M. Mageswari1, K. Deepa2, P. Saravanan3, S. Saravanan3
1Professor and Head of Civil Department, Panimalar Engineering College, Poonamallee, Chennai, 600123, India
2Associate Professor of Civil Department, Panimalar Engineering College, Poonamallee, Chennai, 600123, India
3Students of Civil Department, Panimalar Engineering College, Poonamallee, Chennai- 600123, India
Correspondence to: P. Saravanan, Students of Civil Department, Panimalar Engineering College, Poonamallee, Chennai- 600123, India.
Email: |  |
Copyright © 2014 Scientific & Academic Publishing. All Rights Reserved.
Abstract
High Energy Bricks using Polyisocyanurate Foam (also referred to as PIR Foam) can be considered relatively homogeneous when compared to normal Brick, as it does not contain any aggregrate. However, the properties of Brick depends on the microstructure and composition which are influenced by the type of binder used and method of pre-foamation. Though, it has been widely recognized as an high insulation material, a renewed interest is shown by researchers which exhibits its structural character. Energy Bricks are revolutionary green energy product that progress beyond the energy saving performance of any other conventional standard brick or brick masonry. Energy Bricks are found to have massive insulation rating. They are light in weight so that they can be installed very easily. Hence Energy Bricks reduce the construction time and also the cost of construction. They have very high load bearing capacity when compared to the conventional bricks. These energy bricks do not require any core filling and have a very good fire-resistant. Further thermal insulation is not required as the kernel of the brick has high insulation properties. The kernel of the brick consists of rigid PIR Foam. These energy bricks can be used in all cyclonic zones. We have chosen PIR Foam as the central core of the Energy Brick, because Polyisocyanurate (polyiso) insulation is an excellent choice for a variety of renovation applications because of its excellent energy conserving qualities. It has a high R-value per inch, which helps to reduce energy costs for the user till the life of the building and especially an important factor for considering the expected sustained rise in fuel costs. PIR also has self-extinguishing properties.
Keywords:
Poyisocyanurate, Energy Bricks, Foam, Production, Strength
Cite this paper: M. Mageswari, K. Deepa, P. Saravanan, S. Saravanan, Mechanical Properties of High Energy Bricks Using Polyisocyanurate Foam, Journal of Civil Engineering Research, Vol. 4 No. 2A, 2014, pp. 42-50. doi: 10.5923/c.jce.201401.09.
1. Introduction
1.1. General
Energy Bricks are a revolutionary green energy product that progress beyond the energy saving performance of any other conventional standard brick or brick masonry. Energy Bricks are been found to have massive insulation rating. They are light in weight so that they can be installed very easily. Hence Energy Bricks reduce the construction time, also the cost of construction. They have very high load bearing capacity when compared to the conventional bricks. These energy bricks do not require any core filling and have a good resistant towards fire. These energy bricks can be used in all cyclonic zones.Energy brick is also fire retardant due to the provision of non-combustible Calcium Orthosilicate skins along the sides of the brick and the PIR foam core having the self-extinguishing property. The PIR foam is fire safe with a non-combustible blowing agent who eliminates greenhouse gas emissions, avoids ozone depletion, and non-toxic. Calcium Orthosilicate Board provided along the sides of PIR Foam is of 10mm thickness. This makes the brick light in weight, supporting high load along with an attractive and aesthetic finish. It has excellent properties and functions of a double brick wall when compared to conventional bricks.The brick has a 30mm diameter hole passing vertically through every 95 mm for provision of electrical cabling, telephone lines or television lines after or during the construction of the wall. By using the Energy bricks labor cost can be reduced, faster construction can be facilitated and saves money. Energy Bricks is an initiative to aid individuals with a unique environment and friendly construction technique, so as to reduce the hazardous impact on our environment.
1.2. Selection of Material
1.2.1. Types of Insulation Material
For thermal performance, super-insulated light weight wall have been developed. This combination allows a building system that requires minimum installation and labor with maximum insulation value. The materials are used to reduce heat transfer by conduction, radiation or convection and are employed in varying combinations to achieve the desired outcome. Insulation may be categorized by its composition (material), by its form (structural or non-structural), or by its functional mode (conductive, radiative, convective). Non-structural forms include batts, blankets, loose-fill, spray foam, and panels. Structural forms include insulating concrete forms, structured panels, and straw bales. Sometimes a thermally reflective surface called a radiant barrier is added to a material to reduce the transfer of heat through radiation as well as conduction.Different types of insulation materials are available but we have selected Polyisocyanurate foam and calcium silicate board due to the following reasons. Installing a continuous layer of rigid foam insulation on the exterior side of the wall sheathing will interrupt thermal bridging through the studs while also reducing the rate of air leakage, whereas the other materials like Polyurethane and Isocyanate foams does not fulfill these criteria. Some types of foam insulation, such as polyurethane are blown with heavy gases such as chlorofluorocarbons (CFC) or hydro chlorofluorocarbons (HFCs). However, over time a small amount of these gases diffuse out of the foam and are replaced by air, thus reducing the effective R-value of the product. Rigid foam is more expensive than fiber, but generally has a higher R-value per unit of thickness. Foam-in-place insulation can be blown into small areas to control air leaks, like those around windows, or can be used to insulate an entire house. Spray foam is a type of insulation that is sprayed in place through a gun. Polyurethane and Isocyanate foams are applied as a two-component mixture that comes together at the tip of a gun, and forms an expanding foam. It will block airflow by expanding and sealing off leaks, gaps and penetrations. The cost can be high compared to traditional insulation.
1.2.2. Properties of Polyisocyanurate Foam
We have chosen Polyisocyanurate, also referred to as PIR, as the central core of the Energy Brick, because Polyisocyanurate (polyiso) insulation is an excellent choice for a variety of renovation applications because of its excellent energy conserving qualities. It has a high R-value per inch, which helps reduce energy costs for the homeowner over the life of the building - an especially important factor considering the expected sustained rise in fuel costs. PIR also has self-extinguishing properties.Polyisocyanurate insulation is a thermo set, closed-cell, rigid foam plastic insulation manufactured in the form of a paste. Via a continuous lamination process, liquid raw materials that expand and become light (yet strong) are applied between engineered facing materials. These facings provide strength, improve rigidity, and enhance thermal performance. The paste form of Polyisocyanurate (polyiso) is made rigid and most commonly supplied as 1.2-x-2.4-m or 1.2-x-2.7-m (4-x-8-ft or 4-x-9-ft) sheets in various thicknesses.
1.2.3. Properties of Calcium Silicate Board
The Calcium Silicate skins are non-combustible and form the interior and exterior skins of the brick of 10mm.The Calcium Silicate Board of the Energy brick would be the initial and main protective barrier in any fire situation and hence makes it the best in fire resistance. The Calcium Silicate board skin of the Energy Brick will not ignite or catch fire at temperatures in excess of 1000 degrees Celsius. This becomes particularly important when it is known that during the biggest bushfires in India, that temperatures reached approximately 600 degrees at the heart of the fire. The temperatures of this test far exceed these conditions.
1.3. Design Criteria
1.3.1. Manufacturing of PIR Foam
PIR foams are produced by mixing Polyester Polyol and methylene diphenyl di-isocyanates in a stoichiometric ratio (1:2), together with amine catalysts and other additives. PIR is obtained by the following reaction: At elevated temperatures, Methylene diphenyl di-isocyanate (MDI) in excess reacts with itself forming a highly cross-linked thermosetting complex polymer with a ring-like structure which means difficult to break and have high density. This MDI reaction will result in the compound named tri-isocyanate isocyanurate. 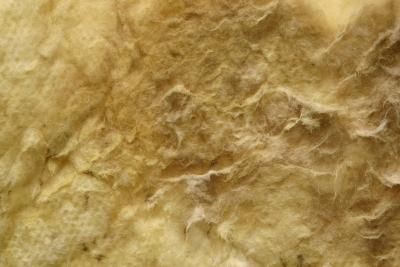 | Figure 1. PIR Foam Paste |
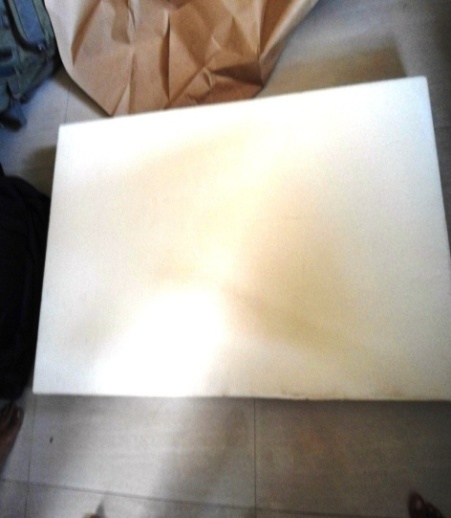 | Figure 2. PIR Foam |
The remaining MDI and polyol is mixed with tri-isocyanate which finally forms polymer of isocyanurate. This isocyanurate polymer has a comparatively strong molecular structure, because of the existence of strong chemical bonds contributing to the greater strength. The greater chemical bond also makes it difficult to break, which results in a stable PIR foam in both the properties of chemistry and thermal effect. The PIR foam was purchased from Shree Venus Energy Systems, Perumbakkam.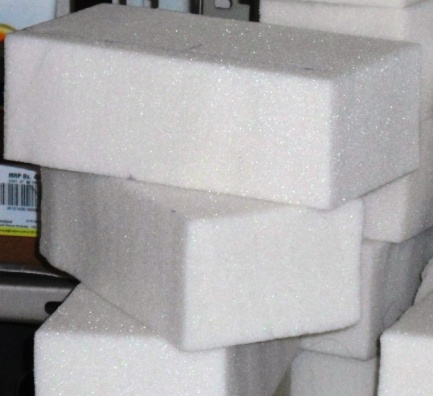 | Figure 3. Foam after Cutting into Brick Size |
1.3.2. Manufacturing of Calcium Silicate Board
A method of manufacturing a lightweight calcium silicate board using the Hatschek sheet machine process comprises of primary curing and thereafter hydrothermally reacted in a pressure vessel which is compact. The Calcium Silicate board was purchased from Ramco Hilux, Jaferkhanpet.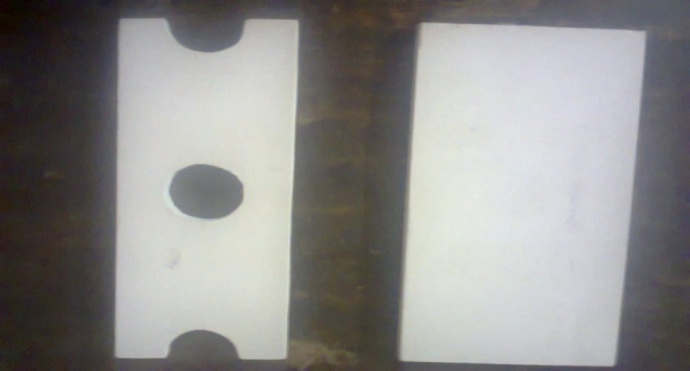 | Figure 4. Calcium Silicate Board after Cutting |
A method of manufacturing a calcium silicate board is characterized by the material slurry comprising its solid content 17 to 50 percent by weight of calcareous material, 15 to 45 percent by weight of siliceous material, 2 to 8 percent by weight of fibrous material, and 5 to 40 percent by weight of inorganic fillers, wherein at least one of the slurries in the first and last slurry tanks is the aforementioned slurry with 2 to 20 percent by weight of one or more species selected from alunites and alums with a Blaine specific surface area of 4000 cm.sup.2 /g or more or aluminum sulfate with a Blaine specific surface area of 2000 cm.sup.2 /g or more added to it, and the compact is subjected to primary curing. This material slurry is formed into board by molding and steaming the board will give dried calcium silicate board.
1.3.3. Connection between Foam and Board
Chloroprene rubber 20 is an elastomeric component derived from an oil resistant synthetic rubber. Its proportion was specially designed to glue polyiso with the insulation boards. This adhesive is applied in a bead form directly to a calcium silicate board. After which the board is placed onto the PIR foam. Once the adhesive is applied, chemical curing takes place for several minutes depending on temperature and weather conditions. 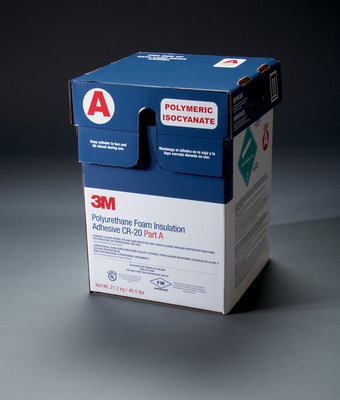 | Figure 5. CR 20 adhesive |
1.4. Brick Types
Each Full sized Energy Brick is 190mm long and 90mm wide (including the Calcium Silicate Board on the internal and external surfaces). Each Half brick is 95mm long. If the external dimensions of building are in multiples of 300mm there will be no need to cut any bricks. But Deduction for the window and door openings is required.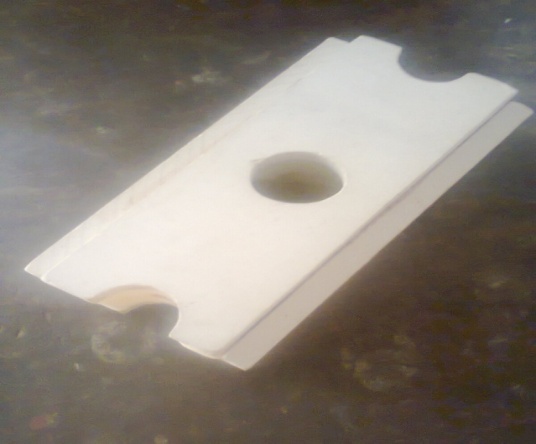 | Figure 6. Full Sized Green Energy Bricks (Type 1) |
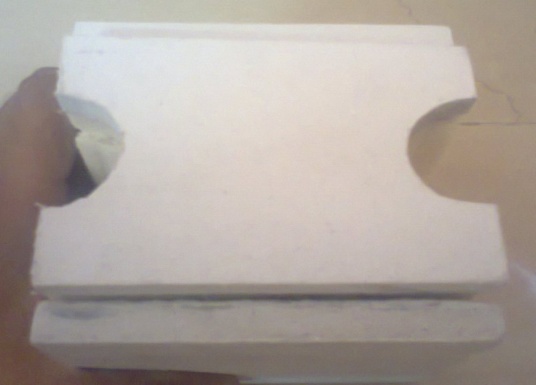 | Figure 7. Half Sized Green Enrgy Bricks (Type 2) |
A type 3 brick is used for corner in any building construction. Half sized calcium silicate board is used in longitudinal face and also in transverse face. 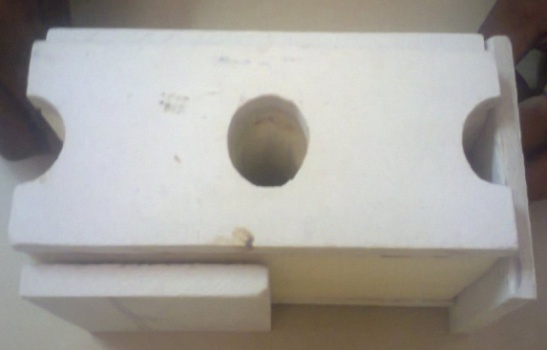 | Figure 8. Corner Bricks - Right Side (Type 3) |
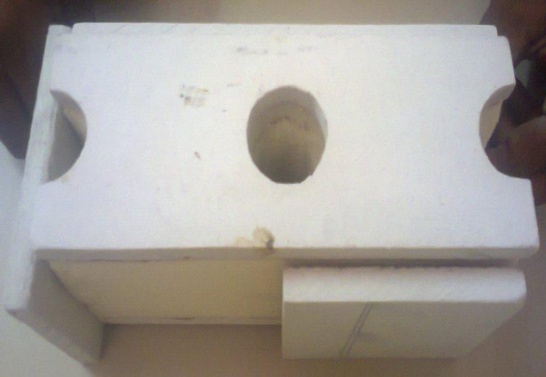 | Figure 9. Corner Bricks - Left Side (Type 4) |
 | Figure 10. Bricks for Openings - Full (Type 5) |
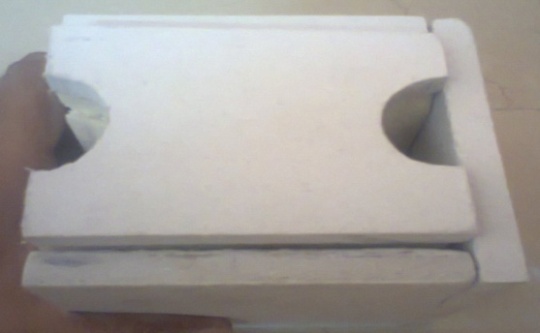 | Figure 11. Bricks for Openings - Half (Type 6) |
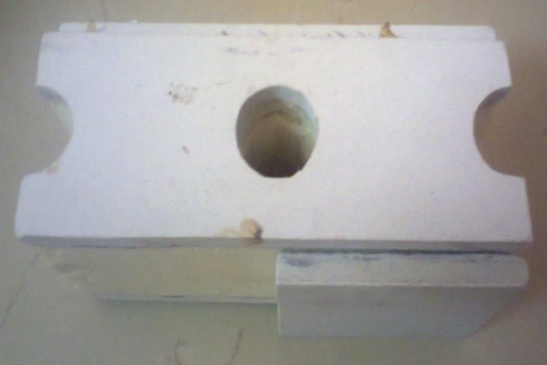 | Figure 12. Bricks for T-Junctions – Right Side (Type 7) |
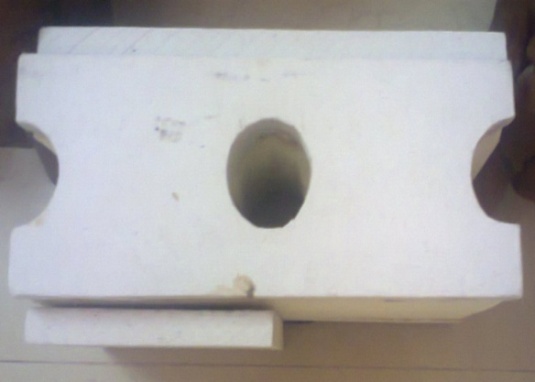 | Figure 13. Bricks for T-Junctions – Left Side (Type 8) |
1.5. Scope and Objectives
1.5.1. Scope
Scope of our project is to manufacture Green Energy bricks which are a revolutionary product that goes far beyond the energy saving performance values of any other brick or wall lining on the market today. The Energy Brick fulfils all the criteria to save time and cost yet gives the maximum energy savings when it comes to building a home.
1.5.2. Objective
The main objective of our project is l To produce Energy bricks which save labor cost, facilitates faster construction and saves money.l To reduce the emission of greenhouse gases and pollutants which are emitted during conventional brick manufacturing.l To improve the sustainability of energy production and increase energy efficiency. l To induce fire resistant qualities this is not found in any other conventional type brick. l To reduce the weight of the bricks as well as making it load bearing.l To minimize the negative impacts on the environment and to bring about healthier and environmentally sustainable buildings.
2. Experimental Studies
2.1. Calcium Silicate Board Test
The Calcium Silicate Board of the Energy brick would be the initial and main protective barrier in any fire situation. This test was to confirm how the Calcium Silicate Board would react to a naked flame of temperatures in excess of 1000 degrees Celsius. Set up a test where a naked flame of temperatures in excess of 1000 degrees Celsius was positioned to directly burn the Calcium Silicate board, and allowed to do so for a 10 minute period.
2.2. Pir Foam Core Test
To test how the rigid polyisocyanurate (PIR) foam, which forms the bulk of the Energy Brick, performs under a naked flame at temperatures in excess of 1000 degrees Celsius. Set up a test where a naked flame of temperatures in excess of 1000 degrees Celsius is directed specifically onto the PIR foam core. At the centre of the flame, the PIR foam core gave off a small amount of smoke without actually igniting at these extremely high temperatures. The moment the naked test flame was removed itself extinguished immediately.
2.3. Comparsion Test
This comparison test was to see how other types of bricks and blocks, which are currently in the market place, would perform under the same conditions of having a naked flame at temperatures in excess of 1000 degrees Celsius. Set up a test where a naked flame of temperatures in excess of 1000 degrees Celsius was positioned to directly burn the face surface of the bricks and blocks, and allowed to do so for a 10 minute period. The clay brick cracked after 7 and 14 seconds before starting to melt around the intense high pressure at the centre of the flame. The solid clay brick did not crack like the wire cut but did melt around the centre of the flame. The concrete blocks had varying results ranging from minor and major cracking, melting of the concrete to form a molten lump on the outside of the block at the most intense part of the flame. The Energy Brick far out performs both clay and concrete blocks under the test conditions with temperatures in excess of 1000 degrees Celsius.
2.4. Compressive Strength Test
To determine the compressive strength of the Energy Brick this has to be used as a structural wall. Crushing tests were carried out on whole block specimens. This material was low density foam which was subsequently modified by doubling the density to approximately 33 kg/m3. The compressive strength of the original sample was 130kPa.
2.5. Heat Transfer Test
A test wall was built using the Energy Bricks. Temperature loggers were placed in varying positions on both the internal and external surfaces of the wall to determine maximum, minimum and average temperatures at these locations. One side of the Energy Brick wall was placed against a furnace, and temperatures were increased until the exposed surface reached 1000°C. The exposed side of the Energy Brick reached 900°C after 35 minutes. The temperature loggers, which were placed on the opposite face of the Energy Brick wall, indicated an average temperature of only 28°C, with the highest temperature recorded at only 40°C.
2.6. Water Absorption Test
To conduct a test to determine the amount of water absorbed by green energy bricks when immersed in water for 24 hours. The specimen is weighed and obtains its weight as M1. The specimen is immersed completely in clean water at room temperature for 24 hours. The specimen is removed from water and any trace of water is wiped out with a damp cloth and the specimen is again weighed. This weight is noted as M2.
2.7. Insulation Test
To determine the "R value" of a wall, insulated window or ceiling requires three simple temperature measurements:1. The "air" or ambient room temperature.2. The inside surface temperature of an exterior wall.3. The outside surface temperature of the same exterior wall.The difference of the interior and exterior wall temperatures is calculated and this is labeled as "Temperature Difference, Interior to Exterior Wall". Now the difference between the "air" or ambient and the interior wall temperature is taken and this is labeled as "Temperature Difference, Air to Interior Wall". The interior to exterior difference is taken and the corresponding point is selected on the bottom of the graph given below. The air to interior difference is selected on the vertical axis of graph. Curve is chosen from these two points.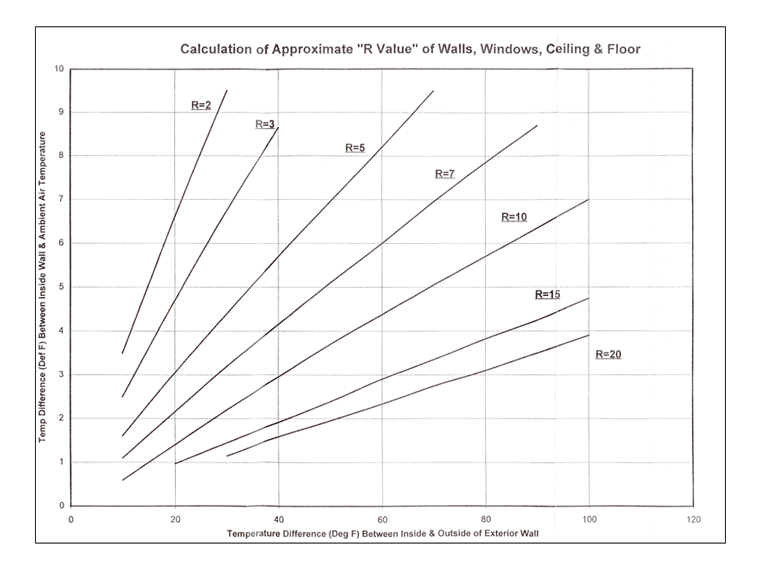 | Figure 14. R-Value Graphs |
3. Results and Discussion
3.1. Calcium Silicate Board Test
The Calcium Silicate Board did not catch fire, ignite or was penetrated in any way by the flame. A 2mm diameter mark was left on the Calcium Silicate Board where the most intense heat of the middle of the flame was situated. When left to cool down after the flame was extinguished the 2mm diameter area was scraped back using a sharp tool to find it only penetrated 2mm into the board and only at the very centre where the flame had been.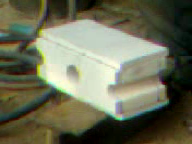 | Figure 15. Green Enery Bricks Set |
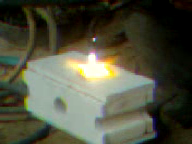 | Figure 16. Brick during Fire Test into Position |
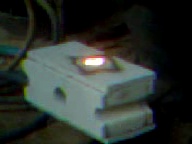 | Figure 17. Brick after Fire Test |
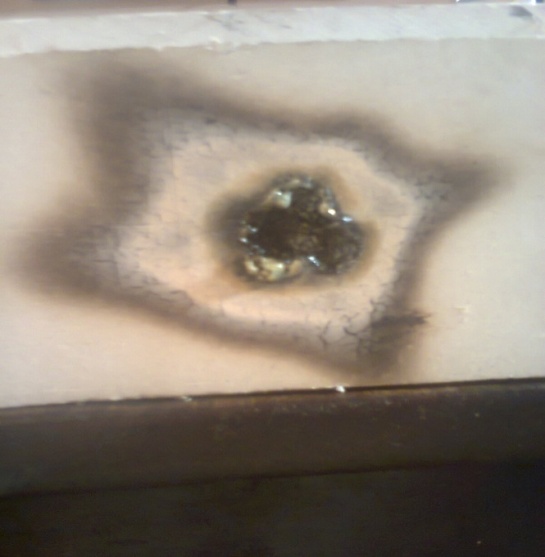 | Figure 18. Brick after Cooling |
It is been found from the test that the calcium silicate board does not spread fire and is resistant towards fire of temperature 1000°C. Black patches were found after the test was completed and was only up to 2mm.
3.2. Pir Foam Core Test
At the centre of the flame, the PIR foam core gave off a small amount of smoke without actually igniting at these extremely high temperatures. The moment the naked test flame was removed itself extinguished immediately. The PIR foam was self-extinguishing with minimal evidence of any fire damage. It is essentially a Non-flammable material. Even though the foam did not actually ignite or catch fire at these temperatures, it stopped having any effect on the rigid PIR foam core when the naked flame was removed. It should also be noted that the chances of any fire flame reaching the rigid PIR foam core would be very minimal. The 8mm protective Calcium Silicate Board of the Energy Brick will act as a major shield in any raging fire. You can feel safe in the knowledge that you will receive some of the best fire protection when the Energy Brick is used as part of the construction process. From this test it was found that the PIR foam has self-extinguishing properties. Even though it catches fire once the flame is removed it extinguishes within 15 seconds. Hence it is highly suitable in bush fire zones.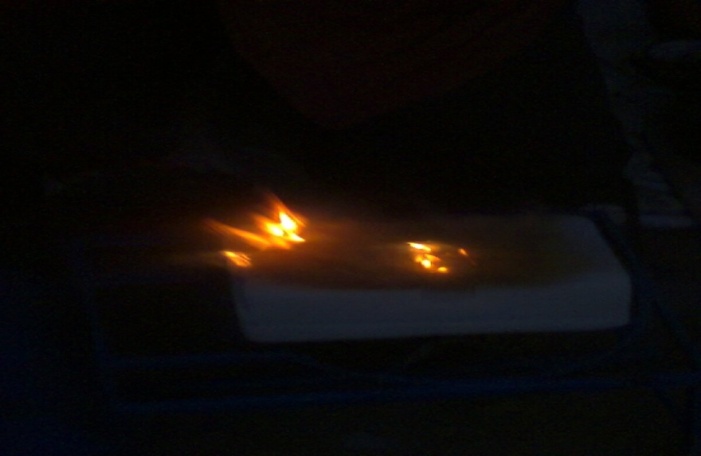 | Figure 19. PIR Foam during Test |
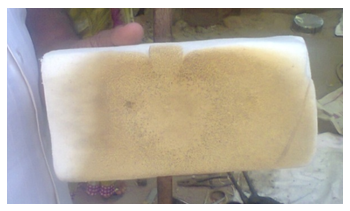 | Figure 20. PIR Foam after Test |
3.3. Comparison Test
The clay brick cracked after 7 and 14 seconds before starting to melt around the intense high pressure at the centre of the flame. The solid clay brick did not crack like the wire cut but did melt around the centre of the flame. The concrete blocks had varying results ranging from minor and major cracking, melting of the concrete to form a molten lump on the outside of the block at the most intense part of the flame.From the comparison test it is observed that the conventional bricks crack when exposed to fire whereas the Energy Bricks does not catch fire and no cracks were observed.
3.4. Compressive Strength Test
Compressive strength tests on the modified sample were carried out. Whole block tests returned the results above, that is, 380kPa. The stress/strain relationship is linear up to the yield point where collapse of the test specimen occurs. This yield point sets the maximum strength of the block. The stress/strain curve shows an initial set of approximately 1mm under test conditions. This suggests that there is a “bedding in” process when loads are applied through the platens. This condition will apply in wall building and a small pre-compression load should be applied through the top wall plate. 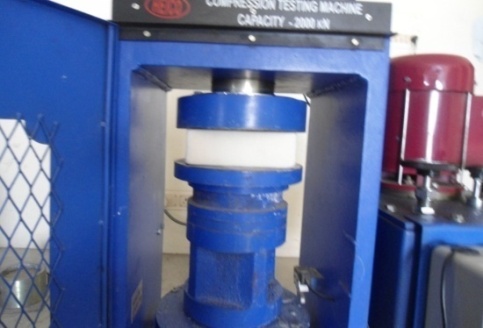 | Figure 21. Foam in Compression Test |
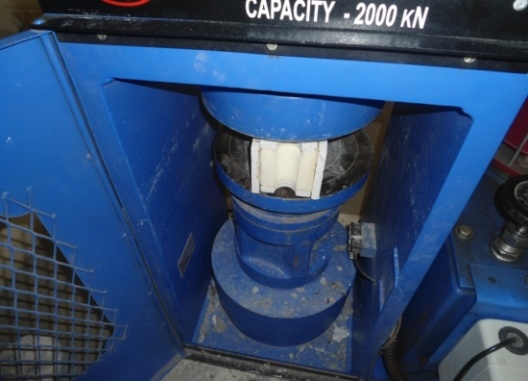 | Figure 22. Brick in Compression Test |
It is found that green energy bricks have high compression strength which can be used as structural element in any buildings. Further it has elasticity properties which means that central core of green energy bricks have the properties of regaining its original size after the removal of application of load. Green energy bricks will get more strength in practical than we tested in laboratory due to high insulation properties of it. This explains that it will get more strength due to wind action and threaded steel rod running vertical through it.
3.5. Heat Transfer Test
The exposed side of the Energy Brick reached 900°C. The temperature loggers, which were placed on the opposite face of the Energy Brick wall, indicated an average temperature of only 28°C, with the highest temperature recorded at only 40°C. The extreme heat on the exposed Energy Bricks was not transferred through the Bricks. This clearly indicates the Energy Bricks’ thermal resistance in extreme heat. An important observation to note is that the heat source did not have an effect on the Energy Bricks until after 10 minutes had elapsed, when temperatures had reached 700°C. After 25 minutes, the temperatures on the unexposed face began to be consistent at the average temperature of 28°C, even though the temperature on the exposed face was still steadily climbing beyond 830°C. Similar thermal resistance can be expected in regard to the Energy Bricks’ exposure to extreme cold.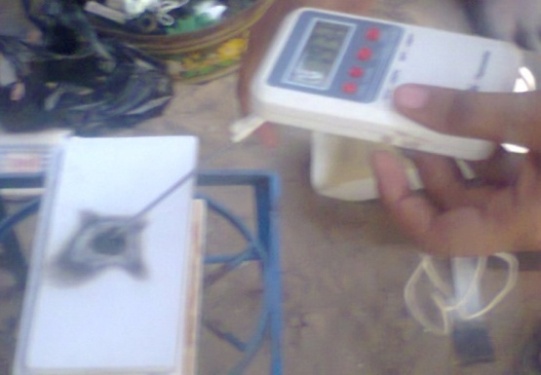 | Figure 23. Temperature Sensor on the Exterior Face |
The Energy bricks does not transfer high amount of heat when compared with conventional bricks. Even when the exterior part of the brick was exposed to 700°C the interior side of the brick remained to be unaffected and recorded room temperature.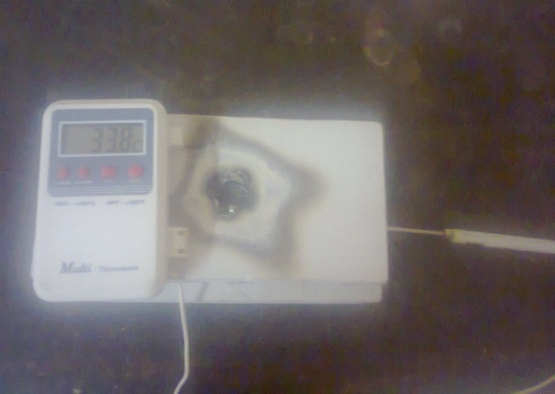 | Figure 24. Temperature Sensor on the Interior Face |
3.6. Water Absorption Test
The weight of the Energy Brick before immersing in water was found to be 0.620 Kg, and the weight of brick after immersing in water for 24 hours it was 0.629Kg. From the weights observed before and after immersing, the water absorption of the Energy Bricks was found to be 1.45%. 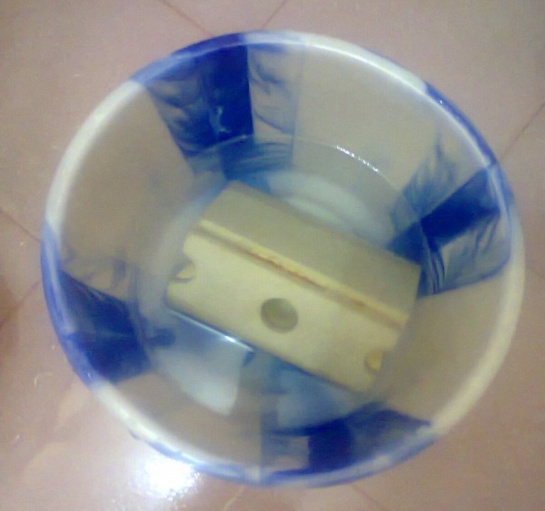 | Figure 25. Green Energy Bricks Immersed in Water |
The weight of the conventional brick before immersing in water was found to be 2.914 Kg and the weight of brick after immersing in water for 24 hours was 3.178 Kg. From the weights observed before and after immersing, the water absorption of the conventional bricks was found to be 9.05%.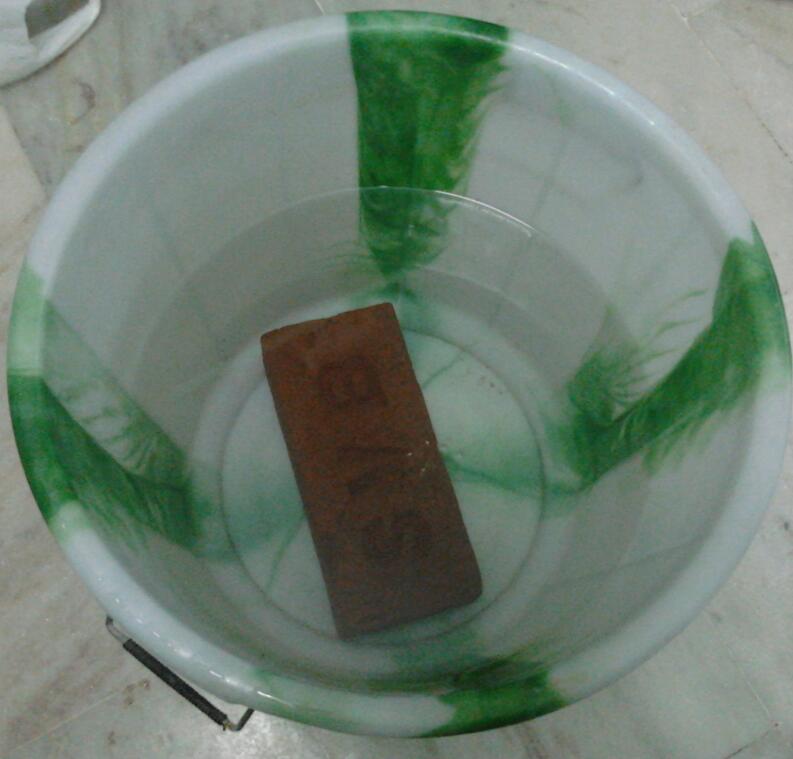 | Figure 26. Conventional Bricks Immersed in Water |
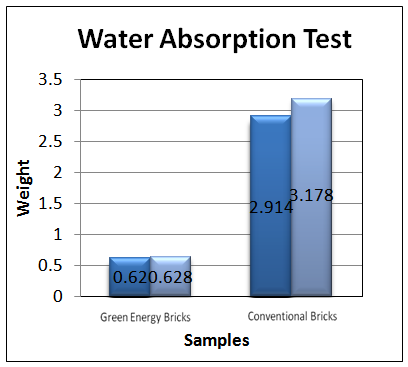 | Figure 27. Curve Showing Water Absorption Test |
From the water absorption test it is been observed that the Energy bricks absorb only 1.04% which is 9 times lesser than the conventional bricks. Further analyzing it is found that the PIR foam does not absorb any water and only the calcium silicate board absorbed water which when dried comes back to its original weight and the compression strength did not change either. Whereas the conventional brick absorbed 9.05% and when dried it strength of the brick was also altered. Hence the Energy Brick absorbs very less amount of water when compared to conventional bricks.
4. Conclusions
Energy Bricks deliver the new novelty in building construction. From the test results it is been observed thatl The bricks are load bearing, but also light weight.l It has superior properties with a massive insulation ratingl The Energy Brick can take up temperatures more than 500°C.l It has enormous R value when compared to conventional bricksl It is been observed that very less amount of heat is transferred by these bricks and can be used in variety of climatic zones. l The necessity of mortar and concrete filling in masonry can be completely eliminated by using the Energy Bricks and it also offers attractive and aesthetic finish. l The release of carbon-di-oxide during the manufacture of conventional clay bricks is nearly 8 million tonnes per year which can be completely reduced by the Energy Bricks as it does not release any gas during its manufacture. l Energy Bricks is an everlasting product that helps to economize construction cost, save labour costs, increase energy efficiency, faster construction times and save money.
References
[1] | Chi T. Do, Dale P. Bentz, and Paul E. Stutzman “Microstructure and Thermal Conductivity of Hydrated Calcium Silicate Board Materials” Building and Fire Research Laboratory National Institute of Standards and Technology Gaithersburg, MD USA 20899-8615. |
[2] | Masato Sakiyama, Takuya Asami, Tomoki Iwanaga “Method of manufacturing calcium silicate board”. |
[3] | C. Hall and Andrea Hamilton, “Physio Chemical Characterization of hydrated Calcium Silicate board” Journal article, 2005. |
[4] | I Boustead “POLYURETHANE RIGID FOAM” Plastic Europe, March 2005. |
[5] | Katrine Sivertsen “Polymer Foams” 3.063 Polymer Physics Spring 2007. |
[6] | Kaneyoshi Ashida “Polyurethane and Related Foams: Chemistry and Technology” 2007 Page no: 11. |
[7] | M.Kumar Kumaran, Ph.D., Phalguni Mukhopadhyaya, John Lackey “ Long-term thermal resistance of polyisocyanurate foam insulation with impermeable facers”. |
[8] | Olga Koronthalyova, Peter Matiasovsky “Thermo physical parameters of calcium silicate insulation measured by guarded hot plate and pulse transient methods” 1995. |
[9] | PIMA. “Polyiso Foam Roof Insulation: It’s More than R-value, It’s Meeting the Codes,” Advisories and other documents on www.polyiso.org, 2005. |
[10] | Sachchida N. Singh, Jody S. Fife, Sheila Dubs and Paul D. Coleman “Effect of Formulation Parameters on Performance of Polyisocyanurate Laminate Boardstock Insulation” Huntsman Advanced Technology Center. |