Niveditha C., Sarayu K., Ramachandra Murthy A., Ramesh Kumar V., Nagesh R. Iyer
CSIR-Structural Engineering Research Centre, CSIR Road, Taramani, 600 113, Chennai
Correspondence to: Sarayu K., CSIR-Structural Engineering Research Centre, CSIR Road, Taramani, 600 113, Chennai.
Email: |  |
Copyright © 2014 Scientific & Academic Publishing. All Rights Reserved.
Abstract
Seaweed (algae), that is a rich source of minerals, vitamins and other vital materials has been used in the present study to strengthen the cement mortar. The processed algae was subjected for chemical characterization using the XRD and SEM to know the chemical components present in it. Based on the observation obtained, the algae was further used for the strength enhancement of cement mortar. The 10% replacement mortar cubes have shown about 4% increase and 20% replacement have shown 3.5% increase in the 28th day compressive strength when compared to that of the control specimens. So, it was found that 10% replacement of algal precipitate was optimum.
Keywords:
Marine algae, Cement mortar, Strength enhancement, XRD, SEM
Cite this paper: Niveditha C., Sarayu K., Ramachandra Murthy A., Ramesh Kumar V., Nagesh R. Iyer, Marine Algae for Cement Mortar Strengthening, Journal of Civil Engineering Research, Vol. 4 No. 2A, 2014, pp. 23-25. doi: 10.5923/c.jce.201401.05.
1. Introduction
Marine algae has long been known as an important contributor of sand and mud-size carbonate sediment from the mid-Jurassic to the Holocene [7], [2]. [11], [6], [18], [15], [17]. [5] and [16] describe the above are the specific marine algal rich Pacific ocean modern sites, and [13], [14], [19], [4] and [10] do the same for the Caribbean sea.Despite the obvious and substantial role that marine algae plays in both ancient and modern ages, the reef environments, actual field studies and sediment production rates for various species of marine algae in today's tropical environments are limited. This is probably due to the difficulty in measuring segment release from a plant that grows by unpredictable "spurts", varies in percentage of CaCO3 with age [1], [4], and varies in growth rate by species [9], [4] and perhaps with depth [3]. Such variables, combined with unpredictable tropical storm damage to sampling sites [12] and patchy nature of the algal growth [8], have discouraged attempts at evaluating production rates. Concrete is the most widely used material in the construction sector. The major ingredients of it are the cement, sand, gravel and water. Cement is the binder material that can harden independently binding the other materials in concrete. Cement manufacturing causes environmental impact at all the stages of its processing, so development of green cement has become the main area of interest. The biomimicry and biotechnological investigation is being conducted to create concrete the way nature does with microorganisms and other bio-products in the environment. Therefore, a bioconcrete would be a suitable substitute for cement based concrete and can be easily produced. Biologically Inducing Precipitation of Calcium carbonate (the cementing agent) from bacteria, algae and fungi can solve the purpose.
1.1. Objective and Scope
Present study deals with the utilization of the marine algal precipitate as a cement replacement product. The algal precipitates are rich in compounds like calcium carbonate and calcium silicate.
2. Materials and Methods
2.1. Collection of Algae and Its Precipitates
The live and dead form of marine algae was collected from the Gulf of Mannar region. Grown in laboratory "Figure 1". The precipitate from the dead algae was collected by grinding the dried algae using a mortar and pestle.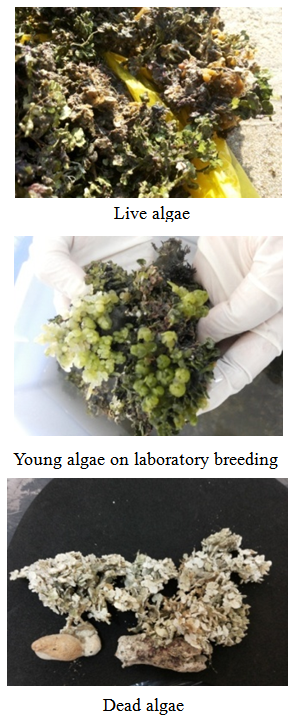 | Figure 1. Laboratory cultivation of the marine algae |
2.2. Characterization of Algae and Algal Precipitate
The morphological arrangement, shape structure of the live algae, dead algae and the precipitate was characterized by obtaining the scanning electron micrographs and the composition of the algal precipitate was characterized using XRD and EDX.
2.3. Algal Cement Mortar
The cement mortar of 70.6mm/70.6mm/70.6mm was prepared using 53 grade ordinary portland cement of IS 12269-1987 standards and grade 2 sand of IS 383-1970 for the study. The water cement ratio was maintained as 0.4 based on the standard consistency tests carried out. Two sets of cubes were casted the first set with 10% replacement of cement with the algal precipitate and the second with 20% replacement. The cubes after curing with water was tested for compressive test on the 3rd, 7th and the 28th days of curing.
3. Results and Discussion
3.1. Characterization of Algal Precipitates
XRD results have shown the presence Quartz in the algal precipitate with a predominant peak at the 2θ (Bragg's angle) = 26, 28 and 40, the presence of calcium is confirmed by the peak obtained at 2θ = 34 and the presence of magnesium is also observed by the peak at 2θ = 38 and 42 "Figure 2". Scanning electron micrographs have revealed the shape and structure of the precipitates "Figure 3". 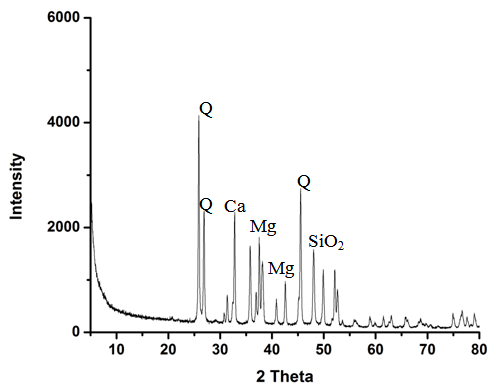 | Figure 2. XRD of the algal precipitates |
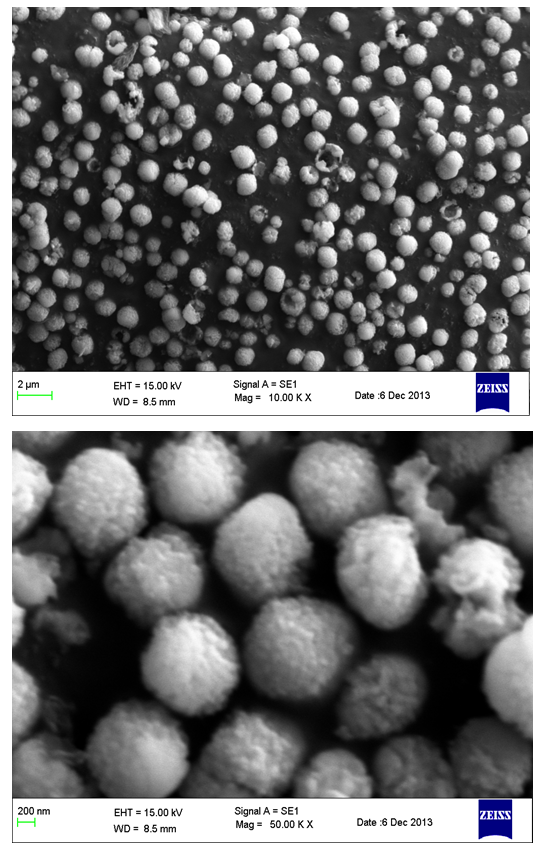 | Figure 3. SEM of the algal precipitates |
The particles appeared to be spherical in shape, porous in nature and were about 200nm in size "Figure 3".
3.2. Evaluation of Improved Mechanical Properties
The control specimens have achieved a strength of 40.2 MPa in 28 days. About 47% of the 28th day compressive strength was achieved in the initial 3 days of curing in water and about 65% of 28th day compressive strength was achieved in the 7 days of curing. Mortar specimens with 10% cement replacement with algal precipitate have demonstrated a compressive strength 19.2, 26.7 and 41.8 MPa on the 3rd, 7th and the 28th day respectively. About 46% of the 28th day compressive strength of the 10% replacement specimens were obtained in initial 3 days of curing and about 64% was obtained in the 7th day "Figure 4". Mortar specimens with 20% cement replacement exhibited a compressive strength of 18.7, 26.2 and 41.6 MPa on the 3rd, 7th and the 28th day of curing. In this about 45% of the 28th day strength was observed in the 3rd day of curing and 63% of the strength was observed in the 7th day of curing. The 10% replacement mortar cubes have shown about 4% increase and 20% replacement have shown 3.5% increase in the 28th day compressive strength when compared to that of the control specimens.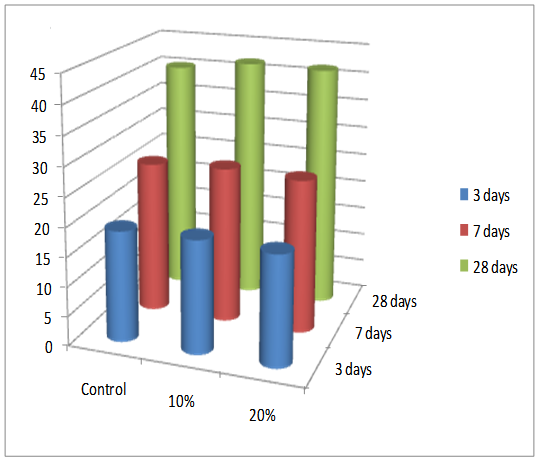 | Figure 4. Evaluation of compressive strength |
4. Conclusions
As the algal precipitate is rich source of calcium, silica and carbonate materials, the compressive strength of the test specimens of 10% and 20% cement replacement with algal precipitate was found to increase with that of the control specimens. This may be due to the enhanced CSH formation.
ACKNOWLEDGEMENTS
The authors are thankful to the Director, CSIR- Structural Engineering Research Centre, Chennai for allowing us to publish this work. Part of the research work has been carried out with equipment of CSIR innovation Complex for which authors would like to thank Director, CSIR-SERC.
References
[1] | Abel, K.M. and Drew, E.A. (1985) ‘Response of Halimeda metabolism to various environmental parameters.’ Proceedings of the 5th International Coral Reef Symposium. 5:21. |
[2] | Achauer, C.W and Johnson, J.H. (1969) ‘Algal Stromatolites in the James Reef Complex (Lower Cretaceous), Fairway Field, Texas. ’Journal of Sedimentary Petrology. 39(4): 1466-1472. |
[3] | Bohn, E.L. (1973) ‘Studies on the mineral content of calcareous algae.’ Bulletin of Marine Sciences. 23:177–190. |
[4] | Colinvaux, H.L. (1980) ‘Ecology and taxonomy of Halimeda: primary producer of coral reefs.’ Advance Marine Biology. 17:1-327. |
[5] | Colinvaux, H.L. (1986) ‘Halimeda growth and diversity on the deep fore-reef of Enewetak Atoll.’ Coral Reefs, Springer. 5(1):19-21. |
[6] | Drew, E.A. (1983) ‘Halimeda biomass, growth rates, and sediment generation on reefs in the Great Barrier Reef Province’. Coral Reefs, Springer 2:101-110. |
[7] | Elliot, G.F. (1960) ‘Fossil calcareous algal floras of the Middle East with a note on a Cretaceous problematicum, Hensonella eylindrica.’ Quarterly Journal of the Geological Society. 115:217-232. |
[8] | Gilmartin, M. (1960) ‘The ecological distribution of the deep water algae of Eulwetok Atoll.’ Ecology 41:210-221. |
[9] | Goreau, T.F.(1963) ‘Calcium carbonate deposition by coralline algae and corals in relation to their roles as reef-builders.’ Annual New York. Academy of Sciences. 109:127 167. |
[10] | Hudson, J.H. (1985) ‘Growth rate and carbonate production in Halimeda opuntia: Marquesas Keys, Florida. In: Toomey DF, Nitecki MH (eds) Paleoalgology: contemporary research and applications.’ Springer, Berlin Heidelberg New York. |
[11] | Maxwell, W.G.H. (1968) ‘Atlas of the Great Barrier Reef.’ Elsevier, Amsterdam. |
[12] | Merten, M.J. (1971) ‘Ecological observations of Halimeda macroloba Decaisne (Chlorophyta) on Guam.’ Micronesia 7:27~44. |
[13] | Milliman, J.D. (1973) ‘Caribbean coral reefs. In: Jones AO, Endean R (eds) Biology and geology of coral reefs.’ Academic Press, New York. 1(1):1–50. |
[14] | Milliman, J.D. (1974) ‘Recent sedimentary carbonates, part I, marine carbonates.’ Springer, Berlin Heidelberg New York. |
[15] | Phipps, C., Davies, P.J., Hopley, D. (1985) ‘The morphology of Halimeda banks behind the Great Barrier Reef east of Cooktown, Queensland.’ Proceeding of the 5th International Coral Reef Symposium.5:27-30. |
[16] | Roberts, H.H., Aharon, P., Phipps, C.V. (1998) ‘Morphology and sedimentology of Halimeda bioherms from the eastern Java Sea (Indonesia).' Coral Reefs. Springer 6 161-172. |
[17] | Scoffin, T.P. and Tudhope, A.W. (1985) ‘Sedimentary environments of the Central Region of the Great Barrier Reef of Australia.’ Coral reefs, Springer. 4(2):81-93. |
[18] | Tudhope, A.W. and Risk, M.J. (1985) ‘Rate of Dissolution of Carbonate Sediments by Microboring Organisms, Davies Reef, Australia.’ Journal of Sedimentary Petrology.55 (3): 440-447. |
[19] | Wefer, G. (1980) ‘Carbonate production by algae Halimeda, Penieillus and Padina.’ Nature. 285:323-324. |