Rahmi Karolina, Syahrizal, M. Agung Putra, Tito Agung Prasetyo
Civil Engineering Department, Universitas of Sumatera Utara, Medan, Indonesia
Correspondence to: Rahmi Karolina, Civil Engineering Department, Universitas of Sumatera Utara, Medan, Indonesia.
Email: |  |
Copyright © 2014 Scientific & Academic Publishing. All Rights Reserved.
Abstract
The initial idea of writing this research was the use of natural materials from Mount Sinabung eruption which could function as the substitute of natural material, used for making concrete. This idea was strengthened by the chemical content which is found in the volcanic ash of Mount Sinabung which contained 74.3% of SiO2, 3.3% of AL2O, and 1.79% of CA O in sand and cement obtained from the Research and Industrial Standardization Center. The research used volcanic ash as the substitution of fine aggregate with the variation of 0%, 5%,, 10%, 15%, 20%, and 25%, within a 28 day-treatment, cylinder testing devices, and batako. The analysis and method of the research were referred to the SNI 03-0349-1989 standard. The result of the analysis showed that the use of volcanic ash in batako with the variation of 0% at the average compressive strength of 166.90 kg/cm2, 5% at the average compressive strength of 173.72 kg/cm2, 10% at the average compressive strength of 207.14 kg/cm2, and 15% at the average compressive strength of 130.97 kg/cm2 had met the quality standard I of SNI 03-0349-1989 with the average compressive strength of 100 kg/cm2. The result of the maximum of split tensile strength showed that the variation was 10% of the average split tensile strength was 12.93%, and in the testing of water absorption in the variation of 0%, 5%, 10%, 15%, 20%, and 25%showed that the maximum value of water absorption was 4.142% which had met SNI 03-0349-1989 standard with the average maximum of water absorption quality I of 25%. It could be concluded that the volcanic ash of Mount Sinabung could be used as batako mixture at the maximum of composition of 10%.
Keywords:
Glass Volcanic Ash, Absorption, Compressive Strength, Tensile Strength
Cite this paper: Rahmi Karolina, Syahrizal, M. Agung Putra, Tito Agung Prasetyo, The Use of Volcanic Ash of Mount Sinabung Eruption as the Substitution of Fine Aggregate in Making Batako (Mass-Produced Brick), Journal of Civil Engineering Research, Vol. 4 No. 3A, 2014, pp. 178-186. doi: 10.5923/c.jce.201402.31.
1. Introduction
Mount Sinabung, which is called Deleng Sinabung in Karonese, is one of the active volcanoes in the world; it belongs to the geological type of Statovolkano. Mount Sinabung eruption increased to the level of 4 (Alert) on November 24, 2013 since it spat out black, thick smokescreen, followed by sand rain and volcanic ash which covered thousands of hectares of farmers’ crops under the radius of six kilometers so that more than 20 thousand people had to be evacuated.This condition constituted the background for the use of volcanic ash material of Mount Sinabung eruption as the alternative for the substitution of the materials usually used for concrete. The idea was strengthened with the chemical content in the volcanic ash which had the same content as the one in sand and cement (SiO2, AL2O3, and CA O) obtained from the Research and Industrial Standardization Center, Medan. The testing material which would be used was batako (mass-produced brick).Batako is building material which consists of stones. Its hardening is not through kilning; it is shaped by the mixture of sand, cement, and water at the ratio of 1 cement: 7 sand. It can also be added by other additives and is molded through the process of compaction so that bars are shaped in a certain size. The process is not through kilning or placed in a damp place and protected from direct sunlight or rain. It is molded in such a way that it meets the requirement and can be used as the substitution of brick for a wall. The increasing demand for batako in the market will increase the need of the main raw material for it, particularly sand and cement. The availability of these materials is influenced by their location; in the mountainous terrain, the availability of sand is minimal since it is dominated by big gradation of materials. This condition has encouraged technicians to develop a material which could substitute or decrease the need for the construction material in order to reduce the cost of raw material without reducing the quality of the products. One of the alternatives which can be used to substitute sand and cement is volcanic ash as the additive for batako.The objective of the research was to find out whether batako, made from volcanic ash, met the qualification of quality I and quality II and to identify each optimum percentage of volcanic ash which met the requirements of the minimum of compressive strength of massive batako, according to SNI-3-0349-1989 standard.This research was expected to be the reference and information about the planning and developing building construction, particularly in batako industry and about the difference in using alternative material of volcanic ash with or without using it from the visual standpoint, water absorption, compressive strength, split tensile strength, and the implementation which could be used as the reference for feasible use of alternative material and of volcanic ash in batako mixture.
2. Research Method
2.1. Materials
Batako is usually made of sand, cement, and water. In this research, the materials used to make batako were cement, water, sand, and volcanic ash. The following was a glimpse of information about the materials which were used in making batako.1. Semen PortlandCement was created by a scientist, Joseph Aspidin in 1784. He was an English bricklayer who succeeded in making cement from the calcinations of limestone. In its process, the limestone and loam were ground to melt. The compound was then kilned in a furnace until the process of decomposition of dried limestone and carbon-dioxide. Dried limestone would react to other compounds to shape clinkers. SNI 15-2049-2004 defines Portland cement as hydraulic cement which is made by grinding Portland cement slag which consists of calciumsilicate with its hydraulic characteristic along with additives which comprises of one or more calcium sulfate compounds and can be added by other additives. Portland cement and pozzolan Portland cement are used in making batako, and since they are used for construction, they should have the quality which is in line with accuracy so that they can be used effectively. Cement will act fast when it is mixed with water so that it will be cement paste. It is not hardened because of drying but because of the reaction of chemical hydration. Therefore, batako should always be wet to ensure that it is properly hard. The hydration reaction releases heat which is called hydration-heat. The amount of heat depends on the type of cement, the fineness of grinding, and the water. This heat development can cause a crack during the cooling.The cement used in the experiment was Andalas cement in 50 kg packaging.2. SandAggregate (which does not react) is mixed materials for batako which are bound by cement paste. Sand and gravels are used as aggregate since they have economical. They are naturally found is shallow water (floating) or located at the bottom of the river and as the remnants when ice melts. The most important characteristic of aggregate (stones, gravels, sand, and others) is its crushing strength, and its resistance to collision which can affect its bound to cement paste, porosity, and the characteristic of water absorption. All of them will affect the resistance to congealment process in the winter and chemical aggression and resistance to shrinkage. The sand used in the research was taken from Binjai. The examination included:a. Analysis on sand strainer;b. Examination on the weight of fine aggregate;c. Examination on the organic content (colorimetric test) in fine aggregate;d. Examination on specific gravity in the cement and the volcanic ash;e. Examination on the mud content and the fine aggregate clay content.3. WaterWater constitutes the material for shaping batako. It is functioned to make chemical reaction possible in cement to be bound, to make it hardened, to wet aggregate, and to be used as mixing lubricant in order to make it easy in the process of making batako. It is also used to make the mixture become thick porridge and as the material for causing reaction in other materials to harden. Therefore, it is highly needed in the implementation of the process. Without it, material construction will not be feasible properly and completely.The water which was used as the mixing material came from the Engineering Material Laboratory of the Department of Civil Engineering, Faculty of Engineering, University of Sumatera Utara.4. Volcanic AshVolcanic ash is the mineral of volcanic stones, including glass material which is as big as sand and gravels with 2 mm (1/2 inch) in diameter from volcanic eruption. These minute ash particles can have section less than 0.001 mm (1/25.000th of an inch). It is very hard and cannot be dissolved in water so that it is often abrasive and slight corrosive, and it can deliver electricity when it is wet.The types of mineral in the volcanic ash depend on the chemical magma of the erupting volcano, by considering that the abundant element in magma is silica (SiO2) and oxygen. Various kinds of magma from volcano eruption are often explained by the parameter of its silica. Eruption which comes from low energy basalt (basalt: dark frozen stones and fine particles which come from the frozen lava of a volcano) produces specific dark ash which contains 74.3% of silica (SiO2), 3.31% of aluminum (AL2O3), and 1.79% of calcium as (CAO).In this research, the volcanic ash material which was used for batako was obtained from Mount Sinabung, about 4,600 meters from its top. Table 1. Chemical content of volcanic ash of Mount Sinabung eruption 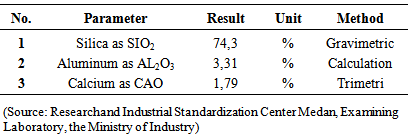 |
| |
|
2.2. Planning for Mixing
In order to calculate the amount of need of each material, the examination of the specific gravity of each material was conducted so that the composition of the materials from the volume of the testing device mold was calculated. The following is the composition of the need for the materials for the making of testing devices.
2.3. Designing of Testing Devices
The design for mixing of the material in arranging batako was the ratio of 1cement: 7 sand. The size of the testing device from outside view and the testing of absorption were made by using batako testing device of 40 x 20 x 10 cm. Cylinder testing device of 15x30 cm with a 10x10 cm batako piece were used to test the compressive strength, and a 15 x 30 cm cylinder testing device was used to test the pull strength. The variation of the adding of volcanic ash was done by reducing the amount of sand from 0%, 5%, 19%, 15%, 20%, and 25% of the weight of sand.
2.4. Treatment of Testing Device
Some tips for the treatment of each testing device are as follows:1. For batako testing device, keep batako from direct sunlight and rain in order that the fastening of the paste does not loose. Batako should be treated in 28 days by soaking the testing device in the soaking tub and keep the room temperature in the Engineering Material Laboratory of the Department of Civil Engineering, Faculty of Engineering, University of Sumatera Utara stable.2. For cylinder device, the treatment of cubic testing device was done by soaking it in the special soaking tub in the Engineering Material Laboratory of the Department of Civil Engineering, Faculty of Engineering, University of Sumatera Utara.
2.5. Testing the Testing Device
Some tips for testing each testing device are as follows:1. The testing of slump value was done by using Abrams’ pyramid, piercing iron, and pedestal. The mixing process was done manually.2. The testing for the size and the outside view was done by using a 40 x 20 x 10 cm batako testing device with a sliding bar. The testing was done when batako was 28 days for all variations.3. The testing for absorption was done by using a 40 x 20 x 10 cm batako testing device with an oven and a scale. The testing was done when batako was 28 days for all variations.4. The testing for compressive strength and pull strength was done by using a 15 x 30 cm cylinder testing device with a compression machine. The testing was done when batako was 28 days for all variations.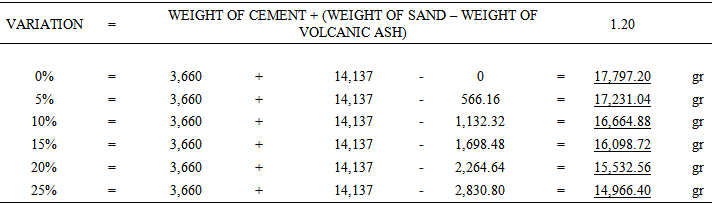 | Table 2. Calculation of the Need forBatako Testing Devices |
 | Table 3. Calculation of the Need for Cylinder Testing Devices |
3. Result and Discussion
3.1. Visual Testing
1. Outside View Testing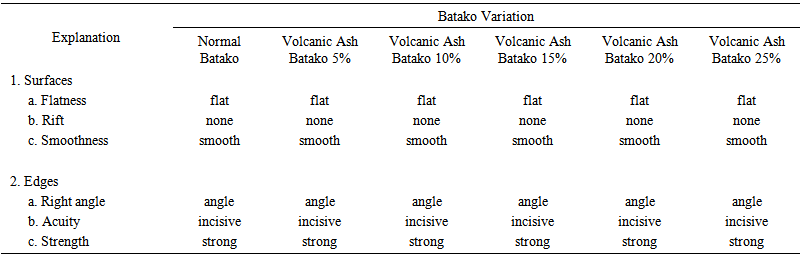 | Table 4. Result of Visual Examination |
The result of the examination showed that the use of volcanic ash as the substitution of fine aggregate from various variations in this research, produced batako which had flat surface, not rift, smooth and no cavity, and had met the requirement of outside view, according to SNI 03-0349-1989.2. Sectional Size ExaminationAfter the outside view had been examined, the examination on the dimension and section which met the provision of SNI 03-0349-1089 was done by using the average of five pieces of complete batako. A 1 mm accuracy of bar as the measurement instrument was used at least 3 (three) times in different places according to the length, width, and thickness of the testing device.The result of the analysis of the deviation of batako size from various variations of volcanic ash was as follows:Table 5. Result of Visual Examination 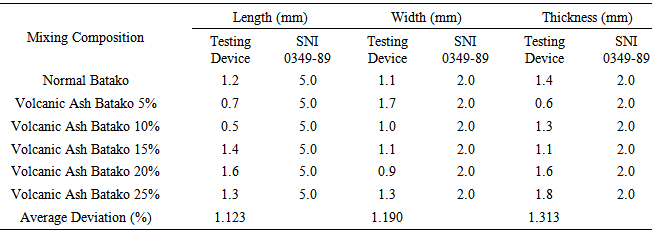 |
| |
|
The batako had met the requirement of SNI 03-0349-1989 standard because the volcanic ash had nearly the same particles as those of cement; it could penetrate the sieve No. 200, and the additives for volcanic ash could fill the cavity among the sand which caused batako to be solid so that its surfaces became flat.From the result of the examination, it was found that the condition of the shape and the section did not indicate significant difference; but, since the batako was made manually, its solidity was not uniformed. Besides that, the density of the pores in batako would highly influence the solidity of its composition.
3.2. Absorption Testing
The result of water absorption testing in batako was listed in Table 6. From the tested batako composition, it was found that the biggest water absorption in batako occurred in normal batako and in 0% of volcanic ash batako at the absorption value of 4.142%, and the smallest absorption in batako occurred in 15% of volcanic ash batako at the absorption value of 3.109%.Table 6. The comparison between the average water absorption and quality requirement 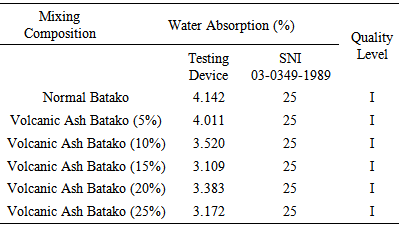 |
| |
|
The requirement of water absorption, according to SNI 03-0349-1989, was below 25% of water absorption for quality I level batako. Thus, it was one of the 5 variations which had met the requirement of water absorption, according to SNI 03-0349-1989.
3.3. Compressive Strength Testing
The recapitulation of the result of batako compressive strength of six types of the experimented mixture was in the following table:Graph 4.4 showed significant difference between the result of compressive testing, based on the tests on shape and concrete treatment method. The value of the testing of concrete compressive strength for cylinder testing device with treatment indicated the increase in the value of the maximum of concrete compressive strength in Volcanic Ash Batako at the mixing composition of 10% at the value of the average compressive strength of 207.14 kg/cm2 and it decreased to 130.97 kg/cm2.According to SNI 03-0349-1989, Volcanic Ash Batako of 0% till 25% with treatment belonged to quality I level, Volcanic Ash Batako of 5% with the average compressive strength of 86.54 kg/cm2 belonged to quality II level, and Volcanic Ash Batako of 10% with the average compressive strength of 105.12 kg/cm2 belonged to quality I level.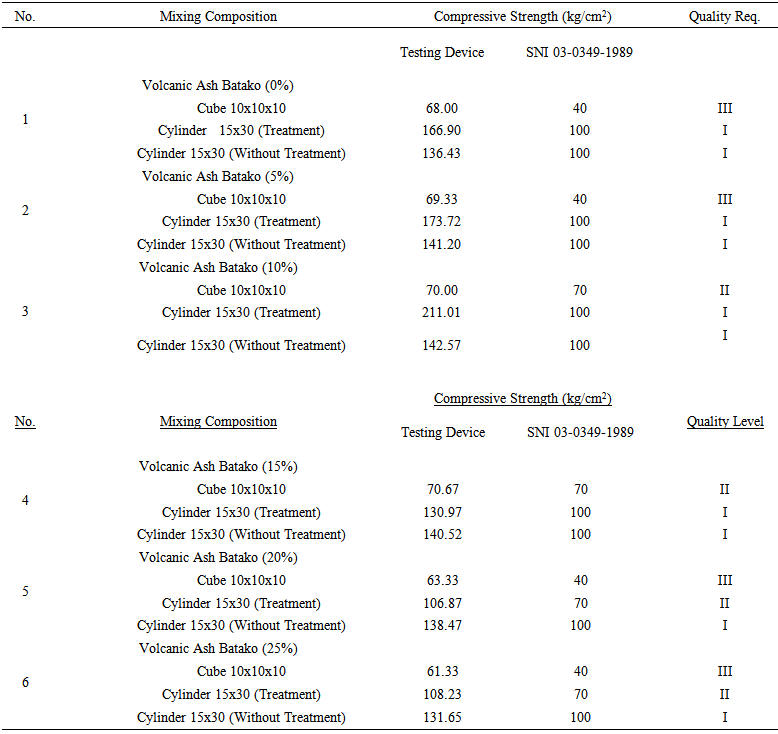 | Table 7. Comparison between the average compressive strength and quality requirement |
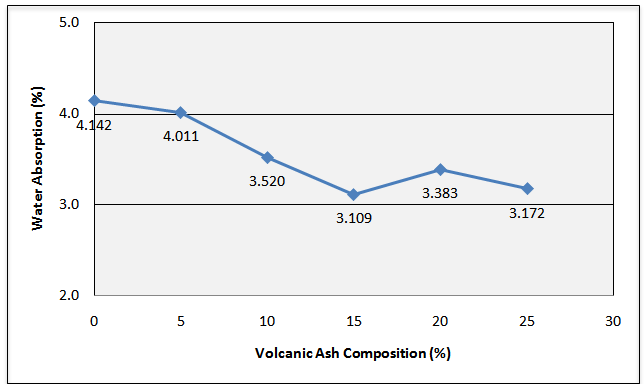 | Picture 1. Graph of Correlation between Batako Absorption and Volcanic Ash |
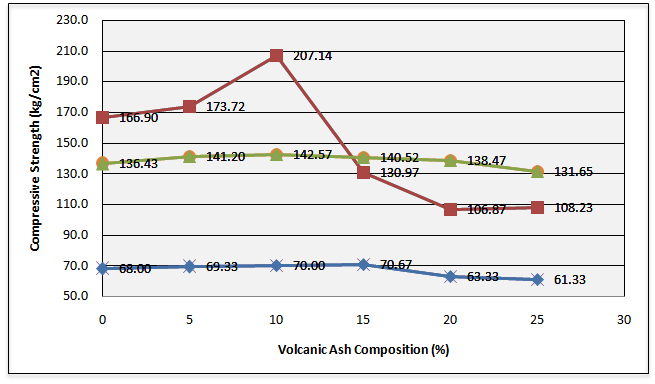 | Picture 2. Graph of the Correlation between batako Compressive Strength and Glass Powder Content |
Based on the compressive strength data and graphs, it was found that volcanic ash batako of 10% with treatment was the best composition and the maximum of compressive strength. This increase in compressive strength was because volcanic ash was domineered by silica arrangement material (SiO2) which had the superiority as the filling material. Empty cavity in the cement particles would be filled with micro-silica so that it functioned as mechanical property and increased its durability. Meanwhile, the decrease in compressive strength in Volcanic Ash Batako of 15% was caused by excessive volcanic ash composition. The consequence was that the mixture was not homogenous, the cement volume as a fastening material was not maximal in fastening the aggregate in arranging batako because it was not followed by the addition of cement and the need for water, and its workability decreased because water absorption was excessive. This condition was strengthened by visual observation of cylinder testing device of split tensile testing in the fragment of cylinder testing device in volcanic ash which could not be mixed well with other aggregates.
3.4. Briquette Pull Strength Testing
The above graph showed that the value of the highest pull strength was involcanic ash Batako of 10% with the treatment of 12.83 kg/cm2. Meanwhile, the lowest pull strength was in the volcanic ash Batako of 20% without treatment of 0.75 kg/cm2. Volcanic ash Batakoof 10% was the longest pull strength because the addition of volcanic ashto the mixture was over.Table 8. The Result the Average Split Pull Strength Testing 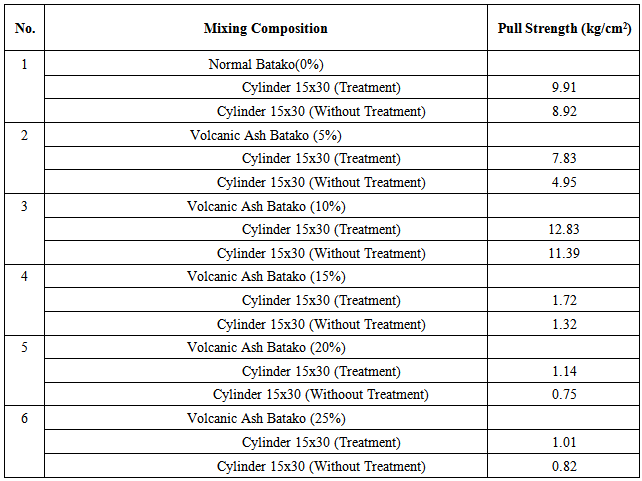 |
| |
|
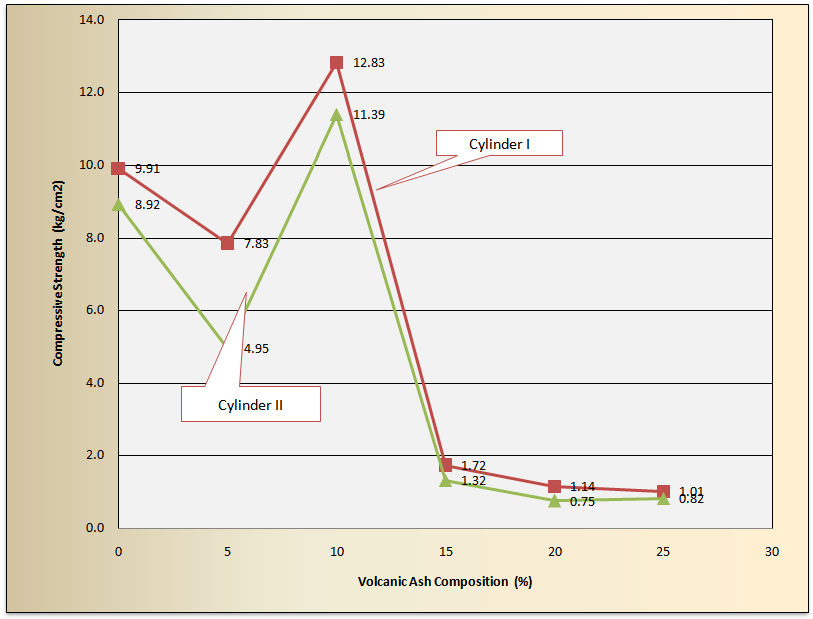 | Picture 3. Graph of the Correlation between Batako Pull Strength and Volcanic Ash Composition |
3.5. The Best Composition
The best composition was drawn from the result of the comparison of the requirement of quality VI mixing composition, molded as cylinder and batako testing devices with SNI 03-0349-1989 standard. The result of the best composition was the compressive strength for cylinder testing device with treatment at the mixing composition of 10% with the average compressive strength of 207.14 kg/cm2. According to SNI 03-0349-1989 quality standard, it belonged to compressive strength Level I at the minimal average of 100 kg/cm2 and composition.In the average pull strength of 12.83 kg/cm2 and the average water absorption of 4.142%, according to SNI 03-0349-1989, water absorption below 25% belonged to quality level Ibatako. The deviation of the average length was 1.123 mm, the deviation of the average width was 1.190 mm, the deviation of the average thickness was 1.313 mm, but they still met the measurement requirement which was in line with SNI 03-0349-1989 standard.
4. Conclusions and Suggestion
4.1. Conclusions
From the result of the research and the discussion, it could be concluded thata. the factor of cement water in batako mixture highly influenced the quality of batako. The higher its f.a.s., the lower its concrete quality; but if the use of the f.a.s. was reduced, the quality of the concrete would be better although the processing would be difficult because the making of batako in this research was done manually. Cement water used in this research was 40%.b. from the visual test, it was found that the surface of batako was average in each section because the volcanic ash which had nearly the same particles as the cement could fill the cavity of the sand so that batako became more solid which caused the surface of batako flat.c. the use of batako volcanic ash as an additive by replacing some of its weight could increase its absorption. The maximum of absorption in batako in this research was 4.142%. d. Based on the compressive strength data and graphs, it was found that batako volcanic ash of 10% with treatment was good composition and obtained the maximum of compressive strength. The increase in compressive strength was because volcanic ash was domineered by silica arrangement material (SiO2) which was superior as filling material. e. From the result of the research above, it was found that volcanic ash could be used as an additive in making batako.
4.2. Suggestion
Based on the conclusion and the discussion above, it is recommended thata. in order to obtain batako maximal compressive strength, volcanic ash with the composition of 10% should be used, and the treatment of concrete should be done by soaking it.b. in order to obtained good quality, accuracy, planning, work method, equipment, and selecting the materials should be done properly, according to the guidelines.c. There were a lot of limitations in the research; therefore, the next researchers should consider the following things:1). Selecting the materials highly influences the quality of batako which will be examine; mud content in sand can decrease the quality of the concrete which will need more cement;2). Chemical content in the volcanic ash should be examined so that the chemical content in the glass minute powder can be detected.3). Need for water as the reaction agent between cement and aggregates should be detected. This research was focused on the condition of soil moisture mixing so that determining and controlling f.a.s. was not done.4). Specific machine in making batako should be used so that maximal result can be obtained. Since the equipment used in the research was not adequate, the process of making batako was done manually so that it took a long time and the quality of batako was not similar and maximal.
References
[1] | Departemen P.U. (1989), SNI 03-0349-1989 Bata Beton untuk Pasangan Dinding, Balitbang, Jakarta. |
[2] | Departemen P.U. (2004), SNI 15-2049-2004 Semen Portland, Balitbang, Jakarta. |
[3] | Departemen P.U. (2002), SNI 03-2491-2002Metode Kuat Tarik Belah Beton, Balitbang, Jakarta. |
[4] | Mulyono, Tri. (2004). Teknologi Beton. Penerbit Andi: Yogyakarta. |
[5] | Nugraha, Paul. danAntoni. 2007. Teknologi Betondan Material, Pembuatan Beton Kinerja Tinggi. Yogyakarta: Andi Offset. |
[6] | Tjokrodimuljo, K. 1992. Teknologi Beton. Yogyakarta: Gramedia. |
[7] | Priantoro, Soerjandani. 2012. Pemanfaatan Abu Vulkanik Gunung Merapi Sebagai Alternatif Cementitious Untuk Campuran Pembuatan Bahan Bangunan. Surabaya: Universitas Wijaya Kusuma Surabaya. |
[8] | Kusumadhana, Ivandre. 2012. Penggunaan abu vulkanik Gunung Merapi untuk bahantam bahpem buatan genteng beton ditinjau dari kualitas fisik dan mekanik, Malang: Universitas Negeri Malang. |
[9] | Muldiyanto, Agus. 2012. Analisis pemakaian abu vulkanik Gunung Merapi untuk mengurangi pemakaian semen pada campuran beton mutu kelas II. Semarang: Universitas Semarang, 27 Juni 2012. |
[10] | Setyawan, TriHana Yuli. 2012. Penggunaan abu vulkanik Gunung Merapi untuk pembuatan batako ditinjau dari efisiensi biaya produksi. Malang: Universitas Negeri Malang. |
[11] | Wahyuni, E.I. 2012. Penentuan komposisi Kimia Abu ulkanindari Erupsi Gunung Merapi. Jurnal Malusiadan Ling kungan, (Online), Vol. 19. No.2, (hhtp://lib.law.ugm.ac.id, diasestahun 2012). |