PVS Subhashini1, NVS Raju2, G. Venkata Rao1
1Department of Mechanical Engineering, Vasavi College of Engineering, Telangana, India
2Department of Mechanical Engineering, JNTUH, Telangana, India
Correspondence to: PVS Subhashini, Department of Mechanical Engineering, Vasavi College of Engineering, Telangana, India.
Email: |  |
Copyright © 2016 Scientific & Academic Publishing. All Rights Reserved.
This work is licensed under the Creative Commons Attribution International License (CC BY).
http://creativecommons.org/licenses/by/4.0/

Abstract
SCARA (Selective Compliance Articulated Robot Arm) is a well-developed manipulator with 4dof (3 revolute &1 prismatic) used specially for pick & place applications. The aim of the paper is to present the verification of the kinematics of a customized SCARA robot for deburring application comparing video graphic analysis with MATLAB analysis. Video graphic analysis is a technical analysis done by the visual observation method by slow motion replay and by freezing the frame. MATLAB analysis is based on the mathematical equations of the SCARA robot. A video is recorded from the customized SCARA robot developed for deburring application. The present application is programmed for rectangular path. Using video graphic analysis angular displacements of joint 1 & joint 2 are calculated, further using differentiation method angular velocities & angular accelerations of joint 1 & joint 2 is derived respectively. As SCARA kinematics are well available in the literature those equations are used for MATLAB analysis. Angular displacements, angular velocities, angular accelerations are calculated using MATLAB. For verification of the kinematics of a SCARA robot a comparison is made between the video graphic analysis & MATLAB and observed that both the analysis are yielding the same results.
Keywords:
Deburring, Kinematics, MATLAB, Rectangular path, SCARA, Video graphic analysis
Cite this paper: PVS Subhashini, NVS Raju, G. Venkata Rao, Videographic Analysis of a SCARA Robot for Deburring of Rectangular Path, Journal of Mechanical Engineering and Automation, Vol. 6 No. 5A, 2016, pp. 109-112. doi: 10.5923/c.jmea.201601.20.
1. Introduction
SCARA is well established manipulator with 3 revolute and 1 prismatic joint. Kinematics and dynamics of a SCARA robot are well available in the literature [1-3]. SCARA is widely used because of its advantages such as high accuracy, precision and smooth in operation. Applications of the SCARA involve pick and place, assembly, drilling, deburring etc.Figure 1 presents the customized SCARA manipulator which is used for deburring operation, Figure 2 presents the deburring of rectangular component by the customized SCARA robot.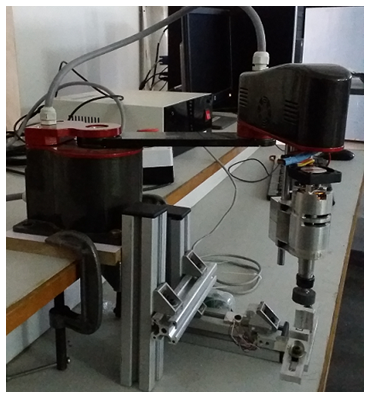 | Figure 1. Customized SCARA robot |
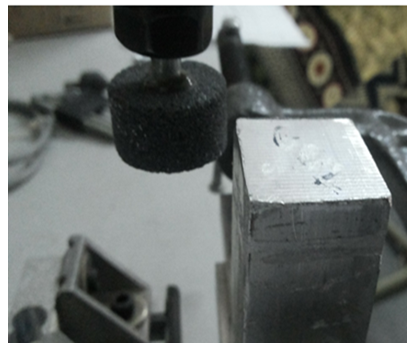 | Figure 2. Deburring of rectangular component |
SCARA manipulator behaves as a human arm, joints of the manipulator helps it to move vertically and horizontally. SCARA arm has limited motion at the wrist i.e. it can rotate but cannot tilt. The limited motion of the wrist is advantageous for many types of assembly operations, such as pick-and-place, assembly, and packaging applications. Figure 3. presents the schematic representation of a SCARA robot. In the present work 2-dof of SCARA robot i.e. joint 1 and joint 2 is used for kinematic verification. Here kinematics include angular displacement, angular velocity, angular accelerations of joint 1 and joint 2 respectively.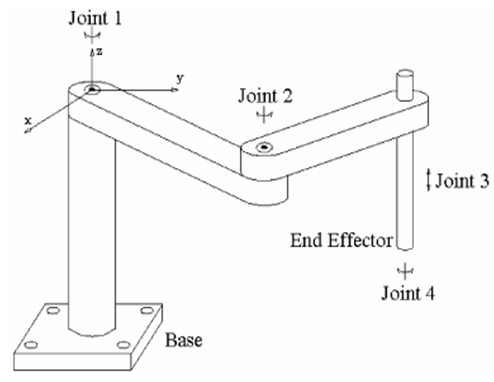 | Figure 3. Schematic representation of SCARA robot |
The SCARA configuration has a work volume that can be closely resembled to heart or kidney shaped prism and is shown in the Figure 4, having a circular hole passing through the middle. This allow a large area coverage in the horizontal plane but relatively little in the vertical plane.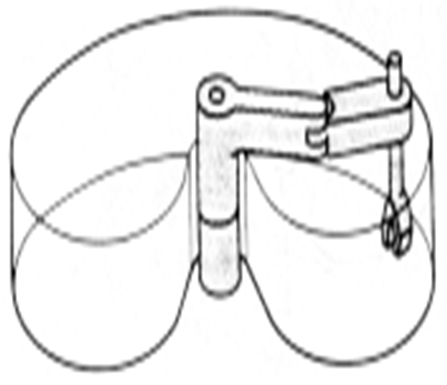 | Figure 4. Work volume of a SCARA robot |
In the present work kinematic equations are programmed in the MATLAB, in video graphic analysis kinematics are computed using time derivative process.The rest of the paper is organized as Data used for the work, Video graphic analysis, Kinematic validation of the SCARA robot, and conclusion.
2. Data Used
Link lengths of the customized robot are link 1=0.200m and link 2=0.150m. The data used produces rectangular path. Figure 5 presents the schematic representation of top view of a SCARA robot used for rectangular path. Here L1 and L2 represents the link length of joint 1 and joint 2 respectively.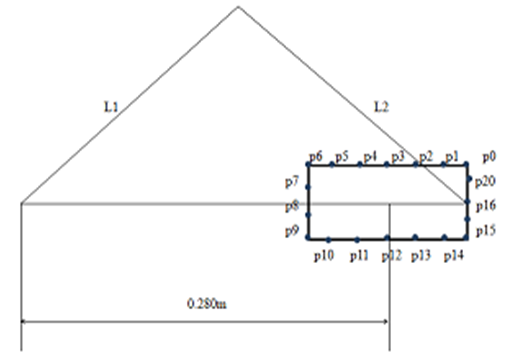 | Figure 5. Schematic representation of SCARA robot for rectangular path |
Table 1 is the input data used for MATLAB analysis. PX and PY are the position of the workpiece in the x and y axis where VX, VY, AX and AY are obtained by differentiating PX and PY values with respect to time which represents the respective velocities and accelerations.Table 1. Input data 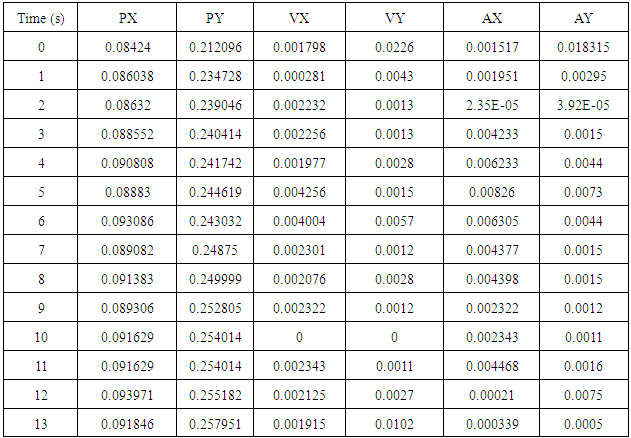 |
| |
|
3. Video Graphic Analysis
Video graphic analysis is a technical analysis [4-6] done by the visual observation method by slow motion replay and by freezing the frame as and when required.In the present work a video is recorded when the deburring of SCARA robot is done. Then virtual protractors are placed on the two joints of SCARA manipulator. These virtual protractors move relative to the motion of the links. The recorded video is imported and analyzed in the VLC player.The purpose of the analysis is to measure the joint angles of the SCARA robot while deburring operation is done, Virtual protractors of the SCARA robot while performing the deburring operation are as shown in the figure 6. The complete deburring operation for one cycle tool is 51 seconds. Therefore, the joint angles of the links are measured with a step length of 1 second. Joint angles of link 1 and link 2 are computed using these virtual protractors and angular velocities and angular accelerations of joint 1 and joint 2 are computed using differentiation method.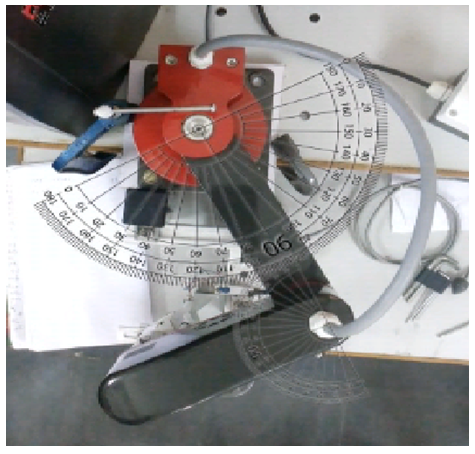 | Figure 6. Top view of SCARA robot withvirtual protractors |
4. Kinematic Analysis of a SCARA Robot
This section presents kinematic validation of a SCARA robot done in video graphic and MATLAB analysis. Figure 7 presents angular displacement of joint 1 with respect to time, from this it is observed that there is no difference between the results obtained from the video graphic analysis and mathematical analysis done in MATLAB. 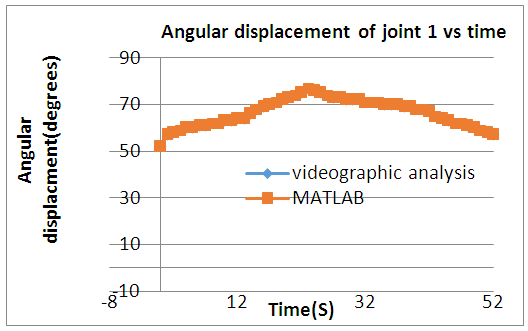 | Figure 7. Angular displacement of joint 1 vs time |
Figure 8 presents angular displacement of joint 2 with respect to time. Figure 9 presents angular velocities of joint 1 with respect to time, Figure 10 presents angular velocities of joint 2 with respect to time, Figure 11 presents angular acceleration of joint 1 with respect to time, Figure 12 presents angular acceleration of joint 2 with respect to time. From all these graphs it is observed that both video graphic analysis and MATLAB are yielding same results. So further placement analysis for rectangular component is carried out in MATLAB.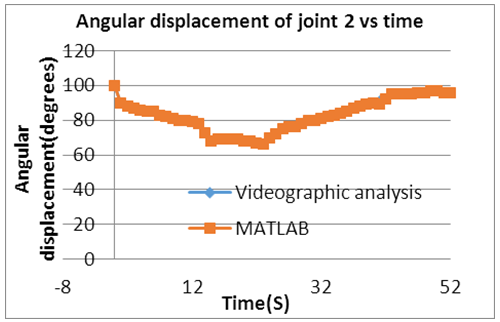 | Figure 8. Angular displacement of joint 2 vs time |
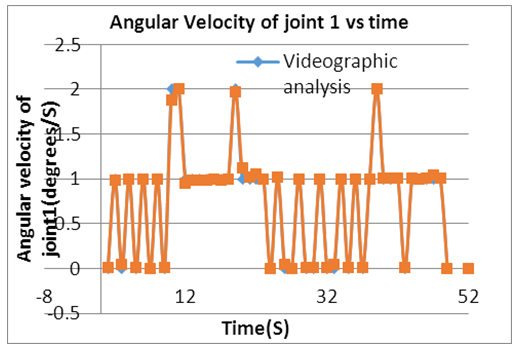 | Figure 9. Angular velocity of joint 1 vs time |
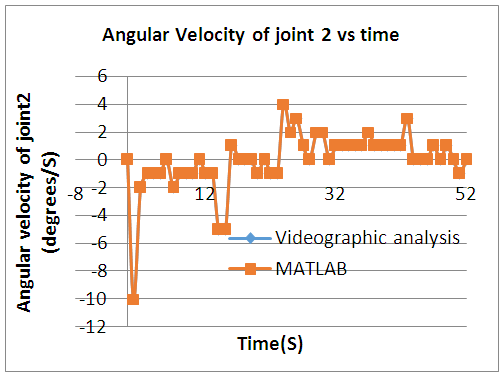 | Figure 10. Angular velocity of joint 2 vs time |
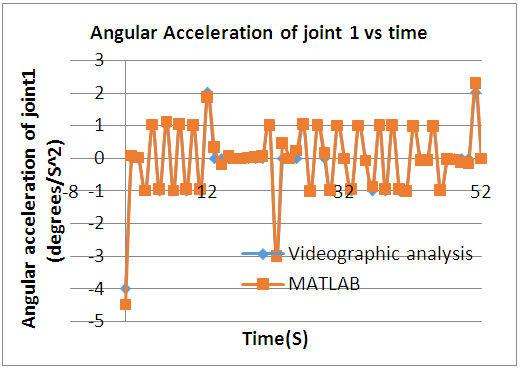 | Figure 11. Angular accelaration of joint 1 vs time |
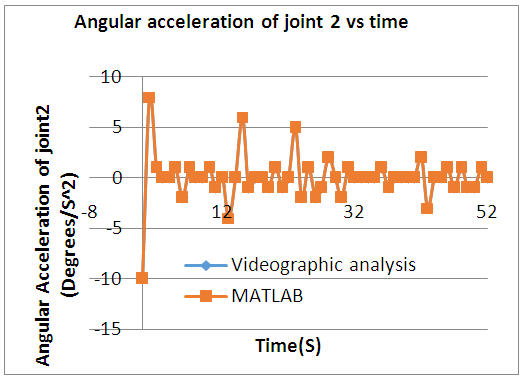 | Figure 12. Angular accelaration of joint 2 vs time |
From all the above figures it is observed that the results of videoggraphic analysis and mathematical analysis are same. So the kinematics of the SCARA robot are verified for further analysis.
5. Conclusions
In the present work, for verification of the kinematics of a SCARA robot video graphic analysis and MATLAB are used. It is observed that video graphic and MATLAB analysis are yielding the same results. Further work can be extended for positional analysis of a rectangular component with in the work volume of a SCARA robot.
ACKNOWLEDGEMENTS
We acknowledge our thanks to UGC (Minor research project) for granting us this project. We also thank our Management and TEQIP-II for sponsoring to attend this conference.
References
[1] | Jian Fang and Wei Li “Four degrees of freedom SCARA robot kinematics modelling and simulation analysis” International Journal of Computer, Consumer and Control (IJ3C), Vol. 2, No.4,Pages 20-27 (2013). |
[2] | Talib EH. Elaikh, Haider J. Abed, Kadhim M. Abed, Salah M. Swadi, Kadhim Karim M “Vibration and Kinematic Analysis of SCARA Robot Structure” Diyala Journal of Engineering Sciences” Vol. 06, No. 03, September, Pages 127-143(2013). |
[3] | Yousif I. Al Mashhadany “Design, Analysis, Simulation, and Virtual-Reality-Verified Intelligent Controller for Industrial-Application SCARA Robot” International Journal of Advanced Computing, Vol.46, No.3, Pages 1316-1325 (2013). |
[4] | Gates, J. W. C “High speed photography” Review optica Acta: International jounal of optics Vol.25, No5, 197. |
[5] | Fielda, J. E “High speed photography”, Contemporary Physics Volume 24, No.5, Pages. 439-459(1983). |
[6] | George H. lunn, “high speed photography”, Review article, Nature 291, Pages 617-619 (1981). |