Prashanth Kamath, Paramashivaiah M. Buksagamath, Niranjan Rai, Srinath N. Salian
Department of Mechanical Engineering, Canara Engineering College, Mangalore, India
Correspondence to: Niranjan Rai, Department of Mechanical Engineering, Canara Engineering College, Mangalore, India.
Email: |  |
Copyright © 2016 Scientific & Academic Publishing. All Rights Reserved.
This work is licensed under the Creative Commons Attribution International License (CC BY).
http://creativecommons.org/licenses/by/4.0/

Abstract
In a Vortex Heat Transfer Enhancement over a surface with an array of surface cavities or dimples each dimple acts as a vortex generator. The array of dimples causes an enhancement in heat transfer over a surface. The vortex provides an intensive and stable heat transfer and air flow between the dimpled surface and heat transfer media. In the present work, an experimental study of heat transfer through a flat surface with arrays of circular dimples was compared with the plane surface. The flow characteristics like Reynolds number (Re), Nusselt Number (Nu), and heat transfer characteristics like convective heat transfer coefficient (h), heat transfer rate (Q) on a forced convection apparatus was measured. The study was carried out for flat metallic surfaces without dimples and compared with dimpled flat surfaces. An array of dimples of 4x4 and 7x7 were prepared onaluminum, copper and stainless steel plates. The study was done for different air stream velocity and plate surface temperatures. The comparative study of heat transfer with smooth surface and dimpled surface was done. The result reveals that an increase in heat transfer rate for dimpled surfaces with 4x4 arrays and 7x7 arrays. Hence it can be concluded that an increase in array of dimple enhances the heat transfer compared to smooth surface.
Keywords:
Vortex, Dimple, Array, Reynolds number, Nusselt number
Cite this paper: Prashanth Kamath, Paramashivaiah M. Buksagamath, Niranjan Rai, Srinath N. Salian, An Experimental Study on Enhancement of Convective Heat Transfer over Dimpled Surfaces, Journal of Mechanical Engineering and Automation, Vol. 6 No. 5A, 2016, pp. 126-130. doi: 10.5923/c.jmea.201601.24.
1. Introduction
The surface having number of depressions on it is known as dimpled surface. A dimpled heat transfer surface is used for transferring heat energy from either a hot fluid or hot object to a cooler fluid. Dimple enhances heat transfer from its surface for laminar air flow while the pressure drop is equivalent or smaller than that of the flat surface. These surfaces do indeed enhance thermal performance without the penalty associated with higher pressure drops. A tremendous amount of effort has been devoted for developing new methods to increase heat transfer from finned surface to the surrounding flowing fluid [1]. It has been found that the heat transfer coefficient and heat transfer rate increases for dimpled surface as compared to plane surface. Dimples are used on the surface of internal flow passages because they produce substantial heat transfer augmentation. The importance of heat transfer enhancement has gained greater significance in such areas as microelectronic cooling, especially in central processing units, macro and micro scale heat exchangers, gas turbine internal airfoil cooling, fuel elements of nuclear power plants, and bio medical devices. The dimples formed on a surface can significantly enhance the heat transfer rate. Some of the examples are, heat transfer increase in cooling of turbine blade, tube and shell type heat exchangers in process industries like chemical and textile industries, radiators of automobiles etc.. Figure 1 shows flow velocity profile on vehicle’s centerline plane near the roof end, which causes the downstream pressure rise, which in turn generates reverse force against the main flow thus develops reverse flow at downstream point C. at point A no reverse flow take place which is located further upstream of point C. this is because the momentum of boundary layer is overcoming the pressure gradient between points A and C, there is separation point B, at which point there is an eqibalance between pressure gradient and the momentum of the boundary layer. In bottom zone nearer to the vehicle’s surface in the boundary layer, the air quickly loses the momentum when it moves downstream because of viscosity of air that results in reversal of air flow. The intension of adding the vortex generators is to provide the momentum from higher region where airflow has higher momentum compared to lower region where it has less momentum value. It is possible due to the stream wise vortices generated from vortex generators located just before the separation point, as shown in Figure 1. This permits separation point to move further downstream. Move in the separation point downstream makes the airflow to continue proportionately longer and flow velocity at the separation point become slower. Hence the static pressure becomes higher. The overall pressure in the entire flow separation region is governed by this static. This reduces the drag by enhancing back pressure. Shifting the separation point towards the downstream provides dual advantages in drag reduction, one is to narrow the separation region another is to raise the pressure of the flow separation region [2].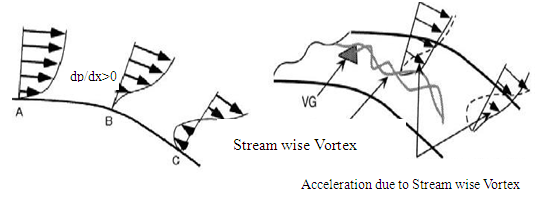 | Figure 1. a. Schematics of vortex generator b. Flow velocity profile around vortex at rear end |
The vortex formed inside dimple cavity creates scrubbingaction of flowing fluid as shown in Figure 2. Vortex Heat Transfer Enhancement (VHTE) is the increase in heat transfer by a system of 3-Dimensional surface cavities called as dimples. Each dimple acts as a “vortex generator” which provides an intensive and stable heat and mass transfer between the dimpled surface and gaseous heating/cooling media.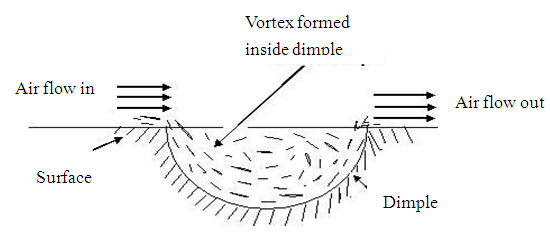 | Figure 2. Vortex heat transfer enhancement mechanism |
M.A. Dafedar et. al. [1] studied on the heat transfer augmentation through various geometries of dimpled surfaces in longitudinal and lateral directions found that in horizontal rectangular plates of aluminum and copper with different dimpled geometries found that the heat transfer coefficient and heat transfer rate increases for various dimpled surfaces as compared to plane surface. It is also found that the heat transfer coefficient and heat transfer rate increases along longitudinal direction as compared to lateral direction. Finally they have concluded that heat transfer enhancement takes place along the dimpled surface. Iftikarahamad H. Patel et.al [2] studied the convective heat transfer in turbulised flow past a dimpled surface. A parametric study is performed with k-ε turbulence model to determine the effects of dimple depth, Reynolds number and Nusselt number on heat transfer enhancement. They have computed heat transfer coefficients in a channel with one side dimpled surface. The Reynolds number based on the channel hydraulic diameter was varied from 200000 to 360000. The results showed that increased heat transfer was observed downstream of the dimples due to flow reattachment. Due to the flow recirculation on the upstream side in the dimple, the heat transfer coefficient was very low. Verma et.al [3] in their study on Heat Transfer enhancement using dimples based on scrubbing action of cooling fluid that take place inside the dimples, have shown good heat transfer characteristics when used as surface roughness.. From their research work they have used various dimple shaped geometries such as circular, square, triangular, ellipsoidal, but the ellipsoidal shape gives better results due to prior vortex formation compared to other geometries. S. D. Hwang et al. [4] in present study, heat transfer of a dimple protrusion patterned surface have been investigated that there is an enhancement of energy-efficiency in heat exchangers. They have used the transient TLC (Thermo chromic Liquid Crystal) technique at low Reynolds number to derive local heat transfer coefficients on the dimple/protrusion walls. The vortices induced from the upstream affect strongly on the downstream pattern. The heat transfer augmentation was higher in low Reynolds number because of the effective vortex interactions. Hence the performance factor when both heat transfer enhancement and pressure loss are considered increases with decrease Reynolds number. Moon et al. [5] observed that, the heat transfer rate is increased and pressure drop is reduced for dimpled surfaces. Practical applications of dimpled surfaces include macro-and micro-scale heat exchangers, electronics cooling, combustion chamber liners, passages for internal cooling of turbine blades in gas turbine engines, biomedical devices, etc. Amjad Khan et.al. [6] studied the fluid flow and heat transfer characteristics of spherical dimples at different angle of orientation from the centre with apex facing the inlet were investigated. The experiments were conducted for laminar natural convection conditions with air as a working fluid. The overall Nusselt number and heat transfer coefficient at different orientation angle of dimples were obtained. It was observed that the Nusselt numbers and heat transfer coefficient increases with decrease in the orientation angle of dimples.
2. Materials and Experimental Details
2.1. Materials
Test plates are of aluminium, Copper and stainless steel sheets of 2mm thickness and 100 mm × 100 mm length and breadth. The dimples produced are hemi-spherical inline dimples of depth 2 mm and 5mm diameter. For rectangular pattern arrangement total number of rows is employed in the stream wise direction Figure 3 shows different types of combinations of test plates. 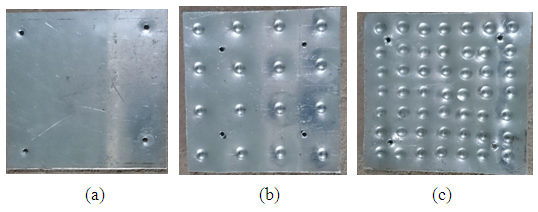 | Figure 3. Test surfaces (a) Flat surface (b) Test Surface with 4x4 array of dimples (c) Test Surface with 7x7x dimples |
Figure 4 shows the schematic diagram of the experimental setup. The major components of the test rig are as listed sequentially.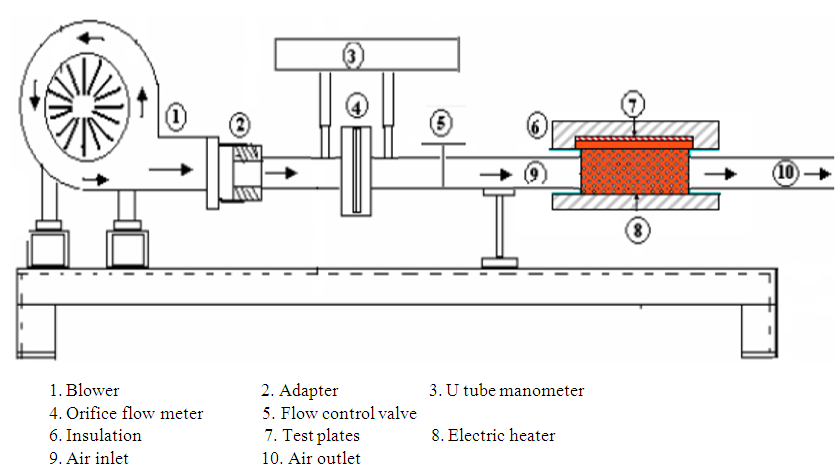 | Figure 4. Schematic diagram of the experimental setup |
2.2. Experimentation
In the present work the individual test plates are mounted one by one in the test section. The test surfaces are placed in the middle of the test channel. Care is taken so that the test sheet can be located in the middle of the test section in order to ensure an equal channel height conditions and airflow rates for both sides of the test plate. The blower is turned on and air is forced through the test setup. The flow rate through the test section is controlled with the help of a valve. After the flow is set across the test section, the heater is turned on and the voltage supplied to the heater is set to desired output. As the temperature of the test sheet reaches steady state the pressure difference across the test section is checked using the manometer. The voltage supplied to the heater and the corresponding current is taken to calculate the heat supplied to the test sheet. The temperatures of the air at the inlet of test section and outlet section are determined. The temperatures at various points on the test plate are also checked using the temperature indicator. The same procedure is repeated for all test specimens.
3. Results and Discussion
The data obtained after experimentation is used to tabulate the flow characteristics like Reynolds number and Nusselt number which shown in table 1, 2 and 3 for different materials. And further it is used to plot different flow and thermal characteristics. The figure 5 shows the variation of Reynolds Number with Nusselt Number for three different surfaces. It shows that Nusselt Number increases with increase in Reynolds Number as the density of dimples on surface is increased. It is found from the figure that for Aluminium plate with 7x7 array of dimples is having highest Nusselt Number, where as stainless steel is having minimum value for same dimple density. The figure 6 and figure 7 shows that variation of rate of heat transfer and percentage increase in heat transfer rate for three different test surface materials with different dimple densities. It is found that, as the dimple density increases, the rate of heat transfer increases for the different test surface materials. The percentage increase in rate of heat transfer over the flat surface for the 4x4 array and 7x7 arrays for stainless steel is 5.01 and 14.63 respectively. The percentage increase in rate of heat transfer over the flat surface for the 4x4 array and 7x7 arrays for Copper is 6.23 and 14.85 respectively. Whereas percentage increase in rate of heat transfer over the flat surface for the 4x4 array and 7x7 arrays for aluminium is 7.46 and 15.12 respectively. This results shows that the increase in rate of heat transfer is maximum for Aluminium surface with dimple density of 7x7 arrays. This is due to the increase in the Reynolds Number which leads to increased turbulence and strong vortex formation over the dimple cavities. The concept of decrease in thermal resistance and hence increase heat transfer is to increase the depth of the dimples. Providing the dimples on the surface enhances the surface area of heat transfer but also decreases the hydrodynamic resistance for the flow of fluid over the surface which results in decreased pressure drop. The vortices formed inside the dimples results in thinning and to disturb the thermal boundary layer formed over the surface during coolant flow and serve ultimately to bring about enhancement of heat transfer between the fluid and its neighboring surface at the price of less increase in pressure. Table 1. Variation of Reynolds Number, Nusselt Number and Heat transfer Rate Q (kJ) for Aluminium sheet  |
| |
|
Table 2. Variation of Reynolds Number, Nusselt Number and Heat transfer Rate Q (kJ) for Copper sheet  |
| |
|
Table 3. Variation of Reynolds Number, Nusselt Number and Heat transfer Rate Q (kJ) for Stainless Steel sheet  |
| |
|
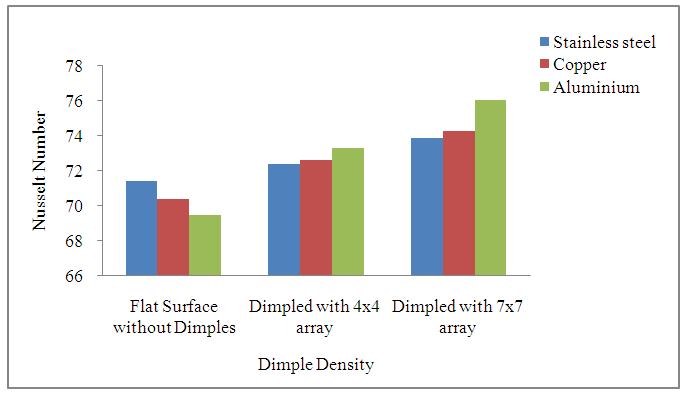 | Figure 5. Variation of Nusselt Number with Reynolds Number |
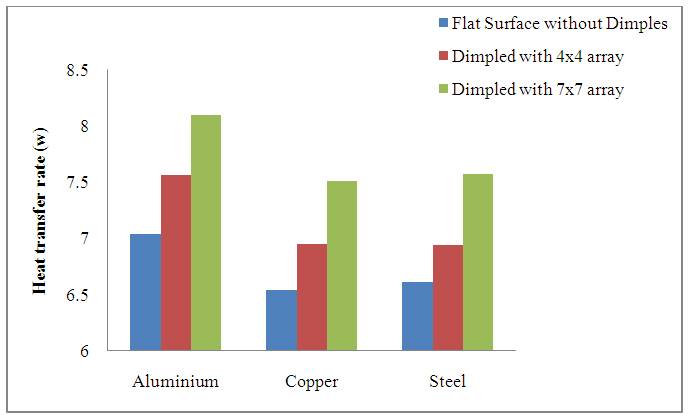 | Figure 6. Variation of Heat transfer rate (kJ) |
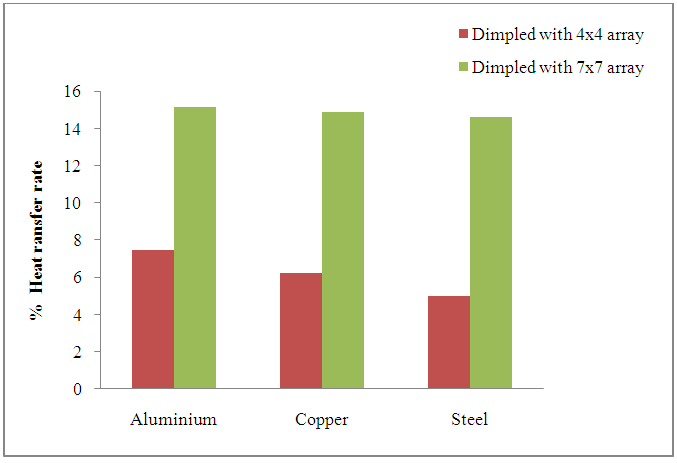 | Figure 7. Variation of Percentage of Heat transfer rate |
4. Conclusions
The study concludes that more heat transfer enhancement on dimpled surfaces with lesser pressure drop penalty is obtained. Heat transfer rate from the test surface increases with increase in Reynolds number of flowing fluid and heat input. The use of dimples on the surface results in heat transfer augmentation in forced convection heat transfer with lesser pressure drop penalty. The more number of dimples increase the strength and intensity of vortices and associated secondary flows. The results shows an increase in heat transfer rate for dimpled surfaces with 4x4 array as 7.46%, 6.23% and 5.13% for Al, Cu and Stainless steel plates, where as it was 15.12%, 14.85% and 14.63% for 7x7 array compared to smooth surface.
References
[1] | M. A. Dafedar, Mujtabalayeeq I, Mohemmed Taher M, Mohammad Idressurf Shahid I Heat Transfer Enhancement Through Different Circular Diametrical Dimple Surface Under Forced Convection –An Experimental Approach, IJRET: International Journal of Research in Engineering and Technology e ISSN: 2319-1163 | ISSN: 2321-7308, Volume: 02 Issue: 07 | Jul-2013. |
[2] | Iftikarahamad H. Patel, Dr. Sachin L. Borse, Experimental Investigation Of Heat Transfer Enhancement Over The Dimpled Surface, International Journal of Engineering Science and Technology (IJEST), ISSN: 0975-5462 Vol. 4 No.08 August 2012. |
[3] | Saurabh R Verma P. M. Khanwalkar, V. N. Kapatkar, A Review on Heat Transfer Augmentation for Various Dimpled Geometries, International Journal on Theoretical and Applied Research in Mechanical Engineering (IJTARME), ISSN: 2319-3182, Volume -4, Issue-1, 2015. |
[4] | S. D. Hwang, H. G. Kwon, H. H. Cho, “Local heat transfer and thermal performance on periodically dimple-protrusion patterned walls for compact heat exchangers,” Energy, 2010, vol. 35, pp. 5357-5364. |
[5] | Moon, H.K, O Connell, T. and Glezer, B."Channel Height Effect on Heat Transfer and Friction in a Dimpled Passage" J of Eng. For Gas Turbines and Power, Vol.122, pp.307-313, 2000. |
[6] | Amjad Khan, Mohammed Zakir Bellary, Mohammad Ziaullah, Abdul Razak Kaladgi, An Experimental Study on Heat Transfer Enhancement of Flat Plates Using Dimples, American Journal of Electrical Power and Energy Systems, ISSN: 2326-9200, May 28, 2015. |