Saravanan M., Karunakaran N.
Department of Mechanical Engineering, Annamalai University, Annamalai Nagar, India
Correspondence to: Saravanan M., Department of Mechanical Engineering, Annamalai University, Annamalai Nagar, India.
Email: |  |
Copyright © 2016 Scientific & Academic Publishing. All Rights Reserved.
This work is licensed under the Creative Commons Attribution International License (CC BY).
http://creativecommons.org/licenses/by/4.0/

Abstract
V-Grooved solar collector (VGSC) was designed and constructed at Measurements and Dynamics lab of Annamalai University and its thermal characteristics were analyzed on an indoor test facility. Integrating the V-Grooved absorber plate with flat plate collector can improve the system performance. VGSC system uses circular heat pipe of length 900 mm and diameter of 18mm. The output responses such as heat output, thermal resistance and overall efficiency has been analyzed with respect to circular heat pipe experimentally by using commercial Design of Expert version DX 9 software by using Box- Behnken design of Response Surface Method (RSM). Contour diagram with factors affecting the thermal behaviour of the heat output, thermal resistance and overall efficiency have been shown. From the mathematical results and RSM optimization it is concluded that experimental setup integrated with circular heat pipe gives higher heat output and overall efficiency with less thermal resistance.
Keywords:
V-grooved solar collector, Heat pipe, Heat output, Thermal resistance, RSM
Cite this paper: Saravanan M., Karunakaran N., Thermal Characteristics of V-Grooved Solar Collector with Circular Heat Pipe, Energy and Power, Vol. 6 No. 1A, 2016, pp. 1-7. doi: 10.5923/c.ep.201601.01.
1. Introduction
Solar energy is the radiation resulted by nuclear fusion reactions in the sun. Only 30% of the solar power actually reaches the Earth, however every 20 minutes the sun produces enough energy to cater to the earth’s demand for an entire year [1] and the easiest way of harnessing solar energy is to directly convert it in to useful thermal energy. Many different kinds of equipment are available for this conversion. Flat plate collectors have been in service for a long time without any significant changes in their design and operational principles [2] typically, conventional solar collectors (SC) use water pipes attached to the collecting plate where water circulates either naturally or forcibly and transfers the heat it collects to a storage tank. Some of the shortcomings of this type of solar collector systems include: the additional expense of a pump and the power to operate it; the extra space required for any natural circulation system; the corrosive effect of water; and the limited quantity of heat transferred by the fluid. Heat pipes offer a promising solution to these problems. The heat pipe is a device of very high thermal conductance; that is, it will transport energy without an appreciable drop in temperature [3]. The heat pipe is suitable for a wide range of applications including solar collector. Thus, solar collectors with heat pipes have a lower thermal mass, resulting in a reduction of start-up time [4]. Thermal diode is important in designing of solar collectors, where heat is transferred only from the evaporator to the condenser, but never in the reverse direction. This feature can cut off the heat loss when the absorber temperature is lower than that of the liquid in the heat exchanger [4-7]. Several studies on heat pipe solar collectors are reported in the literature. Riffat, [4] studied developing a theoretical model to investigate thermal performance of a thin membrane heat-pipe solar collector. In their work thin membrane heat pipe solar collector was designed and constructed to allow heat from solar radiation to be collected and showed it has high efficiency while keeping the capital cost low. Azad [8] investigated the heat pipe solar collector theoretically and experimentally, and gave the optimum ratio of heated length-cooled length of the heat pipe. Hull [9] investigated heat transfer factors and thermal efficiency for heat pipe absorber array connected to a common thermal conductance; that is, it will transport energy without an appreciable manifold and predicted that an array with less than ten heat pipes have significantly less efficiency than conventional flow through collector. Hussein [10] investigated the different design parameters of the natural circulation two phase closed Thermosyphon flat plate solar water heaters using the verified expanded model. Saravanan and Karunakaran [11] investigated the V-type absorber plate solar collector with heat pipe shows great potential in terms of higher absorption per unit area as compared to other conventional solar collectors. Ramkumar and Ragupathy [12] have shown that Response surface methodology (RSM) is a collection of mathematical and statistical techniques for developing, improving and optimizing process parameters by design of experiments. SenthilKumar [13]. Their objective was to optimize the output variable which is influenced by independent input variables. An experiment is a series of tests, called runs, in which changes are made in the input variables in order to identify the reasons for changes in the output response. The objective of present study is to optimize V-Trough solar collector with heat pipe operating parameters like heat input, angle of inclination and mass flow rate of cooling water by response surface methodology on the performance of Copper Deionised water heat pipe with wire mesh screen wicks. This paper analyse the experimental work done and the prediction of empirical relations for heat output, thermal resistance, overall efficiency of collector using response surface methodology. Therefore in the present study V-Grooved solar collector was tested at real conditions with a system installed at indoor conditions.
2. Response Surface Methodology
The experimental performance of the V-trough solar collector is analysed by Response surface methodology using Design of Expert software. Box-Behnken design method is employed with three input parameters namely inclination angle (A), heat input (B) and mass flow rate of water (C) with respect to three responses namely heat output (R1), thermal resistance (R2) and overall efficiency (R3) Table 1 shows the process parameter and their coded levels.Table 1. Process parameter 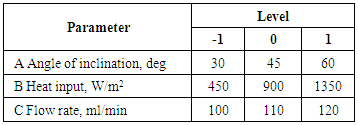 |
| |
|
3. Experimental Procedure
A prototype of V -Grooved solar collector with circular heat pipe was designed and tested at indoor facility of Mechanical measurements and dynamics lab of Annamalai University. V -Grooved solar collector with circular heat pipe is designed to collect and distribute heat by means of vaporization and condensation of a heat transfer fluid is shown in Figure 1. The specifications of heat pipe and solar collector are shown in Table 2. It comprised mainly of copper heat pipe with outside diameter of 18 mm for circular heat pipe with an evaporator length of 630 mm while the wick consisted of two layers of 100-mesh stainless steel screen fitted to the evaporator section. The evaporator section of the heat pipe was placed in V-grooved solar collector. The experimental setup consists of heat pipe, V-grooved solar collector and Water storage tank. The heat pipe was placed on the grooved absorber plate and tied in a flat plate solar collector. Working fluid used in the heat pipe was Deionised water. Glass wool insulation was provided below the absorber plate for reducing the conduction losses, the sides of the absorber plate are covered using thermo cool insulator for minimizing the convective losses. The glass plate is used for reducing the radiation losses by reradiating the heat emitted by the absorber plate in the form infrared rays. Number of glass plates used was one, if not most of solar radiation will get refracted. Solar power meter was used to measure the solar intensity in W/m2. The surface temperature of circular heat pipe, absorber plate and glass plate temperatures was measured using eight K-Type thermocouples. All the thermocouples were connected to the temperature indicator. The uncertainty in temperature measurement was ±0.1°C. Flow to condenser section was controlled by rotometer and flow rate was maintained at 100, 110 and 120ml/min.Table 2. Specifications of Heat pipe and solar collector 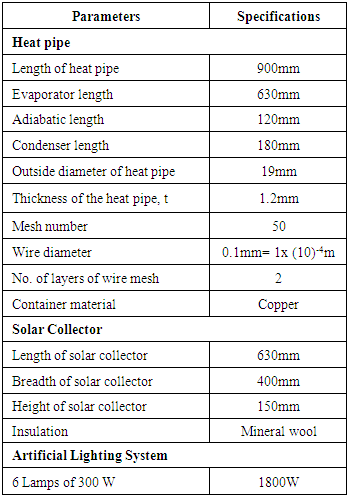 |
| |
|
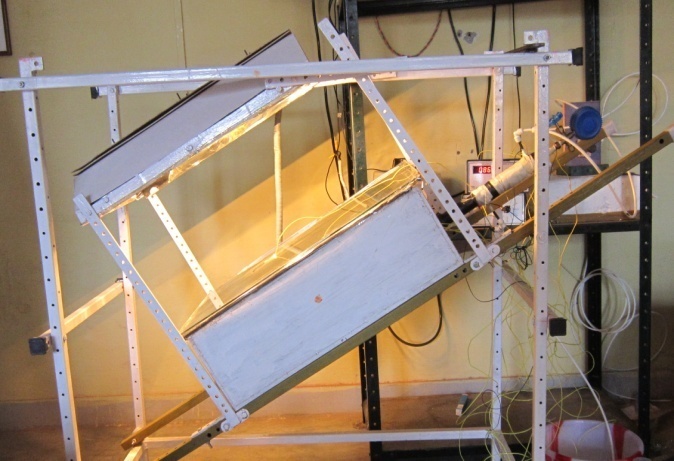 | Figure 1. Photographic view of Experimental Setup |
4. Results and Discussions
The computed values of the heat output, thermal resistance and overall efficiency are entered in the software design matrix. The RSM is used to develop the empirical relationship between experimental variables and the responses are heat output, thermal resistance and overall efficiency. A regression analysis is carried out to develop a best fit model to the experimental data, which are used to generate response surface plots. The table 3 and 4 shows the analysis of variance of variance (ANOVA) for all the three output parameters of V-Trough solar collector with circular heat pipe. For the present work, (A) Angle of inclination and (B) Heat input are producing significant effect than flow rate (C). The square valves of heat input and angle of inclination are also having major effect. The interaction effect between heat input and angle of inclination (AB) has more effect on heat output than heat input and flow rate (AC) and angle of inclination on the flow rate (BC) on heat output. The predicted Model F-value of 642.91 implies the model is significant. There is only a 0.01% chance that a "Model F-Value" of this magnitude could occur due to noise.Values of "Prob > F" less than 0.0500 indicate model terms are significant.In this case A, B, C, AB, A2, B2 are significant model terms.Values greater than 0.1000 indicate the model terms are not significant. Table 3. ANOVA table for response heat output of heat pipe 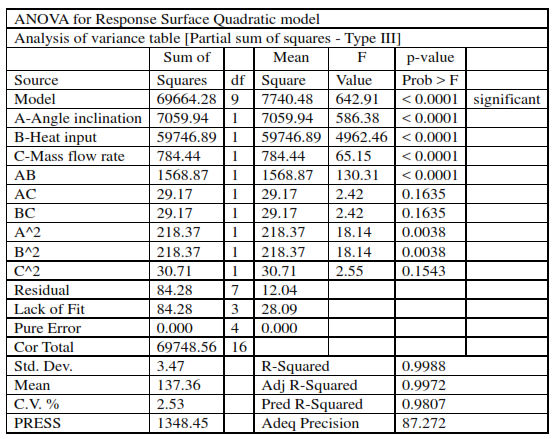 |
| |
|
Based on ANNOVA, the following emprical relation is developed to predict the heat output of heatpipe.Heat output =138.63157+29.706765×A+86.41×B+9.90×C+19.80×AB+2.70×AC+2.70×BC-7.20×A2+7.20B2-2.70×C2. Similarly, The Model F-value of 28.15 implies the model and model terms are significant. In this case A, B, B2, C2 are significant model terms. Values greater than 0.1000 indicate the model terms are not significant. The "Pred R-Squared" of 0.5698 is not as close to the "Adj R-Squared" of 0.9385 as one might normally expect. A ratio greater than 4 is desirable. The ratio of 18.733 indicates an adequate signal. This model can be used to navigate the design space. Thermal resistance = 0.123+0.011×A-0.055×B+0.005×C-0.012×AB+0.005×AC-0.0121×BC-0.002×A2+0.017×B2- 0.014×C2.Similarly, The Model F-value of 36.49 implies the model is significant. There is only a 0.01% chance that an F-value this magnitude could occur due to noise. Values of "Prob > F" less than 0.0500 indicate model terms are significant. In this case A, B, C, A^2 are significant model terms. Values greater than 0.1000 indicate the model terms are not significant. The "Pred R-Squared" of 0.6661 is not as close to the "Adj R-Squared" of 0.9523 as one might normally expect; i.e. the difference is more than 0.2. This may indicate a large block effectors a possible problem with the model and/or data. Things to consider are model reduction, response transformation, outliers, etc. All empirical models should be tested by doing confirmation runs. "Adeq Precision” measures the signal to noise ratio. A ratio greater than 4 is desirable. The ratio of 21.777 indicates an adequate signal. This model can be used to navigate the design space. Table 4. ANOVA table for thermal resistance of heat pipe 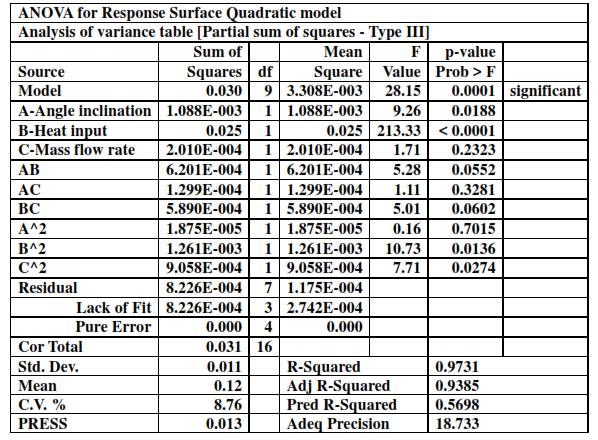 |
| |
|
Overall efficiency = 52.66 +10.66×A+8.09× B +3.93×C +2.51×A×B+1.03×AC-0.68BC-3.70×A2-1.31×B2-0.057×C2.It is observed from Figs. 2 to 4 that the heat output of heat pipe increases linearly with an increase in the heat input and angle of inclination in the evaporator section of V-grooved solar collector. The heat input and thermal resistances are not affecting the mass flow rate at condenser section. The heat output of heat pipe increases with the heat flux, due to temperature gradient between the evaporator section of V-grooved solar collector and condenser section. For higher values of heat input in the evaporator section, the heat generated in the surface is more and the working medium which is in the form of vapour moves vigorously in to condenser section. The cooling waters in the condenser absorbs this excessive heat and as a result, the efficiency of heat pipe increases. The thermal resistance (Rth) of the heat pipe is defined as ratio of temperature difference between the evaporator and condenser to the heat supplied to evaporator. From Figs. 5 to 7, thermal resistance of heat pipe decreases with increase with heat input and inclination angle of heat pipe. Mass flow rate is not affecting thermal resistance. Overall efficiency of the collector is the ratio of heat output to the total heat input over the evaporator section of heat pipe. It was found that whenever heat input and angle of inclination increases the overall efficiency of the setup also increases and the mass flow rate not affecting the efficiency. 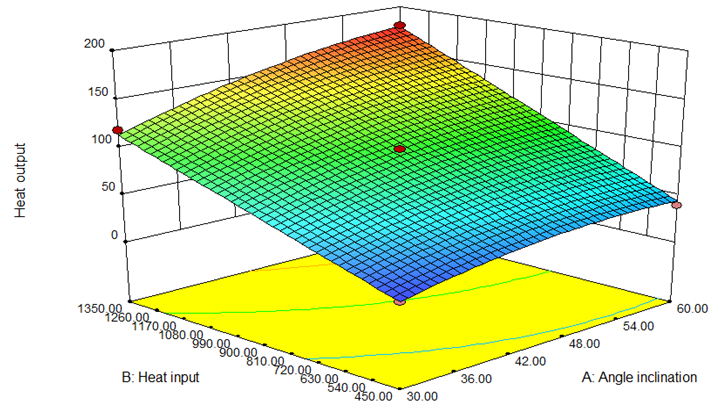 | Figure 2. Effect of heat input and angle of inclination to the heat output |
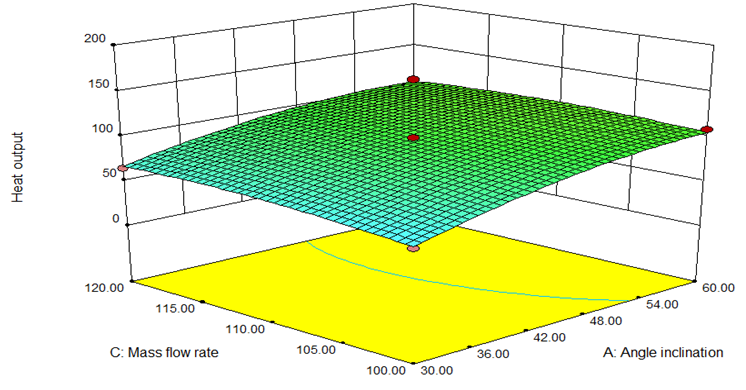 | Figure 3. Effect of mass flow rate and angle of inclination to the heat output |
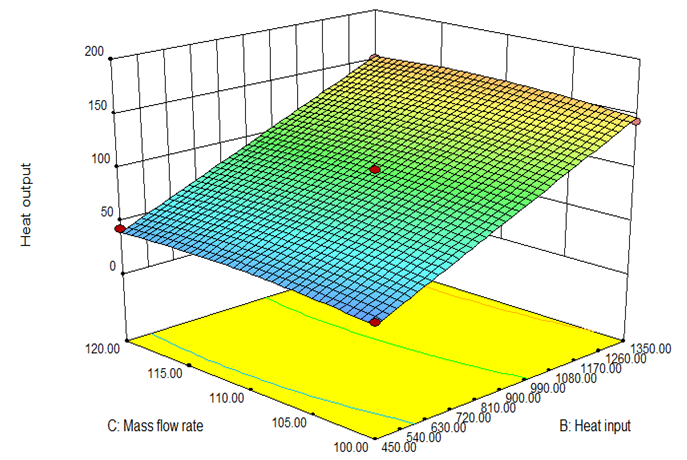 | Figure 4. Effect of mass flow rate and heat input to the heat output |
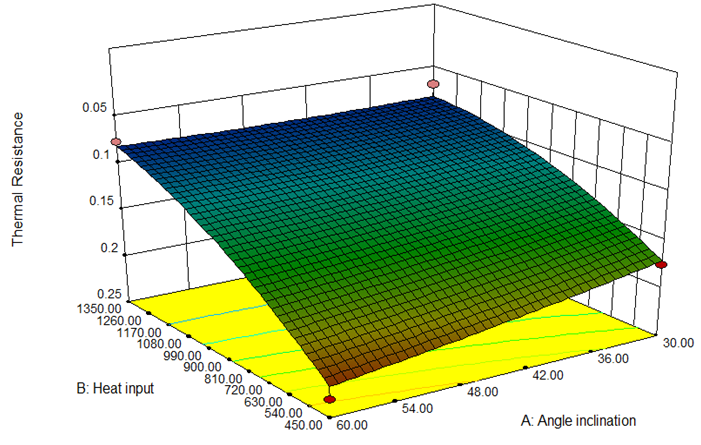 | Figure 5. Effect of heat input and angle of inclination to the thermal resistance |
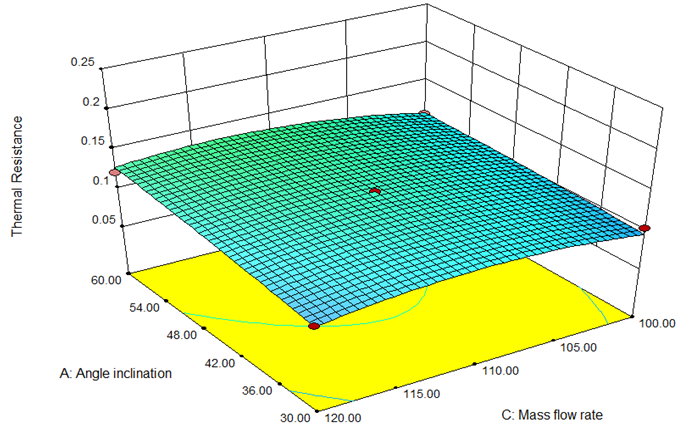 | Figure 6. Effect of mass flow rate and angle of inclination to the thermal resistance |
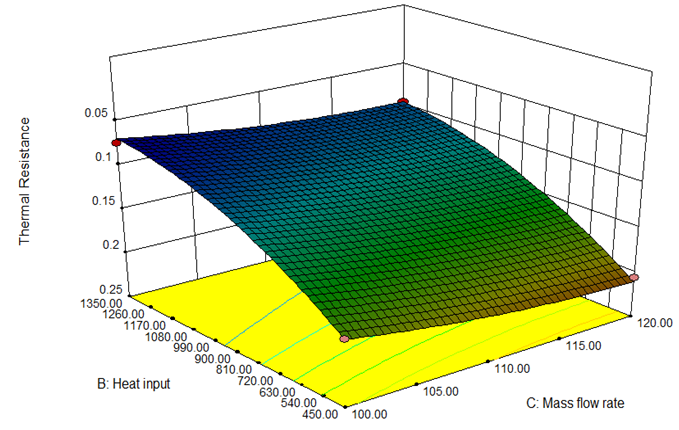 | Figure 7. Effect of mass flow rate and heat input to thermal resistance |
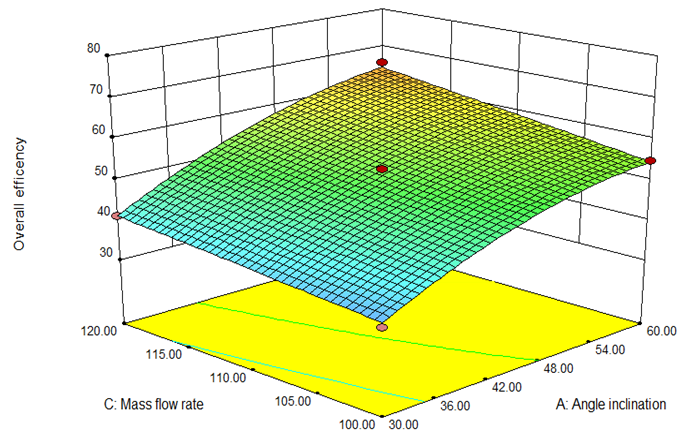 | Figure 8. Effect of mass flow rate and angle of inclination to the overall efficiency |
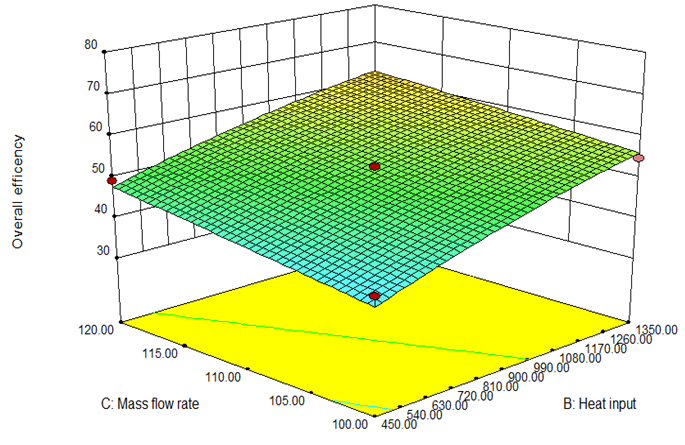 | Figure 9. Effect of mass flow rate and heat input to the overall efficiency |
4.1. Experimental Results
The experimental was conducted on V-grooved collector using Circular heat pipe with respective input parameters. Using observed values results has been calculated by mathematical expressions for Circular heat pipe. When Circular heat pipe is used in the setup, maximum heat output of 277.26W and maximum Overall efficiency of 68.22% is attained with 0.078°C/Wm2 of Thermal resistance with input parameters of 60° angle of inclination, 1350 w/m2 heat input and 110ml/min flow rate.
5. Conclusions
Optimization of the input parameters has been done using Box-Behnken design of RSM method with Design of Expert (version 9) software. It concludes that: Circular heat pipe: Optimum input parameters of the setup integrated with circular heat pipe obtained from RSM method are 55.23° angle of inclination, 1345.59W/m2 Heat input and mass flow rate at condenser section was 102.73ml/min.From the above mathematical results and RSM optimization it is concluded that experimental setup integrated with circular heat pipe gives higher heat output and overall efficiency with lesser thermal resistance.
ACKNOWLEDGEMENTS
The authors thank the authorities of Annamalai University for providing the necessary facilities in order to accomplish this piece work.
References
[1] | Faghri, A., “Heat Pipe Science and Technology”, Taylor and Francis, London, U.K., (1995). Dunn, P. D. and Reay, D.A., “Heat Pipe”, Third Ed. Pergamon Press, New York, U.S.A., (1982). |
[2] | Riffat, S.B., Zhao, X. and Doherrty, P.S., “Developing of a Theoretical Model to Investigate Thermal Performance of a Thin Membrane Heat Pipe Solar Collector”, J. Applied Thermal Eng., Vol. 25, (2005), 899-915. |
[3] | Riffat, S.B. and Zhao, X., “A Novel Hybrid Heat Pipe Solar Collector/CHP System”, J. Renewable Energy, Vol. 29, (2004), 2217-2233. |
[4] | Azad, E. and Bahar, F., “Solar Water Heater using Gravity-Assisted Heat Pipe”, Heat Recovery Systems and CHP, Vol. 7, No. 4, (1987), 343-350. |
[5] | Azad, E. and Bahar, F., “An experimental study of a coaxial heat pipe solar collector”, Journal of Heat Recovery Systems, Vol. 6, (1986), 255-258. |
[6] | Facao, J. and Oliveira, A.C., “Analysis of a Plate Heat Pipe Solar Collector”, Int. Conf. on Sustainable Energy Tech. Nottingham, U.K., (2004), 28-30. |
[7] | Azad, E., “Theoretical and Experimental Investigation of Heat Pipe Solar Collector”, Experimental Thermal and Fluid Science, Vol. 32, (2008), 1666-1672. |
[8] | Hull, J.R., “Analysis of Heat Transfer Factors for a Heat Pipe Absorber Array Connected to a Common Manifold”, J. of Solar Energy Engineering, Vol. 108, (1986), 11-16. |
[9] | Hussein, H.M.S., “Optimization of a Natural Circulation Two Phase Closed Thermosyphon Flat Plate Solar Water Heater”, Energy Conversion and Management, Vol. 44, (2003), 2341-2352. |
[10] | Chun, W., Kang, Kwak, H.Y. and Lee, Y.S., “An Experimental Study of the Utilization of Heat Pipes for Solar Water Heaters”, Applied Thermal Engineering, Vol. 19, (1999), 807-817. |
[11] | Saravanan. M, Karunakaran. N, "Experimental Analysis of Heat Pipe With V-Trough Solar Collector", International Journal Research in Advent Technology, Vol.02, issue11 (Nov 2014), pp19-23. |
[12] | Ramkumar, Ragupathy A "Application of response surface methodology for optimization of operating parameters and performance evaluation of cooling tower cold water temperature ", An International Journal of optimization and control theories & applications, vol.2, pp39-50, 2012. |
[13] | Senthilkumar R, Karthikeyan M "Analysis of energy conservation potential of the heat pipe using response surface methodology", An International Journal development research, vol.4, issue 3, pp570-574, 2014. |