeutectic Al-Si alloys such as LM-21, LM-25 or LM-24 must use cast iron cylinder liners due to poor wear and scuffing resistance which adds extra steps to the manufacturing cycle and also increases the cost of production, reduces weight savings and complicates recycling of the blocks. Hence there is a growing interest in hypereutectic Al-Si alloys as a candidate material instead of the conventional hypoeutectic Al-Si alloys [2]. However in hypereutectic Al-Si alloys, the primary silicon can be presented in several different forms like star shaped primary silicon, polyhedral primary silicon and dendritic primary silicon [3]. Large unevenly distributed primary Si particles causes greater tool wear than does the smaller ones that are more uniformly distributed. Thus, even distribution of the fine primary Si is an essential feature of cast hypereutectic Al-Si alloys [3-5].Modification of primary silicon in hypereutectic Al-Si alloys is usually achieved by the addition of Phosphorous (P) to the melt. Phosphorous reacts with the liquid aluminum to form aluminum phosphide (AlP), which has a crystal structure similar to that of silicon (i.e. a=5.46 Ǻ for AlP and that of Si is 5.43Ǻ) and acts as an effective heterogeneous nucleant [6-7]. The untreated hypoeutectic alloy contains a broad spectrum of Si sizes from 20µm to 120 µm. The best modification occurs with 0.003wt%-0.006wt%P and this causes the Si particle size distribution to become much narrower to about 20µm. Over modification takes place if the P level raised to 0.009wt% and broadening of the size distribution occurs and the most frequently occurring particle size is about more than 30 µm [3]. Gowrishankar and Prabhakar [8] have studied the effect of Mg on the cast microstructure of eutectic and hypereutectic Al-Si alloys and concluded that Mg improves the modification of the hypereutectic alloys and also substantially reduces the primary Si density. It does not refine the primary Si. They also reported that combined addition of Mg and P to hypereutectic and eutectic alloys brings about modification of eutectic Si and refinement of primary silicon.From the literature it has been noticed that the effect of P on the wear and mechanical properties of LM-29 alloy has not been reported. So in the present work an effort has been made to study the effect of minor addition of 0.02wt%-0.06wt%P on the microstructure, wear behavior and mechanical properties of commercial LM-29 alloy.
2. Experimental Details
A commercial LM-29 alloy was melted in an electric induction furnace under a cover flux (45% NaCl+45% KCl+10% NaF) and the melt was held at 720°C. After degassing with solid hexachloroethane (C2Cl6), Cu-14P master alloy chips duly packed in an aluminum foil were added to the melt. The melt was stirred for 30 seconds with zirconia coated iron rod after the addition of master alloy. Melts without and with the five different addition levels of master alloy were prepared and poured into the split type graphite mould (Φ12.5mm x 125mm) at ‘0’ minute and ‘5’ minutes respectively to have microstructure, wear and tensile specimens. Six different cast LM-29 alloys were used during the present study. B1 was the untreated one. B2-B6 were treated with phosphorous in the range 0.02wt%-0.06wt%. About 0.7g of Cu-14P is added to the molten mixture to produce 500g of B2 alloy and 1.14g, 1.4g, 1.8g and 2.14g of Cu-14P added to the molten mixture to produce 500g of B3, B4, B5 and B6 alloys respectively. The details of different amount of Cu-14P master alloy added to the base alloy LM-29 is given in Table 1.Table 1. Compositions of the alloys used for microstructure, wear and mechanical properties studied 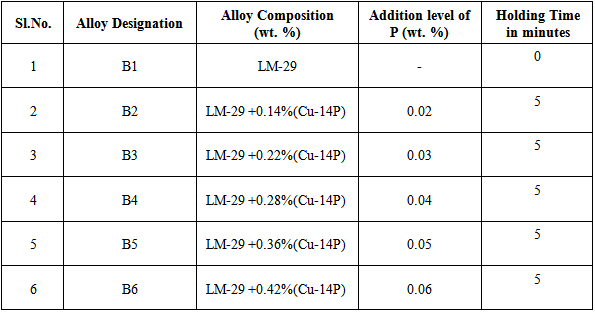 |
| |
|
Specimens of size Φ10mmx10mm were taken for microstructural examination and these were polished and etched with 0.5%HF etchant [9]. These specimens were examined for microstructure and primary Si particle size under optical metallurgical microscope (Carl Zeiss, AxioVert.A1). Wear tests were conducted on all the six samples with a pin-on disc type wear testing machine (DUCOM, TR-20). The size of the wear test pin taken was Φ10mmx 35 mm length [10]. The disc material is made up of En-31 steel (C-0.9%, Si-0.35%, Mn-0.75%, S-0.05%, Cr-1.6% and balance Fe) with a hardness value of HRC 61. The surface roughness of the disc varies from 0.47 to 0.87µm. The pin and the disc were abraded against silicon carbide (SiC) polishing papers and washed with acetone and dried before each sliding test to ensure that the tests were conducted under dry sliding conditions. The test pin was loaded against the disc with a dead weight through a pulley- string arrangement. A constant 90mm track diameter was used throughout the experimental work. An analytical balance with a precision of 0.0001g was used to measure the weight of the pin before and after each test. The sliding wear tests were carried out at constant sliding speed of 1.885m/s (400 rpm) and sliding distance of 565.5m by varying normal pressures from 0.1248N/mm2 to 0.6244 N/mm2. Weight loss of each alloy specimen was obtained from an average of three readings. The frictional force was recorded during the experiment by using frictional sensor (accuracy ±2% measured frictional force and capacity 200 N). The size of tensile test specimen was Φ 9mm x 45mm gauge length. The chemical composition of the commercial LM-29 alloy was assessed using atomic absorption spectrometer (Model; Varian AA-240, Netherlands) and is shown in Table 2. The tensile tests were carried out on a computerized universal testing machine (FIE Make, UNITEK-9450). Hardness tests were conducted on Φ 10mm x 10mm cylindrical test bar using micro Vickers hardness tester (Make: Matsuzawa, Japan, Model: MMTX7) under 1.0 kg load for a dwell time of 10 seconds. The hardness value of each alloy specimen was taken from an average of three readings.Table 2. Chemical composition of cast and master alloy 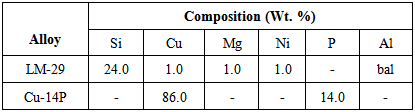 |
| |
|
3. Results and Discussion
3.1. Microstructural Studies
Figure1a-f shows the optical photomicrographs of LM-29 alloy before and after the addition of Cu-14P master alloy. The microstructural examination reveals needle like particles of eutectic silicon and angular particles of primary silicon in a matrix of aluminum solid solution of base alloy. However, polygonal primary silicon particles treated with increasing addition of P (0.02-0.06%) and get distributed uniformly in the matrix (figure1b-f). This could be due to the fact that P reacts with the liquid Al forms AlP and Cu3P particles present in Cu-14P master alloy may act as heterogeneous nucleating sites for modification of primary silicon particles during solidification of hypereutectic alloys [3, 5].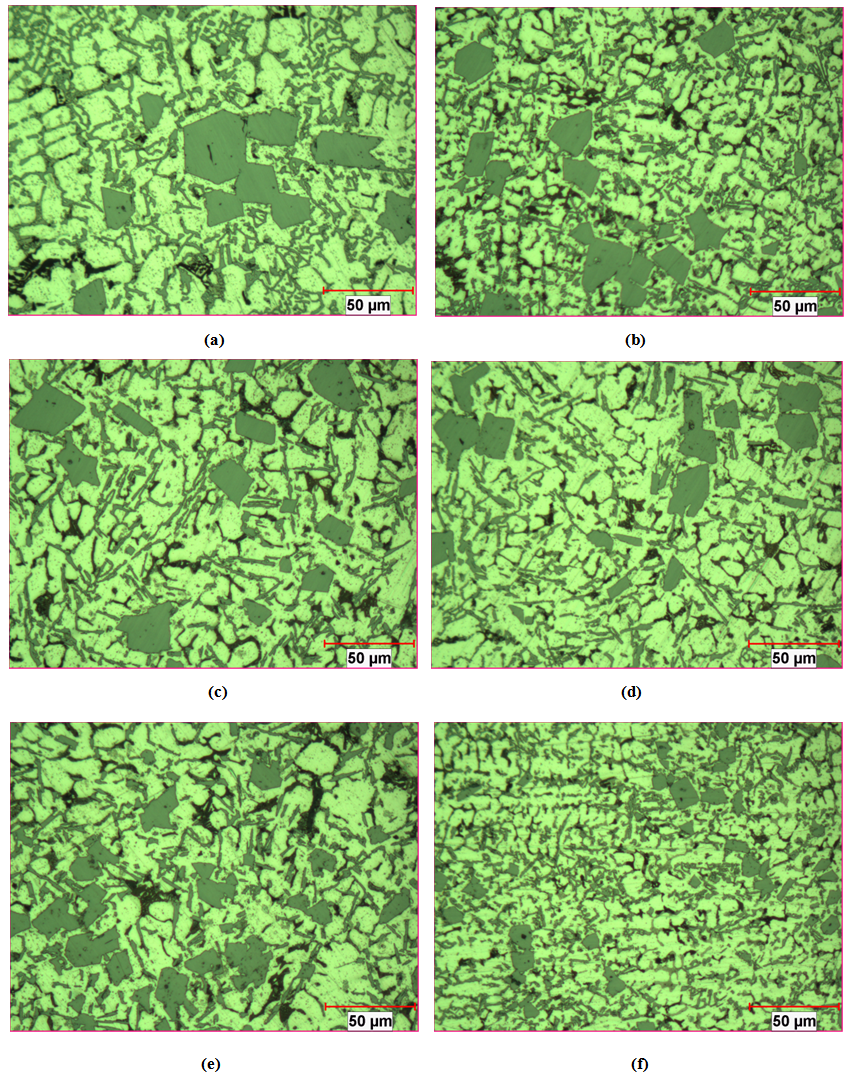 | Figure 1. Optical photomicrographs of LM-29 alloy without and with addition of Cu-14P master alloy (a) As cast condition (b) With 0.02wt%P (c) With 0.03wt%P (d) With 0.04wt%P (e) With 0.05wt%P (f) With 0.06wt%P |
Figure 2 shows the variation in the primary Si particle size with increase in the addition of P (0.02-0.06%). The primary silicon particles size in untreated alloy B1 ranges from 72-31 µm and that in B2, B3, B4, B5 and B6 alloys, it ranges from 55-27µm, 47-26µm, 38-20µm, 38-18µm and 38-14µm respectively. The average primary silicon particle size in untreated alloy is 51.87µm whereas it is 21.53µm in B6 alloy, which is about 60% reduction in primary silicon size.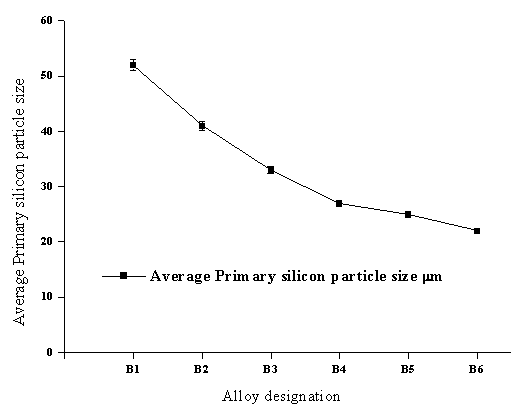 | Figure 2. Variation in the primary Si particle size with alloy composition |
3.2. Effect of Normal Pressure on Weight Loss and Frictional Force
Figure 3-4 show the effect of normal pressure (0.1248, 0.2498, 0.3744, 0.4992 and 0.6244 N/mm2) on weight loss and frictional force under constant sliding speed (1.885m/s) and at constant sliding distance (565.5m). From Figure 3, it is observed that as the content of P in the LM-29 base alloy increases the wear of the specimen comes down. Wear is highest in the base alloy and least in the base alloy containing 0.06%P. It is also clear from the figure that the addition of 0.06% of P to LM-29 alloy has resulted in minimum weight loss when compared to the addition of 0.02-0.05% of P and to the as cast condition. Similarly frictional force LM-29 alloy increase with increase in normal pressure in all the cases studied and the frictional force was higher in case of as cast LM-29 alloy (Figure 4).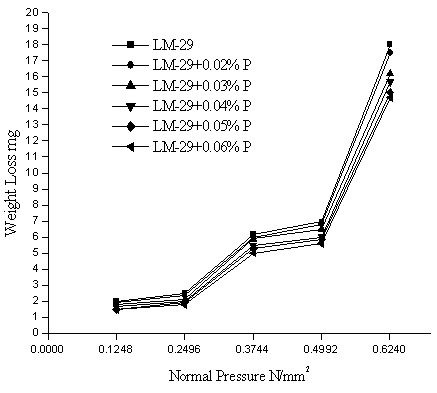 | Figure 3. Effect of normal Pressure on weight loss |
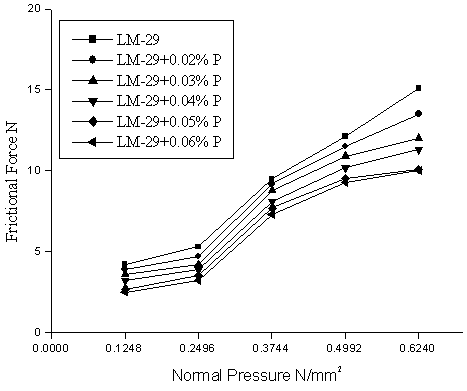 | Figure 4. Effect of normal Pressure on Frictional force |
However, the addition of 0.06%P in the form of master alloy has resulted in minimum frictional force when compared to the as cast condition. Such a decrease in frictional force could be due to the change in microstructure as clearly observed in Figure 2a-f. The lower weight loss and frictional force of LM-29 alloy containing 0.06%P can be explained in the light of microstructural features. The primary silicon size plays an important role in achieving wear resistance of hypereutectic alloy. As the primary silicon size decreased from 72-38µm and also its distribution is more or less uniform in the Al matrix, wear resistance of alloy increases.
3.3. Mechanical Properties
The effect of addition of P on the mechanical properties is shown in Figure 5a-c. From the figures, it is clear that improvement in mechanical properties such as ultimate tensile strength, hardness and percentage elongation of the alloy can be achieved with the addition of P. The alloy without the addition of P shows poor tensile strength, while the alloys with P show more improvement. However, 0.06% P addition to LM-29 alloy shows the maximum improvement in mechanical properties compared to lower addition level of P and to as cast alloy. The maximum values of UTS, VHN and % E observed in the alloy having 0.06wt%P are 212 N/mm2, 160 and 1.56 respectively and these in as cast alloy are 175 N/mm2, 138 and 0.94 respectively. This could be due to the change in microstructure resulting from modification of primary silicon present in LM-29 alloy.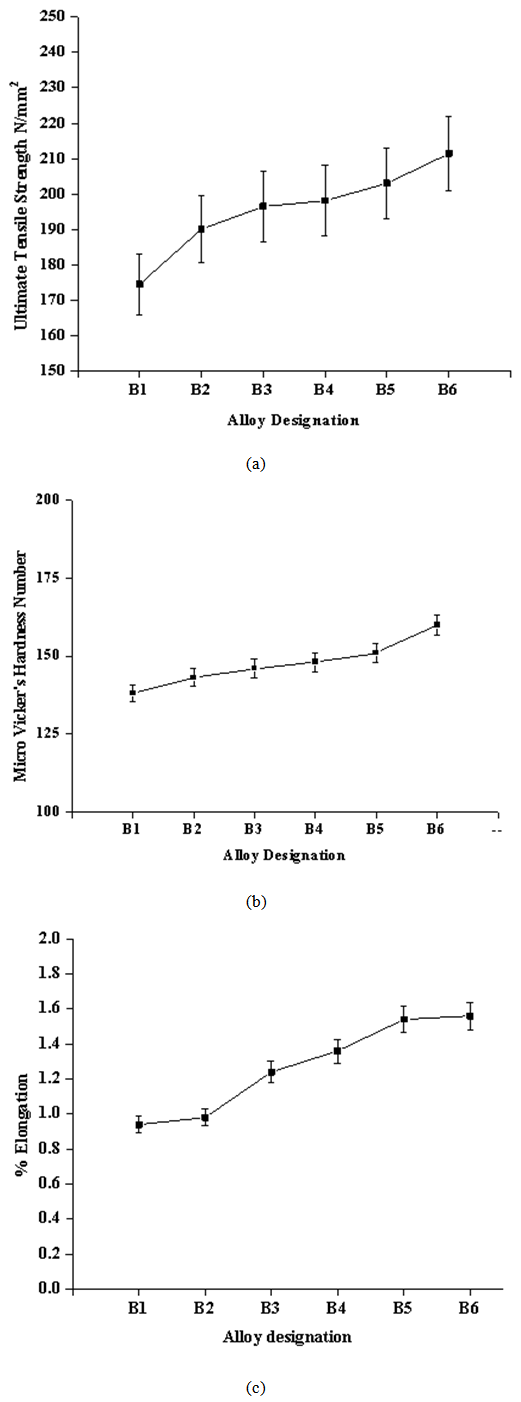 | Figure 5. Mechanical properties; (a) Ultimate tensile strength (b) Micro Vicker’s Hardness Number and (c) % Elongation |
3.4. Worn Surface Studies
The worn-out surfaces were examined under scanning electron microscope. Figure 6 a and b show the SEM photomicrographs of worn out surface of LM-29 alloy without and with the addition of 0.06% phosphorous. The examination of worn surface of as cast alloy shows dimples and patches indicating delaminative wear. However the severity of surface damage decreased in refined alloy showing the evidence of mild abrasive wear. Hence the weight loss of the treated LM-29 alloy is lower than that of the untreated one which could be due to the decrease in primary Si particle size in treated alloy B6.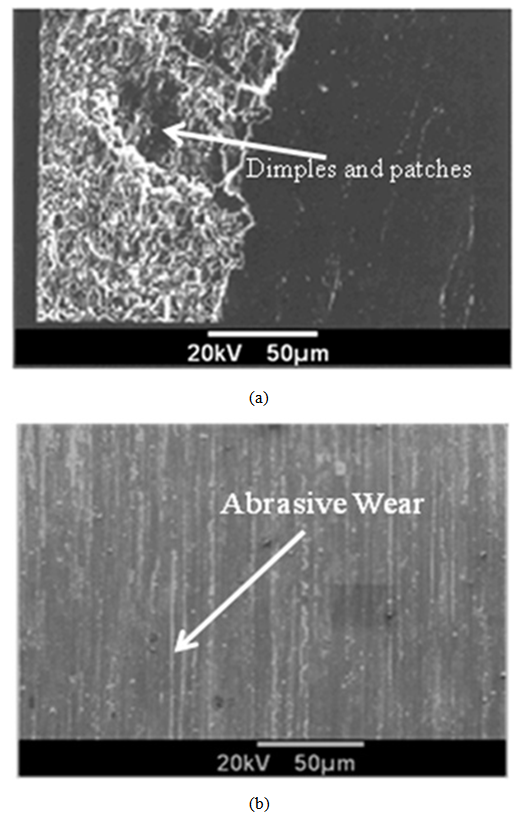 | Figure 6. SEM photomicrographs of worn out surfaces of LM-29 alloy at 0.6244 N/mm2 normal pressure under constant sliding speed (1.885m/s) and at constant sliding distance (565.5m) (a) As cast condition (b) With 0.06wt%P |
4. Conclusions
• The primary silicon size ranges from 14-38 µm in LM-29 alloy containing 0.06%P and that, in as cast alloy it is 31-72µm. There is about 60% reduction in size of primary silicon as compared to as cast alloy.• Increasing the addition of P (0.02-0.06%P) increases UTS, hardness and marginal changes in %E of LM-29 alloy. The maximum improvements in % elongation, hardness and ultimate tensile strength observed in LM-29 with 0.06wt%P are 66%, 16% and 22% respectively.• Weight loss in all the cases increased with increase in normal pressure at constant sliding speed and at constant sliding distance. However Weight loss decreased with different addition levels of P. Better results are observed in the alloy containing 0.06wt%P.• Delaminative wear was observed in case of LM-29 alloy where as in case of alloy containing 0.06%P it is mild abrasive wear.
ACKNOWLEDGEMENTS
The authors are very much grateful to the Vision group on Science and Technology-FIST [L1] GRD No. 372, 2015-16 for the financial support for the present work. The authors are also thankful to the Management and Principals of KIT Tiptur, SJMIT Chitradurga, SSIT Tumkur, CMTI Bangaluru and SRMTS Bangaluru for providing the laboratory facilities to carry out this work.
References
[1] | Saheb, N., Laoui, T., Daud, A.R., Harun, M., Radiman, S., Yahaya, R., 2001, Influence of Ti addition on wear properties of Al-Si eutectic alloys, Wear, 249, 656-662. |
[2] | Elmadagli, M., Perry, T., Alpas, A.T., 2007, A parametric study of the relationship between microstructure and wear resistance of Al-Si alloys, Wear, 262,79-92. |
[3] | Gruzleski, J.E., and Closset, B.M., 1990, The treatment to Liquid aluminum silicon alloys, AFS, Illinois, 1-254. |
[4] | Kori, S.A., Murty, B.S., Chakraborty, M., 2001, Effect of Al-5Ti-1B grain refiner on some hypereutectic Al-Si alloys, Indian Foundry Journal, 47(1), 13-17. |
[5] | Ben Heshmatpour, 1996, High performance phosphorus additives for modification of silicon in Al-Si alloys, TMS Light Metals, Ed., Wayne Hale, 687-695. |
[6] | Chen, S., Wang, Z., Yi, S., Jia, S., 1981, Studies on the modification mechanism of Al-Si alloys with antimony, Jixie Goncheng Xuebao, 17, 68-77. |
[7] | ZHANG Zhong hua., BIAN Xiu fang., WANG Yan., LIU Xiang fa., 2001, Refinement and thermal analysis of hypereutectic Al-25% Si alloy, Trans. Nonferrous Met.Soc. China, 11(3), 374-377. |
[8] | Gowrishankar, N., and Prabhakar, O., 1994, Effect of Mg on the cast microstructure of eutectic and hypereutectic aluminum-silicon alloys, Trans. Indian Inst. Met., 47(4), 229-237. |
[9] | Pengfei Xing., Bo Gao., Yanxin Zhuang., Kaihua Liu.,2010, On the modification of hypereutectic Al-Si alloys using rare earth Er, Acta Metall. Sin. (Engl. Lett.) 23(5), 327-333. |
[10] | ASTM Standards, 1993, Standard test method for wear testing with a Pin-on–disc apparatus, designation G99-90, ASTM, 1916 Raco st. Philodolphia, PA 19103, pp 1-5. |