S. Sahoo, C. R. Mohanty, P. K. Pradhan
Civil Engineering Department, VSSUT, Burla, Odisha, 768018, India
Correspondence to: S. Sahoo, Civil Engineering Department, VSSUT, Burla, Odisha, 768018, India.
Email: |  |
Copyright © 2014 Scientific & Academic Publishing. All Rights Reserved.
Abstract
Solid-waste is a major challenge in urban and rural areas throughout the world. The waste generated from various human activities, both industrial and domestic, can result in health hazards and have a negative impact on the environment. Industrial solid waste is produced in huge amount and required vast area for its disposal.Dolochar is such a solid waste generated during the production of sponge iron. For production of 100 ton sponge iron, there are 154 ton of iron ore and 120 ton of (B-Grade) coal required. The solid waste generated during this process is around 45 ton and out of which 25 ton is dolochar. Till now, dolochar is dumped in neighbouring dump site which acquires Acers of valuable land. Investigation has been carried out on geotechnical properties and CBR value. Characterization study of dolochar reveal that the value of bulk density, maximum dry density, specific gravity, Coefficient of Uniformity,Coefficient of Curvature, pH was found to be 966 kg/mt3, 1.15, 2.13, 13.33, 2.13, 10.5 respectable. The CBR (soaked) value of dolochar sample was quite satisfactory. Number of test was carried for 4 and 7 day soaking with different percentage of lime (3%, 5% and 7%). The CBR value was found between 23-85 for 2.5mm and 5 mm penetration. These tests help us to know that it is a good aggregate and can be used on the construction of road.
Keywords:
Dolochar, CBR, Coefficient of Uniformity,Coefficient of Curvature, Maximum Dry Density
Cite this paper: S. Sahoo, C. R. Mohanty, P. K. Pradhan, Utilisation of Dolochar in Road Construction, Journal of Civil Engineering Research, Vol. 4 No. 2A, 2014, pp. 37-41. doi: 10.5923/c.jce.201401.08.
1. Introduction
Now-a-days disposal of different wastes produced from different Industries is a great problem. These materials possess environmental pollution in the nearby locality. For developing country like India industrialisation was must and still this activity very much demands to build self reliant and in uplifting nation’s economy. However, industrialisation on the other hand has also caused serious problems relating to environmental pollution. India can ill-afford to lose them as sheer waste. On the other hand, with increasing demand for raw materials for industrial production, the non-renewable resources are dwindling day-by-day. Therefore, efforts are to be made for controlling pollution arising out of the disposal of wastes by conversion of these unusable wastes into utilisable raw materials for various beneficial uses [1, 2]. In recent years, applications of industrial wastes have been considered in road construction with great interest in many industrialised and developing countries. The use of these materials in road making is based on technical, economic, and ecological criteria. India has a large network of industries located in different parts of the country and many more are planned for the near future. Several million metric tons industrial wastes are produced in these establishments. If these materials can be suitably utilised in road construction, the pollution and disposal problems may be partly reduced. Keeping in mind the need for bulk use of these solid wastes in India, the possible use of these materials should be developed for construction of low-volume roads in different parts of our country [3]. Dolochar is an industrial solid waste produced as a by-product of direct reduction of iron (DRI) process for the production of sponge iron. For the production of 100 t sponge iron, there are 154 t (65wt% Fe) iron ore and 120 t (B grade) coal required. The solid waste generated during this process is around 45 t and out of which 25 t is char and widely known as dolochar [4, 5]. Because of the non-availability of good grade coal, the sponge iron industries are using poor quality (F grade) coal with more than 40wt% ash content [6]. Therefore, the amount of raw materials required per tonne of product is higher than the ideal values, which in turn generate more waste. It has been estimated that there are 146 rotary kilns operating in Odisha, India. The total capacity of sponge iron production in these kilns is 16000 tonnes per day (TPD) and the corresponding dolochar generated is around 3.8 million tonnes per annum (TPA) [7]. The problem of dolochar generation is exorbitantly high due to the use of inferior quality of coal in the sponge iron manufacturing industry. Disposal of such a huge amount is a major concern. In view of finding out the use of dolochar as a material suitable for road construction, different tests have been carried out for dolochar to evaluate its engineering and geotechnical properties [8].
2. Experimental
2.1. Material
Dolochar sample of 70 kg from a operating sponge iron plant located at Sambalpur was obtained for detailed geotechnical characterisation studies.
2.2. Geotechnical Characterization
2.2.1. Appearance
Dolochar is generally black in colour with irregular size. The sample was passed in 4.75mm and 600µ IS sieve. Figure.1 (a) and 1(b) shows the sample and 600 passed in 4.75 mm µ IS sieve.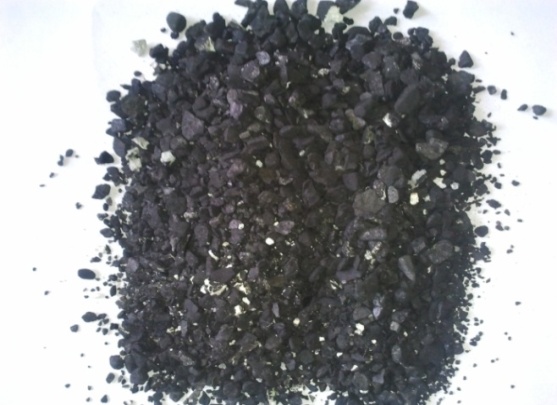 | Figure 1a. Sample passed in 4.75mm IS sieve |
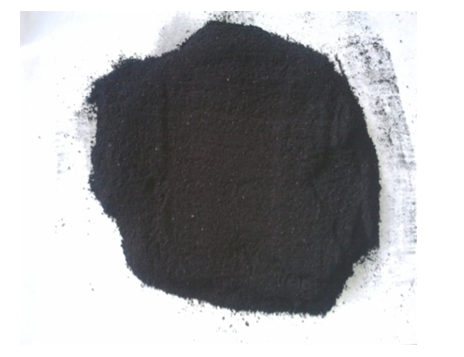 | Figure 1b. Sample passed in 600µ IS sieve |
300 gm of dolochar sample was taken and sieved through a nest of sieves which is consists of 4.75mm, 2mm, 1mm, 600µ, 420µ, 300µ, 150µ, 75µ. The total arrangement was placed in a mechanical sieve shaker and was shake it for 10 minutes.After that the machine was switched off and the total arrangement was unlocked. Dolochar was collected from each of the sieve and weighted it with a weighing machine, Figure.2 shows particle size distribution curve.
2.2.2. Sieve Analysis
This is known as particle size analysis or mechanical analysis. It is a method of separation of soils into different fraction based on particle size (here dolochar is analyse instead of soil).It expresses quantitatively the proportions, by mass, of various sizes of particles present in the dolochar sample.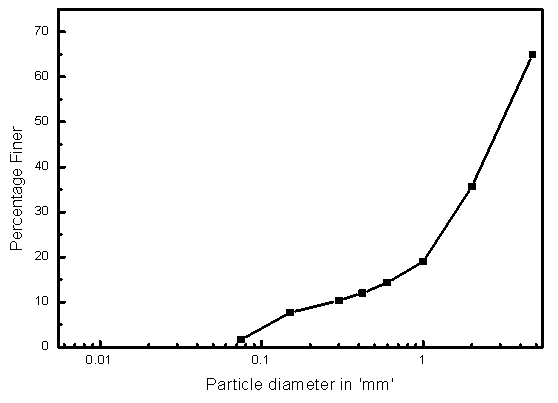 | Figure 2. Particle size distribution curve |
The uniformity of soil is expressed quantitatively by a term known as Uniformity Coefficient (Cu) and it was found to be 13.33. The general shape of the particle size distribution curve is described by another co-efficient known as coefficient of curvature (Cc) and it was found to be 2.13.
2.2.3. Specific Gravity (G)
First some sample was taken and was sieved through 4.75 mm IS sieve. A specific gravity bottle was taken and dried for some hour for the removal of water particles. Then empty weight of specific gravity bottle, specific gravity bottle and dolochar, specific gravity bottle and dolochar along with water and specific gravity bottle and water was taken and specific gravity was found to be 2.13.
2.2.4. Standard Proctor Test
First of all dolochar was sieved in 4.75mm IS sieve and 2.5 kg of sample was taken from that. After that the weight of the clean, empty mould was taken, then the base plate, mould and collar was properly lubricated by applying lubricant on its inner face. First 10% of water corresponding to the weight of dolochar was taken and both the sample was properly mixed with hand. The total dolochar was divided into 3 parts and 1st part was placed in the mould after all the attachment of base plate, mould and collar. Then the sample was compacted by a 2.6 kg rammer, with a free fall of 310 mm. For each layer 25 no of blows was given to the sample.Same procedure was carried out for 2nd and 3rd layer. After that the collar was detected and the surface was levelled by straight edge. The base of the mould was detected and the weight of the mould along with wet dolochar was taken. Then the dolochar sample was taken from the middle of the mould in the moisture tin whose empty weight was taken before. After that sample was placed in the moisture tin and the dolochar was taken out. Then the moisture was placed in the oven for 24 hour at 105-110℃. Then the weight of the moisture tin was taken. The process was repeated for different water content (10, 13, 15, and 18) %. Figure 3 show the relation between moisture content and Dry density.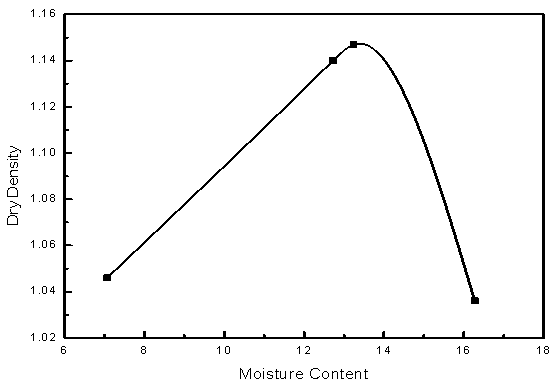 | Figure 3. Relation between maximum dry density & optimum moisture content |
2.2.5. PH value
The pH value of dolochar sample was found to be 10.5. It is alkaline in nature.
2.3. Results
Table 1 shows all the geotechnical properties of the above mention experiment.Table 1. Properties of dolochar 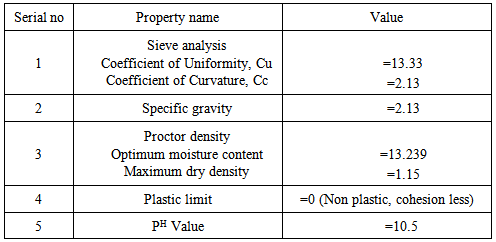 |
| |
|
3. California Bearing Ratio (CBR)
The California bearing ratio (CBR) test was developed by the California division of highway as a method of classifying and evaluating soil sub-grade and base course materials for flexible pavements. The CBR is measure of resistance of a material to penetration of standard plunger under controlled density and moisture conditions. The CBR test may be conducted in re-moulded or undisturbed specimen in the laboratory (we have used remoulded sample). The test is simple and has been extensively investigated for field correlation of flexible pavement thickness requirement [9, 10].First 4.5 kg of dolochar sample was taken and it was then sieved in a 20 mm IS sieve. First the sieved dolochar sample was taken along with optimum moisture content (OMC) 13.239 and was compacted in 3 layers. The sample was then soaked for 4 days and tested. Number of test was conducted with (3%, 5%, and 7%) of lime and soaked for 4 and 7 days and their value were calculated. Table 2 shows the CBR results for 2.5 and 5mm penetration.Table 2. CBR value of dolochar 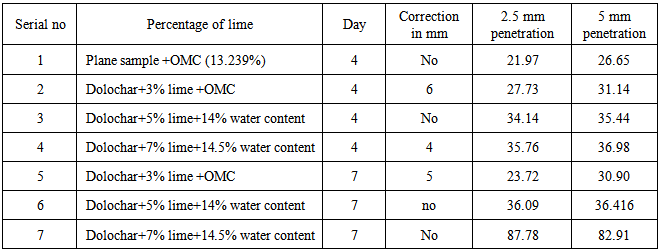 |
| |
|
Figure.4(a), 4(b), 4(c), 4(d), 4(e), 4(f) & 4(g) shows the curves between the proving ring reading and penetration of the plunger. These curves shows plane sample and sample having different percentage of lime with 4 and 7 days of soaking period. The penetration values corresponding to 2.5 and 5.0 mm penetration values (either from the original origin for curve without correction or from the corrected origin for the curve with correction, as the case may be) were found from the graph. Figure.4 (h) shows a typical CBR machine with mould loaded over the pedestal.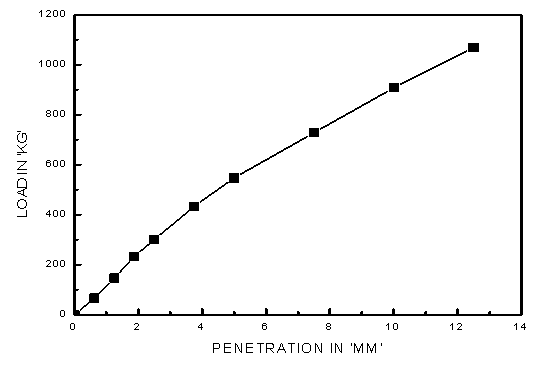 | Figure 4a. Plane sample+ OMC, 4 day soaked |
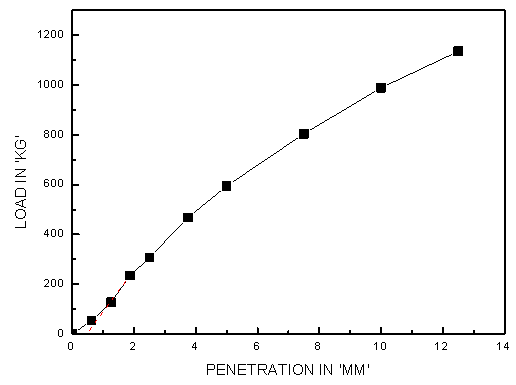 | Figure 4b. 3% lime + OMC, 4 day soaked |
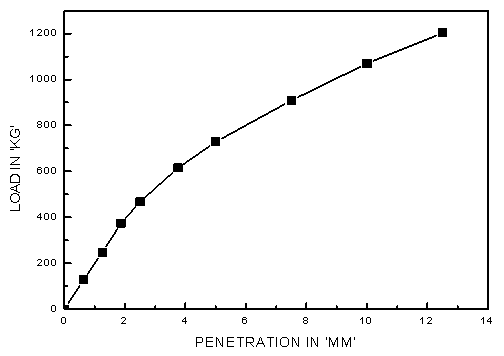 | Figure 4c. 5% lime + 14% WC, 4 day soaked |
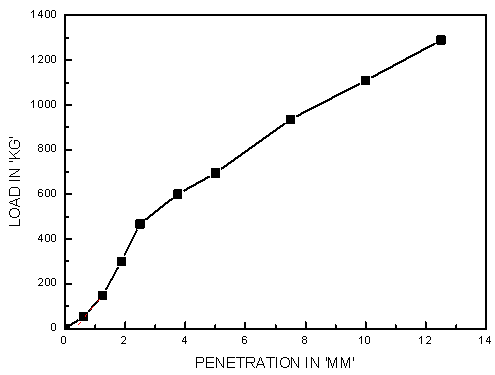 | Figure 4d. 7% lime + 14.5% WC, 4 day soaked |
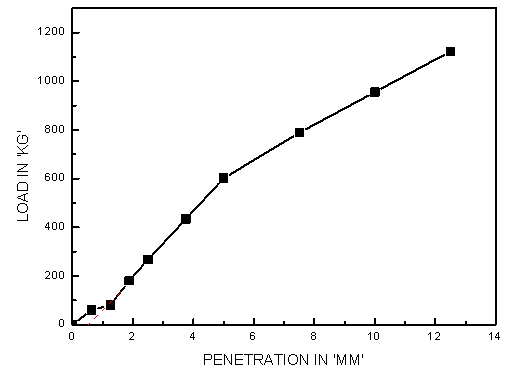 | Figure 4e. 3% limes + OMC, 7 day soaked |
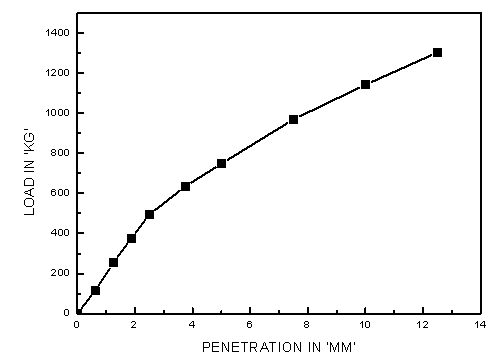 | Figure 4f. 5% lime + 14% WC, 7 day soaked |
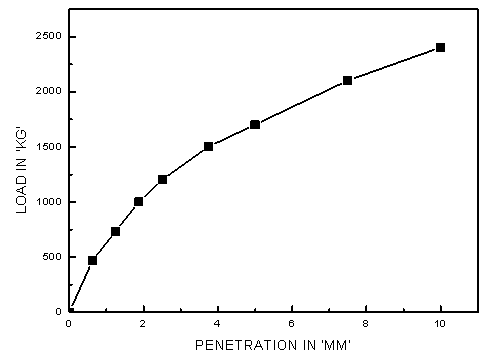 | Figure 4g. 7% lime + 14.5% WC, 7 day soaked |
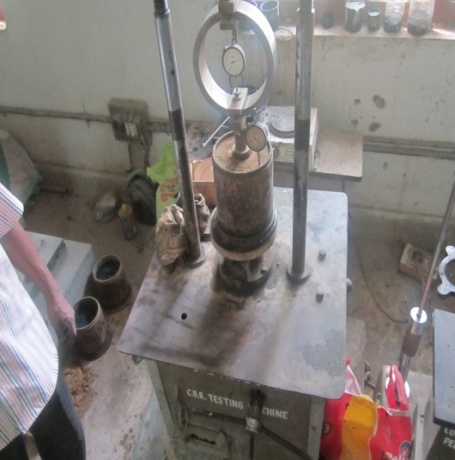 | Figure 4h. Sample tested with CBR machine |
4. Conclusions
It gives good results in CBR (California Bearing Ratio), so it can be used as a sub-base and base course in the construction of road.From the above tests it is clear that dolochar is a good filler material as it obtained less dry density and also contains some other satisfactory data.Leachability test should be conducted to check the possibility of leachate formation. Dolochar contain more than 18 percentage of carbon and which is not used, if this carbon is recovery then it is beneficial to the society and it also help to save some part of fuel.
References
[1] | V Kumar, M Mathur, S S Sinha “A Case Study: Manifold Increase in Fly Ash Utilisation in India@” Fly Ash India 2005. |
[2] | M. Ahmaruzzaman” A review on the utilization of fly ash” Progress in Energy and Combustion Science 36 (2010) 327–363. |
[3] | Tara Sen and Umesh Mishra “Usage of Industrial Waste Products in Village Road Construction”, International Journal of Environmental Science and Development, Vol. 1, No. 2, June 2010 ISSN: 2010-0264. |
[4] | P.U. Asnani “Solid waste management”. |
[5] | P.A. Botha “Iron-ore sinter produced from a mix containing waste Materials” J. S. Afr. Inst. Min. Metall., vol. 93, no. 1. Jan. 1993. pp. 13-19. |
[6] | A. Chatterjee, Acritical appraisal of sponge iron production technologies, [in] Proceedings of National Seminar on Potential of Sponge Iron in Indian Steel Industry, Ranchi, 2005. |
[7] | R K Dwari, D S Rao, A K Swar, P Sita Ram Reddy and B K Mishra) “Characterization of dolochar wastes generated by the sponge iron industry” International journal of minerals, Metallurgy and materials, vol 19, Number 11, Nov 12, p.992. |
[8] | N. S. PANDIAN “Fly ash characterization with reference to geotechnical applications” J. Indian Inst. Sci., Nov.–Dec. 2004, 84, 189–216. |
[9] | K. Bandyopadhyay and Sunanda Bhattacharjee “laboratory cbr values of fly ash under different conditions” IGC 2009, Guntur, INDIA. |
[10] | R.K Sharma “Subgrade Characteristics of Locally Available Soil Mixed With Fly Ash and Randomly Distributed Fibers” International Conference on Chemical, Ecology and Environmental Sciences (ICEES'2012) march 17-18, 2012 Bangkok. |