N. Amulya1, PVS Subhashini1, K. Chinmayi1, Naveen R.2
1Department of Mechanical Engineering, Vasavi College of Engineering, Hyderabad, India
2Department of Mechanical Engineering, St Joseph Engineering College, Mangaluru, India
Correspondence to: N. Amulya, Department of Mechanical Engineering, Vasavi College of Engineering, Hyderabad, India.
Email: |  |
Copyright © 2016 Scientific & Academic Publishing. All Rights Reserved.
This work is licensed under the Creative Commons Attribution International License (CC BY).
http://creativecommons.org/licenses/by/4.0/

Abstract
Heat generation in any machining operation is related to the plastic deformation and friction. The three main sources of heat generation are due to plastic deformation by shearing in the primary shear zone, plastic deformation by shearing and friction on the cutting face, friction between chip and tool on the tool flank. Because of this heat generation, the life of the tool will be reduced, indirectly increasing the cost of production. In order to avoid these disadvantages it is necessary to minimize the generation of heat. These are various techniques available to control the heat generation. One of the method is to optimize the cutting parameters by varying speed, feed, depth of cut. This paper aims to minimize the heat generated in turning operation by optimizing the cutting parameters. To optimize these an TLBO (Teaching-Learning-Based-Optimization) algorithm is used and validated with genetic algorithm.
Keywords:
Heat generation, Turning process, Parametric optimization, Teaching-Learning-Based-Optimization, Genetic algorithm
Cite this paper: N. Amulya, PVS Subhashini, K. Chinmayi, Naveen R., Parametric Optimization of Heat Generation during Turning Operation, Journal of Mechanical Engineering and Automation, Vol. 6 No. 5A, 2016, pp. 117-120. doi: 10.5923/c.jmea.201601.22.
1. Introduction
During orthogonal cutting at speed ranging between 200 and 1200 m/min temperature measurements are presented experimentally. These measured temperatures are compared with temperature fields in the cutting tool obtained from a finite element transient thermal analysis.It is shown that the tool-chip contact area and the proportion of the secondary heat source conducting into the tool changes with cutting speed; it decreases with the cutting speed in the conventional and the transition regions but increases in the HSM region approaching 65% at 1200 m/min. During the machining operation on 27MnCr5 steel work piece an effective heat flux has been transmitted on to the work piece and is measured by thermocouple fixed to the insert holder.Now the inverse heat conduction problem is solved so as to eliminate the heat flux transmitted into the tool for various tested coatings but the direct measurement can’t be done from tool-chip-work piece because of small contact areas and cutting movements. Due to these difficulties researchers have developed many other modeling techniques like slip line solutions which is an analytical technique, the boundary-element method of heat conduction, empirical approaches and method of heat conduction and finite element techniques. These techniques helped to make a parametric study to investigate the effect of operating conditions on the thermal behaviors of chip, tool and the work piece and the heat conduction model helps to predict the temperature distribution in chip, tool and work piece.Tungsten carbide was considered as cutting tool-tip material. Adding to that model takes the geometry of the chip, tool and work-piece, convective losses, temperature dependent thermo-physical properties of the material into consideration. Majorly depth of the cut and cutting speed are the factors which effects heat generation and distribution of temperatures. It has been noticed that maximum temperature in the tool is increased from 709.36K to 1320K as cutting speed is increased from 29.6 m/min to 155.4 m/min.A series of numerical simulations had been done by (Hong et al, 2005), to investigate the effect of machining parameters like cutting speed, depth of cut and tool-tip radius and on the finish hard turning AISI H13 steel using finite element model. From these results it is noticed that maximum work piece temperature increases from around 646 to 922.78C, the maximum tool temperature increases from 147.6C to 406.78C when the cutting speed increased from 150 to 750 m/min. [1]
2. Need for Optimization
Previously there are few optimization techniques used by researchers such as fuzzy logic, neural network, simulated annealing etc. these methods are used for both single and multi-pass turning operation problems.A feed-forward neural network is used for solving the multi-objective problems which involved operation cost, cutting cost and productivity.As on record there are few more advanced optimization techniques like the ant colony algorithm, simulated annealing, genetic algorithms, and particle swarm optimization etc. but it was proven that all these techniques are not handled properly and finally ended up with inaccurate results.All the methods mentioned above are algorithm based and need algorithm specific control parameters along with common controlling parameters like number of generation and population size. For example, the genetic algorithm uses mutation and crossover rates. Similarly, particle swarm optimization uses inertia weight, and social and cognitive parameters. Ant colony optimization involves in setting of random walk and trail diffusion. Simulated annealing also requires fine setting of initial temperatures, which effects in optimum solution. The above methods are based on algorithms so it requires proper turning of parameters which are very important. The improper turning of algorithm specific parameters effects either in increasing of computational efforts or yields the local optimum solution.
3. Input Data
An equation is considered to reduce heat generation in turning operation.Q = 1.68df 0.15V0.85Cutting speed(v)= 15-19 m/minDepth of cut(d)=0.5-1 mmFeed rate(f)=0.2-0.8 mm/revThe equation consists of three parameters namely cutting speed, depth of cut and feed rate. [2]Table. 1 presents the cutting speed data of various materials for operation like turning, threading, drilling and reaming. In present work turning operation data is used for the cast iron material.Table 1. Cutting Speed (M/Min) 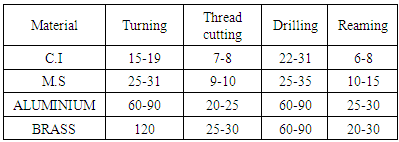 |
| |
|
Table. 2 presents the feed and depth of cut of various materials.Table 2. Feed and Depth 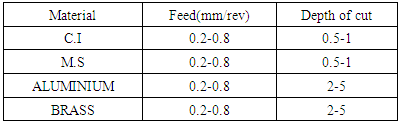 |
| |
|
4. TLBO & Genetic Algorithm
The Teaching–Learning-Based Optimization algorithm (TLBO) is a teaching–learning process inspired algorithm recently proposed, based on the effects of the influence of a teacher on the output of learners in a class.The algorithm mimics the teaching–learning ability of teacher and learners in a classroom. Teachers and learners are the two vital components of the algorithm, which describe two basic modes of learning, through the teacher (known as the teacher phase) and interaction with other learners (known as the learner phase). The design parameters are actually the parameters involved in the objective function of the given optimization problem and the best solution is the best value of the objective function. The teacher phase is the first part of the algorithm, where learners learn through the teacher. During this phase, a teacher tries to increase the mean result of the class room to his or her level. The learner phase is the second part of the algorithm, where learners increase their knowledge by interaction among themselves.The TLBO algorithm has been already tested on a large number of constrained and unconstrained benchmark functions and proved to be better than other advanced optimization techniques, like PSO, DE and ABC, etc. TLBO algorithm is used for the parameter optimization of a heat generation in turning process in this paper. [3]A genetic algorithm (GA) is a method for solving both constrained and unconstrained optimization problems based on a natural selection process that mimics biological evolution. The algorithm repeatedly modifies a population of individual solutions. At each step, the genetic algorithm randomly selects individuals from the current population and uses them as parents to produce the children for the next generation.An optimization based on genetic algorithms (GA) for the determination of the cutting parameters in machining operations is proposed as shown in fig.2. In order to find optimal cutting parameters during a turning process, the genetic algorithm has been used as an optimal solution finder. Process optimization has to yield minimum production time, while considering technological and material constrains. [4]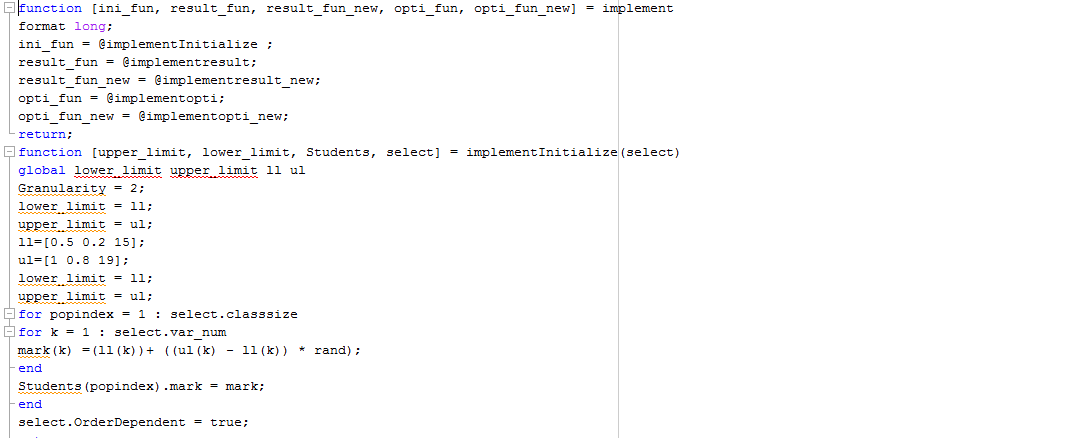 | Figure 1. Partial MATLAB program for TLBO algorithm |
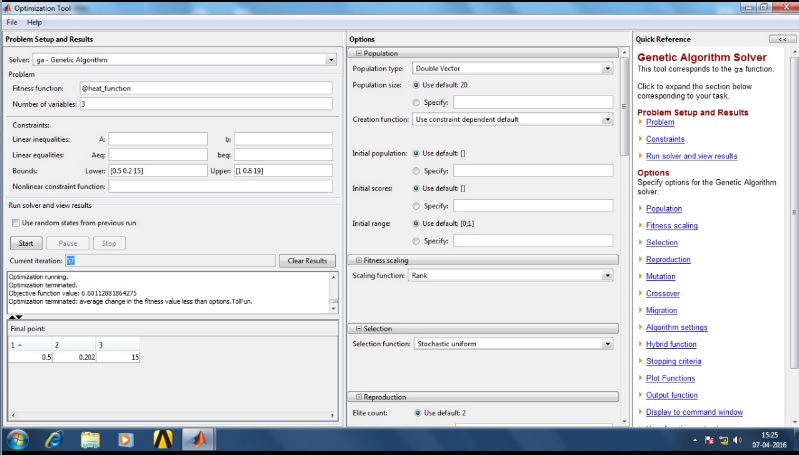 | Figure 2. Input table data for Genetic algorithm |
5. MATLAB Programming
MATLAB is an interpreted language for numerical computation. It allows one to perform numerical calculations, and visualize the results without the need for complicated and time consuming programming. MATLAB allows its users to accurately solve problems, produce graphics easily and produce code efficiently.
6. Result
The result after executing TLBO and Genetic algorithm is shown in table 3Table 3. Result 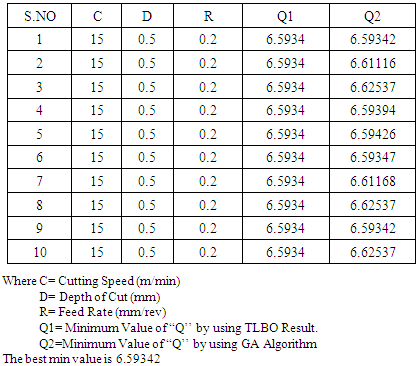 |
| |
|
This result table contain values of cutting speed, feed and depth of cut. Minimum value of Q is obtained by using TLBO and genetic algorithm. All these values are run in MATLAB using TLBO and GA. Among them best minimum values is 6.59342.
7. Conclusions
In present paper, optimization aspects of process parameters of a heat generation in turning operation is considered using a recently developed advanced algorithm known as the teaching-learning-based optimization algorithm. Two different programs are considered, out of which one is TLBO and the second is a genetic algorithm multi-constrained problem.Already program has been written in MATLAB using TLBO algorithm. An equation is considered to reduce heat generation in turning operation considering the valves of feed, depth of cut, and cutting speed. The program is run by taking 10 different values among them the best minimum optimized value is 6.59342.
ACKNOWLEDGEMENTS
We acknowledge our thanks to management of vasavi college of engineering and teqip-ii for sponsoring us to present paper.
References
[1] | Abdil Kush et.al. “Thermocouple and Infrared Sensor-Based Measurement of Temperature Distribution in Metal”, Sensors (Basel) 2015 Jan 12; 15(1): 1274-91. |
[2] | G.krishanaiah et al. parametric analysis and multi objective optimization of cutting parameters in turning operation of AISI4340 alloy steel with CDV cutting tool. IJIET, volume 2, Issue 9, March 2013. |
[3] | R. Venkata Rao et.al. Parameter optimization of machining processes using teaching–learning-based optimization algorithm, Springer, March 2012. |
[4] | Arun Tom Mathew, et al. Implementation of Genetic Algorithm to Optimize the Assembly Sequence Plan Based on Penalty Function. ARPN Journal of Engineering and Applied Sciences. Vol. 9, No. 4, April 2014. |
[5] | L Babhang, et al. Parametric Optimization of Machining Parameters using Graph Theory and Matrix Approach. (AIMTDR 2014) December 12th–14th, 2014, IIT Guwahati, Assam, India. |
[6] | K.A. Patel et al. Experimental Investigation of welding distortion of Austenitic Stainless Steel 316 in TIG Welding. IJEDR 2015, Volume 3, Issue 2. |
[7] | Jagtar Singh et al Effect of Cryogenic Treatment on Microstructure of T-15 Tool Steel, IJESRT, December, 2015. |