Swaraj D. Lewis, Noel D. Shiri, Vikesh K., Sonali C. Olivera, Vishram Konde, Prakash C. Dsouza
Department of Mechanical Engineering, St Joseph Engineering College, Mangaluru, India
Correspondence to: Swaraj D. Lewis, Department of Mechanical Engineering, St Joseph Engineering College, Mangaluru, India.
Email: |  |
Copyright © 2016 Scientific & Academic Publishing. All Rights Reserved.
This work is licensed under the Creative Commons Attribution International License (CC BY).
http://creativecommons.org/licenses/by/4.0/

Abstract
The Hoverbike prototype is one-third scaled model of full sized Hoverbike (manned). This is an attempt to develop a prototype having propellers that are driven electrically incorporating tilt motor mechanism, wherein servo motors are used to manoeuvre the model. The objective is to fabricate a light weight prototype that consists of a payload bay, achieve longer endurance and range, decrease the cost, utilise less power to achieve lift, provide longer battery life, reduce programming steps and be simple in design compared to the existing drones. Based on the idea of existing four propellers, a research based on trial and error methods was made to develop two propeller Hoverbike. The fabricated Hoverbike prototype had a weight of less than 1kg. It could fly at a range of around 800m within the range of remote control. An endurance of maximum 5-10 minutes was obtained. The payload obtained in case of two blade propeller was 0.3kgs and in case of three blade propeller was 0.5kgs.
Keywords:
Hoverbike, Tilt Motor Mechanism, Manoeuvre, Surveillance
Cite this paper: Swaraj D. Lewis, Noel D. Shiri, Vikesh K., Sonali C. Olivera, Vishram Konde, Prakash C. Dsouza, Fabrication and Testing of Scaled Prototype of Hoverbike, Journal of Mechanical Engineering and Automation, Vol. 6 No. 5A, 2016, pp. 71-74. doi: 10.5923/c.jmea.201601.13.
1. Introduction
A Hover bike can be defined as a combination between a motorcycle and a helicopter. That is it has the simplicity of a motorcycle and the freedom of a helicopter. Ideally, such a vehicle would be able to allow people to navigate the earth in a new and unique way. The Hoverbike flies like a quadcopter, and can be flown manned or unmanned, while being a safe level - low level aerial workhorse with low on – going maintenance. It is easy to operate and can be applied to various purposes because it does not need a runaway and is capable of hovering from any terrain. For this reason, the military has shown continued interest in hover vehicles. A Hover bike is mobile and can be deployed rapidly. Also, it is aerodynamically efficient because the lift generated by the duct can create a thrust force that is higher than the other VTOL (vertical and/or short take-off and landing) vehicles, which have no duct and therefore no hovering flight mode. In the case of the ducted-fan type flying bike, its rotor is covered with duct which lowers the risks of rotor damage caused by tiny bugs and foreign object. To date, there are no commercially viable Hoverbike being built, though some test prototypes do exist and are in development [1].
2. Literature Survey
The original Hoverbike was built by Chris Malloy of New Zealand, after work and studies in his garage in suburban Sydney, Australia. His project started out as a hobby, but quickly grew into a commercial enterprise, with interest from people and group such as universities, farmers, military, with notable visits from US Army G-3/5/7 and Lockheed Martin’s ‘Skunk Works’. Most of the frame of original Hoverbike was handcrafted from carbon fibre and aluminium with a foam core [2].
2.1. Design and Development of Prototype of Hoverbike by Students of SCE, Karnataka
Dr. E Madhusudhan along with his students developed a Hoverbike which was a flying motorised machine designed to fly with four mini helicopter blades. They used chopper as the basis for their Hoverbike. The propeller was located three feet away from the normal surface.The experiment was attempted three times and later decided not to run because of unprotected housing. The prototype failed due to maximum stress [4].
2.2. Flying Hoverbike, a Small Aerial Vehicle for Commercial or Surveying Purpose
Madhan Kumar in his paper discussed the modelling of a ducted fan Flying Bike. It is a compact aerial vehicle with a ducted fan configuration which can able to survey and spy the surroundings and also a simple design is used for commercial purposes like a motor bike. It consists of coaxial type of propeller mounted on a high speed brushless electric motor and powered by rechargeable Li-Po fuel cells. It is designed with a ducted fan so that the slip of air is less. Hence its aerodynamic efficiency is high. Moreover it can able to take off and land vertically from any terrain. The cost of the bike was very high [5].
3. Objectives
Designing of scaled prototype of Hoverbike powered by battery source mounted with propellers. Rudders or tilt motor mechanism is used for optimal manoeuvring. Selection of light weight materials for the construction. Fabrication of light weight prototype to achieve lift. Testing of fabricated prototype and determining the range, endurance and payload results. To be made use for general purpose applications.
4. Devices and Specifications
Table 1. Devices Used and Their Specifications 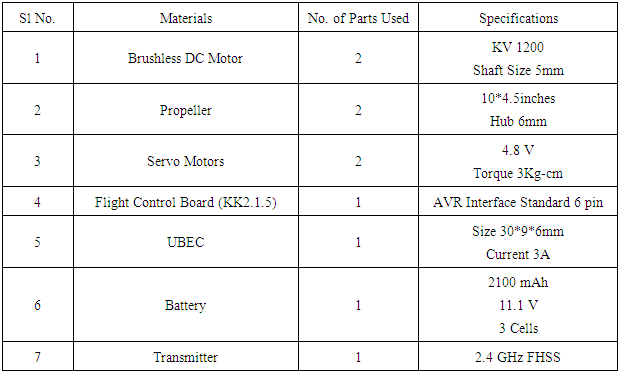 |
| |
|
5. Standard of Equipments
5.1. Flight Control Board
The control board controls the automatic regulation of Hoverbike balance with the gyroscope induction system. The KK2.1.5 is packed with new found power with updated sensors, memory and header pins.
5.2. ESC
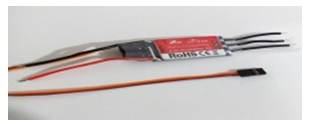 | Figure 1. Electronic Speed Controller |
An ESC is an electronic circuit with the purpose to vary electronic motor speed. The throttle of each ESC is controlled by a separate channel and has a gyro between the receiver and ESC.
5.3. UBEC
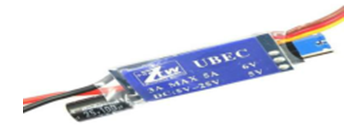 | Figure 2. Universal Battery Eliminating Circuit |
A “Universal Battery Elimination Circuit” is an external electronic circuit that taps power from motor’s battery pack and regulates the voltage down to the necessary 5 or 6 volts for the receiver and servos.
6. Equations
 | (1) |
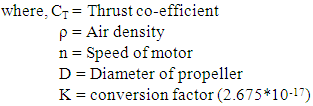
7. Design
7.1. Frame Design 1
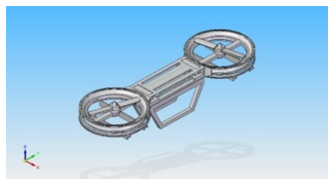 | Figure 3. Initial fabricated prototype |
Based on the calculations, a CAM sketch of the prototype was designed. Assuming the weight of the model, initially wooden strip was selected for frame and rudders. Four servo motors were connected to each rudder. During the first test, model didn’t lift from the ground as the weight of the model exceeded 1kg.
7.2. Frame Design 2
For the second design, two servo motors were used to reduce the weight where two pair of rudders on either end was operated by just two servo motors with the help of linkages. During the test the model used to flip towards either left or right and would crash just after takeoff because of instability. This was due to the lesser surface area of the rudders.
7.3. Frame Design 3
For the third design test, to increase the stability, the surface area was increased by providing ultra light plastic duct which increased the weight of the model by some amount. The flight was unstable again so we dropped the idea of rudders.
7.4. Frame Design 4
For the fourth design, to gain better performance, the concept of tilt motor using servo motors was used. Two servo motors were used to tilt the DC motors on either end for the desired angle during flight. These servo motors were connected to the DC motors using linkages. Reprogramming was done. The stability slightly increased. In order to improve the stability further, we tested for many trails, each time implementing new changes.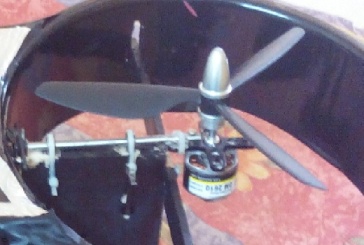 | Figure 4. Tilt motor mechanism |
7.5. Frame Design 5
For the fifth model, to provide safe landing, an inverted T shaped stand with certain length and height from the ground was fixed to the prototype and was attached to the frame as shown in the figure which lifted the model by 10cm from the ground. The stand was made up of aluminum and thermocole was added at its bottom for the smooth landing. During flight there was oscillations created by the stand which used to increase for each cycle which caused the model roll uncontrollably and crash.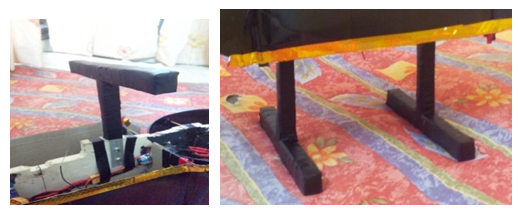 | Figure 5. T Stand |
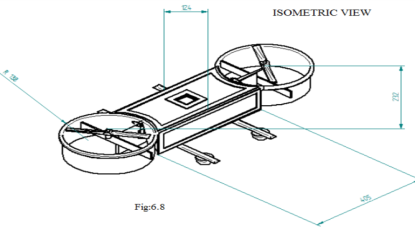 | Figure 6. 2D model with dimensions |
7.6. Frame Design 6
For the sixth design, to achieve better stability and smooth landing, a stand made up of wood with larger length was directly attached to the wooden frame without providing any vertical distance from the frame to the ground which is as shown in figure below. Sponge balls at the ends were used to obtain smooth landing. The payload bay was created using ultra light cardboard material. The required stability was almost obtained.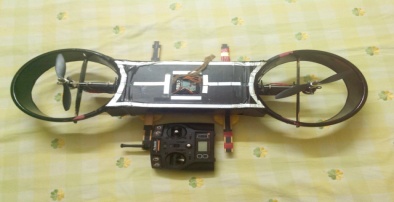 | Figure 7. Final fabricated Hoverbike |
8. Advantages and Disadvantages
The most obvious advantage of Hoverbike is its low cost, because it is significantly cheaper to purchase, fuel, and maintain than regular airplanes. Hoverbike is significantly easier and faster to deploy than most alternatives. It can perform precise, repetitive and hard tasks and can also fly in hostile conditions. Most importantly, it is smaller and can fly lower than traditional airplanes, therefore reducing the risk to military hardware.Unmanned vehicles may not have the same reaction time as manned vehicles. The flight actions are more difficult when using a camera and remote system. Battery power could be limited. Also the camera footage is not as reliable as the naked eye.
9. Applications
1. Used in Policing duties 2. Can be used Traffic spotting3. Sports events film coverage4. Aerial photography5. Surveillance of coastal borders, road traffic, etc. 6. Disaster and crisis management search and rescue. 7. Environmental monitoring.8. It has the ability to carry supplies if extraction is impossible. 9. The full scaled model could be used as a future mode of transportation.
10. Conclusions
The designed light weight Hoverbike could successfully achieve lift and stability during flight. It could fly at a range of around 800m within the range of remote control. An endurance of maximum 5-10 minutes was obtained. The payload obtained in case of two blade propeller was 0.3kgs and in case of three blade propeller was 0.5kgs. According to our model the fabricated design was suitable for general purpose and hence this fulfilled our goal.
ACKNOWLEDGEMENTS
We would like to convey our gratitude to all those who have provided guidance regarding our project at each and every stage. Our sincere gratitude to the management of SJEC for providing the necessary guidance and facilities.
References
[1] | Suraj G. Gupta, Mangesh M. Ghonge, Dr P M Jawandhiya, 2013, Review of Unmanned Aircraft System (UAS), (2), 1646 – 1658. |
[2] | Bulletin of defence research and development organization, 2010, Unmanned Aerial Systems and Technologies, 971(18), 569–571. |
[3] | David Glade, Lt Col, USAF, 2000, Unmanned Aerial Vehicles, Implications for Military Operations, Occasional Paper Center for Strategy and Technology Air War College, (16), 38. |
[4] | B. Lokesh, Navyashree, Karthik D C, Momon Singh, Dr E Madhusudhan, 2015, Design and Development of Prototype of Hoverbike, International Journal of Innovative Research In Science, Engineering and Technology, 5(4), 5. |
[5] | B. Madhan Kumar, 2013, Flying Hoverbike a Small Aerial Vehicle for Commercial or Surveying Purpose”, International Journal of Scientific and Engineering Research, 7(4), 4. |
[6] | https://quadcopterproject.wordpress.com/static-thrust-calculation/ |