Reuben Lasrado , Melroy Furtado , Anil Melwyn Rego , Prinson Veigas
Department of Mechanical Engineering, St Joseph Engineering College, Mangaluru, India
Correspondence to: Reuben Lasrado , Department of Mechanical Engineering, St Joseph Engineering College, Mangaluru, India.
Email: |  |
Copyright © 2015 Scientific & Academic Publishing. All Rights Reserved.
Abstract
Water resource management involves planning, developing, distributing and managing the optimum use of water resources. The current study attempts to automate the water management process in a beach resort using LabVIEW, a graphical programming language. The purpose of this study is to reduce water wastage and human effort by partial/complete automation of existing water management system. The current work uses LabVIEW environment for initial code development and simulation of the proposed system. The real time situation is modelled into a small scale prototype. Components are tested individually and then connected to form different subsystems. Subsystems are connected, monitored and controlled using LabVIEW. The given solution controls the water resources automatically leading to an efficient water management system. The system executes this task independently while reducing human labour with a slight increase in electricity usage.
Keywords:
Water Management, LabVIEW, Automation
Cite this paper: Reuben Lasrado , Melroy Furtado , Anil Melwyn Rego , Prinson Veigas , Automation of Water Management System Using LabVIEW, Journal of Mechanical Engineering and Automation, Vol. 5 No. 3B, 2015, pp. 89-93. doi: 10.5923/c.jmea.201502.18.
1. Introduction
Water is an essential part of almost all human activities: it is required in homes as well as in industries. Water is becoming a scarcer resource with each passing year, due to improper water allocation, inefficient use, unmonitored wastage and lack of overall water management [5]. In order to conserve and reduce wastage of water, we must plan and regulate the distribution of water.Water resource management involves activities such as planning, developing, distributing and managing the optimum use of water resources. Ideally, it must allocate water in such a manner, so as to satisfy all demands for water without wastage. The task of managing this activity increases in complexity with any change in factors such as the number of uses, number of sources or the seasonal availability of water. This complexity is further compounded due to the change in salinity of water in coastal regions during high summer, which renders a few sources of water unusable for a period during the year. This task becomes too challenging for a single person to handle effectively.This task is delegated to a machine in the current work, to automatically control the distribution of water to all required areas, while checking the potability of the water. Current systems, available commercially, lack the ability to monitor and distribute water, from multiple sources to multiple uses. Research is being carried out on microcontroller based water level sensing and controlling systems and also in the use of LabVIEW as feedback control [6]. Microcontroller based water controlling system developed by S.M Khaled Reza is used in a domestic environment. The system code is developed for the PIC16F84A controller. Code is stored and executed by the microcontroller [1].The current work is to develop an automated system, which controls the distribution and management of water, through an interconnected system of pipes; which allows for water to be taken from any source and given to any sump. This system is being developed for use on a local beach resort having an existing pipe layout, which will be incorporated into the final water management system. Current For this work, LabVIEW is selected to develop the initial code, carry out software testing and to execute during field operation. LabVIEW is selected due to its inherent parallel processing capability; since a block of code is executed as soon as it receives all the inputs [8]. This allows for easy parallel programming of the loops, in the monitoring and distribution functions. The Arduino development board is selected as a low cost, easy to use hardware interface. LabVIEW and Arduino communicate, through a plugin for LabVIEW, over a serial connection [7].LabVIEW is a system design platform and development environment for the visual programming language G. LabVIEW requires the user to draw blocks of code instead of writing functions. It connects different functions together through wires instead of variables. Unlike other programming languages, such as C or C++, which are executed in a sequence, LabVIEW executes a block of code as soon as all the inputs, for the block, are received. This is beneficial since it allows easy parallel process programming as shown in Figure 1 [8]. Parallel processing is required in the current work to carry out two main functions in tandem i.e. monitor and indicate levels of water in all sources and sumps and fill up a sump that is below required levels.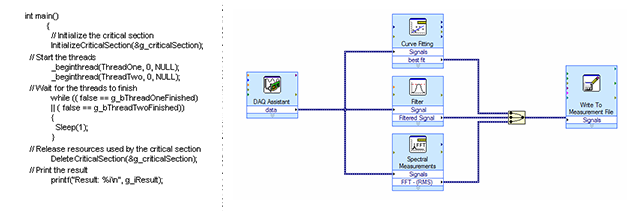 | Figure 1. Parallel Programming in Text Based Languages and LabVIEW |
Automation is the use of technology and equipment to control the required parameters of a process in order to obtain the required outputs from the system automatically and accurately [3]. Automation is necessary when the process to be carried out is complex or laborious [4]. In case of the aforesaid beach resort, the current water management system requires the person in-charge to walk around an eight acre campus in order to distribute water from various sources to the required sumps. This increases chances of water wastage from spillage, drying of wells due to over pumping and ineffective distribution of water. The system being developed distributes water from multiple sources such as borewells, surface wells and waste treatment plants to different uses of water namely, irrigation and domestic use, etc. The system operates while constantly monitoring the levels of water in the source being used and sump being filled. This ensures that wells do not run dry nor is water wasted from spillage.
2. Development Using LabVIEW
The code is first developed and tested purely in software simulation of the system to eliminate any bugs or logical errors as well as to test the stability of the code to function continuously [2]. Figure 2 shows the interface used for testing, which is also used during real world testing.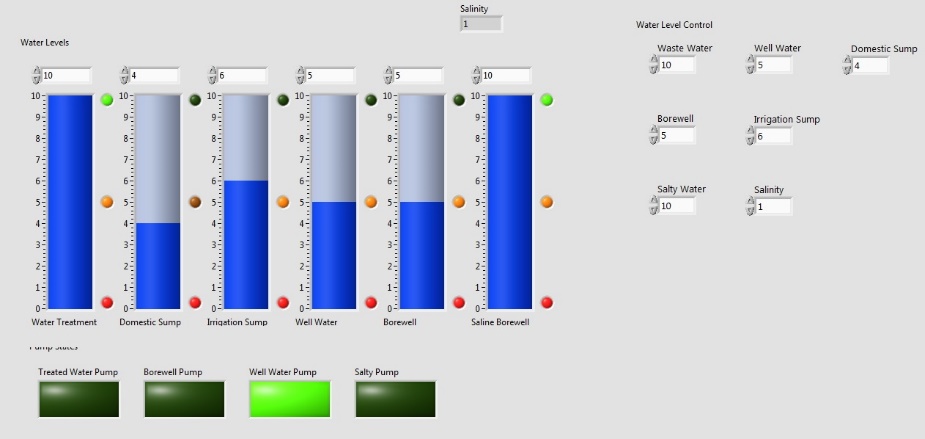 | Figure 2. LabVIEW interface used for software simulation |
The interface has 6 water tanks: irrigation sump, domestic sump, well, borewell 1, borewell 2. Each tank has 3 LEDs positioned at the level of water they indicate. • Green LED – High Water Level• Orange LED – Medium Water Level• Red LED – Low Water LevelThe 4 large rectangular indicators, below the tanks, indicate the operation of the pumps connected to each source. When water is being pumped from a source, the respective LED is turned on.Levels of water in all the sources and sumps is also indicated in number format. The range of level can be adjusted for higher accuracy.The code developed for the current work contains three loops executing in parallel. They are – indicator loop, irrigation sump check loop and domestic sump check loop.
2.1. Indicator Loop
The function of this loop is to continuously check various parameters of the system.• High water level in source• High water level in sump• Low water level in source• Low water level in sumpThe levels of all sources and sumps are indicated on the screen as well as a physical output board which uses different colour LEDs. Figure 3 shows the flowchart of logic in the block of code.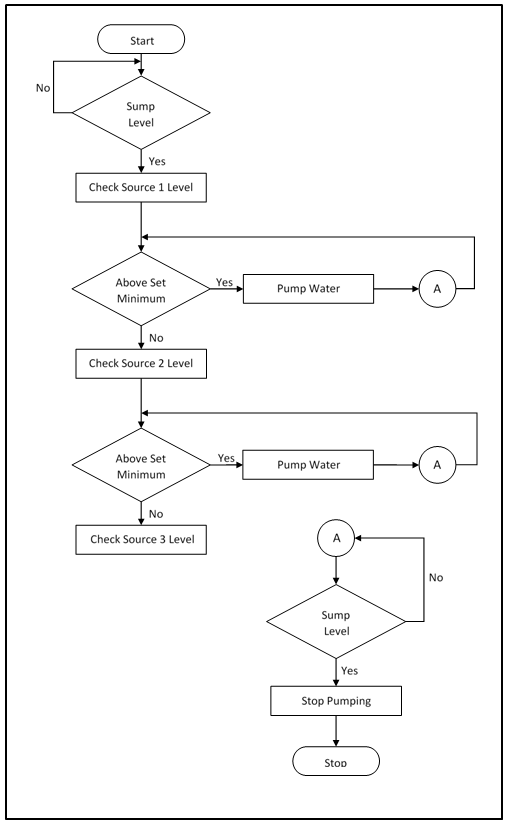 | Figure 3. System Logic Flowchart |
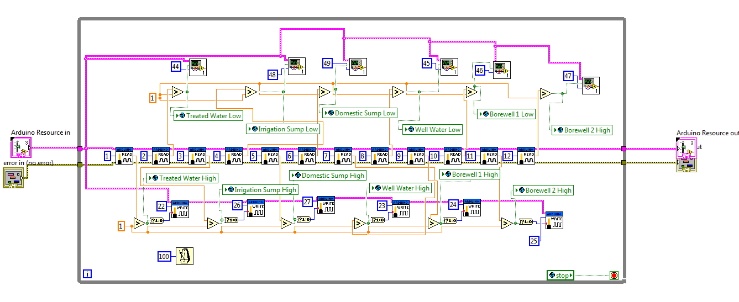 | Figure 4. Indicator Loop |
Three contact type probes are installed in the tanks. The lowest probe in the tank is used to inject +5 VDC into the water. The other two probes, one placed a little above the +5V probe and another at the top of the tank, are used to detect the water level. When water comes in contact with these probes, the water acts as a conductor and a voltage is developed in the probes. This voltage is measured by the analog input of the Arduino board.LabVIEW reads the voltage measured by the Arduino on its analog input 1 – 12 in serial order. LabVIEW ensures that this voltage is not below a certain threshold and is constant. This makes sure that water level is at a steady level and did not momentarily touch the probe. When it is determined that water is at a certain level, the LED on the output board and in the interface is turned on.The loop carries out two sub functions that is reading the voltages from contact type water probes and determining the level of water present in each source. This loop runs continuously during program execution.
2.2. Irrigation Sump Check Loop
The function of this loop is to check the level of water in the irrigation sump and maintain a required level of water in it. The minimum and maximum levels of water for the sump can be specified by the user. This loop consists of nested if statements which follow a specified priority of sources when drawing water.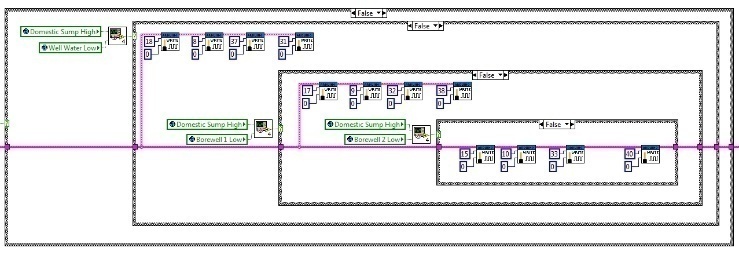 | Figure 5. Nested If Statements Checking Source Levels |
Irrigation Sump: Treated Water Tank → Well →Borewell The preceding line indicates the order in which sources are checked when there is low level of water in the irrigation sump. The first source to be checked is the treated water tank of the waste water treatment plant of the resort. Since the water is going to be used for irrigation, the primary source of water is treated water. If the level of water in the treated water tank is sufficient, water is pumped from the treated water tank. If the water level is less than the specified minimum, the system draws water from the well and then the borewells. This continuously checks the level of water in a sump. If the current level is less than a specified minimum, the loop then checks through the sources of water, in the order mentioned previously, to determine the best source.
2.3. Domestic Sump Check Loop
The function of this loop is to continuously check the level of water in the domestic sump. Like the irrigation sump check loop, the minimum and maximum levels of water to be maintained in the sump can be specified by the user. However, priority of checking the sources is different.Domestic Sump: Well → BorewellLike the irrigation sump, the preceding line indicates the order in which sources are checked when the level of water in the domestic sump is low. This water is kept for use in the rooms at the resort, hence treated water is not included in the source check list.The loop checks whether the level of water in the source being used is sufficient and if the sump is full. The condition of the condition block is only satisfied when the sump is not full and there is sufficient water in the source.When it is TRUE, the condition block turns on the required pump and electromechanical valves through the relay. Moreover, the loop turns on the pump and electromechanical valve LEDs to indicate that they are in operation.When it is FALSE, the condition turns off the pump, electromechanical valves and the respective LEDs of the previous source and then goes on to check the next source.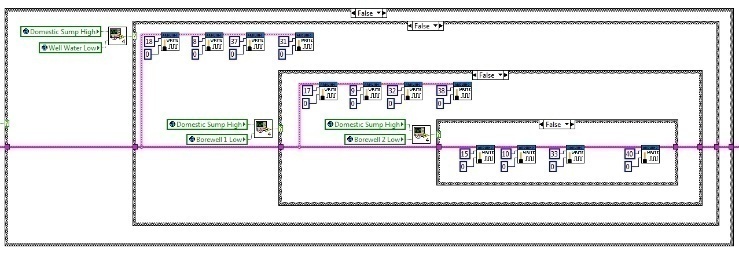 | Figure 6. Domestic Sump Check Loop |
The primary function of the loop is to check the level of water. Its secondary function is to indicate on the output board, the pump states and the sump to which water is being diverted. When the loop turns on a pump and an electromechanical valve, it turns on the corresponding LEDs on the physical output board to indicate that they are in operation.
3. Hardware Set-up and Test Model
Once the code has been simulated in software, the code is modified, in syntax, to now communicate with the Arduino. A small scale model is built to physically test the system. This is done to eliminate any problems resulting from physical phenomena, such as back EMF generated from the closing of relay switch and jittering of the relay if the water level is unstable.An output board is constructed to display the parameters such as water levels in the sources and sumps, pump states and electromechanical valve states. It can be mounted in a control room to allow the person in charge to assess the conditions of the entire campus from a single location.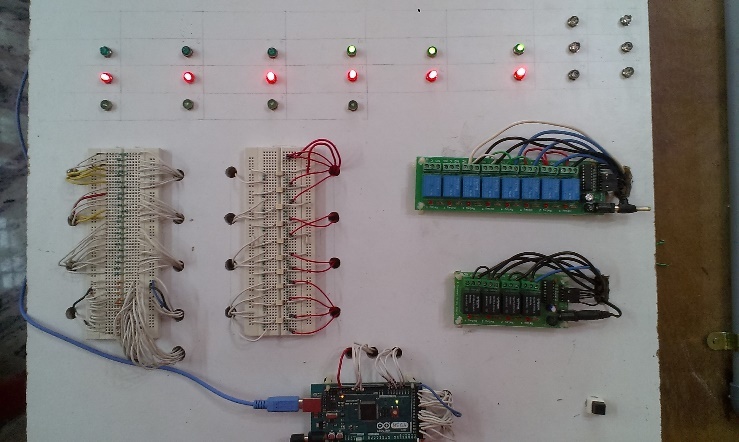 | Figure 7. Physical Output Board |
This output board is provided in tandem with the software interface. This is useful since the software interface can be updated later to allow remote monitoring of the system.This output board can be placed at any convenient location in the premises for the person in-charge to monitor if required. The software interface for the system provided need not be in the same location as the output board. Therefore, it can be monitored remotely by the administrators.
4. Conclusions
Water is one of the most important basic needs of all living beings.It is becoming a scarcer resourcepartly due to huge amount of water being wasted by uncontrolled use. Existing water level monitoring systems lack functionality in terms of being able to monitor and manage multiple sources of water. The system developed carries out the desired task, effectively and reliably, which obviates the need for a human operator to be present continuously at the system. The minimum and maximum allowable levels of the source and sumps can be defined by the user. The code can be easily updated to integrate more sources or sumps into the system. The remote physical interface present in the system displays all necessary data in a single location.The system reduces human effort and water wastage at the cost of a small increase in electricity consumption. Modelling of the present system and implementation of the automation layer can be easily carried out. This system can be adapted for use in any industry, large or small, which has multiple sources of water or shortage of labour. In future revisions, features such as remote monitoring, code that adapts to different seasons, use of additional sensors and solid state relays and long term data logging can be added to the system.The code written for a particular season can be developed by studying the long term sensor data i.e. a particular source can be used less during summer or vice versa.Electromechanical relays produce back EMF when switching states. This can be avoided by using solid state relays which have proved to be more reliable and durable over a long period of time.
References
[1] | S. M. Khaled Reza, Shah Ahsanuzzaman Md. Tariq, “Microcontroller Based Automated Water Level Sensing and Controlling: Design and Implementation Issue”, Proceedings of the World Congress on Engineering and Computer Science 2010 Vol I WCECS 2010, October 20-22, 2010, San Francisco, USA. |
[2] | Samuel Daniels, Dave Harding, Mike Collura, “Introducing Feedback Control to First Year Engineering Students using LabVIEW”, School of Engineering & Applied Science, University of New Haven. |
[3] | Rogers C.O. Morton, Gilbert G. Stamm, “Water Systems Automation”, A State of the Art report by the Water Systems Automation Team, July 1973. |
[4] | Y.V. Satyanarayana, “Automation & Controls in Water & Waste Water Treatment Plants”, Ion Exchange (India) Ltd. |
[5] | Leak Facts. Retrieved from http://www.epa.gov/WaterSense/pubs/fixleak.html. |
[6] | Neena Mani, Sudeesh T.P, Vinu Joseph, Titto V.D, Shamnas P.S, “Design and Implementation of a Fully Automated Water Level Indicator”, International Journal of Advanced Research in Electrical, Electronics and Instrumentation Engineering 2014 Vol 3 Issue 2, February 2014. |
[7] | Carey Williamson, “Introduction to LabView Programming Including Arduino Toolkit”. |
[8] | “Multicore Programming with LabVIEW Technical Resource Guide”, http://www.ni.com/labview/. |