Shreeranga Bhat1, Jnanesh N. A.2, Prashanth P. Kamath1, Rajat R. Nayak1, Nithin M. D’souza1
1Department of Mechanical Engineering, St Joseph Engineering College, Mangaluru, India
2Department Mechanical Engineering, KVG College of Engineering, Sullia, India
Correspondence to: Shreeranga Bhat, Department of Mechanical Engineering, St Joseph Engineering College, Mangaluru, India.
Email: |  |
Copyright © 2016 Scientific & Academic Publishing. All Rights Reserved.
This work is licensed under the Creative Commons Attribution International License (CC BY).
http://creativecommons.org/licenses/by/4.0/

Abstract
The objective of the research is to identify challenges in an automobile service center and to determine optimal solutions to improve the overall performance. More specifically the research has the following objectives: To increase the productivity using Lean strategy; To reduce the wastage, non-value added activities; To create an easy and simple work environment; To develop a 5S Auditing control system to sustain the improved process; To educate Janitorial level people about benefits of using Lean strategy. The research reported in this research is based on a single case study carried out in an organization using Lean PDCA (Plan-Do-Check-Act) approach, 5S tool and its applications to enhance the productivity. The root causes for the problem in the servicing of cars has been identified through the data based analysis at different stages in the research. The process parameters have been optimized and measured for sustainability in the process. Lean strategy resulted in reduced amount of energy and non-value added activities associated with its production processes. Further, research resulted in the creation of a visual workplace, which has enhanced the production atmosphere, and created a simple and easy process design to lay the foundation to a future of continuous improvement. As a result of this research, the productivity would increase by 15 cars/day, which would be a remarkable achievement for the organization. The research provides guidance to organizations regarding the applicability and importance of quality concepts. Organizations need to work continuously with development-orientated activities in order to survive; irrespective of how these activities are labeled. The research will also serve as a basis for further research in this area, focusing on practical experience of these concepts.
Keywords:
Lean Thinking, PDCA, 5S, Automobile Service Industry
Cite this paper: Shreeranga Bhat, Jnanesh N. A., Prashanth P. Kamath, Rajat R. Nayak, Nithin M. D’souza, Enhancing the Performace of an Automobile Service Industry: Lean Thinking Approach, Journal of Mechanical Engineering and Automation, Vol. 6 No. 5A, 2016, pp. 40-48. doi: 10.5923/c.jmea.201601.08.
1. Introduction
1.1. Lean Services
The service sector is concerned with the soft part of the economy; where people render their time, skills and technical know-how to enhance productivity and performance. Producing services require relatively less of natural capital but more of human capital than agricultural or industrial goods. In line with the global trend, service sector in India has also grown rapidly in the last decade. Its growth has in fact been higher than the growth in agriculture and manufacturing sector. It now contributes around 51 percent of GDP. In the trade mode, services trade has also grown at the same rate as goods trade over the 1990s (i.e., about 6.5 per cent) and its share in total trade has reached around 24 per cent [1].Guiding principles for Lean management include: • Defining value from the standpoint of the end customer.• Identifying each step in a business process and eliminating those steps that do not create value.• Making the value-creating steps occur in tight sequence.• Repeating the first three steps on a continuous basis until all waste has been eliminated.Working from the perspective of the client who consumes a product or service, "value" is any action or process that a customer would be willing to pay for. Lean also takes into account waste created through overburden ("Muri") and waste created through unevenness in workloads ("Mura"). Working from the perspective of the client who consumes a product or service, "value" is any action or process that a customer would be willing to pay for. The concept of Lean can be traced back to Japanese industries. Toyota was the first company to successfully implement Lean in their car manufacturing systems [2].Essentially, Lean is centered on making obvious what adds value by reducing everything else. Lean manufacturing is a management philosophy derived mostly from the Toyota Production System (TPS) (hence the term Toyotism is also prevalent) and identified as "Lean" only in the 1990s. TPS is renowned for its focus on reduction of the original Toyota seven wastes to improve overall customer value, but there are varying perspectives on how this is best achieved. The steady growth of Toyota, from a small company to the world's largest automaker, has focused attention on how it has achieved this success [3].Service processes tend to have long cycle times, many complex variables, multiple decision points and interactions with a variety of computer systems and much of the value-added work does often take place out of sight, in peoples’ minds that makes Lean philosophy and tools a great fit and can be of huge benefit for services industries. Since service processes are not physically observable, especially useful are tools like visual management that make otherwise invisible work processes visible, and techniques that specifically develop a team member’s creative problem-solving and critical thinking abilities to the fullest [4].
1.2. Background and Motivation
The service sector is concerned with the soft part of the economy; where people render their time, skills and technical know-how to enhance productivity and performance. Producing services require relatively less of natural capital but more of human capital than agricultural or industrial goods. In line with the global trend, service sector in India has also grown rapidly in the last decade. Its growth has in fact been higher than the growth in agriculture and manufacturing sector. It now contributes around 51 percent of GDP. In the trade mode, services trade has also grown at the same rate as goods trade over the 1990s (i.e., about 6.5 per cent) and its share in total trade has reached around 24 per cent [2].
1.3. Problem Discussion
Infrastructural needs in rural as well as urban areas are inadequate to cater to different industries. Problems like power and water shortage are still prevalent and are detrimental to the industry’s growth.Service sector has been considered as the fastest growing sector in the last decade and has contributed more than 57% of the GDP. Despite that, it has been responsible for the creation of only 25% of the total employment.Customer satisfaction is directly dependent upon the etiquettes and behavior towards the customers. These are the hallmarks of a good service industry.Unfair competition, lack of incentives, high interest rates, improper forecasting mar the growth of commerce.
1.4. Problem Formulation
Value Stream Mapping has been used to define the problem. It has been used to analyze the current state and also to propose a future state. Value Stream Map takes into account not only the activity of the product, but the management and information systems that support the basic process. This is especially helpful when working to reduce cycle time, because one can gain insight into the decision making flow in addition to the process flow [3, 5].
1.5. Aim and Objectives
Aim:To apply the concepts of Lean into service industry to reduce wastes and consequently improve the production time.Objectives:• To improve the productivity and performance of the system through Lean Principle.• To improve the bottom line status of any one product which has adverse effect on the system performance.
2. Case Study
2.1. About the Industry
The organization is the first and Largest Dealership of Cars in India. Its parent company has nearly 75 years of experience in the Automotive Industry. The company has a strong culture of excellence in everything that it does. This has helped it earn tremendous loyalty from Customers, resulting in a large percentage of its business coming through references from the existing Customers. Today, it boasts of the largest network among all the dealers in Karnataka, with 5 Showrooms and 16 Sales Information Centers, 25 Workshops and 5 Showrooms for Used Car Sale. It has a team of over 2550 dedicated professionals committed to provide the best possible service to its customers.
2.2. Process Flow
Arrival of the vehicle: The car arrives at the entrance of the plant. Here, a Service Advisor is allotted to that car, who registers the customer’s complaints, if any, into a logbook, known as a Job Card. A test drive is conducted, along with the customer to identify run-time issues with the car. The technical problems are explicitly jotted down in the job card and an estimated delivery time is notified to the customer. A supervisor oversees the operations that the car undergoes, during its time in the plant.Washing: The car to be serviced is sent to the first stage wash. This serves two purposes: i) scratches and dents made prior to the servicing of the car can be known; ii) since the whole body of the car is washed free of dirt, servicing can be performed with considerable simplicity.Drying: Washed cars are dried with a high velocity jet of air to speed up the evaporation process. The body and interiors are then wiped with a clean cloth to completely remove remnants of water and dust particles.Process at Bay: The next step is taking the car to an available bay for processing. For those requiring oil replacement, the car is lifted up using hydraulic jacks to expose the underbody. Once that is done, other functions like wheel removal, repair of axle and leak checking can be performed with relative ease.Inspection: The processed cars now need to be scrutinized for errors. Accordingly, the inspectors are assigned to check for the blunders that might have been overlooked during the process at the bay. A second test drive may be conducted if major repairs have been performed; which also necessitates the second-stage wash.Dispatch: Finally, after the inspector’s consent, the car is all set to be delivered to the customer by the agreed upon time limit. The customer’s billing and transaction takes place in the office.
3. Results and Discussions
3.1. Plan
The first phase of the research involved finding the key areas in which changes and improvements had to be made. The process of analysis consisted of discussion, observation and extensive brainstorming of problems and the possible causes. As a result of this, the problems existing and the root causes were found out by various Lean analysis techniques. The key areas to be focused and the problems discovered were: Redundant motion of cars; Excess inventory; Downtime due to spares shortfall.The first analysis was done to find the root cause of Redundant Motion of Cars. For this analysis after consultation with the people involved in the process a root cause analysis was created. The table was categorized under People, Process, Tools, Management, Equipment and Inventory [6]. The Root Cause Analysis is shown in Table 1.Table 1. Root Cause Analysis 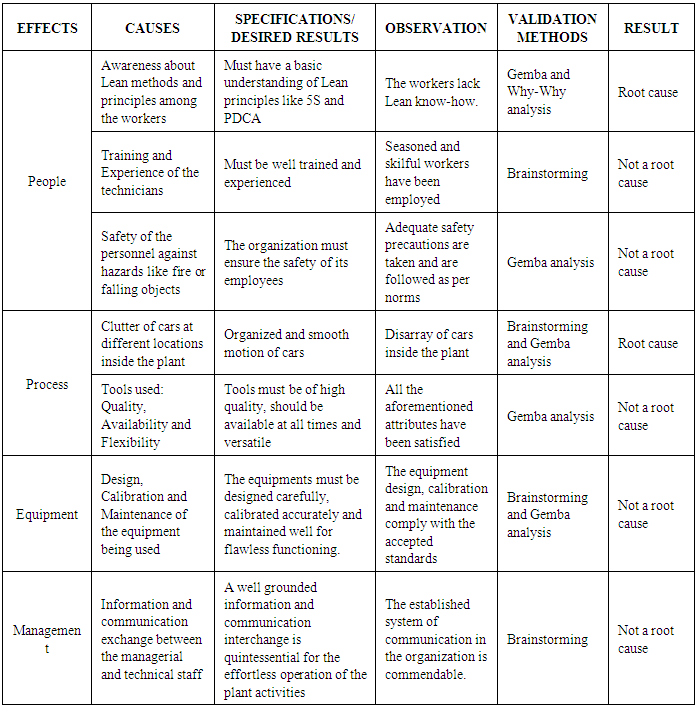 |
| |
|
Based on the root cause analysis for Redundant Motion of Cars Brainstorming and Gemba sessions were conducted which led to the discovery of two causes– Lack of Lean Awareness among the Workers; Clutter of Cars.The next step involved elaborating more on the problem of Lack of Lean Awareness among the Workers. There was a need to find what led to such a scenario and search for the possible causes. This step needed the use of the fish bone diagram (Fig 1, Fig. 2). It was categorized into People, Tools, Equipment, Process and Management. The probable causes were identified [6].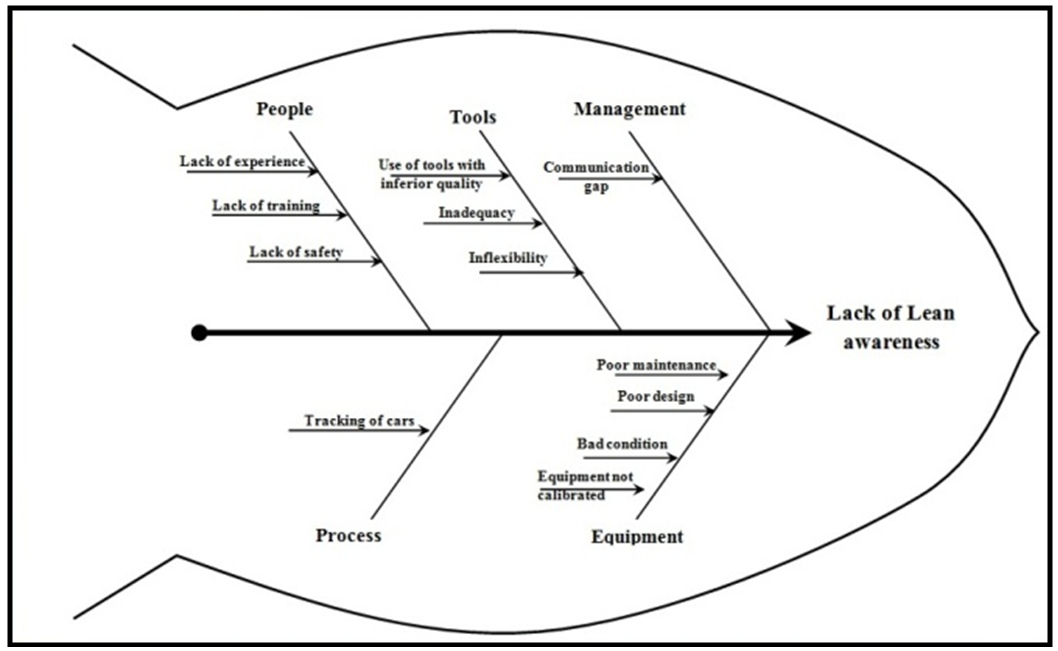 | Figure 1. Fish Bone Diagram for Lack of Lean Awareness |
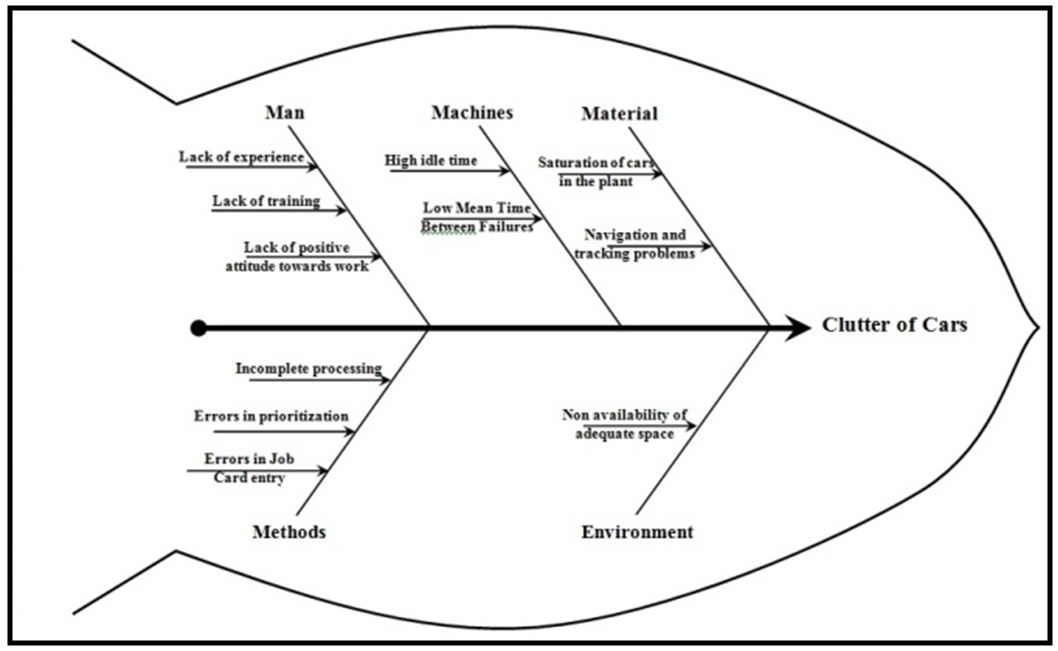 | Figure 2. Fish Bone Diagram for Lack of Clutter of Cars |
The second focus was given to the problem of Excess Inventory. To get a clear picture the problem solving technique used was Why-Why analysis. Why-Why analysis is a root cause evaluation technique which involves asking a series of the questions why to reach the source of the problem. The number of times the question “why” is asked depends on the arrival of the answer and does not have a minimum or maximum limit [5]. The analysis was thus done and three main causes for the existing problems were found. They are• Space constraint at parking area• Change in process lead time of the carsWhy-Why analysis is shown in Fig 3. The third emphasis was given on the Shortfall of Spares. A Why- Why Analysis was conducted to arrive at the solution (Fig 4). From the chart, it can be seen that the spares are not stockpiled in appropriate amounts. Also the damaged parts need to be checked for warranties, if any and suitable measures are to be taken to address the issue. This process consumes time, thus adding to the process lead time.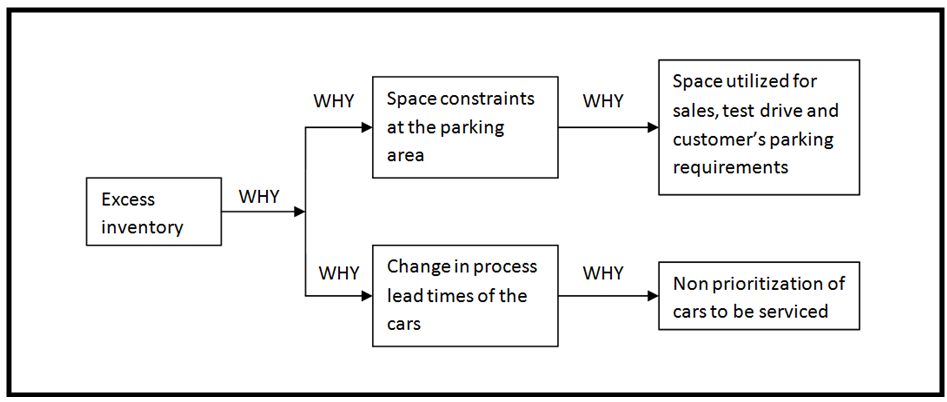 | Figure 3. Why-Why Analysis for Excess Inventory |
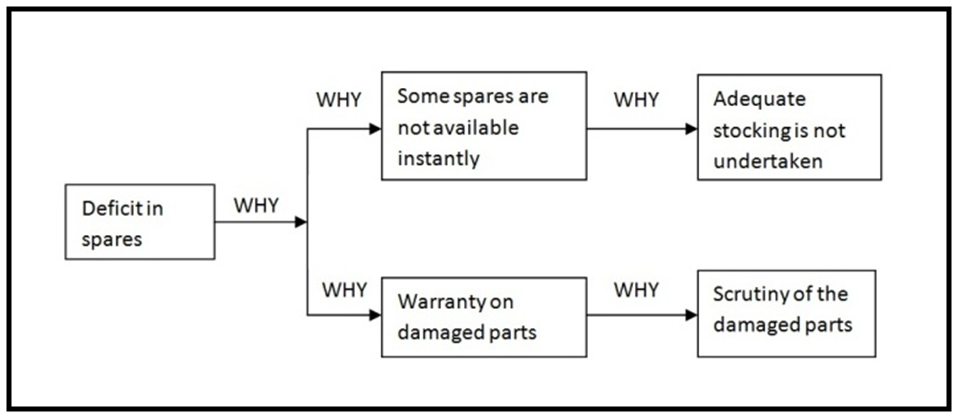 | Figure 4. Why-Why Analysis for Deficit in Spares |
3.2. DO
The second phase in this problem solving cycle is Do. Following steps were taken as solutions to the causes found in the previous step.The first step to be performed is to prepare a Value Stream Mapping (Fig. 5), current layout (Fig. 6), and to analyze the current state start with the application of 5S and Visual Kanban. It was applied on all the concerned equipments and the cars not only in a particular section but also was incorporated in all the solution steps that were undertaken.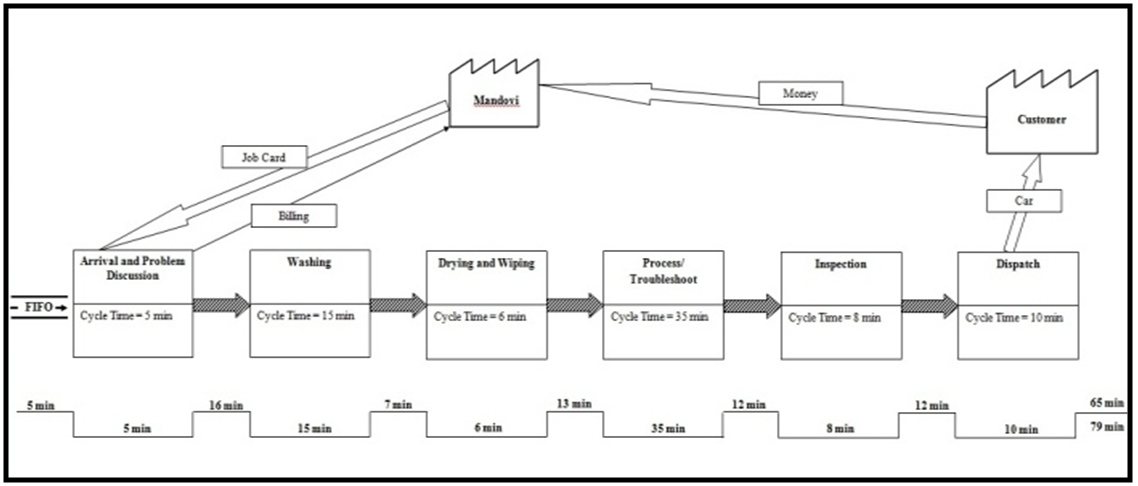 | Figure 5. Value Stream Mapping – Current Scenario |
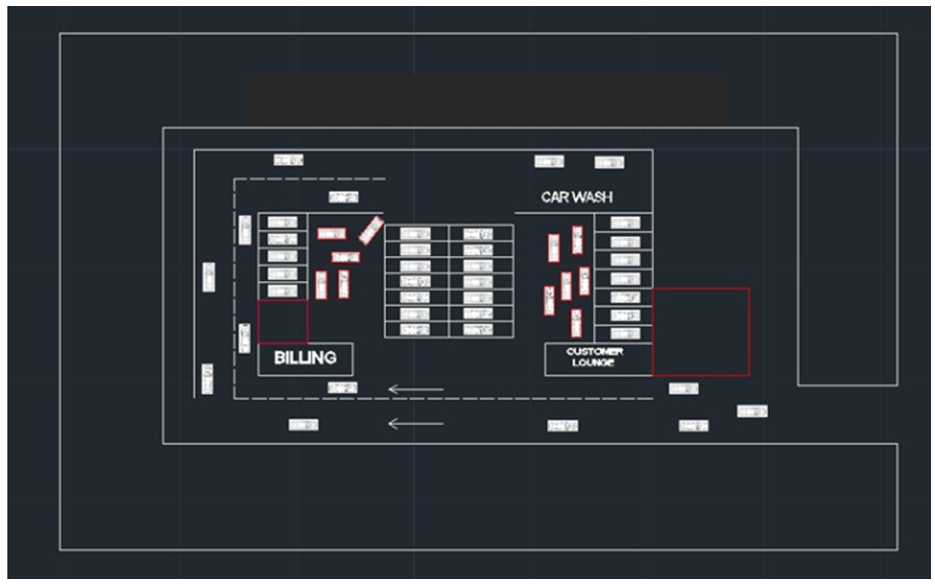 | Figure 6. Current layout |
The first S that is the 5S Sort is to be applied throughout the entire factory space. This step is used to set apart those items that are needed on the factory floor and those which are to be kept at a different location or be discarded. To help with this task researchers used the highly reliable technique of Red tagging. This involves creation of a paper tag that has the information of the equipment to be tagged. The tag is tied on the item that is supposedly thought to be out of place for set time duration. The concept of the process is explained to the personnel involved. After the time duration the tags are to be removed [7]. The next step was to develop an improved layout, which facilitates faster and quicker movement of the cars within the plant. The changes made are to be consulted with the organization Managing Director, General Manager, Service Advisors, Supervisors, the Inspectors and the Technicians involved in the plant. The new layout has all the vital changes that are required. Visual Kanban assists in segregation of Free Service cars from Paid Service cars, or the cars with major complications from minor complications. Spares could be fetched in time for the ongoing process by intimating the supervisor, who fetches the spares instead of the technician so that downtime is reduced to minimum.The changes that are anticipated with the incorporation of the revised layout are:• Motion of the cars within the plant can be brought under check• Increase in productivity• Cars with shorter lead times can be clearly distinguished from those with longer lead times• Possible elimination of night shift with sustained implementation of the suggested measuresThe new layout (Fig. 7) was also developed in such a way that more floor area was available to do value added work. The new layout also brought down the inventory on the floor area considerably. An estimated increase in productivity is provided in the next phase.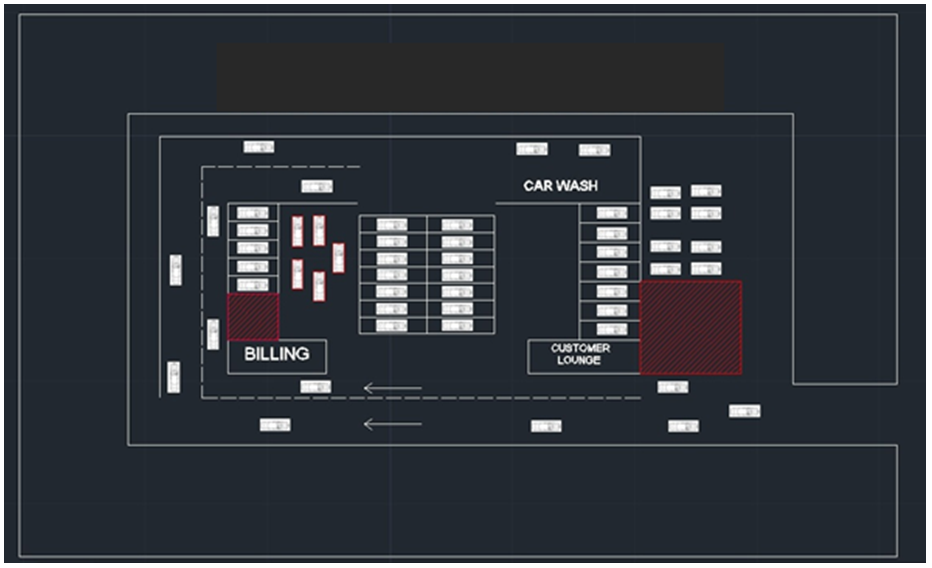 | Figure 7. New layout |
3.3. CHECK
In the Check phase, researchers validate the changes made above using a software simulation. By using the concept of “Gemba” or real time observation, the process time of the car at each bay is determined. The reduction in the process lead time is determined using Gemba and Brainstorming. These values form the input to the model created to propose a future state (Fig. 8).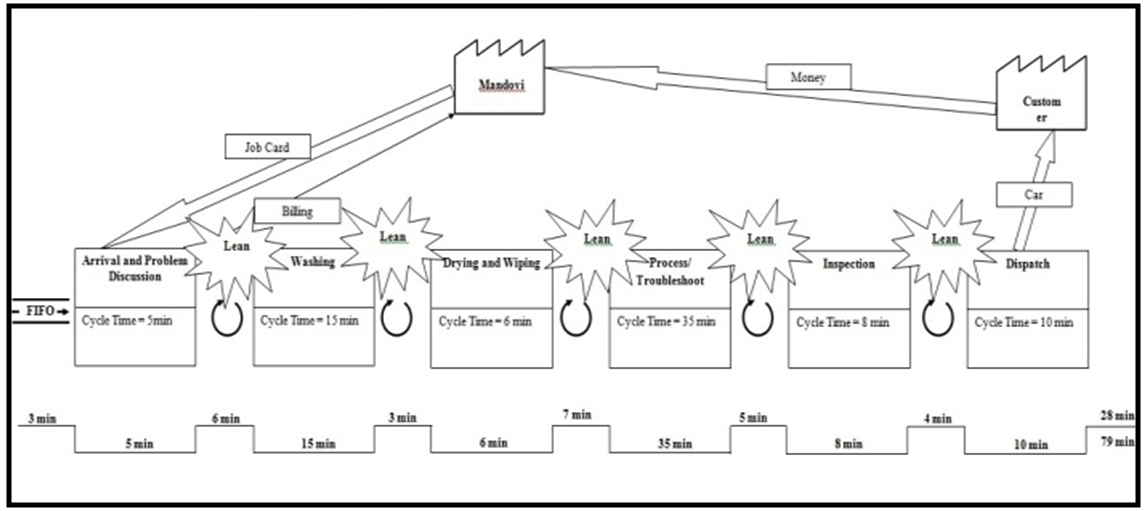 | Figure 8. Value Stream Mapping – Future Scenario |
Due to resource and technical constraint, the ARENA simulation software was utilized to calculate the average value added time for each of the processes [6-8]. Simulation models were developed as per the flow chart. The data collected (inter-arrival time and its distribution, entities per arrival, service rate and its distributions, number of staff and their working schedules) was fed to the model. The model thus prepared, was run for 5 replications of 8-hour shift per day (because the plant is operative only for two hours per day). The model was run without any warm-up period as it is a termination model and the KPIs (Key Performance Indicators) were identified. In order to validate the model, researcher in the beginning closely examined the animation screen along with the dynamic statistics to determine whether the animations imitate the actual system. Then face validity was performed by the panel of experts formed for the research, and their valuable comments helped to augment the model. Finally, the output of the simulation model was compared with the real system output. Thus, a one-day study was conducted to identify the KPI and which was then compared with the output of the simulation model. Since the differences between the results are less than 10%, which is within the standard total differences allowed, the simulation model is considered as acceptable and valid.
3.4. ACT
All the changes have been recommended (Table 2) to be implemented on a permanent basis. The procedures for the standardization of the changes are being developed as per the rules and policies of the concerned organization. This phase also involves creating awareness among the factory personnel and all the concerned people about 5S, proper tool keeping methods, Cleanliness of the bay and simple Lean techniques [9, 10]. The various checklists were developed for standardization.Table 2. Solutions to the Root Causes 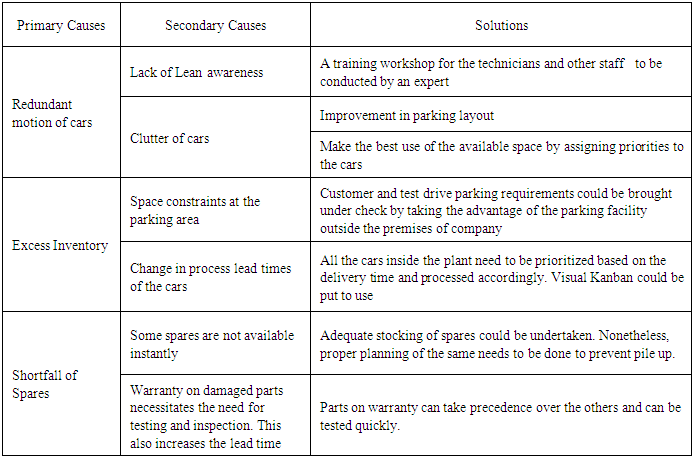 |
| |
|
Based on the study made, an improved layout of the plant is made, as shown in Fig 8. The hatched portion shows the area which could be cleared for the motion of cars. Here, the area inside the plant with unused furniture pieces could be cleared; similarly, the GM’s former office could be used to augment the parking capacity, provided it is not put to any other use. Further, customer’s parking inside the premises of organization restricted, and this space can be used to keep the processed cars. The customer four wheeler parking facility provided at the side of the road.
4. Conclusions
The Lean concepts can be applied to any type of industry. This research proves that Lean approach can be applied, and followed in any automobile service industry. The key lessons learned during the research are summarizes as follows.• The application is very simple and can be implemented economically, as it does not require the involvement of highly skilled people. A simple training of the existing workforce for creation of awareness is needed.• The principle of 5S, which is a Lean tool, is an effective technique which serves as a doorway to continued improvement. The five steps once made understood give an immediate improvement by creating a visual workplace. It does not follow a single approach but a multidimensional use of productivity improvement techniques.• Lean manufacturing mainly involves awareness and involvement leading to a highly productive work environment. • The results of the study conducted have been verified and validated using computer simulation software (ARENA).The research has resulted in reduced traffic of cars inside the plant. A comprehensive implementation of the suggestions would result in an increase of up to 10 cars per day. The feedback given by the Company on its working is quite positive. Encouraged by its success, the Company has informed us that, they are planning to implement our other suggestions in Toto on pilot basis.
References
[1] | M. L. George, 2002, Lean Six Sigma, New Delhi, Tata McGraw Hill. |
[2] | U. Lehtinen and M. Torkko, 2005, The Lean Concept in the Food Industry: A Case Study of Contract a Manufacturer, Journal of Food Distribution Research, 36(3), 57-67. |
[3] | S. Bhat, and N.A. Jnanesh, 2013, Transforming Higher Education with Lean Six Sigma, HEF Indian Journal of Higher Education, 3(2), 81-85. |
[4] | S. Bhat, N.A. Jnanesh, R. A. Melvyn, and R. A. D’souza, 2015, Application of Operations Research Technique to Improve the Performance of the HID of a Hospital, Journal of Mechanical Engineering and Automation, Vol. 5(3B), 81-83. |
[5] | D. Okes, 2009, Root Cause Analysis: The Core of Problem Solving and Corrective Action, Milwaukee, ASQ Quality Press. |
[6] | S. Bhat, E.V. Gijo, and N.A. Jnanesh, 2014, Application of Lean Six Sigma methodology in the registration process of a Hospital, International Journal of Productivity and Performance Management, 63(5), 613-643. |
[7] | S. Bhat, E.V. Gijo, and N.A. Jnanesh, 2015, Productivity and Performance Improvement in Medical Records Department of a Hospital: An Application of Lean Six Sigma, International Journal of Productivity and Performance Management, 65(1), 98-125. |
[8] | S. Bhat, and N.A. Jnanesh, 2014, Application of lean Six Sigma methodology to reduce the cycle time of out-patient department service in a rural hospital, International Journal of Healthcare Technology and Management, 14(3), 222-237. |
[9] | E.V. Gijo, S. Bhat, and N.A. Jnanesh, 2014, Application of Six Sigma methodologies in a small scale foundry industry, International Journal of Lean Six Sigma, 5(2), 193-211. |
[10] | S. Bhat, and N.A. Jnanesh, 2013, Enhancing Performance of the Health Information Department of a hospital using Lean Six Sigma Methodology, International Journal of Six Sigma and Competitive Advantage, 8(1), 34-50. |