Pruthvi Serrao, Ravikanth Prabhu, Chiranth B. P., Yazid Mohammed
Department of Mechanical Engineering, St Joseph Engineering College, Mangaluru, India
Correspondence to: Pruthvi Serrao, Department of Mechanical Engineering, St Joseph Engineering College, Mangaluru, India.
Email: |  |
Copyright © 2016 Scientific & Academic Publishing. All Rights Reserved.
This work is licensed under the Creative Commons Attribution International License (CC BY).
http://creativecommons.org/licenses/by/4.0/

Abstract
The commercially pure (CP) titanium cylindrical flat pins were subjected to wear on a standard pin-on-disc machine against a SiC abrasive disc for a dry sliding condition in the atmospheric air. The design of experiments (DOE) approach using Taguchi method was employed to predict the wear behavior against variable parameters such as load, speed and sliding duration. Also signal-to-noise ratio and analysis of variance (ANOVA) were used to study the influence of these parameters on the wear loss. It was observed that load has a significant effect on wear followed by speed and duration. A multiple linear regression equation has been developed and the error associated with confirmation test is 1.52% to 10.96%.
Keywords:
Titanium, Abrasive wear, Taguchi orthogonal array, Pin-on-disc, ANOVA
Cite this paper: Pruthvi Serrao, Ravikanth Prabhu, Chiranth B. P., Yazid Mohammed, Application of Taguchi Method to Predict the Abrasive Wear Behavior of CP Titanium, Journal of Mechanical Engineering and Automation, Vol. 6 No. 5A, 2016, pp. 13-17. doi: 10.5923/c.jmea.201601.03.
1. Introduction
Pure Titanium (Grade 2) is light weight and highly corrosion resistant, offering an excellent balance of strength and ductility but it has much lower strength than alpha-beta or beta titanium alloys. But it suffers poor resistance to wear and is prone to galling [1]. There has been extensive research work carried out to enhance its wear resistance and a considerable enhancement is only achievable by any established surface treatments that involve changes in surface chemistry. However, certain applications requiring the use of titanium in its purest from for example, in case of medical implants for bones and joints, requires it to be designed considering the influence of the various process parameters acting as per the service condition [1, 2]. Thus, to understand the wear behaviour of titanium and predict the wear against the service conditions, a statistical method can be employed involving design of experiments by Taguchi method [3-5].In the present work, a statistical approach based on Taguchi and ANOVA techniques was adopted to determine the degree of importance of each process parameter on the variance of wear loss of the commercially pure titanium. Mathematical models have been developed between the process variables and its wear behaviour.
2. Taguchi Method
Taguchi method is employed to design the experiment for abrasive wear study in order to obtain optimum results with minimum number of experiments. The experimental design proposed by Genichi Taguchi involves the use of orthogonal arrays to organize the factors affecting the process and also the levels these factors need to be varied systematically in order to complete the experiment with minimum trials in order to save the time, money and resources instead of performing all possible combinations [5, 6].
2.1. Plan of Experiments
An orthogonal array was constructed up on identifying the control factors, their levels and responses as shown in Table 1. This experiment has 3 variables at 3 different levels. A full factorial experiment would require (3^3) = 27 experiments. We conducted a Taguchi experiment with a L9 (3^3) orthogonal array (9 tests, 3 variables, 3 levels).Table 1. Parameters and their levels for wear test 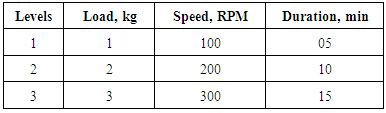 |
| |
|
The orthogonal array for the present work is as shown in Table 2. Here different parameters of load, speed and duration are considered for analysis.Table 2. Taguchi L9 Orthogonal array 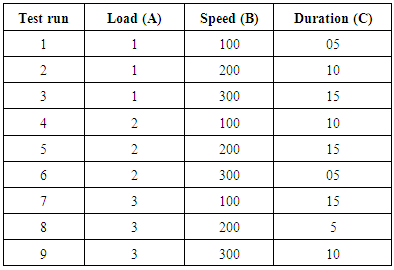 |
| |
|
3. Experiment Details
3.1. Material
The material chosen for the present work is commercially pure grade 2 titanium. The cylindrical specimen of 6mm diameter and 25mm long were prepared for wear test with smoothly polished ends. The surface was polished using water proof silicon carbide emery paper with a grit size of P200, P320, P1000 and P2000; thereafter, thoroughly cleaned with acetone before the wear test.
3.2. Pin-on-Disc Wear Test
The DUCOM pin-on-disc tester as shown in Figure 1 is used to study the abrasive wear of titanium under dry sliding condition at normal temperature in atmospheric air. 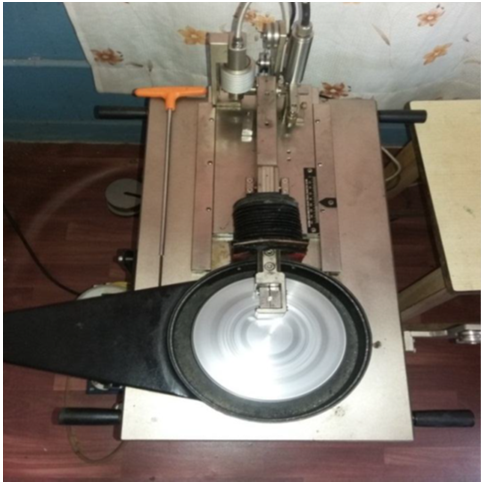 | Figure 1. Pin-on-disc setup |
The specimen is clamped and held against a P220 grit size SiC abrasive disc during testing; the load is applied on the specimen through the cantilever mechanism with a track radius of 100mm. The weight loss is measured during the test for the variable parameters of load, speed and duration.Table 3. Specifications for wear testing 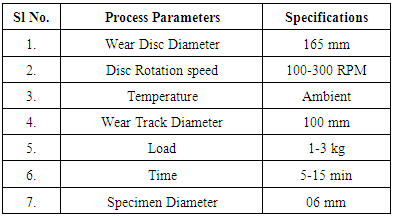 |
| |
|
4. Results and Discussion
A statistical analysis of wear loss was carried out using the software MINITAB14 specifically used for the design of experiment applications. Test conditions with output results using L9 orthogonal array are presented in Table 4. Table 4. L9 orthogonal array with mean wear loss and S/N ratio 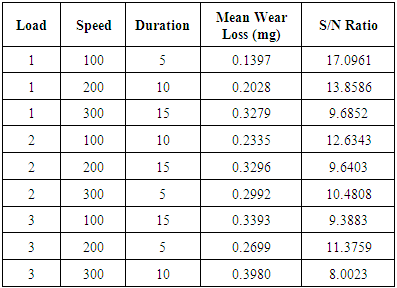 |
| |
|
4.1. S/N Ratio Analysis
Considering the different factors the S/N ratio was computed for the wear loss of the material as the response. The S/N ratio was calculated using the equation 1 for smaller is better quality characteristic. | (1) |
Where, n is the number of observation, and y is the observed dataThe S/N ratios and the response were plotted for each factor against each of its levels with a smaller-the-better condition for wear loss and are as shown in Figure 2.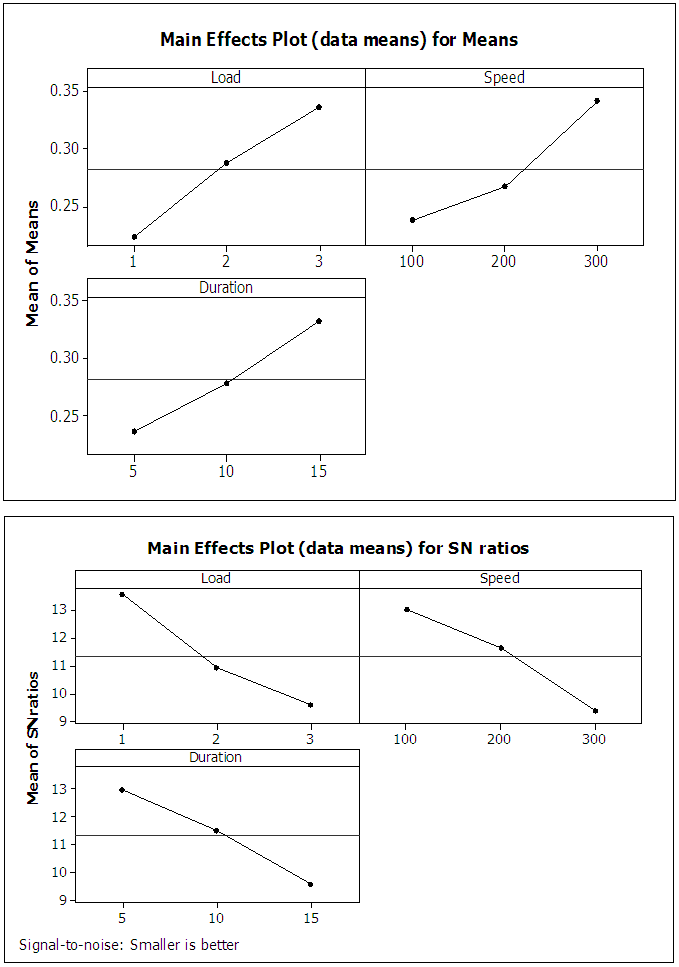 | Figure 2. Main effects plot for means and S/N ratios |
Analysis of the results leads to the conclusion that the factors in consideration show an increase in mean wear loss of the material due to abrasion with increasing levels of the factors. The wear loss increases almost linearly with increasing load (A), speed (B) and duration (C). As for minimization of wear is concerned, factors A, B and C has significant effect; a combination of A1, B1 and C1 gives minimum wear. In order to justify/conform the factors and its significance a further statistical analysis is necessary i.e. analysis of variance.Table 5. Response table for S/N Ratio (Smaller is better) 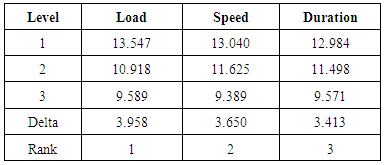 |
| |
|
Table 6. Response table for means 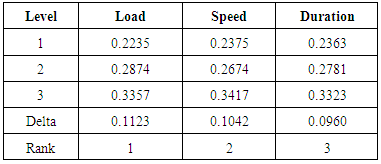 |
| |
|
4.2. Analysis of Variance
A statistical analysis of variance (ANOVA) is conducted along with the Taguchi technique to find the contribution of each of the process parameters for the wear loss. The percentage contribution of various process parameters to the selected performance characteristic can be estimated by ANOVA [6, 7]. The table 7 and 8 shows the results of the ANOVA where the analysis is carried out for a confidence level of 95%. Sources with a p-value less than 0.05 were considered to have a statistically significant contribution to the performance measures. The last column in Table 7 and 8 shows the percentage contribution of each parameter and it can be observed that the load has the highest influence of 38.96% on wear loss followed by speed and duration considering the S/N ratios; the speed and duration have an influence of 32.53% and 28.13% respectively. Hence load is an important parameter to be considered during abrasive wear of CP titanium followed by speed and duration.Table 7. Analysis of Variance for S/N Ratio, using Adjusted SS for Tests  |
| |
|
Table 8. Analysis of Variance for Mean, using Adjusted SS for Tests 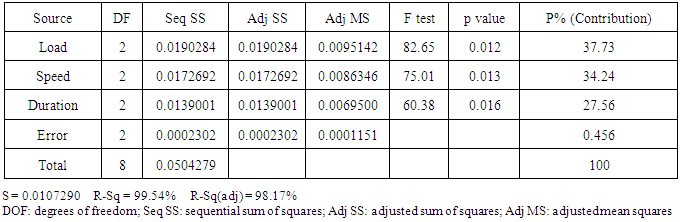 |
| |
|
4.3. Multiple Linear Regression Model Analysis
In order to establish the correlation between the wear parameters load, speed, duration with the wear loss multiple linear regression model was used. 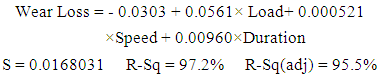 | (1) |
The confirmation test was performed by selecting the set of parameters as shown in Table 9. The Table 10 shows the results obtained, where comparison was carried out between the foreseen values from the model developed in the present work (Equation 1), with the values obtained experimentally. From the analysis of the referred table we can observe that the calculated error varies from 1.52% to 10.96% for wear loss. Therefore, the multiple regression equation derived above correlate the evaluation of the wear of the CP titanium with the reasonable degree of approximation.Table 9. Parameter used in the Confirmation test 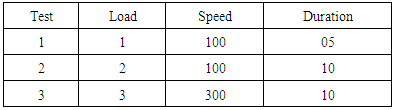 |
| |
|
Table 10. Comparison of confirmation test with regression model 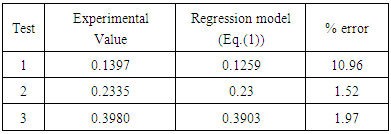 |
| |
|
4.4. Taguchi Confirmation Experiment
Also Taguchi confirmation test is performed to validate the experimental results and to evaluate the accuracy of the analysis. The comparison of the estimated value and the actual value is shown in Table 11. The improvement of S/N ratio from mean to optimum process parameters is 5.5dB.Table 11. Comparison of confirmation experiment 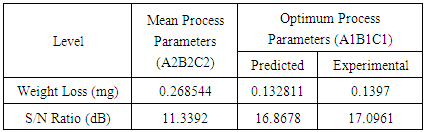 |
| |
|
5. Conclusions
Taguchi’s design method can be used to analyze the dry sliding abrasive wear behaviour of the CP titanium as described in the paper. The following are general conclusions which can be drawn from the work.• Load (38.96%) is the factor which is having highest physical as well as statistical influence on the abrasive wear followed by speed (32.53%) and duration (28.13%).• Multiple linear regression equation has been developed with R-Sq value 97.2%. Confirmation experiment shows that the error associated with the wear loss of the specimen varies from 1.52% to 10.96%.• The Taguchi confirmation experiment has shown that an improvement of 5.5dB can be achieved by implementing the optimum process parameters as per Taguchi design with an error of less than 2-3% between the experimental and predicted values.
ACKNOWLEDGEMENTS
The authors wish to acknowledge the resources provided by the Research Centre, Department of Mechanical Engineering, St Joseph Engineering College, Mangaluru.
References
[1] | Gerd Lütjering, James C. Williams. Titanium. 2nd edition, Springer, 2007. |
[2] | Blau, P.J. (1992). “Friction, Lubrication, and Wear Technology” ASM Handbook 10th edition, ASM International, Materials Park, OH. |
[3] | Rachit Marwaha, Mr. Rahul Dev Gupta, Dr. Vivek Jain and Er. Krishan Kant Sharma., 2013, “Experimental Investigation & Analysis of Wear Parameters on Al/Sic/Gr - Metal Matrix Hybrid Composite by Taguchi Method,” Global Journal of Researches in Engineering, 13(09), 15-21. |
[4] | M.R. Shivakumar, N.V.R. Naidu., 2013, “Taguchi’s Orthogonal Array Approach to Study the Wear Behavior of Aluminium Alloy/Soda Lime Glass Composites,” International Journal of Engineering Research & Technology, 02(08), 2328-2334. |
[5] | H. Unal, F. Ficici, A. Mimaroglu, A. Demirkol, and A. Kırdar., 2015, “Prediction and optimization of tribological behavior of nylon composites using Taguchi analysis method,” Journal of the Brazilian Society of Mechanical Sciences and Engineering, doi:10.1007/s40430-015-0398-1. (Accepted manuscript, published online on 13th August 2015 and yet to be assigned to an issue) |
[6] | N. Naresh, K. Rajasekhar and P. Vijaya Bhaskara Reddy., 2013, “Parametric analysis of GFRP Journal of Mechanical and Civil Engineering, e-ISSN: composites in CNC milling machine using Taguchi method,” IOSR 2278-1684 Vol 6, Issue 1, 102-111. |
[7] | M. S. Sukumar, P. Venkata Ramaiah and A. Nagarjuna., 2014, “Optimization and Prediction of Parameters in Face Milling of Al-6061 Using Taguchi and ANN Approach,” Procedia Engineering, 97, 365 – 371. |