Shreeranga Bhat 1, Anil Melwyn Rego 1, Jnanesh N. A. 2, Rahul A. D’souza 1
1Department Mechanical Engineering, St Joseph Engineering College, Vamanjoor, India
2Department Mechanical Engineering, KVG College of Engineering, Sullia, India
Correspondence to: Shreeranga Bhat , Department Mechanical Engineering, St Joseph Engineering College, Vamanjoor, India.
Email: |  |
Copyright © 2015 Scientific & Academic Publishing. All Rights Reserved.
Abstract
Application of industrial engineering tools has never been more important than it is today in service sector in general and hospitals in specific. Operations Research is one such technique which has its proven effect in manufacturing sector, and also can be effectively applicable in Hospitals. The research demonstrates one such application in the Health Information Department (HID) of a super speciality hospital in India. The study has been carried out in order to improve the productivity and performance in the department by assigning right person to the right job. The study adopted an exploratory research methodology and collected data was subjected to statistical analysis. Further, assignment technique has been used to determine the right person for the right job. The study reported a drastic improvement in the productivity of the department.
Keywords:
Operations Research, Assignment Technique, Health Information Department, India
Cite this paper: Shreeranga Bhat , Anil Melwyn Rego , Jnanesh N. A. , Rahul A. D’souza , Application of Operations Research Technique to Improve the Performance of the HID of a Hospital, Journal of Mechanical Engineering and Automation, Vol. 5 No. 3B, 2015, pp. 81-83. doi: 10.5923/c.jmea.201502.16.
1. Introduction
The health care industry is one of the world’s largest and fastest-growing industries. The largest emerging markets such as China and India might be expected to enjoy competitive advantage of medical tourism. The healthcare industry in India is facing increasing pressure to improve quality but also to reduce costs. In the heat and pressure of competition, it is important to build an organization that drives change quickly [1]. Another important point was that generally there was a feeling among the doctors and nurses that there was nothing to improve in the hospital, especially in Indian Healthcare sector [2]. Generally, improvement activities in hospitals, especially in India, are rarely based on the industrial engineering tools and techniques. This is due to the fact that there is a lack of interaction among the engineering institutions and healthcare sectors [3]. The study shows that industrial engineering tools could be effectively used in the healthcare industry as well [1]. Since industrial engineering tools and techniques are not wide-spread in hospitals, quality improvement initiatives could be facilitated with academic partnership or research [4]. Table 1 shows some early research done by industrial engineering pioneers in the healthcare sector for better service quality and cost reduction [5]. Table 1. Early research on the process improvements in healthcare 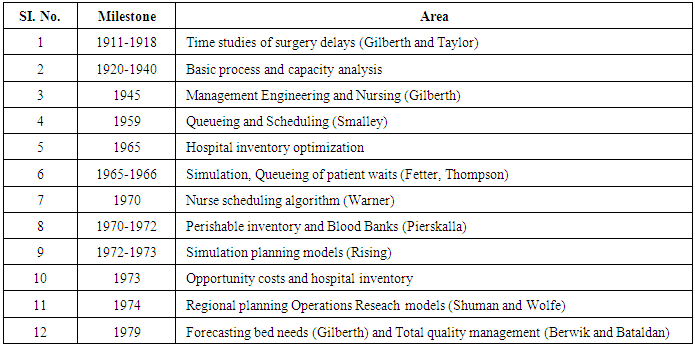 |
| |
|
2. Research Methodology
Case study research design and method is an empirical inquiry that investigates a contemporary phenomenon within its real-life context, especially when the boundaries between phenomenon and context are not clearly evident [6]. It is the most appropriate methodology for the exploratory nature of the study and to develop a conceptual framework [7]. ‘Action Research’ is a variation of the case study where the researcher is not an independent observer, but a participant in the process [8] [9]. Unlike other research methodologies, ‘Action Research’ is concerned with creating organizational change, and simultaneously, studying the process involved [10]. This also ensures the active participation of the members from the organization under study. Thus, ‘Action Research Methodology’ has been adopted in this research. Operations research technique and numerous statistical techniques are applied to arrive at robust conclusion. Minitab statistical software was used to analyze the data collected at different stages in the case study.
3. Case Study
The case study has been carried out in HID (Health Information Department) of a super-specialty hospital having 1000 beds. The HID of the hospital has two divisions, namely, OP (Out Patient) -HID and IP (In Patient) - HID, with 16 staff and 5 attendants headed by an MRO. The employees are relocated between these two divisions on a rotational basis every month. The OP-HID had the problem of longer processing time which has been ultimately resulted in heavy inventories. Thus, management decided to improve the productivity and performance IP-MRD using industrial engineering tools. The department under study is responsible for preparing patients’ medical records, attending to patients’ queries and retrieving medical records as and when needed by the physicians, preparing birth and death reports, legal reports, reporting daily census and preparing the name list of patients, attending medico-legal cases, preparing reports as per management directions, attending physicians and different department queries. The medical records preparation process was selected for the study, since it was resulting in an inventory of 40 WIP (Work-In-Process) files. The TAT (Turn Around Time) was found to be 30 minutes for the preparation of medical records. The process, consisting of 5 major steps/workstations/counter, starts at the Reception Counter. At this workstation, medical records are checked by the staff for completeness, signature of physicians, discharge summary, and history sheet. If any mistakes are found or any information is found missing including signatures, the medical records are sent back to the respective department for correction. Once the medical records are found up-to-date, they are sent to the next workstation for assembling forms in the standard order. The Assembler assembles the forms, staples them, signs and hands it to the Coder for further processing. The Coder searches the ICD-10 coding book for relevant / correct code of the diagnosis [11] [12]. Observation method was adopted for the data collection. The five staffs selected from IP-HID were posted in rotation in all five counters for five days. The 5 employees were named as A, B, C, D, and E for the purpose of data collection. Data was collected in the morning duty hours between 10am to 12.30pm. The collected data was analyzed by Mean, Standard Deviation, Coefficient of variation [13]. From the data analysis it was observed that interpretations were not enough to find out the right person for the right job. Every staff has good performing ability in one or the other counter. To find out the optimum allocation of person for the job, ‘Assignment Problem’ of OR technique was adopted. In that the ‘Hungarian Method’ was selected. The name assignment problem originates from the classical problem where the objective is to assign a number of origins (jobs) to equal number of destination (persons) at a minimum cost. The assignment is a problem because people possess vary abilities for performing different jobs and therefore the cost of performing the jobs by different people are different [14]. The collected data in seconds (processing time at each work station) with respect to each staff was shown in the table 2. After applying the ‘Hungarian Method’ the final reduced matrix is shown in the table 3. Optimal assignment for the collected data after the calculation are shown in table 3. The TAT of the medical records preparation with respect to the optimal assignment is shown in table 4, and resulted total TAT was found to be 18 minutes (Table 5). Once the results are communicated to the management, a risk analysis has been performed. After the implementation of results of the study the data was collected on the improved process. Data shown that the TAT was reduced to 18 minutes and inventory was reduced to 5 at the end of the day. The results motivated the staff and the management to implement industrial engineering technique in hospital wide. Ultimately, the case study has brought a culture change in the organization.Table 2. Processing time (sec) of staff Vs Workstation 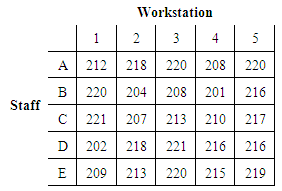 |
| |
|
Table 3. Reduced matrix of staff Vs Workstation after the application of Hungarian Method 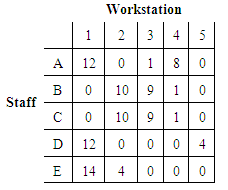 |
| |
|
Table 4. Optimal Assignment of staff Vs Workstation 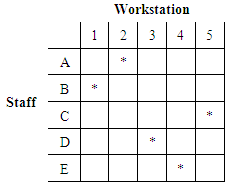 |
| |
|
Table 5. TAT with respect to optimal assignment 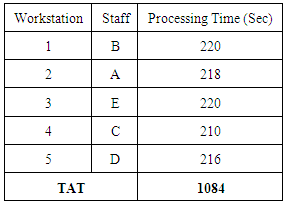 |
| |
|
4. Conclusions
The healthcare organizations in India are eyeing to gain competitive advantage in Medical Tourism (MT). Among manufacturing industries, the Operations Research techniques are recognized as an effective business strategy of cost reduction to improve the organization’s profitability and growth. This methodology can be effectively applied to hospitals. The new tools and techniques were appreciated by all those involved as they were able to make scientifically-based decisions, instead of an intuitional one. This changed the mindset, ‘It is not evolved here, hence not applicable to our processes’.
References
[1] | S. Bhat, E.V. Gijo and N.A. Jnanesh, 2014, Application of Lean Six Sigma methodology in the registration process of a hospital, International Journal of Productivity and Performance Management, 63(5), 613-643. |
[2] | E.V. Gijo and J. Antony, 2014, Reducing Patient Waiting Time in Outpatient Department Using Lean Six Sigma Methodology, Quality and Reliability Engineering International, 30, 1481-1491. |
[3] | S. Bhat and N.A. Jnanesh, 2013, Enhancing performance of the health information, Int. J. Six Sigma and Competitive Advantage department of a hospital using lean Six Sigma Methodology, 8(1), 34-50. |
[4] | D.J. Fine, 2006, Toward the Evolution of a Newly Skilled Managerial Class for Healthcare Organizations, Frontiers of Health Services Management, 22, 31-35. |
[5] | Y. Huang, X. Li, J. Wilck and T. Berg, 2012, Cost Reduction in Healthcare via Lean Six Sigma, in Proceedings of the 2012 Industrial and Systems Engineering Research Conference, G. Lim and J.W. Herrmann, eds. |
[6] | R.K. Yin, 2003, Case Study Research Design and Methods, Thousand Oaks, California: SAGE. |
[7] | C. Voss, N. Tsikriktsis and M. Frohlich, 2002, Case research in operations management, International Journal of Operations & Production Management, 22(2), 195-219. |
[8] | V.R. Prybutok and R. Ramasesh, 2005, An action-research based instrument for monitoring continuous quality improvement, European Journal of Operational Research, 166(2), 293-309. |
[9] | E.H. Schein, 2008, Clinical inquiry/research. In: Reason, P. and Bradbury, H. (Eds.), in The SAGE Handbook of Action Research: Participative Inquiry and Practice, Thousand Oaks, CA, SAGE, 266–279. |
[10] | D. Avison, R. Baskerville and M. Myers, 2001, Controlling action research projects, Information Technology & People, 14(1), 28-45. |
[11] | WHO ICD-10, 1992-1994, International Statistical Classification of Diseases and Related Health Problems, Geneva: World Health Organization. |
[12] | A. Karjalainen, 1999, International statistical classification of diseases and related health problems (ICD-10) in occupational health, Geneva: World Health Organization. |
[13] | D.C. Montgomery and G.C. Runger, 2007, Applied Statistics and Probability for Engineers, New York, John Wiley & Sons. |
[14] | C.Z. Frank, 1984, Game Theory: Concepts and Applications, New York, SAGE. |