Divakara Shetty 1, Debjyoti Sahu 1, Ravi Kumar 2, Sudesh Bekal 3
1Department of Mechanical Engineering, School of Engineering, Amrita Vishwa Vidyapeetham, Kasavanahalli, Bengaluru, India
2Department of Mechanical Engineering, Dr. MV Shetty Institute of Technology, Moodbidri, Mangalore, India
3Department of Mechanical Engineering, Nitte Mahalinga Adyanthaya Memorial Institute of Technology, Nitte, India
Correspondence to: Debjyoti Sahu , Department of Mechanical Engineering, School of Engineering, Amrita Vishwa Vidyapeetham, Kasavanahalli, Bengaluru, India.
Email: |  |
Copyright © 2015 Scientific & Academic Publishing. All Rights Reserved.
Abstract
Kerosene stoves are extensively used in villages of India and even in other countries. Kerosene being a petroleum product is not expected to last long at affordable price. Hence full or partial replacement of kerosene is to be explored. In this work, it is intended to see the possibility of using Pongamia oil in kerosene stoves (both pump stove and wick stove), however due to high viscosity and low capillarity action, use of virgin vegetable oil may not be successful without modification of existing cooking stoves. In order to improve the capillary action, a blend of kerosene and Pongamia oil has been tried. Transesterification of Pongamia oil is carried out in laboratory and suitably characterized before being subjected to combustion in standard commercial stove. Blends of 10 to 90% Pongamia oil-kerosene mixture and Pongamia oil-kerosene ester have been tested for emission aspect as well. Performance parameters like fuel consumption per unit time, time taken for heating water through fixed temperature are used for comparing various blends. Best efficiency is found at 40-50% of blend and is ~7.5% for a pump stove and for a wick stove it is ~5.6%. Further, it was observed that CO emission decreased with increase in Pongamia proportion in the blend at similar conditions.
Keywords:
Biokerosene, Esterification, Pongamia oil, Cooking stove, Emission
Cite this paper: Divakara Shetty , Debjyoti Sahu , Ravi Kumar , Sudesh Bekal , Performance and Emission Characteristics of Pongamia Oil-Kerosene Blend Used in Commercial Kerosene Stove, Energy and Power, Vol. 5 No. 1A, 2015, pp. 19-27. doi: 10.5923/c.ep.201501.05.
1. Introduction
The petroleum products which are being used for transport and domestic use are derived from depleting reserves [1-2]. Kerosene is a popular fuel for cooking among under privileged class in urban and rural India. As per an estimate by TEDDY, during the year 2011-12, approximately 855 people use 9.01 MT kerosene for cooking [2], in India. Kerosene is sold at highly subsidized price in India hence put a burden on the exchequer. Several blend variants are being tried for reducing use of pure kerosene. Non edible vegetable oils and their esters have great prospect in this cause. Generally for cooking a pump (pressurized) stove or a wick stove is used in India and other developing nations [3-4]. In wick stove the combustion mainly facilitated by the raise of fuel to the tip of the wick by the capillary action. Pure Kerosene, being a low viscous fluid, with high capillary action can easily rise up through the wick. Whereas vegetable oil will have viscosity of nearly fifteen times more than that of kerosene. Therefore it might not be preferable to use it in wick stove. However, a mixture of neat vegetable oil and kerosene can be burnt in wick stove. Singh reported that Jatropa oil blend upto 30% in biokerosene can be used in a pressurized stove and <10% can used in a wick stove [5]. Nagaraju and Gopal reported that Pongamia oil can be used in pressurized stove upto 100% [1]. Natarajan et al., reported that a modified stove can have overall efficiency of ~48% against 34% in a normal stove [6]. Jambhulkar et al., reported that with 50% blend with spent cooking oil a pressurized kerosene stove will have more efficiency (at 1.5 bar) than with pure kerosene [7].Bio-kerosene is a mixture of kerosene with vegetable oil. Here virgin Pongamia (karanja) oil and Pongamia oil methyl ester is mixed with kerosene in different proportions. Various parameters like viscosity, boiling point, flash point, fire point and calorific value are measured to characterize the fuel. Emission of CO CO2, unburnt hydrocarbon and NOx during combustion is measured for selected blends. This work aims at determining the appropriate biokerosene blend derived from Pongamia oil and Pongamia oil methyl ester for use in cooking stove.
2. Preparation of Blends
A mixture of kerosene and neat Pongamia oil/ Pongamia oil methyl ester have been tried in proportions of 10, 20, 30, 40, 50, 60, 70, 80 and 90% v/v. Esterification is carried out at 65°C following the procedure reported in literature [8-9]. First the oil is mixed with 6 ml 1 N H2SO4 and 17.6 ml methanol and stirred for 3h then cooled down to room temperature and separated from froth. Acidified oil is again mixed with 17.6 ml methanol and 1.02 g KOH stirred at 65°C. Separation yielded 750 ml of Pongamia oil methyl ester.
3. Characterization of Blends
The viscosities of various fuels were determined using Saybolt viscometer at a temperature of 40°C. The flash and fire point of fuels were determined using Cleaveland open cup tester. The boiling point of the mixture and density were also determined for all the blends.
4. Experimental Investigation
A commercial wick stove and a pump stove was used without any modification. The specifications of the wick stove and pump stove is given in table 1 and 2 respectively.Table 1. Specification of Wick stove 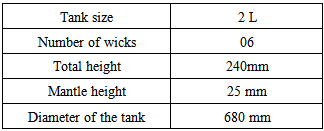 |
| |
|
Table 2. Specification of pump stove 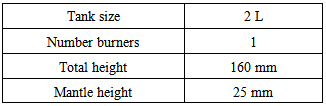 |
| |
|
The prepared fuel is poured in to the stove tank. The wick is adjusted for maximum height, after allowing for fuel rise fire was started and mantle was put in place (schematic is as shown in Fig. 1). One liter of water is taken in steel vessel (flat bottom) for heating in the stove. The time required for 20°C increase in temperature was noted. An arrangement was made to monitor the temperature of water. The fuel consumed was determined by comparing the weight of stove before and after the combustion with each blend. A range of experiments were conducted with kerosene and neat Pongamia oil followed by kerosene and esterified pongamia oil blends.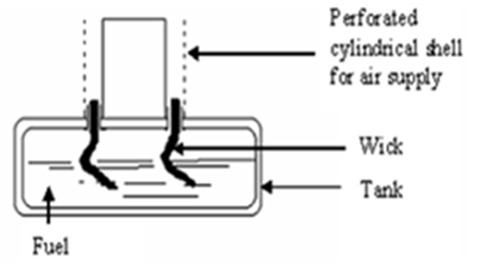 | Figure 1. Schematic diagram of a wick stove |
Experiments were conducted with blends of Pongamia oil and kerosene in the same proportion in the pump stove as done in case of the wick stove (schematic is as shown in Fig. 2). For building up fuel pressure number of pumping (five times pumping builds up ~1.5 bar pressure), (ii) the time allowed from starting of flame to beginning of heating process (five minutes) were maintained similar for each blend. Flame photographs were taken using a Sony cybershot T99 (14.5 MP) camera. A 5-gas analyzer equipped with vacuum pump was used to measure the CO, CO2, NOx and unburnt Hydrocarbon emission. Gas probe was inserted through outlet of a hood fixed at the top covering the entire flame range of the stove.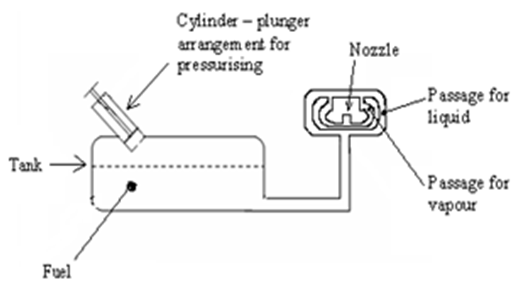 | Figure 2. Schematic of a pump stove |
5. Results and Discussions
In the operation of wick stove one of the important parameter for efficient working is capillary action. The variation in capillary height for two combinations of fuels is shown in Fig 3. Higher capillary action is required for continuous replenishment of oil to the wick tip. The kerosene and esterified Pongamia oil blend has higher capillary action compared to the kerosene and neat Pongamia oil blend.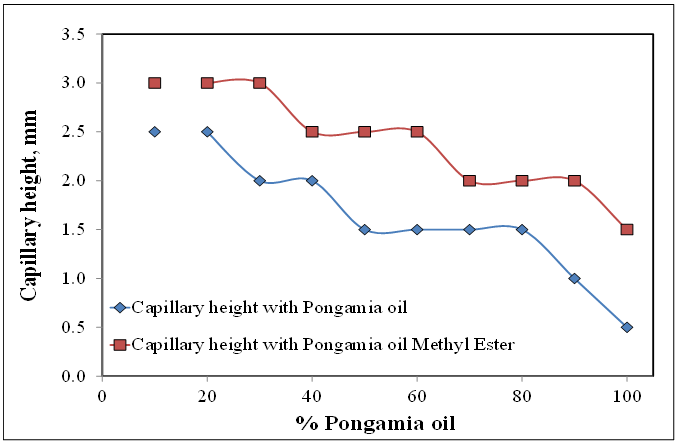 | Figure 3. Capillary height for different blends |
Vegetable oils have very high viscosity which results in lower capillary action thus lowering the burning efficiency. The difference with respect to blend proportion is almost linear. As shown in Fig. 3, it was observed that kerosene and esterified Pongamia oil blend has lower viscosity and due to this capillary effect is expected to be more than blend with virgin Pongamia oil. For wick stove there is increase in the time consumed with increase in Pongamia oil/ester proportion in the blend. The percentage increase in time consumed, given in Fig. 4 and 5 indicate a sharp increase (~200%) beyond 40% for Pongamia oil-kerosene blend. However, kerosene and esterified Pongamia oil blend show no such dramatic increase. However, the time consumed increases almost linearly with proportion of kerosene and esterified Pongamia oil blend. Incidentally, the flash and fire point, show higher values, again beyond 40% and no such increase observed for Pongamia oil methyl ester. The reason that can be attributed to the above behavior for kerosene and neat Pongamia oil blend is that the oil coming up by capillary action appears to be taking longer time to vaporize and form air fuel mixture, thus, when it is ready for burning, the previous flame - that is if flame is compartmentalized - would diminish; thus producing a low intensity flame. In the case of kerosene and esterified pongamia oil blend no such difficulties arose. The phenomenon goes on deteriorating, consequently producing poorer flame for kerosene-neat Pongamia oil blend. Also seen in Fig. 6, is the variation in viscosity for various blends of kerosene-neat Pongamia oil. At the fringe value of 50P, the viscosity has increased by almost 170%. This might be causing a decrease in capillary action with resulting poor flame. The corresponding increase in viscosity for kerosene and esterified Pongamia oil blend is 25% only. In fact, viscosity for different proportions of ester in kerosene and esterified Pongamia oil blend is almost the same.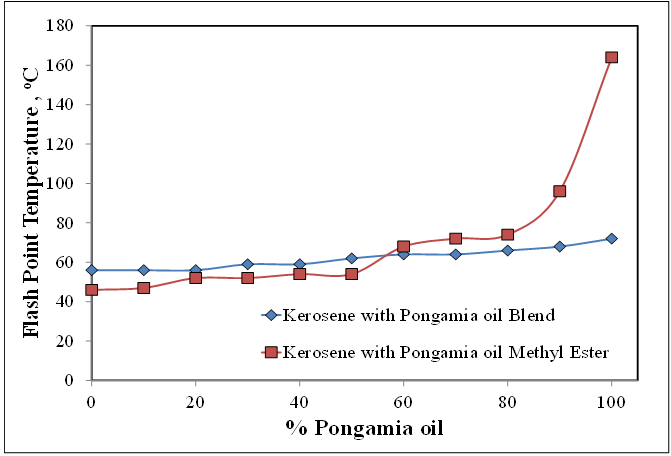 | Figure 4. Variation of flash point temperature of different blends |
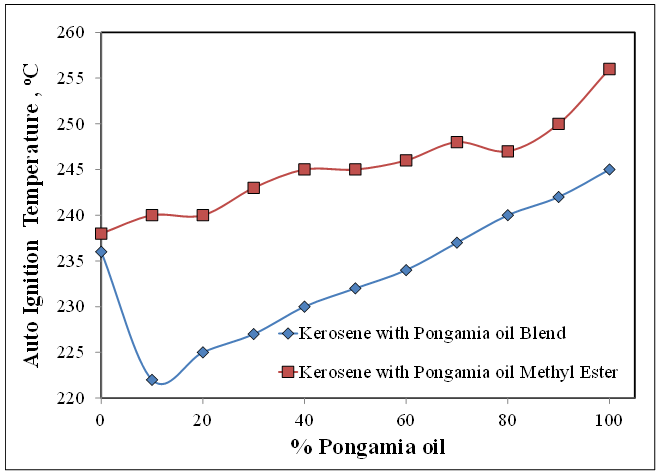 | Figure 5. Variation of fire point temperature of different blends |
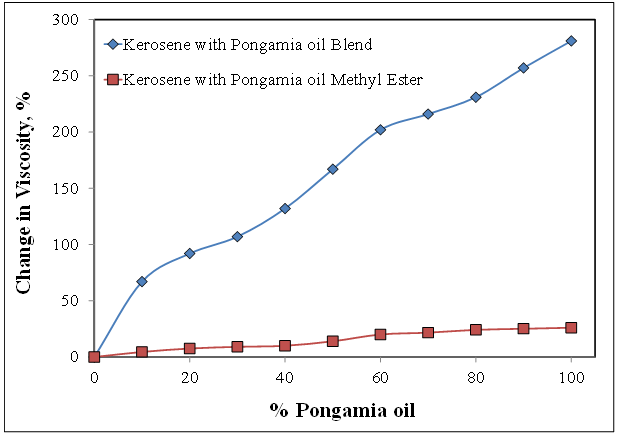 | Figure 6. Variation of viscosity of kerosene-Pongamia oil and kerosene/esterified Pongamia oil blends |
The variation in time consumed for rising the temperature of water by 20°C when using Kerosene-virgin Pongamia oil is presented in Fig. 7 for both wick and pump stove. The difference in thermal efficiency derived from water boiling technique is plotted in the secondary axis in the same figure. Fuel consumption increases and the efficiency decreases linearly with higher proportion of Pongamia oil in the blend in a wick stove. However in pump stove the fuel consumption rate does not change much between 20-40% of Pongamia oil.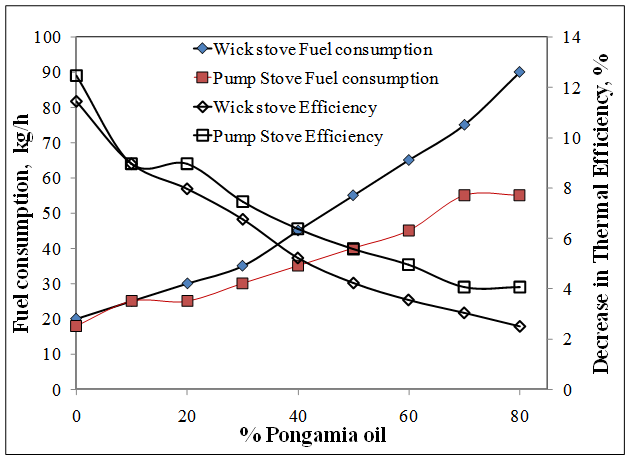 | Figure 7. Fuel consumption and difference in efficiency with respect to kerosene using kerosene/Pongamia oil blends |
The variation in time taken for increase in temperature with wick stove and pump stove for kerosene-esterified Pongamia blend is given in Fig. 8. As seen in the figure there is no appreciable change in “time consumed” with pump stove operation. This may be because of the fact that in a pump stove the flow of oil to the nozzle is not due to capillary action, but due to pressurization. Subsequently, the flame will form if the oil reaching the nozzle vaporizes. Till a blend of 80%, a stable flame is formed, however, for 90% blend the flame formation abruptly stops, and oil simply spurts out of the nozzle. This might be attributed to oil reaching cut-off boiling temperature which the initial heating was not capable of producing, thus resulting in no vapour formation; on opening the knob just the liquid comes out and fails to form air-fuel mixture. However for kerosene-esterified Pongamia oil no such difficulties are observed even at higher proportion of ester in the blend. On recognizing reason for the above difficulty with kerosene-neat Pongamia oil blend, the time of initial heating was increased and it was found that a proper flame was formed. Subsequently, on increasing the proportion of Pongamia oil to 100%, as expected, only liquid surged out. As with 90%, initial heating time was increase, which resulted in proper flame formation. However, flame was sustained for only a short period of time, the reason behind that being the flame produced was not strong enough to sustain vapour formation.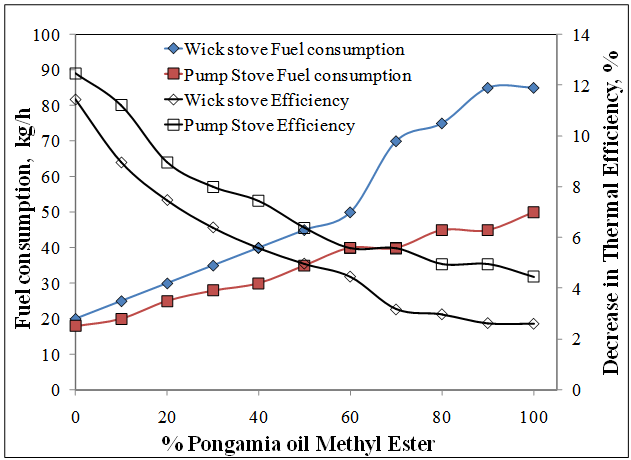 | Figure 8. Fuel consumption and difference in efficiency with respect to kerosene using kerosene/Pongamia oil methyl ester |
The flame produced by pump stove for various blends of kerosene and Pongamia oil is shown in Fig. 9, and one produced by wick stove in Fig. 10. In the Fig. 9, it is seen that the flames are more bluish for blends 50%, 60%, 70% and 80%. A proper burning results in a bluish flame as results of good fuel vapour and air mixture formation. Even though, the viscosity increases with increase in oil content, contrary to the belief that it would result in poor flame formation, may be the oxygen concentration increases with increase in oil proportion thus aiding the burning process, resulting a bluish flame. However, at much higher proportion of oil, all the advantage gained by the increased oxygen concentration, is lost due to substantial increase in viscosity. 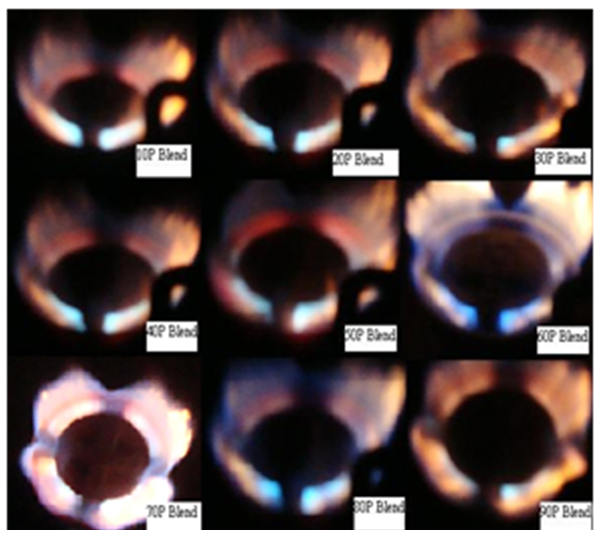 | Figure 9. Comparison of flames produced by pump stove for various combinations of kerosene and Pongamia oil (Left to right: increasing order of Pongamia oil in blend) |
The flames produced by wick stove as seen in Fig. 10 are similar to the ones produced by pump stove. The same reasoning which was put forth earlier for pump may still holds good here.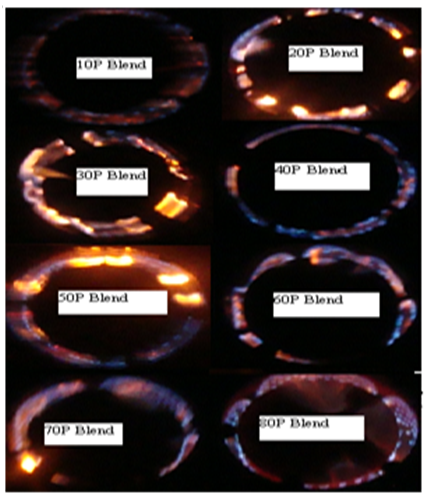 | Figure 10. Comparison of flames produced by wick stove for various combinations of kerosene and Pongamia oil (Left to right: increasing order of Pongamia oil in blend) |
The flame produced by pump stove for various blends of kerosene and esterified Pongamia oil is shown in Fig. 11, and one produced by wick stove in Fig. 12. It can be seen that, generally in all cases good blue flame is visible for all proportions of biokerosene in the blend.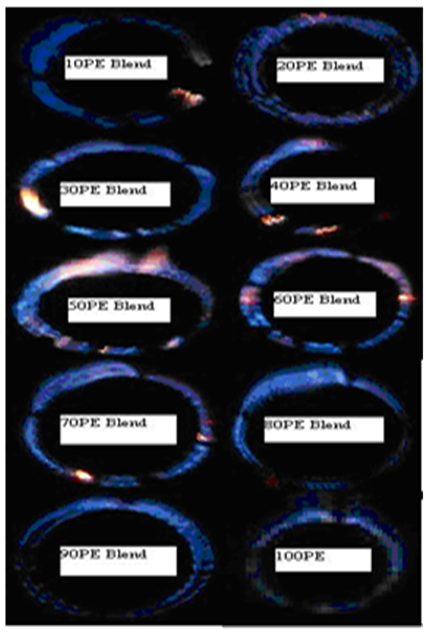 | Figure 11. Comparison of flames produced by wick stove for varying proportion of kerosene and Pongamia oil methyl ester (Left to right: increasing order of Pongamia oil methyl ester in blend) |
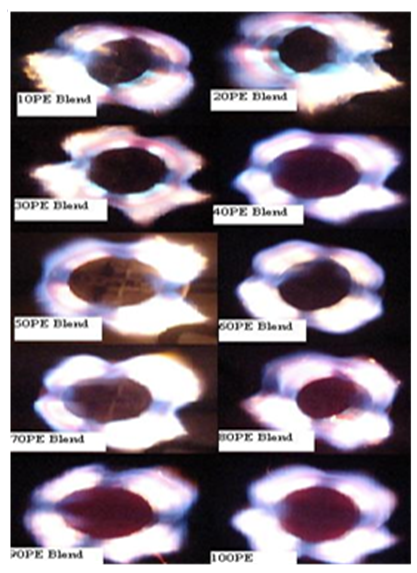 | Figure 12. Comparison of flames produced by pump for varying proportions of kerosene and Pongamia oil methyl ester (Left to right: increasing order of Pongamia oil methyl ester in blend) |
Measuring emission of gases like CO, CO2, NOx and unburnt hydrocarbon is utmost important. As Kathleen and Elizabeth reported the direct effect of gases emitted from stoves may cause asthma while using it indoor [10]. Fig 13 and 14 shows the variation of such gases with respect to % Pongamia oil or % Pongamia oil methyl ester content in the blend in a wick stove. There is no NOx formation while using blend of Pongamia oil/ esterified Pongamia oil in a wick stove and the CO emission decrease with higher proportion of blend. However, heat release is less with higher proportion blend as the calorific value decreases. Increase of CO2 emission may indicate a better combustion in case of esterified Pongamia oil as it’s a better oxygenated fuel [11].Similarly various product gas quantities as detected by the gas analyzer are represented in Fig. 15 and Fig. 16 respectively. In pump stove there is a formation of NOx (Fig. 16) and higher order of CO2 than the wick stove and for pure kerosene the emission is marginally higher. Increase of NOx emission may indicate a higher heat release in case of esterified Pongamia oil as it’s a better oxygenated fuel [12]. It was observed that CO emission decreased with increase in Pongamia oil proportion in the blend for both pump stove as well as wick stove. However, the cooking can be done faster in a pump stove when compared to a wick stove even when using biokerosene blends [7] as it has better efficiency when compared to wick stove (Fig. 7). Therefore blend of ~50% Pongamia oil methyl ester is seems most suitable with least emission and reasonable efficiency in cooking stove. 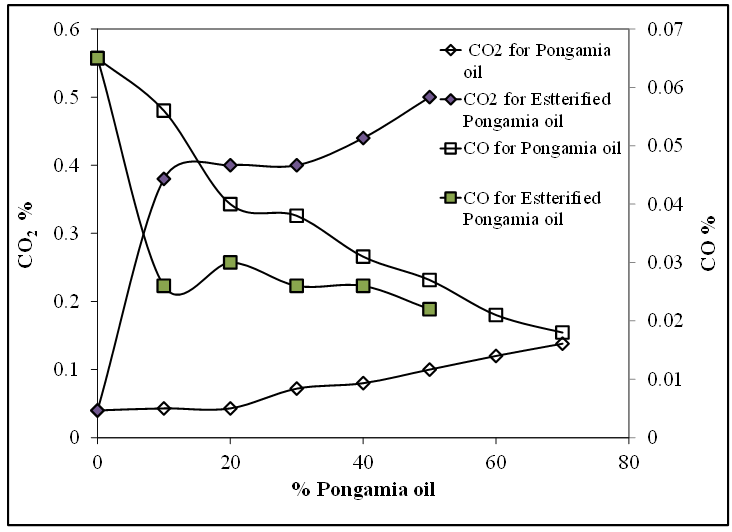 | Figure 13. Variation of CO and CO2 emission using different blends in wick stove |
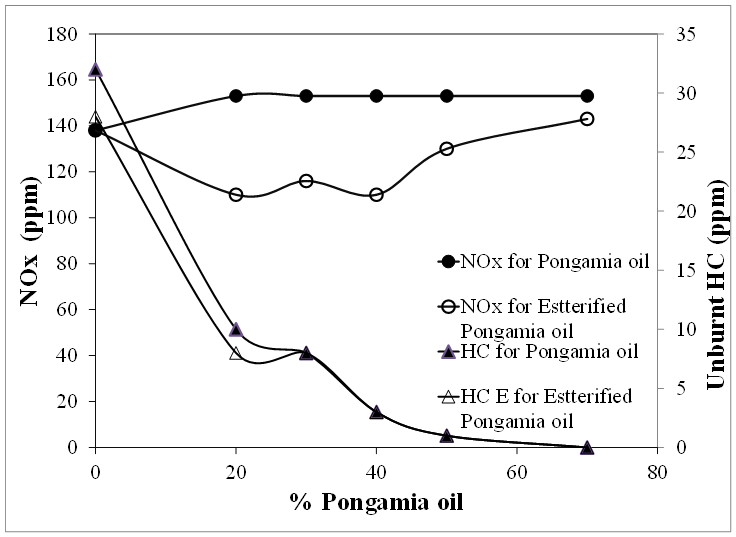 | Figure 14. Variation of NOx and unburnt hydrocarbon emission using different blends in wick stove |
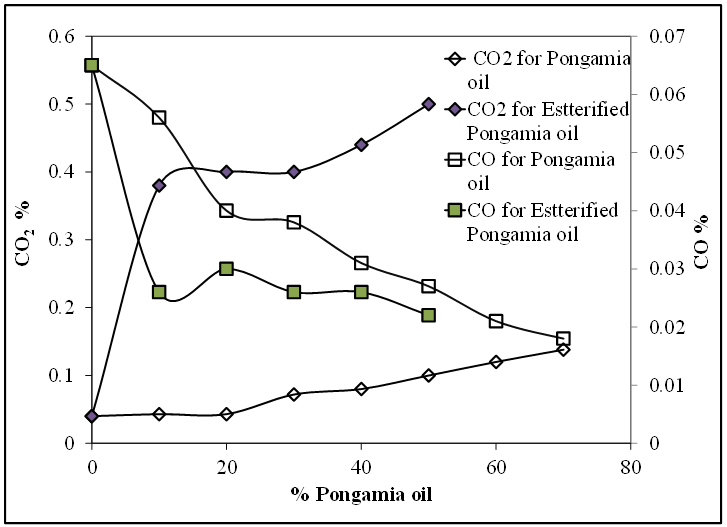 | Figure 15. Variation of CO and CO2 emission using different blends in pump stove |
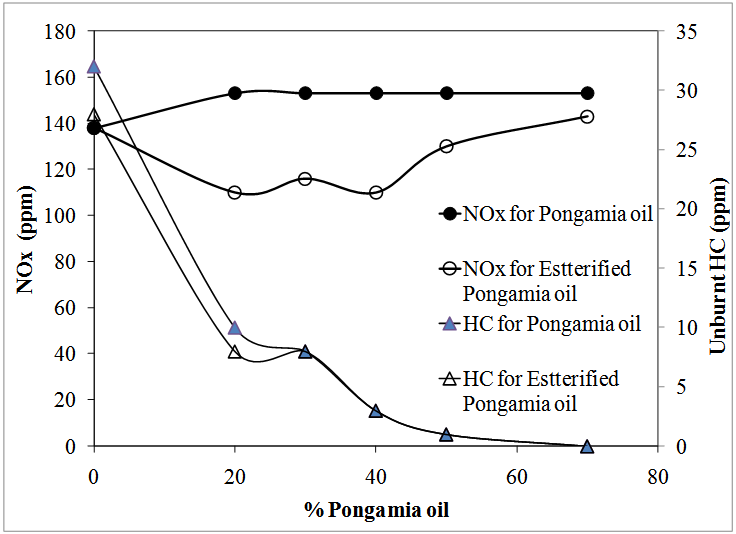 | Figure 16. Variation of NOx and unburnt hydrocarbon emission using different blends in pump stove |
6. Conclusions
The operation with pump stove is better than wick stove when using kerosene and biokerosene blends as fuel. Use of kerosene and Pongamia oil blend beyond certain proportion (80P) of virgin Pongamia oil results poor combustion. Hence higher proportion of kerosene and virgin Pongamia oil blend is not recommended for wick stove. When using pump stove any proportion of kerosene and Pongamia oil blend can be used. However use of kerosene and esterified Pongamia oil blend will reduce fuel consumption.As far as proportion of blend to be used is concerned higher proportions can be used in pump stove without much loss in efficiency. However, when using wick stove use of lower proportions of biofuel is recommended as higher proportions results in large drop of efficiency. From emission point of view CO2 and NOx emission in case of a pump stove is much higher than wick stove. However CO emission drops to higher blending of Pongamia oil or Pongamia oil methyl ester both in pump stove and in wick stove.
ACKNOWLEDGEMENTS
Authors are thankful to Atulya Udaykumar and Srikanth K. M. from Amrita Vishwa Vidyapeetham, Bengaluru for their support in conducting few experiments during this work.
References
[1] | Nagaraju, Y., Gopal, L., 2013, Development and Performance Assessment of a Pressurized Cook Stove Using a Blend of Pongamia Oil and Kerosene, Int. J. Sci. Res., 2(4), 99-100. |
[2] | Dorland, E. and Jain, M., 2009, Kerosene marketing program in India, (www.scaindia.org/control). |
[3] | Stephen, K., John K. and Oscar O., 2008, Energy access among the urban poor in Kenya, Energ. Sustain. Dev., 12(4), 38-48. |
[4] | Prasad, G., 2008, Energy sector reform, energy transitions and the poor in Africa, Energ. Policy, 36(8), 2806-2811. |
[5] | Singh, R. N., 2011, Straight vegetable oil: An alternative fuel for cooking, lighting and irrigation pump, IIOAB Journal, 2(7), 44–49. |
[6] | Natarajan, R., Karthikeyan, N. S., Avinash A. and Sathiyanarayanan, K., 2008, Use of vegetable oil as fuel to improve the efficiency of cooking stove, Renewable Energ., 33(11), 2423-2427. |
[7] | Jambhulkar, N. V., Pal, M., Fuke, N., Khandelwal, P., Sonule, P., Narnawre, S., Katekar V. P., 2015, Performance Evaluation of Cooking Stove Working on Spent Cooking Oil, Int. J. Emerg. Sci. Eng., 3(4), 26-31. |
[8] | Venkatesan, M., Vikram C. J. and Naveenchandran P., 2012, Performance and Emission Analysis of Pongamia Oil Methyl Ester with Diesel Blend, Middle-East J. Sci. Res., 12 (12), 1758-1765. |
[9] | Bekal, S. and Babu, T. P. A., 2008, Bio-fuel variants for use in CI engine at design and off-design regimes: An experimental analysis, Fuel, 87, 3550-3561. |
[10] | Kathleen, B. and Elizabeth, W. T.; 2008, Indoor Combustion and Asthma, Immunol. Allergy Clin. North Am., 28(3), 507-519. |
[11] | Venkatraman, M., Devaradjane, G., 2014, Performance and exhaust emissions of a low heat rejection diesel engine using Jatropha oil as a fuel, J. Chem. Pharmaceutical Res., 6(11); 561-569. |
[12] | Baskar, P., Nanthagopal, K. and Elango, T., 2011, The effect of two oxygenates on diesel engine emissions, ARPN J. Eng. Appl. Sci., 6(3), 55-60. |